中厚板生产压下规程课程设计轧制规程设计.docx
《中厚板生产压下规程课程设计轧制规程设计.docx》由会员分享,可在线阅读,更多相关《中厚板生产压下规程课程设计轧制规程设计.docx(30页珍藏版)》请在冰豆网上搜索。
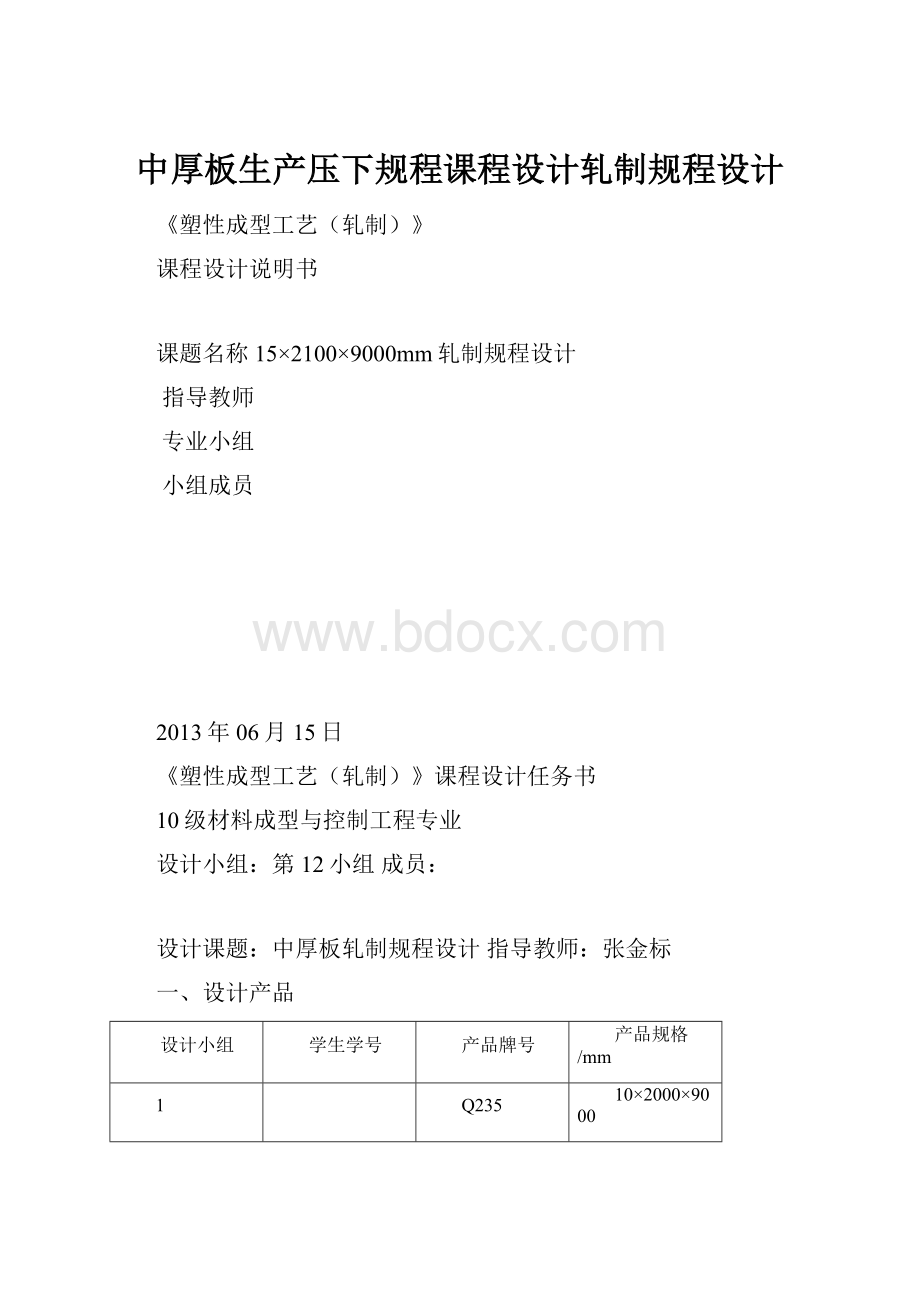
中厚板生产压下规程课程设计轧制规程设计
《塑性成型工艺(轧制)》
课程设计说明书
课题名称15×2100×9000mm轧制规程设计
指导教师
专业小组
小组成员
2013年06月15日
《塑性成型工艺(轧制)》课程设计任务书
10级材料成型与控制工程专业
设计小组:
第12小组成员:
设计课题:
中厚板轧制规程设计指导教师:
张金标
一、设计产品
设计小组
学生学号
产品牌号
产品规格/mm
1
Q235
10×2000×9000
2
45
10×1900×10000
3
12CrNi3A
12×1800×10000
4
4Cr13
13×1700×9000
5
Q235
12×2100×12000
6
45
8×1800×13000
7
12CrNi3A
14×2000×9000
8
4Cr13
12×2000×8000
9
Q235
9×2050×12000
10
45
10×2300×12000
11
12CrNi3A
13×1900×12000
12
4Cr13
15×2100×9000
二、设计条件
机组:
双机架串列式可逆机组(二辊可逆轧机粗轧,四辊可逆轧机精轧)。
主电机:
二辊轧机主电机型号ZD250/120,额定功率2500⨯2kw,转速0~40~80rpm,过载系数2.25,最大允许传递扭矩1.2⨯2MN.m;四辊轧机主电机型号ZD250/83,额定功率2050⨯2kw,转速0~60~120rpm,过载系数2.5,最大允许传递扭矩0.83⨯2MN.m。
三、设计内容
制定生产工艺及工艺制度;确定轧制方法;确定轧制道次,分配道次压下量;设计变形工具;计算力能参数;校核轧辊强度及主电机负荷;绘制轧辊零件图、轧制表。
四、设计时间
设计时间从2013年06月03日至2013年06月14日,为期两周。
五、设计要求
每个设计小组提供6个以上设计方案,1成员完成1个设计方案的全部设计工作;组内分析、评价各个方案的设计结果,以最佳方案作为本组设计方案;小组提交最佳方案的设计说明书1份,组员提交个人的设计小结(简述方案、设计思路、计算过程和结果评价)。
材料成型教研室
2013.05.30
4.2四辊轧机强度校核选工作辊材质为铸铁;支撑辊材料选合金锻钢;
第一章制定生产工艺及工艺制度
1.1制定生产工艺及工艺制度
1.1.1制定生产工艺:
选择坯料→原料清理→加热→除鳞→纵轧二道(使宽度接近成品宽度)→转90°横轧到底→矫直→冷却→表面检查→切边→定尺→表面尺寸形状检查→力学性能试验→标记→入库→发货。
1.1.2制定工艺制度:
在保证压缩比的条件下,坯料尺寸尽量小,加热时出炉温度应在1120-1300℃,温度不要过高,以免发生过热或过烧现象;用高压水去除表面的氧化铁皮;矫直时选用辊式矫直机矫直,开始冷却温度一般要尽量接近纵轧温度,轧后快冷到相变温度以下,冷却速度大多选用5-10°或稍高一些。
切边用圆盘式剪切机进行纵剪,然后用飞剪定尺。
1.2坯料选择
1.2.1选择坯料
根据生产经验和实践,因为连铸坯更加节能,组织和性能好,成材率高;主要用于生产厚度小于80mm中厚板,且目前生产中厚板选择连铸坯已成为主流,所以选择连铸坯。
1.2.2坯料尺寸的确定
1.2.2.1坯料厚度的确定:
产品的厚度h=15mm,首先选取压缩比,压缩比由经验值选取,我国压缩比一般在8以上,考虑到成材率,因此本设计压缩比选取9,则坯料厚度H=135。
1.2.2.2坯料长度的确定:
由成品(b+△b)←坯长L,切头尾△L=90mm,切边△b=25mm,展宽为500~700,取展宽为500mm,则L=(2100+50)-500=1650mm。
1.2.2.3坯料宽度的确定:
金属烧损系数一般为1%,由体积不变定律可得:
99%×H×B×L=(l+2×90)×(b+2×25)×15
带入数据解得:
B=1340mm
校核成材率:
94%
1.3变形量分配
1.3.1轧制方法的确定
先经过二辊轧机纵轧二道,然后转90度,横轧到底。
1.3.2道次压下量的确定
坯料尺寸:
H×B×L=135×1340×1650mm,则总的压下量为135-15=120。
根据经验值选取轧制道次n=12,制定压下规程。
由于开始轧制时受咬入能力限制,所以在轧制前设计一个除鳞箱,保证咬入能力较好,并选取咬入条件较好的经验方法。
道次压下量与道次关系如图1所示。
由图1所示,各道次的压下量逐渐减小,同时幅度也在逐渐减小,所以粗轧的压下量较大,而精轧的压下量较小。
设定总轧制道次为十二道次,粗轧为七道次(选取二辊可逆轧机),精轧为后五道次(选取四辊可逆轧机)。
制定压下规程如表
表1-1
表1-1道次压下量的分配
道次
轧制方式
机架
轧件厚度
h/mm
轧件度宽b/mm
轧件长度l/mm
压下量△h/mm
变形程度ε/%
0
除鳞
高压水
1
纵轧
二辊
2
横轧
二辊
3
横轧
二辊
4
横轧
二辊
5
横轧
二辊
6
横轧
二辊
7
横轧
二辊
8
横轧
四辊
9
横轧
四辊
10
横轧
四辊
11
横轧
四辊
12
横轧
四辊
第二章设计变形工具
2.1二辊轧机尺寸设计
2.1.1辊身长度
由L=bmax+a,又因为bmax=2150mm,当bmax=1000-2500mm时,a=150-200mm(轧钢机械P80),取a=200mm,则L=2200+200=2400mm
2.1.2辊径尺寸
中厚板轧机L/D=2.2-2.8,则D=857-1090mm,取D=880mm
2.1.3辊颈尺寸
查表3-5取d/D=0.75(轧钢机械P81)得d=660mm;
辊颈长度l:
取d/l=1.0得l=660mm
2.1.4辊头设计
因为对于中厚板轧机来说轧辊调整行程比较大,倾角在8°-12°之间所以应选择万向辊头,其各部分的尺寸关系如下:
Dmin=Dmax-Dmax×重车率,中厚板轧机最大重车率5%-8%,取重车率为5%
则Dmin=880-880×5%=836mm
D1=Dmin-(5-15)mm取D1=Dmin-6=830mm
S=(0.25-0.28)D1取S=0.25D1=207.5mm
a=(0.5-0.6)D1取a=0.5D1=415mm
b=(0.15-0.20)D1取b=0.2D1=166mm
c=b=166mm
2.1.5辊颈与辊身的过度圆角r
由r/D=0.1-0.12取r/D=0.1得r=0.1×880mm=88mm
2.2设计四辊
2.2.1支承辊设计
2.2.1.1辊身长度
同前L=2400mm
2.2.1.2辊径尺寸D2
查表(轧钢机械)L/D2=2.0得D2=1200mm
2.2.1.3辊颈尺寸
取d2/D2=0.75则d2=1200×0.75=900mm
辊颈长度l2/d2=1.0则l2=900mm
2.2.1.4辊头设计
选择万向辊头,因为对于中厚板轧机来说轧辊调整行程比较大,倾角在8°-12°之间所以选择万向辊头。
各部分的尺寸关系如下:
Dmin=Dmax-Dmax×重车率取重车率为5%
则Dmin=1200-1200×5%=1140mm
D1=Dmin-(5-15)mm取D1=Dmin-10=1130mm
S=(0.25-0.28)D1取S=0.27D1=300mm
a=(0.5-0.6)D1取a=0.5D1=565mm
b=(0.15-0.2)D1取b=0.2D1=226mm取b=230mm
c=b=230mm
2.2.1.5辊颈与辊身的过度圆角r2=0.1D2=120mm
2.2.2工作辊设计
2.2.2.1辊身设计
同前L=2400mm
2.2.2.2辊径尺寸
根据(轧钢机械P80),当轧件较厚时,由于要求较大工作辊直径,取D2/D1=1.5,得D1=800mm。
2.2.2.3辊颈尺寸
取d1/D1=0.75则d1=600mm
辊颈长度:
取l1/d1=1.0,得l1=600mm
2.2.2.4辊颈与辊身的过度圆角r1
取r1=0.1D1=80mm
2.2.2.5辊头设计
选择万向辊头,选择原因同上。
各部分的尺寸关系如下所示:
Dmin=Dmax-Dmax×重车率重车率取5%,则Dmin=800-800×5%=760mm
D1=Dmin-(5-15)mm取D1=Dmin-10=750mm
S=(0.25-0.28)D1取S=0.28D1=210mm
a=(0.5-0.6)D1取a=0.5D1=375mm
b=(0.15-0.2)D1取b=0.2D1=150mm
c=b=150mm
2.3校核咬入能力
热轧钢板时咬入角一般为15°-22°,低速咬入可取为20°,故△hmax=D1(1-cosa)=43mm,故咬入不成问题。
第一章计算力能参数
3.1选择速度图
由于整个轧制过程中,轧件较长,所以选择梯形图较理想。
3.2设计轧制速度(n1、n2、n3、a、b)
目前,可逆式中厚板轧机粗轧机的轧辊咬入和抛出转速一般在10-20rpm和15-25rpm范围内选择,精轧机的轧辊咬入和抛出转速一般在20-60rpm和20-30rpm范围内选择。
根据经验资料取平均加速度a=40rpm/s,平均减速度b=60rpm/s。
所以在二辊轧机上轧制时,取咬入转速n1=10rpm,n2在四辊轧机上轧制时,取咬入转速n1=20rpm,n23.3速度图(梯形图)
图5-1梯形速度图
3.4计算各道次时间
第一道:
空载加速时间为t1,加速轧制时间为t2,设等速轧制时间为t3,减速轧制时间为t4,空载减速时间为t5
对于二辊轧机
空载加速时间:
t1=n1/a=0.25s
加速轧制时间:
t2=(n2-n1)/a=(30-10)/40=0.5s
等速轧制时间:
t3=1/n2×[n12/2a+60L/πD+n32/2b-n22×(a+b)/ab]=0.17s
减速轧制时间:
t4=(n2-n3)/b=(30-20)/60=0.17s
空载减速时间:
t5=n3/b=20/60=0.33s
所以纯轧时间:
tz=t2+t3+t4=0.5+0.17+0.17=0.84s
如果轧件长度l≤3.5m取间隙时间tj=2.5s;
如果轧件长度3.5m如果轧件长度l>8m取间隙时间tj=4s
所以tj1=2.5s
其他道次的各组成时间如下表所示:
表3-1
道次
t1(s)
t2(s)
t3(s)
t4(s)
t5(s)
tj(s)
tz(s)
t总
1
0.25
0.5
0.17
0.17
0.33
2.5
0.84
43.67
2
0.25
0.5
0.50
0.17
0.33
2.5
1.17
3
0.25
0.5
0.36
0.17
0.33
2.5
1.03
4
0.25
0.5
0.76
0.17
0.33
2.5
1.43
5
0.25
0.5
1.15
0.17
0.33
6
1.82
6
0.25
0.5
1.55
0.17
0.33
6
2.22
7
0.25
0.5
2.43
0.17
0.33
6
3.10
8
0.5
0.5
2.61
0.33
0.33
6
3.44
50.56
9
0.5
0.5
3.25
0.33
0.33
6
4.08
10
0.5
0.5
3.64
0.33
0.33
4
4.47
11
0.5
0.5
4.10
0.33
0.33
4
4.93
12
0.5
0.5
4.66
0.33
0.33
4
5.49
3.5计算各道次轧制温度
为了确定各道次轧制温度,必须求出逐道的温度降。
高温时轧件温度降可以按辐射热计算,而认为对流和传导所损失的热量大致可与变形功所转化的热量相抵消。
由于辐射热所引起的温度降在热轧板、带材时,可用以下公式近似计算:
△t=12.9×Z/h×(T1/1000)4
Z—该道次的轧制时间与上道次间隙时间之和
T1—前一道的绝对温度,K
h—轧出厚度
根据经验,双机架中厚板轧机轧制材料为Q235的钢板时,其粗轧开轧温度为1200℃,精轧的开轧温度为1080℃。
所以第一道温降为:
△t1=12.9×Z/h×(T1/1000)4=12.9×0.84/80×[(1200+273)/1000]4=1℃
精轧开轧温度为1080℃
则△t8=12.9×Z/h×(T1/1000)4=12.9×9.44/15×[(1080+273)/1000]4=27℃
所以第8道轧后轧件温度为:
1080℃-27℃=1053℃
所有道次轧制温度如下表所示:
表3-2
道次
1
2
3
4
5
6
7
8
9
10
11
12
Z(s)
0.84
3.67
3.53
3.93
4.32
8.22
9.10
9.44
10.08
10.47
8.93
9.49
温度(℃)
1200
1199
1166
1160
1152
1136
1114
1080
1049
1014
985
954
3.6计算各道次变形抗力
轧件在二辊轧机上轧制时平均轧制速度为:
V1=Dn2/60=3.14×880×30/60=1382mm/s(n为稳定轧制速度)
轧件在四辊轧机上轧制时平均轧制速度为:
V2=Dn2/60=3.14×800×40/60=1675mm/s(n为稳定轧制速度)
故平均变形程度:
έ=2V/(H+h)×
所以έ1=2×1.382/(100+80)×
=3.3
由έ1和t1查图17-3(金属塑性加工学)得:
σs1=60Mpa,再由ε1=20%得修正系数K=0.98
所以变形抗力σsT1=Kσs1=0.98×60=58.8MPa
其他道次变形抗力如下表所示:
表3-3
道次
1
2
3
4
5
6
7
8
9
10
11
12
έ
3.3
3.7
4.1
4.8
4.8
4.8
7.1
11.4
8.5
6.7
7.3
8.0
ε
20
20
20.31
21.57
17.5
15.15
25
28.57
13.33
7.69
8.33
9.09
T
1200
1199
1166
1160
1152
1136
1114
1080
1049
1014
985
954
σsT
58.8
60.8
61.7
62.7
65.1
71.0
104.0
113.9
92.7
79.8
97.2
103.8
3.7选用Sims公式计算各道次轧制力
求第一道轧制力因为变形抗力K=1.155σsT所以K1=1.155×58.8=67.91Mpa
接触弧长l=
=
=94mm
R/h=440/80=5.5查曲线5-24求外摩擦影响系数n΄σ1
由ε1与R/h,查得n΄σ1=0.8
又因为为无张力轧制所以张力影响系数n΄΄΄σ1=1.0
求外端影响n΄΄σ1,由l/h=1.175,因为在轧制薄板时计算平均单位压力可取n΄΄σ1=1.0,即不考虑外端的影响。
由轧制力计算公式P=n΄σ×n΄΄σ×n΄΄΄σ×K×b×l
则P1=n΄σ1×n΄΄σ1×n΄΄΄σ1×K1×b1×l1=0.8×1.0×1.0×67.914×1.600×0.094=8.17MN同理其它道次轧制力如下表所示:
表3-4
道次
1
2
3
4
5
6
7
8
9
10
11
12
轧制力P(MN)
8.17
9.44
13.11
15
10.9
10.2
20.3
19.9
8.6
5.3
6.4
6.9
第四周校核
4.1二辊轧机强度校核
由上面计算知二辊轧机最大轧制力Pmax=P7=7.14MN
4.1.1求辊身的弯曲力矩Msh
Msh=Pmax(L+l/4-b/8) L—辊身长度,l—辊颈长度,b—轧件长度
则Msh=Pmax(L+l/4-b/8)=7.14×[(2.3+0.45)/4-2.15/8]=2.99MN•m
4.1.2 求辊颈的弯曲力矩Mj
Mj=Pmax•l/4=7.14×0.45/4=0.8MN•m
4.1.3 求辊身的弯曲应力σsh
σsh=Msh/(0.1D3)=2.99/(0.1×0.863)=47Mpa
4.1.4求辊颈的弯曲应力σj
σj=Mj/(0.1d3)=0.8/(0.1×0.53)=64.3Mpa
4.1.5 求辊颈的扭转力矩Mn
Mn=Pφ
=0.27MN•mΔh—最大轧制力时的压下量
4.1.6求辊颈的扭转应力τj
τj=Mn/(0.2d3)=0.27/(0.2×0.53)=10.6Mpa
4.1.7求合成应力σh
对于钢轧辊σh=
=66.9Mpa
4.1.8辊头的弯曲应力
K由图7-21查得K=1.215
b0=2
=867.8mm;b=1.5s=1.5×240=360mm;x=0.5(b0-2b/3)sinα+x1=303.4mm;
σj=60MKx/(b0-2b/3)bs2=60×0.27×1.215×303.4/627.8×360×2402=45.07Mpa
4.1.9轧辊材料选择
已知σsh=47Mpa;σj=64.3Mpa;σh=66.8Mpa所以由表6-1(轧钢车间设备潘慧勤主编)
表6-1
材料
合金锻钢
碳素锻钢
铸钢
铸铁
球墨铸铁
强度极限σb
686—735
588—637
490—588
343—392
392—588
许用应力[σ]
137.2—149
117.6—127.4
98—117.6
68.6—78.4
78.4—117.6
材料的抗拉强度σb=686—735Mpa取σb=700Mpa
因为σb/σsh=700/66.3=10.56>3所以辊身安全符合要求;
σb/σj=700/64.3=10.89>3所以辊颈安全符合要求
σb/σh=700/66.8=10.48>3所以安全
4.2四辊轧机强度校核选工作辊材质为铸铁;支撑辊材料选合金锻钢;
由上面计算知四辊轧机最大轧制力Pmax=5.43MN
4.2.1支撑辊强度校核
4.2.1.1辊身
Msh2=P(L+l/4-L/8)=5.43×;[(2300+600)/4-2300/8]=2.38MN•m
则σsh2=Msh2/(0.1D23)=2.38/(0.1×9403)=28.11Mpa
因为σb/σsh2=686/28.11=24.4>3所以辊身安全;
4.2.1.2辊颈
Mj2=P/4×l2=5.43/4×0.6=0.81MN•m
则σj2=Mj2/(0.1d23)=0.81/(0.1×0.73)=23.75Mpa
因为σb/σj2=686/23.75=28.89>3所以辊身安全;
4.2.1.3辊头无校核内容
4.2.2工作辊强度校核
4.2.2.1辊身
由于有支承辊承受弯曲力矩,故工作辊只考虑扭转力矩。
在轧制过程中前后张力差不大,工作辊辊身不需要校核。
4.2.2.2辊颈
Mn=Pφ
=0.14MN•m
Δh—最大轧制力时的压下量
τj1=Mn/(0.2d13)=16.15Mpa;
[σ]=70~80Mpa;
4.2.2.3辊头
K由图7-21查得K=1.19
b0=2
=493.2mm
α=8°
X1=a/2=150mm
S=130mm
b=1.5S=195mm
x=0.5(b0-2b/3)sinα+x1=175.4
σj=60MKx/(b0-2b/3)bs2=14.5Mpa<[σ]=70~80;
满足要求
4.2.2.4接触应力计算
σmax=
σmax=884.19MPa
因为支承辊表面硬度Hs=40~50[σ]=2100Mpa[τ]=640Mpa所以验算通过。
4.3计算各道次轧制力矩
MZ=2P
=2P
l
式中:
φ—力臂系数,一般取0.4—0.6,这里取0.5 ,
l—接触弧长
所以MZ1=2×0.5×88.4×2.13=0.19MN•m
其他各道次计算值见表
4.4 附加摩擦力矩确定
4.4.1轧辊轴承中的附加摩擦力矩Mm1=pfd
d—轧辊辊颈直径;
f—轧辊轴承摩擦系数;
滚动轴承f=0.003;
摩擦轴承f=0.01~0.02;
对于二辊:
Mm1=2.13×0.003×0.5=0.0032MN•m;
其他各道次计算公式相同,其结果见表;
对于四辊:
Mm1=pfd(Dg/Ds)
Dg—四辊轧机工作辊直径520mm;
Ds—四辊轧机支承辊直径1000mm;
Mm1=5.439×0.01×0.7×520/1000=0.019MN•m;
其他各道次计算值见表
传动机构中的摩擦力矩
Mm2=(1/ŋ-1)(Mz+Mm1)/i
ŋ—传动机构的效率为0.85
i—传动比取0.1
第一道次Mm2=(1/0.85-1)(188.3+3.19)/1=0.338MN·m
其他各道次计算值见表
4.4.2附加摩擦力矩的计算
二辊:
Mm=Mm1/i+Mm2
Mm1—轧辊轴承中的附加摩擦力矩
Mm2—传动机构中的摩擦力矩
第一道次Mm=3.19/1+33.79=36.98KN·m
四辊:
Mm=Mm1D工/iŋD支+(1/ŋ-1)Mz/i
第八道次Mm=0.604MN·m
其他各道次计算值见表
4.5电动机额定力矩的计算
二辊轧机主电机额定力矩计算
MH1=9550NH1/nH1=9550×2500×2/80=596.9KN·m
四辊轧机主电机额定力矩计算
M