先进的蒸汽转化制氢工艺.docx
《先进的蒸汽转化制氢工艺.docx》由会员分享,可在线阅读,更多相关《先进的蒸汽转化制氢工艺.docx(21页珍藏版)》请在冰豆网上搜索。
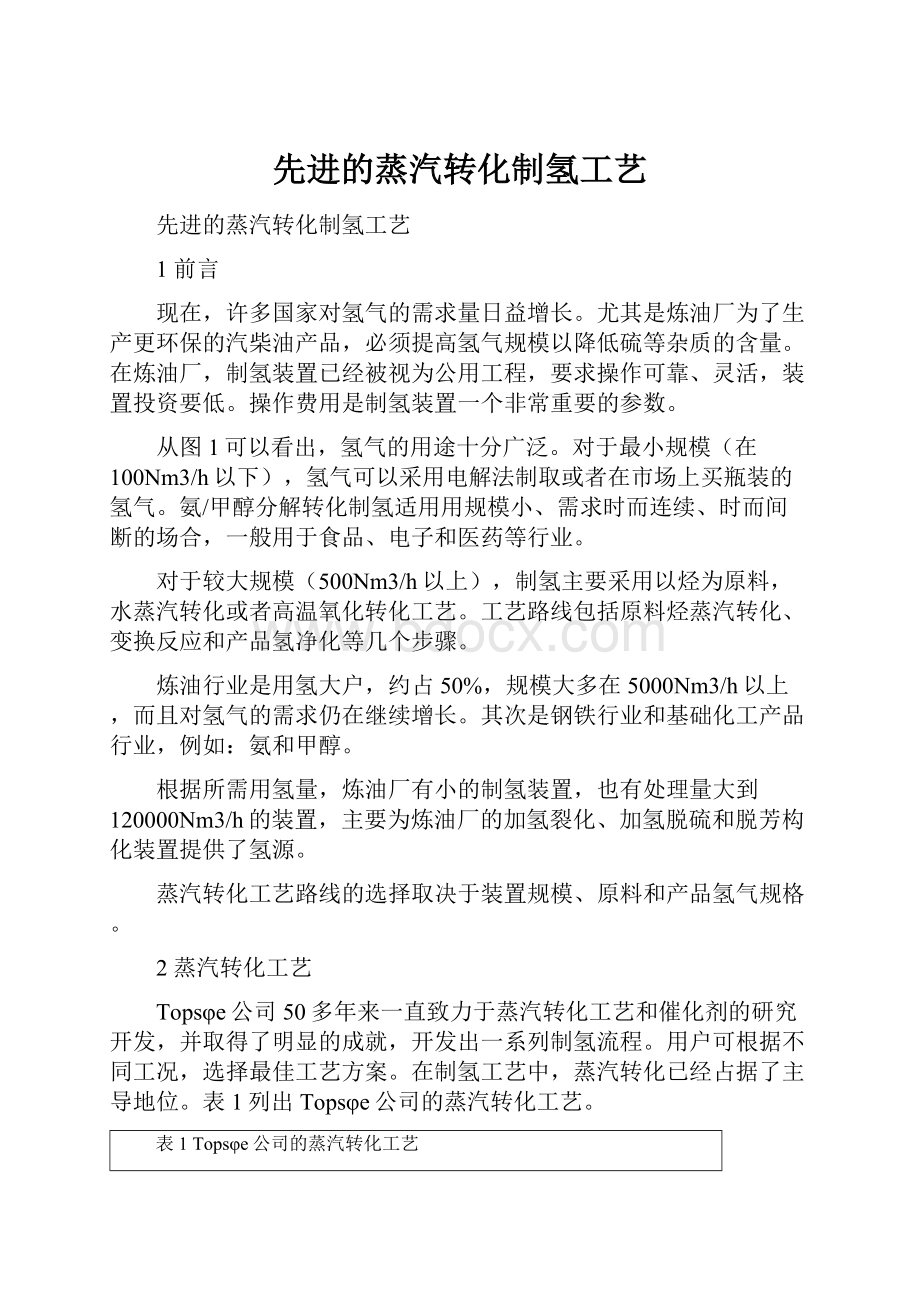
先进的蒸汽转化制氢工艺
先进的蒸汽转化制氢工艺
1前言
现在,许多国家对氢气的需求量日益增长。
尤其是炼油厂为了生产更环保的汽柴油产品,必须提高氢气规模以降低硫等杂质的含量。
在炼油厂,制氢装置已经被视为公用工程,要求操作可靠、灵活,装置投资要低。
操作费用是制氢装置一个非常重要的参数。
从图1可以看出,氢气的用途十分广泛。
对于最小规模(在100Nm3/h以下),氢气可以采用电解法制取或者在市场上买瓶装的氢气。
氨/甲醇分解转化制氢适用用规模小、需求时而连续、时而间断的场合,一般用于食品、电子和医药等行业。
对于较大规模(500Nm3/h以上),制氢主要采用以烃为原料,水蒸汽转化或者高温氧化转化工艺。
工艺路线包括原料烃蒸汽转化、变换反应和产品氢净化等几个步骤。
炼油行业是用氢大户,约占50%,规模大多在5000Nm3/h以上,而且对氢气的需求仍在继续增长。
其次是钢铁行业和基础化工产品行业,例如:
氨和甲醇。
根据所需用氢量,炼油厂有小的制氢装置,也有处理量大到120000Nm3/h的装置,主要为炼油厂的加氢裂化、加氢脱硫和脱芳构化装置提供了氢源。
蒸汽转化工艺路线的选择取决于装置规模、原料和产品氢气规格。
2蒸汽转化工艺
Topsφe公司50多年来一直致力于蒸汽转化工艺和催化剂的研究开发,并取得了明显的成就,开发出一系列制氢流程。
用户可根据不同工况,选择最佳工艺方案。
在制氢工艺中,蒸汽转化已经占据了主导地位。
表1列出Topsφe公司的蒸汽转化工艺。
表1Topsφe公司的蒸汽转化工艺
●预转化工艺
●管式转化炉
●自热式转化(ATR)
●二段转化
●对流式转化炉(HTCR)
绝热预转化工艺可将原料中重烃转化为甲烷和一氧化碳,确保下游设备,如:
管式转化炉、对流式转化炉或者自热式转化(取决工艺方案),能在苛刻条件的操作。
Topsφe管式转化炉设计是基于侧烧模式,这种炉型通过对炉管温度精确控制,确保高合金管材的最优使用,延长炉管的使用寿命。
侧烧式蒸汽转化炉实现其它炉型不能达到的操作条件。
在有氧气来源的场所,自热式转化工艺是有效的选择。
原料和氧气以及水蒸汽在装有专用转化催化剂的反应器中反应,进入自热式反应器的原料可以是烃,也可以是经过预转化的气体;氧气燃烧二段转化工艺,又称二段转化,原料首先在常规转化炉中反应,然后出口的气体进入氧气燃烧转化炉。
合成氨厂直接用空气作为氧化剂,有相似的流程。
火嘴是这两种工艺的关键设备,它应根据每个工况专门设计,确保操作的可靠性能。
对流式转化炉(HTCR)是一个全新理念,它将常规转化炉的辐射段和废热回收段置于一体,结构紧凑,强化了蒸汽转化反应的热量传递,避免了常规转化炉过剩的热量(常用于产汽)。
小型转化炉是撬装供货或安装成可移动的设备。
以上每种工艺都有与之适用的制氢规模,图2为每种工艺的适用范围。
在两种技术重叠区域范围内,有可选择的工艺方案路线。
小规模的装置,HTCR流程最有优势;规模在5000Nm3/h以上的制氢装置,选择HTCR流程,还是管式转化流程,取却于工厂的要求和装置的投资。
规模在5000—120000Nm3/h之间的制氢装置,管式转化工艺完全处于主导地位;当规模大于10000Nm3/h制氢装置时,氧化转化工艺,例如二段转化和自热式转化,备受关注。
规模在5000到120000Nm3/h制氢装置,一般考虑HTCR工艺和常规转化工艺。
2.1绝热预转化工艺
绝热预转化工艺是指将原料中的重烃在一个绝热反应器中得到转化。
然后预转化反应物进入转化炉,再进一步转化,生成富含氢气的混合物。
根据不同工艺要求,转化炉可为管式炉、对流式转化炉或自热式转化炉。
图3是预转化和转化炉组合工艺流程图。
从图中可以看出,进出预转化反应器的工艺流体,经转化炉的对流段预热,分别进入预转化反应器和转化炉。
当转化炉入口温度达到650℃,转化炉所需的热负荷降低大约20%。
在进入预转化反应器前,脱硫后的含氢烃类原料按所需的水碳比与水蒸汽混合。
在预转化反应器出口,所有的重烃转化为甲烷化、变换反应等反应的平衡产物,即一氧化碳、二氧化碳、氢气和甲烷的混合物。
根据原料和水碳比的不同,预转化反应入口温度在350~550℃之间。
预转化反应物可以很安全地预热到700℃,因为不含重烃的反应产物在预热段不会发生蒸汽裂解生成烯烃的反应。
制氢原料可以从天然气到石脑油。
工业实验表明,甚至柴油馏分在预转化催化剂的作用下,也能够完全转化。
但柴油馏分作为制氢原料需要更深度脱硫,硫含量达到更低的PPb级别,实现起来比较困难而且成本很高。
Topsφe公司已经开发出了针对不同原料、温度和水碳比范围的预转化催化剂:
对于液化石油气(LPG)到重的石脑油原料,通常选择RKNGR;对于轻原料,例如天然气:
R-67-GR催化剂是最佳选择。
这两种催化剂都是改良的Ni基蒸汽转化催化剂。
预转化工艺流程有如下优点:
●所有重烃完全转化成碳氧化物和甲烷。
●脱除所有微量硫,提高转化催化剂和中低温变换催化剂的使用寿命。
●由于进入转化炉管的工艺流体中不含有硫和重烃,积碳的几率大大降低。
●转化炉对水碳比和原料组成变化的敏感性大大降低。
在蒸汽转化工艺的所有工厂都具有上面的优势,例如:
合成氨厂、甲醇厂、制氢厂、氧气厂、CO厂和还原气厂等。
预转化技术已经得到了工业生产的认可,尤其在以石脑油或类似原料的制氢装置。
Topsφe公司已有了包括了以石脑油为原料的工业经验,水碳比可降至1.5。
在工业化示范装置中,以天然气为原料,水碳比可降到0.3,这可能与在预转化后配入二氧化碳有关。
另外,自热式转化工艺的水碳比也较低。
2.2管式转化炉
2.2.1转化炉的设计
Topsφe管式转化炉设计是基于侧烧模式,这种炉型通过对炉管温度精确控制,确保高合金管材的最优使用,并延长炉管的使用寿命。
根据装置的规模,可以设置一个或两个辐射室,每个炉膛内,转化炉管沿辐射室的中心线布置。
火嘴分几排位于在辐射墙的内侧,一般为6排。
火焰直接反烧炉墙,炉管所需的热量由炉墙辐射热和烟气对流热提供,消除了火焰直接正对着炉管。
由于这个优点,位于侧烧炉墙内的火焰较短,确保了烟气中NOx含量很低,如:
对没有空气预热的转化炉,NOx含量一般在50PPm以下。
高温烟气从辐射室的顶部,经过耐火衬里通道离开,其热量在对流室中得到回收。
设有庞大的空气预热器的制氢装置,对流段一般横卧于地面。
图4是出口设计温度较高的单套转化炉。
该转化炉出口设有一个冷壁集合管,由一段短直管与炉管连接。
转化出口温度较高,大约在850℃以上,由于在此温度下,下尾管的管材容易发生晶格间氧化和析碳,因此取消了常规的出口下尾管,开发出炉管通过一过渡系统与冷壁集合管连接的结构,与高温气体接触的部件可以采用耐高温的合金。
侧烧炉能够控制沿炉管长度的温度分布,只有这种炉型才能够在低水碳比和高出口温度的条件下操作。
2.2.2管壁温度和热通量的分布
图5是在相同工况开始运行时,顶烧炉和侧烧炉管壁温度和热通量分布图。
温度分布曲线测量于转化炉的操作数据;而热通量分布是根据温度分布数据由计算模块计算的结果,该计算模块既考虑了转化炉辐射室的几何结构,又考虑了热量传到炉管并通过炉管的传热模型、管内的传热模型和反应模型等因素。
图5表明:
顶烧炉的管壁温度在炉管的三分子一处有一个缓平的峰值;而侧烧炉的管壁温度,沿管长方向可以控制,在出口处达到最大值。
顶烧炉的热通量在炉管顶部形成较陡的峰值,在峰值处管壁温度相对较高;而侧烧炉的热通量分布缓平,没有明显的峰值,局部最大热通量比顶烧炉低的多,但平均热通量相对较高。
管长,%
图5:
管壁温度和热负荷分布图
另外,在热通量最大处,侧烧炉比顶烧炉的管壁温度低的多,很明显侧烧炉比顶烧炉所允许的平均热通量要高,因此基于相同的平均热通量的比较是不适当的,而基于最大局部热通量的比较才有意义。
由于在相同的最大局部热通量时,顶烧炉的热通量最大处管壁温度最高,炉管操作条件将会更苛刻。
这意味着,在同样的最大热通量时,侧烧炉的炉管承受的应力较小,因此其炉管在相同直径下可选用更薄的管壁或在相同壁厚下选用更大直径的炉管。
值得注意是,转化炉的设计要适应催化剂活性的变化。
催化剂由于老化或中毒,如硫中毒,活性变化是不可避免的。
各种类型的转化炉都采用高活性的催化剂,热传递决定转化率的大小。
这说明只要达到所需的热量,催化剂活性的损失不会影响转化率的下降,只会带来转化炉出口温度略微升高,这对炉管上部壁温有明显的影响。
这是因为,催化剂失活意味着更少的反应发生,消耗的热量降低,因此,壁温上升。
对于顶烧炉,由于最高炉管的壁温位于炉管上部分,这意味着最高炉管的壁温相应升高。
因此,炉管必须设计成开始运行就要满足最高温度的工况,或者降低装置的处理量,因为降低炉管上部热流通量的唯一方法只有减少热量的输入。
另外,高的管壁温度会出现象热带一样的狭窄的高温区,更容易使催化剂积碳,产生严重的后果。
对于侧烧炉,即使在正常操作条件下,不调整燃烧分布,顶部的温度也会有明显的升高。
然而,这并不意味着最大管壁温度达到设计温度,因为设计温度由管子下部的条件确定。
因此,在苛刻的工况下,即使管壁温度接近设计温度,也能够调节侧烧炉的燃烧分布。
降低装置负荷,热带现象和过早更换催化剂等情况都可以避免。
2.2.3先进的蒸汽转化工艺
Topsφe公司最新开发先进的蒸汽转化工艺。
工艺特点如下:
●高出口温度
●低水碳比
●高空气预热温度(可选)
●绝热预转化工艺(可选)
●高热通量
在先进的制氢装置中水碳比较低,一般为2.5,这样经过装置的质量流量相对减少,因此减低了设备尺寸,降低投资费用。
然而,低水碳比意味着转化炉出口残余甲烷含量增加,通过提高出口温度来补偿,一般可达920℃。
另外,在低水碳比下操作,中温变换催化剂可采用非铁基催化剂,例如:
铜基催化剂。
以石脑油为原料的制氢装置中,在转化炉之前增设绝热预转化反应器有许多优点。
由于一方面所有重烃原料在预转化催化剂作用下达以转化,另一方面进转化炉的入口温度可提高到650℃,这样转化炉的热通量可设计较高,平均热通量可达80000kcal/m2/h,整个转化炉炉的尺寸可减少,直接降低其投资。
高的预热空气温度可降低燃料的消耗和产汽量。
可以通过改变预热空气温度来调节外输蒸汽量。
工业上已经应用的侧烧炉空气预热温度可达到550℃。
2.3高温转化工艺
在有氧气来源时,氧气作为原料和烃类原料进行部分氧化(或者部分氧化原料),利于甲烷和其它烃类的转化,为吸热式蒸汽转化反应提供热量。
有关的技术如下:
●空气氧化的二段转化
●纯氧氧化的二段转化
●自热式转化(ATR)(氧气或富空气)
对大规模制氢装置,在氧气廉价的场所,纯氧氧化的二段转化和自热式转化(ATR)工艺具有吸引力。
2.3.1反应器结构和工艺特点
工艺原料同氧气和蒸汽混合,然后在装有镍基催化剂的绝热反应器(见图6)中反应。
在进入催化剂床层前,原料和氧化剂在混合器/火嘴中混合,发生部分氧化反应。
混合器/火嘴设计是该技术中的一个关键部件。
反应器结构紧凑,为一个耐火衬里压力容器,由顶部的混合器/火嘴,燃烧室和催化剂床层构成。
在ATR工艺,原料烃直接(或者经过预转化反应)和氧气进行部分氧化二段转化,原料来自于管式转化炉的出口气体。
上面所有工况,反应是放热反应,出口温度高达900-1100℃,压力一般可达100bar(1420psig),或更高。
对于类似天然气或预转化的原料,水碳比较低,可达到0.6,或更低。
在以上操作条件下,不会产生烟灰。
因为在混合器/火嘴中生成的烟灰起始物,在催化剂床层中转化,避免了生碳。
产物气体是变换和甲烷化反应的平衡结果,不含高级烃。
2.3.2原料和温度
三种工艺的原料和操作参数各不相同,见表2。
从操作温度来看,ATR工艺最高,而空气氧化的二段转化最低。
从可燃烃的浓度,ATR比二段转化高的多。
与ATR相比,两段转化中与烃/水蒸汽物流混合的氧化剂相对较少。
因此,三种工艺对火嘴的要求各不相同,必须分别设计,以获得最佳操作性能。
2.4对流式转化炉
Topsφe公司根据设计大型制氢装置转化炉和用于燃料电池的换热式转化炉的经验,已成功开发出对流式转化炉(HTCR)。
一套规模为840Nm3/h制氢示范装置在休斯顿进行中试,已成功运行2000小时。
自从1992年开发出该技术以来,已售出12套。
其中最大的一套为双系列,单套规模为5000Nm3/h,正在西欧运行之中。
对流式转化炉为中小规模制氢装置提供了新的途径。
为了提高制氢的生产能力,HTCR对流式转化炉或对有瓶颈问题的制氢装置提供了一种有效的选择,设计安装HTCR可提高生产能力卡边的制氢装置。
HTCR装置具有操作灵活、安装快速以及自动开/停工等特点。
该装置可以做成可移动设备,根据当地的氢气需求,能够从一现场运到另一个现场。
表2高温转化工艺特点
空气式二段转化
氧气式二段转化
自热式转化
原料
CH4、H2、CO
CH4、H2、CO
天然气
氧化剂
空气
氧气
氧气
原料与气体氧化物比
3-4
7-12
1-3
绝热火焰温度℃
1200
1200-1500
1300-2100
产物
氨
甲醇氢气
H2+CO甲醇氨
对流式转化炉由一系列刺刀炉管构成,这些管子安装在耐火衬里的容器内,结构见图7。
工艺物料从顶部经过一个总管分布到装有催化剂的炉管的环隙中,通过催化剂后,工艺气体从底部环隙中心管上升,最终汇集在出口总管出转化炉管。
燃烧室位于炉管的下方,由一个火嘴和分流板组成。
分流板起到防止火嘴对炉管的直接辐射的作用。
转化反应需要的大部分热量主要由管外侧向上流动的烟气提供,一部分热量由向上流动的转化气自身提供。
转化管的冷端安装一套管,强化由烟道气到炉管的传热;管子的热端,设有一个对流控制设施(已申请专利),用来保护管子,防止自身过热。
这样,即使在高转化率条件下,金属的最高温度也在预确定值以下,几乎不受操作条件变化的影响。
通过热交换,出转化炉的工艺气体和烟气温度都降到大约600℃(11000。
F)。
对流式转化炉的80%热负荷由炉管壁传递,而常规转化炉子只有50%,这样就可能做到转化炉所需热负荷与常规转化炉装置中PSA尾气提供的热量相匹配,从而避免像常规转化炉装置中能量过剩。
对流式转化炉将常规转化炉的辐射段、火嘴和对流段置于一体,因此设备相对较小。
对流式转化炉结构紧凑,例如规模10000Nm3/h制氢装置的转化炉,直径约2m,高约20m。
虽然对流式转化是新的工艺,但用此技术制氢的需求还在增加。
自从1992开发以来,十套工业装置已经运行,规模从450Nm3/h到5000Nm3/h不等。
HTCR工艺主要原料是天然气,但是,也有用较重的原料,如煤油馏分的业绩。
另外还有两套采用石脑油为原料生产合成气的HTCR正在设计之中。
用HTCR技术设计的制氢装置规模至少可到20000Nm3/h。
3工业实验
Topsφe公司已经提供了大约30套预转化、170套管式转化炉、7套纯氧氧化二段转化、25套氧烧式自热转化和19套换热式转化炉/对流式转化技术。
其中约90套装置用于制氢,25套转化炉采用先进的转化工艺,出口温度超过900℃。
所用装置均选用Topsφe专利转化催化剂。
Topsφe公司经过多年自身的研究开发和努力,在各种蒸汽转化技术的应用中取得了广泛的经验,确保了给新的客户提供最佳、有效和可靠的方案。
下面是采用不同工艺流程制氢装置举例,以及大规模制氢技术的主要研究结果。
3.1天然气制氢流程
3.1.1工艺说明
图8以天然气为原料中等规模制氢装置的典型流程图。
天然气经转化炉废热回收段的盘管预热,经氧化锌催化剂脱硫,配入工艺蒸汽,混合后的天然气和工艺蒸汽进一步预热,进入转化炉管。
在转化炉Ni基催化剂的作用下,烃类转化成氢气、一氧化碳和二氧化碳平衡组成。
转化炉出口温度根据不同的工况可高达900~930℃。
转化炉出口的转化气通过产汽被冷却下来,进入变换反应器。
变换反应一般选择中温变换,转化气在变换催化剂作用下,一氧化碳和水蒸汽变换成二氧化碳和氢气,生产更多的氢气。
变换气进一步冷却到常温,进入PSA装置。
经过PSA装置后,得到高纯度的氢气。
PSA尾气作转化炉的燃料,不足部分由天然气补充。
供燃烧器所需的空气可以在转化炉对流段盘管中预热。
在制氢装置中,产生的蒸汽一部分作为工艺蒸汽参加反应,多余的外输。
3.1.2装置举例
表3操作数据:
天然气为原料
规模,Nm3/hH2
13,500
原料
天然气
水碳比
2.5
转化入口/出口温度℃
535/920
变换反应
中温变换
空气预热温度℃
360
平均热负荷,kcal/m2/h
73,500
性能,Gcal/1000Nm3/hH2
天然气
3.82
外输蒸汽
0.78
净能耗
3.04
1994年6月,Topsφe公司在欧洲签订了为一套13500Nm3/h制氢装置提供专利服务、工程设计和整套硬件供应合同。
部分详细设计以及设备和材料的供应转包给当地一家工程公司。
该项目按整个计划进行,于1996年7月竣工。
转化炉设计的水碳比为2.5,没有预转化,出口温度为920℃,空气预热温度为360℃。
这些操作条件,使整个工艺净能耗和氢气成本降低。
表3列出了操作数据以及生产和消耗指标。
这套装置自从第一次开工以来,一直成功运行,操作良好。
非计划停工也是由装置外的问题造成的,如电源故障。
3.2石脑油制氢流程
3.2.1工艺说明
图9为石脑油为原料大规模制氢装置的流程图。
石脑油经过预热、气化、脱硫,与工艺蒸汽混合,进一步预热,进入绝热预转化反应器。
绝热预转化反应器尤其适合以石脑油为原料的制氢装置,反应器中装有高活性的转化催化剂,在催化剂的作用下,所有重烃完全转化生成氢气、碳氧化物和甲烷的混合物。
该流程的主要优点在于转化炉能够在更苛刻的条件下操作,如低水碳比、高的转化炉入口温度;另外预转化工艺增加原料选择的灵活性,同时也可以防止转化催化剂硫中毒。
在转化炉管中,在Ni基催化剂的作用下,预转化气发生由甲烷生成氢气、一氧化碳和二氧化碳的等以系列平衡反应。
转化炉出口温度根据不同的工况高达800~930℃。
转化炉出口的转化气通过产汽冷却下来,进入变换反应器。
在变换催化剂作用下,一氧化碳和水蒸汽变换成二氧化碳和氢气,生产更多的氢。
变换气进一步冷却到常温,进入PSA装置。
经过PSA装置后,得到高纯度的氢气。
PSA尾气作转化炉的燃料,不足部分由炼厂气或气化的石脑油补充。
3.2.2装置举例
表4重原料的操作数据
规模,Nm3/hH2
72600
89300
原料
炼厂气
C4
水碳比
2.5
2.5
预转化
有
有
转化入口/出口温度℃
630/850
650/850
平均热负荷,kcal/m2/h
74000
78800
变换反应
中温变换
中温变换
空气预热温度℃
245
240
性能,Gcal/1000Nm3/hH2
原料+燃料
3.98
3.79
外输蒸汽
0.72
0.58
净能耗
3.26
3.21
1992年,一套规模为76700Nm3/h制氢装置在亚洲的投产。
原料是石脑油和炼厂气。
开工以来,操作性能令人满意。
1996年,另一套新的装置在同一地点开工,以C4为原料。
这两套制氢是大型综合炼厂的一部分,为炼厂加氢装置提供氢气。
表4列出了这两套装置的操作数据和能耗值。
从表4可以看出,两套装置的操作条件基本相似。
水碳比为2.5,转化炉出口温度为850℃,都是中变反应器。
两套装置都设有预转化反应器,其催化剂已经表现出非常优良性能。
其中72600Nm3/h这套制氢装置,开工五年来,没有更换催化剂,性能评价表明催化剂还能再用五年。
由于该装置投资低,所以这种工艺方案有很强的竞争力。
在能源价格低,原料和燃料价格没有差异时,以石脑油为原料时,此流程为最佳制氢流程。
3.3对流式转化工艺流程
3.3.1典型的工艺说明
图10为对流式转化制氢装置的流程图。
含烃原料预热经过加氢脱硫后,与水蒸汽混合进入对流式转化炉,在常规Ni基转化催化剂的作用下,发生甲烷转化反应。
离开对流式转化炉的工艺流体通过产汽冷却下来,进入一氧化碳变换反应器。
变换气经过产汽、空冷、水冷,最后进入PSA氢提纯装置。
转化炉的烟气,用于蒸汽过热、预热原料或者预热空气,回收其余热。
PSA尾气作转化炉的燃料,只需少量补充燃料(正常由原料供应)。
采用这种工艺流程的工厂,在蒸汽和燃料方面能够自我平衡。
所有的废热包括变换段的热量都用来产汽,产生的蒸汽只作为工艺蒸汽。
该装置输入为原料、水和电;输出为产品氢、烟气和锅炉排污水。
HTCR转化炉需要的燃料量少,因为转化反应所需的热量由高温转化气和烟气提供。
装置开工需要的热量由转化炉火嘴燃烧提供,操作自动化程度高。
转化炉设计结构紧凑,操作灵活,能快速适应负荷变化。
3.3.2装置举例
1996年,Topsφe公司同欧洲某公司签定了一个双系列制氢装置的合同。
单系列规模为5000Nm3/h。
两套装置在1997年末开工。
表5为操作数据和能耗值。
表5操作数据:
HTCR流程
规模,Nm3/hH2
5000
原料
天然气
水碳比
3.2
HTCR上/下温度℃
445-840
变换反应
高温变换
性能,Gcal/1000Nm3/hH2
原料+燃料
3.44
外输蒸汽
0
净能耗
3.44
HTCR工艺降低装置投资。
其流程特点:
无预转化,水碳比相对较高,转化炉底部温度低,高温变换。
此外,选择的合适操作条件保证了工艺中蒸汽和燃料自我平衡。
与管式转化工艺相比,HTCR工艺原料和燃料的消耗低,净能耗略高(原料+燃料-蒸汽),投资比常规转化工艺低约10%。
对流式转化与管式转化工艺相比,在以天然气为原料时,其外输蒸汽量少,甚至不输出,当原料和燃料价格相同,此时HTCR工艺投资更低,更具有竞争优势。
3.4大规模制氢工艺
大规模制氢装置可考虑不同转化技术:
●蒸汽转化(SMR):
可以采用双系列甚至多系列平行管式蒸汽转化,满足大规模制氢的要求。
●二段转化:
只需要一个系列,前面为管式转化,后面跟一个氧气燃烧二段转化。
●自热式转化(ATR):
只需要一个系列,含有一个自热式转化反应器。
图8为管式蒸汽转化制氢工艺流程。
图11为二段转化制氢工艺流程,图12是一套ATR制氢工艺流程。
三种工艺比较基础是:
原料为天然气,生产能力220000Nm3/h氢气装置。
管式转化工艺采用等规模双系列流程,二段转化和自热式转化工艺可采用一个系列流程。
表6为比较结果汇总,可以看出:
二段转化的组合流程比SMR工艺投资减少了15%,主要是节省在转化炉部分以及产汽系统。
然而,增加了所需要的供氧费用,这取决于当地条件。
表6大规模制氢流程:
以236000Nm3/h为例
转化形式
SMR
二段转化
ATR
性能,Gcal/1000Nm3/hH2
原料
2.85
3.20
3.51
燃料
0.67
0.22
—
蒸汽
(0.52)
(0.42)
(0.39)
外输燃料
—
—
(0.07)
净能耗
3.00
3.00
3.05
氧气消耗
—
47.3
70.8
相对建设费用
100
85
75
ATR与SMR工艺相比,也得出同样的结论,只是投资费用降低的更多。
假设天然气的价格为US$12/Gkcal,SMR投资回收期(含外输蒸汽还贷)为五年,二段转化和ATR所需氧气费用为盈亏平衡点,其价格为US$5~10/t。
也就是当氧气价格低时,三种工