40m3卧式液氧储罐施工方案.docx
《40m3卧式液氧储罐施工方案.docx》由会员分享,可在线阅读,更多相关《40m3卧式液氧储罐施工方案.docx(12页珍藏版)》请在冰豆网上搜索。
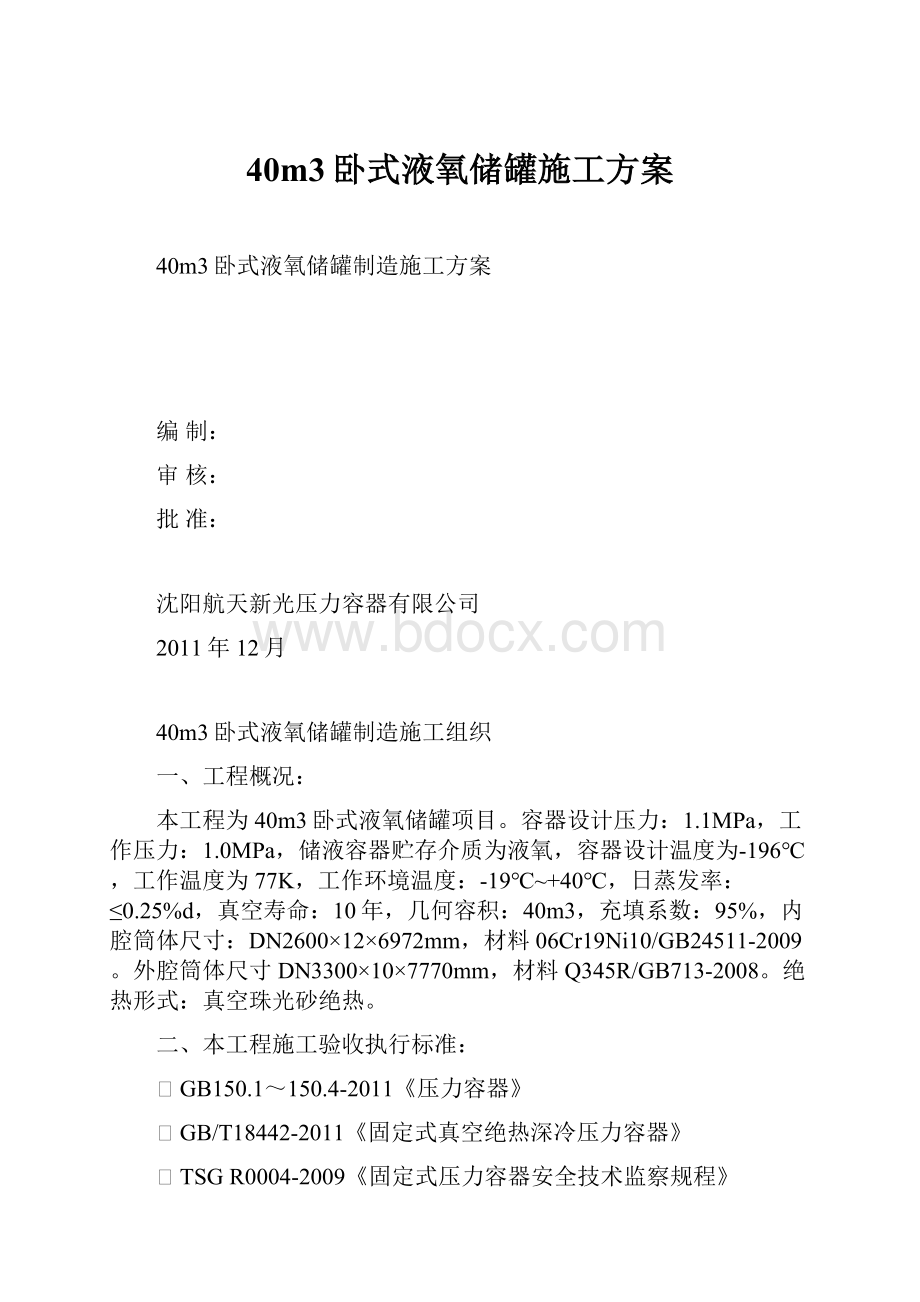
40m3卧式液氧储罐施工方案
40m3卧式液氧储罐制造施工方案
编制:
审核:
批准:
沈阳航天新光压力容器有限公司
2011年12月
40m3卧式液氧储罐制造施工组织
一、工程概况:
本工程为40m3卧式液氧储罐项目。
容器设计压力:
1.1MPa,工作压力:
1.0MPa,储液容器贮存介质为液氧,容器设计温度为-196℃,工作温度为77K,工作环境温度:
-19℃~+40℃,日蒸发率:
≤0.25%d,真空寿命:
10年,几何容积:
40m3,充填系数:
95%,内腔筒体尺寸:
DN2600×12×6972mm,材料06Cr19Ni10/GB24511-2009。
外腔筒体尺寸DN3300×10×7770mm,材料Q345R/GB713-2008。
绝热形式:
真空珠光砂绝热。
二、本工程施工验收执行标准:
ØGB150.1~150.4-2011《压力容器》
ØGB/T18442-2011《固定式真空绝热深冷压力容器》
ØTSGR0004-2009《固定式压力容器安全技术监察规程》
三、保证实现工期目标的组织技术措施
3.1施工技术准备
3.1.1组织有关人员熟悉施工合同内容和文件中关于技术规范的规定,熟悉国家现行施工规范,建筑法规及本施工组织设计中关于施工方案工期、质量、安全、文明施工等各项措施。
3.1.2组织技术人员读识施工图纸,深刻领会设计意图和图纸的全部内涵,分清重要部分项工程及其技术特点,核对图纸的平立剖关系及几何尺寸,为图纸会审作准备。
3.1.3在业主和监理的组织下,与设计单位进行图纸会审形成会审记录。
3.2.4编制主要分部分项工程的施工规范,报业主审批,编制总体施工进度计划,制定各项制度。
3.2.5根据实际需要组织对专业施工队伍进行技术和安全培训。
3.1.6制定材料、设备采购计划,并组织实施。
3.1.7准备各种技术资料记录用品。
3.2组织材料设备进场
根据材料需要量计划,分阶段按施工进度需要组织材料进场,进场后需要检查的立即进行检查,并保证在施工需要前完成。
四、主要施工方案及技术措施
4.1设备的制造及安装
1、内胆筒体的制造
内胆圆筒内径DN2600×12×6972mm。
机加工筒节及环焊缝、角焊缝坡口。
具体要求如下:
(1)筒体按照设计图纸和焊接工艺的要求,进行筒体内外表面、接管孔和环向焊接接头坡口加工。
机加工筒节及环焊缝、角焊缝坡口:
坡口表面不得有裂纹、分层、夹渣、挤压、鱼鳞状痕迹等缺陷,表面粗糙度不低于25。
(2)筒体焊接或吊运时尽量避免在其上焊接临时卡具、吊耳等。
临时工装去除时不得伤及筒体,同时进行渗透检测,按标准JB/T4730.5-2005执行,严格按焊接工艺要求进行焊接。
2、内胆封头的制造
储罐内胆上、下封头都采用椭圆形封头,材料为06Cr19Ni10板,GB24511-2009。
封头制造的工艺流程为:
下料旋压成型刨边加工环缝
1)下料:
等离子下料,清除氧化物及渣瘤、飞溅。
修磨周边圆滑,端面不得有裂纹、夹渣。
2)旋压成型:
外委
3)刨边:
坡口表面不得有裂纹、分层、夹渣、挤压或鱼鳞状痕迹等缺陷。
粗糙度不低于25。
4)加工环缝及接管处坡口组焊接管:
机械加工表面和非机械加工表面的线性尺寸极限偏差,应分别符合GB/T1804中m级和c级的规定。
坡口表面不得有裂纹、分层、夹渣、挤压、鱼鳞状痕迹等缺陷,表面粗糙度不低于25,之后按照
《焊接工艺规程》进行组对焊接。
3、内胆的焊接
(1)焊接工艺评定
设备的主材为06Cr19Ni10,必须按NB/T47014-2011《承压设备焊接工艺评定》进行评定,其中对接焊分别采用埋弧焊、手工电弧焊等焊接方法进行评定。
使其符合NB/T47014-2011《承压设备焊接工艺评定》。
施焊前,受压元件焊缝、与受压元件相焊的焊缝、熔入永久焊缝内的定位焊缝、受压元件母材表面补焊以及上述焊缝的返修焊缝都应依据NB/T47014-2011进行焊接工艺评定或具有经过评定合格的焊接工艺支持。
(2)焊接方法
筒体之间、筒体与封头之间的焊接采用手工电弧焊焊接,坡口形式采用单面V形坡口。
(3)焊接程序与检验方法
1.焊接环境
焊接环境出现下列任意情况时,应采取有效防护措施,否则禁止施焊:
1)风速:
气体保护焊大于2m/s,其他焊接方法大于10m/s;
2)相对湿度大于90%。
3)雪雨环境:
①各种小型器材必须设棚以保证不受雨雪淋湿。
②机电设备必须加防雨罩,以免因潮湿而损坏设备,做好接地保护,安装漏电保护装置,以防漏电伤人。
雨后应对电气设施进行检查。
③雨季施工时施工人员要备齐各种防雨用具,使用电动工具的操作人员穿绝缘胶鞋、戴绝缘手套。
④各种通行的通道均设防滑条或有防滑措施。
⑤每日早晨及时掌握天气情况,对职工加强思想教育,保证雨季施工的顺利进行,防止各类事故在雨季施工中发生。
4)焊件温度低于-20℃。
2.焊前准备
1)焊前根据焊接工艺评定编制出焊接工艺指导书。
2)焊前按技术条件要求清理焊接坡口表面及两侧、表面的油、水、污物、熔渣和其他有害物质,并按技术标准施焊。
3)焊条按规定烘干、保温;焊丝需去除油、锈,保护气体应当干燥。
4)制造过程中如原有标志被裁掉或材料分成几块时,应及时完成标志的移植,不允许采用硬性标记。
3.组对定位
1)组对定位后,坡口间隙、错边量、棱角度等应符合图样规定或施工要求。
2)避免强力组装,定位焊缝长度及间距应符合焊接工艺文件的要求。
3)定位焊缝不得有裂纹,否则应清除重焊。
如存在气孔、夹渣时亦应去除。
4.焊接焊缝
1)焊工应当根据图样、工艺文件、技术标准施焊。
2)多层焊时将熔渣清理干净再焊下层,清渣应在完全凝固后进行。
3)按《焊接工艺规程》要求:
1选用A107焊条进行焊接,烘干温度为250℃/1h。
焊接过程中层间清理干净,检验员按层检查,记录焊接工艺参数,焊后焊工填写“施焊记录”,焊后清理。
2清理表面焊渣,自检合格后,做焊工代号标记。
5.焊接检查与检验
焊前:
1)母材、焊接材料:
选用焊接材料保证焊缝金属的力学性能高于或等于母材规定的限值,或符合设计文件规定的技术条件。
2)焊接设备、仪表、工艺装备
3)焊接坡口、接头装配及清理
4)焊工资质
5)焊接工艺文件
施焊过程中:
1)焊接规范参数
2)执行焊接工艺情况
3)执行技术标准情况
4)执行设计文件规定情况
焊后:
1)实际施焊记录
2)焊缝外观及尺寸
3)产品焊接试件
4)无损检测
A、B类焊接接头应进行100%射线检测。
按JB/T4730.2-2005的要求,技术等级不低于AB级,合格等级为II级。
C、D类焊接接头应进行100%渗透检测,符合JB/T4730.5-2005中的Ⅰ级为合格。
5.2内胆气压试验
①压力试验过程
试验时应先缓慢升压至0.13Mpa,保压5min,并且对所有焊接接头和连接部位进行初次检查;确认无泄漏后,再继续升压至0.67Mpa;如无异常现象,其后按规定试验压力的10%逐级升压,直到试验压力1.342Mpa,保压10min;然后降至1.1Mpa,保压足够时间进行检查,检查期间压力应保持不变。
②压力试验注意事项
进行气压试验的容器焊缝应经100%的无损探伤检验合格。
气压试验的容器试压前,要全面复检有关技术文件制定试压方案,要有可靠的安全措施,并经厂技术部门和安全部门负责人检查、批准后方可进行。
试验所用气体应为干燥洁净的空气、氮气或其他惰性气体。
气压试验应有安全措施,试验单位的安全管理部门应当派人进行现场监督。
试验压力和必要时的强度校核按GB150.1-2011的规定。
③气压试验的合格标准
对于气压试验,容器无异常声响,经肥皂液或其他检漏液检查无漏气,无可见的变形。
4、外胆筒体的制造
外胆圆筒内径DN3300mm,直筒段长度7770mm,罐壁厚度10mm,总长度约9276mm。
机加工筒节及环焊缝、角焊缝坡口。
具体要求如下:
(1)筒体按照设计图纸和焊接工艺的要求,进行筒体内外表面和环向焊接接头坡口加工。
机加工筒节及环焊缝、角焊缝坡口:
坡口表面不得有裂纹、分层、夹渣、挤压、鱼鳞状痕迹等缺陷,表面粗糙度不低于25。
(2)筒体焊接或吊运时尽量避免在其上焊接临时卡具、吊耳等。
临时工装去除时不得伤及筒体,同时进行MT检测,按标准JB/T4730.4-2005执行,严格按焊接工艺要求进行焊接。
2、外胆封头的制造
储罐外胆上、下封头都采用浅碟形封头,材料为Q345R板。
封头制造的工艺流程为:
下料旋压成型刨边加工环缝及接管处坡口组焊接管
1)下料:
气割下料,清除氧化物及渣瘤、飞溅。
修磨周边圆滑,端面不得有裂纹、夹渣。
2)旋压成型:
外委
3)刨边:
坡口表面不得有裂纹、分层、夹渣、挤压或鱼鳞状痕迹等缺陷。
粗糙度不低于25。
4)加工环缝及接管处坡口组焊接管:
机械加工表面和非机械加工表面的线性尺寸极限偏差,应分别符合GB/T1804中m级和c级的规定。
坡口表面不得有裂纹、分层、夹渣、挤压、鱼鳞状痕迹等缺陷,表面粗糙度不低于25,之后按照
《焊接工艺规程》进行组对焊接。
3、外胆的焊接
(1)焊接工艺评定
设备的主材为Q345R,GB713-2008。
必须按NB/T47014-2011《承压设备焊接工艺评定》进行评定,其中对接焊分别采用埋弧焊、手工电弧焊等焊接方法进行评定。
使其符合NB/T47014-2011《承压设备焊接工艺评定》。
施焊前,受压元件焊缝、与受压元件相焊的焊缝、熔入永久焊缝内的定位焊缝、受压元件母材表面补焊以及上述焊缝的返修焊缝都应依据NB/T47014-2011进行焊接工艺评定或具有经过评定合格的焊接工艺支持。
(2)焊接方法
筒体之间、筒体与封头之间的焊接采用手工电弧焊焊接,坡口形式采用单面V形坡口。
(3)焊接程序与检验方法
1.焊接环境
焊接环境出现下列任意情况时,应采取有效防护措施,否则禁止施焊:
1)风速:
气体保护焊大于2m/s,其他焊接方法大于10m/s;
2)相对湿度大于90%。
3)雪雨环境:
①各种小型器材必须设棚以保证不受雨雪淋湿。
②机电设备必须加防雨罩,以免因潮湿而损坏设备,做好接地保护,安装漏电保护装置,以防漏电伤人。
雨后应对电气设施进行检查。
③雨季施工时施工人员要备齐各种防雨用具,使用电动工具的操作人员穿绝缘胶鞋、戴绝缘手套。
④各种通行的通道均设防滑条或有防滑措施。
⑤每日早晨及时掌握天气情况,对职工加强思想教育,保证雨季施工的顺利进行,防止各类事故在雨季施工中发生。
4)焊件温度低于-20℃。
2.焊前准备
1)焊前根据焊接工艺评定编制出焊接工艺指导书。
2)焊前按技术条件要求清理焊接坡口表面及两侧、表面的油、水、污物、熔渣和其他有害物质,并按技术标准施焊。
3)焊条、焊剂按规定烘干、保温;焊丝需去除油、锈,保护气体应当干燥。
4)焊前需要预热,预热温度用表面温度计来测量,应在加热面的背面测定温度。
如做不到,应先移开加热源,待母材厚度方向上温度均匀后测定温度。
温度均匀化的时间按每25mm母材厚度需2min的比例确定。
5)测温点的位置
焊件焊缝处母材厚度大于50mm时,测温点的位置距焊接接头要大于或等于75mm。
6)制造过程中如原有标志被裁掉或材料分成几块时,应及时完成标志的移植,不允许采用硬性标记。
3.组对定位
1)组对定位后,坡口间隙、错边量、棱角度等应符合图样规定或施工要求。
2)避免强力组装,定位焊缝长度及间距应符合焊接工艺文件的要求。
3)定位焊缝不得有裂纹,否则应清除重焊。
如存在气孔、夹渣时亦应去除。
4.焊接焊缝
1)焊工应当根据图样、工艺文件、技术标准施焊。
2)多层焊时将熔渣清理干净再焊下层,清渣应在完全凝固后进行。
3)按《焊接工艺规程》要求:
3定位焊,选用J507焊条,烘干温度为350℃/1h。
焊接过程中层间清理干净,检验员按层检查,记录焊接工艺参数,焊后焊工填写“施焊记录”,焊后清理。
4清理表面焊渣,自检合格后,做焊工代号标记。
5.焊接检查与检验
焊前:
1)母材、焊接材料:
选用焊接材料保证焊缝金属的力学性能高于或等于母材规定的限值,或符合设计文件规定的技术条件。
2)焊接设备、仪表、工艺装备
3)焊接坡口、接头装配及清理
4)焊工资质
5)焊接工艺文件
施焊过程中:
1)焊接规范参数
2)执行焊接工艺情况
3)执行技术标准情况
4)执行设计文件规定情况
焊后:
1)实际施焊记录
2)焊缝外观及尺寸
3)产品焊接试件
4)无损检测
A、B类焊接接头应进行20%射线检测,且不小于250mm。
按JB/T4730.2-2005的要求,技术等级不低于AB级,合格等级为III级。
C、D、E类焊接接头应进行100%渗透检测,符合JB/T4730.5-2005中的Ⅰ级为合格。
5.3真空粉末绝热的绝热层应符合下列要求:
a)粉末绝热材料装填前,应确认其含水率符合要求,必要时应进行干燥处理;
b)装填时,应控制粉末绝热材料的装填密度,且尽可能采取防沉降措施;
c)真空粉末绝热深冷容器,可添加适量阻光剂。
阻光剂应具有良好的化学稳定性,且应均匀分布在粉末绝热材料中。
储存液氧介质的深冷容器不应添加在富氧环境下会产生爆炸的阻光剂。
5.4容器抽空的具体操作为:
容器是通过抽气嘴与抽气管道和机械泵、扩散泵组成的高真空抽气机组连接后进行抽空。
(1)容器置于保温炉内,从抽空管路通人高纯氮气,然后加热至120~130度(这个温度的设定是根据绝热材料和支撑材料的最高承受温度而定),启动旋片泵和罗茨泵组合开始抽气,一般抽气3h,冲氮保温4h,反复进行气体热冲洗和预抽过程,且不少于6次。
这样可以将夹层空间内空气和材料表面及吸附剂表面吸附和解吸的部分水蒸气抽出,随着充气次数的增加,夹层空间内的空气组分发生变化,逐步变为充入的氮气,氮气在抽气很容易被抽出。
(2)当容器真空度抽至2Pa时。
对容器夹层重新充入氮气,并加热至120~130度后开始用扩散泵机组连续抽空,当容器在热状态下真空度达到8×10-2Pa并稳定时,容器离开保温炉持续抽空。
(3)容器室温抽空至真空度达到8~9x10-3pa时,停止抽空并关闭工装阀门,记录真空度数值。
(4)产品室温下静置2h,记录此时的夹层真空度数值,根据计算常温状态下的漏放气速率,如果计算的漏放气速率数量级已达到为10-7,即可判断夹层漏放气速率符合要求。
如果计算所得的漏放气速率数量级为10-6,延长产品静置时间,最长静置为72小时己录夹层真空度数值并计算漏放气速率。
漏放气速率符合要求后,封口真空度≤3pa,产品进行封结并将真空阀打上铅封,容器抽空结束。