物流技术与装备案例.docx
《物流技术与装备案例.docx》由会员分享,可在线阅读,更多相关《物流技术与装备案例.docx(28页珍藏版)》请在冰豆网上搜索。
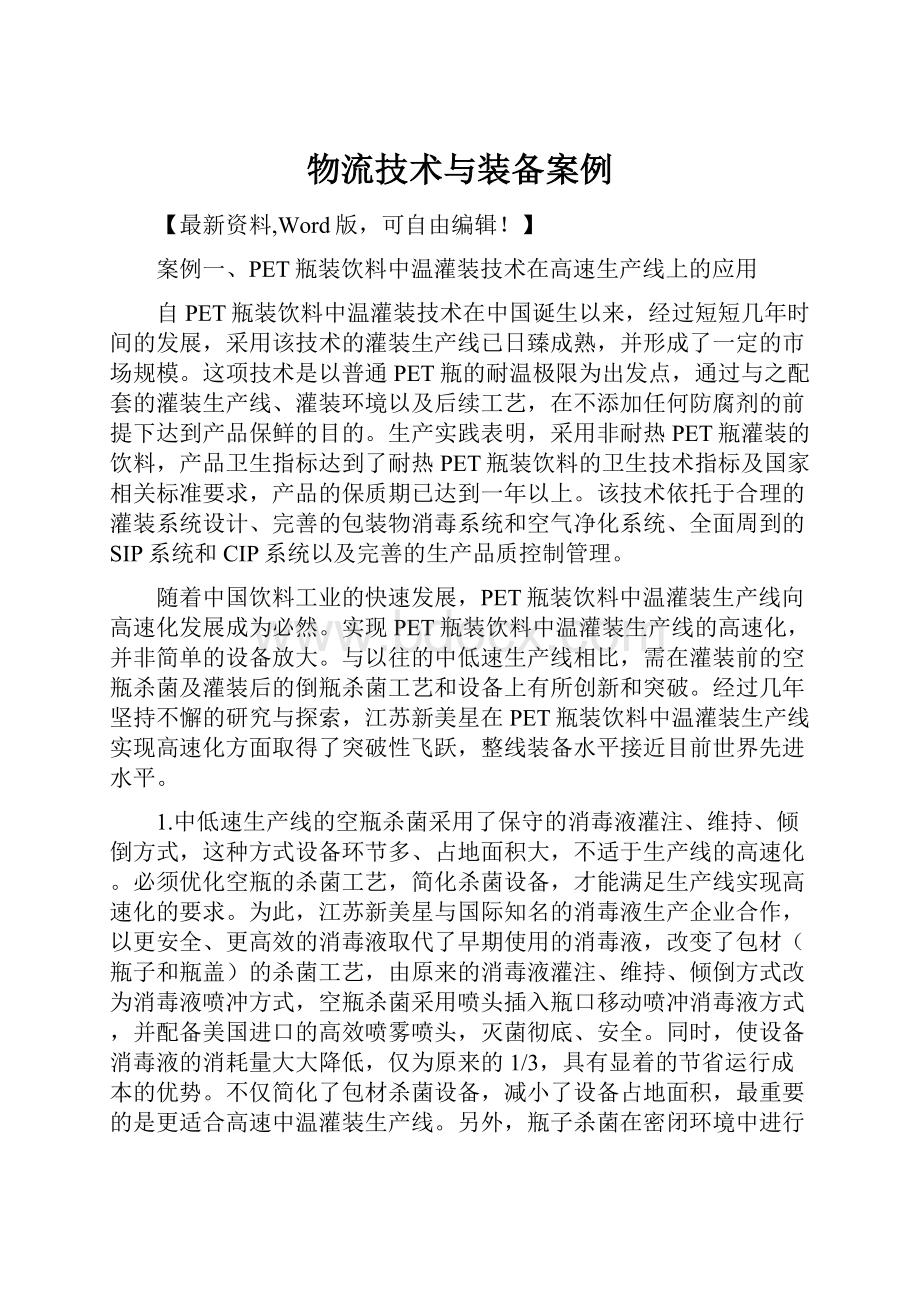
物流技术与装备案例
【最新资料,Word版,可自由编辑!
】
案例一、PET瓶装饮料中温灌装技术在高速生产线上的应用
自PET瓶装饮料中温灌装技术在中国诞生以来,经过短短几年时间的发展,采用该技术的灌装生产线已日臻成熟,并形成了一定的市场规模。
这项技术是以普通PET瓶的耐温极限为出发点,通过与之配套的灌装生产线、灌装环境以及后续工艺,在不添加任何防腐剂的前提下达到产品保鲜的目的。
生产实践表明,采用非耐热PET瓶灌装的饮料,产品卫生指标达到了耐热PET瓶装饮料的卫生技术指标及国家相关标准要求,产品的保质期已达到一年以上。
该技术依托于合理的灌装系统设计、完善的包装物消毒系统和空气净化系统、全面周到的SIP系统和CIP系统以及完善的生产品质控制管理。
随着中国饮料工业的快速发展,PET瓶装饮料中温灌装生产线向高速化发展成为必然。
实现PET瓶装饮料中温灌装生产线的高速化,并非简单的设备放大。
与以往的中低速生产线相比,需在灌装前的空瓶杀菌及灌装后的倒瓶杀菌工艺和设备上有所创新和突破。
经过几年坚持不懈的研究与探索,江苏新美星在PET瓶装饮料中温灌装生产线实现高速化方面取得了突破性飞跃,整线装备水平接近目前世界先进水平。
1.中低速生产线的空瓶杀菌采用了保守的消毒液灌注、维持、倾倒方式,这种方式设备环节多、占地面积大,不适于生产线的高速化。
必须优化空瓶的杀菌工艺,简化杀菌设备,才能满足生产线实现高速化的要求。
为此,江苏新美星与国际知名的消毒液生产企业合作,以更安全、更高效的消毒液取代了早期使用的消毒液,改变了包材(瓶子和瓶盖)的杀菌工艺,由原来的消毒液灌注、维持、倾倒方式改为消毒液喷冲方式,空瓶杀菌采用喷头插入瓶口移动喷冲消毒液方式,并配备美国进口的高效喷雾喷头,灭菌彻底、安全。
同时,使设备消毒液的消耗量大大降低,仅为原来的1/3,具有显着的节省运行成本的优势。
不仅简化了包材杀菌设备,减小了设备占地面积,最重要的是更适合高速中温灌装生产线。
另外,瓶子杀菌在密闭环境中进行,微生物易于控制,操作环境得到充分改善,更易于废气的集中回收与处理,利于环保,可最大程度地保护操作人员免于消毒液的侵害。
2.中低速生产线的倒瓶杀菌采用倒瓶时间较长的网链输送带方式,该方式占地面积大、需辅以人工扶正瓶子,不适于生产线的自动化和高速化。
为满足生产线高速化的要求,我公司借鉴并采用了高温灌装生产线的倒瓶杀菌链模式。
同时为满足瓶盖的杀菌时间要求,将喷淋冷却机设计成喷淋杀菌机,以弥补倒瓶杀菌时间不足的缺陷,使产品在冷却前得以充分灭菌。
此外,整条生产线关键设备(空瓶两次杀菌、冲洗、灌装、封盖五合一机)具有如下特点:
1.采用风送道与进瓶拨轮直连技术,进瓶拨轮采用创新设计的具有分瓶功能的瓶口夹持机构,省掉了进瓶螺杆及输送链,变换瓶形无须更换及调整任何零件。
2.瓶子传输全部采用卡瓶颈技术,并采用卡瓶口瓶夹代替传统的拨轮,变换瓶形无须调整设备高低,也无须更换及调整任何零件。
3.特殊设计的全不锈钢冲瓶夹结实耐用,不接触瓶口螺纹部位,避免了瓶口二次污染。
消毒液及无菌水冲洗管路均配备压力检测开关,具有低压保护功能。
4.采用UHT与灌装机直连方式,减少污染环节。
进料方式为主液管通过动静密封与分配器相连,采用了无缸结构。
灌装机设有CIP清洗杯,可以使灌装阀与物料接触的内、外壁均能进行有效CIP清洗和SIP杀菌。
5.消毒液冲瓶机、无菌水冲瓶机、灌装机、旋盖机、过渡拨轮等转动件与非转动件之间均采用液槽密封隔离,有效保护轴承等碳钢零件免受消毒液的腐蚀。
同时隔绝外界不洁空气侵入,保持洁净的灌装环境。
6.配备百级空气净化系统及隔离封窗,并在进瓶口及出瓶口设有净化风帘,防止不洁空气侵入洁净室。
封窗上设有多副隔离手套,便于进行简单维护。
配备设备表面喷雾杀菌及洁净室熏蒸系统。
PET瓶装饮料中温灌装技术为国内首创,目前新美星是国内唯一拥有该技术并提供采用该技术的饮料灌装生产线的供应商。
案例分析:
1.结合所学,谈谈案例中所用包装设备在整个生产线中的作用
案例二、十六年集装箱发展之路
1989年5月16日成立的多特蒙德集装箱到发场有限责任公司是德国铁路一家私营公司,主要由多特蒙德港口(31.42%股份)、德国铁路货运公司(30%股份)、RehnusGruppe公司(14.28%股份)、Eurogate公司(10.72%股份)等公司组成。
其中多特蒙德港口提供土地,德铁组织铁路班列。
公司的地理位置颇具优势,可以通过水运、铁路、公路将比利时、荷兰、卢森堡三国的港口和德国港口连接。
成立之初,公司只有5个人,现在则增至24人。
现场工人9人,其一是负责技术的组长,另外8人分为2组,分早、晚班工作。
公司设有铁路分配部、运输分配部(包括前期任务分配、仓储、重载汽车分配部)、办公室和营销部。
建立初期,公司没有先进的计算机系统支持现场操作,工人使用集装箱桥式门吊要对照很大的草图,经过确认后,才能将需换装的集装箱放到集装箱换装场上合理放置,偶尔会发生错误换装。
如今,由于业务的扩大,集装箱换装场地由4.3万平方米相应扩大到9万平方米,换装能力也整体提高了1倍,同时使用了计算机系统操作,精确程度得到了很大提高。
公司的主要业务是集装箱的装卸、保管、、出售和修理等,同时办理危险货物集装箱、冷藏集装箱、大型平托盘和特种集装箱的运输、换装与保管。
德国公司的作息时间相对来说比较合理。
多特蒙德集装箱到发场有限责任公司现场工人分早、晚班工作,在现场7个半小时的工作分为两部分,主要考虑吊车司机长时间从事吊装任务,腰椎和眼睛比较疲劳,容易产生事故。
前3个小时工人操作吊车进行换装集装箱,后3个小时在重载汽车入口处(相当于国内的场区门房)工作,使用公司专用的系统,根据办公室对集装箱的要求、吊车的现工作位置和换装,进行任务分配。
德国工人工资比较高,为节省劳动力,公司的人员基本都是一岗多能。
现场的工人往往掌握吊车、叉车、重载汽车等多种机械的操作技能。
办公室人员一般能够互相补充,工作可以互换,这得益于德国良好的培训方式。
公司没有生产集装箱的能力,但利用集装箱换装场的有利地势出售各种集装箱,根据顾客需要,及时将信息反馈给集装箱经营业务伙伴,通过中间差价获得赢利。
公司也没有能力修理集装箱,但将部分场地出租给其他公司,由其他公司代替该公司修理集装箱。
这样增强了公司的业务范围,提高了整体竞争能力。
在1989年组建之初,公司换装能力为3500个集装箱,1990年换装能力为10200个集装箱,1991年换装能力26000个集装箱,1994年换装能力为36000个集装箱,2004年换装能力为60000个集装箱。
业务的不断增长得益于集装箱换装场的有利位置和该地区集装箱运量的增长,而该公司由于良好的经营和飞速的发展,被称为“多特蒙德港的珍珠”。
公司拥有90000平方米集装箱换装场,同时拥有多特蒙德威斯特豪因茨货物转运站的专用线。
公司有4股到发线,其中3股均为300米长、1股为400米长。
公司同时拥有多特蒙德港口的400多米长码头,该港口是属于多特蒙德至埃姆运河的一部分。
公司的任务是:
每周5次的从多特蒙德港口到不来梅和汉堡的“信天翁”铁路专列运输,Necoss公司每周4次的铁路集装箱专列运输和每周3次的船运集装箱任务
案例三、海尔自动化立体仓库系统设备与技术应用
单就个体应用而言,或许国内物流设备的现代化程度与发达国家并没有太大差距。
海尔集团首席执行官张瑞敏就曾自豪地说,他参观过德国、日本一些最现代化的物流中心,与之相比,海尔的全自动化物流系统要更为先进。
只不过,在社会化物流还没有发育完善的现实情况下,一些现代化设备和技术仅被少数大型制造企业和商业企业采用。
例如,随着对物流对降低仓储成本的作用逐渐被认识,一些大企业发现自己有足够的能力建立物流自动化立体仓库系统(AutomatedStorage&RetrievalSystem),并且通过其取得了巨大成效。
近两年来,建立自动化立体仓库开始成为大型制造企业和商业企业追求的新时尚。
一个完善的自动化立体仓库系统,应当由高层货架,巷道堆垛起重机(有轨堆垛机)、入出库输送机系统、自动化控制系统、计算机仓库管理系统及其周边设备组成,是一个可对集装单元货物实现自动化保管和计算机管理的智能仓库。
此外,由有轨堆垛机或无轨堆垛机与高架货架等组成的各类机械化、半自动化高架货架仓库、拣选式高层货架仓库,也是自动化立体仓库系统的具体应用形式。
该系统不仅可以应用于大型生产性企业的采购件与成品件仓库、柔性自动化生产系统(FAS),也可以应用于流通领域的大型流通中心、配送中心。
按照操作对象的不同,自动化立体仓库系统类型包括托盘单元式自动仓库(PalletUnitAS/RS)、箱盒单元式自动仓库(FineStocker)、拣选式高层货架仓库(PickStocker)、单元/拣选式自动仓库(Unit-PickStocker)、高架叉车仓库(RackForkStocker)等。
其中,采用托盘集装单元方式来保管物料的自动仓库,被国内企业较为广泛地采用。
事实上,业内通常所说的“自动仓库”,指的就是托盘单元式自动仓库。
它一般由巷道堆垛起重机、高层货架、入出库输送机系统、自动控制系统、周边设备和计算机仓库管理系统等组成。
根据高层货架与建筑物之间的关系不同,大致可以可以分为以下两种。
一种是整体式自动仓库,它由货架顶部支撑建筑屋架,在货架边侧安装墙围,货架与建筑物成一整体。
特点是建筑费用低,抗震,尤其适用于15米以上的大型自动仓库。
另外一种是分离式自动仓库,它的货架与建筑无关,呈独立、分离状态,适用于车间仓库、旧库技术改造和中小型自动仓库。
根据自动控制的方式不同,则可以分为以下几种:
一、单机设定,自动运转;二、单机设定,红外通讯,自动运转;三、计算机遥控设定多台单机,自动运转;四、计算机脱机/联机/实时自动控制。
尽管发展时间不长,但目前国内物流设备厂商也具备了一定的技术能力,下面,让我们走近海尔的自动化立体库,了解相关设备的构成以及它们在各自物流环节中的具体应用。
一、计算机及电控系统
用于对物流系统进行调度管理,以及对各种物流设备进行控制。
其中,电控系统分为组群控制层与设备控制层,组群控制层将计算机系统的指令分解、下发给设备控制层,完成对物流系统底层设备的控制,设备控制层将现场物流信息通过组群控制层上报计算机系统。
计算机系统在网络系统与数据库环境支持下,以集成技术为核心,实现生产和物流数据的快速、准确、完整的收集、传送、存储、处理和分析,并作出正确的决策,协调各业务环节,从而高效的组织生产,完成对物流系统的调度、管理和控制。
除了能够为更高层的CIMS系统提供生产和物流组织状态及物资库存信息外,计算机系统还能够根据CIMS系统下达的生产计划和指令,对生产和物流的组织进行相应的调整。
二、TD系列型巷道式堆垛起重机
用于在高层货架之间对货物进行自动存取。
它的性能参数如下:
(以下请制表)
主要性能参数值
额定起重量(吨):
0.1/0.25/0.6/1.0/1.5/2.0/2.5/3.0
起升范围(米):
30
水平运行速度(米/分钟):
80/100/125/140/160/180/200/250
起升速度(米/分钟):
16/20/25/31.5/40/63/80/100
货叉伸缩速度(米/分钟):
12.5/16/20/31.5/40/50
通讯方式:
红外通讯
操作方式:
手动/自动/在线
供电方式:
滑触电缆供电
三、CG型货架
用于以托盘、货箱为载体的物料的储存。
它的性能参数如下:
主要性能参数值:
CG11 CG112 CG4
最大高度(米):
0.4 1 6
单货位最大载量(吨):
3 0.6 0.12
四、BW5型激光自动搬运车
这是一种由激光导引,计算机控制的自动货物搬运车。
适用于自动化立体仓库及平面仓库中多层或单层货物的存取作业。
它的性能参数如下:
主要性能参数值
导引方式:
激光定型
承载重量(吨):
0.3/0.6/1.0/1.5/2.0
最大运行速度(米/秒):
1
定位精度(毫米):
±5
通讯方式:
无线电
供电方式:
电瓶(DC24V/DC48V)
五、QK型机器人与QY型机器人
主要用于物料的拆垛和码垛。
它们的性能参数如下:
主要性能参数值
机动性能:
圆柱坐标
最大直线速度(米/秒):
1.2
重复定位精度(毫米):
±1.0
最大工作能力(个/分):
8
最大抓取重量(公斤):
80
六、入出库输送、配送系统
用于自动化仓库、配送中心的入出库输送、配送系统。
该设备由SLZ型链式输送机、SG型辊子输送机、SDZ型带式输送机、BY3型穿梭车、STC型带升降辊子输送机的链式输送机、JWZ型托盘单元外形检查站、MK3型托盘码分机等部件组成。
案例四、上海联华生鲜食品加工配送中心物流案例
联华生鲜食品加工配送中心是我国国内目前设备最先进、规模最大的生鲜食品加工配送中心,总投资6000万元,建筑面积35000平方米,年生产能力20000吨,其中肉制品15000吨,生鲜盆菜、调理半成品3000吨,西式熟食制品2000吨,产品结构分为15大类约1200种生鲜食品;在生产加工的同时配送中心还从事水果、冷冻品以及南北货的配送任务。
连锁经营的利润源重点在物流,物流系统好坏的评判标准主要有两点:
物流服务水平和物流成本。
本案例(联华生鲜食品加工配送中心)就是其中在这两个方面都做得比较好的一个物流系统。
本案例中的软件系统,是由上海同振信息技术有限公司开发完成的。
?
生鲜商品按其秤重包装属性可分为:
定量商品、秤重商品和散装商品,按物流类型分:
储存型、中转型、加工型和直送型;按储存运输属性分:
常温品、低温品和冷冻品;按商品的用途可分为:
原料、辅料、半成品、产成品和通常商品。
生鲜商品大部分需要冷藏,所以其物流流转周期必须很短,节约成本;生鲜商品保值期很短,客户对其色泽等要求很高,所以在物流过程中需要快速流转。
两个评判标准在生鲜配送中心通俗的归结起来就是“快”和“准确”,本文下面分别从几个方面来说明一下联华生鲜配送中心是如何做的。
订单管理
?
门店的要货订单通过联华数据通讯平台,实时的传输到生鲜配送中心,在订单上制定各商品的数量和相应的到货日期。
生鲜配送中心接受到门店的要货数据后,立即生成到系统中生成门店要货订单,按不同的商品物流类型进行不同的处理:
?
1、储存型的商品:
系统计算当前的有效库存,比对门店的要货需求以及日均配货量和相应的供应商送货周期自动生成各储存型商品的建议补货订单,采购人员根据此订单再根据实际的情况作一些修改即可形成正式的供应商订单。
?
2、中转型商品:
此种商品没有库存,直进直出,系统根据门店的需求汇总按到货日期直接生成供应商的订单。
?
3、直送型商品:
根据到货日期,分配各门店直送经营的供应商,直接生成供应商直送订单,并通过EDI系统直接发送到供应商。
?
4、加工型商品:
系统按日期汇总门店要货,根据各产成品/半成品的BOM表计算物料耗用,比对当前有效的库存,系统生成加工原料的建议订单,生产计划员根据实际需求做调整,发送采购部生成供应商原料订单。
?
各种不同的订单在生成完成/或手工创建后,通过系统中的供应商服务系统自动发送给各供应商,时间间隔在10分钟内。
物流计划?
在得到门店的订单并汇总后,物流计划部根据第二天的收货、配送和生产任务制订物流计划。
?
1、线路计划:
根据各线路上门店的订货数量和品种,做线路的调整,保证运输效率。
?
2、批次计划:
根据总量和车辆人员情况设定加工和配送的批次,实现循环使用资源,提高效率;在批次计划中,将各线路分别分配到各批次中。
?
3、生产计划:
根据批次计划,制定生产计划,将量大的商品分批投料加工,设定各线路的加工顺序,保证和配送运输协调。
?
4、配货计划:
根据批次计划,结合场地及物流设备的情况,做配货的安排。
储存型物流运作?
商品进货时先要接受订单的品种和数量的预检,预检通过方可验货,验货时需进行不同要求的品质检验,终端系统检验商品条码和记录数量。
在商品进货数量上,定量的商品的进货数量不允许大于订单的数量,不定量的商品提供一个超值范围。
对于需要重量计量的进货,系统和电子秤系统连接,自动去皮取值。
?
捡货采用播种方式,根据汇总取货,汇总单标识从各个仓位取货的数量,取货数量为本批配货的总量,取货完成后系统预扣库存,被取商品从仓库仓间拉到待发区。
在待发区配货分配人员根据各路线各门店配货数量对各门店进行播种配货,并检查总量是否正确,如不正确向上校核,如果商品的数量不足或其他原因造成门店的实配量小于应配量,配货人员通过手持终端调整实发数量,配货检验无误后使用手持终端确认配货数据。
?
在配货时,冷藏和常温商品被分置在不同的待发区。
中转型物流运作?
供应商送货同储存型物流先预检,预检通过后方可进行验货配货;供应商把中转商品卸货到中转配货区,中转商品配货员使用中转配货系统按商品再路线再门店的顺序分配商品,数量根据系统配货指令的指定执行,贴物流标签。
将配完的商品采用播种的方式放到指定的路线门店位置上,配货完成统计单个商品的总数量/总重量,根据配货的总数量生成进货单。
中转商品以发定进,没有库存,多余的部分由供应商带回,如果不足在门店间进行调剂。
?
三种不同类型的中转商品的物流处理方式:
*不定量需秤重的商品
设定包装物皮重;
由供应商将单件商品上秤,配货人员负责系统分配及其他控制性的操作;
电子秤秤重,每箱商品上贴物流标签。
*定量的大件商品
设定门店配货的总件数,汇总打印一张标签,贴于其中一件商品上。
*定量的小件商品(通常需要冷藏)
在供应商送货之前先进行虚拟配货,将标签贴于周转箱上;
供应商送货时,取自己的周转箱,按箱标签上的数量装入相应的商品;
如果发生缺货,将未配到的门店(标签)作废。
?
加工型物流运作?
生鲜的加工按原料和成品的对应关系可分为两种类型:
组合和分割,两种类型在BOM设置和原料计算以及成本核算方面都存在很大的差异。
在BOM中每个产品设定一个加工车间,只属于惟一的车间,在产品上区分最终产品、半成品和配送产品,商品的包装分为定量和不定量的加工,对于秤重的产品/半成品需要设定加工产品的换算率(单位产品的标准重量),原料的类型区分为最终原料和中间原料,设定各原料相对于单位成品的耗用量。
?
生产计划/任务中需要对多级产品链计算嵌套的生产计划/任务,并生成各种包装生产设备的加工指令。
对于生产管理,在计划完成后,系统按计划内容出标准领料清单,指导生产人员从仓库领取原料以及生产时的投料。
在生产计划中考虑产品链中前道与后道的衔接,各种加工指令、商品资料、门店资料、成分资料等下发到各生产自动化设备。
?
加工车间人员根据加工批次加工调度,协调不同量商品间的加工关系,满足配送要求。
配送运作?
商品分捡完成后,都堆放在待发库区,按正常的配送计划,这些商品在晚上送到各门店,门店第二天早上将新鲜的商品上架。
在装车时按计划依路线门店顺序进行,同时抽样检查准确性。
在货物装车的同时,系统能够自动算出包装物(笼车、周转箱)的各门店使用清单,装货人员也据此来核对差异。
在发车之前,系统根据各车的配载情况出各运输的车辆随车商品清单,各门店的交接签收单和发货单。
?
商品到门店后,由于数量的高度准确性,在门店验货时只要清点总的包装数量,退回上次配送带来得包装物,完成交接手续即可,一般一个门店的配送商品交接只需要5分钟。
案例五、松下配送中心
松下物流(PanasonicLogistics)负责松下电气及电子产品的配送工作,它的一个配送中心于1997年10月在英国Northampton成立。
该中心由于在运作中有效的利用了高科技而声名鹊起。
?
?
松下清楚地认识到,由于操作系统不能达到自动化,致使操作人员在仓库内外转来转去,这实在是太浪费时间。
新配送中心的指导思想是:
采用自动传送装置及自动数据采集(ADC)技术(主要是射频数据通信(RF/DC)即条码技术),将产品传送到操作人员面前,而不是操作人员移动到产品所在之处。
为此,松下安装了一系列的自动化设施。
这不但减少了人工数据采集系统所需的员工数量,而且提高了整个操作过程的效率。
?
?
配送中心自采用新技术以来,纸张的使用量大大减少,工作的准确率提高,对客户的需求反映灵敏。
同时,员工也非常欢迎这个分拣系统,因为它不象纸张作业那样枯燥无味;另外,该系统使员工更多地融入到高技术体系中,使他们感到自身的存在价值。
?
?
该配送中心采用了ADC系统,以实现对公司8万多台电视机、录像机、复印机,乃至医疗设备等产品的跟踪和配送。
由于仓库面积为3.6万平米,拥有2.3万个托盘站点,每个托盘站点高22米,有5个通道,高层货舱存储;还有10万个分检站点,从完整的托盘和箱体流开始,然后将其转移到圆盘传送带,直至最终搁置与货架上。
设计这一套设施时,松下研究人员了解到,ADC系统是跟踪货物出入仓库的关键。
?
?
仓库的自动化
?
?
该中心的建立旨在将不同的配送场所统一为一个配送中心,因此另外三各地区的仓库都已关闭,并入Northampton。
抵达的货物包括成品,零部件以及备用零件。
成品和备用件被送到独立的零售商和国内客户。
?
?
跟踪仓库中的产品由ADC系统完成,它包括射频数据通信(RF/DC)终端、手持式条码扫描器、标签打印机和"按键亮灯"(put-tolight)分类系统。
另外Microlise公司还提供射频终端和扫描器。
?
?
货物一到达仓库,就由仓库工作人员人工码成托盘。
一旦托盘被码好,就贴上一个交叉二五条码(ITF)标签。
该条码包括产品号、数量和目的地的编号。
标签是由放置于叉车上的Blaster直接热敏式条码打印机打印。
然后,叉车将托盘放在传送带上,运送到仓库的高层货舱。
标签将一直贴在托盘上直至托盘被拆卸或作为一个完整的托盘送出仓库。
?
?
分拣过程
?
?
仓库中有许多用于组装客户订单的分拣站。
箱体流库存(由与传送带相邻的重力自动供给架支撑)主要服务于快速移动产品,也为移动速度较慢的产品提供搁置架。
另外,还有4个垂直圆盘传送带传送小零件,2各水平传送带传送组件。
?
?
订购的货物被装入塑料装运箱中,大件产品则装入单个的箱体中,如电视机。
分拣每一件产品时,打印Code39条码标签并贴在装运箱上。
该条码对产品、订单号及客户的信息进行编码。
?
?
操作人员利用带有累加器的特制分拣车针对客户订单组装货物。
此种工具车装备有名为Tracker的射频终端,该终端与条码扫描器和Blaster打印机连接。
在每个圆盘传送带上的分件和输入工作由一个PC终端机装备有利用模糊运算进行译码的手持式激光扫描器,而标签打印机的作用是指导操作人员检查备件货物是否正确。
?
?
一旦备件货物全部被分拣出来,累加器就被转移至用以发货的传送装置上。
装有成品的箱体被分拣出来并放置于传送带上等待分类,箱体上的条码被扫描以识别其所属订单。
?
?
小型货物的特殊处理
?
?
备用件和小件货物,如轮齿、电阻器或芯片的分拣方式不同。
按键亮灯系统时操作人员能够将20件不同的订货作为一个批次装入同一装运箱中。
操作人员并不知道哪些货物应发给那个客户,他只要将装运箱放置到运送装置上,并贴上含有订单号的条码即可。
装运箱在寄销运送装置上传送时,其标签将被安装在运送装置上的固定式扫描器扫描,系统再将装运箱送往分类系统。
?
?
分类工作站有三个组,每组20个站点,每个站点分别为一个用户准备一个专门的物料箱。
操作人员将装运箱顶部的号码输入PC机之后,用射频扫描器扫描装运箱中的所有货物。
与该号码对应的物料箱的指示灯就会发亮,这便指示出了需要该货物的客户地址。
据此,该货物就放置在这一物料箱中。
?
?
当所有的货物都被放置到正确的物料箱中后,物料箱则被转移到另一边。
在那里,操作人员将他们包装起来等待发货。
此时,下一个物料箱已经到达。
操作人员将第二批货物分拣出来并进入下一20个站点组,接着是第三个站点组,然后再重返第一组站点。
该系统提高了在备件