循环流化床必备知识.docx
《循环流化床必备知识.docx》由会员分享,可在线阅读,更多相关《循环流化床必备知识.docx(21页珍藏版)》请在冰豆网上搜索。
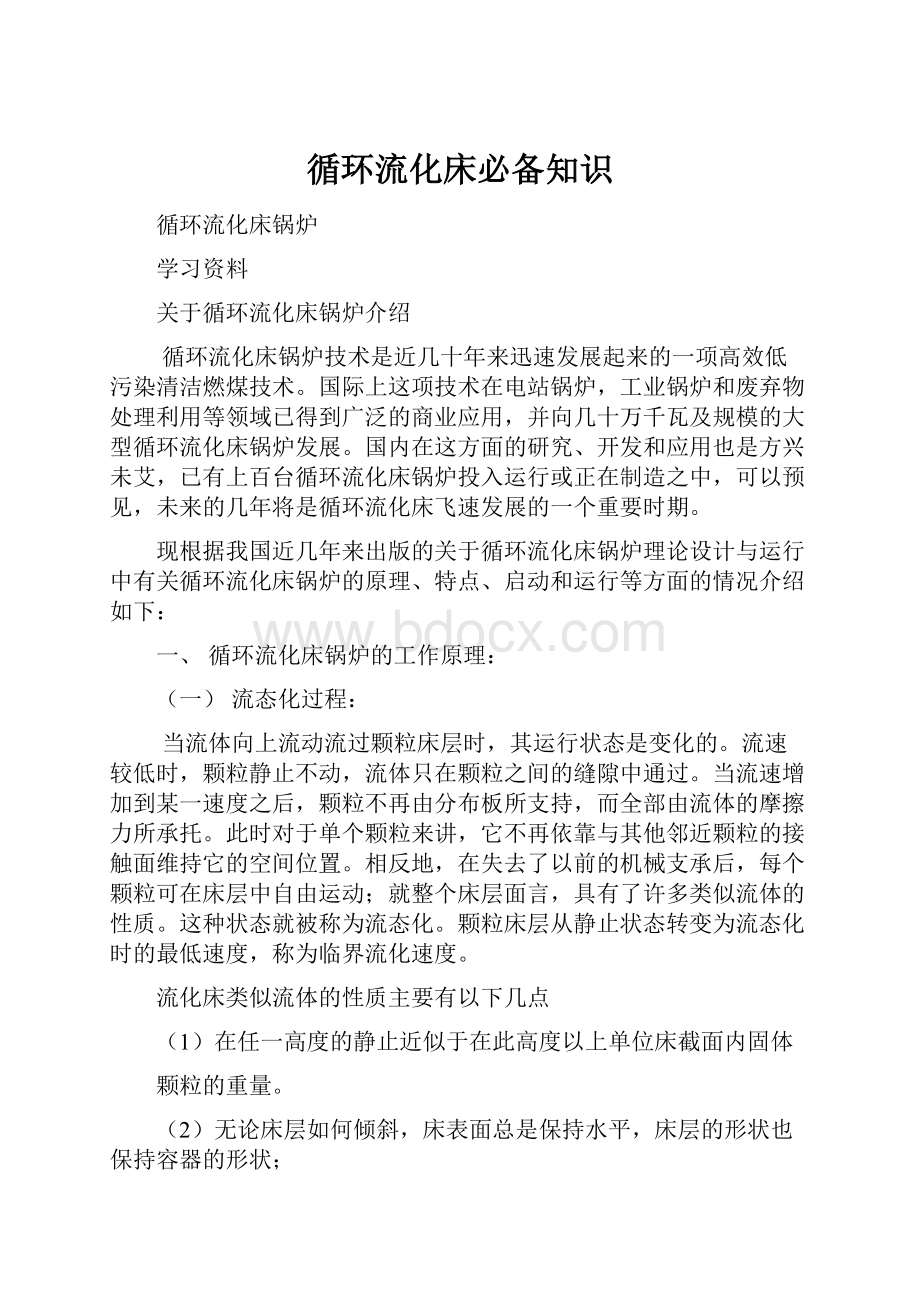
循环流化床必备知识
循环流化床锅炉
学习资料
关于循环流化床锅炉介绍
循环流化床锅炉技术是近几十年来迅速发展起来的一项高效低污染清洁燃煤技术。
国际上这项技术在电站锅炉,工业锅炉和废弃物处理利用等领域已得到广泛的商业应用,并向几十万千瓦及规模的大型循环流化床锅炉发展。
国内在这方面的研究、开发和应用也是方兴未艾,已有上百台循环流化床锅炉投入运行或正在制造之中,可以预见,未来的几年将是循环流化床飞速发展的一个重要时期。
现根据我国近几年来出版的关于循环流化床锅炉理论设计与运行中有关循环流化床锅炉的原理、特点、启动和运行等方面的情况介绍如下:
一、循环流化床锅炉的工作原理:
(一)流态化过程:
当流体向上流动流过颗粒床层时,其运行状态是变化的。
流速较低时,颗粒静止不动,流体只在颗粒之间的缝隙中通过。
当流速增加到某一速度之后,颗粒不再由分布板所支持,而全部由流体的摩擦力所承托。
此时对于单个颗粒来讲,它不再依靠与其他邻近颗粒的接触面维持它的空间位置。
相反地,在失去了以前的机械支承后,每个颗粒可在床层中自由运动;就整个床层面言,具有了许多类似流体的性质。
这种状态就被称为流态化。
颗粒床层从静止状态转变为流态化时的最低速度,称为临界流化速度。
流化床类似流体的性质主要有以下几点
(1)在任一高度的静止近似于在此高度以上单位床截面内固体
颗粒的重量。
(2)无论床层如何倾斜,床表面总是保持水平,床层的形状也保持容器的形状;
(3)床内固体颗粒可以像流体一样从底部或侧面的孔口中排出;
(4)密度高于床层表观察的物体化床内会下沉,密度小的物体会浮在床面上;
(5)床内颗粒混合良好,颗粒均匀分散于床层中,称之为“散式”流态化。
因此,当加热床层时,整个床层的温度基本均匀。
而一般的气、固体态化,气体并不均匀地流过颗粒床层。
一部分气体形成气泡经床层短路逸出,颗粒则被分成群体作湍流运动,床层中的空隙率随位置和时间的不同而变化,因此这种流态化称之为“聚式”流态化。
煤的燃烧过程是一个气、固流态化过程。
二、循环流化床的原理和特点:
循环流化床在不同气流速度下固体颗粒床层的流动状态也不同。
随着气流速度的增加,固体颗粒分别呈现固体床、鼓泡流化床、湍流流化床和气力输送状态。
循环流化床的上升阶段通常运行在快速流化床状态下,快速流化床流体动力特性的形成对循环流化床是至关重要的,此时,固体燃料被速度大于单颗燃料的终端速度的气流所流化,以颗粒团的形式上下运动,产生高度的返混。
颗粒团向各个方向运动,而且不断形成和解体,在这种流体状态下气流还可携带一定数量的大颗粒,尽管其终端速度远大于截平均气速。
这种气、固运行方式中,存在较大的气、固两相速度差,即相对速度,循环流化床由快速流化床(上升段)气、固燃料分离装置和固体燃料回送装置所组成。
循环流化床的特点可纳如下:
(1)不再有鼓泡流化床那样的界面,固体颗粒充满整个上升段空间。
(2)有强力的燃料返混,颗粒团不断形成和解体,并向各个方面运行。
(3)颗粒与气体之间的相对速度大,且与床层空隙率和颗粒循环流量有关。
(4)运行流化速度为鼓泡流化床的2-3倍。
(5)床层压降随流化速度和颗粒的质量流量而变化。
(6)颗粒横向混合良好。
(7)强烈的颗粒返混,颗粒的外部循环和良好的横向混合,使得整个上升段内温度分布均匀。
(8)通过改变上升段内的存料量,燃料在床内的停留时间可在几分钟到数子时范围内调节。
(9)流化气体的整体性状呈塞状流。
(10)流化气体根据需要可在反应器的不同高度加入。
三、流化床燃料设备的主要类型:
流化床操作起初主要用在化工领域,自60年代开始,流化床被用于煤的燃料,并且很快成为三种主要燃料方式之一,即固定床燃料(层燃),流化床燃料和悬浮燃烧(煤粉燃烧)流化床燃烧过程的理论和实践也大大推动了流态化学科的发展,目前流化床燃烧已成为流态化的主要应用领域之一,愈来愈得到人们的重视。
流化床燃烧设备按流体动力特性可分为鼓泡流化床锅炉,和循环流化床锅炉,按工作条件分又可分为常压和增压流化床锅炉,这样流化床燃烧锅炉可分为常压鼓泡流化床锅炉,常压循环流化床锅炉,增压鼓泡流化床锅炉和增压循环流化床锅炉正在工业示范阶段。
(四)循环流化床锅炉的特点:
(1)循环流化床锅炉的工作条件:
项目
数值
项目
数值
温度(℃)
850-950
床层压降KPa
11-12
流化速度(m/s)
4-6
炉内颗粒浓度kg/m3
150-600炉膛底部
床料粒度(μm)
100-700
10-40炉膛上部
床料密度(kg/m3)
1800-2600
Ca/s摩尔比
1.5-4
燃料粒度(mm)
<12
壁面传
210-250
脱硫剂粒度(mm)
1左右
(2)循环流化床锅炉的特点:
循环流化床锅炉可分为两个部份,第一部份由炉膛(块速流化床)气,固物料分离设备,固体物料再循环设备,(旋风份离器)等组成,上述部分形成了一个固体物料循环回路。
第二部份为对流烟道,布置有过热器,再热器,省煤器和空气予热器等。
典型循环流化床锅炉燃烧系统,燃烧所需的一、二次风分别从炉膛的底部和炉膛侧墙送入,燃料的燃烧主要在炉膛中完成,炉膛四周布置水冷壁,用于吸收燃料所产生的部分热量,由气流带出炉膛的固体物料在气、固体分离装置中被收集并通过返料装置返回炉膛再燃烧
循环流化床燃烧锅炉的基本特点:
可概括以下:
1、低温的动力控制燃烧:
循环流化床燃烧是一种在炉内使高速运行的烟气与其所携带的湍流扰动极强的固体颗粒密切接触,并具有大量颗粒返混的流态化燃烧反应过程,同时,在炉外将绝大部分高温的固体颗粒捕集,将这部分颗粒送回炉内再次参予燃烧过程,反复循环地组织燃烧。
显然,燃料在炉膛内燃烧的时间延长了,在这种燃烧方式下,炉内温度水平因受脱硫最佳温度限制,一般850℃左右,这样的温度远低于普通煤粉炉中的温度水平(一般1300-1400℃),并低于一般煤的灰烤点(1200-1400℃),这就免去了灰熔化带来的种种烦恼。
这种低温燃烧方式好处较多,炉内结渣,及碱金属,析出均比煤粉炉中要改善很多,对灰特性的敏感性减低,也无须用很大空间去使高温灰冷却下来,氮氧化合物生成量低。
并可与炉内组织廉价而高效的脱硫工艺。
从燃烧反应动力学角度看,循环流化床锅炉内的燃烧反应控制在动力燃烧区(或过渡区)内。
由于循环流化床锅炉内相对来说燃烧温度不高,并有大量固体颗粒的强烈混合,这种状况下的燃烧速率主要取决于化学反应速率,也就决定于燃烧温度水平,面燃烧物理因素不再是控制燃烧速率的主导因素,循环流化床锅炉内燃料燃尽度很高,通常,性能良好的循环流化床锅炉燃烧率可达98-99%以上。
2、高速度、高浓度、高通量的固体物料流态化循环过程:
循环流化床锅炉内的固体物料(包括燃料残炭,脱硫剂和惰性床料等)经由炉膛,分离器和返料装置所组成的外循环。
同时,循环流化床锅炉内的物料参于炉内、外两种循环运行。
整个燃烧过程的及脱硫过程都是在这两种形式的循环运行的动态过程中逐步完成的。
3、高强度的热量、质量和运行传递过程:
在循环流化床锅炉中,大量的固体物料化强烈湍流下通过炉膛,通过人为操作可改变物料循环量,并可改变炉内物料的分布规律,以适应不同的燃烧工况,在这种组织方式下,炉内的热量、质量和动量传递是十分强烈的,这就使整个炉膛高度的温度分布均匀,实践也充分证实际这一点。
4、循环流化床锅炉与其它炉型相比较:
一般固体燃料的燃烧可分为:
层燃、流化床燃烧和紧浮燃烧,流化床燃烧又可分为鼓泡流化床和循环流化床燃烧。
为了解循环流化床锅炉的优点以及需要进一步研究解决的问题,有必要对循环流化床锅炉与其他炉型炉进行比较。
(1)燃烧过程的比较:
特征
层燃炉
循环流化床
悬物燃烧炉
燃料颗粒平均直径(mm)
<300
0.05-0.1
0.02-0.08
燃料室区域风速(m/s)
1-3
3-12
15-30
固体运行状态
静止
大部份向上,部分向下
向上
床层与受热面传热系数w.m2.k
50-150
100-250
50-100
磨损
小
中
较小
(2)脱硫过程的比较:
煤粉炉的喷钙脱硫是将钙基脱硫剂(如石灰石、白方石或消石灰)直接喷入炉内,在高温下脱硫剂大段烧进行如瓜反应:
CaCO3CaO(S)+CO2(g)
MgCO3·(OH2)CaO(S)+MgO(S)+2CO2(g)
Ca(OH2)Ca0(S)+H2O(g)
在通常燃烧温度下,燃烧过程在不到200ms的时间内就基本完成了(脱硫剂粒径为10μm左右),脱硫剂燃烧后形成多孔的氧化钙颗粒,一旦脱硫剂燃烧生成CaCO,它就和反应成硫酸钙
CaO(S)+SO2(g)+O2(g)CaSO4(S)
据煤粉炉喷钙试验,最佳喷入温度为1100℃左右,石灰石料度在8-10μm之间脱硫效率较佳,脱硫剂的利用率一般为20%,脱硫效率为50%。
而循环硫化床锅炉的燃烧脱硫过程是将脱硫剂(石灰或白方石)送入炉内,然后与燃烧生成的二氧化硫气体反应,达到脱硫目的。
与煤粉炉一样,脱硫剂进入循环流化床锅炉后大段烧形成氧化钙,氧化钙再与二氧化硫气体反应。
在循环流化床锅炉中,由于独特的设计和运行条件,整个循环流化床锅炉的主循环回路运行在脱硫的最佳温度范围内(850-900℃)。
同时由于固体物料在炉内、外循环(通过分离装置和回送装置)脱硫剂在炉内的停留时间大大延长,通常平均停留时间可达数十分钟。
此外,炉内强烈的湍流混合也十分有利于循环流化床锅炉燃烧脱硫过程在Ca/S为1.5-2.5时,脱硫效率通常可达90%,脱硫剂利用率可达50%,将比煤粉脱硫效果提高一倍。
(3)各种形式锅炉主要技术经济指标的比较:
锅炉型号
主要技术经济指标
YG-35/39-M3
循环流化床炉
BG-35/39-M煤粉炉
L-35/39-W/I链条炉
锅炉实际热效率(%)
87.8
87.96
50
燃料种类
贫煤
贫煤
贫煤
低位发热量(KJ/kg)
21736
22003
21736
锅炉耗煤量(kg/h)
4959
4883
8707
锅炉耗标煤(kg/h)
3684
3677
6468
辅机耗电总容量(KW)
470
587.1
362.3
辅机耗电总容量折标煤(kg)
100
235
145
总耗标煤(kg/h)
3872
4218
6613
每吨汽耗标煤(kg)
110.69
109.25
188.94
燃烧效率(%)
98-99
98-99
88.1
负荷调节范围
较大
小
大
对煤种变化的适应性
适应了
较单一煤种
单一煤种
操作维护水平
一般
高
简单
锅炉设备费(本体)(万元)
82.68
97
86.59
系统投资费(万元)
245
400
200.7
锅炉钢材耗量(吨)
157
165
186
二氧化硫排放量
加石灰石可脱硫
全部排放
全部排放
二氧化氮排放量
生成少
生成多
生成较多
飞灰排放量
较大
大
小
注:
锅炉投资按90年代初估价
循环硫化床锅炉与其他型式锅炉比较
锅炉
特性
链条炉
煤粉炉
循环硫化床炉
床高或燃料燃烧区高度m
0.2
15-40
27-45
截面风速m/s
1.2
4-8
4-6
过剩空气系数
1.2-1.3
1.2-1.25
1.15-1.3
截面热负荷MW/M2
0.5-1.5
3-5
4-6
煤的粒度过mm
6-32
6以下
0.1以下
负荷调节比
4.1
3:
4.1
燃烧效率%
85-90
95-99
99
NO2排放PPM
400-600
50-200
400-600
炉内脱硫效率
低
80-90
从上表可看出:
循环硫化床锅炉明显优于其他型式的锅炉
五、循环硫化床锅炉的优点:
优点:
由于循环硫化床锅炉独特的流体动力特性和结构,使其具备有许多独特的优点,以下分别加的简述。
1、燃料适应性:
这是循环流化床锅炉主要特性优点之一。
在循环流化床锅炉中按重量计,燃料仅点床料的1%-3%,其它是不可燃的固体颗粒,如脱硫剂、灰渣或砂。
循环流化床锅炉的特殊流体动力特性使得气、固和固与固体燃料混合非常好,因此燃料进入炉膛后很快与大量床料混凝土合,燃料被此速加热至高于看火温度,而同时床层温度没有明显降低,只要燃料热值大于加热燃料本身和燃料所需的空气至着火温度所需的热量,循环流化床锅炉不需要辅助燃料而砂用任何原料。
循环流化床锅炉既可用优质煤,也可烧用各种劣质煤,如高灰分煤、高硫煤、高灰高硫煤、煤矸石、泥煤、以及油页岩、石油焦、炉渣树皮、废木料、垃圾等。
2、燃烧效率高:
循环流化床锅炉的燃烧效率要比链条炉高得可达97.5-99.5%,可与煤粉炉相媲美。
循环流化床锅炉燃烧效率高是因为下述特点:
气、固混合良好,燃烧速率高,特别是对粗粉燃料,绝大部分未燃尽的燃料被再循环至炉膛再燃烧,同时,循环流化床锅炉能在较宽的运行变化范围内保持较高的燃烧效率。
甚至燃用细粉含量高的燃料时也是如此。
3、高效脱硫:
循环流化床锅炉的脱硫比其它炉型更加有效,典型的循环流化床锅炉脱硫可达90%。
与燃烧过程不同,脱流反应进行得较为缓慢,为了使氧化钙(燃烧石灰石)充分转化为硫酸钙,烟气中的二氧化硫气体必须与脱硫剂有充分长的接触时间和尽可能大的反应面积。
当然,脱硫剂颗粒的内部并不能完全瓜,气体在燃烧区的平均停留时间为3-4秒钟,循环流化床锅炉中石灰石粒径通常为0.1-0.3mm,无论是脱硫剂的利用率还是二氧化硫的脱除率,循环流化床锅炉都比其他锅炉优越。
4、氮氧化物(NO2)排放低:
氮氧化物排放低是循环硫化床锅炉一个非常吸引人的一个特点。
运行经验表明,循环流化床锅炉的二氧化氮排放范围为50-150PPM或40-120mg/mJ。
NO2排放低的原因:
一是低温燃烧,此时空气中的氮一般不会生成NO2,二是分段燃烧,抑制燃料中的氮转化NO2,并使部分已生成NO2得到还原。
5、其他污染物排放低:
循环流化床锅炉的其他污染物如:
CO、HC1、HF等排放也很低。
6、燃烧强度高、炉膛截面积小
炉膛单位截面积的热负荷高是循环流化床锅炉的主要优点之一。
循环流化床锅炉的截面热负荷约为3.5-4.5MW/m2接近或高于煤粉炉
7、给煤点少:
循环流化床锅炉因炉膛截面积较大,同时良好的混合和燃烧区域的扩展使所需的给煤点数大大减少,只需一个给煤点,也简化了给煤系统。
8、燃料预处理系统简单:
循环流化床锅炉的给煤粒度一般小于12mm,因此与煤粉炉相比,燃料的制粉系统相比大为简化。
此外,循环流化床锅炉能直接燃用高水分煤(水分可达30%以上)。
当燃用高水分煤时,也不需要专门的处理系统。
9、易于实现灰渣综合利用:
循环流化床锅炉因燃烧过程属于低温燃烧,同时炉内优良的燃尽条件,使得锅炉灰渣含碳量低,易于实现灰渣的综合利用。
如灰渣作为水泥掺和料或做建筑材料,同时做温烧透也有利于稀有金属的提取。
10、负荷调节范围大,负荷调节快:
当负荷变化时,当需调节给煤量、空气量和物料循环量、负荷调节比可达(3-4):
1,此外,由于截面风速高和吸热高和吸热控制容易,循环流化床锅炉的负荷调节速率也很快,一般可达每分钟4%。
11、循环床内不布埋受热面管:
循环流化床锅炉的床内不布置埋管受热面,不存在磨损问题,此外,启动,停炉,结焦处理时向短、同时长时间压火之后可直接启动。
12、投资和运行费用适中:
循环流化床锅炉的投资和运行费用略高于常规煤粉炉但比配制脱硫装置的煤粉炉低15-20%。
六、循环流化床锅炉尚待进一步研究的问题:
为使循环流化床锅炉的设计和运行达到优化的目的,充分发挥循环流化床的优点,尚需对下列几个方面进行深入研究。
1、循环物料的分离
循环流化床锅炉的分离装置接工作温度分为高温、中温和低温分离,接分离的作用形式又可分为旋风分离,惯性分离等。
以目前循环流化床的运行情况来看,高温旋风分离器还是比较成熟的。
但使用高灰燃料时的磨损问题尚未解决。
而且分离的体积也十分庞大,基本上和炉膛直径相近。
受旋风分离器最大尺寸的限制,大容量循环流化床锅炉必需配置多个分离器。
由于旋风分离器内衬有较厚的防磨耐火材料,热惯性大,因此延长了锅炉启动时间。
负荷变化动态特性变差,故采用惯性分离器是值得探讨的,因为惯性分离器设备经较简单,体积小,结构布置比较方便。
流动阻力也相对较小。
此外不应操付中,低温分离器。
根据循环流化床锅炉的发展要求将设计、效率高、体积小、阻力低、磨损小和制造及运行方便的物料分离装置。
2、循环流化床的固体颗粒的浓度选取:
循环流化床内固体颗粒浓度对燃烧过程,脱硫过程和传热过程都有很大影响。
但合适的循环流化床内固体颗粒浓度的确定却十分困难。
目前各循环流化床各制造厂家所采用的炉内颗粒浓度的一个重要参数是循环倍率。
国内的一些循环流化床锅炉的循环倍率通常在10以下,而国外的循环倍率常达到50,甚至更高。
在分析循环流化床锅炉的工作过程时,不仅要考虑物料的内部循环,亦要考虑炉外循环,在高风速运行时,物料内循环更为显著。
因此,合理的循环床内固体颗粒的浓度的选取对燃烧脱硫,传热、磨损、能耗等一系列因素都有影响。
3、炉内受热面布置和温度控制
为了保证循环流化床锅炉的炉内温度控制在一定范围内,在固体颗粒循环回路中必须吸一部分热量。
目前炉内吸热主要有以下两种方法:
一种是炉膛内布置水冷壁或隔墙;另一种是炉膛内布置部分受热面(如过热器等)在固体物料循环回路上再布置流化床换热器。
这两种形式都可行的。
但这两种方法,对床温控制方式是不同的,前者主要是靠调节返料量来调节床内固体颗粒浓度,以改变水冷壁的换热系数。
从而改变炉内吸热量来控制床温,否者仅需调节进入流化床换热器和热接返回炉内固体物料量的比例,便可控制床温,相对比较灵活,特别适合于大容量循环流化床锅炉。
4、运行风速(或截面热负荷)的确定
循环流化床锅炉的运行风速是一个重要的参数。
一般运行风速为4-10m/s/。
运行风速提高会使炉子更为紧凑。
截面热负荷相应增大,此时为了保证燃料和石灰石颗粒有足够的停留时间和布置足够的受热面,必须增加炉膛高度。
这样不仅磨损增加,而且锅炉造价增加。
风机功率会增大,厂用电也会相应增加。
但风速过低则发挥不了循环流化床的优点,因此对各种燃料都应具有最佳的运行风速。
5、返料机构:
在循环流化床中,被分离下来的固体物料必须通过返料机构送回炉内。
返料机构还应对返回的物料量进行灵活的调节,但由于返料机构中的温度很高,磨损较大,如采用一般机械阀门之类的调节装置,会很容易产生卡死,转动不灵等现象,目前循环流化床中一般采用非机械阀。
(L阀)和流化床返料机构,一方面调节物料流量,另一方面防止燃料在燃烧室反串型分离器,造成短路。
目前许多制造厂家对返料机构都是保密的。
6、循环流化床锅炉部件的磨损:
由于循环流化床锅炉内的高颗粒浓度和高运行风速,锅炉部件的磨损是比较严重的。
磨损主要与风速、颗粒度以及流场的不均匀性有关,磨损与风速及浓度成正比。
在设计时,一般应防止烟气走廊突缩突扩的形式。
目前研究比较落弱。
7、低污染燃料:
循环流化床锅炉已获得迅速发展。
一个重要的原因就是循环流化床的低污染燃料特性,在脱硫研究方面目前相对一致,但对于脱硫最佳温度,脱硫剂的高效利用方面尚有许多内容要研究。
如降低NO2、床温、烟气再循环,注氨以及脱硫剂对NO2的影响等有待进一步研究。
9、尾部受热面的设计:
目前在循环流化床锅炉中,尾部烟道受热面的设计一般比较忽视,如何更加合理布置尾部烟道受热面尚待进一步研究。
10、除尘:
尾部烟道现在国内大部分采用电除尘。
七、循环流化床锅炉的发展:
国外:
60年代就开始研究,是芬兰奥期龙公司,第一台为热功率15MW由燃油炉改造而成的商用循环流化床锅炉,后由美国巴特利多固体循环流化床锅炉及德国,瑞典、加拿大、意大利等国分别制造出各种型式的循环流化床锅炉,最大的为发电功率165MW配套的循环流化床锅炉同加拿大1993年制造。
国内:
(1)主要有东北电力学院,于1986年7月与吉林锅炉厂研制的10t/h鼓泡式循环流化床锅炉,现已生产出4、6、10、15、20t/h系列产品,汽压为1.27-2.45Mpa温度为194-350℃,同时,清华大学热能系亦研制类似型式的循环流化床锅炉。
(2)中国科学院工程热物理研究所于1984年承国家科委“煤的流化床锅炉燃烧技术研究”1985年与开封锅炉厂联合开发的10t/h循环流化床锅炉。
并获国家专利,后与济南锅炉厂联合开发35t/h,50、65、75、130t/h系列循环流化床锅炉,并采用一级万叶窗,二级旋风分离器的多级分离装置,在山乘果热电厂运行。
(3)清华大学在循环流化床技术虽比中科院晚,旦发展迅速。
其基本构思是采用二级分离:
柱板惯性分离器加S型分离器优点是阻力较低,已在中、日美分别申请专利。
1989年与福期特惠勒公司和日本石川岛播磨重工业公司联合开发由江西锅炉厂制造了20t/h和与四川锅炉厂制造出四台35t/h,示范流化床锅炉和75t/h循环流化床锅炉已投产运行。
(4)由浙江大学自80年代对循环流化床燃烧技术进行研究开展了包括循环流化床特性、传热特性,脱硫硫硝特性,磨损特性,分离器,返料机构,灰渣冷却装置、循环流化床汽、汽联产技术等方面的研究,并获“高温物料冷却装置”专利,目前与杭锅厂与加拿大有关大学,公司进行燃用高硫煤的220t/h循环流化床锅炉的联合开发。
此外,哈工大、电力部热工形容院,太锅、车锅、某单位都在研究和制造开发35、65、75、220t/h循环流化床锅炉。
总之,90年代循环流化床锅炉应达到以下技术标准:
(1)燃烧效率100%;
(2)电厂效率大于40%;
(3)SO2排放小于10PPM;
(4)NO2排放小于30PPM。
浙江大学发展的煤水混合物高效低污染流化床燃烧技术的主要特点如下:
一、煤水混合物结团燃烧
凝聚结团现象是煤水混合物在燃烧过程中的一个十分重要的现象。
实验表明:
对相当一部分煤而言,由细粒组成的煤水混合物被以较大体积的聚集状态送入高温流化床时,它们往往并不是在干燥后还原成细颗粒,而是迅速形成具有一定强度和耐磨性的较大块团。
次外,煤水混合物还会通过反复或粘连床内的其他颗粒,而形成较大的块团。
对于这种现象,我们称为凝聚结团现象。
由凝聚结团作用生成的块团称为凝聚团。
煤水混合物凝聚团的存在,对保证流化床的稳定运行造成很大影响。
凝聚结团往往使流化床床料的粒度不断增加的趋势,形成大凝聚团极易在流化床内沉积,逐步破坏流化床质量,使流化床燃烧难以稳定地运行。
但凝聚结财现象的存在,对保证了燃料即使在较高的运行风速下也不会被扬析。
所以强凝聚结团现象对煤水混合的流化床燃烧有着十分重要的积极意义。
它不但为在流化床内组织正常燃烧提供了有利条件,而且为在较高的断面热负荷下降低流化床燃烧过程中燃料的扬析损失创造了有利条件。
因可燃物扬析损失通常占流化床锅炉燃烧效率损失的绝大部分。
这一损失值得注意。
二、异重流化床
为了清除大粒凝聚团对稳定燃烧的感受,对于通常的流化床燃烧而言,由于所用燃料粒度分布较宽,流化床内往往要出现一定程度的偏析。
即粒度大的较集中分布于炉底。
在床内有凝聚团现象出现有时比煤水混合物粒度大10几倍。
这样大凝聚团在形成后甚至还未干燥,就很快沉积到流化床底部的布风板区域。
该区域的温度较低,使燃烧反应速率很低,连燃烧水份蒸发都很慢,这样就降低了流化风速和流化质量很差,又降低了该区域的传热。
传热过程和颗粒运行以及相互的作用。
使沉积