造型作业规范.docx
《造型作业规范.docx》由会员分享,可在线阅读,更多相关《造型作业规范.docx(9页珍藏版)》请在冰豆网上搜索。
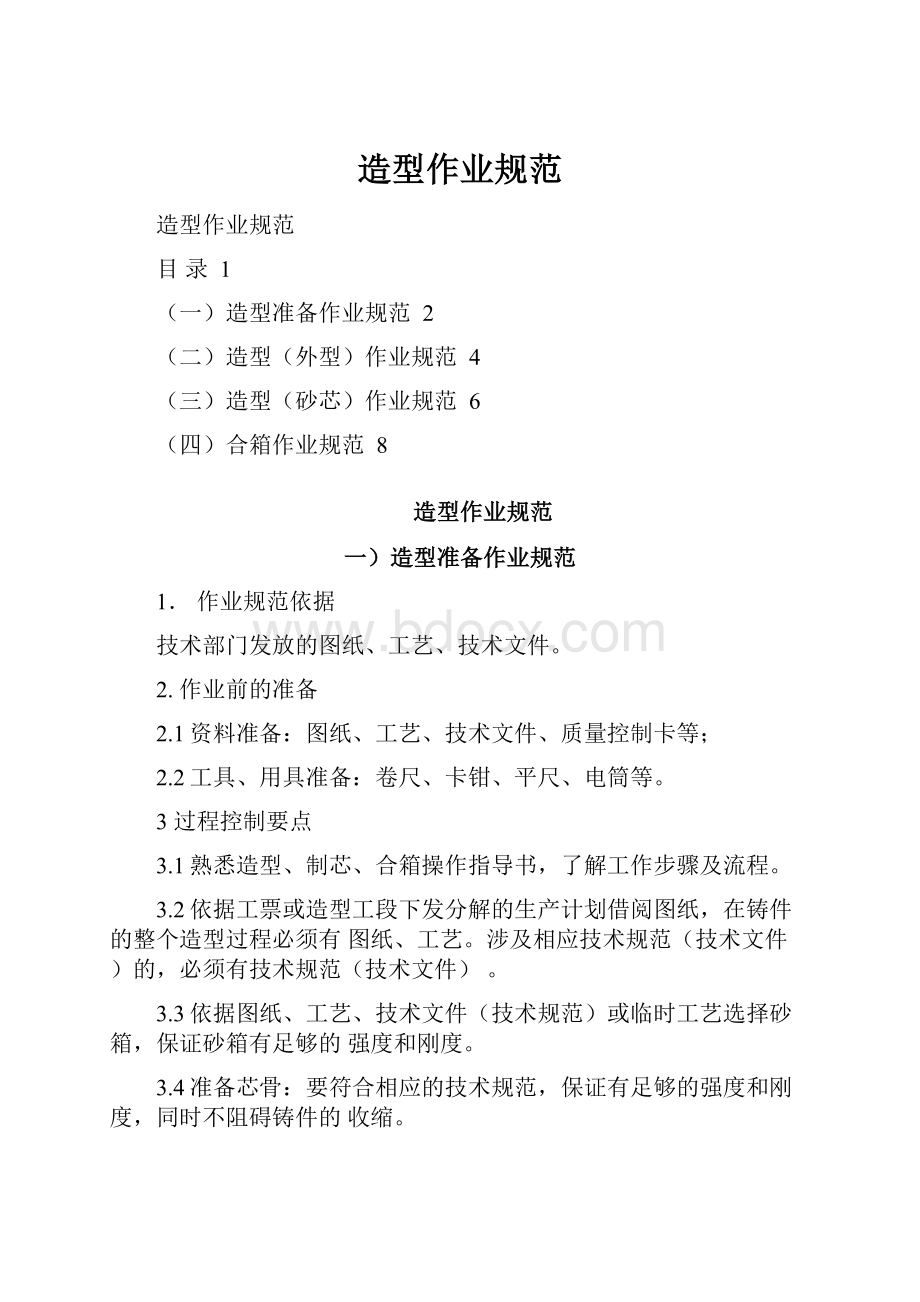
造型作业规范
造型作业规范
目录1
(一)造型准备作业规范2
(二)造型(外型)作业规范4
(三)造型(砂芯)作业规范6
(四)合箱作业规范8
造型作业规范
一)造型准备作业规范
1.作业规范依据
技术部门发放的图纸、工艺、技术文件。
2.作业前的准备
2.1资料准备:
图纸、工艺、技术文件、质量控制卡等;
2.2工具、用具准备:
卷尺、卡钳、平尺、电筒等。
3过程控制要点
3.1熟悉造型、制芯、合箱操作指导书,了解工作步骤及流程。
3.2依据工票或造型工段下发分解的生产计划借阅图纸,在铸件的整个造型过程必须有图纸、工艺。
涉及相应技术规范(技术文件)的,必须有技术规范(技术文件)。
3.3依据图纸、工艺、技术文件(技术规范)或临时工艺选择砂箱,保证砂箱有足够的强度和刚度。
3.4准备芯骨:
要符合相应的技术规范,保证有足够的强度和刚度,同时不阻碍铸件的收缩。
3.5仔细查看图纸等资料,了解工件形状、浇注系统、冒口、冷铁等信息。
3.6根据图纸检查木模。
检查要点:
3.6.1检查木模主要部位尺寸是否正确、结构是否完整、活块、芯盒是否齐全、有无损
坏;
3.6.2检查木模有无定位装置、起吊装置,设置是否合理。
3.7准备冷铁。
要点:
3.7.1冷铁形状、数量、大小要符合图纸要求;
3.7.2冷铁使用面必须经打磨等处理,去除铁锈、氧化皮等杂物。
3.8浇注系统:
用陶管砖接的浇注系统,根据工艺要求选择陶管砖,将陶管砖内的砂子等杂物清除干净。
在制作浇注系统时,接头处必须用胶带包裹,直浇道、横浇道、内浇道大小、数量要符合工艺要求。
直浇道、内浇道等的开口处先用胶带封住,打制完砂型、芯后去除。
注意保证浇注系统对接准确、畅通、干净无杂物、砂子等。
3.9涂料:
3.9.1醇基涂料是以酒精(工业乙醇)为溶剂的快干涂料,同时本涂料具有极强的挥发性和易燃性,在使用和保管过程中容易发生事故。
3.9.2石墨涂料沉积严重,涂料使用前必须充分搅拌均匀。
3.9整个生产过程中,有任何疑问必须及时报告,不允许擅自处理。
4质量记录按规定做好质量记录以分析、改进、总结、提高、稳定操作及工艺。
对异常情况要记载清楚,交接班记录要全面清楚。
二)造型(外型)作业规范
1作业依据生产指令、铸造工艺图纸、操作指导书及相关技术文件。
2准备工作
2.1模型准备。
检查模型活块是否齐全完好、模型表面质量是否达到要求、模型起吊是否可靠合理。
模型尺寸抽检。
2.2冷铁准备。
检查冷铁质量,主要是形状、尺寸大小、数量、工作面打磨是否符合工艺。
2.3冒口、出气棒、木模浇道、浇口砖准备。
按工艺要求的规格、数量准备好冒口、出气棒和木模浇道。
同时按工艺要求准备好所需浇口砖,挑选出合格的并用封口胶带固定
2.4砂箱准备。
找好所需砂箱,检查吊耳是否安全可靠。
2.5试样模型准备。
按工艺要求准备好试样模型数量。
3作业程序
3.1造型
3.1.1冷铁安置。
按工艺要求安置冷铁,必要时用钢筋点焊固定。
3.1.2浇道安置。
按工艺要求安置浇道,并固定。
3.1.3砂箱摆放。
清除模样上的杂物,正确摆放砂箱,特别是将箱带摆正确(注意分清砂箱上下)。
必要时同一砂型多个砂箱之间用螺杆紧固连接。
3.1.4冒口、出气孔及盖箱吊芯孔安置。
按工艺要求安置好冒口、出气孔。
注意盖箱吊芯孔位置。
3.1.5检查树脂和固化剂桶内的树脂和固化剂是否够用,随后开启混砂机,并检查树脂砂的强度。
3.1.6预埋砂芯制作,刷涂料,注意铸件标识号。
3.1.7放砂造型。
在放砂过程中必须用捣砂棒紧实型砂。
大件必须保持三人,其余二人才能进行此工作。
3.1.8取冒口和气眼模型。
放砂结束时,刮平砂箱,待砂型有一定强度时松动冒口和气眼模型,随后取出,刷上涂料并点火。
3.1.9取模。
采用合理的方式取模。
3.1.10清除模型上杂物,归位模型。
3.2修型
3.2.1将砂型安置在合适的位置。
3.2.2用砂轮或砂纸去除多余的型砂。
3.2.3去除明冷铁表面积砂。
3.2.4修补缺损砂型。
3.2.5修补强度不好部位砂型。
3.2.6尤其注意浇道处砂型质量、分型面是否平直。
3.3刷涂料。
3.3.1清理干净砂型表面浮砂。
3.3.2按要求勾兑、搅拌涂料。
3.3.3刷第一遍涂料。
3.3.4点火。
轮毂刷三分之一后点火,中件刷二分之一后点火。
3.3.5清除砂型表面杂物,必要时进行打磨。
3.3.6刷第二遍涂料。
用干净涂料涂刷,点火烧结。
3.3.7刷第三遍涂料。
用干净涂料涂刷,点火烧结。
不允许堆积。
3.3.8尤其注意一遍、二遍、三遍涂料质量和浓度,不允许热刷涂料。
3.4自检尺寸、表面质量和铸件标识号,填写相应记录表后,交付专检。
3.5清理现场。
工作完毕,将所属区域现场的辅助材料和杂物清理干净,剩余涂料返回管理员处。
4整理作业质量记录,以分析、改进、总结、提高、稳定操作及工艺。
对异常情况要记载清楚,并交相应人员保存。
交接班记录要全面清楚。
三)造型(砂芯)作业规范
1作业依据生产指令、铸造工艺图纸、操作指导书及相关技术文件。
2准备工作
2.1模型准备。
检查芯盒活块是否齐全完好、芯盒表面质量是否达到要求、芯盒起吊是否可靠合理、芯盒尺寸抽检。
2.2冷铁准备。
检查冷铁质量,主要是形状、尺寸大小、数量、工作面打磨是否符合工艺。
2.3芯骨准备。
检查芯骨的结构和吊臂是否合理、安全可靠。
2.4排气材料准备。
准备好所需通气绳、焦碳等。
2.5尤其注意芯骨强度。
3作业程序
3.1制芯
3.1.1活块安放。
清除干净芯盒内杂物,注意是否变形,按要求检查尺寸,并紧固。
3.1.2冷铁安置。
按工艺要求安置冷铁,必要时用钢筋点焊固定。
3.1.3砂芯排气设置。
按工艺要求用通气绳、通气管或焦碳等设置。
3.1.4检查树脂和固化剂桶内的树脂和固化剂是否够用,随后开启混砂机,并检查树脂砂的强度。
3.1.5放砂制芯。
在放砂过程中必须用捣砂棒紧实型砂。
根据工艺要求安置冷铁、芯骨和排气装置。
3.16取芯。
采用合理的方式取芯,芯盒复位,吊运到合适位置。
3.2修芯
3.2.1将砂芯安置在合适的位置。
3.2.2用砂轮或砂纸去除多余的型砂。
3.2.3去除明冷铁表面积砂。
3.2.4修补缺损砂型。
3.2.5修补强度不好部位砂型。
3.2.6检查砂芯尺寸,并做好相应记录。
3.2.7注意掏出起吊装置。
3.3刷涂料。
3.3.1清理干净砂芯表面浮砂。
3.3.2按要求勾兑、搅拌涂料。
3.3.3刷第一遍涂料。
3.3.4点火。
轮毂刷三分之一后点火,中件刷二分之一后点火。
3.3.5清除砂型表面杂物,适当修磨。
3.3.6刷第二遍涂料。
用干净涂料涂刷,按第④条点火。
3.3.7刷第三遍涂料。
用干净涂料涂刷,按第④条点火。
不允许堆积。
3.3.8做好自检记录。
3.3.9尤其注意一遍、二遍、三遍涂料质量和浓度,不允许热刷涂料。
3.4清理现场。
工作完毕,将所属区域现场的辅助材料和杂物清理干净。
4整理作业质量记录,以分析、改进、总结、提高、稳定操作及工艺。
对异常情况要记载清楚,并交相应人员保存。
交接班记录要全面清楚。
四)合箱作业规范
1作业规范依据
技术部门发的图纸、工艺、技术文件。
2作业前的准备
2.1图纸、工艺、技术文件、质量控制卡等资料准备;
2.2工具、用具准备:
卷尺、卡钳、平尺、电筒等。
3过程控制要点
3.1检查铸型、砂芯
3.1.1砂型是否有足够的吃砂量,芯骨有无裸露。
3.1.2冷铁表面是否平整,无锈蚀。
3.1.3铸字是否清晰、正确、完整,铸字内容是否能与工票对应。
3.1.4砂型(芯)形状、尺寸是否符合图纸要求,冷铁、冒口数量、尺寸是否符合图纸要求。
3.1.5铸型、砂芯紧实度是否足够,是否有良好的排气性。
3.1.6定位装置是否完好、有效。
3.1.7砂型(芯)是否有尖角,涂料涂刷质量是否良好,有无漏刷的部位(各个角落,尤其是仰面)。
3.2清理合箱场地,放置底箱、找平、垫牢固。
3.3根据3.1条检查的情况,进行修型
3.3.1发现局部松软和损坏处,应将松软处和损坏处出去除、吹尽浮砂,然后再用树脂砂修补,保证几何尺寸准确。
3.3.2修补处砂子有足够的强度,不易脱落。
3.3.3铸字错误的要挖掉,重新下正确的铸字砂芯。
3.3.4凡被铁水包围的砂型棱角,当木模未做出圆角时,应根据工艺要求修出圆角,有特殊要求的除外。
3.3.5为了保证质量,对于大面积疏松、严重分层的砂型(芯),要通知有关技术人员商定,决定是否修补或报废,操作者不得随意决定。
3.4铸型修好后,打扫干净,将醇基涂料严格按工艺要求进行稀释,刷涂料,必须刷均匀,不得有堆积。
点燃涂料,等燃烧完后,对有浮砂和局部粗糙处等影响铸件表面粗糙度的铸型部位进行适当打磨,再刷第二遍涂料,同样应刷均匀,不得有堆积。
3.5下芯
3.5.1将砂芯按工艺要求准确下在相应的砂型中,并按图纸检查各部位的壁厚和各中心尺寸,不得存在偏芯现象。
3.5.2下芯过程中,砂芯应紧固牢靠,防止浇注过程中浮芯。
3.5.3注意浮砂掉入铸型死角地带。
一面下芯,一面将死角地带浮砂用高压风抽尽,砂芯下完后,彻底抽砂一次,将下芯带入的浮砂、散砂抽尽。
3.5.4用未超过可使用时间的树脂砂补好芯头间隙、砂芯接缝及其它需要补砂的部位,待固化后按工艺要求刷好涂料。
3.5.5下完芯后必须将砂型型腔内的浮砂和杂物清除干净,随后等待合箱浇注。
3.6合箱
3.6.1再检查一遍砂型(芯)的尺寸,检查盖箱冒口(数量尺寸是否符合工艺要求,浮砂是否清理干净)、浇口杯(浮砂是否清理干净)和通气孔(是否打穿),检查浇口杯、冒口(过桥)涂料的厚度,表面是否平整,注意清除其浮砂和杂物。
3.6.2将砂型(箱)翻转到合箱状态,按合箱顺序和定位基准,先验箱,检查型腔的壁厚是否满足图纸和工艺要求,砂芯的排气孔是否与盖箱的孔对准。
3.6.3验箱后立即通知检查员检查,经检查员确认合格或处理合格后方可进行合箱。
3.6.4先在冒口孔、浇口杯里塞上造型纸,以防异物掉入型腔。
3.6.5按壁厚、箱的平整程度在芯头和分型面压好石棉绳或泥条,然后合箱,将盖箱、底箱组合成一个完整的铸型。
随后用紧固螺栓或卡子将整个铸型把紧。
3.6.6按铸件序号作箱号标识,注意清除以前的标识,以免混淆。
3.7在生产过程中对图纸、工艺、操作有疑问、不清楚时要及时报告工段、车间,任何人不得擅自处理。
4质量记录
4.1按规定做好记录以分析、改进、总结、提高、稳定操作及工艺。
对异常情况要记载清楚。
4.2将质量记录、工票一同交检查员处,检查员根据实际情况在质量记录及工票上盖“合格”、“让步接受”、“报废”章,签署检查员姓名。