皮革及毛皮加工工业污染防治可行技术指南.docx
《皮革及毛皮加工工业污染防治可行技术指南.docx》由会员分享,可在线阅读,更多相关《皮革及毛皮加工工业污染防治可行技术指南.docx(61页珍藏版)》请在冰豆网上搜索。
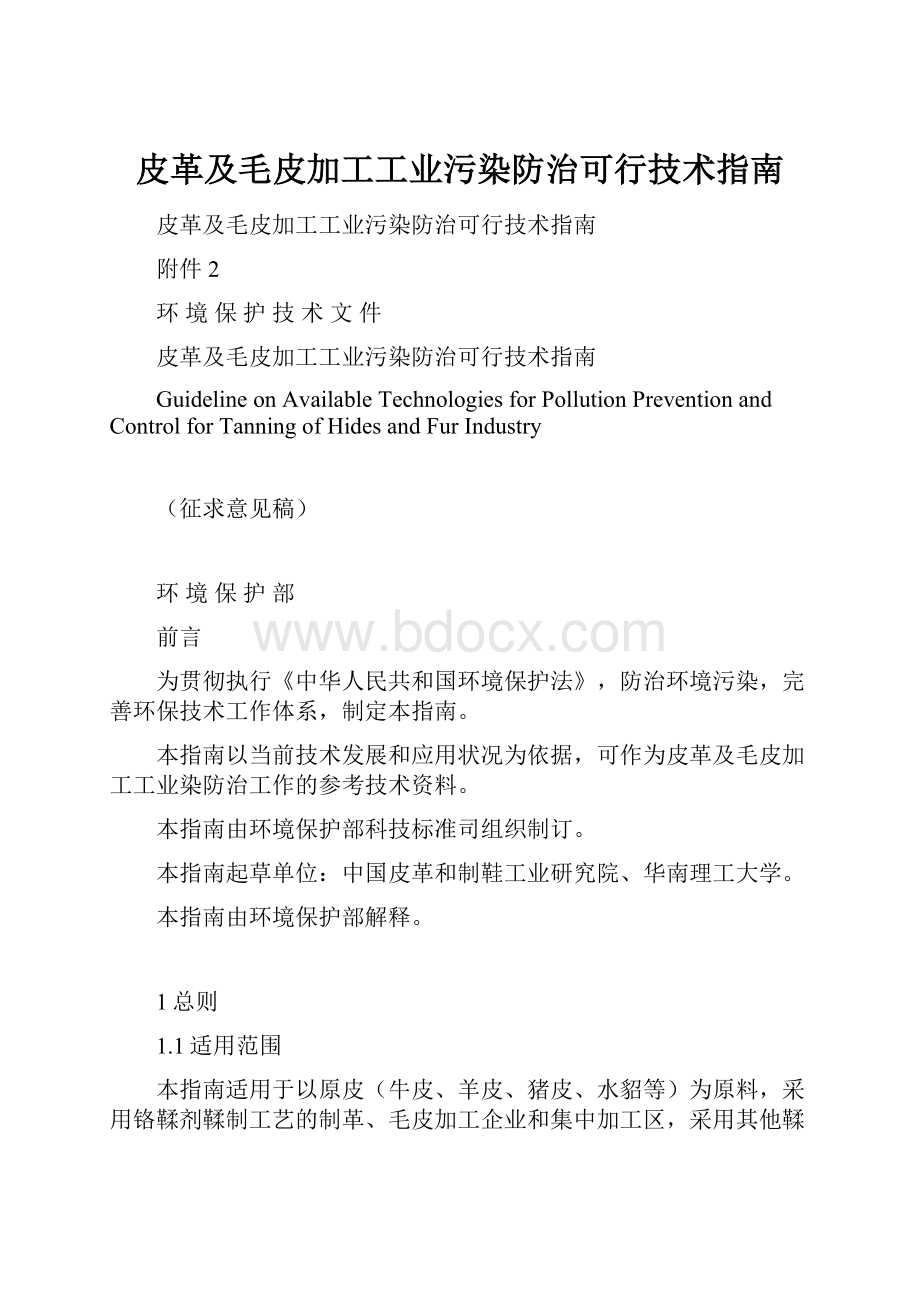
皮革及毛皮加工工业污染防治可行技术指南
皮革及毛皮加工工业污染防治可行技术指南
附件2
环境保护技术文件
皮革及毛皮加工工业污染防治可行技术指南
GuidelineonAvailableTechnologiesforPollutionPreventionandControlforTanningofHidesandFurIndustry
(征求意见稿)
环境保护部
前言
为贯彻执行《中华人民共和国环境保护法》,防治环境污染,完善环保技术工作体系,制定本指南。
本指南以当前技术发展和应用状况为依据,可作为皮革及毛皮加工工业染防治工作的参考技术资料。
本指南由环境保护部科技标准司组织制订。
本指南起草单位:
中国皮革和制鞋工业研究院、华南理工大学。
本指南由环境保护部解释。
1总则
1.1适用范围
本指南适用于以原皮(牛皮、羊皮、猪皮、水貂等)为原料,采用铬鞣剂鞣制工艺的制革、毛皮加工企业和集中加工区,采用其他鞣剂和鞣制工艺的制革及毛皮加工企业和集中加工区的污染防治技术可参照采用。
1.2术语和定义
1.2.1原皮
制革的基本原料取自各种动物(主要是家畜)的皮,包括制革加工前未经或已经防腐处理的皮。
1.2.2盐湿皮
用大量盐腌透的湿皮,保存期较长。
1.2.3鞣制
胶原蛋白与鞣质相结合,性质发生根本改变的过程,即由皮变成革。
1.2.4鞣剂
能进到皮组织中去,而且能改变皮的性质,使皮变成具有柔软性、弹性、强度好、耐水、耐热、耐腐蚀、有化学稳定性的革的物质。
2生产工艺和污染物排放
2.1生产工艺简介
2.1.1皮革加工工艺
牛皮、猪皮、羊皮革(以铬盐为鞣剂)加工生产工艺及产污节点见图1。
图1轻革加工工艺流程及主要产污节点图
2.1.2毛皮加工工艺
毛皮生产工艺及产污节点见图2。
图2毛皮加工工艺流程及主要产污节点图
2.2主要污染物的产生与排放
2.2.1水污染物
皮革的生产要经过浸水、浸灰脱毛、脱灰、浸酸、鞣制、中和、加脂、染色等多种复杂的物理化学过程,制革废水组分复杂,浓度高,色度大,有一定的毒性,属于污染较严重且较难处理的工业废水。
毛皮加工过程大体与制革相似,毛皮加工不涉及浸灰、脱毛、脱灰等工序。
毛皮各工序废水中主要污染源和制革废水相似。
废水中主要污染源见表1。
表1制革各工序的污水来源和污染物特性
工段
内容
准备工段
污水来源
水洗、浸水、脱脂、脱毛浸灰、脱灰、软化等工序(毛皮加工不涉及脱毛浸灰、脱灰)
主要污染物
废水:
包含污血、蛋白质、油脂、脱脂剂、助剂等有机物和
盐、硫化物、石灰、Na2CO3、硝酸盐等无机物;
固废:
大量的毛发、泥沙等固体悬浮物
污染物特征指标
CODCr、BOD5、SS、S2-、pH、油脂、总氮、氨氮
污染负荷比例
污水排放量约占制革总水量的60%~70%
污染负荷占总排放量的70%左右,是制革污水的主要来源
鞣制工段
污水来源
浸酸和鞣制工序
主要污染物
废水:
包含无机盐、三价铬、悬浮物等
固废:
包含含铬污泥
污染物特征指标
CODCr、BOD5、SS、Cr、pH、油脂、总氮、氨氮
污染负荷比例
污水排放量约占制革总水量的8%左右
复鞣、染色、加脂工段
污水来源
中和、复鞣、染色、加脂、喷涂、除尘等工序
主要污染物
废水:
包含色度、有机化合物(如表面活性剂、染料、各类复鞣剂、树脂)、悬浮物
污染物特征指标
CODCr、BOD5、SS、Cr、pH、油脂、氨氮
污染负荷比例
污水排放量约占制革总水量的20%~30%左右
2.2.2大气污染物
大气污染物主要产生于磨革、涂饰、干燥和脱毛工序。
制革行业的大气污染物主要可以分为涂饰有机废气(VOC)、磨革粉尘、总颗粒物、恶臭废气(H2S)等。
涂饰有机废气:
制革生产过程中在后整饰阶段产生的有机废气,主要是各类涂饰剂树脂内所含的挥发性有机物、有机稀释剂、有机清洗剂等。
磨革粉尘:
在皮革生产的打软、磨皮、摔软等工序产生粉尘等。
恶臭:
原皮在存放过程中,由于细菌的存在,造成蛋白质腐败,其中氨基酸被氧化成甲基吲哚,脱氨放出氨气,水解生成硫醇,散发出臭味。
另外,制革脱毛废水中硫化物含量较高,当pH值低于9.0时,硫化物以H2S气体形式散发在空气中,是强烈的神经性毒物,少量时刺激呼吸系统的粘膜,高浓度时会导致人畜死亡,H2S气体与空气混合还会产生爆炸。
其他一些恶臭废气主要来自皮革加工过程和污水处理设施运行过程产生的异味和恶臭。
2.2.3固体废物
固体废物主要产生于刮肉、片皮和削匀、铬沉淀及废水处理等过程。
制革、毛皮加工过程中产生的固体废物包括废毛、无铬皮固废、含铬皮固废、含铬污泥及综合污泥。
.
2.2.4噪声
制革、毛皮加工过程产生的噪声为机械的撞击、摩擦、转动等运动引起的机械噪声以及气流的起伏运动或气动力引起的空气动力性噪声,主要噪声源有:
转鼓、去肉机、磨革机、抛光机、污水系统中鼓风机、喷浆机、挤水机、剖层机、削均机、真空干燥机、挂晾干燥机、滚涂机、压花机、循环过滤器等。
一般情况下,在采取噪声控制措施前,各主要噪声源源强均大于80dB(A)。
3生产过程污染预防技术
3.1有害化学原料替代技术
皮革、毛皮加工过程中用到多种化学材料,使用更为清洁的化学原料替代有害原料,可减轻皮革、毛皮加工工业对人类健康和环境的不利影响。
有害化学原料替代技术见表2。
表2清洁化学原料替代技术
工序
有害化学原料
清洁技术
浸水、浸灰、脱脂、染色等
烷基酚聚氧乙烯醚(APEO)
以脂肪醇聚氧乙烯醚或支链脂肪醇聚氧乙烯醚替代APEO
脱脂
有机卤化物
使用非卤化溶剂,如线性烷基聚乙二醇醚、羧酸、烷基醚硫酸、烷基硫酸盐,采用水相脱脂系统;
对卤化溶剂采用封闭系统,溶剂回用,减排技术和土壤保护等措施
脱灰
铵盐
使用硼酸,乳酸镁,和有机酸如乳酸、甲酸、醋酸等,以及有机酯降低废水中铵盐的污染,但废液中CODCr和BOD5会增加
鞣制、铬复鞣
铬鞣剂
使用钛盐(仅用于预鞣以及复鞣)、铝盐、锆盐等非铬金属鞣剂替代或部分替代铬鞣剂;
植物单宁与非铬金属鞣剂/醛类化合物结合替代或部分替代铬鞣剂
鞣后各工序
有机卤化物
禁用染料
未吸收的油脂、染料
使用不含有机卤化物的加脂剂、染料、防水剂、阻燃剂等;
使用与铬具有高亲和及高吸收的复鞣剂以减少向污水的排放量;
使用氮含量及盐含量低的复鞣剂;
使用高吸收加脂材料(如乳液加脂剂);
采用低盐配方、易吸收、液态的染料,停止使用含致癌芳香胺基团的染料
涂饰
溶剂型涂饰材料
使用清洁的涂饰材料,如,高吸收染色材料和固色材料、水基涂饰材料、涂饰层高效交联材料、环保型胶黏剂和整饰剂等
各工序
杀菌剂、杀虫剂等
使用环境友好杀菌剂、杀虫剂代替
湿整饰工序
络合剂,如乙二胺四乙酸(EDTA)和次氮基三乙酸(NTA)
使用生物降解性好的络合剂
3.2原皮保藏和浸水清洁工艺
3.2.1少盐原皮保藏技术
少盐原皮保藏技术是采用食盐和脱水剂结合使用或采用食盐和杀菌剂、抑菌剂结合使用的保藏方法,达到中短期保藏的目的。
该技术可有效降低原皮保藏中食盐的使用量,适用于短期保存原料皮。
3.2.2干燥处理技术
干燥处理技术即直接晾晒原皮,或使用干燥器及其他机械方式。
此过程可以配合使用环境友好的杀菌剂。
该技术处理过程中不使用盐和其他化学品,无环境污染,成本较低。
但受气候条件限制,仅适于湿度较低而气候温暖地区的企业采用。
3.2.3低温处理技术
低温处理技术是使用低温冷藏,保藏温度为2℃左右,可以使原皮保存3周以上,也可以配合使用杀菌剂,并与常规盐腌工艺结合使用。
该技术可以基本消除浸水废液中盐的排放,但需设置冷藏库,能耗较大,且运输成本增大。
该技术适用于屠宰场与制革厂距离较近、原皮购销渠道固定、原皮能在短期内投入生产的生产企业。
3.2.4转笼除盐技术
转笼除盐技术是盐腌皮浸水前在转笼(用纱网做的转鼓)中转动,使皮张外的食盐脱落,回收的食盐可以重新使用。
该技术可以去除和回收盐腌皮上多余食盐,可节约盐的使用量,减少污水中盐的排放量。
回收盐再利用前需进行处理,且原皮的品质可能会受影响。
适合以腌制方法保存的皮革、毛皮。
3.3脱毛浸灰工序清洁技术
3.3.1保毛脱毛技术
保毛脱毛技术,也称“免疫”法脱毛技术,即首先对毛干进行护毛(也称“免疫”)处理,再通过控制碱和还原剂对毛的作用条件,使脱毛作用主要发生在毛根,毛较完整地从毛囊中脱除,再使用循环过滤系统将毛回收利用。
该技术能有效减少废水中CODCr、BOD5、悬浮物、有机物等的排放,降低后期污水处理成本,废毛可被加工为蛋白填充剂回用于制革。
该技术适用于安装有循环过滤设备的企业。
3.3.2低硫脱毛技术
低硫脱毛技术是指用含硫有机物,代替或部分替代无机硫化物进行脱毛。
该技术可减少硫化物用量及废水中污染物的排放量,适用于保毛脱毛工艺或毁毛脱毛工艺。
3.3.3脱毛浸灰液直接循环利用技术
脱毛浸灰液直接循环利用技术是收集含硫化物的保毛脱毛浸灰废液,过滤并调节浴液化学成分后,重新用于另一次脱毛浸灰作业。
该技术可减少50%~70%硫化物污染,废水中的BOD5、CODCr也大大降低,浸灰废液回收率50%~70%。
蛋白质、中性盐等会在循环液中累积,要求严格的过程控制。
该技术适用于处理制革生产中以硫化物为脱毛剂的脱毛浸灰废水。
3.3.4浸灰废液全循环利用技术
在密闭容器中,加入酸性材料使硫化物转化为硫化氢气体逸出,并用碱性材料吸收,重新用于保毛脱毛的浸灰阶段,同时回收废液中的蛋白质,将废液回用于预浸水工序,将回收的硫化钠回用于脱毛工序,回收的蛋白质制备成蛋白填料后回用于复鞣工序,使浸灰废液完全得到回收利用。
该技术省去了反应釜中的搅拌装置,提高了硫化氢气体的回收率及容器的密封性能。
硫化物回收利用率达到99%以上,节水30%以上。
该技术适用于处理制革生产中以硫化物为脱毛剂的脱毛浸灰废水。
3.4浸酸工艺
3.4.1浸酸废液循环利用
浸酸废液收集、过滤,并适当调整后,回用于下次浸酸过程。
该技术可大大节省食盐的用量,同时减小酸的消耗。
3.4.2无盐/少盐浸酸技术
采用非膨胀酸或酸性辅助性合成鞣剂替代或部分替代浸酸,不会引起裸皮的膨胀,不需加入食盐。
该技术可使浸酸后裸皮粒面平滑细致,有利于对酸皮进行削匀和剖层,铬鞣时有利于铬的渗透和吸收,有效减小盐对环境的影响。
3.5鞣制工艺
3.5.1高吸收铬鞣技术
通过优化工艺参数,采用小液比工艺,延长处理时间,添加助鞣剂等方法提高传统铬鞣工艺中铬的吸收率。
该技术不需引入新的工艺及设备,可将铬吸收率提高至90%左右。
结合助鞣剂,铬吸收率可达到95%以上。
采用该工艺可降低铬粉用量,减少含铬废水和污泥产生。
3.5.2铬鞣废液直接循环利用技术
鞣制、复鞣工序在鞣制结束后,将废铬液单独全部收集,过滤并调节组成后回用于浸酸工序或鞣制工序。
该技术可使杂质(蛋白、油脂)和化学品会在循环中累积,因此回用次数有限。
该工艺不能解决鞣制后清洗废水中铬的问题。
3.5.3铬鞣废液全循环利用技术
通过过滤、沉淀、水解、氧化和还原等技术措施,去除废液中的固形物杂质、水溶性杂质、以及与铬盐结合的杂质,重新恢复铬盐的鞣性。
该技术与未经再生处理直接回用铬鞣剂相比,鞣后皮革具有收缩温度高、蓝湿革外观浅淡等优点。
该技术铬的回用率达到99%以上,可以完全解决铬盐污染的问题。
3.5.4白湿皮技术
在铬鞣前先用铝、钛、硅、醛等非铬鞣剂进行预鞣,然后剖层削匀后再进行铬鞣,或者完全用非铬鞣剂代替铬鞣。
该技术可消除铬污染,剖层削匀精度较高,产生固体废物中不含铬。
白湿皮预鞣还可以提高后续铬鞣工序中铬的吸收率。
3.5.5植鞣技术
完全用植物鞣剂(栲胶)或与少量其他鞣剂结合鞣制。
该技术可消除铬污染,但完全的植鞣工艺在产品性能方面很难达到铬鞣皮革的品质。
3.5.6无铬鞣技术
该技术使用铝、锆、钛等矿物鞣剂或其他有机无铬鞣剂代替铬鞣。
该技术可完全消除铬污染。
目前用单独使用非铬矿物鞣剂无法获得铬鞣革的品质,需要配套助剂的开发及平衡鞣制前后工艺。
3.6涂饰工艺
该技术除了使用清洁的涂饰材料外,还可以采用高体积低压(HVLP)系统、泡沫喷涂系统、辊涂等清洁的涂饰方法。
3.7节水工艺技术
3.7.1闷水洗工艺
该技术将制革工序中流水洗改为闷水洗或闷水、流水交替进行。
该技术用水量可以减少25%~30%,而且对产品质量有益而无害。
该技术适用于新建及已有制革、毛皮加工企业。
3.7.2采用小液比工艺
该技术采用新型节水设备,如倾斜转鼓或星形分隔转鼓等。
该技术可有效降低液比,节水分别可达30%~40%以及40%~50%。
结合闷水洗,可节水70%以上。
3.7.3工序合并工艺
该技术将复鞣、中和、染色、加脂在同浴中一次完成。
该技术与传统工艺相比,此工序可减少废液排出量50%左右。
3.7.4过程废水回用技术
该技术将制革加工过程中湿整饰工序的废水过滤收集处理后回用到指定工序。
各工序产生的废水分开收集并分别处理。
包括:
(1)盐腌皮的浸水废水回用于浸酸;
(2)制革生产中保毛脱毛浸灰废液回用;(3)软化、浸酸废液工序内部循环使用;(4)铬鞣、复鞣废液处理后工序内部循环使用或回用于浸酸;(5)复鞣染色前脱脂工序的废水用于浸水和地面清洁;(6)浅色的染色废水循环用于深色染色;深色废水进行脱色后用于染色或铬复鞣;(7)对多组分加脂废液工序内部循环使用。
该技术可节水30%以上,循环使用的最后废水进行终水处理。
各工序可因需要废水收集、处理和调控设备,使用时需考虑额外的投资及运行费用。
3.8工艺过程污染预防新技术
3.8.1热处理盐回收技术
该技术将盐腌皮上的盐抖落下来,再次使用。
热处理法能有效杀灭回收盐中的细菌并分解有机污染物,从原皮上回收的盐经热处理杀菌及干燥后还能用于冬天路面防滑,减少精盐的使用量。
在不改变传统原料皮保藏方法的基础上,对盐进行再利用,可以大大减少废水中盐的排放量。
但同时也会增加能源消耗,且需要配备相关的操作设备,如储水池,给料箱、热处理系统(温度110℃到140℃)及干燥设备,而且将盐抖落的过程中可能引起皮的擦伤。
3.8.2超临界液体脱脂
当气体被压缩到具有液体密度的超临界状态时,开始表现出显著的萃取性,该类物质成为超临界液体。
初步研究表明:
脂肪和油脂可采用超临界液体从毛皮中提取出来,为皮革生产提供清洁高效的脱脂效果。
在CO2在超临界条件(31.1℃,73.8bar)下可以允许在皮革未被鞣制的状态下将油脂从中萃取出来,从而大大减少了有机溶剂和清洗剂的使用。
另外这个过程没有废水产生,并可在干净及不改变油脂化学性质的状态下,将其回收利用。
该技术所采用的超临界CO2液体既不产生废水、有毒废物又不会产生挥发性气体,被认为是具有前途的环境友好型技术。
此外,超临界液体也可以用于皮革染色,并具有较好的染色效果,降低制革染色废水的排放量。
3.8.3非铬鞣制技术
3.8.3.1铁鞣
该技术使用混合二价铁络合物作为鞣剂,将铁及其络合物鞣剂鞣制,再与铝鞣剂和植物鞣剂结合,所处理的皮革的收缩温度可达到89℃以上。
同时还有研究采用铁与其他金属(如铬、锌、铝)的多金属络合鞣剂混合后用于皮革鞣制工序,可大大提高铬吸收率,减少六价铬的排放。
3.8.3.2有机物鞣制
有机鞣剂中有机物易被分解及去除,其中新型两性有机复合物无铬鞣剂,可在鞣制过程中,既和胶原的氨基结合,也与羧基结合,释放出氢离子,而使浴液的pH值自动降低,简化了制革的生产工序:
裸皮软化后直接鞣制、前期不浸酸、后期不提碱,并在鞣制过程中不使用铬鞣剂,避免了浸酸、提碱过程中盐及铬鞣过程中铬的污染。
3.8.4连续复鞣及染色
在半连续式装置中实现复鞣、染色、填充等工序的连续运行,具有铬鞣效果好、耗水量低、排污量少的优点。
连续复鞣及染色装置由三个不同构件组成:
(1)用于复鞣/填充的滚轧机。
由于其独特设计,该设备有助于化学物质渗透进入皮革,还能将过量的化学物质挤压出来用于后续的复鞣。
另外由于存在两个浸渍水槽,皮革能在设备两边同时加工,提高了鞣制及染色效率;
(2)用于控制压力、湿度和温度的稳定室。
稳定室可调节控制最佳状态,有助于化学物质的分散;(3)能使皮革在短时间内(数秒)完成染色的浸染系统。
该技术的滚轧机和浸染系统均以短时间水洗模式运作,耗水量少,废水排放量低,而且挤出来的多余化学品可以循环利用,但废水中化学物质浓度较高。
此外,还需配备传感器用于监测主要运行参数(温度,pH值和电导率)以维持设备运行稳定。
3.8.5整饰
3.8.5.1粉末涂饰
粉末涂料是一种细粉状的固体,主要成分有树脂、粘结剂、色素、助流剂和其他添加剂。
粉末涂饰工艺是先将粉末涂料涂于皮革或镀膜皮革上,再进行烘烤,直到溶解并形成光滑的薄膜。
粉末涂料的主要应用技术包括静电喷涂、流化床预热沉积以及静电流化床沉积。
由于皮革不耐高温,导电导热性能均不好,粉末涂料暂不适用于皮革。
3.8.5.2非有机溶剂涂饰
4末端污染治理技术
4.1水污染治理技术
4.1.1废水分质预处理技术
4.1.1.1脱脂废水预处理技术
脱脂废水预处理包括酸提取和浮选法等工艺。
酸提取处理脱脂废水包括破乳、皂化、酸化和水洗工序,在酸性条件下破乳,使油水分离、分层,将分离后的油脂层回收,经加碱皂化后再经酸化水洗,最后回收得到混合脂肪酸。
浮选法是投加化学药剂将废水中部分乳化油破乳,通过微小气泡携油上浮出,并在水体表面形成含油泡沫层,然后通过撇油器将油去除。
4.1.1.2含硫废水预处理技术
含硫废水预处理包括催化氧化、化学絮凝和酸化法等工艺。
锰盐催化氧化法是通过空气中的氧,锰盐作为催化剂,在碱性条件下将S2-氧化成无毒的存在方式:
硫酸根、硫代硫酸根或单质硫。
常用催化剂有硫酸锰、氯化锰和高锰酸钾等。
化学絮凝法是向脱毛液中加入可溶性化学药剂,使其与废水中的S2-起化学反应,并形成难溶解的固体生成物,进行固液分离而除去废水中的S2-。
常用的沉淀剂有亚铁盐、铁盐等。
酸化吸收法是在酸性条件下产生极易挥发的H2S气体,再用碱液吸收硫化氧气体,生成硫化碱回用。
参见3.3.4。
4.1.1.3脱灰软化废液预处理技术
脱灰软化废液调节pH值10.0~11.0,采用空气吹脱法处理,氨氮去除率70%~80%。
采用上述预处理技术,可减轻后续生化处理的难度和负荷,处理后废水一般合并入综合废水进行后续处理。
4.1.1.4含铬废水预处理技术
参见3.5.2和3.5.3
4.1.2生化处理技术
4.1.2.1好氧生物处理技术
(1)氧化沟工艺
氧化沟工艺是活性污泥法的一种改型,其曝气池呈封闭的沟渠型,污水和活性污泥的混合液在其中进行不断的循环流动。
该技术构筑物简单,运行管理方便,处理效果稳定,出水水质好,并可实现脱氮。
(2)序批式活性污泥法(SBR工艺)
SBR法是序批式活性污泥法,属好氧活性污泥处理工艺。
废水分批进入池中,在活性污泥的作用下得到降解净化。
沉降后,净化水排出池外。
整个运行过程可分为进水期、反应期、沉降期、排水期和闲置期。
该工艺技术可有效降解有机物,具有良好的脱氮功能。
该技术适用于皮革及毛皮加工企业综合废水处理。
但处理周期较长,且在进水流量较大时,其投资会相应的增加。
(3)生物接触氧化
该技术利用池内好氧型的微生物,以污染物作为营养物质,在新陈代谢过程中,将污染物分解消化,使污水得到净化。
该技术占地面积小,不需要设污泥回流系统,但总体去除效果不理想,且耗电量较大,目前小水量制革废水的处理中应用较多。
4.1.2.2厌氧—好氧生物组合处理技术
“上流式厌氧污泥床(UASB)+好氧”处理工艺
UASB是上流式厌氧污泥床,属厌氧活性污泥处理工艺。
厌氧处理后的废水进入曝气池,将残余的还原性有机物生物氧化。
该技术可使用95%以上的硫化物得到回收,同时,CODCr去除率达到98%以上,采用UASB可以降低后续处理过程的污染负荷,减少运行成本和减少污泥的产生量。
由于废水中大量硫化物存在,设备投资成本较高。
4.1.2.3厌氧—好氧生物脱氮系统(A/O工艺)
(1)A/O工艺
A/O工艺法称为缺氧-好氧生物法,A段为厌氧/兼氧行处理,O段则相当于传统活性污泥法。
该工艺流程简单,装置少,建设费用低。
除了可去除废水中的有机污染物外,还可同时去除氨、氮和磷。
但缺氧池抗冲击负荷能力差,出水COD浓度偏高。
(2)二级A/O工艺
第一级的功能以去除有机物为主要功能,第二级采用生物膜法以去除氨氮为主要功能。
该技术针对氨氮浓度高的制革废水,处理效果稳定,氮去除效率高,能承受水量水质冲击负荷,可操作性强。
(3)A2/O工艺
在A/O工艺中缺氧池前增加一个厌氧池,利用厌氧微生物先将复杂的复杂有机物降解为小分子,使废水的可生化性显著提高,从而大幅度降低进入后续A/O系统的有机物浓度,第二段A2/O采用活性污泥工艺。
该工艺可同时实现有机物降解和氨氮硝化反硝化过程;但占地面积大,工艺流程长,运行费用较高。
(4)A/O2(厌氧/好氧-好氧)工艺
A/O2又称为短流程硝化-反硝化工艺,其中A段为缺氧反硝化段,第一个O段为亚硝化段,第二个O段为硝化段。
该工艺能有效去除酚、氰及有机污染物,但占地面积大,工艺流程长,运行费用较高。
(5)O-A/O(初曝-厌氧/好氧)
由两个独立的生化处理系统组成,第一个生化系统由初曝池(O)+初沉池构成,第二个生化系统由缺氧池(A)+好氧池(O)+二沉池构成。
该工艺降解有机污染物能力强,抗毒害物质和系统抗冲击负荷能力强,产泥量少。
4.1.3深度处理技术
4.1.3.1膜处理技术
(1)膜生物反应器(MBR)强化废水生化处理技术
MBR是高效膜分离技术与活性污泥法相结合的新型污水处理技术。
内置中空纤维膜,利用固液分离原理,取代常规的沉淀,过滤技术,有效去除固体悬浮颗粒和有机颗粒以及难降解物质。
该技术用于皮革及毛皮加工企业综合废水处理,进水使用范围大,产泥量小,有机物及氨氮去除率高,成本相对较低。
(2)膜处理技术
①微滤技术
该技术是在静压差作用下,小于微滤膜孔径的物质通过微滤膜,而大于微滤膜孔径的物质则被截留到微滤膜上,使大小不同的组分得以分离。
微滤膜孔径为0.2μm或0.2μm以下。
该技术能耗低、效率高、工艺简单、操作方便、投资小。
该技术适用于皮革及毛皮加工企业二级处理后废水的深度处理。
②超滤技术
该技术以超滤膜为过滤介质,只允许水、无机盐及小分子物质透过膜,而阻止水中的悬浮物、胶体、蛋白质和微生物等大分子物质通过。
截流相对分子质量500~500,000左右,相应孔径大小的近似值约为0.002~0.1μm。
该技术设备体积小,结构简单,易于操作管理,投资费用低。
适用于皮革及毛皮加工企业各工序废水以及综合废水回用或排放前的深度处理。
③反渗透技术
该技术是在高压下,借助反渗透膜的选择截留作用来除去水中的无机离子,由于反渗透,只允许水分子通过,而不允许钾、钠、钙、锌、病毒、细菌通过。
该技术能耗少,设备紧凑,占地少,操作简单,适用性强,易于实现自动化,除盐率可达98%以上。
该技术适用于皮革及毛皮加工企业处理后废水排放或回用前的除盐处理。
4.1.3.2深度脱氮技术
(1)曝气生物滤池
该技术是生物反应器内装填高比表面积的颗粒填料,提供微生物膜生长的载体,废水由下向上或由上