工序控制.docx
《工序控制.docx》由会员分享,可在线阅读,更多相关《工序控制.docx(20页珍藏版)》请在冰豆网上搜索。
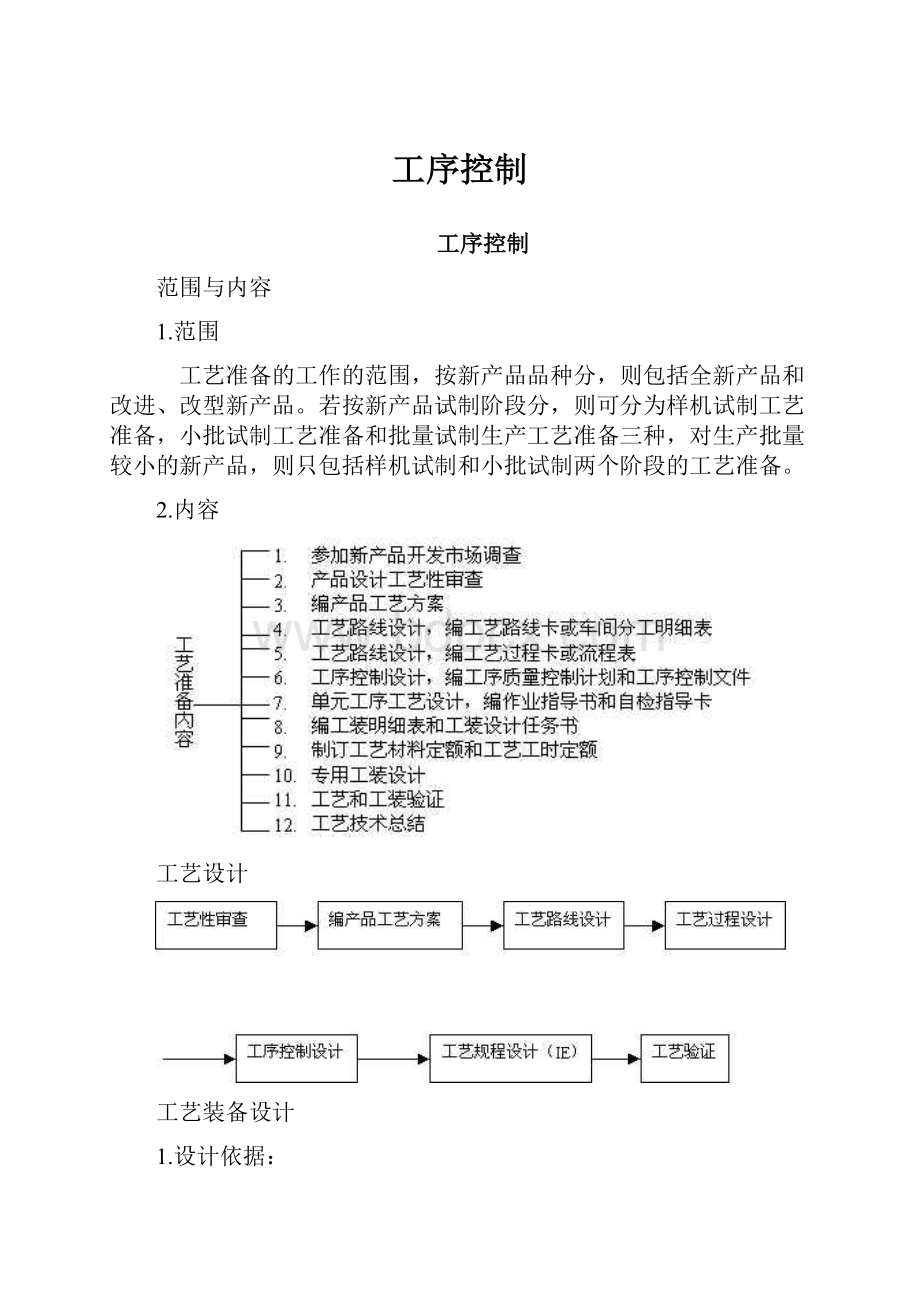
工序控制
工序控制
范围与内容
1.范围
工艺准备的工作的范围,按新产品品种分,则包括全新产品和改进、改型新产品。
若按新产品试制阶段分,则可分为样机试制工艺准备,小批试制工艺准备和批量试制生产工艺准备三种,对生产批量较小的新产品,则只包括样机试制和小批试制两个阶段的工艺准备。
2.内容
工艺设计
工艺装备设计
1.设计依据:
∙工装设计任务书(主要依据)和工装明细表;
∙产品图纸及有关设计文件;
∙工艺规程文件,主要是作业指导书和工人自检指导卡;
∙工装设计手册;
∙与工装及其设计有关的各种标准;
∙本企业设备的有关资料;
∙国内外典型工装图样及有关资料;
∙本企业同类产品同类工装的图样和设计资料。
2.设计原则:
∙工装的先进性与使用的现实性;
∙工装设计的可靠性与经济上的继承性;
∙设计工装的创造性与科学的合理性;
∙设计工装的理论性与实践性;
∙工装使用的安全性;
∙工装设计的标准化原则。
3.工装图样设计
∙总图和部件装配图的设计;
∙零件图的设计;
∙表格图的设计;
∙编号技术要求。
4.工装标准化
∙夹具、模具设计标准化
∙量具、刀具设计标准化
工艺定额
1.劳动消耗工艺定额
A.范围
∙凡能计算考核工作量的工种和岗位,均应制订劳动定额。
B.依据
∙产品图样;
∙工艺规程文件;
∙企业生产类型及产品计划批量;
∙定额标准及企业同类产品及其零部件的劳动定额实际资料。
C.制订的要求尤其具有讽刺意味和黑色幽默味道的是,在千均一发之际力挽狂澜,召唤出自我领域的巫妖王克拉克盖博和慕尼黑人面巨枭也死在了乱军之中,他们俩因为释放领域后奥力损失严重,未及缓冲和调息就被随即而来地禁咒冲击波吹成了天丝,以他们俩这么强大的实力却遭遇这么雷锋的死法,显然有点不能瞑目。
∙所制订定额应该先进合理,达到平均先进水平;
∙注意综合平衡,防止不合理差异。
D.制订的方法
∙经验估计法;
∙统计分析法;
∙类推比较法;
∙技术测定法。
2.材料消耗工艺定额
A.范围
∙构成产品的原材料(含外购件);
∙产品生产过程中所需辅助材料。
B.制订依据
∙具有净重的产品零部件图纸和零部件明细表;
∙产品工艺规程文件;
∙产品所需各种材料标准、加工余量标准和下料公差标准等技术资料。
C.制订的原则
∙先进可行
∙促使材料节约
∙供应可能
D.制订的方法
∙技术计算法
∙实际测量法
∙经验统计法
工艺文件管理
1.分类
管理性工艺文件:
∙各种工艺文件的目次;
∙产品设计工艺性审查记录与报告;
∙产品工艺方案;
∙产品或零件工艺路线表或车间分工明细表;外协件明细表;
∙工艺过程卡片(或工艺流程表)和装配工艺流程图;
∙专用工装明细表和专用工装设计任务书;
∙材料消耗定额和劳动工艺定额明细表和汇总表;
∙工艺或工装验证记录(书)和工艺技术总结。
操作性工艺文件:
∙工艺过程卡或工艺流程表;装配工艺流程图;
∙工艺卡片、作业指导书或工序卡片;
∙自检指导卡(自检表);
∙专用工装图样、技术要求和专用工装使用说明书。
2.管理
∙底图的管理
∙兰图的管理
∙使用部门的文件管理
3.更改
∙更改的原则
∙更改的场合
∙更改的方法
计算机在工艺设计中的应用(CAPP)
1.应用形式和方法
∙检索式的CAPP系统;
∙创成式的CAPP系统;
∙变异式的CAPP系统;
2.内容
∙提出CAPP系统的结构;
∙设置系统的功能;
∙确定系统的输入参数和输入的信息;
∙设计工艺文件的格式和内容;
∙编制标准工艺规程方案;
∙设计数据库的结构和内容;
∙确定专家系统的工作范围和工作内容。
3.数据库
∙机床或设备数据库;
∙夹具、模具、量具、刀具数据库;
∙工时定额数据库;
∙工序图库系。
特殊工序质量控制导则
以下是引用片段:
中华人民共和国机械行业标准
JB/T5059-91
特殊工序质量控制导则
1主题内容与适用范围
本标准规定了机械制造中对特殊工序进行质量控制时应遵循的基本原则和控制内容。
本标准适用于各种生产类型的机械电子企业的特殊工序质量控制。
本标准仅规定了各种特殊工序质量控制的通用原则和要求,以及提出了几种典型特殊工序质量控制的要点。
各种工艺或产品实行质量控制的具体要求或特殊要求,则应在本标准的指导下编制专用工艺文件来进行实施。
2引用标准
GB4863 机械制造工艺 基本术语
GB/T10300.5 质量管理和质量体系要素指南
JB/Z220 工序质量控制通则
JB/Z187.3 工艺规程格式
JB/Z187.4 管理用工艺文件格式
TJ36 工业企业卫生设计标准
3术语
本标准采用GB4863中的术语和定义。
为了正确应用本标准,参照GB/T10300.5补充下列术语。
3.1工序
一个或一组工人,在一个工作地对同一个或同时对几个工件所连续完成的那一部分工艺过程。
3.2关键工序
对产品质量起决定性作用的工序。
它是主要质量特性形成的工序,也是生产过程中需要严密控制的工序。
3.3特殊工序
工序的加工质量不易或不能通过其后的检验和试验充分得到验证,这种工序属于特殊工序。
例如焊接、热处理、电镀、涂漆、充液(仪表行业)、发泡(冰箱行业)、塑料压制等,以及铸造、锻造中若干主要工序。
4特殊工序质量控制的基本原则
4.1 工序质量控制的严格程度应视产品的类型、用途、用户的要求、生产条件等情况而有所区别,允许结合本企业的具体情况,使用不同的控制方法。
4.2 特殊工序的质量控制以加强过程控制为主,辅以必要的多频次的工序检验,检查人员与质量保证人员对现场操作负有监督的责任和权限。
4.3 应从工序流程分析着手,找出各环节(或分工序)影响质量特性的主要因素,研究控制方法,配备适当手段,进行工序过程的系统控制。
特殊工序应遵循“点面结合”的原则,在系统控制的基础上,对关键环节进行重点控制。
4.4 应根据产品的工艺特点,加强工艺方法的试验验证。
制定明确的技术和管理文件,严格控制工艺参数及影响参数波动的各种因素,使工序处于受控状态。
4.5 特殊工序操作、检验人员要经过技术培训和资格认证。
4.6 特殊工序所用工艺材料、被加工物资应实行严格控制,必要时应进行复检。
使用中的各种工作介质应定期分析、调整和更换,保证其成分在规定的范围内。
4.7 必须使用经确认合格的模具、工装、设备和计量器具,并积极采用先进的检测技术和控制手段,对影响质量特性的主要因素进行快速、准确的检测和调整,力争实现自动控制,以减少人的因素引起的质量波动。
4.8 应对工作环境(尘埃、温度、湿度等)进行控制,满足工艺文件的要求,必要时应加以验证。
5特殊工序质量控制的主要内容
5.1 工艺规程和技术文件
5.1.1 特殊工序的工艺规程除明确工艺参数外,还应对工艺参数的控制方法、试样的制取、工作介质、设备和环境条件等作出具体的规定。
5.1.2 工艺规程必须经验证认可并符合有关标准。
主要工艺参数的变更,必须经过充分试验验证或专家论证合格后,方可更改文件。
5.1.3 对特殊工序,根据不同产品的技术要求和工艺特点,可在工序流程的必要环节设置控制点,进行重点控制,设立控制点的条件参见JB/Z220。
控制点可按零件的质量特性、工序或设备来设置。
5.1.4 对控制点应进行工序质量分析和验证,找出主要影响因素,明确控制方法,并进行连续评价。
控制点的工艺文件应包含质量控制的内容,如对控制的项目、内容、方法、检测频次、检查方法、记录及测定人员等做出具体规定。
5.1.5 工艺部门应根据质量控制要求,编制原始记录表格并规定填表要求,包括让检验人员、质保人员对工艺参数和操作状况进行检查、监督、认定、签字的要求。
例如,可编制工艺参数核对表、晶粒度测定的波动图、关键件的热处理温升曲线、槽液分析与调整数据的记录、焊接检查卡、关键件的履历卡等。
主要原始记录表格应汇总归档,并规定制件加工档案的保存期限,以备查考。
5.1.6 规定并执行工艺文件的编制、评定和审批程序,以保证生产现场所使用文件的正确、完整、统一性。
工艺规程格式参照JB/Z187.3的规定,管理用工艺文件格式参照JB/Z187.4的规定。
5.1.7 制订并执行技术文件的保管、使用、更改和销毁制度(或标准)。
文件更改的审批程序应与原文件的审批程序相同,重要的更改应有试验验证。
5.2 人员的培训和考核
5.2.1 特殊工序的操作、检验人员必须经过定期考核和培训,并持有上岗操作证。
对有特殊要求的关键岗位,必须选派经专业考核合格、有现场质量控制知识、经验丰富的人员担任。
5.2.2 明确规定特殊工序操作、检验人员应具备的专业知识和操作技能,组成技术考核委员会进行理论和实际操作的考核,各项成绩应填入考核档案,合格者发给相应的上岗操作证。
5.3 设备、仪表和工艺装备
5.3.1 特殊工序使用的设备、仪器仪表和工艺装备(含冶金辅具),必须符合工艺规程的要求。
5.3.2 新制、改进或大修后的设备和仪器仪表应按其技术条件验收,经调试、鉴定合格签证后,方可正式投入使用。
工艺装备必须按规定进行验收、验证(或试用)合格后,方可使用。
5.3.3 设备必须完整、配套,配有显示(或自动控制)工艺参数的检测、计量仪器仪表。
各种供监控用的仪表,一般应按其功能分别设置。
必要时,还应配备工艺参数自动记录仪和安全报警装置。
5.3.4 制订和执行设备、工艺装备的维修保养,仪器仪表的定期检定、校准制度。
设备主管部门应建立设备使用、点检、维修和校准的技术档案。
工装主管部门应对主要工装建立使用维修技术档案。
5.3.5 控制点的设备、工装应参照JB/Z220的要求加以重点控制,以尽量减少设备及工装的误差引起的质量波动。
5.4 环境
5.4.1 环境条件(厂房内温度和湿度,冷却介质的温度和压力,压缩空气的压力,施工现场的风速等)应满足工艺技术文件的要求。
5.4.2 作业场所应配置有效的进、排风系统及安全技术措施,厂房空气中有害物质的最高浓度应符合TJ36的有关规定。
5.4.3 应对车间一些重要的噪声源设施(如通风机、鼓风机、空气压缩机等)采取适宜的减噪或隔音措施,以控制车间的环境噪声在85Db以下(脉冲声除外,但应进行适当控制)。
5.4.4 车间应有良好的自然采光或照明,操作工位应有足够的照度。
5.4.5 含有害物质的废水、废气、废渣必须进行有效的净化处理,三废排放标准应符合国家对环境保护的有关规定。
5.4.6 车间应配置必要的安全、防护设施,作业场地必须遵守防火和技术安全制度的规定。
5.5 工艺材料
5.5.1 工艺材料的采购文件应明确规定物品规格、材质和技术要求,必要时,还应提出质量保证的要求。
5.5.2 重要工艺材料应严格按规定的技术要求择优定点采购。
采购部门选点时,必须经质量管理部门组织有关部门人员对供应厂进行质量考察,并经试用验证认可后才能定点。
5.5.3 进厂工艺材料必须有制造单位的合格证明文件,重要材料必须按规定复验,无合格证或复验不合格的材料禁止入库和使用。
5.5.4 超过保管期限的材料必须按规定重新复验,办理延期使用文件,经审批后方可使用。
5.5.5 应提供符合使用要求的贮存场所和配套设施,并建立严格的保管、标志、发放、使用和回收制度。
5.5.6 使用中的各种槽液、介质等材料必须按技术文件的要求进行定期分析,保证其成分在规定的范围内。
对不符合技术要求的槽液和介质等应进行调整或更换,不合格者不准用于生产。
5.5.7 采用新牌号的重要工艺材料应进行试验及生产验证,提出试验验证报告,经主管部门组织鉴定审批后方可使用。
5.6 被加工物资
5.6.1 转入本工序的被加工物质(原材料、毛坯、半成品等),必须符合技术文件的规定,并具有合格证明文件,必要时需附有所要求提供的化学成分、机械性能及检测数据等技术资料,或进行抽查复验。
5.6.2 制定适用于本厂生产要求的外购物资标准,规定物资规格和技术要求,以及进厂入库的取样、检验项目和方法。
5.6.3 重要的外购物资应择优定点采购,并进行进厂复验。
必要时,应对供应厂进行质量保证能力的考察和监督,并建立合格供方的技术质量档案。
5.6.4 应建立进料验证、入库、保管、标志、发放制度,并认真执行。
5.7 工艺过程控制
5.7.1 加工前,操作人员应熟悉工艺规程,严格按工艺规程作好各项准备工作,包括设备、材料、介质、环境条件的检查,进行各种预处理,工艺参数的试样验证等,并做好原始记录。
对特殊的关键件,工艺人员应向操作人员进行技术交底,以保证操作人员真正掌握工艺规程。
5.7.2 严格按工艺规程操作。
工件的装卡、摆放,工艺参数的调整,试样的抽取、检验和保管等应根据不同物资的技术要求,按工艺规程的有关条款执行。
5.7.3 应认真、如实、完整地填写原始记录,并按规定程序签名、处理、传递和保管。
5.7.4 操作中应密切注意加工情况,如发现问题,应立即自行或通知有关部门采取有效措施予以解决,并作好原始记录。
5.7.5 每批制件必须进行首件检查,并作好标记,填写首件记录卡,并在记录上签章。
5.7.6 工序检验员应对生产现场进行巡回检查,对工艺的执行和原始记录的记录情况进行监督,抽检制件的加工质量,做好监督检查记录。
对巡检中发现的质量问题,应督促有关人员及时纠正。
5.7.7 关键件加工中的主要分工序,根据需要可设立“见证点”,由对质量不负直接责任的质保工程师实施见证性审核。
对工序加工中操作者是否处于自控状态,检验员是否忠于职守,图纸、工艺文件是否有效贯彻,工序加工质量是否符合规定要求等方面进行监督性检查,以确保现场质量控制的有效性。
5.7.8 制件在工序间的存放、周转与运输,应按定置管理规定及期量标准加以控制,并备有适用的工位器具和储运设备,防止损伤制件。
5.8 质量检验
5.8.1 应规定工艺质量标准,明确技术要求,检验项目、项目指标、方法、频次、仪器等要求,并在工序流程中合理设置检验点,编制检验规程。
5.8.2 按技术要求和检验规程对半成品和成品进行检验,并检查原始记录是否齐全,填写是否完整,检验合格后应填写合格证明文件并在指定部位打上合格标志(或挂标签)。
5.8.3 严格控制不合格品,按规定程序进行处理。
不合格件的回用应按规定程序审批,并按有关规定返修、返工和重新检验。
回用件应打上回用标志,回用、返修单据作为质量信息流转、存档。
对待验品、合格品、返修品、废品应加以醒目标志,分别堆放或隔离。
5.9 质量信息的反馈和处理
5.9.1 特殊工序的各种质量检验记录、理化分析报告、控制图表等都必须按归档制度整理保管,随时处于受检状态。
5.9.2 应编制和填写现场加工缺陷分类统计日报表及其它各种质量问题反馈单。
对突发性质量信息应及时处理,填写相应表格。
5.9.3 应制订对后续工序(包括产品使用中)发现的特殊工序质量问题及时反馈、汇总和处理的制度,并认真执行。
5.9.4 应制订和执行质量改进制度。
按规定的程序对各种质量缺陷进行分类、统计和分析,针对主要缺陷项目制订质量改进计划,并组织实施,必要时应进行工艺试验,取得成果后纳入工艺规程。
6 几种典型特殊工序质量控制的要点
本章结合几种典型特殊工序,提出了一些控制要点。
企业在进行特殊工序的质量控制时,应根据第5章的要求,给予补充完善,对人、机、料、法、环(4M1E)的控制做出全面安排。
6.1 热处理工序质量控制
6.1.1 全过程控制
应建立自来料验收、热处理前清理、预热、加热、保温、冷却、回火、清理、校正、检验、防锈入库等全过程的质量控制系统。
6.1.2 控制点
通过热处理常见缺陷(变形、裂纹、白点、过热、过烧、脱碳、硬度不足、硬度不均、机械性能差等)的统计调查,找出存在的主要质量缺陷,进行工序质量因素分析。
在工艺试验验证的基础上,确定主要原因及其控制措施,设立控制点。
同时,对重要的关键件也应加强工序检查,细化工艺文件,进行重点控制。
6.1.3 前工序质量的影响
应重视热处理前工序质量对最终热处理质量的影响,合理安排工艺路线和前道工序的质量控制。
例如,机械加工应尽量减少加工应力,注意过渡圆角,防止应力集中,对长径比较大的轴类零件在粗加工或半精加工后,应安排消除内应力的退火,以减少淬火变形及开裂。
锻件应防止过热、过烧、终锻温度过低等造成的热处理缺陷。
6.1.4 工艺参数的监督
加强对工艺参数的检测和记录。
一般热处理时要控制加热温度、升温速度、保温时间、冷却方式、冷却速度、冷却介质及温度、出炉温度等工艺参数。
化学热处理时对渗碳过程还应严格控制碳势,离子氮化时还应控制氮化温度、保温时间、升温速度等参数。
应严格按工艺文件的规定执行,对关键件应填写热处理技术记录卡片,记录主要工艺参数及有关的条件,操作工人现场记录数据,检验人员现场核对并签字。
6.1.5 工序检验
加强工序过程中的质量抽检,实行工序流转的签卡制度,凡抽检不合格的产品不得转序。
研究代用质量特性值与质量特性的相关关系,用检测代用质量特性值来快速、准确评定工艺质量,以便及时调整工艺参数。
例如,高速钢的淬火可通过对试件(或试样)晶粒度的测定,控制晶粒度的波动范围来防止制件过热或硬度不足,减少热处理变形。
又如锻后热处理时,可通过控制含氢量来防止锻件出现白点。
6.1.6 工装与设备
6.1.6.1 关键或主要设备应备有温度指示仪表及报警装置,并实行自动记录。
应合理、正确地设计与使用工装,加强对热处理工装、设备的日常管理与维护保养,关键的工装与设备应实行日点检。
6.1.6.2 各种热处理设备必须进行定期检查与维修。
加热炉、渗碳炉、渗氮炉及感应加热设备等应定期进行工艺性能的检测,以保证炉温的均匀性、渗层均匀性及感应加热的要求,并保证各种冷却设备的冷却性能。
各类仪表要定期进行校对、修正与周检。
6.1.6.3 要不断提高各种热处理设备的完好率,积极采用先进设备及控制仪表,实现对热处理质量的自动控制。
6.1.7 介质
加热介质(油、煤气、盐浴用盐等)和冷却介质(空气、水、盐水、淬火油、合成淬火剂等)以及保护气体(氩气、氨气等)应符合有关技术标准要求,并能达到要求的热处理加热、冷却性能,不含有过量有害物质,对制件无腐蚀及其它有害影响。
使用中的各种介质必须按有关技术要求定期分析,对不符合技术要求的介质应进行调整或更换,不合格者不准用于生产。
6.2 焊接工序质量控制
6.2.1 全过程控制
应建立自材料供应、焊前准备(预处理、放样、下料、坡口加工、冷热成形等)、组焊(组对、焊接)、焊后处理(喷丸、热处理等)和成品检验等全过程的质量控制系统。
6.2.2 焊缝等级
根据焊件的受力情况、重要程度、失效危害等因素,将焊缝划分为三个等级,并在设计、工艺文件中做出相应标志。
一级焊缝:
承受很大的静载荷、动载荷或交变载荷的焊件,焊缝破坏会导致产品失效或危及人员的生命安全。
二级焊缝:
承受较大的静载荷、动载荷或交变载荷的焊件,焊缝破坏会降低产品的性能,但不会导致失效或危及人员的生命安全。
三级焊缝:
承受较小的静载荷或动载荷的一般焊件。
6.2.3 控制点
一级焊缝必须重点控制;二级焊缝可根据企业工艺质量稳定情况,来决定是否进行重点控制。
企业也应根据焊接全过程中(焊前准备、组焊、焊后处理)的薄弱环节设立控制点,进行重点控制。
压力容器还应按有关规定设立监督点(见证点和停止点)。
6.2.4 焊接工艺评定
改变焊接工艺参数、焊接方法及首次列入工艺规程的一、二级焊缝的焊接工艺参数,必须先经焊接工艺评定。
应制订《焊接工艺评定管理办法》,对工艺评定的条件、目的、评定试验的内容、方法、责任部门、评定报告、工作程序等做出规定。
焊接工艺评定合格后,将焊接方法的重要参数计入工艺评定报告,经企业技术负责人批准后,编号存档,作为制订工艺规程的依据。
严格执行经过评定的焊接规范。
6.2.5 焊材控制
加强对焊材的质量控制,焊材进厂必须按规定的技术条件进行检验,合格后方可入库和使用。
焊材必须分类堆放,并按规定温度和保温时间进行烘干。
焊材库必须干燥通风,严格控制库内温度和湿度。
应建立严格的保管、清理、烘干、发放和回收制度。
6.2.6 人员资格
严格实行焊工的资格认证。
压力容器焊工资格评定应依据劳动部颁发的《锅炉压力容器焊工考试规则》的要求进行,并报上级主管部门和当地劳动部门审批。
焊接检验工必须具有连续五年以上焊接工作经验,经过焊接检验基础知识培训并考核合格。
从事无损检测的人员必须按劳动人事部《锅炉压力容器无损检测人员资格考试细则》的要求考试合格。
6.2.7 设备p; 焊接设备必须完整配套,并配有显示焊接工艺参数(电流、电压、焊接速度、预热温度、真空度等)的检测、计量仪器或仪表。
焊接一、二级焊缝的焊接设备,应根据产品需要,配备电参数自动记录仪,用于监督和记录焊接工艺参数。
焊接设备必须定期测试和检修。
6.2.8 工艺过程及监督
6.2.8.1 焊件、焊材在焊前必须按规定进行预处理(表面清理、烘干等),并在规定时间内焊接。
6.2.8.2 一、二级焊缝或有特殊要求的产品应设置焊接试板,焊接试板按产品试板检验规定检验,合格后方可对产品施焊。
6.2.8.3 一、二级焊缝的产品应设立中间检验站,在下料、组对等分工序进行工序检验。
同时,对焊接成品进行最终检验。
以确保下料、组对的工序质量能满足焊接的质量要求,使最终成品质量合格。
6.2.8.4 加强焊接过程的质量监督,定期或巡回抽检焊件的焊接质量和影响焊接质量的主要因素(如电流、电压、焊接速度、波峰焊的焊药温度、焊锡比重等)。
6.2.8.5 一级、二级或有专门规定的熔焊焊缝,应控制焊接规范,将规范参数和产品检验结果记入熔焊检查卡,工艺参数由焊工填写,检验结果由检验员填写,检验卡应存档。
一级、二级或有专门规定的电阻焊焊缝,在焊前、焊接过程中,每批零件焊接终了都应做工艺试验,对焊接参数进行验证。
每次工艺试验结果记入电阻焊检验卡,工艺参数由焊工填写,检验结果由检验员填写,检验卡应存档。
应在规定的位置,对一级、二级焊缝标打焊工及检验员钢印标记。
6.2.9 焊接热处理的