地下矿用汽车车架的动态特性研究.docx
《地下矿用汽车车架的动态特性研究.docx》由会员分享,可在线阅读,更多相关《地下矿用汽车车架的动态特性研究.docx(16页珍藏版)》请在冰豆网上搜索。
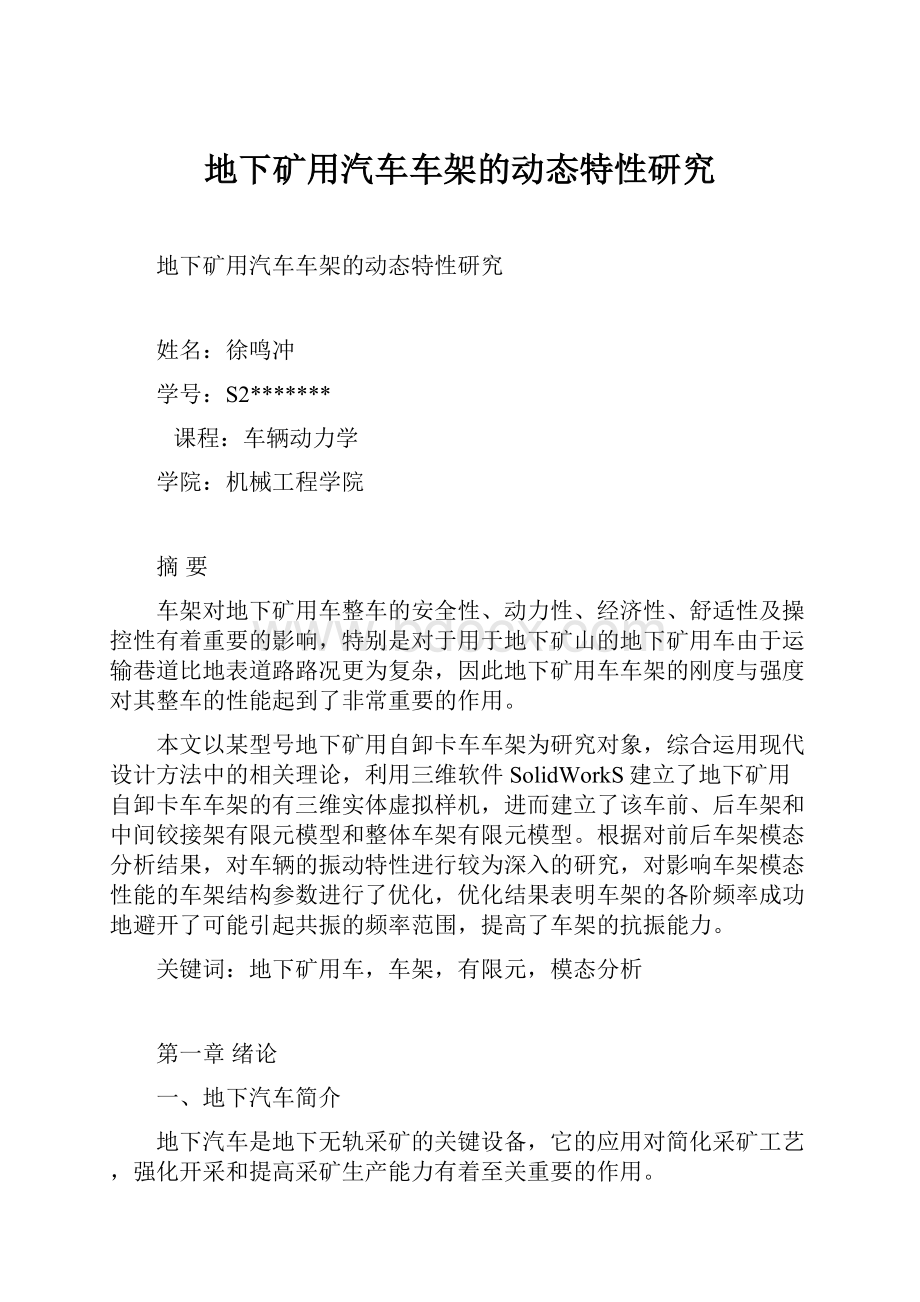
地下矿用汽车车架的动态特性研究
地下矿用汽车车架的动态特性研究
姓名:
徐鸣冲
学号:
S2*******
课程:
车辆动力学
学院:
机械工程学院
摘要
车架对地下矿用车整车的安全性、动力性、经济性、舒适性及操控性有着重要的影响,特别是对于用于地下矿山的地下矿用车由于运输巷道比地表道路路况更为复杂,因此地下矿用车车架的刚度与强度对其整车的性能起到了非常重要的作用。
本文以某型号地下矿用自卸卡车车架为研究对象,综合运用现代设计方法中的相关理论,利用三维软件SolidWorkS建立了地下矿用自卸卡车车架的有三维实体虚拟样机,进而建立了该车前、后车架和中间铰接架有限元模型和整体车架有限元模型。
根据对前后车架模态分析结果,对车辆的振动特性进行较为深入的研究,对影响车架模态性能的车架结构参数进行了优化,优化结果表明车架的各阶频率成功地避开了可能引起共振的频率范围,提高了车架的抗振能力。
关键词:
地下矿用车,车架,有限元,模态分析
第一章绪论
一、地下汽车简介
地下汽车是地下无轨采矿的关键设备,它的应用对简化采矿工艺,强化开采和提高采矿生产能力有着至关重要的作用。
地下汽车与一般汽车就其功能来看,都是运输货物,但二者在运行经济性上却大不相同。
一般汽车是为公路运输而设计的,它的底盘较高,自重大,转弯半径大。
由于一般汽车为后轿驱动,容易在井下恶劣的道路状况下产生轮胎打滑现象,因而轮胎磨损加剧,使用寿命短。
二、矿用车车架研究方法
车架是汽车的承载基体,不仅承担发动机、底盘和牵引货物的质量,而且还要承受汽车行驶过程中所产生的各种力和力矩。
因此,其强度不仅关系到整车能否正常行驶,而且还关系到整车的安全性。
对车架设计的要求是:
在保证足够的强度、刚度和稳定性下,尽可能达到质量轻、形状合理,并最大限度地减缓过渡区的应力集中。
近年来,国内外许多学者对车架的有限元分析进行了大量的研究。
矿用自卸卡车车架所受的载荷分为静载荷和动载荷两种,对车架的强度计算
方法主要有以下三种:
1、经典力学法
2、经验类比法
3、计算机仿真计算
第二章车架有限元建模
一、车架的要求
1、有足够的强度。
保证在各种复杂受力的情况下车架不会破坏。
要求有足
够的疲劳强度,保证汽车大修里程内,不至于有严重的疲劳损伤。
2、有足够的弯曲刚度。
保证汽车在各种复杂受力的使用条件下,固定在车
架上的各总成不至因为变形而早期损坏或失去正常的工作能力。
3、有适当的扭转刚度。
当汽车行驶于不平路面时,为了保证汽车对路面的
不平度的适应性,提高汽车的平顺性和通过能力,要求具有合适的扭转刚度。
通
常要求车架两端的扭转刚度大些,而中间部分的扭转刚度适当小些。
4、尽量减轻质量。
由于车架较重,对于钢板的消耗量相当大。
二、地下矿用车车架的结构简况及设计参数
该型号地下矿用自卸卡车在国外无同类机型可供参考,在收集研究国外各种型号的地下汽车的性能参数、结构特点等样本与资料,结合我国大多数地下无轨矿山生产现状及大厂矿务局对研制地下汽车的技术要求,确定全部选用国产件自行设计而成。
地下矿用自卸卡车采用整体铰接式车体结构,四点悬挂,低污染柴油机,液力机械传动,司机室前置侧座,双桥结构轮胎的总体设计方案。
车架的模型如图2-1所示,其长宽高分别为:
8290x2326x837。
其结构主要由前车架,中间铰接架和后车架三部分组成,前车架和中间铰接架由中心枢轴连接,可以进行横向转动,后车架和中间铰接架由轴承连接,可以进行周向转动。
图2-1原车架模型图
为提高车架的稳定性,前车架前部为车架保护杠,中部由65#角钢和18#槽钢支撑,后车架前部,中部和后部各有一根连接横梁,横梁由四块厚度为16mm的钢板组成。
车架的整体结构由不同厚度的钢板通过焊接组成,主体结构为四根纵梁和六根横梁,通过立梁连接。
车架连接耳板、纵横梁连接处以及立梁与纵梁连接处均用不同尺寸的加强筋加强。
三、车架有限元模型
由于车架模型的复杂性,以及分析需要,分别建立了四个车架的有限元模型,分别为:
整车车架网络图(图2-1),前车架网格图(图2-2),后车架网格图(图2-3),中间铰接架网格图(图2-4)
图2-1整车车架网格图图2-2前车架网格图
图2-3后车架网格图图2-4中间铰接架网格图
第三章车架动态特性研究
一、模态分析方法
本文研究的模态分析是指以振动理论为基础、以模态参数为目标的分析方法。
更确切地说,模态分析是研究系统物理参数模型、模态参数模型和非参数模型的关系,并通过一定手段确定这些系统模型的理论及其应用的一门学科。
计算模态分析实际上是一种理论建模过程,主要是运用有限元法对振动结构进行离散,建立系统特征值问题的数学模型,用各种近似方法求解系统特征值和特征矢量。
由于阻尼难以准确处理,因此通常均不考虑小阻尼系统的阻尼,解得的特征值和特征矢量即系统的固有频率和固有振型矢量。
二、模态分析理论基础
汽车车架是一个多自由度结构,设车架已按某种方式离散化了,离散后车架结构是一个n自由度的系统。
令{u}为广义坐标的位移列阵,[K]、[M]和[C]为与{u}相对应的刚度矩阵、质量矩阵和阻尼矩阵,根据达朗贝尔原理,只要在车架所受的外力中加入惯性力,就可以建立动力学方程。
即车架的振动方程:
对于无阻尼的自由振动系统:
由于弹性体的自由振动总可以分解为一系列的简谐振动的迭加,因此可以设上式的解为:
带入方程得:
由线性代数理论可知,要使方程(4-4)有非零解的充分必要条件是:
。
由于结构离散后有n个自由度,则「K」和「M」都是n阶方阵,解方程即可得到结构的n阶固有频率和相应的主振型。
三、动态性能的评估
汽车在行驶过程中,会受到由车轮传来的不平路面的激励和发动机工作时曲柄连杆活塞产生的激励。
为了减小汽车的振动,提高驾乘舒适性,就要使车架的动力学性能与发动机、悬架以及运行工况相匹配。
在汽车发动机和悬挂一定的情况下,车架各阶模态必须最大限度地避免与发动机和路面激励频率之间的共振,其一是车架模态频率应尽可能避开由车轮传来的路面激励的频率范围,其二是车架的模态频率应该避开发动机经常工作的频率范围。
1、路面激励对车架动态性能的影响
汽车在行驶过程中,乍架要受到由车轮传来的路面不平度的激励。
由路面不平度激励引起车架的振动,与汽车的行驶速度有关,当汽车以速度v(m/s)行驶在路面不平度的空间频率为}(m-})的路面上时,输入的时一间频率f(Hz)是。
和v的乘积即
路面激励频率与车架结构的模态频率的共振车速为:
为防止道路激励频率引起车架的共振,车架的一阶频率f需满足如下要求:
该型号汽车常用车速空载时为18km/h,行驶路面为未铺装路面,
满载时车速一般为5km/h,
而路面激励是通过油气弹簧传到车架上的,油气弹簧具有缓解、吸收因路面不平传递给车架的振动和冲击的能力,所以实际的f值可以比计算值更低。
2、发动机激励对车架动态性能的影响:
发动机是汽车振动的主要激励源之一,缸内气体产生的爆发压力、运动产生的惯性力和惯性力矩通过发动机和车架之间的连接支撑传递到车架上。
由于本矿车所用的发动机是八缸四冲程风冷柴油机,发动机的激振频率取决于发动机的转速及气缸数,计算公式为:
因此对于该发动机,z=8,z=4。
当怠速转速n=800r/min时,怠速激励频率儿为53.33Hz。
常用车速下发动机转速万=2300r/min,所以相应的一阶激励频率为153.33Hz以下。
四、车架模态分析及结果计算
本文所分析的车架主要由前车架、中间铰接架、后车架组成,其中前车架和后车架是对结构的动力影响最大,因此本文分别对前车架和后车架的模态进行了分析。
1、前车架模态分析
根据上述模型进行自由模态求解,提取了车架的前16阶频率,忽略其中前六阶频率为0的模态,各阶频率值如表所示。
从图表可以看出,第七阶模态是33.997Hz,主要是弯曲模态,最大变形量发生在前车架。
第八阶模态为42.302Hz,以扭转模态为主。
第九阶模态为44.770Hz,主要为弯曲模态,最大变形量发生在车架的前端,车架的前端振幅比较大。
前三阶模态属于低阶模态。
后七图中的模态属于高阶模态,从图中可以看出,第十五阶模态是高阶弯曲模态,频率为145.83Hz,最大变形量发生在车架中部柴油机支座位置。
而第十六阶模态是高阶扭转模态,频率为157.72Hz,最大变形量发生在车架L形筋梁位置,因此如果激励频率等于这个频率时,车架就会受到很严重的扭曲,这是需要避免的。
2、后车架模态分析
根据上述模型进行自由模态求解,提取了车架的前16阶频率,忽略其中前六阶频率为0的模态,各阶频率值如表所示。
从图表可以看出,前四阶模态为车架的低阶模态,最大变形均发生在车架后端;其中第七阶模态为侧向扭转模态,最大变形出现在车架尾部,这与汽车在凹凸路面的行使工况非常相似,如果激振频率接近该阶模态频率,则较易发生变形破坏,因此设计时应避免路面激振频率与该阶频率重合。
第10-14阶模态属于二阶模态,多表现为较复杂的弯扭变形。
第15,16阶模态为车架的高阶模态,车架变形较大,弯扭情况复杂,但是其属于较高阶模态,对车架的影响并不严重。
五、模态分析结果
由上述分别对前车架、后车架和中间铰接架的模态分析可知:
前车架、后车架以及中间铰接架的最低模态频率分别为33.997Hz,47.109Hz远高于f的值,即路面激励对车架的影响较小。
从模态分析结果可知,车架的模态频率存在一定的不足之处,主要表现在:
前车架第十阶频率为52.421Hz,与发动机怠速频率53.33Hz非常接近,极易引起共振,后车架第十三阶模态频率为151.60Hz,与发动机常用转速下频率153.33Hz比较接近,较易发生共振,因此需要分别对前后车架做相应的改进优化。
第四章车架结构优化设计
一、优化设计概述
优化设计是一门新发展起来的科学,也是一项新技术,在工程设计的各个领域得到了广泛应用。
优化设计的理论基础是数学规划,采用的工具是电子计算机。
能使各种设计参数向更优的方向进行逼近,直至找到一个尽可能完善的或最合适的方案。
二、优化设计的数学模型
一个优化问题必须要有一个数学模型来描述,这种描述必须能够把类似问题的基本目标及其所受的各种限制和约束列举清楚,在各种设计变量和参数之间必须保持应有的、严格的逻辑结构和协调关系,否则无法通过计算。
一个优化问题的数学模型有三个要素:
设计变量、目标函数、约束条件。
优化设计的描述是:
给定系统描述和目标函数,选取一组设计变量及其范围,求设计变量的值,使得目标函数最小(或者最大)。
一种典型的数学表达式为:
1、设计变量
在优化设计中不断变化的一组参数,叫做设计变量。
设计的变量数目越多,可能的设计方案也就越多,因而可变可选择的余地也就越大,计算量也随之相应增大,因而应当尽量减少设计变量的总数,把那些变化不大的影响较小的变量作为给定条件或转化为约束条件予以必要的限制和保证。
2、目标函数
在确定的设计思想指导下,由设计变量表达的,用来评价所追求指标的函数,称为目标函数。
目标函数是根据设计的要求,按着设计准则建立起来的,这些准则可以是:
距离、速度、位移、体积、受力、重量、效率、能耗、成本等等。
在优化设计发展的初期,多以投资费用和利润作为目标函数,所以目标函数也称为评价函数。
3、约束条件
在优化设计过程中,设计变量不断改变其取值,以其达到目标函数的最小值,但设计变量的改变和取值要受到一系列的限制和约束,如零件设计中的强度、刚度、失稳条件等都要满足,以及运动学参数中的连杆构成条件,运动条件,传动角条件等。
此外,设计变量在该设计中的取值范围,上下边界也都必须有一定限制。
三、前车架的模态优化:
1、目标函数与状态变量的确定:
前车架模态不足之处主要表现在第十阶频率与发动机怠速频率非常接近,为了防止发生共振导致车架变形过大而产生破坏,优化的目的是要提高前车架第十阶频率,使第十阶频率远离发动机怠速频率3Hz为目标,以结构总质量最小为目标函数。
2、设计变量的确定
为了计算和优化的方便,首先对前车架中间的18#槽钢和65#角钢进行简化处理,18#槽钢简化为宽180mm,高70mm,厚度为1Omm的C形横梁,65#角钢简化为30X30X4的L形横梁。
选择对车架模态影响比较重要的五个变量进行优化:
1)连接耳板厚度;2)立梁板厚;3)纵梁厚度;4)L形筋梁厚度;5)槽钢厚度。
3、约束条件的确定
为了使前车架模态频率避开发动机怠速频率,需要对第十阶模态频率进行约束,以避开怠速频率3Hz为宜,故约束第十阶频率范围为57-70Hz.
4、优化前后后尺寸对比:
从图表可以看出,前车架模态频率基本避开了发动机怠速频率范围,其中第九阶频率和第十阶频率与发动机怠速频率比较接近,但是差值都在3Hz以上基本能够避免共振的发生。
前车架质量有了大幅度的下降,从优化前的1560.9Kg降低到1237.2Kg,降低了20.7。
车架整体尺寸变化明显,其中连接耳板和纵梁厚度变化最大,基本以变量下限取值,槽钢尺寸也有很大改变,需重新选择槽钢型号。
四、后车架模态优化
1、目标函数与状态变量的确定:
车架模态不足之处主要表现在第13阶频率与发动机常用转速下频率非常接近,较易发生共振,为了防止共振的发生,优化的目的是要降低后车架第13阶频率,使第13阶频率远离发动机常用转速下频率3Hz为目标,同时控制低阶模态尤其是第七、八阶模态不与发动机怠速频率发生共振,以结构总质量最小为目标函数。
2、设计变量的确定:
选择对后车架模态影响比较重要的五个变量进行优化:
1)立梁板厚;2)纵梁板厚;3)横梁板厚;4)第一与第二横梁宽度;5)第三横梁高度。
3、约束条件的确定
4、优化结果分析
从优化后图表可以看出,后车架模态频率基本避开了发动机怠速频率范围,同时也避开了常用转速频率范围,其中低阶模态全部大于发动机怠速频率,达到了化的目的。
车架质量有了大幅度的下降,从优化前的1173.3Kg降低到882.83Kg,降低了24.8。
车架整体尺寸变化明显,其中连接筋板、立梁厚度、第一、二横梁宽度变化最大,基本以变量下限取值。
车架的模态优化并没有考虑对车架整体刚强度的影响,因此有必要对尺寸优化后的车架重新进行静态分析。
第五章总结
本文针对某型号地下矿用自卸卡车车架的结构特点,利用有限元软价ANSYS对汽车车架进行了模态分析和结构轻量化设计,主要工作如下:
1、建立车架模型:
地下汽车车架主要由前车架、中间铰接架和后车架组成,本文分别建立了整体车架的有限元模型,前车架有限元模型、后车架有限元模型和中间铰接架有限元模型。
2、针对前车架、后车架和中间铰接架的有限元模型,分别对前后车架和中间铰接架进行模态分析,分析结果表明:
中间铰接架模态频率分布合理,抗振能力比较强:
前、后车架模态频率存在不足之处,具体表现为,前车架的第十阶模态频率和发动机怠速频率非常接近,后车架第十三阶模态频率与发动机常用转速下频率比较接近。
如果车架结构得不到改善,就会发生共振,导致车架破坏。
3、根据前、后车架的模态分析结果,找出车架在振动方面的不足之处,分别对影响前、后车架模态比较重要的尺寸进行了优化,优化结果表明车架的各阶频率成功避开了可能引起共振的频率范围,提高了车架的抗振能力。
参考文献
[1].杨忠炯.地下矿用自卸卡车的经济性与发展趋势[J].矿用研究与开发,1994.2
[2].高云凯.汽车车身结构分析[M].北京:
北京理工大学出版社,2006:
116148
[3].李梅龙,108t自卸车车架强度分析及结构改进[J],矿山机械,1999.3
[4].靳晓雄,张立军,江浩.汽车结构分析[M].上海:
同济大学出版社,2002:
134154
[5].靳晓雄,张立军.汽车噪声的预测与控制[M[.上海:
同济大学出版社,2004:
2741