外文翻译应用计算机辅助工程设计重型卡车车架.docx
《外文翻译应用计算机辅助工程设计重型卡车车架.docx》由会员分享,可在线阅读,更多相关《外文翻译应用计算机辅助工程设计重型卡车车架.docx(15页珍藏版)》请在冰豆网上搜索。
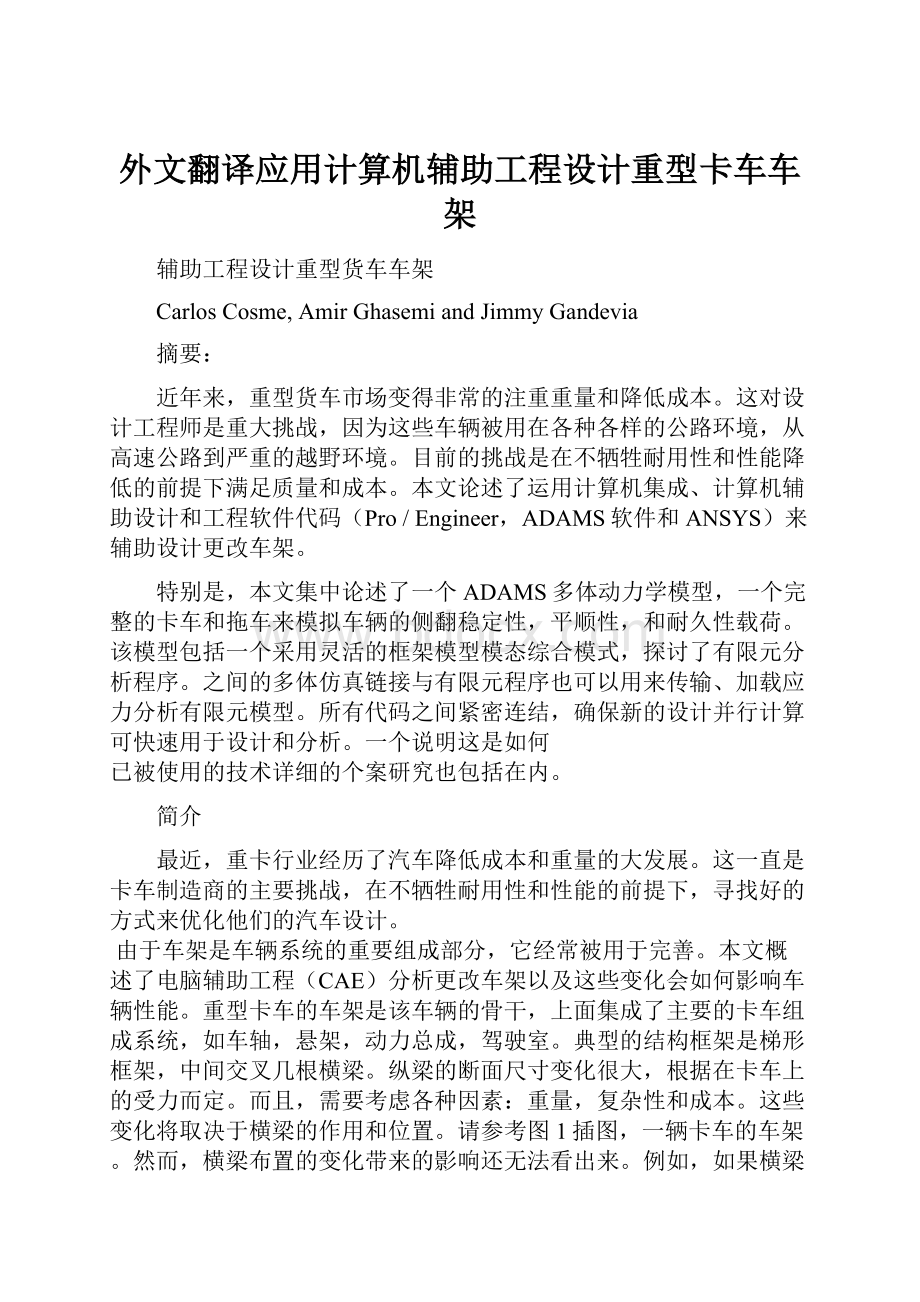
外文翻译应用计算机辅助工程设计重型卡车车架
辅助工程设计重型货车车架
CarlosCosme,AmirGhasemiandJimmyGandevia
摘要:
近年来,重型货车市场变得非常的注重重量和降低成本。
这对设计工程师是重大挑战,因为这些车辆被用在各种各样的公路环境,从高速公路到严重的越野环境。
目前的挑战是在不牺牲耐用性和性能降低的前提下满足质量和成本。
本文论述了运用计算机集成、计算机辅助设计和工程软件代码(Pro/Engineer,ADAMS软件和ANSYS)来辅助设计更改车架。
特别是,本文集中论述了一个ADAMS多体动力学模型,一个完整的卡车和拖车来模拟车辆的侧翻稳定性,平顺性,和耐久性载荷。
该模型包括一个采用灵活的框架模型模态综合模式,探讨了有限元分析程序。
之间的多体仿真链接与有限元程序也可以用来传输、加载应力分析有限元模型。
所有代码之间紧密连结,确保新的设计并行计算可快速用于设计和分析。
一个说明这是如何
已被使用的技术详细的个案研究也包括在内。
简介
最近,重卡行业经历了汽车降低成本和重量的大发展。
这一直是卡车制造商的主要挑战,在不牺牲耐用性和性能的前提下,寻找好的方式来优化他们的汽车设计。
由于车架是车辆系统的重要组成部分,它经常被用于完善。
本文概述了电脑辅助工程(CAE)分析更改车架以及这些变化会如何影响车辆性能。
重型卡车的车架是该车辆的骨干,上面集成了主要的卡车组成系统,如车轴,悬架,动力总成,驾驶室。
典型的结构框架是梯形框架,中间交叉几根横梁。
纵梁的断面尺寸变化很大,根据在卡车上的受力而定。
而且,需要考虑各种因素:
重量,复杂性和成本。
这些变化将取决于横梁的作用和位置。
请参考图1插图,一辆卡车的车架。
然而,横梁布置的变化带来的影响还无法看出来。
例如,如果横梁的抗扭刚度降低,对汽车的侧倾稳定性和耐久性的影响是怎么的呢?
设计工程师们需要对这些类型的问题给出答案以指导他们的工作。
特别是,及时的设计和分析程序是必需的,这样新的设计可以快速评估。
图1重型载货汽车车架
计算机辅助工程
在过去的二十年中汽车自动化设计工具CAE得到了巨大的发展。
这项技术的已被很多汽车制造商采用以改善汽车设计来满足快速增长的市场要求。
当今的结构设计通常是使用两个CAE工具:
有限元分析(FEA)和多体系统(MSS),结合CAD提高设计和分析。
在过去十五年里,CAD系统已取代绘图板作为首选设计方法。
它们使设计师和工程师能够快速画出卡车零部件,汽车真实模型和设计图纸。
先进的CAD系统功能丰富,如参数化实体建模和大型装配管理。
他们已经发展成为主要的数据库,为工程信息尤其是CAD系统提供下游CAE应用的重要数据。
工程师通常使用有限元分析研究结构构件的强度。
典型的有限元分析的重点是结构应力,挠度和自然频率。
首先对通常被称为网格的离散结构进行分析。
该网格是由节点和元素组成,而且经常从CAD创建几何系统。
这些节点代表位移计算的结构。
他们定义的局部质量,刚度和阻尼性能结构。
有关这些数量方程,可以自动开发节点位移。
其他投入,如边界条件,载荷和材料特性,必须是由用户定义。
所有这些效果都需要小心的判断和对有意义的结果进行认真的分析。
结果后处理包括图像变形负载结构,彩色应力轮廓,振型动画。
MSS多体系统仿真方法研究了运动部件和组件,并经常用来研究车辆暂停或车辆的操作和动态响应。
一个典型的完整的车型MSS将刚体组成(车轮,车轴,车架,发动机,驾驶室)模拟成关节连接和理想化力元。
MSS代码自动发展非线性微分方程和代数方程定义模型中的物体运动。
该方程在数值上集成刚体位移,速度,加速度和受力。
结果以图形和动画显示该系统的运动。
至于有限元分析,CAD数据经常使用MSS的发展模式。
CAD几何数据是用于建立MSS的布局模式,如接头和力量元素的位置。
CAD实体模型数据也可以用来估计每个刚体的位置,质心和惯性特性。
作用在刚体上的力可以用作MSS的输入负载,有限元分析确定该刚体的结构应力。
CAE技术在本文所讨论的工具包括基与CAD的Pro/Engineer,ANSYS进行有限元分析,以及基于ADAMS的MSS。
下面的讨论引用的是某型卡车的车架有限元分析。
CAE重型汽车建模
如上所述,在目前提供的CAD与CAE工具提供了大量的整合。
尽管如此,这些工具是非常粗略的分析,仍然需要努力分析重型卡车和卡车车架。
为了充分了解车架影响汽车操纵的变化,滚动稳定性,平顺性和持久性,需要一个详细的MSS模型,可以模拟所有这些影响。
使用ADAMS软件代码,建立了WesterStar卡车的模型。
图二展示了在ADAMS环境下的模型。
图2ADAMS的MSS的模型
该模型包括以下几个特点:
•100刚体
•180力元
•45共同元素
•415度-的自由度
1.“MechanicsofHeavy-DutyTrucksandTruckCombinations”,UMTRICourseNotes,July,1995.
2.Stasa,FrankL.,“AppliedFiniteElementAnalysisforEngineers”,CBSCollegePublishing,1985.
3.Ottarsson,Gisli,“ModalFlexibilityMethodinADAMS/FLEX”,MechanicalDynamics,Inc.,March,1998.
4.“UsingADAMS/FLEX”,MechanicalDynamics,Inc.,1997.
5.“ADAMS/FiniteElementAnalysisReferenceManual”,MechanicalDynamics,Inc.,November15,1994.
6.“Pro/MESHandPro/FEMPost,User’sGuide”,ParametricTechnologyCorporation,1997.
7.“ANSYSStructuralAnalysisGuide”,Analysis,Inc.,1994.
8.Gillespie,ThomasD.,“FundamentalsofVehicleDynamics”,SocietyofAutomotiveEngineers,Inc.,1992.
9.Gobessi,MarkandArnold,Wes,“TheApplicationofBondedAluminumSandwichConstructionTechnologytoAchieveaLightweight,LowCostAutomotiveStructure”,SAEpaper982279.
1999-01-3760
ApplicationofComputerAidedEngineeringintheDesignofHeavy-DutyTruckFrames
CarlosCosme,AmirGhasemiandJimmyGandevia
WesternStarTrucks,Inc.
Copyright©1999SocietyofAutomotiveEngineers,Inc.
ABSTRACT
Inrecentyearstheheavy-dutyClass8truckmarkethasbecomeveryfocusedonweightandcostreduction.Thisrepresentsamajorchallengefordesignengineerssincethesevehiclesareusedinawidevarietyofvocationsfromhighwaylinehaultologginginsevereoff-roadenvironments.
Thechallengeistomeettheweightandcost
reductiongoalswithoutsacrificingdurabilityandperformance.Thispaperdiscussestheintegrationofcomputeraideddesignandengineeringsoftwarecodes(Pro/Engineer,
ADAMS,andANSYS)tosimulatetheeffectofdesignchangestothetruckframe.Inparticular,thispaperdiscusesthedevelopmentofanADAMSmulti-bodydynamicsmodelofafulltruckandtrailertosimulatevehiclehandling,rollstability,rideperformance,anddurabilityloading.Themodelincludesaflexibleframemodelusingacomponentmodesynthesis
approachwithmodesimportedfromafiniteelementanalysisprogram.Thelinkbetweenthemulti-bodysimulationandthefiniteelementcodeisalsousedtotransfer
loadsbacktothefiniteelementmodelforstressanalysis.Tightlinksbetweenallthecodesensuresthatnewdesigniterationscanbequicklyevaluatedforconcurrent
designandanalysis.Adetailedcasestudyshowinghowthistechnologyhasbeenusedisalsoincluded.
INTRODUCTION
Recentlytheheavytruckindustryhasexperiencedalargepushtodevelopvehicleswithreducedcostandweight.Thishasbeenamajorchallengefortruckmanufacturers
astheylookforwaystooptimizetheirvehicledesignswithoutsacrificingdurabilityorperformance.
Sincethetruckframeisamajorcomponentinthevehiclesystem,itisoftenidentifiedforrefinement.Thispaperoutlinesacomputeraidedengineering(CAE)procedureforanalyzingchangestothetruckframeandhowthesechangesaffectvehicleperformance.Theframeofaheavytruckisthebackboneofthevehicleandintegratesthemaintruckcomponentsystemssuchastheaxles,suspension,powertrain,cab,andtrailer.
ThetypicalframeisaladderstructureconsistingoftwoCchannelrailsconnectedbycross-members.Theframe
railsvarygreatlyinlengthandcross-sectionaldimensionsdependingonthetruckapplication.Likewise,the
cross-membersvaryindesign,weight,complexity,andcost.Thesevariationswilldependuponthecross-memberpurposeandlocation.RefertoFigure1foranillustration
ofatruckframe.However,theeffectsofchangestotheframeandcross-membersarenotwellunderstood.
Forexample,ifthetorsionalstiffnessofasuspensioncross-memberislowered,whatistheeffectonthevehicle’s
rollstability,handling,ride,anddurability?
Designengineersrequireanswerstothesetypesofquestionstoguidethemintheirwork.Inparticular,aconcurrentdesignandanalysisprocedureisrequiredsothatnew
designscanbequicklyevaluated.
Figure1.Class8Heavy-DutyTruckFrame
COMPUTERAIDEDENGINEERING
InthelasttwentyyearstherehasbeenanenormousgrowthinthedevelopmentofCAEtoolsforautomotivedesign.Muchofthistechnologyhasbeenadoptedbythetruckindustryastruckmanufacturerslooktoimprovetheirdesignsinarapidlygrowingmarket.TodaystructuraldesignistypicallyperformedusingtwoCAEtools:
finite
elementanalysis(FEA),andmulti-bodysystemsimulation(MSS).Thesearecombinedwithcomputeraideddesign(CAD)softwaretoimprovedesignandanalysis
communication.
CAD–InthelastfifteenyearsCADsystemshavereplaceddrawingboardsasthemethodofchoicefordesign.Theyenabledesignersandengineerstoquickly
createrealisticmodelsoftruckcomponents,vehicleassemblies,anddesigndrawingsformanufacturing.
AdvancedCADsystemsarerichinfeaturessuchasparametricsolidmodelandlargeassemblymanagement.Theyhaveevolvedtobecomemajordatabasesforengineeringinformation.Inparticular,CADsystemsprovideimportantdatafordownstreamCAEapplications.
FEA–Finiteelementanalysisisusuallyusedbyengineerstostudythestrengthofstructuralcomponents.
TypicalFEAactivityisfocusedonanalyzingstructuralstresses,deflections,andnaturalfrequencies.Theanalysisbeginswithadiscretizedrepresentationofastructure
knownasamesh.ThemeshiscomposedofnodesandelementsandisoftencreatedwithgeometryfromaCADsystem.Thenodesrepresentpointsonthestructurewheredisplacementsarecalculated.Theelementsareboundedbysetsofnodesandencloseareasorvolumes.Theydefinethelocalmass,stiffness,anddampingpropertiesofthestructure.Equationsrelatingthesequantities
tothenodaldisplacementsareautomaticallydevelopedbythesoftwarecodes.Otherinputs,suchasboundaryconditions,appliedloads,andmaterialproperties,mustbedefinedbytheuser.Eachofthesequantitiesrequirescarefuljudgementformeaningfulresultstobeachieved.Resultspost-processingincludesimagesofdeformedstructuresunderload,colouredstresscontours,andmodeshapeanimations.
MSS–Multi-bodysystemsimulationisusedtostudythemotionofcomponentsandassembliesandisoftenusedtostudyavehiclesuspensionoravehicle’shandlingandrideresponse.AtypicalMSSmodelofafullvehiclewillbecomposedofrigidbodies(wheels,axles,frame,engine,cab,andtrailer)connectedbyidealizedjointsand
forceelements.TheMSScodeautomaticallydevelopsthenon-lineardifferentialandalgebraicequationsthatdefinethemotionofthebodiesinthemodel.Theequationsarenumericallyintegratedtoproducetimehistoriesofrigidbodydisplacements,velocities,accelerations,andforces.Resultsareviewedasgraphsandanimationsof
thesystemmotion.AswithFEA,CADdataisoftenusedtodevelopaMSSmodel.GeometrydatafromaCADassemblyisusedtoestablishthelayoutoftheMSSmodelsuchasthelocationofjointsandforceelements.CADsolidmodeldataisalsousedtoestimatethelocationofthecenter-of-massandtheinertialpropertiesofeachrigidbody.ForcesactingonarigidbodyfromaMSScanbeusedasinputloadstoafiniteelementanalysistodeterminethestructuralstressesinthatrigidbody.
TheCAEtoolsdiscussedinthispaperincludePro/EngineerforCAD,ANSYSforFEA,andADAMSforMSS.Thefollowingdiscussionreferencesthespecificcapabilitiesofthesecodesindevelopingacustomizedenvironmentfortheengineeringanalysisoftruckframes.
CAECUSTOMIZATIONFORHEAVYTRUCK
MODELLING
Asdescribedabove,thecurrentofferingofCADandCAEtoolsprovideagreatdealofintegration.Nonetheless,
thesetoolsareverygeneralinscopeandasignificantcustomizationeffortisrequiredfortheanalysisofheavydutytrucksandtruckframes.Tofullyunderstandhowcha