中频炉的筑炉补炉炉衬烧结工艺.docx
《中频炉的筑炉补炉炉衬烧结工艺.docx》由会员分享,可在线阅读,更多相关《中频炉的筑炉补炉炉衬烧结工艺.docx(48页珍藏版)》请在冰豆网上搜索。
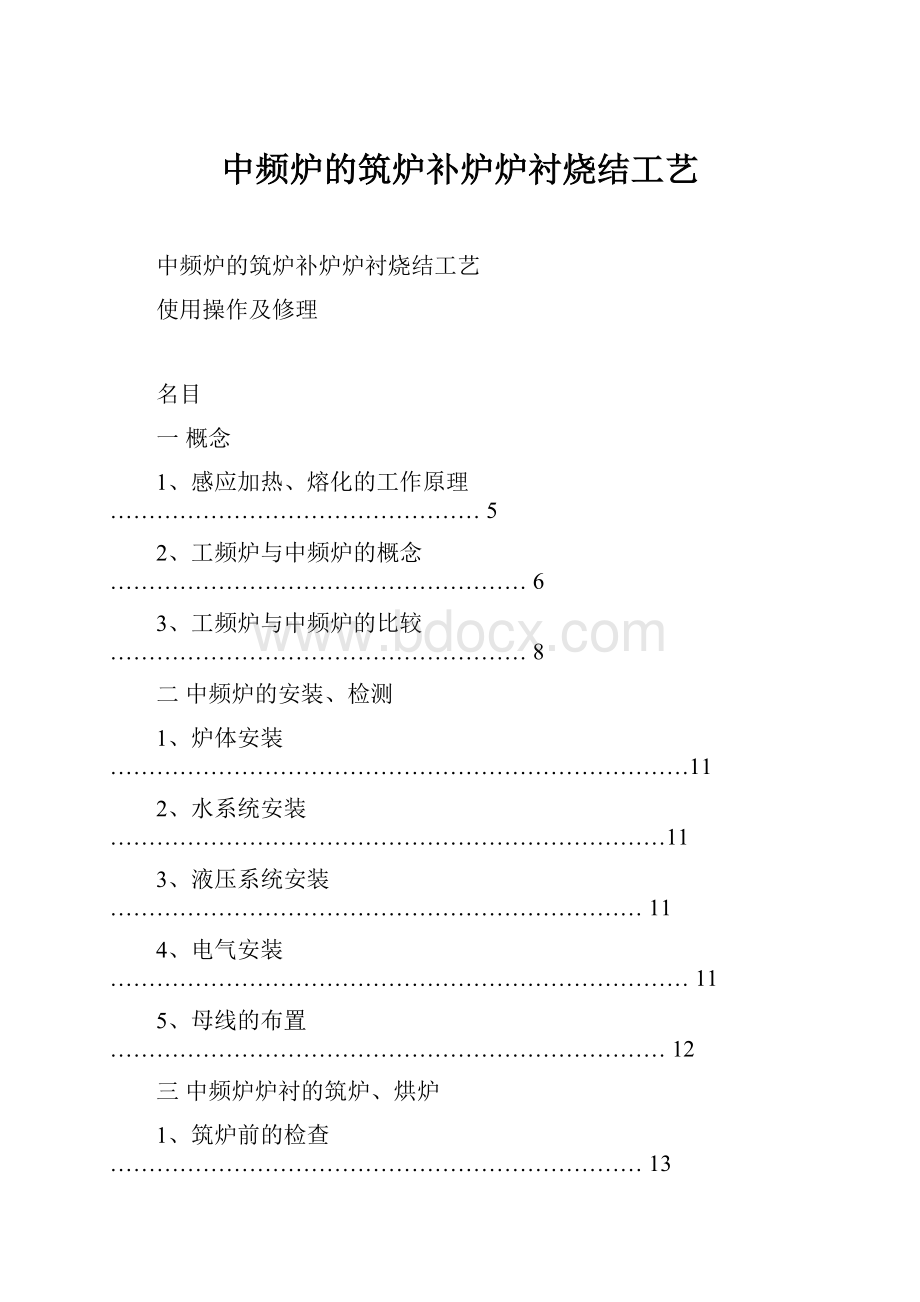
中频炉的筑炉补炉炉衬烧结工艺
中频炉的筑炉补炉炉衬烧结工艺
使用操作及修理
名目
一概念
1、感应加热、熔化的工作原理…………………………………………5
2、工频炉与中频炉的概念………………………………………………6
3、工频炉与中频炉的比较………………………………………………8
二中频炉的安装、检测
1、炉体安装…………………………………………………………………11
2、水系统安装………………………………………………………………11
3、液压系统安装……………………………………………………………11
4、电气安装…………………………………………………………………11
5、母线的布置………………………………………………………………12
三中频炉炉衬的筑炉、烘炉
1、筑炉前的检查……………………………………………………………13
2、筑炉………………………………………………………………………13
3、烘炉、炉衬烧结机理及三层结构………………………………………16
四炉衬的损坏机理及预防
1、过热………………………………………………………………………20
2、裂纹………………………………………………………………………21
3、剥落………………………………………………………………………22
4、腐蚀………………………………………………………………………23
5、炉瘤………………………………………………………………………25
6、浸润………………………………………………………………………25
7、其它延长炉衬使用寿命的措施…………………………………………25
五炉衬的修补
1、热补法……………………………………………………………………27
2、冷补法……………………………………………………………………28
六中频炉的使用
1、开炉前的预备及检查……………………………………………………28
2、开机操作…………………………………………………………………29
3、停机操作…………………………………………………………………29
4、冷启动……………………………………………………………………30
5、使用中的操作……………………………………………………………30
6、严格禁止的操作…………………………………………………………33
七中频炉的日常爱护和检修要点
中频炉的日常爱护检修要点(见“周期表”)……………………………34
八事故处理
1、停电………………………………………………………………………34
2、漏液………………………………………………………………………35
3、冷却水事故………………………………………………………………36
九其它
1、中频炉的熔化率与生产率………………………………………………36
2、冷却水泵供电……………………………………………………………37
3、冷却水……………………………………………………………………37
4、中频炉熔化比工频炉快的要紧缘故……………………………………37
5、中频炉比工频炉节能……………………………………………………38
6、冷却水塔…………………………………………………………………38
7、感应圈与磁轭间的绝缘材料……………………………………………38
8、关键元件的制造商(国外)……………………………………………38
9、熔化炉额定功率的配置…………………………………………………38
10、保温中频炉最小功率配置………………………………………………39
11、冷却水管接头卡篐材质要求……………………………………………39
12、磁轭的作用………………………………………………………………39
13、无碳胶管的作用…………………………………………………………40
14、坩埚(炉衬)的作用与厚度……………………………………………40
15、感应器及坩埚的高度……………………………………………………41
16、阻碍熔化单耗指标的因素………………………………………………42
17、关于“防电蚀管”………………………………………………………44
18、感应炉冷却水的特点及对水质的要求………………………………44
中频炉的筑炉、炉衬烧结、使用操作及修理
一概述
1、感应加热、熔化的工作原理
(1)一个无芯感应炉,要紧由线圈及放入其中熔化的金属炉料所构成,运行的差不多原理是电磁感应。
感应电炉中有一个感应线圈,当它通上交流电时即建立交变磁场。
要加热的金属炉料放置于交变磁场中(见图1),由于电磁感应作用,金属炉料内产生电流,电流通过金属炉料电阻时使金属炉料发热。
可见,感应电炉是应用电磁感应原理将电能传递给金属炉料,而电能交换为热能的方式属于电阻加热。
Q=I2Rt(J)
式中:
Q-电流通过电阻产生的热量(J)
I-电流(A)
R-金属炉料等效电阻(Ω)
t-通电时刻(S)
感应炉确实是利用那个热量使金属炉料发热熔化。
我们能够看出,要进行感应加热,必须满足两条件:
1)用交流电;
2)被加热物体必须是金属材料。
由于注入线圈中的电流总是滞后于电压,熔炼时感应线圈的典型功率因数仅为0.1。
因此,就要把电容同线圈并联连接以进行功率因数的补偿,因为电容电流总是超前于电压,因此选择正确的电容、线圈组合,功率因数可达到1.0,这确实是使用补偿电容的缘故(见图2)。
2、工频炉与中频炉的概念
1)工频炉
工频感应电炉是直截了当利用都市电网交流电(频率为50HZ或60HZ)工作的。
小容量电炉由380V网提供,大、中容量电炉由6KV以上高压电网供电。
2)中频炉
(1)概念
中频感应电炉采纳大电流半导体(如:
IGBT、可控硅)构成变频器,将电网50HZ交流电通过变频器升为200HZ~10000HZ的中频电流,然后送至电炉的感应圈。
中频电流产生的磁场具有更高的耦合效率,能够使更多的能量送到炉内被熔化的金属中,从而能够获得高效和快速的熔化。
中频电源的工作功能为(见图3):
交流(50HZ)→直流→交流(100HZ~10000HZ)→炉体线圈
图3中频电源工作功能示意图
1-三相交流输入3-滤波器5-逆变器7-感应线圈
2-全波整流4-单相直流电6-单相交流电
(2)常用的二种逆变电路
a、并联电路(电流型逆变器,见图4)
并联型逆变器一样具有一个产生可变直流电压的整流器,一个直流电抗器和一个全桥逆变部分,其高频输出同炉子线圈相连,线圈两端接有并联功率因数补偿电容。
图4并联电路原理
1-三相交流电3-整流器5-滤波电抗器7-补偿电容器I-电流
2-输入端4-单相直流电6-逆变器8-炉子感应圈
优点:
电流I只在补偿电容和线圈间流淌,因而效率较高。
其结构严密,操纵全面,运行可靠性高。
缺点:
低功率运行状态下其功率因数较低。
b、串联电路(电压型逆变器,见图5)
串联型逆变器一样具有一个固定直流输出电压的整流器和一组较大的直流电容,向逆变部分提供了一个低阻抗的电压源。
现代串联电路使用一半桥逆变器,电源输出连接到同功率因数补偿电容相串联的炉子线圈上。
图5串联电路原理
1-三相交流电3-整流器5-滤波电容器7-补偿电容器I-电流
2-输入端4-限流电抗器6-逆变器(串联)8-炉子感应圈
要紧优点是:
(1)在所有功率水平下都有专门好的功率因数。
(2)采纳不控整流,工作时整流可控硅全导通,因此高次谐波重量小,对电网阻碍小。
(3)其启动成功率不论是冷炉依旧热炉均为100%。
要紧缺点是电流I不仅流经补偿电容器和线圈,还流经SCR,使SCR长期在大电流下运行,阻碍寿命。
3、中频炉与工频炉的比较
尽管中频炉和工频炉均属感应电炉,但除了使用的电源频率不同以外,还有许多差异:
(1)中频炉升温快,熔化率高
中频炉功率密度大,每吨容量炉料的功率比工频炉大50%~200%。
工频:
250KW/t,而中频500KW/t以上(高密度达到700~1000KW/t)
(2)适用性和灵活性
中频炉在空炉、满炉情形下都能100%启动,并在专门短时刻内达到满功率。
同时,中频炉能够倒空铁水,更换炉料方便,适应多种牌号的铁水的生产。
由于没有存留铁液,调整铁水成分方便,不受限制,宜少批量、多品种材质生产方式。
另外,中频炉投入熔化功率能够从5%~100%无级调剂,铁水温度操纵也精确。
(3)中频炉由电子操纵,连续可调,能够恒定满功率输入。
(4)相同容量的中频炉占地面积比工频炉小(无庞大的电容空间,中频炉补偿电容少,能够安装在一个柜子内),一次投资可减少10%~15%。
(5)中频炉内铁水搅拌力与功率密度成正比,与频率平方根成正比,因而容易操纵。
既能充分搅拌,又不像工频炉那样猛烈翻动。
由于工频炉的频率(50HZ)固定,但随功率的变化而变化,因此当功率提高时,搅拌力提高专门大,能把浮在铁液上面的炉渣卷入铁液内,且铁水在翻动中不断同空气中的O2接触而氧化,元素烧损严峻(1小时烧损1%),使铁液纯度下降,阻碍产品质量。
中频炉实际上也是变频炉,熔化过程频率在变化,会自动全过程跟踪。
频率变化范畴:
下限为额定频率的50%,上限为额定频率的120%。
附:
铁水驼峰运算公式
H=695×N×P÷ρ÷
÷
÷
式中:
H-铁水驼峰高度(mm)F-频率(HZ)A0-坩埚直径(英寸)N-线圈效率(0.838)L-线圈高度(英寸)W-炉料重量(磅)P-输入功率(KW)ρ-熔化金属密度(0.26磅/立方英寸)R-金属电阻率(200微欧姆/cm)
(6)假如倒空铁水后加料,则炉料干湿程度不受限制。
工频炉由于不能倒空铁水熔炼,因此熔化过程不能加湿料,否则会产生爆炸。
(7)中频炉冶炼时刻短,从冶金角度看,熔化金属液只存在一次过热,而不像工频炉那样多次、长时刻过热,铁水内在质量好。
(8)中频炉电效率比工频炉高
中频炉在批量熔化作业前期,由于金属炉料电阻大,磁性固态冷料启动时的线圈电效率高达95%。
在温度高于居里点(799℃)以上时,由于炉料间存在接触电阻,线圈电效率可高达90%左右。
当金属炉料完全熔化时,现在线圈电效率为80%左右,与工频炉残液熔化法时的线圈电效率相同。
可见中频炉的批料熔化法在整个作业周期内平均电效率可达88%,高于工频炉残液法熔化周期内的80%。
(9)中频炉在节假日不生产时能够倒空铁水,不必像工频炉那样要做液态保温,故能够减少保温铁水用电耗,也不必派人值班。
(10)中频炉炉衬的寿命比工频炉低,其缘故是:
1)通过把功率和频率的专门好匹配,中频炉有效电磁场集中在炉衬的热表层而成功地提高了熔化效率,其炉料从外向里开始熔化,外部炉料与其接触的炉衬会专门快过热(无芯工频炉则从里向外熔化炉料),对炉衬不利。
2)作为熔化炉的中频炉由于熔化率高,意味着炉衬长期处于高温铁水的浸蚀。
炉料中的碳等元素在高温下会发生“坩埚反应”,使炉衬SiO2被还原成Si,形成炉渣,故炉衬逐步被浸蚀变薄。
SiO2+2C→Si+2CO↑
(11)中频炉电源柜可控硅、电容器均应用水冷却,对水质要求高,而工频炉电器不必水冷却。
(12)中频炉电耗比工频炉低
由于中频炉电效率高,熔化率高,同样熔化相同炉料所需时刻中频炉比工频炉短,熔化过程的热缺失相对比较少,因而电耗低。
(13)由于中频坩埚式感应电炉的功率密度较工频坩埚式感应电炉的高,在相同的熔化率要求下,其炉子容量小,相应的热缺失也小。
二中频炉的安装检测
中频炉的安装要注意如下咨询题:
1、炉体安装第一要在平的地基上安装炉架,然后安装倾炉油缸、炉体等。
2、水冷系统的安装安装前应检查系统中的各种管道、软管以及相应的接头尺寸是否符合设计要求。
开式水冷系统的进水管最好使用镀锌管,与中频炉配套的闭式水冷系统的所有水管应选用铜管或不锈钢管,备用水源及其他切换系统也应安装完毕。
水冷系统安装完毕要进行耐压试验(试验水压为使用压力的1.5倍保持10min,所有焊缝及接头均无渗漏为合格。
3、液压系统安装油泵站一样安装在有一定高度的基础上,便于修理时从油箱内排油。
同时,即使发生严峻漏炉事故也能保证油箱不受金属溶液的侵害(安装油管也应做此考虑)。
液压系统安装完毕也应做耐压试验(1.5倍工作压力保持10min)。
然后做倾炉试验。
4、电气系统电气系统安装应注意如下咨询题:
1)所有操纵线两端均应有端子号。
安装完毕后要认真检查并试验电气动作,使所有电气及其连接装置的工作准确无误。
2)感应器通水前,检测感应器的绝缘电阻,并做耐压试验。
感应器应能承担2Un+1000V(但不低于2000V)的绝缘耐压试验1min而无闪络和击穿现象(Un为感应器的额定电压)。
在高压试验时,电压从1/2规定值开始,在10S内达到最大值。
感应器中不同感应圈之间、感应圈与地之间以及感应圈与磁轭间的电阻要满足如下要求:
额定电压在1000V以下,用1000V兆欧表,其绝缘电阻值不低于1MΩ;额定电压1000V以上者,用2500V兆欧表,其绝缘电阻值不低于1000Ω/V。
若发觉绝缘电阻值低应对感应器进行干燥处理(可借助放于炉内加热器或吹热风),但现在应注意防止对绝缘有害的局部过热。
3)磁轭的每一个穿芯螺栓对硅钢片及对地面应有良好的绝缘,用1000V兆欧表测量,其绝缘电阻值不低于0.5MΩ。
5、母线的布置
1)尽可能缩短母线距离,例如补偿电容与炉体尽可能靠近;
2)从改善冷却成效提高母线载流量角度动身,母线宜竖放,即母线宽的一面彼此相对(母线平放则承诺负荷将降低8%左右);
3)邻近效应也会导致导体有效截面利用率的降低,单相多条并联母线宜采纳交错组合,三相系统则以A、B、C、D交替排列,使导体电感减少。
4)不同极性的母线间的距离在绝缘强度的承诺下,要尽量靠近,因母线的感抗随着母线间的距离增大而增大。
5)不应用铠装或有金属包皮的工频单芯电缆传输中频电流,可用两芯或四芯铠装或有金属包皮的电缆,但芯线必须载往返方向电流,同极性的芯线要对角布置(四芯电缆)。
6)当母线电流大于1500A时,在其邻近300mm范畴内不应有钢铁构件。
三中频炉衬的筑炉、烘炉
1、筑炉前的检查
1)检查电气、液压、水冷系统,作送电、倾炉、通水试验。
2)检查感应器的绝缘情形。
3)检查报警器。
4)选择合适的坩埚坩埚模用δ=6~10mm钢板卷焊而成。
模体带一定锥度,采纳连续焊接(幸免通电时焊缝打火,造成电流不稳,甚至过流爱护)。
焊缝不处应打磨光滑,并排除氧化锈(以免渗入炉壁结渣阻碍炉衬寿命)。
整个坩埚模外表面应光滑平坦,专门是侧壁与底部相连圆弧处应选择较大为宜(通常取坩埚模内径的0.1倍为最大承诺圆弧半径)。
另外坩埚模表面应布满φ3.0mm的小孔供烘炉时排放水汽,孔距200mm。
5)筑炉人员应穿戴洁净的工作服,鞋子也要洁净,戴帽;炉台周围洁净无杂物,整个筑炉过程不得有杂物(专门是残铁)进入炉衬内。
2、筑炉
1)、铺设绝缘层、隔热层及报警电极
a、炉壁自感应器至炉子中心顺序铺设
耐火水泥(抹上δ=8~10mm)→钢丝网(报警电极)→耐火水泥(δ=8~10mm)→云母板(δ=1.5mm)→石棉板(δ=3~4mm)→石棉布(δ=2mm)。
铺设时用张紧圈顶紧,每层平坦无皱折,竖缝搭接,横缝对接,相邻两层的接缝错开,不得有杂物混入。
目前另一种报警装置为“地漏监视装置”,不需要在炉衬材料内安装上述第二电极(但底电极仍需要),直流低压电加在感应圈电源线与地之间。
炉衬正常时电阻专门大,电流专门小。
假如发生炉衬低电阻现象(如炉衬变薄,金属液渗漏都会造成炉衬低电阻),这时电流表的读数专门大,装置的跳闸继电器动作并发生报警信号。
3)筑炉底
a、若有炉底打结机,则用炉底打结机打结。
手工打结用风动平锤,分两次打结,打实四遍以上。
打结后其体积密度达到2.3Kg/cm3。
在第二次加料前拆除下部张紧圈,刮平炉底表面料层,用平板和水平仪沿各个方向检查,保证炉底底料水平。
b、每次投料后,第一用钢叉插一遍,除去炉衬材料中的气体,再将炉料刮平,然后从中央开始捣固,逐步向外缘扩展。
c、再次投料前,用钢叉将捣固的炉衬划一遍,防止炉衬分层。
d、最后一次捣固后要保证炉底厚度比实际厚度突出50mm以上,再刮出余外的炉料,并用水平尺找平,注意找好中心,炉底以外的部分不要刮出,否则安放坩埚钢模后处理打结好炉底较困难,容易产生分层。
4)坩埚模的放置(清除外表面铁锈及污物)
放中后,四周用固定尺寸的木块固定,测量坩埚模与铺设的石棉板间距离,以保证炉衬侧壁尺寸平均。
各方向误差操纵在±5mm之间,保证模子对中。
5)捣固斜坡部位
斜坡部位是关键部位之一,因为该部位机械冲刷厉害,腐蚀严峻(俗称“大象脚”现象),也是捣固最困难的地点,是整个炉衬最薄弱的环节,必须保证打结质量。
a、第一用钢叉将炉底面拉毛,划松,以防止分层。
b、确定没有异物掉入后,开始加料。
每加入一遍料要用钢叉叉一遍(手工除气),然后再捣固。
捣固时尽量贴近坩埚模,以免损坏感应圈内壁的云母绝缘片。
检查确认没有异物掉入后,再加料,重复上述过程。
6)侧壁部位的捣固
捣固方法同上。
但炉口应留尺寸,因为炉衬再烧结时,体积会膨胀。
同时整体炉壁打结完后,刮去坩埚模的余外部分。
注:
假如使用电动筑炉机,可采纳整体筑炉壁的方法:
7)筑制铁流槽
用耐火砖水玻璃石英砂和筑炉用石英砂筑制流铁槽。
炉衬本体与流铁槽结合处不得有间隙和孔洞。
3、烘炉、炉衬烧结机理及三层结构
(1)炉衬烧结过程机理及结构
1)机理
a、当炉衬被加热到573℃时,炉衬中的的β-石英快速转化成α-石英,体积膨胀0.82%。
b、温度连续上升到1200~1400℃经半安定方适应转化为α-鳞石英,体积膨胀16%。
c、当炉衬温度连续升高到1470℃,α-鳞石英转化为α-方石英,现在炉衬完成烧结过程。
在烧结过程中,由于晶型的转变,硅质干振炉衬发生急剧变化,它把捣结的炉衬变得更加致密。
由于石英的慢变化过程是不可逆转的,这就使获得烧结良好的炉衬的膨胀和收缩变得比较稳固。
含有较多α-方石英的烧结层具有较长的使用寿命。
2)炉衬的三层结构及阻碍
三层结构的炉衬:
烧结层、半烧结层、缓冲层(松散层)。
各层初始厚度各占炉衬厚度的1/3,界线清晰。
烧结层表面光滑呈釉面状,截面内无明显粗大裂纹,挂渣少。
缓冲层作用:
万一铁水钻过烧结层和半烧结层时能在此停住。
a、炉衬材料
具有高的SiO2含量和低的Fe2O3含量的优质石英精细晶型的硅砂,沉积岩型为最佳。
b、具有科学的配比颗粒等级,以达到理想的捣实密度(2.1g/cm3以上)。
最大的粒度6~7mm。
c、尽可能选用硼酐做粘结剂,以缩短烘炉时刻。
硼酸在301℃时被分解为水和硼酐,采纳硼酐的用量为硼酸的58%左右,且升温速度快50%。
d、选择合适的保温层厚度,可有效操纵烧结层厚度,调剂炉衬的热缺失;
过厚的保温层虽能够降低热缺失,但却明显提高了保温层与炉衬接口的温度,其结果是降低了炉衬内的温度梯度,使合理的分层结构受阻碍。
(2)烘炉过程的操纵
新炉炉衬筑完后应尽快烘炉,不宜长期搁置。
a、送电烘炉前,第一应检查炉子电气、水冷系统、液压系统等各个方面是否正常,确认没有专门情形后方能进入烘炉程序。
b、送电前,通过炉盖观看孔设置热电偶。
为防止加料时砸坏热电偶,可采取爱护措施(将热电偶置于钢管内并焊在钢制坩埚模内壁)。
同时热电偶容易伸入底部,现在冷却水压调整为0.05~0.08Mpa。
c、严格按照烘炉曲线烘炉烧结,通过调剂电压严格操纵中频炉的输入功率以操纵升温。
严格操纵烘炉过程,升温速度极为重要。
只有严格操纵升温速度,使石英在几个温度区范畴内,有充分时刻完成所需的晶型转变,是猎取理想烧结层的必要条件。
烧结过程中,最高电压不能超过额定电压的70%~80%。
同时严格操纵冷却水的流量,在炉温升高过程中逐步增大冷却水流量(炉子温度达到600℃时,水压调整为0.18~0.2Mpa。
d、烘炉温度达到1100℃时应装入清洁无锈的生铁块(也有的在烘炉前先将炉料加入钢坩埚内),逐步提高功率至额定值。
连续加料至金属液面与炉衬上端口齐平。
e、铁液温度达到1550℃时,降低功率保温3~4个小时后才出铁水。
f、在1350℃保温烧结期间,严格操纵铁水搅拌,力争炉衬静态烧结。
g、烘炉加入的炉料选用
由于不使用起熔块,因此大块生铁和不规则的回炉料使负荷变动增大而阻碍频率的变换(此外并联变频电炉在处于高负荷时产生频率变换错乱;由于存在“坩埚反应”(在金属液中:
SiO2+2C→Si+2CO↑)而烘炉时炉衬未烧结好,铁水易浸入与炉衬发生上述反应,对炉衬不利。
基于上述二个缘故,烘炉时最好选用小块回炉料,而不采纳生铁(生铁含碳量高),同时要填堆密实(可在层间用铁屑填补间隙)。
因此还要轻放(连续逐次加入)。
h、烘炉记录:
从开始送电至首次出铁水,每15min记录炉内温度1次,水压1次。
i、新炉稳固后,三天内每次出铁水量不超过1/3.半个月内严格操纵炉温,不得超过熔炼工艺所要求的铁水温度;无生产任务的班次,应把4/5的铁水保温在1350℃左右,一个月内不得停炉(专门情形例外)。
J、烘炉完成后倾炉让铁水滞留在出铁槽上5~8min,便于铁流槽初次烧结。
四、炉衬的损坏机理及预防
炉衬的好坏直截了当阻碍炉衬寿命,也与生产紧密相关。
中频炉炉衬损坏机理要紧有过热、裂纹、剥落、腐蚀、结瘤或浸润等因素。
1、过热
过热的缘故要紧有:
1)不合理的加料引起炉料搭桥;
2)捣筑时炉衬截面遗留金属物料;
3)炉温失控引起溶池超温;
具体分析如下:
a、冷炉料堆积在溶池表面时(专门是浇冒口料),易形成搭桥。
如搭桥炉料仍处于固态而连续送入较大功率的电时,则能够使溶池底部的金属液显现过热现象。
b、当炉衬开始烧结时,遗留在炉衬材料中的金属物件大量吸取功率并使局部过热,炉衬被迅速熔化并被腐蚀掉),形成空穴。
c、硅质干料的熔点温度为1704℃,炉温失控在短时刻内会超过该温度,从而引起过热而烧熔(最好高温不超1540℃)。
作业:
(周日)不生产的班次铁水保温1300~1350℃,浇注前送高功率迅速升温。
2、裂纹
金属翅浸透进炉衬截面而会引起炉衬损坏。
金属翅是由于炉衬显现裂纹渗进金属液所致,裂纹有三种:
1)横面裂纹由于筑炉时炉衬材料分层,或由于炉子结构上的缘故使炉衬松动所致。
分层:
振动捣实时,最小颗粒(专门是粉状料),集中表面形成薄薄的粉层,强度专门低。
再次加料时没有耙松,则上层捣实后即形成分层。
筑炉过程为了防止分层,每层加料前要把表面耙松,(20mm左右)。
在筑炉时每层炉料的加入厚度要依照筑炉方法和使用的筑炉工具的不同而调整(使用电动筑炉工具时每层加料厚度以60~80mm为宜)。
大型炉子的底部和侧壁下部的炉衬材料的加入(加料厚度大于500mm时)要求用漏斗加入,以防止炉衬材料掉落过程中产生颗粒偏析现象。
引起横向裂纹的另一种可能的缘故是炉子冷却时靠近出铁口的炉衬被粘附挂住,炉衬冷却而收缩时,产生裂纹。
◆抬炉:
保温铁水过低,造成上部铁水冷凝,再用大功率投入时,下部铁水(温度快升)将上部冷却料向上抬,从而带动炉料横向裂纹。
◆预先砌筑出铁口时,使它的内外轮廓与上部炉圈耐火材料的轮廓相同,便于炉衬冷却收缩时能自由滑落,不被挂住。
2