压力容器制作生产加工工艺.docx
《压力容器制作生产加工工艺.docx》由会员分享,可在线阅读,更多相关《压力容器制作生产加工工艺.docx(31页珍藏版)》请在冰豆网上搜索。
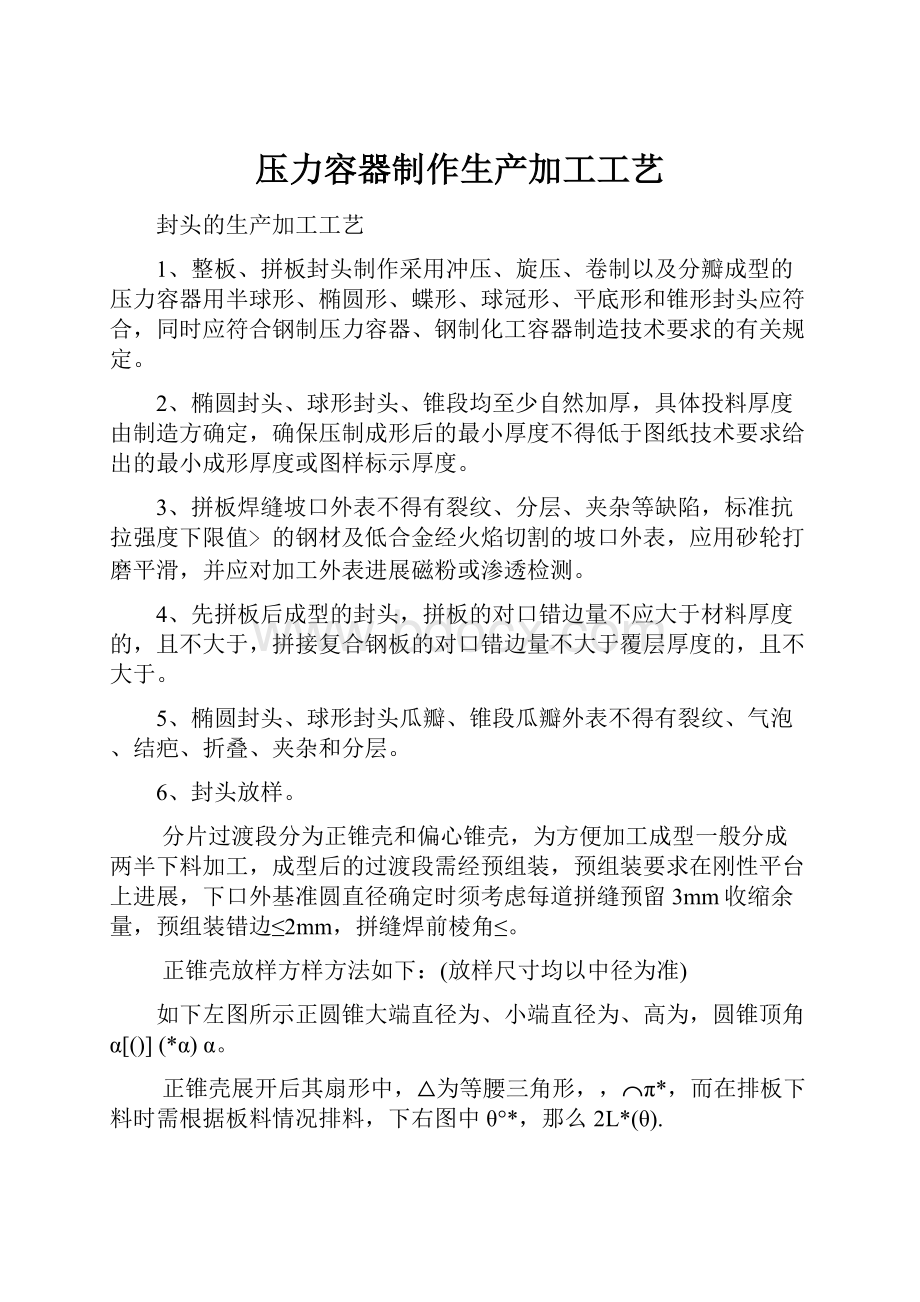
压力容器制作生产加工工艺
封头的生产加工工艺
1、整板、拼板封头制作采用冲压、旋压、卷制以及分瓣成型的压力容器用半球形、椭圆形、蝶形、球冠形、平底形和锥形封头应符合,同时应符合钢制压力容器、钢制化工容器制造技术要求的有关规定。
2、椭圆封头、球形封头、锥段均至少自然加厚,具体投料厚度由制造方确定,确保压制成形后的最小厚度不得低于图纸技术要求给出的最小成形厚度或图样标示厚度。
3、拼板焊缝坡口外表不得有裂纹、分层、夹杂等缺陷,标准抗拉强度下限值﹥的钢材及低合金经火焰切割的坡口外表,应用砂轮打磨平滑,并应对加工外表进展磁粉或渗透检测。
4、先拼板后成型的封头,拼板的对口错边量不应大于材料厚度的,且不大于,拼接复合钢板的对口错边量不大于覆层厚度的,且不大于。
5、椭圆封头、球形封头瓜瓣、锥段瓜瓣外表不得有裂纹、气泡、结疤、折叠、夹杂和分层。
6、封头放样。
分片过渡段分为正锥壳和偏心锥壳,为方便加工成型一般分成两半下料加工,成型后的过渡段需经预组装,预组装要求在刚性平台上进展,下口外基准圆直径确定时须考虑每道拼缝预留3mm收缩余量,预组装错边≤2mm,拼缝焊前棱角≤。
正锥壳放样方样方法如下:
(放样尺寸均以中径为准)
如下左图所示正圆锥大端直径为、小端直径为、高为,圆锥顶角α[()](*α)α。
正锥壳展开后其扇形中,△为等腰三角形,,⌒π*,而在排板下料时需根据板料情况排料,下右图中θ°*,那么2L*(θ).
画的中垂线,使,那么就找出圆心,再以点为圆心为半径画圆弧就可得到展开的两半正锥壳。
偏心锥壳需用三角形展开法画出,偏心锥壳根本采用整体外委加工,验收时必需检查上下口平行度。
三角形展开画法:
在右边图的右(或左)半边两圆周上均分一样的等分,再在大圆周上每个点连接小圆周上相邻的两个点。
画一直角三角形其高度为,斜边为偏心锥壳的最长边。
在直角三角形的底边上分别以垂足为圆心右图的连线为半径画上对应的点。
在钢板上以为长度确定一条直线的两点,再以此两点为基准,直角三角形上顶点到底边的各对应点的距离及各自圆周上的弦长(这些长度尺寸均可用方便的标出)为半径确定在展开图上的各对应点,圆滑的连接这些点即可。
、所有先拼板后成形的椭圆形、球形封头拼缝,须在成形后进展射线探伤,按Ⅱ级合格。
、制造方须提供的资料有:
合格证,板材、焊材质保书及复验报告,无损检测报告,焊接工艺评定报告,焊接记录,加热曲线,正火曲线,几何尺寸检查报告,监检报告,测厚报告,有预热、后热或焊后热处理要求的还须提供相应的曲线及热处理报告。
、封头一般采用热冲压的方法成形,采有冷成形的封头应进展热处理。
当制造单位确能保证冷成形封头的性能符合设计、使用要求时,那么不受此限。
冷成形的奥氏体不锈钢封头可不进展热处理。
、封头、过渡段下料时必需按艺的要求进展相关标记的移植。
、封头在制作完成后,应按照进展验收。
筒节下料工艺
1、领料:
1.1材料须具有合格质保书,标记齐全。
1.2钢板外表不允许存在有裂纹、气泡、结疤、折叠和夹杂等缺陷。
钢板不得有分层。
如有上述外表缺陷,允许清理,清理深度从钢板实际尺寸算起,不得超过钢板厚度公差之半,并应保证钢板的最小厚度。
缺陷清理处应平滑无棱角。
其他缺陷允许存在。
但其深度从钢板实际尺寸算起,不得超过钢板厚度公差之半,并应保证缺陷处厚度不超过钢板允许最小厚度。
1.3图样及标准规定进展超探的材料应检验合格。
1.4不锈钢及复合板复层外表下料前应有防污染措施。
2、号料
3、按排板图号料,一般同材料,同焊接方法的筒体纵缝加工一组产品试板。
4、划线、号料时须考虑卷制管马鞍口形状和接收焊接型式〔内伸或平齐〕,并预留机加工余量,按理论最长点尺寸保证。
注意图纸中接收外伸高度、内伸高度的解释。
注意设计对标准人孔组合件的特殊备注,如锥段上人孔接收须加长。
5、筒节板长、宽号料允差为±,对角线允差≤,刨削余量为。
6、号料后板面各项标记应齐全,如筒节编号、产品编号〔见排板图〕。
7、如超出滚制能力,根据筒节直径和壁厚,板两端合理预留-的带头板,一般是直径越小壁厚越厚预留的带头板越长。
8、标记移植
9、按附图二、三标移统一内容,包括材质、质保书自编号。
不锈钢、钢、高强钢、低温钢材料外表不得打制钢印。
10、标移时如焊接工艺为内坡口,那么需标移在画线一面的反面,此时必需在画线一面用记号笔写上相关标记。
11、下料
12、复核材料标记,包括钢号、炉批号、机械性能和化学成分或入厂复验号或者检验结果报告单。
13、做到“五不〞即图纸不清不下料、代料不见材料代用通知单不下料、外表质量不合格不下料、材料不清不下料、检验工序不完善不下料。
13.1不锈钢板下料采用等离子切割机切割或用剪板机剪切。
13.2其余板材下料采用小车式氧-乙炔切割,或者手工气割。
13.3剪切、切割后相对于检查线偏差为±1mm。
13.4采用剪切下料后剪切面允许有深度≤1mm的磕痕和厚度≤的毛刺。
13.5板料剪切下料允差如下表
板材尺寸
〔〕
下偏差
上偏差〔〕
板厚〔〕
-
-
-
-
-
<
.
.
.
.
.
>-
.
.
.
.
.
>-
.
.
.
.
.
>-
.
.
.
.
.
>-
.
.
.
.
.
>-
.
.
.
.
.
>-
.
.
.
.
.
>
.
.
.
.
.
14、坡口切割
14.1、、等钢板可用氧-乙炔切割坡口。
14.2板切割后坡口外表不得有沟槽和缺肉,不得有氧化铁等杂物。
应均匀光滑,坡口钝边允差为±1mm。
14.3筒节板长宽度及对角线允差应符合下表
筒节直径Φ
对角线差
±
±
±
±
长度偏差Δ
±
±
±
±
14.4切割的坡口必须磨去氧化层、渗碳层、淬硬层,直至露出金属光泽。
15刨边
15.1钢板坡口均采用刨边机。
15.2需削薄处理的筒节钢板不得在钢板未圈圆的情况下采用刨边机削薄。
15.3板刨边后坡口外表不得有挤压或鱼鳞状痕迹,粗糙度不得低于
坡口钝边允差为±,角度允差为±°。
15.4筒节板长宽度允差为±,对角线允差≤。
15.5需进展坡口探伤的板料其坡口探伤前,须进展外表打磨,直至露出金属光泽。
图二
附图三
、尺寸具体见试板工艺
、特殊技术要求:
钢及σ≥的高强钢坡口外表须作或。
换热器壳程筒体内直径允许偏差可通过外圆周长加以控制,其外圆周长允许上偏差为10mm,下偏差为零。
此工艺规程同时适用于筒体、裙座筒体、锥段、卷制接收。
筒体滚圆、校圆工艺
、准备工作
卷板工作场地应保持清洁、平整,无各种影响操作的障碍物,卷制有色金属及不锈钢筒体时,工作堆放处应铺木板或多或橡胶板。
检查卷板机的辊筒,消除毛刺、焊疤、飞渣等,保持辊筒光滑。
准备好各种工具、工装,如压头靠模板、拉紧器、大锤、撬棍、样板等。
按照卷板机承载能力选择卷板机。
、卷板操作
卷板机在开动之前,操作人员应先检查各部位及注油管路防护装置有无损坏,再进展分钟空载运转检查,各部运转正常方可进展工作。
不要在卷板机上锤击、施焊各种工作,以免损坏辊子外表及设备,或发生连电而造成设备事故。
筒体板料上所有毛刺都必须清理干净。
筒体外表不允许存在任何凸出的缺陷及杂物,拼接焊缝应尽量及母材外表平齐,焊缝高出母材超出以下值时应打磨。
当钢板厚<时,焊缝高出母材,>时,焊缝高出母材1。
卷制不锈钢及有色金属筒体,应在钢板外表垫胶皮或牛皮纸。
卷制圆形筒体时应认真调整上、下辊筒间距。
[〔++〕()]
式中:
上下辊中心线的垂直相离:
:
滚制时弯曲半径;
:
筒体壁厚
:
两下辊中心距之半
:
上轴半径
:
下轴半径
〔上式中为每次弯曲半径,未计回弹〕。
图2.4
预弯
预弯宽度不应小于卷板机下辊中心距之半。
压头使用弯模在压机上预弯,也可以在卷板机上用压头靠模板预弯,压头靠模板预弯时应符合下述条件:
压头靠模板厚度不小于两倍筒体厚度;
弯板负荷不大于卷板机能力的倍。
卷板机注意毛坯放正,使筒体中心线及轴筒平行,防止轴向错边。
卷制大直径、薄钢板时应借助吊车协助操作,操作人员不应站在被卷曲工件的正面。
卷制较厚板时,要增加滚圆次数,不要急于求成。
锥体的卷制
锥体坯料板头不宜过长。
锥体的卷制可采用分区滚制法或小口减速法。
分区滚制法,将坯料等分为假设干个区域分别滚制最后矫形。
小口减速法,要锥体小口及卷板机头之间做一靠模,利用摩擦减低小口的滚边速度,到达锥体卷制成型。
弯卷时应分别用样板检查大、小口曲率。
、校圆
筒体焊接后应进展校圆,可以在卷板机上完成。
尽量减少锤击校圆。
使用锤击校圆必须加垫板或垫平锤,严防锤坑。
使用卷板机校圆时应根据经历或参考节提供的算式,调整上下辊中心距,反复矫正焊缝附近,然后滚卷整个筒体,使曲率均匀一致,最后逐步卸载。
筒体的纵缝无损探伤应要校圆后进展。
校圆后筒体尺寸形状误差的允许值如下:
同一断面上最大直径及最小直径之差〔〕应符合下述规定。
内压筒体<%且不大于25mm。
当被检断面及开孔中心的距离小于开孔直径时,那么断面最大直径及最小直径之差,应不大于该断面内径的及开孔直径的之和,且不大于25mm。
C换热器,壳体按的规定。
因焊接在环向形成的棱角E用弦长等于是/且不小于300mm的内样板或外样板检查〔见图〕,不大于〔δ/+〕且不大于5mm,因焊接在轴向形成的棱角〔见图〕用长度不小于300mm的检查尺检查,其E值不得大于〔δ〕,且不大于5mm。
D且不小于300mmD且不小于300mm
样板
样板
δδ
A、B类焊缝对口错边量,应符合表的规定,复合钢板对口错边量不大于钢板复层厚度的%,且不大于2mm。
表
按厚度的名义厚度δ
按焊缝类
≤
<δ≤
<δ≤
<δ≤
>
≤4δ
≤
≤
≤
≤δ且不大于
≤/δ
≤/δ
≤
≤/δ
≤/δ且不大于
校圆后外圆周长误差应符合表规定,同一筒体各筒节周长差应符合表规定。
表 校圆后筒体外圆周长公差
公称直径
<
>
-
>
-
≥
-
≥
≥
周长差
换热器
+
-
+
-
+
-
/
/
/
一般容器
±
±
±
±
±
±
表 同一筒体各筒节外圆周长差
筒体板厚
≥
周长差
筒体端面的不平度不大于1.5mm,壳体直线度允差Δ除图样另有规定外,应不大于筒体长度的‰,当直立容器的壳体长度超过30m时,其筒体直线度允差不大于〔〕
筒体内外外表应符合以下要求:
.无机械损伤、毛刺、飞溅物等,焊疤应磨平,对严重的锋利伤痕应进展修磨,并使修磨范围内的斜度至少为,筒体外表缺陷的深度不得超过名义厚度δ的%,且不大于2mm,不锈耐酸钢容器的外表如有局部伤痕,刻槽等影响耐腐蚀性的缺陷应予修磨,修磨深度不应超过钢板厚度〔复合钢板指复层厚度〕的负偏差值。
.筒体各种标记:
材质编号中心线、环向基准圆线均应保持清晰及永久性。
筒体纵缝组对工艺
1、组对时,坡口间隙、错边量、棱角度等应符合规定。
具体尺寸允差见附表一。
2、组对时尽量使用枪、手位葫芦等,少用工卡具,以防止机械损伤。
不锈钢、钢、低温钢及σ≥的高强钢所用工卡具撤除后,母材经补焊后打磨平滑用永久记号笔做好标记,以进展磁粉或着色检测。
3、工卡具、吊耳、等须统一设置,及筒体同材质,组对时须严格控制错边、间隙,并保证错边、间隙的均匀一致性。
4、立位焊接的筒体及分片到货的锥段、椭圆封头、球形封头纵缝组对须在经找正水平的平台上〔或拼接的钢板〕上进展,以保证圆度及端面不平度。
锥段组对纵缝间隙允许有的不一致性。
5、封头组对时,保证瓜瓣下口平齐,控制理论拱高,组对间隙均匀。
6、严禁强力组对,点固焊缝间距和厚度要符合规定,严禁对材料外表进展烧烤。
7、焊接接头拘束度大时,推荐采用抗裂性能更好的焊条施焊。
8、点固焊缝不得有裂纹,否那么应去除重焊。
如存在气孔、夹渣时亦应去除。
9、熔入永久焊缝内的定位焊缝两端应便于接弧,否那么应予修整。
10、有预后热要求时,严格执行工艺。
纵缝点焊预后热采用氧—乙炔火焰加热,时间不得少于,保证温度,保证点焊焊缝长度≥和厚度,间距,防止焊前开裂。
11、无法或回床困难的筒体纵缝组对时须预留反变形。
12、临时工卡具、吊耳的焊接须采用和筒体一样的焊接工艺及焊材。
附表一
壳体
项目
φ×δ
样板弦长
≥,且不小于300mm
错边量
纵缝
≤1mm
环缝
δ<10mm,错边量≤δ
δ≥10mm30mm,错边量≤2mm
δ>30mm,错边量≤
棱角(焊前焊后)
焊前≤δ,焊后≤δ,且不大于
端面不平度
≤‰,且≤2mm
圆度
≤,且≤25mm〔卷制管≤,且≤5mm〕
相邻筒节周长偏差
≤6mm
此工艺规程同时适用于筒体、封头、裙座筒体、锥段、卷制接收
筒体环缝组对工艺
、组对前应进展相关数据的检查
检查材料移植标记及号料标记及筒节外观质量:
磕碰及其它机械损伤和变形情况等
检查几何尺寸:
如椭圆度、焊接坡口型式及尺寸、直边高度等。
核验及其相接的筒节互相吻合的尺寸。
检查外观质量:
如有无起包、重皮、起皱、壁厚拉薄及其它外伤。
检查筒节的几何尺寸:
包括椭圆度、长度、周长、端面斜度、焊接坡口型式及尺寸等。
当操作者发现零部件不符合要求时,应及时向有关人员反映,要求做到不合格的零件不组装。
、工具及工装准备
根据工作内容不同,准备好必要的工具和工艺装备:
如大锤、扁铲、撬棍、盘尺、板尺、角尺、划规、砂轮机、钢丝绳以及胀管器等。
、根据设备产品不同,选好装配场地,组织好各配合工种〔气焊、电焊、行车等〕,然后进展装配操作。
、组对应尽可能在无约束或低应力状态下进展,尽量防止强行组对,引出板、产品焊接试板不应锤击撤除。
、组对时,纵缝布置方位按排板图给出的方位,坡口间隙、错边量、棱角度等应符合规定。
具体尺寸允差见附表二。
、组对时尽量少用工卡具,确需点焊码铁等工卡具时,应尽量防止机械损伤。
必需焊接工卡具、吊耳时须统一设置,及筒体同材质,不锈钢筒体组对用工卡具可用碳钢,但必需在筒体及工卡具间加薄不锈钢板,减少对母材的损伤。
、组对时必须附加吊耳、吊环等,其材质性能及其点焊,焊接工艺要求应和元件一样或相似。
、组装点焊用的焊条材质规格、点焊长度、间距等均按焊接工艺执行,点焊次序应在径向对称位置依次点固后再按规定的点焊长度和间距依次点焊。
附表二
壳体
项目
φ×δ
样板弦长
不小于〔直尺〕
错边量
纵缝
≤1mm
环缝
δ<10mm,错边量≤δ
δ≥10mm30mm,错边量≤2mm
δ>30mm,错边量≤
棱角(焊前焊后)
焊前≤δ,焊后≤δ,且不大于
端面不平度
≤‰,且≤2mm
圆度
≤,且≤25mm
壳体直线度
〔记入封头、裙座等〕
除图纸另有规定外,壳体直线度允差应大于壳体长度的‰;当直立容器的壳体长度超过时,其壳体直线度允差应不大于.
直线度
〔分段交货的容器〕
除图纸另有规定外,任意内的筒体直线度允差为;当筒体长度<时,直线度允差为,筒体长度>时,直线度允差为。
、筒体、封头组装
采取立式组装或卧式组装方法,要根据现场的具体情况决定,一般小直径的筒节,采用卧式组装,大直径的筒体采用立式组装;
当吊装筒体时,两吊钩夹具卡紧点之间,应用管子支撑以防筒体椭圆。
夹具必须卡紧,以防脱落。
在吊装封头时,根据工件轻重不同在顶部中心焊不同规格的吊耳,以便挂钢丝绳,吊耳必须焊牢。
吊耳应及容器同材质、同工艺焊接。
焊前应去除坡口及其焊缝两侧20mm范围内〔以离坡口边缘距离计〕的油污、铁锈、氧化物及其它有害杂质。
铸钢件应打磨铸钢外表使其显露金属光泽。
对不锈钢筒节,焊前尚需在焊缝两侧150mm范围内均匀刷白粉浆。
筒节组对前要将各筒节的A、B类焊缝按组装位置顺序编号,按排幅员组对。
装配周长不同的筒节时要使错边量沿周长均匀分布,局部对口错边量不准超差。
每点焊两节筒体后,在完全施焊前要测量直线度,直线度的测量应采用通过中心线的水平和垂直面〔即在组装后筒体两端离筒节口50mm处且离纵焊缝距离不小于100mm处,沿圆周、、、四个部位拉细钢丝测量〕进展测量,根据具体情况对直线度及时进展调整。
对用设备法兰连接的塔体及容器壳体,当法兰端面至开孔中心700mm距离内有大接收和焊接件时,为防止法兰密封面变形,应在塔及容器壳体内加衬圈〔衬圈大小要根据设备的大小和壁厚确定〕,接收和补强圈或焊接件先及塔体〔容器〕壳体焊接好,然后再将设备法兰及塔体〔容器〕壳体进展装配。
并拧紧螺栓后再进展联接处的焊接,焊后卸下衬圈。
相邻筒节纵环焊缝严禁采用“十”字形焊缝。
两相邻筒节上的两相邻纵缝或封头焊缝端点及筒体纵焊缝距离,应根据焊缝条数及管口方位按丁字焊合理分布。
最小距离应大于钢材厚度δ的3倍且不小于100mm。
筒体对口错边量应符合-钢制压力容器及铆装工艺卡要求。
对焊接形成的棱角度E不得大于+2mm,且不大于5mm。
检查时,纵焊缝用弦长等于D且不小于300mm的外样板或内样板检查,环焊缝应用长度不小于300mm的直尺检查。
在本体上焊接的工、卡具、临时吊耳等,组装完成后,应将其撤除,焊疤及残留物应磨平,修磨处的深度不得超过名义厚度的%,且不大于2,修磨范围的斜度至少为。
超出要求的允许补焊,但要按有关工艺要求进展。
容器组装完成后,检查壳体的圆度;同一断面上最大直径及最小直径之差允值如下。
内压容器≤%D且≤25mm。
如果被检查断面在开孔中心一倍开孔内径范围内时,那么≤%D且≤25mm。
〔注:
为开孔内径〕
有装配间隙要求的容器,内径允差如下表:
长度〔〕
≤
<≤
<≤
<≤
<
允差〔〕
±
±
±
±
±
图面有要求的容器按照图面要求。
外压容器用样板检查并按规定查图表。
组装后筒体直线度允差如下:
6.一般压力容器应不大于壳体总长度的‰〔注:
壳体总长度不含封头尺寸〕。
当壳体长度超过时,按规定。
〔即:
任意长圆筒段偏差不得大于;圆筒长度≤时,偏差≤‰,当>时,偏差≤‰〕
外圆周长允差
7.1一般压力容器,当设计外径≤650mm,周长允差±5mm,
当设计外径>650mm,周长允差为±周长;
1)、对于内件较多的容器和塔器,组对封头端的筒节一端需将外部四条心线用角尺引入筒节内部并用样锪或记号笔做好标记。
2)、严禁强力组对,点固焊缝间距和厚度要符合规定,严禁对材料外表进展烧烤。
3)、焊接接头拘束度大时,推荐采用抗裂性能更好的焊条施焊。
4)、点固焊缝不得有裂纹,否那么应去除重焊。
如存在气孔、夹渣时亦应去除。
5)、熔入永久焊缝内的点固焊缝两端应便于接弧,否那么应予修整。
6)、有预后热要求时,严格执行工艺。
环缝点焊预热采用氧—乙炔火焰加热,时间不得少于,保证温度,保证点焊焊缝长度≥150mm和厚度16mm,间距500mm,防止焊前开裂。
7)、点焊及临时工卡具的焊接须采用和筒体一样的焊接工艺及焊材。
接收法兰组焊工艺
1、领料
1.1接收法兰必须有材料确认标记,并经材料质检员验收合格,方可领料。
1.2管材须具有合格质保书,标记齐全。
1.3图样及标准规定进展超探的材料应检验合格。
1.4三类容器用材料须复验合格,母材抽样复验须合格,否那么不得领料。
1.5法兰订货前必须考虑设计的特殊备注,如法兰内径,以保证和系列薄壁、厚壁接收相匹配。
1.6不锈钢管外表下料前应铺设保护膜。
2、号料
2.1按图纸规定的伸出长度减去法兰厚度进展接收划线、号料,接收须考虑马鞍口形状和接收焊接型式〔内伸10mm或平齐〕,并预留8mm机加工余量,按理论最长点尺寸保证。
注意图纸中接收外伸高度、内伸高度的解释。
注意设计对标准人孔组合件的特殊备注,如锥段上人孔接收须加长。
2.2内伸式接收端部采用气割下料时需预留3mm的余量待切割后再用打磨等方法去除。
3、标记移植
3.1按附图四标移接收统一内容,包括材质、质保书号。
4、下料
4.1切割或上车床加工接收。
4.2不锈钢接收下料切割须采用等离子切割机进展。
5、坡口加工
5.1切割或上车床加工接收坡口。
5.2不锈钢接收坡口切割须采用等离子,再上车床加工或用不锈钢专用砂轮片打磨。
5.3切割的坡口必须磨去氧化层、渗碳层、淬硬层,直至露出金属光泽。
附图四
6、环缝组对
6.1法兰领料进后,要用石棉板将法兰密封面保护好。
人孔、大型卷制接收等安装过程人须频繁出入的管口法兰,石棉板内圆直径比密封面内径小20mm,石棉板外圆直径比法兰外径大20mm;其余管口法兰用整圆板,外圆直径比法兰外径大20mm。
6.2引弧板、引出板不应锤击撤除。
6.3组对尺寸允差见附表三。
6.4组对时尽量少用工卡具,以防止机械损伤。
不锈钢、钢、低温钢、σ≥的高强钢所用工卡具撤除后,母材经补焊后打磨平滑,并用永久记号笔做好标记,以进展磁粉或着色检测。
6.5工卡具、吊耳等须统一设置,及筒体同材质,减少对母材的损伤。
6.6对于先切割出马鞍型口的接收,在放样前就需划出对满意线,并以心线为马鞍的底部;组对接收时此心线必须相对法兰螺栓孔跨中。
如以下列图所示:
6.7组对前须找正筒节圆度,并测量端口周长,根据周长进展修复、调整。
组对时须严格控制错边、间隙,并保证错边、间隙的均匀一致性。
6.8严禁强力组对,定位焊缝间距和厚度要符合规定,严禁对材料外表进展烧烤。
6.9焊接接头拘束度大时,推荐采用抗裂性能更好的焊条施焊。
6.10定位焊缝不得有裂纹,否那么应去除重焊。
如存在气孔、夹渣时亦应去除。
6.11熔入永久焊缝内的定位焊缝两端应便于接弧,否那么应予修整。
6.12有预后热要求时,严格执行工艺。
环缝点焊预热采用氧—乙炔火焰加热,时间不得少于,保证温度,保证点焊焊缝长度≥150mm和厚度16mm,间距500mm,防止焊前开裂。
6.13点焊及临时工卡具、吊耳的焊接须采用和接收一样的焊接工艺及焊材。
6.14接收环缝组对前须将弯头圆度调整处理合格,圆度≤3mm,假设因代用接收和法兰内壁按标准就不平齐,须将接收或法兰内壁上卧车削薄至平齐,以保证氩弧焊焊缝质量。
6.15做好法兰密封面的保护工作,摆放法兰时加垫小方木块,制造过程密封面涂上黄油。
6.16预制过程检查法兰螺栓孔跨中〔对中〕时,将石棉板拆卸;交给焊工焊接时,石棉板必须和法兰拧紧在一起;石棉板损坏后,须随时更换。
6.17浮头式换热器的浮头盖及浮头法兰组对时,需按图样尺寸的高度点焊上定位钢板,然后将浮头盖吊入法兰内圈,调整好四周间隙,加以点焊。
附表三
法兰
规格
接收规格材质
坡口角度
钝边
错边
不直度
及筒体组装允差
水平(垂直)
端面距离
无缝接收、法兰〔单侧〕坡口°;卷制接收〔