液压挖掘机讲座一.docx
《液压挖掘机讲座一.docx》由会员分享,可在线阅读,更多相关《液压挖掘机讲座一.docx(18页珍藏版)》请在冰豆网上搜索。
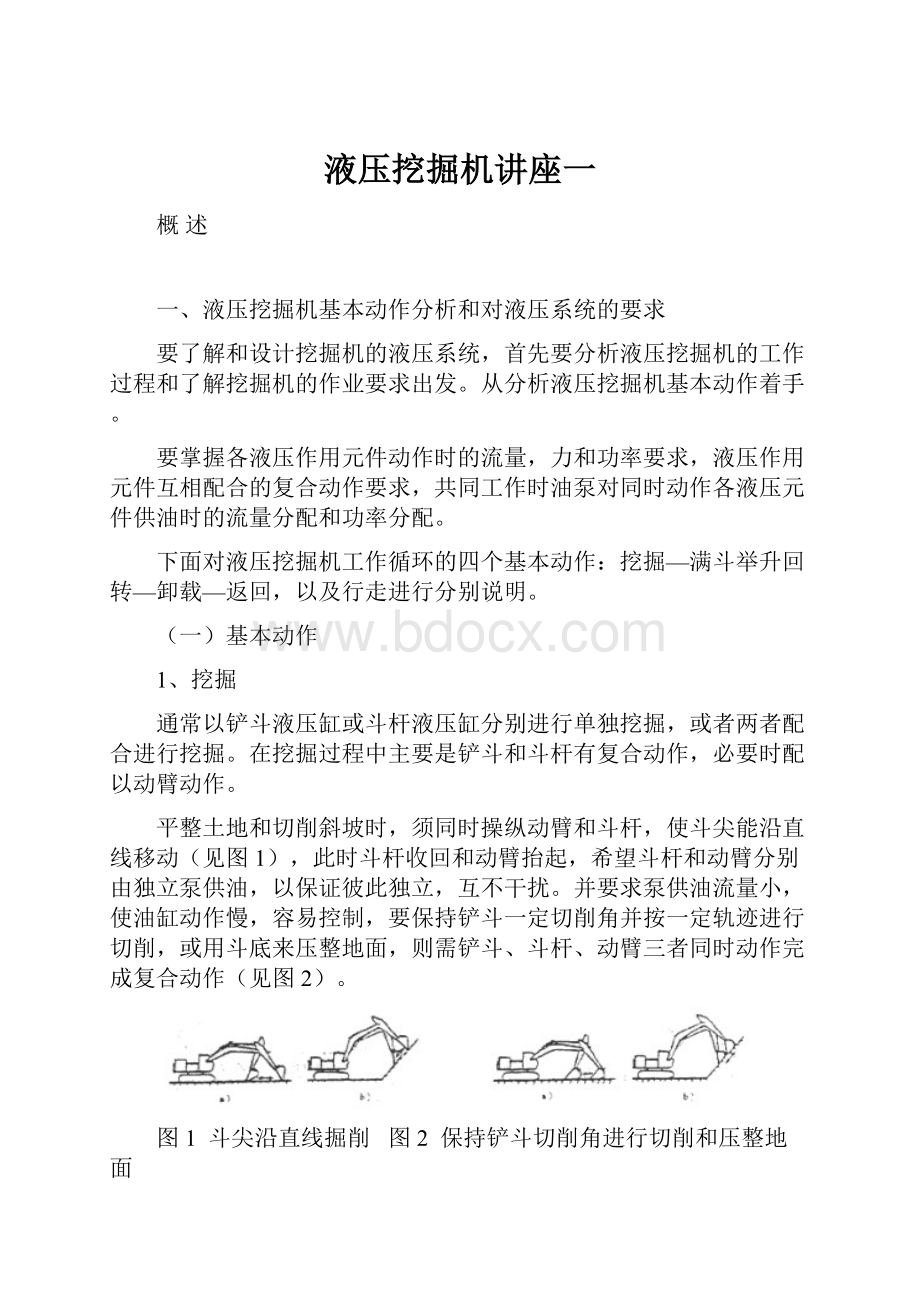
液压挖掘机讲座一
概述
一、液压挖掘机基本动作分析和对液压系统的要求
要了解和设计挖掘机的液压系统,首先要分析液压挖掘机的工作过程和了解挖掘机的作业要求出发。
从分析液压挖掘机基本动作着手。
要掌握各液压作用元件动作时的流量,力和功率要求,液压作用元件互相配合的复合动作要求,共同工作时油泵对同时动作各液压元件供油时的流量分配和功率分配。
下面对液压挖掘机工作循环的四个基本动作:
挖掘—满斗举升回转—卸载—返回,以及行走进行分别说明。
(一)基本动作
1、挖掘
通常以铲斗液压缸或斗杆液压缸分别进行单独挖掘,或者两者配合进行挖掘。
在挖掘过程中主要是铲斗和斗杆有复合动作,必要时配以动臂动作。
平整土地和切削斜坡时,须同时操纵动臂和斗杆,使斗尖能沿直线移动(见图1),此时斗杆收回和动臂抬起,希望斗杆和动臂分别由独立泵供油,以保证彼此独立,互不干扰。
并要求泵供油流量小,使油缸动作慢,容易控制,要保持铲斗一定切削角并按一定轨迹进行切削,或用斗底来压整地面,则需铲斗、斗杆、动臂三者同时动作完成复合动作(见图2)。
图1斗尖沿直线掘削图2保持铲斗切削角进行切削和压整地面
为提高掘削速度,采用斗杆挖掘时,一般采用双泵合流(个别采用了3泵合流)。
铲斗单独挖掘时,也有采用双泵合流(特别是大型挖掘机)。
下面以3泵系统来说明复合动作挖掘时,油泵流量分配和分合流油路连接供油情况。
当斗杆和铲斗复合运动挖掘时,供油情况如图3所示,斗杆油压接近溢流阀压力时,原来溢流的油供给铲斗有效利用。
图3斗杆和铲斗复合挖掘时供油情况图4斗杆和动臂复合动作时供油情况
当斗杆和动臂复合动作时,因动臂仅是起调整位置作用,主要是斗杆挖掘,因此采用斗杆优先合流,双泵供油,如图4所示。
当动臂、斗杆和铲斗复合运动时,为了防止同泵供油,相互动作干扰,对三泵系统,各泵单独供一个液压作用元件较好。
对2泵系统,复合动作相互干扰可能性大,需采用节流等措施进行流量分配,其流量分配要求和3泵系统相同。
进行沟槽侧壁掘削和斜坡整修时,为进行有效的垂直掘削,要求向回转马达提供压力油,产生回转力,保持铲斗贴紧侧壁进行切削,因此需回转和斗杆同时供油,一起动作,如图5所示。
图5沟槽侧壁掘削
回转和斗杆收缩同时动作,由同一泵供油,需采用回转优先油路,否则油流向压力低处,使得掘削时紧贴侧臂很困难。
在斗杆油缸活塞杆端回油路上设置可变节流阀,此阀开口大小和节流程度由回转先导压力来控制,回转先导压力大,节流大,则斗油缸回油压力增高,使泵供油压力提高。
因此随着回转操纵杆行程增大,回转马达油压增加,回转力增大。
在挖掘过程中,有可能碰到石块和树根等,往往挖不动,需短时增大掘起力时,希液压系统能暂时增压,把主压力阀压力提高,增力把障碍物挖掉。
2、满斗举升回转
挖掘结束后,动臂缸将动臂顶起,满斗提升,同时回转液压马达使转台转向卸土处。
此时主要是动臂和回转的复合动作。
动臂举升和回转同时动作时,两者要求在速度上匹配,要求回转到指定卸载位置时,动臂和铲斗自动举升到正确地卸载高度。
由于卸载所需回转角角度是不同的,随挖掘机相对自卸车的位置而变,因此动臂举升速度和回转速度相对关系应该是可调整的。
卸载回转角度大,则要求回转速度快些,而动臂举升速度慢些。
在回转起动时,由于惯性较大,油压会升得很高,有可能从溢流阀溢出,此时应将溢流的油供给动臂如图6所示
图6动臂和回转同时动作图7工作装置同时动作图8工作装置同时动作(3泵系统)
在回转举升时,除了动臂举升外,斗杆要同时外放,有时还需对铲斗进行调整,此时是回转、动臂、斗杆和铲斗进行复合动作。
由于满斗举升时动臂油缸压力高,导致变量泵流量减小,为使动臂举升和回转、斗杆外放相配合,因此除一个泵专供动臂缸以外,另一泵除供回转和斗杆外,另有部分油供动臂,如图7所示,但由于动臂举升油压较高,大部分时间单向阀是关闭的,左泵只供回转和斗杆
3泵系统供油情况如图8所示。
各泵分别供给一液压动作元件,动作无干扰。
回转运动一般所需流量较小,宜采用较小流量泵,用大流量泵驱动,在启动和制动过程中转动惯量很大,产生功率损失较大。
3、卸载
转至卸土位置时,转台制动,用斗杆调节卸载半径和卸载高度,用铲斗缸卸载。
为了调整卸载位置,还需动臂配合动作。
卸载时,主要是斗杆和铲斗复合作用,间以动臂动作。
4、空斗返回
卸载结束,转台反向回转动臂,同时动臂缸和斗杆缸相配合动作,把空斗放到新的挖掘点。
此工况是回转、动臂和斗杆进行复合动作。
动臂下降有重力作用,压力低,变量泵流量大,下降快,要求回转速度快,因此该工况的供油情况是:
一个泵全部流量供回转,另一泵大部分油供动臂,少部分油经节流供斗杆如图9所示。
图9空斗返回同时动作
当发动机在低转速时,油泵供油量小,为防止动臂因重力作用迅速下降,动臂油缸产生吸空现象,可采用动臂下降再生补油,利用重力将动臂缸的油缸腔的油供至活塞杆腔。
5、行走时复合动作
在行走的过程有可能要求作业装置液压元件(回转、动臂、斗杆和铲斗)动作进行调整。
在双泵系统,一泵供左行走,另一泵供右行走。
此时如某一液压元件动作,使某一泵分流供油,就会造成一侧行走速度降低,影响直线行驶性。
特别是当挖掘机进行装车运输,上下卡车行走时,行驶偏斜会造成事故。
为了保持直线行驶性:
(1)对三泵系统供油情况如图10所示,左右行走分别一泵供油,另一泵供作业液压作用元件(动臂、斗杆、铲斗和回转)
图10行走时三泵供油情况图11一泵供行走,一泵供作业图12双泵合流并联向作业和行走供油
(2)双泵系统:
目前液压挖掘机采用以下方式:
a.一泵并联供左右行走,另一泵供作业液压作用元件,供作业装置液压作用元件多余的油,可通过单向阀向行走供油,如图11所示
b.双泵合流并联向左、右行走马达和作业装置液压作用元件同时供油,如图12所示。
(二).液压挖掘机对液压系统的性能要求
液压挖掘机具有多种机构:
行走、回转、动臂、斗杆和铲斗等、多自由度,液压作用元件数量多,要求实现的动作很复杂,对液压系统提出了很高的要求,挖掘机的液压系统是工程机械液压系统中最复杂的。
挖掘机液压系统的主要要求:
1.操纵控制性能要求高,各作用元件的调速性要好,精细作业要求微动,高生产率要求快速动作,调速范围要求广,作业阻力变化大,各种不同作业工况所需功率变化范围大。
2.挖掘机作业需各液压作用元件单独动作,但更多情况下要求各作用元件互相配合实现复合动作,而且动臂、斗杆、铲斗、回转和行走之间几乎都要复合动作,复合动作范围广,形式多样复杂,同时要求复合动作时有良好的复合操纵性能,能合理地分配共同动作时各液压作用元件的流量和功率。
为了实现这些要求液压系统必须采用各种措施,因此液压系统很复杂。
3.挖掘机作为生产设备,工作时间长,能量消耗大,要求液压系统效率高,节能降低能耗和排放,使总发热量小,液压油温不要太高,因此对各液压元件和管路都要求降低能耗。
在液压系统中要充分考虑节能措施。
4.提高挖掘机生产效率很重要,液压系统要考虑能与发动机很好匹配,能充分利用发动机全功率。
5.挖掘机工作条件恶劣,载荷变化剧烈,冲击振动大,对各液压元件的可靠性和耐久性有很高的要求。
二液压挖掘机液压回路的基本类型
液压挖掘机液压系统很复杂,形式和种类很多,可以从不同的角度进行分类,下面从阀和泵两方面进行分类。
(一)从多路阀的型式来看:
可以分成两大类
1.中位开式系统:
采用六通阀,该阀特点是有两条供油路,一条是直通供油路,另一条是并联供油路,如图13所示
图13开式油路
这种油路调速方式是进油节流和旁路节流同时起作用的形式,其调速性能差,调速特性受负荷压力和油泵流量的影响。
因此这种阀系统操纵性能差。
同时这种油路系统的液压作用元件一起复合动作时,相互间有干扰,使得复合动作操纵非常困难。
对液压挖掘机来说调速性能和复合动作操纵性是很重要的,因此这是中位开式系统的大缺点。
2.中位闭式负荷传感压力补偿系统
图14闭式油路
闭式油路如图14所示,可以采用一个泵同时供给所有液压作用元件,每一个液压元件动作速度只和操纵阀的阀杆行程有关,与负荷和泵流量无关,多个液压元件同时动作时相互无干扰。
操纵性好是闭式油路的主要优点。
3.开式和闭式油路的对比
开式油路主要问题是:
阀调速特性随负荷波动;多负荷同时工作互相干扰,液压元件最大速度不能任意设定。
这些问题采用闭式油路后都可以解决,而且对各种附属装置适应性强,根据附属装置需要,可以通过调整补偿程度来实现完全补偿特性、接近开式油路特性和中间状态特性。
闭式油路主要问题是:
动态性能差,目前已有改进措施;有人认为压力补偿产生压差会使系统效率降低,能量损失大。
根据日本小松在10T级和20T级二种挖掘机所作实际测试结果,作业效率以每小时土方量来表示:
以开式油路为1,对闭式油路,10T级为1.04,20T级为1.13;燃料消耗量以每升燃料的土方量来表示:
以开式油路为1,对闭式油路,10T级为1.02,20T级为1.09。
结论是闭式回路的作业效率高,燃料消耗量低,因此日本小松把大量挖掘机从开式油路改为闭式油路。
(二)从泵的型式和控制方式来看
1.泵的数量:
单泵、双泵、三泵和多泵
采用液压泵的数量多少要考虑以下因素:
(1)液压传动的缺点是遵守“帕斯克”原理,泵的油压按共泵供油液压元件的最高压力来确定,多液压元件同时工作所需油压不同,必然存在压差损失,从这点来看,油泵数宜多。
(2)通常中位开式系统,泵数量增加,可以不受相互干扰的独立动作的液压元件数目增多。
双泵系统由于只有两个泵,只能保证二个动作完全独立,三个液压元件同时复合动作时,必然失去相互动作的独立性,产生动作不确定性的缺点,三泵系统可实现三个动作独立。
(例如:
三泵能使回转、动臂和斗杆三者独立动作),从而使挖掘机操纵性提高。
(3)但液压泵数量增多,液压零部件数量增加,泵的驱动麻烦,泵的结构也较复杂,变量泵的控制比较困难,制造成本提高,液压回路损失也会增大,对经济性和可靠性不利。
液压系统泵的数量的选取,主要应该考虑同时动作的需要,日本厂商挖掘机油路中主要考虑二个液压作用元件同时动作情况居多,因此采用双泵系统较多。
欧美国家为保证回转作业的独立性(特别是用于起重作业),采用3泵系统,回转油路采用排量较小的定量泵或变量泵。
液压小挖掘机工作装置往往增加了推土板和动臂偏转二个液压作用元件,液压作用元件数较多,因此不少采用三泵系统。
大型和特大型挖掘机因为所需的流量和功率大,只能采用多个泵组合。
一般来说一个泵采用一个阀块,双泵采用二个阀块,即2P2V系统,三泵三个阀块,即3P3V系统。
2.泵的型式:
定量泵和变量泵
定量泵结构简单、制造方便,用于需要价格便宜的微型挖掘机。
但定量泵角功率大(最大压力乘最大流量),要求发动机功率大,使发动机功率利用率低,影响生产率。
同时定量泵不能按需变流量供油,功率损失大,因此油耗高、经济性差和排放不好。
从挖掘机作业要求来说应该采用变量泵。
3.泵的控制方式
节能控制方式:
有负流量控制、正流量控制和负荷敏感压力补偿控制三种,目前挖掘机都选用其中一种控制方式来实现节能要求。
与发动机匹配控制方式:
有压力感应控制和转速感应控制,目前挖掘机一般都具有这两种控制方式。
另外一般液压挖掘机还有工况控制、自动怠速控制、平稳操纵控制和自动掘削控制等。
三、中位开式多路阀设计布置
(一)、多路阀内阀杆油路连通方式有串联式、并联式、优先式(串并联)三种。
1.串联式:
如图15所示
前联换向阀的回油口和后联换向阀的进油口相连,串联油路的特点可以实现两个和两个以上液压动作元件同时动作。
液压泵的工作压力是同时工作液压元件压力的总和。
图15串连油路
在初期挖掘机上曾采用过这种油路。
但是挖掘机一般都在重负荷下工作,为了使结构紧凑,减轻重量,每个液压作用元件都按液压泵压力设计,不允许两个液压元件串联工作,因此串联油路目前在挖掘上不采用。
2.并联式
液压泵出口压力油并联供给各阀杆,各阀回油并联相通回油箱并联油路特点是多阀杆同时动作时,泵供油首先进入负荷压力最低的液压元件,负荷高的液压元件由于压力低不能动。
要实现多液压元件同时动作,必须通过阀杆节流,控制去各液压元件的流量来实现同时动作时的调速。
因此并联方式要实现复合动作,须有高超的技术,而且不稳定,随各液压元件负荷变化情况和发动机转速等因素变化。
可以说该油路实现同时复合动作较困难。
3.优先式(串并联式)
液压泵出口压力油顺序供油,上游的阀杆打开进行工作时,就把下游阀杆的进油路切断了,因此下游阀就得不到液压泵压力油,就无法动作。
优先阀回油路并联回油,虽然如果上游阀杆不在最大开度位置,部分油会通过节流口流向下流阀,存在下流阀控制的液压元件动作的可能性。
但是严格来说优先油路只能一个液压作用元件动作。
因此在挖掘机上不能全部采用优先油路,只能采用局部优先油路。
如图四所示,右边二个阀组采用行走优先油路,当行走阀操纵时,下游阀的供油被切断,这样就可防止下游阀杆动作,使泵分流,使左右行走马达供油不均,破坏直线行驶性。
目前开式油路采用六通阀,有两条供油通路:
直通供油道:
在阀杆中位时,该油道通,可通过各阀杆回油箱,实现中位卸载功能,该供油道是优先式油道,在各阀杆之间可组成优先油路,上游阀杆动作,切断此油道,下游阀杆得不到供油。
并联供油道:
并联地向各阀杆供油,在各阀杆之间组成并联油路。
目前挖掘机上采用的开式油路都是两者组合油路,利用不同的组合方式,可以形成各种形式并联和优先复杂组合的油路系统。
进一步还可以在直通供油道和并联供油道中加上液控阀和电控阀,可实现更为复杂供油关系的阀组,来满足挖掘机复杂多样的作业工况要求。
(二)日立OHS液压系统(OptimumHydraulicSystem)
早期挖掘机的液压系统的改进,主要是在多路阀直通供油和并联供油的联通方式上,和增加一些合流阀和直线行走阀等,使得液压系统更好的符合作业要求、作业过程各工况要求。
OHS系统是日立80年代设计的液压系统,当时自称是最优液压系统。
该液压回路是并联油路和优先油路的组合,充分考虑动臂、斗柄、铲斗、回转和行走复合动作要求而设计的一个实例。
如图16所示。
图16OHS液压系统
P2泵供右阀组,该阀组行走阀优先,下面是备用、动臂和铲斗三阀并联,下游是斗杆阀。
P1泵供左阀组,该阀组连接关系较复杂,回转阀和动臂阀之间联通关系是并联加优先,回转和动臂上升是并联关系,回转和动臂下降是优先关系。
回转和斗杆、行走三者并联,但通往斗杆进油路节流,通往行走阀进油路有单向阀和节流口。
该液压系统具有以下功能:
1、作业过程中
1)动臂和斗杆单独动作,可实现阀外双泵合流供油。
2)回转和动臂举升同时动作时,P2单独供动臂,P1并联供油给回转和动臂,使回转加速时不产生溢流阀溢流。
回转和动臂下降同时动作时,P1供油给回转,不向动臂供油,仅P2供油给动臂,由于两泵分别给回转和动臂,油路上互相独立,这样就避免了油路相连,由于动臂重力快速下降,建立不起油压,使回转加速性能差的缺点。
3)回转和斗杆同时工作时,P1并联供油给回转和斗杆(经节流孔),P2供油给斗杆。
4)回转、动臂、斗杆三者同时工作时,P1并联供油给回转、动臂和斗杆(经节流孔),P2供油给动臂。
5)回转、动臂、斗杆、铲斗四者同时工作时,P1并联供油给回转、动臂和斗杆(经节流孔),P2供油给动臂和铲斗。
2、在行走过程中,回转、动臂和斗杆三者中只要有一个动作就会产生先导油压,作用在合流阀上,使合流阀处于通路状态。
此时P2并联供左右行走,P1供回转、动臂和斗杆。
当P1压力高于行走油压P2时,P1通过单向阀和节流孔也可与P2合流向行走供油,保证行驶的直线性。
由于采用优先油路,行走时铲斗阀杆操纵,不会影响行驶直线性,但由于铲斗供油路被切断,不能动作,即行走和铲斗不能同时动作。
(三)、多路阀的阀组分块和分泵供油
液压挖掘机按泵分阀组供油,挖掘机六个液压作用元件(动臂、斗杆、铲斗、回转和二个行走马达)。
在通常的双泵供油时分成两个阀块,分别控制三个液压作用元件,考虑到需要经常同时动作的液压元件,不要由同泵供油,因此最常用的分组方式是
回转、斗杆和行走在一个阀组,由一个泵供油
动臂、铲斗和行走在一个阀组,由一个泵供油
这是因为动臂和回转、斗杆和铲斗需经常同时动作和左右履带要求分别驱动。
(四)、合流问题
为了提高挖掘机生产效率,缩短作业循环时间,要求动臂提升,斗杆收放和铲斗转动有较快的工作速度,要求能双(多)泵合流供油,一般中小型挖掘机动臂液压缸和斗杆液压缸均能合流,大型挖掘机的铲斗液压缸也要求合流。
这是挖掘机油路系统设计中需要考虑的问题。
目前采用的合流方式有以下几种:
1.阀外合流,如图17所示
图17阀外合流油路
该油路是并联油路和优先油路的组合,两阀组都前三阀杆并联连接,然后与第四阀杆优先方式联结。
这样合流方式,合流的液压作用元件由两个阀杆供油,该两阀杆分别布置在两个阀组中,由两泵分别供油。
合流供油的液压元件,由两个阀杆供油,由先导液压操纵油路联动打开两阀杆,压力油通过阀外管道连接合流供给液压作用元件。
合流的阀杆被布置在优先油路的下游,当其他液压元件动作时,油流就被切断,不能实现合流。
图17方案斗杆是单独的一个合流阀杆,因此斗杆操纵收放两个方向都能合流供油。
而动臂和铲斗是合用一个合流阀杆,因此动臂只能举升时合流下放时不合流。
铲斗只在挖掘时合流,卸载时不合流。
阀外合流,操纵阀数量增多,需要通过阀外管道来连接,管道和接头数量增多,使用上不方便。
2.阀内合流,泵和阀块的连接、阀杆的布置如图18所示,用于小挖掘机上,有三个泵和三组阀,通过连接板把所有阀连成整体。
合流的油道在内部沟通。
图18阀内合流油路(Husco)
动臂和铲斗单独动作时,泵P1和泵P2可合流供油给动臂缸或铲斗缸,为双泵合流。
斗杆单独动作时,泵P1、泵P2和泵P3可合流供油给斗杆缸,为三泵合流。
不行走时P3可单独供回转;行走时P1和P3分别供给行走马达;P2供给动臂、斗杆和铲斗,不影响直线行驶性,但行走时进行回转动作,P3分流供回转,将影响直线行驶性。
阀内合流,外面管路连接简单,但内部通道稍复杂。
阀杆直径流通面积的设计要综合平衡考虑,各种分合流供油情况下通过的流量。
照理说斗杆阀杆是三泵合流可能通过的流量最大,阀杆直径应该设计的大些。
但从设计制造角度考虑,最好是各阀杆尺寸取得一样。
3.用合流阀供油(如图19所示)。
阀外合流,采用连动操纵的两个操纵阀杆,分别将两个泵的油供给液压元件。
使操纵阀杆数增多,有的挖掘机油路采用结构较简单的合流阀代替一个操纵阀来实现合流。
图19中增加了一个动臂合流阀和一个斗杆合流阀,它们分别布置在两液压泵供油阀块的下游。
图19合流阀合流油路(CAT)
当动臂阀在先导操纵油压A作用下,处于动臂缸大腔进油位置,该先导操纵油压A同时作用在动臂合流阀上,使该阀处于图下位,后泵的油就会通过动臂合流阀和单向阀通向动臂大腔和前泵通过动臂阀流向动臂大腔的油合流。
当动臂阀在先导操纵油压B作用下,处于动臂缸活塞杆进油位置时,由于油压B不作用于动臂合流阀,因此仅前泵供动臂缸,无合流作用。
当斗杆阀在先导操纵油压作用下,斗杆油缸动作时(收或放),该先导作用油压同时作用于斗杆合流阀上,使斗杆合流阀处于上位关闭状态,通过右阀块各阀流向回油的油被切断,这样不仅后泵供给斗杆油腔,前泵也通过单向阀供油给斗杆阀起合流作用。
动臂合流属于阀外合流,在通向动臂油缸大腔处合流。
斗杆合流属于阀内合流,两个泵的油合流后进入斗杆操纵阀。
(五)、行走和工作装置同时动作时直线行驶性问题
双泵液压系统,挖掘机行驶时往往一个油泵供左行走马达,另一个油泵供右行走马达,如果在行驶中需要工作装置动作,就会造成将其中一个油泵的油分流供其他液压作用元件,使该泵供油的行走马达速度降低,形成挖掘机意外偏转造成事故(特别是上下装载卡车时)。
这也是挖掘机油路系统设计中需考虑的问题。
1.CAT直行阀系统
为了实现工作装置同时动作时直线行驶性问题,一般采用直行阀,图19表示CAT系统直行阀的布置,图20为直行阀工作原理图。
在行驶过程中,当作业装置(动臂、斗杆、铲斗和回转)任一动作时,作业装置先导操纵油压就会作用在直行阀上,克服弹簧力,使直行阀处于上位,这时油路连接如图20所示。
图20直行阀工作原理图(CAT)
前泵并联供左右行走
后泵并联供回转、斗杆、铲斗和动臂
后泵还可通过单向阀和节流孔和前泵合流供给行走
(a)液压系统(b)直行阀工作原理
图21NaBco液压系统和直行阀原理图
2.NABCO挖掘机油路直行阀系统
图21为NaBco液压系统和直行阀原理图,它由三个泵、八个操纵阀杆和一个直行阀组成,左右行走、铲斗、斗杆和动臂阀五个阀杆上,有控制先导油的阀道,其作用是自动控制直行阀起作用。
直行阀一端受弹簧力作用,另一端受先导油压PP作用,当先导油卸压,在弹簧力作用下,直行阀在上位,不起作用,当先导油压PP建立了油压,克服了弹簧力,使直行阀处于下位,直行阀起作用。
直行阀是与其他阀杆动作联动的,在铲斗、动臂、斗杆和行走等阀杆中,都具有控制先导油PP通或断的阀道。
当左行走阀杆在中位,PP油通过它通回油卸压;
当右行走阀杆在中位,PP油通过它通回油卸压。
PP能通过行走阀杆(不管它处于什么位置)到斗杆阀,如斗杆阀处于中位,能通过它至铲斗阀。
如铲斗阀在中位,能通过它至动臂阀,如动臂阀在中位,能通过它回油卸压。
作用在直行阀上的先导油压PP,只要满足下列一个条件就卸压回油:
(1)右行走阀有一个在中位。
(2)动臂、铲斗和斗杆阀都处于中位。
反过来说,要使直行阀处于下位起作用的位置,必须要两行走阀离开中位处于操纵位置,同时动臂、铲斗和斗杆三个阀至少有一个离开中位处于操纵位置,即当行走和作业同时操纵时,直行阀自动起作用。
在直行阀起作用时,P1泵和P2泵合流,分别经过节流孔,并联供油给两侧行走马达和作业装置(动臂、铲斗和斗杆),注意回转是单独P3供油,不受行走影响。
上面两种保证直线行驶系统,CAT直行阀系统比较好,因为它保证单泵只供行走,有单向阀阻止流向其他作业装置。
另外一泵供给其他的作业装置,多余的油还可以通过单向阀供给行走,因此作业装置的动作操纵不会影响行走。
而NaBco液压系统,直行阀起作用时,液压泵与行走和作业装置是并联供油关系,因此工作装置动作就可能引起行走速度波动。
四.挖掘机液压系统的组成
挖掘机液压系统可以划分为下述4个部分:
(一)各液压作用元件液压子系统:
包括动臂、斗杆、铲斗、回转和行走液压系统,还有许多附属装置液压系统,因不属于基本装置就不准备讨论了;
(二)多路阀液压系统;
(三)液压泵及其控制系统(包括与发动机综合控制);
(四)多路阀操纵和控制系统(包括液压操纵和电操纵);