重点基础材料技术提升与产业化重点专项钢铁材料模块要点.docx
《重点基础材料技术提升与产业化重点专项钢铁材料模块要点.docx》由会员分享,可在线阅读,更多相关《重点基础材料技术提升与产业化重点专项钢铁材料模块要点.docx(36页珍藏版)》请在冰豆网上搜索。
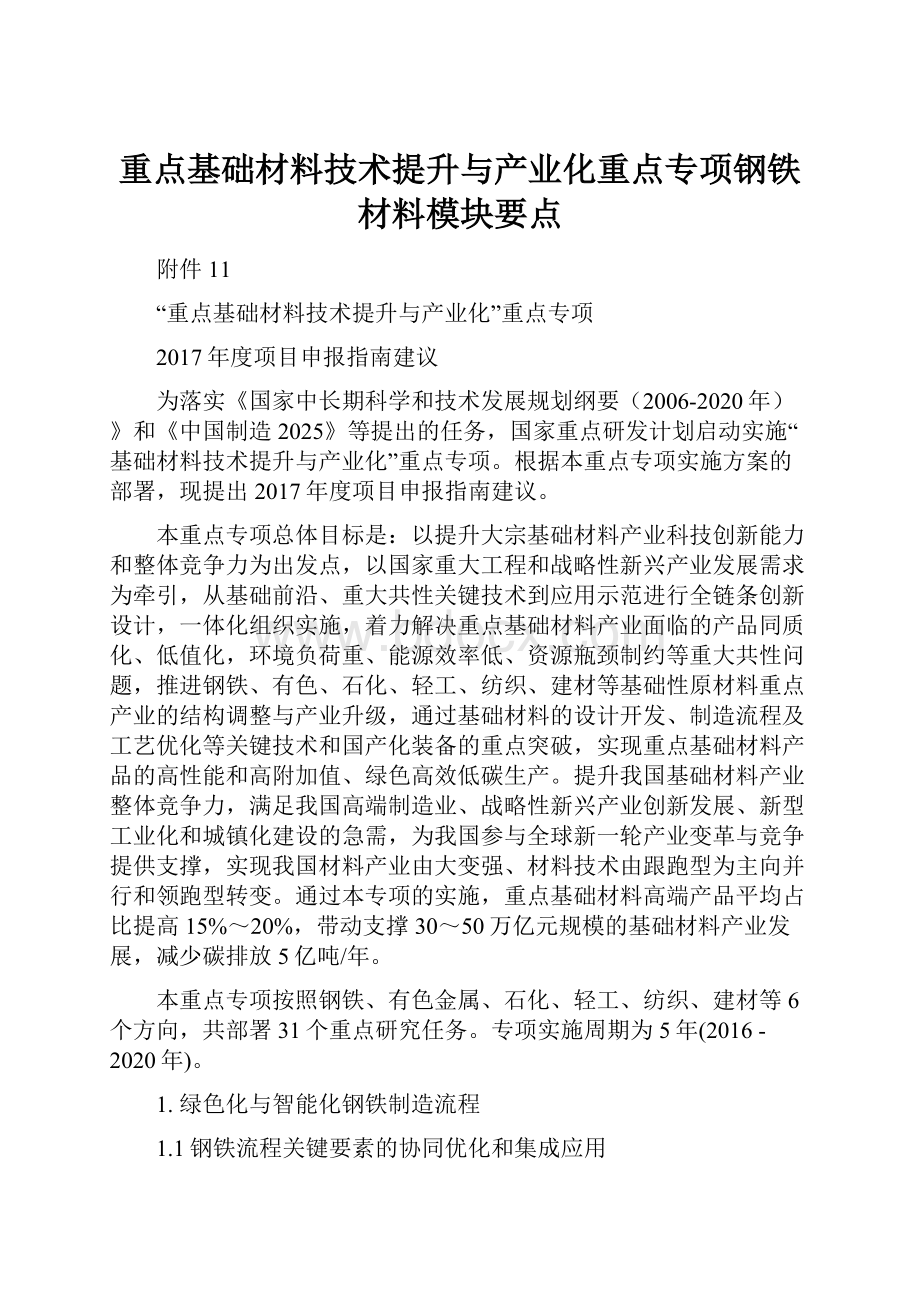
重点基础材料技术提升与产业化重点专项钢铁材料模块要点
附件11
“重点基础材料技术提升与产业化”重点专项
2017年度项目申报指南建议
为落实《国家中长期科学和技术发展规划纲要(2006-2020年)》和《中国制造2025》等提出的任务,国家重点研发计划启动实施“基础材料技术提升与产业化”重点专项。
根据本重点专项实施方案的部署,现提出2017年度项目申报指南建议。
本重点专项总体目标是:
以提升大宗基础材料产业科技创新能力和整体竞争力为出发点,以国家重大工程和战略性新兴产业发展需求为牵引,从基础前沿、重大共性关键技术到应用示范进行全链条创新设计,一体化组织实施,着力解决重点基础材料产业面临的产品同质化、低值化,环境负荷重、能源效率低、资源瓶颈制约等重大共性问题,推进钢铁、有色、石化、轻工、纺织、建材等基础性原材料重点产业的结构调整与产业升级,通过基础材料的设计开发、制造流程及工艺优化等关键技术和国产化装备的重点突破,实现重点基础材料产品的高性能和高附加值、绿色高效低碳生产。
提升我国基础材料产业整体竞争力,满足我国高端制造业、战略性新兴产业创新发展、新型工业化和城镇化建设的急需,为我国参与全球新一轮产业变革与竞争提供支撑,实现我国材料产业由大变强、材料技术由跟跑型为主向并行和领跑型转变。
通过本专项的实施,重点基础材料高端产品平均占比提高15%~20%,带动支撑30~50万亿元规模的基础材料产业发展,减少碳排放5亿吨/年。
本重点专项按照钢铁、有色金属、石化、轻工、纺织、建材等6个方向,共部署31个重点研究任务。
专项实施周期为5年(2016-2020年)。
1.绿色化与智能化钢铁制造流程
1.1钢铁流程关键要素的协同优化和集成应用
研究内容:
研究基于冶金工程流程学的钢铁流程绿色化与智能化协同机制、能源转换及综合能效提升规律;发展基于工序功能耦合匹配及界面/亚界面重构理论的炼铁-炼钢和连铸-轧制各区段智能化调控技术;研究钢材定制化生产与窄窗口智能化控制机理;开发多工序优化组合、不同工序生产节奏动态有序匹配和低成本的钢水质量窄窗口智能化稳定控制技术及应用示范;发展基于能量流网络模型的物质流与能量流智能协同调配技术及应用示范。
考核指标:
通过应用基础研究,形成钢铁制造流程物质流、能量流和信息流协同理论。
通过钢铁流程绿色化与智能化技术集成开发、应用,钢铁流程能效由目前的45%左右提高到55%,吨钢能耗比2015年降低8%,吨钢气体污染物排放比2015年降低30%。
为显著提升钢材质量稳定性、可靠性和适用性,扩大钢材的品牌增值提供关键技术支持。
1.2扁平材全流程智能化制备关键技术
研究内容:
开发面向产品价值链协同制造模式、智能化生产动态排程等钢材定制化生产技术及应用示范;开发产品全流程质量在线监控、诊断与优化技术及应用示范;开发多工序协调匹配与质量窄窗口智能化控制技术及应用示范;开发产品加工过程温控-变形耦合-性能匹配及表面质量控制智能化技术及应用示范;开发近终型、低温增塑、变厚度与复合轧制及热处理技术。
考核指标:
通过全流程智能化技术开发、应用,实现全流程智能化控制,流程数控化率超过80%,生产效率提高10%,建立具有国际先进水平的以信息深度感知、智慧优化决策和精准控制执行为特征的扁平材智能化工厂样板,形成典型产品全流程智能化协同控制的成果包;显著提升钢材质量稳定性、可靠性和适用性,产品性能波动减少20%,扩大钢材的品牌增值;关键技术研发形成应用示范。
1.3长型材智能化制备关键技术
研究内容:
开发长型材连铸恒温、恒量出坯与轧制节奏匹配的智能化控制、长型材炼钢-轧制全过程负能制造、多工序生产成本综合优化、基于大数据的温度场-应力场-应变场耦合及产品多等级质量控制等钢材定制化生产与窄窗口智能化控制技术,并应用示范;研究全废钢电炉连续加料-快速熔炼应用基础,开发短流程电炉冶炼和全废钢电炉连续加料-快速熔炼关键技术及应用示范。
考核指标:
实现长型材生产智能化控制,流程数控化率超过80%;规模化直轧率不小于95%,同类型长型材轧钢工序吨钢能耗降低20公斤标煤,长型材炼钢-轧制全过程吨钢能耗小于零;显著提升钢材质量稳定性、可靠性和适用性,扩大钢材的品牌增值。
全废钢电炉实现连续加料、快速熔炼,建立环境友好型电炉短流程示范。
1.4钢铁流程绿色化关键技术
研究内容:
研究矿相结构及高效成矿机理、结焦过程胶质体快速形成的传热传质规律和基于大数据的高炉低能耗热状态形成机理,开发基于高效低耗的烧结、焦化和炼铁绿色化技术;开发低漏风率、少烟气量和低返矿率的烧结关键技术与装备;研究烧结过程有毒有害物质的产生与代谢轨迹,开发其过程烟气选择性循环的烧结多污染物深度脱除及其相关副产物的资源化技术与应用示范;开发资源节约型高耐蚀、除雾霾抗菌涂镀技术。
考核指标:
通过钢铁流程绿色化关键技术开发及应用,为高效低耗冶金绿色化生产和多种污染物脱除及资源化提供解决方案,实现钢铁制造流程绿色化生产。
吨焦能耗降低5公斤标煤以上,吨烧结矿能耗降低3公斤标煤以上,吨铁能耗降低5公斤标煤以上;烧结机漏风率比2015年指标减少15%以上,返矿率比2015年指标减少10%以上;吨钢气体污染物排放比2015年指标降低20%以上;副产物资源利用率比2015年指标提高10%以上;镀层厚度减少30%的情况下钢材寿命提高1倍以上,在可见光下24小时致霾气体去除率≥60%、抗菌率≥90%;
2.高性能交通与建筑用钢
2.1高性能超高强汽车用钢
研究内容:
研究高性能超高强汽车用钢多相与相变强韧化机理;第三代先进汽车用钢的多相组织设计与调控、生产工艺与装备及制造关键技术;复杂成形条件下汽车用钢的微观组织结构演变、宏观变形及回弹控制技术原理、延迟开裂机理;高强度钢成形关键工艺与控制技术、应用及轻量化评价技术;全面打通第三代高强塑积汽车用钢的设计、研发、生产与应用产业链,实现抗拉强度为1000-1500MPa的高强塑积第三代汽车用钢铁材料的研发、生产及关键部件制造产业化示范。
考核指标:
第三代超高强汽车用钢形成系列产品和应用,性能指标达到:
1000MPa级延伸率≥21%,1200MPa级延伸率≥17%,1500MPa级延伸率≥14%,建立超高强汽车用钢品种体系、生产体系、标准体系和用户评价体系,形成年产10万吨超高强汽车用钢生产示范线,建成具有世界先进水平高强度汽车用钢零部件先进成形技术示范线;更高强塑积(≥30GPa·%)的第三代汽车用钢取得突破,性能指标达到:
1000MPa级延伸率≥35%、1200MPa级延伸率≥30%,1500MPa级延伸率≥20%,实现1000-1500MPa的高强塑积第三代汽车用钢的制备与应用示范。
大幅度、大规模地推动车身轻量化和节能减排,实现汽车关键零部件减重8-21%,汽车轻量化钢铁材料研发与应用达到国际领先水平。
2.2高耐磨高强韧重载钢轨用钢
研究内容:
研究重载条件下钢轨钢的耐磨损、耐疲劳、抗冲击行为的组织调控机制;开展在线热处理工艺下组织结构的精确控制与配套焊接技术研究;开发重载铁路用耐磨损过共析钢轨;开发适合苛刻线路条件应用的低成本、高强韧贝氏体钢轨;开展重载钢轨的服役性能评价及应用技术研究,实现干线铁路应用示范。
考核指标:
开发出抗拉强度≥1330MPa、轨头顶面硬度390-450HB,耐磨损性能较现役钢轨至少提高20%,满足线路年运量5亿吨服役需求;开发出抗拉强度≥1380MPa、延伸率≥12%、-20℃断裂韧性≥60MPa·m1/2的高强高韧贝氏体钢轨,整组道岔通过总重达3亿吨以上;示范应用总量达到千吨级以上,形成我国具有自主知识产权的重载铁路钢轨品种体系、生产体系和应用体系;形成3个以上具有世界先进水平的重载钢轨研发、生产和应用示范基地。
2.3苛刻环境下铁路车辆关键部件用钢
研究内容:
研究高速车轴用钢耐疲劳、高韧性的组织细化和第二相控制机制;研究铁路车辆车体用钢的耐大气腐蚀和局部腐蚀行为;开发窄成分冶炼、超低氧、高洁净度的稳定控制技术;开发高寒地区用高韧性高速车轴用钢、高耐候高强度易焊接转向架构架用钢和车体用钢等关键品种,实现示范应用。
考核指标:
开发出屈服强度450MPa级高韧性空心车轴用钢,-40℃U型缺口冲击功达40焦耳以上,满足高寒地区高铁运输需求;开发出高铁用屈服强度390MPa级高耐候易焊接转向架构架用钢及配套焊接材料与工艺,满足30年服役寿命要求;开发出高耐候货车用屈服强度500MPa级车体用钢,满足25年服役寿命要求;示范应用总量达到千吨以上,满足我国设计时速350公里以上高铁用钢和高耐候货车用钢需求,形成3个以上具有世界先进水平的铁路车辆用钢研发、生产和应用示范基地。
2.4建筑结构用抗震耐候耐火钢
研究内容:
研究长期腐蚀环境和高温火灾条件下合金耐蚀性与高温组织稳定性的耦合调控机理;开发建筑钢结构用钢低屈强比与高耐蚀耐火性能关键控制技术;开发加速锈层稳定的合金化及表面预处理关键技术;开发高层及超高层建筑用高强抗震耐蚀耐火建筑结构用钢板、型钢及其配套焊接材料与工艺;开展全寿命周期耐腐蚀性能评价,建立耐蚀耐火钢应用技术与服役性能评价体系,形成建筑结构用耐蚀耐火钢研发、生产及应用示范。
考核指标:
开发出460MPa级及690MPa级耐蚀耐火钢板、型钢,屈强比≤0.85,断后伸长率≥18%,耐火极限性能为600℃下3小时其屈服强度高于室温屈服强度的2/3;焊材及焊接接头的耐蚀性、耐火性与母材匹配;使用寿命达到50-100年;形成沿海海洋大气环境下建筑结构用耐蚀钢的服役性能评价体系,制定标准和应用设计规范或建筑钢结构设计指南;形成3个以上建筑结构用抗震、耐蚀、耐火钢研发、服役评价和生产示范基地。
2.5高性能桥梁用钢
研究内容:
研究桥梁用钢腐蚀与断裂失效行为、疲劳与止裂控制原理;开发低屈强比桥梁钢合金成分与组织结构控制关键技术;研究合金成分体系、深加工工艺对桥索钢缠绕、弯曲和扭转性能的影响机理,开发超高强度桥索钢控轧及离线铅浴淬火关键工艺;开发锈层稳定化表面预处理、锈层损伤修补等控制技术;开发构件大型化、厚壁化条件下免预热焊接桥梁用钢的合金体系及生产控制技术;开发满足100年使用寿命的420MPa级焊前不预热或少预热耐候桥梁钢以及690MPa级高强耐候桥梁钢工业化制造技术,开发配套焊接与螺栓连接等关键技术;建立服役环境及结构评价体系,形成标准、规范,实现应用示范。
考核指标:
开发出焊前不预热或预热温度≤75℃的420MPa级耐候桥梁钢,-40℃断口纤维断面率≥70%、屈强比≤0.85;开发出2000MPa级桥索钢,缠绕弯曲和扭转均达到8次以上;无涂装耐候桥梁钢稳定化锈层形成时间小于1月;开发出690MPa级屈强比≤0.85的桥梁钢;完成配套焊接材料及工艺的开发;开发出与母材耐候性相当的12.9级耐候螺栓钢,100小时延迟断裂试验,0.9倍抗拉强度加载,饱和充氢含量[H]c≥3ppm,不发生断裂;提出桥梁构件防断设计选材规范,建立无涂装耐候桥梁钢使用规范;实现千吨级示范应用,耐候桥梁钢使用寿命达到100年。
3.先进能源用钢
3.1低温、高压服役条件下高强度管线用钢
研究内容:
针对极寒地区气温条件,研究在低温、高压服役条件下高强度管线钢的断裂力学行为和韧化机理,阐明在低温条件下控制塑性断裂和裂纹止裂的物理冶金学原理,二氧化碳驱服役环境下钢管腐蚀机理;突破低温用特宽、特厚钢板/带和二氧化碳驱专用耐蚀钢的合金设计、在线全流程组织细化热机械处理、微观结构精细调控和应用评价等关键技术;开发低温超大输量和二氧化碳驱管道用钢的成套工业化制造技术;制定专用标准规范,实现示范应用。
考核指标:
开发出宽度满足Φ1422毫米制管要求,钢板最大厚度31.8毫米,钢带最大厚度21.4毫米,屈服强度555MPa级,-40℃夏比冲击功≥245焦耳的低温管线钢,满足450亿立方米/年超大输量或-40℃极寒地区服役的国家重大管道工程建设对板材的技术要求,实现低温用管线钢的完全国产化;二氧化碳驱耐蚀钢在典型服役环境下腐蚀速率低于0.076毫米/年,服役寿命比现用金属管道提升2倍以上;建立低温超大输量和二氧化碳驱管道用钢的研发、生产、应用和标准规范体系,示范应用达到千吨级。
3.2超低温及严苛腐蚀条件下低成本容器用钢
研究内容:
研究储罐用钢组织形态与微结构对超低温(-196℃)强韧性和断裂行为的影响,阐明低成本合金化设计原理和组织精细化调控的冶金学规律,研究异质金属间高温压力复合的原子互扩散行为和界面脆性相形成规律;为确保低成本储罐用钢的超低温强韧性,开发超纯净冶炼与低偏析连铸技术、显微组织与析出相调控的热机械处理与热处理技术、专用焊材与焊接技术,以及异质金属全轧制复合工艺与装备;形成低成本储罐用钢和异质钢板轧制复合成套工业化生产技术;制定专用标准规范,实现示范应用。
考核指标:
开发出厚度规格5-60毫米节Ni型液化天然气储罐用钢,满足大型储罐建设要求,与9Ni钢综合使用性能相当,且比9Ni钢合金成本降低20%以上;“钢-钛”与“钢-耐蚀合金”复合板界面剪切强度分别达到200MPa和350MPa以上,内、外弯曲180度后无分层和裂纹。
建立我国低成本储罐用钢标准规范,节Ni型液化天然气储罐用钢和双金属复合板形成应用示范。
3.3煤炭采运用高耐磨性钢板
研究内容:
研究煤炭采运工况下钢材的磨损行为和机理,研究在保持良好的加工性和焊接性的前提下,提高钢材耐磨性的合金设计和组织控制理论,突破煤炭采运用高耐磨性钢板合金设计、冶炼、铸造和精细组织控制等关键技术,形成煤炭采运用高耐磨性钢成套生产制造技术,开展应用与评价技术研究,建立相关标准规范,实现产业化及应用示范。
考核指标:
钢板表面布氏硬度400~500HB,心部硬度不低于表面硬度的90%;在机械加工性能和焊接性达到相同硬度传统马氏体耐磨钢水平前提下,耐磨性提高到相同硬度传统马氏体耐磨钢的1.5倍以上;钢板最大厚度规格65毫米,满足年产煤量一千万吨高产高效工作面所需重型、超重型刮板输送机的制造需求;建立煤炭采运用高耐磨性钢的理论体系、生产技术体系和标准规范体系,完成产业化和应用示范,示范达到千吨级。
3.4先进超超临界锅炉高温弯管和铸锻件
研究内容:
研究700℃超超临界锅炉用新型马氏体耐热钢、新型镍基和铁镍基耐热合金的高强韧、长寿命机理及其在高温高压复杂介质环境下的失效机理,研发基于耐热材料高温性能稳定性的基体组织与析出相控制技术,实现700℃超超临界燃煤锅炉工程用高温弯管、锻件和铸件产业化制造。
考核指标:
对5吨级典型件,新型马氏体耐热钢高温弯管、锻件和铸件650℃10万小时外推持久强度≥100MPa,纯固溶强化型镍基耐热合金锻件675℃10万小时外推持久强度≥100MPa,铁镍基和镍基耐热合金锻件700℃10万小时外推持久强度≥100MPa。
3.5新一代压水堆核岛用钢及临氢化工大单重特厚板
研究内容:
研究第三代先进核能系统用钢(含铸锻件和宽厚板)高强韧和组织细化调控机理,研发新一代高品质宽厚板和大型铸锻件高洁净、均质化制造技术。
研究大单重、特厚(100mm以上)临氢设备用Cr-Mo容器钢及配套关键材料。
考核指标:
核压力容器用钢锻件尺寸Ф2000毫米×700毫米,厚度T/2处取样无塑性转变温度RTNDT≤-60℃,350℃抗拉强度≥600MPa。
核反应堆安全壳用钢板尺寸4000毫米×60毫米,厚度T/4处取样,室温下,屈服强度Rel≥485MPa,抗拉强度Rm:
655-795MPa,-45℃冲击功KV8≥54焦耳。
大单重指标≥21吨、150-200毫米厚Cr-Mo钢板T/2取样性能达到临氢工程设备设计要求。
4.新型稀有/稀贵金属材料
4.1超高纯稀有/稀贵金属制备技术
研究内容:
研究超高纯稀有/稀贵金属材料制备过程中深度除杂与净化机理,建立相关的痕量杂质元素精确检测方法并研制标准样品;开发高效率、短流程和环保型的稀有/稀贵金属超高纯原材料联合纯化技术,以及超高纯、低缺陷铸锭制备技术和高品质粉体原料制备技术;实现产业化示范应用。
考核指标:
铸锭或粉体原料按电子行业标准分析纯度达到:
Au、Ag≥6N,Pt、Pd、Ru、Ir、Re、Co、Ni、Ti、W、Mo、Ta纯度≥5N,非金属杂质元素C、N、O、H、S含量满足电子行业标准要求;建立GDMS(辉光放电质谱法)、LA-ICP-MS(激光剥蚀电感耦合等离子体质谱仪)等配套纯度检测方法,分析痕量杂质元素40-70个、检出限达到10-9-10-11量级,形成系列化的标准样品,形成国家/行业标准≥5项;超高纯金属铸锭尺寸≥150毫米,缺陷率≤0.5%;高纯粉末原料粒度1~30微米、呈正态分布;形成Au、Ag、Pt、Pd、Ru、Ir、Co、Ni各1~5吨/年的系列化超高纯原料规模生产能力。
4.2大规格稀有/稀贵金属靶材制造技术
研究内容:
研究高端元器件用新型超高纯稀有/稀贵金属及其合金材料塑性变形及微观组织演化规律与机理;开展超高纯金属靶材及制品微观组织均匀成型控制工艺研究,突破铁磁性靶材磁性能/电性能控制关键技术;开发铂族、铁磁性稀有/稀贵金属靶材及TFT(薄膜晶体管)制造用超高纯铜旋转靶材,以及大面积异质金属高性能焊接及高精度加工技术;实现产业化示范应用。
考核指标:
超高纯铂族单质金属靶材按电子行业标准分析Pt、Ru、Ir纯度≥5N(分析杂质元素40-70个),坯锭尺寸≥150毫米,相对密度≥99.5%,氧含量≤50ppm(百万分比浓度);铁磁性超高纯稀有/稀贵合金靶材,杂质元素总量≤100ppm(百万分比浓度),晶粒尺寸≤80微米,二次相均匀分布,透磁率不均匀性≤5%,靶材最大尺寸≥200毫米;超高纯铜旋转靶纯度≥4N,氧含量≤5ppm,靶材晶粒尺寸≤150微米,靶材长度≥2.5米、尺寸精度为±0.1毫米;形成贵金属靶材、铁磁性靶材和高纯铜旋转靶材的规模化生产能力。
4.3大尺寸高纯稀有金属制品制备技术
研究内容:
探索高端装备用高纯稀有金属材料制备加工过程的微观组织演化规律与综合性能的控制机理,突破大规格高纯稀有金属材料的高温高压烧结、高精度变形加工、超高纯硅单晶制品的精密制备技术等,开发大尺寸精深加工发热体/热屏、坩埚等工业化产品,实现高端装备用发热体/热屏和坩埚等的1-2代升级。
考核指标:
钨坩埚/钨管尺寸外直径Ф外)≥1000毫米,高度≥1200毫米,密度≥18.5克/厘米3,晶粒度≤50微米;钨、钼板宽度≥800毫米,钼板坯单重≥800千克,钼板最薄厚度0.1毫米,大型高温炉热场温度均匀性±2℃;铼板纯度≥6N,宽度≥600毫米;钨及钨合金靶材纯度≥5N,Na+K+Li≤1ppm(百万分比浓度),相对密度≥99.5%,平均晶粒尺寸≤20微米;超纯硅单晶环和多孔电极纯度≥11N,最大尺寸≥300毫米,多元Si合金靶纯度≥4N,致密度≥90%,成分波动≤±5%;形成年产高端装备用大尺寸精加工高纯稀有金属制品1500吨/年的工业化规模生产能力。
4.4稀贵金属焊接/装联导电材料制备技术
研究内容:
探索稀贵金属合金粉末应用及焊接与装联过程中异质界面反应机理、复杂耦合条件下焊点失效机制及微观组织/结构/形态对界面反应的影响。
突破粉体颗粒形貌、氧含量、粒度及分布、表层钝化等精确控制关键技术;开发新型超细、窄粒度锡基等稀有金属和贵金属合金钎料粉末、配套环保型助焊剂及相关制备工艺与装备。
考核指标:
系列钎料熔化温度100-1200℃,焊接/装联强度35-300MPa,电阻率<40欧姆·厘米,热导率>21焦耳/米·秒·开;锡基合金焊粉粒度及分布20-38微米、15-25微米、15-5微米、2-11微米,贵金属粉径<74微米,超限比例<5%,C、O含量均<300ppm(百万分比浓度),球形度长短轴比<1.2,制粉一次收得率>90%;丝材直径0.01-0.03毫米,带材厚度0.01-0.05毫米,箔材厚度0.005-0.008毫米;膏体连续使用48小时保持流动性、存储6月粘度变化≤30帕·秒;形成锡基和贵金属粉末2000吨/年的生产能力,新增产值8亿元。
5.高品质粉末冶金难熔金属材料及硬质合金
5.1超细3D打印有色/难熔金属球形粉末制备技术
研究内容:
探索金属熔体在雾化过程中的高效分散机制、熔滴的球化过程和凝固行为、共性关键参数对粉末物化特性的影响,研究用于3D打印用高品质球形粉末的低成本雾化制备技术,开发应用于航空航天、精密模具、医疗等领域的超细球形粉末,形成具有自主知识产权的工业化制备技术与装备。
考核指标:
开发出适用于3D打印的高品质钛基、镍基合金球形粉末,粒度≤53微米的细粉收得率钛基合金≥40%、镍基合金≥70%, 其钛基合金平均粒径D50≤45微米、镍基合金平均粒径D50≤35微米,粉末球形度≥90%,松装密度≥50%,流动性≤30秒/50克,钛合金、镍合金粉末氧含量分别≤1000ppm(百万分比浓度)、≤200ppm(百万分比浓度);形成钨钼等3D打印难熔金属粉末制备技术原型;建立具有自主知识产权的3D打印用高品质球形金属粉末的低成本雾化制备技术,生产制备过程实现智能化控制,形成1000吨/年的工业化规模生产能力。
5.2高性能新型结构硬质合金制备技术
研究内容:
研究硬质合金及金属陶瓷组织强韧化机理;针对先进加工、高硬度钢材和复合材料等的加工要求,开展超细晶硬质合金材料及带涂层刀具工具等制备技术研究;针对高负载、高效率掘进复杂工况,开展高韧性超粗晶粒和梯度成分硬质合金材料及其带涂层刀具工具的制备技术研究;与现有产品相比,新型超细晶/超粗晶/梯度成分硬质合金的综合性能提升20%以上、高端涂层刀具工具综合性能提升50%以上;形成高性能硬质合金和超纯超细均质原料制备产业化示范线。
考核指标:
超纯超细硬质合金粉体:
碳化钨原料BET(比表面积法)>3.5平方米/克,氧含量<0.4%;超细晶硬质合金平均截线晶粒度dm≤0.2微米,抗拉强度Rm≥4900MPa,洛氏硬度HRA≥94;超粗晶硬质合金平均截线晶粒度dm≥6.0微米,抗拉强度Rm≥3000MPa,断裂韧度KIC≥22MP·m1/2;梯度成分硬质合金抗拉强度Rm≥3200MPa,冲击韧性ak≥14焦耳/平方厘米;形成2条以上高性能硬质合金及高端涂层刀具工具制造和超纯超细粉末原料制造产业化示范线,新增产值8-10亿元。
5.3大规格高性能难熔金属制品制备技术
研究内容:
探索难熔金属耐高温/耐冲击/耐磨损第二相设计理论及大规格难熔金属材料致密化、均质化及形变机理;研究大尺寸难熔金属成形、烧结及变形过程中关键工艺技术和复杂形状制品近终成形与强化烧结技术,开发高端装备用高性能大规格钨基高比重合金、钼及钼合金的工业化制造技术。
考核指标:
大规格高均质高比重合金直径≥850毫米,高度≥800毫米,抗拉强度≥900MPa,延伸率≥15%,疲劳强度+/-200MPa,≥100万次,冲击韧性≥60焦耳/平方厘米;钼棒最大直径200毫米,抗拉强度≥500MPa,延伸率≥10%;钼钛锆合金最大直径150毫米,抗拉强度≥600MPa,延伸率≥10%,氧含量<100ppm(百万分比浓度);钼合金板尺寸L×1500×(0.6-6)毫米,抗拉强度≥1000MPa,延伸率≥10%;近终形钨、钼零件相对密度≥99%,尺寸精度±0.3%;钼辊轮相对密度≥99%,平均晶粒度≤30微米,抗拉强度≥500MPa;形成年产高性能大规格难熔金属材料3000吨/年的工业化生产能力。
6.有色/稀有/稀贵金属材料先进制备加工技术
6.1新型复合涂层/易反偏析合金快速凝固成形制备技术
研究内容:
探索新型多组元合金粉末、复合涂层和易反偏析有色金属坯锭制备过程中的非平衡凝固/复合凝固机理及控制技术;针对高温耐熔融金属腐蚀部件/重载液压支架/固体氧化物燃料电池/燃机热端部件等应用需求,开展新型复合涂层设计和制备过程模拟、合金粉末快冷/超快冷凝固制备及涂层快速制备工艺;开发新一代海洋工