TPM全面改善的案例.docx
《TPM全面改善的案例.docx》由会员分享,可在线阅读,更多相关《TPM全面改善的案例.docx(8页珍藏版)》请在冰豆网上搜索。
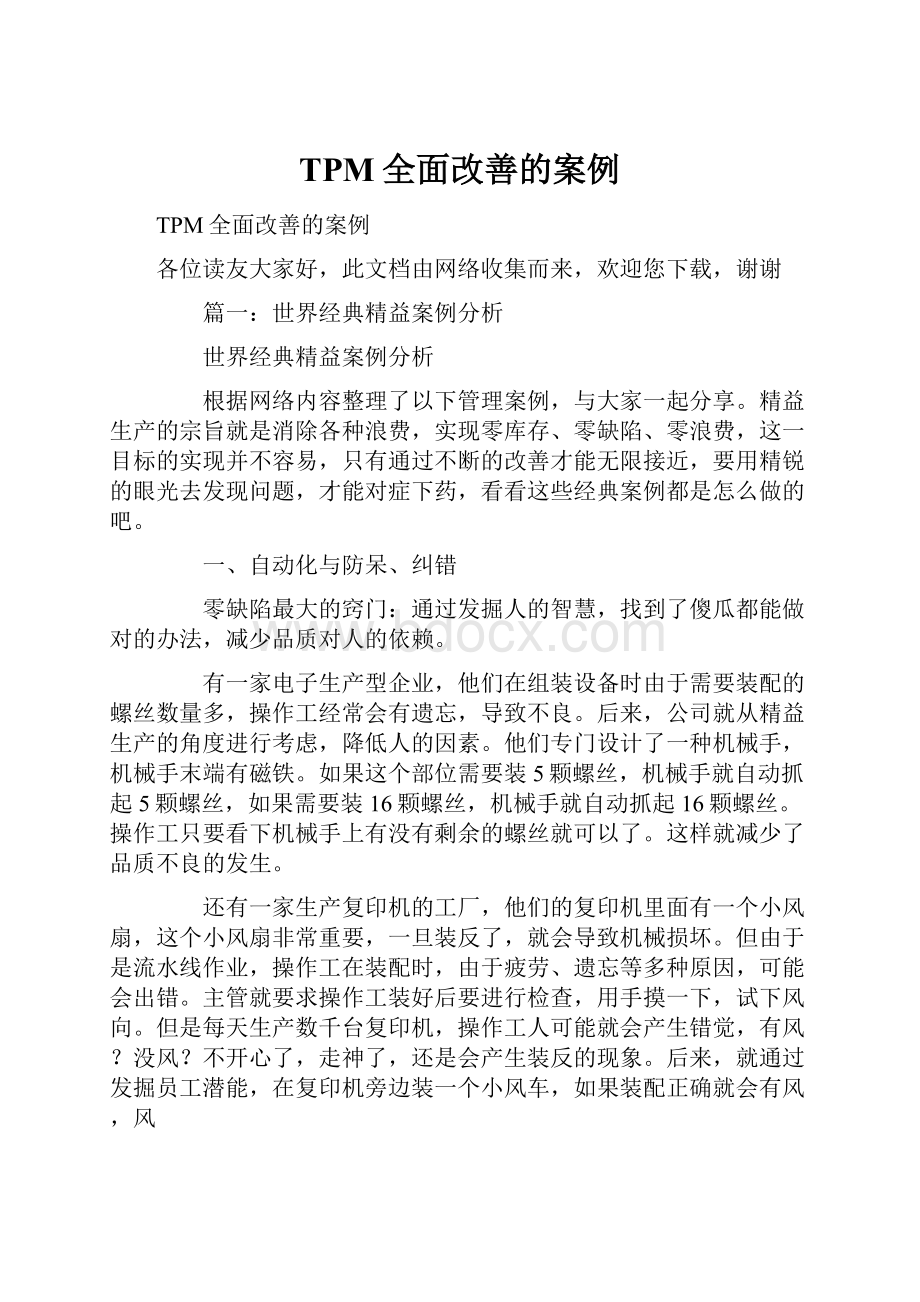
TPM全面改善的案例
TPM全面改善的案例
各位读友大家好,此文档由网络收集而来,欢迎您下载,谢谢
篇一:
世界经典精益案例分析
世界经典精益案例分析
根据网络内容整理了以下管理案例,与大家一起分享。
精益生产的宗旨就是消除各种浪费,实现零库存、零缺陷、零浪费,这一目标的实现并不容易,只有通过不断的改善才能无限接近,要用精锐的眼光去发现问题,才能对症下药,看看这些经典案例都是怎么做的吧。
一、自动化与防呆、纠错
零缺陷最大的窍门:
通过发掘人的智慧,找到了傻瓜都能做对的办法,减少品质对人的依赖。
有一家电子生产型企业,他们在组装设备时由于需要装配的螺丝数量多,操作工经常会有遗忘,导致不良。
后来,公司就从精益生产的角度进行考虑,降低人的因素。
他们专门设计了一种机械手,机械手末端有磁铁。
如果这个部位需要装5颗螺丝,机械手就自动抓起5颗螺丝,如果需要装16颗螺丝,机械手就自动抓起16颗螺丝。
操作工只要看下机械手上有没有剩余的螺丝就可以了。
这样就减少了品质不良的发生。
还有一家生产复印机的工厂,他们的复印机里面有一个小风扇,这个小风扇非常重要,一旦装反了,就会导致机械损坏。
但由于是流水线作业,操作工在装配时,由于疲劳、遗忘等多种原因,可能会出错。
主管就要求操作工装好后要进行检查,用手摸一下,试下风向。
但是每天生产数千台复印机,操作工人可能就会产生错觉,有风?
没风?
不开心了,走神了,还是会产生装反的现象。
后来,就通过发掘员工潜能,在复印机旁边装一个小风车,如果装配正确就会有风,风
车会转,因此只要风车会转,装配就是完好的,否则,就是错误的。
这样这家公司复印机的合格率就大大提高了。
二、如何强化管理。
某企业有一个开放式的大办公室,有200人在一起办公。
由于管理不到位,经常发生办公室的灯、空调没有关的现象。
最近,公司高层也知道了此事,指示行政部必须强化管理,尽快解决此问题。
于是行政部想了许多办法,如:
出台制度、人走灯灭、保安检查、领导值班检查、进行处罚、公告等。
一开始还能起到一定作用,但时间一长,由于监督不到位,老问题还是继续发生,制度落实不好。
其实,制度固然重要,但不能迷信制度。
这属于无意识犯错,无意识犯错是不可以用制度来约束的。
管理很重要,但员工的自主管理更重要。
某酒店想出了一个好方法:
他们在每位客人的房间钥匙上都有一个卡,这个卡插进去,通过感应电源才能开通,只要一锁门,钥匙一拿出来,就自动断电了,灯也就灭了。
某公司通过努力也想出了好办法:
他们在公司的门上设计了一个卡通画,只要一锁门,就会有一个卡通画跳出来,问“你关灯了吗?
”。
通过这种人性化的管理和提醒,忘记关灯和空调的现象终于杜绝了。
三、美国西南航空学丰田
日本产品曾经是低劣产品的代名词,美国人曾经看不起日本企业。
但二十世纪头十年,美国先生发生了恐怖袭击、全球金融危机,于是美国人也放下身段向日本人学习。
美国西南航空学习日本丰田公司,推行精益生产。
他们所有的机型就只有一种,就是737客机。
这样设备操作简单化,机师维护简单化,设备配件也简单化,他们是空姐负责飞机的清扫飞机卫生,这样降低了成本,飞机的中转时间也大大缩短了。
另外,还有一个好处,就是这里的飞行员、机师、空姐等非常稳定,为什么?
因这他们就只熟悉737机型,到其他航空公司不好找工作。
四、关于洗手间的改善
在提倡TPM—工厂全面改善的过程中,小小的洗手间也是一个大有作为的地方,可以创造出你意想不到的价值。
1、利用马桶节?
ahref=““target=“_blank”class=“keylink”>加盟N私谠加盟彻驹惫は氤鲆桓霭旆ā>啻问匝椋诼硗澳诩由隙樽锩孀暗乃蜕倭耍庋茨鼙Vこ逑锤删唬材芙谠加盟?
/p>
2、小便池前滴漏。
由于男生在小便时离便池远,导致小便池前滴漏。
解决这种问题用行政命令显然不行,于是他们想出了一个好主意。
他们在小便前帖了一些幽默小故事,标题很大,但内容字体很小,须走近才能看得清楚。
于是这一
困惑管理的难题较好的解决了。
但是在实际中千万不能搞反了,如果内容字体很大,他们就会离得远才看的清楚。
3、水龙头忘记关。
可以采用延时开关。
4、电灯忘记关。
可以用声音感应开关。
5、厕纸浪费。
一开始他们把纸放在洗手间便池隔间里,但是这样用的很快。
经过观察他们发现,是许多员工浪费,甚至装在自己口袋里带走了。
后来,他们就把纸放在隔间外面,这样由于洗手间人来人往,有了监督,大家就不好意思浪费,更不好意思私自带走了。
简单做管理,需要大智慧。
五、看理光、丰田如何做管理?
日本公司留人的故事
有一家日本公司,他们的总经理是一位65岁的老人,他是退休后又被公司返聘的。
他说,留人的关键是真正爱员工,全神贯注地考虑员工需求,去满足他们。
他有一个好习惯是每周陪员工工作2小时,了解他们的辛苦。
我始终为一线员工说话,让每一个弱势群体感觉到有一个为他们撑腰的人。
为了员工成长,他们身体力行,全力付出。
同时要善待每一位离开的员工。
让他们想念、怀念这个曾经的家园!
六、如何鉴别真改善和假改善?
如果我们推动精益生产,提倡降低成本,就要能够分辨出哪些改善是真的?
哪些是假的?
有一家企业的老板十分困惑,在推动精益生产以后,研发部设计的产品经常出现问题,然后研发部就进行改善,然后就要求奖励。
这让老板很困惑,很无奈,不奖励好象和提案制度相违背,奖励吧又有些不甘心。
其实,他是没有分清哪些上真改善?
哪些是假改善,被假象欺骗了。
改善=主动*改方法*善结果
任何被动的工作都是义务,是假改善不是真改善。
七、用三天的时间造就一个“懂规则,识文化”的职业经理人
第一天由行政部来讲文化,讲公司的制度、理念等,然后考核,让每一个人都得100分。
如果有人不了解,可以让他把公司答案抄写一遍,让他明白公司倡导的东西。
第二天班级长教员工5S,谈体会,放图片。
然后让大家打扫卫生,地板不是用来扫的,是要用擦布蹲下来去擦的。
第三天找问题。
6人一个小组,找问题点,改善前、发送后进行对比。
这样用三天的时间,就可以打造一个“懂规则,识文化”的职业经理人。
这些都是世界知晓的经典案例,我们可以发现没有最好,只有更好。
篇二:
精益生产经典案例
二0一0年十月二十二日笔者参加了3A顾问公司刘承元博士如何构建持续竞争优势—《精益生产与成本改善》的管理课程。
精益生产提倡:
0缺陷、0库存、0浪费、0事故。
事实上这是我们的追求和信仰,只能无限靠近却无法真正实现。
我们要用正确的思维,分析存在问题,是什么原因?
然后对症下药,这样管理就变得好简单,接下来就是行动。
根据课程内容整理了以下管理案例,与大家一起分享。
一、自动化与防呆、纠错
零缺陷最大的窍门:
通过发掘人的智慧,找到了傻瓜都能做对的办法,减少品质对人的依赖。
有一家电子生产型企业,他们在组装设备时由于需要装配的螺丝数量多,操作工经常会有遗忘,导致不良。
后来,公司就从精益生产的角度进行考虑,降低人的因素。
他们专门设计了一种机械手,机械手末端有磁铁。
如果这个部位需要装5颗螺丝,机械手就自动抓起5颗螺丝,如果需要装16颗螺丝,机械手就自动抓起16颗螺丝。
操作工只要看下机械手上有没有剩余的螺丝就可以了。
这样就减少了品质不良的发生。
还有一家生产复印机的工厂,他们的复印机里面有一个小风扇,这个小风扇非常重要,一旦装反了,就会导致机械损坏。
但由于是流水线作业,操作工在装配时,由于疲劳、遗忘等多种原因,可能会出错。
主管就要求操作工装好后要进行检查,用手摸一下,试下风向。
但是每天生产数千台复印机,操作工人可能就会产生错觉,有风?
没风?
不开心了,走神了,还是会产生装反的现象。
后来,就通过发掘员工潜能,在复印机旁边装一个小风车,如果装配正确就会有风,风车会转,因此只要风车会转,装配就是完好的,否则,就是错误的。
这样这家公司复印机的合格率就大大提高了。
二、如何强化管理。
某企业有一个开放式的大办公室,有200人在一起办公。
由于管理不到位,经常发生办公室的灯、空调没有关的现象。
最近,公司高层也知道了此事,指示行政部必须强化管理,尽快解决此问题。
于是行政部想了许多办法,如:
出台制度、人走灯灭、保安检查、领导值班检查、进行处罚、公告等。
一开始还能起到一定作用,但时间一长,由于监督不到位,老问题还是继续发生,制度落实不好。
其实,制度固然重要,但不能迷信制度。
这属于无意识犯错,无意识犯错是不可以用制度来约束的。
管理很重要,但员工的自主管理更重要。
某酒店想出了一个好方法:
他们在每位客人的房间钥匙上都有一个卡,这个卡插进去,通过感应电源才能开通,只要一锁门,钥匙一拿出来,就自动断电了,灯也就灭了。
一个公司通过努力也想出了好办法:
他们在公司的门上设计了一个卡通画,只要一锁门,就会有一个卡通画跳出来,问“你关灯了吗?
”。
通过这种人性化的管理和提醒,忘记关灯和空调的现象终于杜绝了。
三、美国西南航空学丰田
日本产品曾经是低劣产品的代名词,美国人曾经看不起日本企业。
但二十世纪头十年,美国先生发生了恐怖袭击、全球金融危机,于是美国人也放下身段向日本人学习。
美国西南航空学习日本丰田公司,推行精益生产。
他们所有的机型就只有一种,就是737客机。
这样设备操作简单化,机师维护简单化,设备配件也简单化,他们是空姐负责飞机的清扫飞机卫生,这样降低了成本,飞机的中转时间也大大缩短了。
另外,还有一个好处,就是这里的飞行员、机师、空姐等非常稳定,为什么?
因这他们就只熟悉737机型,到其他航空公司不好找工作。
四、关于洗手间的改善
在提倡TPM—工厂全面改善的过程中,小小的洗手间也是一个大有作为的地方,可以创造出你意想不到的价值。
1、利用马桶节约用水。
为了节约用水,某公司员工想出一个办法。
经过多次试验,他在马桶内加上二块砖,里面装的水就少了,这样即能保证冲洗干净,也能节约用水。
2、小便池前滴漏。
由于男生在小便时离便池远,导致小便池前滴漏。
解决这种问题用行政命令显然不行,于是他们想出了一个好主意。
他们在小便前帖了一些幽默小故事,标题很大,但内容字体很小,须走近才能看得清楚。
于是这一困惑管理的难题较好的解决了。
但是在实际中千万不能搞反了,如果内容字体很大,他们就会离得远才看的清楚。
3、水龙头忘记关。
可以采用延时开关。
4、电灯忘记关。
可以用声音感应开关。
5、厕纸浪费。
一开始他们把纸放在洗手间便池隔间里,但是这样用的很快。
经过观察他们发现,是许多员工浪费,甚至装在自己口袋里带走了。
后来,他们就把纸放在隔间外面,这样由于洗手间人来人往,有了监督,大家就不好意思浪费,更不好意思私自带走了。
简单做管理,需要大智慧。
五、看理光、丰田如何做管理?
日本公司留人的故事
有一家日本公司,他们的总经理是一位65岁的老人,他是退休后又被公司返聘的。
他说,留人的关键是真正爱员工,全神贯注地考虑员工需求,去满足他们。
他有一个好习惯是每周陪员工工作2小时,了解他们的辛苦。
我始终为一线员工说话,让每一个弱势群体感觉到有一个为他们撑腰的人。
为了员工成长,他们身体力行,全力付出。
同时要善待每一位离开的员工。
让他们想念、怀念这个曾经的家园!
六、如何鉴别真改善和假改善?
如果我们推动精益生产,提倡降低成本,就要能够分辨出哪些改善是真的?
哪些是假的?
有一家企业的老板十分困惑,在推动精益生产以后,研发部设计的产品经常出现问题,然后研发部就进行改善,然后就要求奖励。
这让老板很困惑,很无奈,不奖励好象和提案制度相违背,奖励吧又有些不甘心。
其实,他是没有分清哪些上真改善?
哪些是假改善,被假象欺骗了。
改善=主动X改方法X善结果
任何被动的工作都是义务,是假改善不是真改善。
七、用三天的时间造就一个“懂规则,识文化”的职业经理人
第一天由行政部来讲文化,讲公司的制度、理念等,然后考核,让每一个人都得100分。
如果有人不了解,可以让他把公司答案抄写一遍,让他明白公司倡导的东西。
第二天班级长教员工5S,谈体会,放图片。
然后让大家打扫卫生,地板不是用来扫的,是要用擦布蹲下来去擦的。
第三天找问题。
6人一个小组,找问题点,改善前、发送后进行对比。
这样用三天的时间,就可以打造一个“懂规则,识文化”的职业经理人。
篇三:
TPM实施经典案例分析
广州精弘益企业管理咨询有限公司
GuangzhouHLEANSYSTEMConsultingCo.,Ltd
TPM实施经典案例分析
先进的设备管理系统是制造型企业生产系统的最有力的支持工具之一,能够保证生产计划的如期执行以及时响应客户的市场需求。
同时能够有效地降低企业的制造成本,如库存积压成本,维修维护成本及其它管理(人工、时间)成本,而且能够有效降低不良品的产生机率,从过去认为维护只是生产费用的管理提升为企业在失常竞争力的关键项目之一,最终提高企业的经济增值水平。
TPM活动就是通过全员参与,并以团队工作的方式,创建并维持优良的设备管理系统,提高设备的开机率(利用率),增进安全性及高质量,从而全面提高生产系统的运作效率。
在一家采用TPM技术的制造公司中,TPM团队在一开始选择了一个冲床作为分析对象,对它进行了深入细致的研究和评估,经过一段较长时间的生产,建立了冲床生产使用和非生产时间的对比记录。
一些团队成员发现冲床在几种十分相似状态下的工作效率却相差悬殊。
这个发现使他们开始考虑如何才能提高其工作状态。
随后不久他们就设计出一套先进的冲床操作程序,它包括为冲床上耗损的零部件清洁、涂漆、调整和更换等维护作业,从而使冲床处于具有世界级水平的制造状态。
作为其中的一部分,他们对设备使用和维修人员的培训工作也进行了重新设计,开发了一个由操作人员负责检查的按日维护作业清单,并由工厂代理人协助完成某些阶段的工作。
1
《TPM全面改善的案例》
各位读友大家好,此文档由网络收集而来,欢迎您下载,谢谢