摩擦.docx
《摩擦.docx》由会员分享,可在线阅读,更多相关《摩擦.docx(20页珍藏版)》请在冰豆网上搜索。
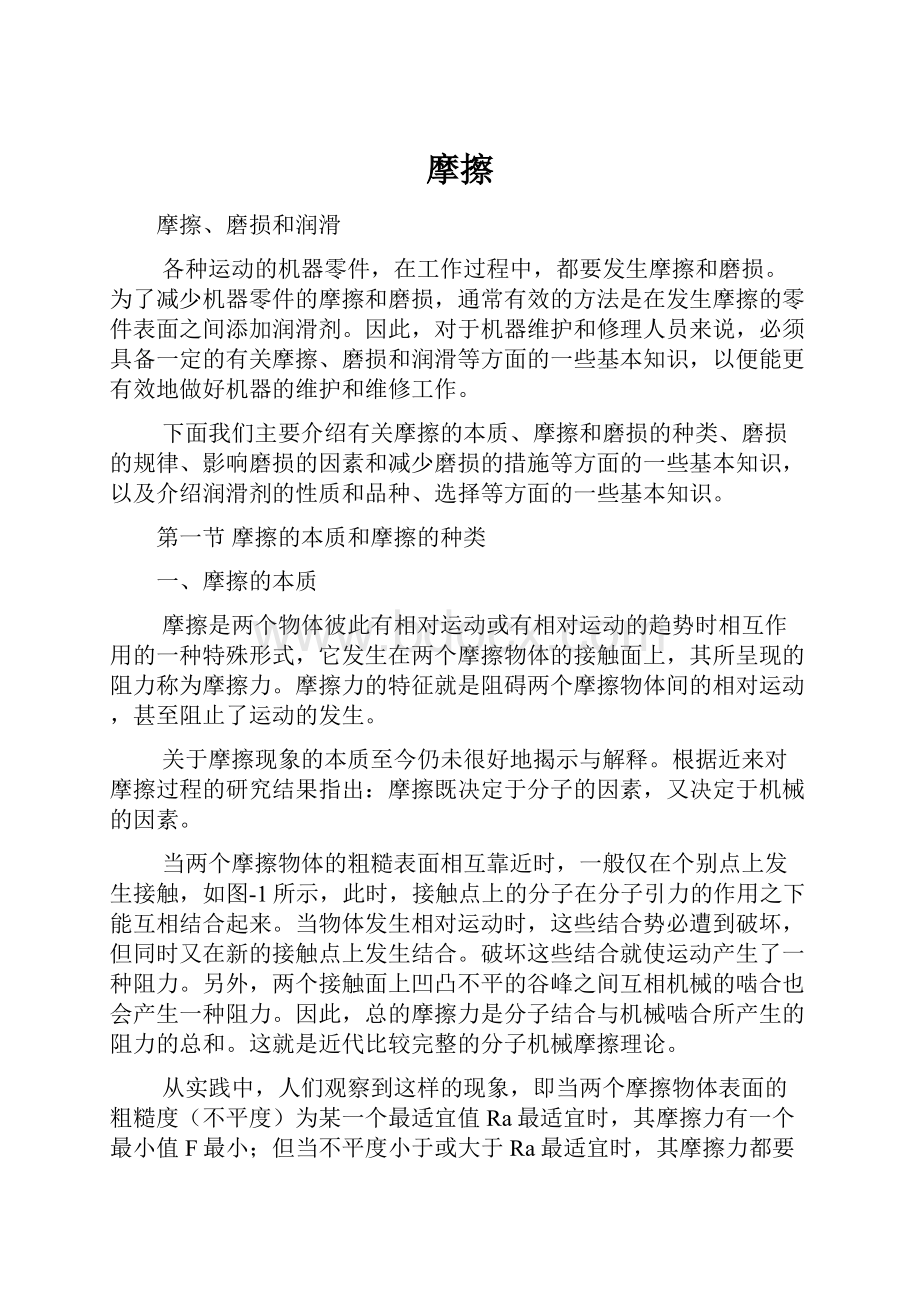
摩擦
摩擦、磨损和润滑
各种运动的机器零件,在工作过程中,都要发生摩擦和磨损。
为了减少机器零件的摩擦和磨损,通常有效的方法是在发生摩擦的零件表面之间添加润滑剂。
因此,对于机器维护和修理人员来说,必须具备一定的有关摩擦、磨损和润滑等方面的一些基本知识,以便能更有效地做好机器的维护和维修工作。
下面我们主要介绍有关摩擦的本质、摩擦和磨损的种类、磨损的规律、影响磨损的因素和减少磨损的措施等方面的一些基本知识,以及介绍润滑剂的性质和品种、选择等方面的一些基本知识。
第一节摩擦的本质和摩擦的种类
一、摩擦的本质
摩擦是两个物体彼此有相对运动或有相对运动的趋势时相互作用的一种特殊形式,它发生在两个摩擦物体的接触面上,其所呈现的阻力称为摩擦力。
摩擦力的特征就是阻碍两个摩擦物体间的相对运动,甚至阻止了运动的发生。
关于摩擦现象的本质至今仍未很好地揭示与解释。
根据近来对摩擦过程的研究结果指出:
摩擦既决定于分子的因素,又决定于机械的因素。
当两个摩擦物体的粗糙表面相互靠近时,一般仅在个别点上发生接触,如图-1所示,此时,接触点上的分子在分子引力的作用之下能互相结合起来。
当物体发生相对运动时,这些结合势必遭到破坏,但同时又在新的接触点上发生结合。
破坏这些结合就使运动产生了一种阻力。
另外,两个接触面上凹凸不平的谷峰之间互相机械的啮合也会产生一种阻力。
因此,总的摩擦力是分子结合与机械啮合所产生的阻力的总和。
这就是近代比较完整的分子机械摩擦理论。
从实践中,人们观察到这样的现象,即当两个摩擦物体表面的粗糙度(不平度)为某一个最适宜值Ra最适宜时,其摩擦力有一个最小值F最小;但当不平度小于或大于Ra最适宜时,其摩擦力都要增大,如图-2所示。
这种现象可以用分子机械摩擦理论来合理地加以解释:
这是因为提高表面的加工光洁度,就会增加接触点(结合点)的数目,所以摩擦表面之间的分子引力和摩擦力也就相应地增大,这时,影响摩擦力大小的主要因素是分子的结合而不是机械的啮合,但当摩擦表面的粗糙度(不平度)大于最适宜的粗糙度(不平度)时,摩擦力将随着不平度的增加而迅速增大,这时,影响摩擦力大小的主要因素是机械的啮合而不是分子的结合。
二、摩擦的种类
根据摩擦物体的运动状态,摩擦分为静摩擦和动摩擦两大类。
静摩擦的摩擦系数总是要比动摩擦的摩擦系数大一些。
根据摩擦物体的运动方式,摩擦分为滑动摩擦和滚动摩擦两大类。
在干燥状态下,滑动摩擦的摩擦系数要比滚动摩擦的摩擦系数大10~100倍。
根据摩擦物体的表面润滑程度,摩擦可分为干摩擦、液体摩擦、界限摩擦、半干摩擦和半液体摩擦等五种。
1、干摩擦
在两个滑动摩擦的表面之间,由于不加润滑剂,因而使两表面直接接触,这时的摩擦称为干摩擦,干摩擦的摩擦系数很大,大约0.1~0.5,有时也会超过1.0,干摩擦时摩擦表面上的磨损是很厉害的。
但是,随着使用条件的不同,干摩擦的作用也可以成为有益的,也可以成为有害的。
如在各种摩擦传动装置和制动中干摩擦是有益的,所以我们利用它;而在各种滑动轴承中的干摩擦是有害的,因此我们要防止它。
2、界限摩擦
在两个滑动摩擦表面之间,由于润滑剂供应非常不足,根本无法建立液体摩擦,而只能依靠润滑剂中的极性油分子在摩擦表面形成一层极薄(厚度0.1~0.2um)的“绒毛”状油膜,这层油膜能牢固地吸附在金属的摩擦表面上,这时,相互接触的不是摩擦表面本身(或有个别点直接接触)而是表面的油膜。
这种油膜润滑状态下的摩擦是液体摩擦过渡到干摩擦的最后界限,所以称为界限(临界或边界)摩擦。
界限摩擦的摩擦系数0.01~0.1,其磨损还是相当大的。
在实际使用中,当机器在启动和制动时,各对摩擦表面间都可能发生界限摩擦。
3、液体摩擦
在两个滑动摩擦表面之间,由于充满润滑剂,因而表面不发生直接接触,这时的摩擦不是发生在两摩擦表面上,而是发生在润滑剂的内部,所以称为液体摩擦。
液体摩擦的摩擦系数很小,大约0.003~0.01,液体摩擦时摩擦表面不发生磨损。
在一切机器零件的摩擦表面上,必须尽力建立液体摩擦,只有这样才能延长零件的使用寿命。
一般滑动轴承在正常工作和润滑条件下能获得液体摩擦。
4、半干摩擦和半液体摩擦
半干摩擦是指摩擦表面上同时存在着干摩擦和界限摩擦的情况,半液体摩擦是指在摩擦表面上同时存在着液体摩擦和界限摩擦的情况。
半干摩擦和半液体摩擦都叫混合摩擦。
半干摩擦较接近干摩擦,半液体摩擦较接近液体摩擦。
半干和半液体摩擦的摩擦系数在很大的范围内(从干摩擦到液体摩擦之间)变动。
半干和半液体摩擦常在以下几种情况下发生:
机器启动和制动时;机器在作往复运动和摆动时;机器的速度和负荷剧烈变化时;机器在高温和高压下工作时;及其所用的润滑剂粘度过小和供应不足时。
磨损的种类和磨损的规律
机器零件在工作过程中,由于摩擦而引起零件表面层材料的破坏,这种现象就称为磨损。
根据磨损延续时间的长短,它可分为自然磨损和事故磨损两类。
1、自然磨损
自然磨损是指机器零件在正常工作条件下,在相当长的时间内逐渐产生的磨损。
这种磨损的特点是,其磨损量是均匀地、逐渐地增加的,它并不引起机器工作能力过早地或迅速地降低。
由于这种磨损是一种不可避免的自然现象或正常现象,所以称它为自然磨损或正常磨损。
自然磨损是由于下列因素造成的:
①零件配合表面摩擦力的作用②冲击负荷的作用③高温氧化的作用④介质的化学和电化学腐蚀的作用等。
自然磨损可分为机械磨损、氧化磨损和腐蚀磨损等三种,其中以机械磨损为最主要。
因此,润滑工作的目的就是为了减少机器零件在工作过程中的机械磨损。
2、事故磨损
事故磨损是指机器零件在不正常的工作条件下,在很短的时间内产生的磨损。
这种磨损的特点是,其磨损是不均匀地、迅速地增加的,它会引起机器工作能力过早地或迅速地降低,甚至会突然发生机器或零件的损坏事故,所以称它为事故磨损或不正常磨损。
事故磨损是由于下列因素造成的:
机器构造有缺陷,零件材料的质量低劣,零件的制造和加工不良,部件或机器的装配或安装不正确,违反机器的安全技术操作规程和润滑规程,修理不及时或修理质量不高,以及其他意外的原因等。
在一般的情况下,当自然磨损达到一定的极限之后,而没有及时地进行修理,这是发生事故磨损的主要原因。
因此,为了防止事故磨损的发生,就必须首先了解和掌握磨损的变化规律。
磨损的规律
机器在工作过程中,其中各个零件的磨损速度是不同的,但是他们之间仍然有着共同的变化规律。
图3中所示为机器中常见的轴颈和轴承组合件的磨损前后配合间隙的变化情况,这种组合件的磨损变化规律可用图4所示的磨损曲线来表示。
图中曲线段I表示组合件在新装配或修理好后的试车初磨(跑合)期,在这段时期内曲线急剧上升,表示组合件在试车的初期内的磨损速度较大,这是由于零件在加工时所得到的最初不平度最容易被破坏、擦伤或磨平而形成新的不平度的结果,这时的间隙由刚装配好的初始间隙(或公称间隙)Δ初始增大到Δ初磨,当曲线趋近A点时磨损速度将逐渐降低。
初磨结束,应重新换新油再投入正常运转。
直线段Ⅱ表示组合件在正常运转时的自然磨损期(或正常磨损期),组合件的磨损成直线均匀地上升,与直线成α角,这时的间隙由Δ初磨逐渐增大到最大的允许间隙Δ最大。
曲线段Ⅲ表示组合件的事故磨损期,间隙超过Δ最大后,过大的间隙将会增加冲击的作用,破坏润滑油膜,加快磨损速度,使组合件处于危险的状态中,这时机器若继续工作,就可能立即发生以外的损坏事故。
由此可见,当组合件的配合间隙达到或将要达到Δ最大时,就应及时地停车进行修理,以免事故磨损的发生。
组合件从正常运转开始到事故磨损以前为止的这一段时间称为组合件的正常工作时间或修理间隔期,它可以由下列公式计算:
T=(Δ最大-Δ初始)/tgα
T——组合件的正常工作时间或修理间隔期,小时;
Tgα——组合件的正常磨损速度(即单位时间内配合间隙的增加量),毫米/小时。
正常磨损的速度决定于下列因素:
机器构造的特点,机器工作时的工艺条件,制造零件所选用的材料质量,零件的加工精度和光洁度,摩擦表面的润滑情况,润滑剂的性质和品种,轴承压强的大小,机器的修理和装配质量,机器的操作和维护保养质量等。
各种组合件的磨损速度是不同的,它们的数值可以通过试验或以现场经验来确定。
影响磨损的因素和减少磨损的措施
一、润滑对磨损的影响
润滑对减少机器零件的磨损具有特别重大的意义。
因为在摩擦表面之间建立液体摩擦以后,摩擦系数可以降低到原来的几十分之一至几百分之一。
由此可见,在摩擦表面之间建立液体摩擦是减少磨损的主要措施。
那么,如何才能在摩擦表面之间建立液体摩擦呢?
现以轴颈和轴承组合件为例说明。
轴颈和轴承之间建立完全液体摩擦的过程可分为三个阶段:
1、静止阶段
如图a所示,这时,轴颈和轴承在母线A处接触,但是,因为轴颈尚未旋转,所以不发生摩擦。
2、起动阶段
如图b所示,这时,轴颈开始旋转并沿轴承的内壁上爬,在B处不断地发生界限摩擦、半干摩擦和半液体摩擦,所以起动阶段也可称为润滑不稳定阶段。
3、稳定阶段
如图c所示,这时,由于润滑油供应充足,轴的转速又足够高,所以,粘附在轴颈表面上的润滑油被旋转的轴颈不断地带入楔形间隙中去,润滑油从间隙大处进入,而从间隙小处排出。
因为润滑油在楔形间隙中的流动阻力是随着间隙的减少而不断增大的,所以它能产生一定的压力,将轴颈向旋转方向推移,以便形成能承受压力的油楔,当油楔中总的压力大于负荷R时,就能将轴颈抬起来,所以这里的摩擦变成了完全的液体摩擦,此时间隙最小处的油膜厚度为h。
当轴颈的转速趋近于无穷大而负荷又不大时,在理论上来说,轴颈的旋转中心就会与轴承的中心完全重合,但是,这是一个不稳定的位置,因为,此时油楔消失,油膜没有承载能力,故轴颈不可能永远处在轴承的中心位置上,而会自动地下落。
在稳定阶段时,润滑油膜在油楔最狭窄处的厚度与配合间隙的大小、油的粘度、轴承的压强和轴颈的尺寸之间的关系可根据流体力学理论得出下面公式:
h=(υnd2)/(18.36pΔC)
h—楔形间隙最狭窄处的油膜厚度,毫米;
υ—润滑油的绝对粘度,公斤.秒/米2
n—轴颈的转速,转/分
d—轴颈的直径,毫米
p—轴承摩擦表面上的压强,公斤/米2
Δ—轴颈与轴承的配合间隙,毫米
C—考虑轴承长度影响的修正系数,C=(d+l)/l
l—轴承的长度,毫米
从公式中可以看出:
当润滑油的粘度、轴颈的转速和直径增加时,油膜的厚度也将随之增加;而当轴承上的压强、配合间隙和修正系数增加时,油膜的厚度将减小。
但是,这许多因素中以配合间隙对油膜厚度的影响为最主要,其次为润滑油的粘度。
根据实验结果,在轴颈和轴承的组合件中,当配合间隙与油楔最狭窄处油膜厚度之间能满足:
h=Δ/4,其摩擦和磨损为最小。
这个配合间隙称为最适宜的间隙Δ最适宜,而相应的油膜厚度也称为最适宜的厚度h最适宜。
因此,可将上面的式子写成h最适宜=Δ最适宜/4
因此
Δ最适宜=0.467d*[(υn)/(pC)]^(1/2)(5)
当其他条件不变时,上面的公式(5)确定了最适宜的间隙和润滑油粘度之间的相互关系(在液体摩擦条件下),即最适宜的间隙是随着粘度的增加而增大的。
在实际中,对于一般的滑动轴承取Δ最适宜=(0.001~0.002)d,而对于重要的滑动轴承取Δ最适宜=0.0005d,d为轴颈的公称直径(100~500毫米范围内)。
因此,根据润滑油的粘度、轴承的压强、轴颈的直径和转速以及修正系数,就可以算出最适宜的间隙。
轴承在工作过程中不断地受到磨损,结果使间隙逐渐增大,这样就引起油膜厚度h值的逐渐减小,最终会使轴颈和轴承的表面直接发生接触,即液体摩擦条件开始被破坏。
由此可见,间隙Δ的增大而使油膜厚度h减小,将受到轴颈和轴承表面不平度的限制,即
h最小=δ轴颈+δ轴承=δ
h最小—油楔最狭窄处油膜的最小的允许厚度,毫米
δ轴颈—轴颈表面的不平度,毫米
δ轴承—轴承表面的不平度,毫米
δ—δ轴颈和δ轴承的总和,一般δ=0.005~0.01毫米
当轴承间隙增大到最大的允许间隙时,轴承的正常工作条件被破坏,此时油楔最狭窄处油膜的最小允许厚度等于轴颈和轴承表面不平度的总和,即
δ=(υnd2)/(18.36pΔC)
(4δ/Δ最适宜)=(Δ最适宜/Δ最大)
Δ最大=(Δ2最适宜/4δ)
因此,当δ值确定后,就可算出Δ最大,但其值应在下式所规定的范围内
Δ最大=(2~5)Δ最适宜
对于低速重载机器的轴承取较大值,而对高速轻载机器的轴承取较小值。
综上所述,在轴颈和轴承的滑动摩擦表面之间建立液体摩擦的必要条件如下:
(1)润滑油的供应要充分,漏损要最少。
(2)注油孔和油槽应开设在轴承的承载区以外。
(3)润滑油的粘度和润滑性能要符合工作要求。
(4)轴颈的转速要足够高。
(5)轴颈和轴承表面应有最适宜的加工粗糙度(不平度)。
(6)轴颈和轴承之间应有最适宜的配合间隙。
二、零件表面层材料的性质对磨损的影响
零件表面层材料的硬度、韧性、化学稳定性和孔隙度是影响磨损的主要因素。
因为增加硬度就可提高材料表面层的耐磨性;增加韧性就可防止或减少磨粒的产生;增加化学稳定性就可减少腐蚀磨损;增加孔隙度就可蓄集润滑剂,从而减少机械磨损,提高零件的耐磨性。
在制造和修理工作中,减少磨损和提高耐磨性的方法如下:
1、增加零件表面层材料的硬度
(1)在零件材料中增加含碳量或加入合金元素,如铬、锰、钼、钒、磷等。
但这方法不是最经济的,因仅仅为了增加表面的硬度,却在全部材料中加入稀有的较贵的合金元素。
(2)用电镀、喷镀和堆焊的方法在零件表面上覆盖一层抗摩材料。
(3)利用表面淬火和化学热处理的方法来增加表面层的硬度。
如:
火焰表面淬火、高频表面淬火、铁的氧化处理、氮化处理、渗氮处理、氰化处理、硫化处理和磷酸盐处理等。
(4)利用机械强化法来增加表面层的硬度。
如:
滚压法、喷砂法、和喷丸法等,他们不但能使表面硬化,而且还可以提高内疲劳的能力。
在提高硬度时,还应注意,过高的硬度往往会造成脆性,使材料颗粒易于剥落,所以,还必须使材料保持足够的韧性。
在抗拉强度极限相同而延伸率不同的材料,延伸率较大者多半是比较耐磨的。
2、应用减磨合金(如巴氏合金、青铜和耐磨铸铁等)可以减少磨损。
3、应用非金属抗摩材料(如层压酚醛塑料、尼龙、聚酰亚胺、填充四氟乙烯等)制造轴承零件,在具有强力散热装置的条件下,它的耐磨性很高。
4、增加轴承材料的孔隙度,以保证润滑油的蓄集,这是提高耐磨性的另一途径。
如用细碎的金属屑和金属粉末压制成的所谓金属陶制轴套(孔隙度10~50%),是最好的轴承材料。
三、零件表面加工质量对磨损的影响
零件表面的加工质量越高,即不平度越小,一般来说对提高耐磨性是有利的。
但是,实验指出,过于光滑的表面不一定具有最好的耐磨性能。
因为表面过于光滑,使润滑油不能形成均匀的油膜(形成球状油滴),所以,反而使耐磨性变坏。
如图所示的曲线,它表示零件的最小磨损量并不是在表面最光滑的时候得到的,而是在不同的负荷条件下,当表面不平度为最适宜的值R1和R2时,才能得到最小的磨损量Q1和Q2。
四、零件的工作条件对磨损的影响
零件的工作条件是指单位面积的负荷(压强)、相对运动的速度和摩擦面运动的性质等。
通常单位面积的负荷增大会使零件的磨损速度增加。
零件相对运动的速度对磨损的影响比较复杂。
一般在干摩擦和界限摩擦中,当速度增大时,磨损速度在开始时是增加的,但达到最大后又开始减小,这种情况在由淬火钢、铸铁和硬的青铜制造的零件中存在。
当摩擦表面为液体摩擦时,则相对运动速度的增大反使磨损减小。
但是零件运动的速度对磨损的影响最大是发生在机器起动和制动的时候,因在这时零件的运动速度突然改变,往往会发生界限摩擦、半干和半液体摩擦,甚至有可能发生干摩擦,所以,机器起动和制动的次数愈多,零件的磨损也愈大。
零件摩擦表面间各种不同相对运动的性质,使表面的磨损分布也不同。
(1)负荷的方向固定不变并作用在旋转的零件上,此时,旋转的零件受到均匀磨损,固定的零件受到局部磨损,
(2)负荷作用在旋转的零件上,并一同以角速度随旋转零件一起旋转,此时,旋转零件受到局部磨损,固定零件受到均匀磨损;(3)负荷的方向固定不变,两个零件各以不同的角速度作同方向的旋转,此时,两个零件都受到均匀磨损,(4)负荷作用在旋转零件上,并以不同的角速度随旋转零件作同方向的旋转,此时,两个零件也都受到均匀磨损。
局部磨损的发展速度比均匀磨损要快,因此,受局部磨损的零件其使用寿命也较短。
除此之外,环境的清洁和温度等,对磨损也有很大的影响。
五、安装、修理质量对磨损的影响
机器安装修理的质量对其使用寿命有很大的影响。
如不正确地拧紧轴承盖与轴承座的连接螺栓;齿轮和轴等相互配合的零件不同轴或装配的不好;轴颈和轴承等相互配合的表面不平整等;都能引起单位面积的负荷分布不均匀或者增加了附加负荷;因而使其磨损加速。
摩擦组合件修理和调整后,若其配合间隙过大或过小,也会使磨损迅速增加,最后必然会引起事故磨损和损坏。
因此,为了延长组合件的寿命,必须保证安装和修理的质量。
第四节润滑剂
一、润滑油
液体状态的润滑剂称为润滑油或稀油。
动物油和植物油的润滑性好,容易获得液体摩擦,但容易腐臭(氧化),价格又高,所以在工业上多应用廉价的矿物油作为润滑油。
为了改善矿物油的性能,以适应不同的要求,常在矿物润滑油中掺入植物油或动物油而制成混合油。
此外,合成润滑油也获得广泛的应用。
润滑油的主要功用是减磨、冷却和防腐。
润滑油的主要物理化学性能包括:
粘度、闪点、燃点、凝固点、水分、机械杂质、水溶性酸和水溶性碱、油性等。
1)粘度:
它是指液体内部分子与分子之间发生相对运动时所产生的摩擦阻力。
粘度是润滑油最重要的质量指标,润滑油常以它来划分牌号。
粘度可分为绝对粘度(动力粘度)、运动粘度、相对粘度(条件粘度)三种。
a)绝对粘度:
相距单位长度(米或厘米)的两个单位面积(米2或厘米2)的油层,以单位速度(米/秒或厘米/秒)作相对移动时,克服摩擦阻力所需的力(公斤或达因)称为绝对粘度(动力粘度)。
工程单位为公斤*秒/米2;物理单位为达因*秒/厘米2或称为“泊”。
b)运动粘度;它是绝对粘度与同温度的润滑油密度的比值。
工程单位为米2/秒;物理单位为厘米2/秒或称为沲。
c)相对粘度:
润滑油的粘度通常都应用相对粘度(条件粘度)。
相对粘度是以恩格列尔粘度计测出的恩氏粘度来表示的,即在某温度t0C下200毫升的润滑油式样在恩氏粘度计中流出所需的时间与200C时同体积蒸馏水流出所需的时间的比值。
在压力变化不大的情况下,润滑油的粘度不会改变,但是压力在50公斤/厘米2以上,粘度就会随压力的升高而增加。
压力愈大,粘度增加得愈快。
若果没有适当粘度的润滑油,则可以用两种粘度不同的润滑油(粘度略大和略小的油)混合起来使用。
各种机器是用什么样的粘度的润滑油,应根据该机器工作条件来决定。
比如高速机器要使用粘度较小的润滑油,而在较高温度条件下工作的机器,宜选择粘度较大的润滑油。
同一机器,在冬季和夏季应分别选用粘度较小和较大的润滑油。
2)闪点和燃点:
将润滑油在一定的条件下加热到一定的温度,其蒸气与空气混合,用火焰点燃,发生闪光的温度叫闪点。
如果闪光时间长达5秒钟,则此温度称为燃点。
燃点一般比闪点高22~280C。
根据闪点的高低可以知道润滑油中低沸点蒸馏物含量的多少,因此就可以判断该润滑油着火危险性的大小。
润滑油的闪点对于在高温条件下工作的机器来说具有特别重要的意义。
在高温条件下工作的机器应选择闪点较高的润滑油,这样可以保证润滑油不会自行燃烧而失去润滑作用。
3)凝固点:
当润滑油冷却到完全失去流动性而具有塑性体的性能时的最高温度称为凝固点。
润滑油的凝固点对于在低温条件下工作的机器来说具有特别重要的意义。
在低温条件下工作的机器应选择凝固点较低的润滑油,这样可以保证润滑油有足够的流动性和较小的起动阻力。
4)水分:
润滑油中的水分能降低润滑油的润滑性能,能使与其接触的金属表面氧化(生锈),同时还能促使油中形成沉渣凝结物而堵塞油路。
因此,润滑油中不应该含有水分。
5)机械杂质:
润滑油中的悬浮物或沉淀物总称为机械杂质,如金属屑末、尘埃和砂土等等。
机械杂质能使摩擦表面过早的磨损、发热和管路堵塞。
因此,润滑油中不应该有机械杂质。
6)水溶性酸和水溶性碱:
润滑油中的无机酸和碱称为水溶性酸和碱。
他们能引起金属的强烈腐蚀,所以不应该让它们存在。
7)油性:
它是说明润滑油吸附于金属表面上形成强固油膜的性质。
这种强固油膜的形成主要是由于润滑油中具有少量极性物质所致,润滑油的油性除了与极性物质的存在有关以外,还与润滑油的表面张力以及摩擦表面的物理化学性质等有关,但与粘度无关。
在同样负荷的工作条件下,在摩擦表面上保持油膜完整的时间较长者,就认为是具有较高的润滑性。
吸附性的油膜能够承受很大的压力(几千公斤/厘米2)而不破裂,同时它的剪切阻力非常小,所以它对于界限摩擦润滑具有很重要的意义。
2、常用润滑油的品种
3、润滑油的选择原则
润滑油的品种应根据机器的工作条件(负荷、温度和转速等)来选择。
润滑油的一般选择原则如下:
1)在充分保证机器摩擦零件安全运转的条件下,为了减少能量的消耗,应优先选用粘度最小的润滑油。
2)在高速轻负荷条件下工作的摩擦零件应选用粘度小的润滑油;而在低速重负荷条件下工作的应选用粘度大的润滑油。
3)在冬季工作的摩擦零件应选用粘度小和凝固点低的润滑油;而在夏季工作的应选用粘度大的润滑油。
4)受冲击负荷(或交变负荷)和作往复运动的摩擦零件应选用粘度较大的润滑油。
5)工作温度较高、磨损较严重和加工较粗糙的摩擦表面应选用粘度较大的润滑油。
6)在高温下工作的蒸汽机汽缸和压缩机应选用闪点高的润滑油,如过热汽缸油、饱和汽缸油和压缩机油。
7)冷冻机应选用凝固点低的润滑油,如冷冻机油。
8)变压器和油开关应选用绝缘性能好的润滑油,如变压器油和油开关油等。
9)氧气压缩机应选用特殊的润滑剂,如蒸馏水和甘油的混合物。
10)当没有合适的专用润滑油时,可选择主要质量指标(粘度)相近(等于或稍大)的代用油或配制代用的混合油。
但是,它的使用应该是临时的,如规定的润滑油到厂后应停止使用。
11)要尽量采用储运、保管、来源方便、使用性能好而价格又低的润滑油。
二、润滑脂
半固体的润滑剂称为润滑脂或干油。
润滑脂主要是由矿物油与稠化剂混合而成的。
最常用的稠化剂为钙皂和钠皂。
润滑脂的静摩擦系数很大,因此它会增加机器起动的困难。
但润滑脂动摩擦系数较小,所以当摩擦零件在运转时,其工作状况与普通润滑油基本上是一样的,而且在运转或停车时它都不会泄露。
润滑脂的主要功用是减摩、防腐和密封。
1、润滑脂的主要物理化学性能:
润滑脂的主要物理化学性能主要包括:
针入度、滴点和皂分。
1)针入度:
表示润滑脂的软硬程度,它是润滑脂重要的质量指标之一。
测定时,将重量为150克的标准圆锥穿入温度为250C的润滑脂试样中,以5秒钟内的穿入深度作为该润滑脂的针入度,以十分之一毫米为单位。
针入度愈大则润滑脂愈软,针入度愈小则润滑脂愈硬。
各种润滑脂的牌号是根据针入度来划分的。
润滑脂的针入度是随温度的增高而增大的(即润滑脂变软),所以对于工作温度变化较大的摩擦零件应选用针入度变化较慢的润滑脂。
2)滴点:
滴点表示润滑脂的抗热特性,它也是润滑脂重要的质量指标之一。
测定时,将润滑脂试样装入测定器内加热,以润滑脂液化后的第一滴油滴落下来时的温度作为该润滑脂的滴点。
普通润滑脂的滴点大约在75~1500C之间。
选择润滑脂时应使其滴点比摩擦零件的工作温度大20~300C.
3)皂分含量:
在润滑脂中金属皂分的含量愈多则针入度愈小,滴点也就愈高。
测定时,将润滑脂溶于苯中,用丙酮沉淀润滑脂苯溶液中的肥皂,然后用重量法测