连铸新型中间包可行性分析.docx
《连铸新型中间包可行性分析.docx》由会员分享,可在线阅读,更多相关《连铸新型中间包可行性分析.docx(12页珍藏版)》请在冰豆网上搜索。
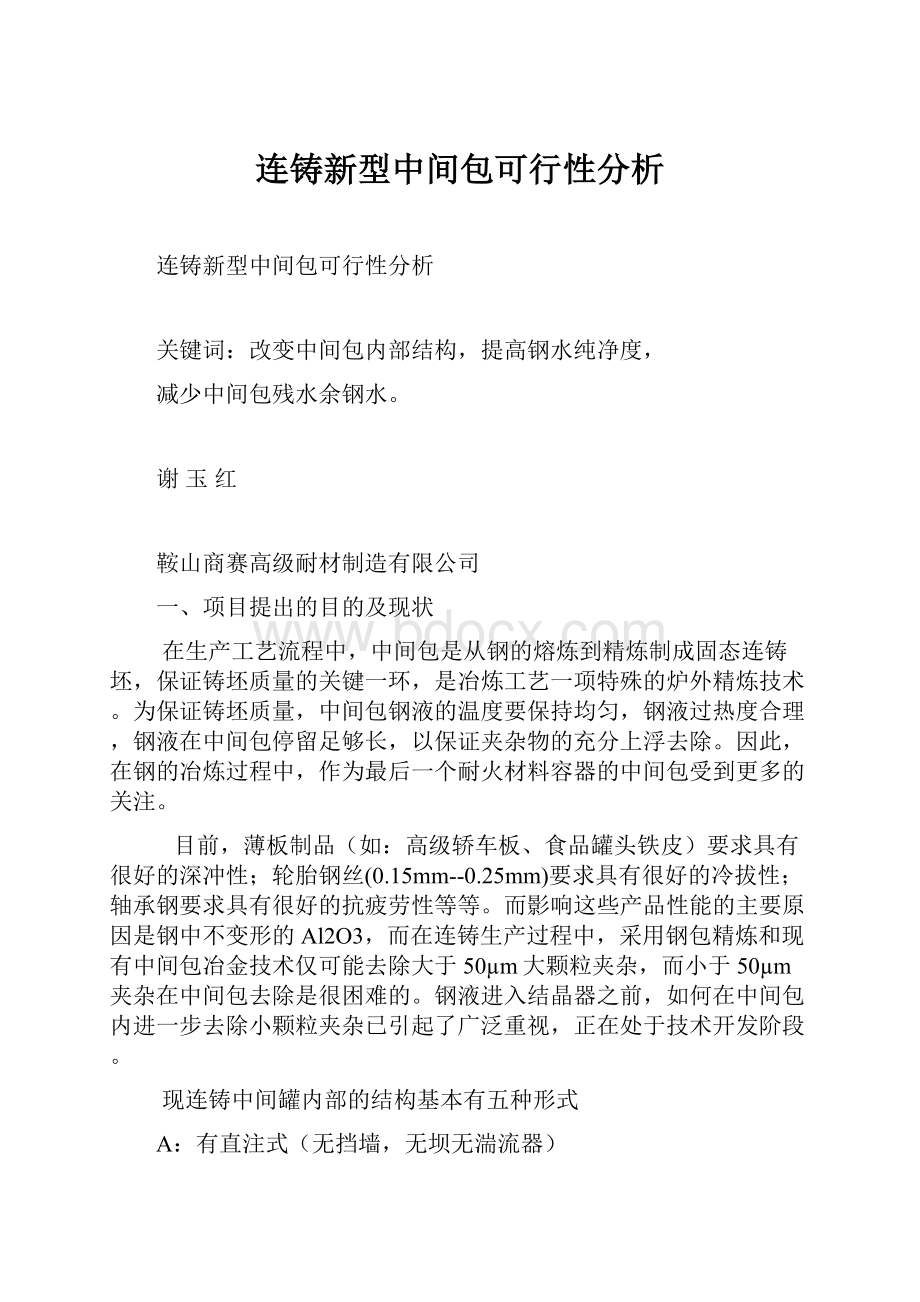
连铸新型中间包可行性分析
连铸新型中间包可行性分析
关键词:
改变中间包内部结构,提高钢水纯净度,
减少中间包残水余钢水。
谢玉红
鞍山商赛高级耐材制造有限公司
一、项目提出的目的及现状
在生产工艺流程中,中间包是从钢的熔炼到精炼制成固态连铸坯,保证铸坯质量的关键一环,是冶炼工艺一项特殊的炉外精炼技术。
为保证铸坯质量,中间包钢液的温度要保持均匀,钢液过热度合理,钢液在中间包停留足够长,以保证夹杂物的充分上浮去除。
因此,在钢的冶炼过程中,作为最后一个耐火材料容器的中间包受到更多的关注。
目前,薄板制品(如:
高级轿车板、食品罐头铁皮)要求具有很好的深冲性;轮胎钢丝(0.15mm--0.25mm)要求具有很好的冷拔性;轴承钢要求具有很好的抗疲劳性等等。
而影响这些产品性能的主要原因是钢中不变形的Al2O3,而在连铸生产过程中,采用钢包精炼和现有中间包冶金技术仅可能去除大于50µm大颗粒夹杂,而小于50µm夹杂在中间包去除是很困难的。
钢液进入结晶器之前,如何在中间包内进一步去除小颗粒夹杂已引起了广泛重视,正在处于技术开发阶段。
现连铸中间罐内部的结构基本有五种形式
A:
有直注式(无挡墙,无坝无湍流器)
图一
B:
有挡墙并在挡墙上开口
图二
C:
有挡墙(坝)
图三
D:
有挡墙(坝)和防湍流器
图四
E:
有湍流器
图五
由中间包容量与中间包钢液流量求出的钢液停留时间称为理论停留时间,然而在实际生产中,中间包内钢液流动是不均匀的。
有的地方快,有的地方慢,尤其是中间包底部区域存在不活跃的钢液停滞区,夹杂物上浮困难,钢液在中间包的实际平均停留时间要比理论平均停留时间要短些。
为充分有效地利用中间包容积,提高夹杂物上浮量,采取的措施是在中间包设置挡墙和坝。
其目的:
A消除中间包底部的区域流动存在死区
B改善钢液流动轨迹,使钢液流动沿钢渣界面进行缩短夹杂物上浮距离,有利于钢渣吸收排除。
C促使热流分布合理,使各水口处钢液的温度差减少到最低程度。
D挡渣墙还能将钢包注流冲击所引起的强烈涡流限制在局部区域防止絮流,扩散引起表面波动把钢渣卷入钢液中
对于高效连铸而言,由于它比一般连铸拉坯速度更快其钢包浇注速度也就更快,这样在中间包内产生的湍流现象就更为严重。
中间包内急剧的湍流,一方面会冲破渣层将钢渣卷入到钢液内,并使钢液暴露于空气中被二次氧化。
另一方面湍流还会严重的冲刷中间包侧墙,将其耐火材料卷入到钢液内,降低了中间包工作层的使用寿命。
此外,在开浇时,钢液飞溅严重还会促使中间包内结渣。
为解决上述问题,东北大学首先在国内部分钢厂推出防湍流冲击板(它使从钢包冲击的钢流向注流中心折回,防止湍流的产生)。
采取这一方法,在一定程度上提高了铸坯质量。
在实际生产过程中,由于连铸连浇换罐时钢液液面波动过大,大罐引流砂进入中间包或连浇时间长,钢液液面低于下挡坝或挡墙所开的孔时,使大量钢渣和夹杂进入浇注区,影响铸坯质量。
蔡开科教授经多年研究,认为采取挡坝和挡墙等方法只能去除夹杂颗粒直径大50µm,小于50µm很难去除。
中间包夹杂颗粒直径分布
r=1-35µmn(r)=2.0×1013exp(-0.576r)
r=36-75µmn(r)=7.75×106exp(-0.188r)
r>75µmn(r)=0
式中,n为夹杂物浓度(单位:
个/m³)
二、中间包夹杂去除机理
在中间包内夹杂物去除基本通过四种去除。
一是大颗粒夹杂通过上浮由钢液中排除。
二是夹杂通过碰撞长大上浮排除。
三是包衬壁上的粘附使夹杂物去除。
四是通过化学方法使杂物排除。
传统去除夹杂物方法是:
利用钢液密度(7.08ɡ/
)与夹杂物密度(0--3.5g/
)之间的差别。
使夹杂物上浮被钢渣吸收。
夹杂物上浮去除速度,服从斯托克斯(stokes)公式。
u=(ρm-ρs)ɡd²p
18μ
式中u为夹杂物上浮去除速度,ρm为钢液的密度,ρs为夹杂物密度,ɡ为重力加速度,dp为夹杂物直径,μ为钢液黏度系数。
用上式计算,dp=100mm的夹杂物上浮速度u≈0.36cm/s。
从本质上来说,斯托克斯(stokes)公式所计算的颗粒上浮速度是在克服介质摩擦阻力而达到的终速度,其初速度比该值还要小的多。
在中间包内流体本身的流动速度往往比上浮速度高出很多。
在冲击区域平均速度达0.12--0.15m/s,浇注区域平均速度为0.005-0.007m/s中间包夹杂颗粒跟随钢液流动,只有在流速较低的区域大颗粒有时间上浮,而小颗粒很难做上浮运动去除。
夹杂物上浮到熔池表面,由于其界面张力的不同,由钢液排出的倾向也不同。
对钢液不润湿的夹杂物,能由钢液中分离出来。
⑴中间包内钢液的流动特征,决定了其中物质和能量传输过程,为充分发挥中间包的各种冶金功能必须掌握中间包钢液流动的规律。
A液-液射流
中间包内钢液流动的动量来源于盛钢桶内液面-中间包液面-结晶器内弯月面在浇铸时的高度差,通过下降注流传递给中间包内钢液。
下降的钢液注流是中间包内注入区钢液运动状态的决定性因素。
由于中间包内液-液射流的流速分布对包内钢液流动有重要影响,因此有必要对其进行进一步分析。
普朗特(L.Prondtl)从理论上阐明,雷诺数很大的自由射流会在充满静止流体的足够大空间里扩展开来。
由于包内其他位置流速很低,可近似地按静止考虑。
射流内区域雷诺数很大,属于湍流流动,其纵向速度脉动的均方根值和横向速度脉动的均方根值差不多相等。
而对于工程应用,射流特性可用时均速度
(简化表示为速度u)的分布剖面具有自模化性质,中心速度
随距离的增加而减小,而且速度分布为高斯分布,在射流所有横截面上都是相似的。
因为射流内外压力几乎都与周围流体的压力相等,湍流剪应力不断地把新的静止流体卷进射流中,使射流宽度b不断加大。
由于压力为常数,所以对于所有位置(x),射流的动量是守恒的。
即:
上式右边为注流刚接触液面时的动量即初始动量。
由于I为常数,可见
与1/b成正比,也与1/x成正比。
沿射流轴线上速度分布为:
射流各截面的速度分布为:
式中kj为动量传递系数,λj为截面速度分布系数,λj=2kj2。
在湍流剪切力作用下,射流周围的液体被卷入,因此包内液-液射流是产生循环流动的主要原因。
B驻点流动
注流以液-液射流的方式冲击到中间包包底,转变成典型的驻点流动。
流体经过驻点以后,向四周铺展开来,转变为受固体包底限制的射流,速度方向基本与包底平行。
在驻点附近,随着压强的降低,径向速度最初有所增大;在驻点流动以外,已没有压强降推动的流体的流动,径向速度逐渐减小。
钢液沿包底的流动,在流动过程中,由于摩擦力及射流抽引周围钢液,速度逐渐减小。
在包底未设置坝时,则极有可能形成短路流,直接进入中间包的浇铸水口而流入结晶器。
C注流卷吸气体
注流卷吸空气,是二次氧化的主要原因。
从钢包水口流出的高速注流。
在周围形成一个负压区,把大量空气卷入熔池中。
D出口汇流旋涡
对于中间包冶金来讲,还有一个重要的流动现象,这就是在水口处钢液流出时产生的汇流旋涡。
由经验可知,液体由垂直出口向下流出时,当液面低于某一临界高度时,在出口上方会形成旋涡漏斗,这就是汇流旋涡。
E自然对流的影响
自然对流的驱动力是由流体的密度差引起的,而密度差则可能由温度差或浓度差所引起,温度差引起自然对流的情况较多见。
在更换盛钢桶时,盛钢桶内钢液和中间包内钢液温度不同,也就是有较热或较冷的钢液注入中间包熔池。
中间包钢液散热损失降低了温度,使熔池温度分布不均匀而且和注入的钢液间形成温度差;
⑵在流动的钢液中,夹杂物颗粒容易碰撞而凝并成大颗粒,液态夹杂物凝并后成为较大液滴,固态的Al2O3夹杂和钢液间的湿润角大于90º,碰撞后能够相互黏附在钢液静压力和高温的作用下,很快烧结成珊瑚状群落,尺寸直达100mm以上,甚至还要大得多。
所以颗粒的碰撞凝并是夹杂物去除的主要形成。
颗粒碰撞有以下四种形式
A斯托克斯碰撞:
颗粒上浮速度与其大小有关,大颗粒上浮速度大,上浮时可能追上较小颗粒与之碰撞成为更大的颗粒。
因而浮速度更大,更容易捕获其他颗粒,斯托克斯碰撞的频率函数:
颗粒直径大,上浮速度快,两颗粒直径差值大。
碰撞机会增加,都能促使βij增加,碰撞后形成更大颗粒就更容易上浮,在中间包内斯托克斯碰撞是夹杂物凝并去除的重要形成之一。
B布朗碰撞:
颗粒半径为ri和rj的两种夹杂物,单位体积中的数目分别为ni和nj,在单位时间、单位体积内碰撞次数nij为
式中β(ri×rj)称为颗粒i和j的碰撞频率函数,符号简写为βij,单位为m3/s。
颗粒极小的夹杂物(小于10mm),在钢液中作无规则的热运动(布朗运动)而产生的碰撞其碰撞频率函数
式中k为玻耳兹曼常数,由式可知颗粒直径大,βij值小,小颗粒碰撞机率大。
C速度梯度碰撞:
颗粒沿流线轨迹运动,高速流线上的颗粒,将追上低速流线上的颗粒,只要两颗粒的距离不超过他们的半径之和,颗粒将发生碰撞,这种碰撞和流场速度有关。
其碰撞频率函数
当流场速度不够大时,梯度碰撞不是主要的方式,但在某些速度场有急剧变化的部位梯度碰撞才能发生。
D湍流碰撞。
湍流中由于速度的脉动作用于颗粒,促使他们相互碰撞。
考察颗粒i周围为R=ri+rj的区域,R称为冲突半径,当颗粒j进入半径为R的球体表面,就可能由于脉动速度而与之碰撞,湍流碰撞频率函数:
式中C为常数,
是张立峰更新计算了萨福曼(saffman)关于湍流扩散研究数据而得出的。
f为导致稳定凝并的碰撞所占分率,取f=1,∈为流场的湍动能耗散率,v为钢流的运动黏度。
湍流碰撞是夹杂物颗粒凝并长大重要形式。
中间包流场中湍动能耗散率∈值大的区域,很容易发生湍流碰撞。
用数学模型计算中间包流场时,可求得∈值分布,利用该分布计算夹杂物碰撞长大速率。
设半径为ri,rj的两个颗粒碰撞后生成了半径r=ri+rj的颗粒,则ri减少的速率。
碰撞后所产生新颗粒的速率
两式的代数和所表示夹杂物颗粒的变化速率。
碰撞频率函数具加和性,在计算颗粒浓度变化时,不同形式的碰撞均可导致新颗粒生成,所以各种类型的βij,可以加在一起应用于计算公式中。
夹杂物在包衬壁面上的黏附
各种尺寸的夹杂物,和包衬上耐火材料接触时,将会黏附在包壁上而脱离钢液。
颗粒黏附到表面上检出的过程,从形式上可看作是一和优质过程,但具有以下两个特点:
第一,黏附在表面上的颗粒,受界面力的影响,不能返回钢液,可认为表面浓度以及逆反应速率均为零。
第二,颗粒只有依靠垂直壁面的脉动法向分速度的推动,才能运动到壁面,扩散对颗粒的传质不起作用。
在壁面附近的湍流中,脉动法向分速度
沿壁面法向逐渐衰减。
称为均方根脉动速度分量。
设壁面处法向坐标y=0由湍流理论可知。
也就是说,在壁面附近脉动法向分速度和y²成正比,脉动衰减很快。
μ
=u'v'=τ/ρ,μf称切应力速度或摩擦速度,表示脉动造成的附加切应力。
按照戴维斯(J.T.Davies)关于搅拌时悬浮颗粒和液体间的传质理论,能量耗散率和肪动速度间有以下关系:
ε=(μf)³/le
因此切应力速度:
μf=(ε×le)1/3
公式中,le为湍流淌的特征尺度,le=(v³/E)¼
恩格(T.A.Engh)和林斯科格(N.Lindskog)应用湍流理论研究颗粒向壁面检出,得出其结质系数βρ:
公式中r为夹杂物颗粒半径,所以黏附于壁面而去除夹杂的速率:
化学方法去除夹杂Al2O3夹架
Al2O3(熔点约2000℃),利用Al2O3与钙的反应生成低熔点的12CaO·7Al2O3(熔点约1400℃)上浮排出。
三、新型中间包括结构设计思路
最初的中间包,仅仅作为储存和分配钢液的容器,对中间包容量没有严格要求.为了节省投资,一般倾向采用小容量中间包。
随着对铸坯清洁度要求的提高,为了增加中间包去除夹杂物的效果,往往是加大溶池深度,增大中间包容量.由于原始设计存在问题,增大中间包容量(钢体)需改变中间罐车,中间罐等投资很大。
为节省投资,中间包容量大小还与换大包时间有关。
换罐时往往使中间包液面降低,夹杂进入结品器影响铸坯质量。
为保证铸坯质量应保持中间包液面高度为0.4-0.5m以上,防止出口汇流旋涡。
为解决进一步去除中间包夹杂的问题,必须对中间包的结构进行改进。
改进后的新型中间包核心特点是:
一是将中间包分为相对独立的两个或三个区域。
二是用一种新型导管将冲击区和浇注区连通。
中间包分为相对独立的两个或三个区域的理论基础与作用:
依据中间包钢液流动的特性合夹杂去除机理,我们重点研究如何利用钢液流动特性让湍流碰撞、布朗碰撞、速度梯度碰撞、斯托克斯碰撞增多,让夹杂有机会碰撞长大排除,基于上述理论我们采取的方法是用挡板(不开口)将中间包分为冲击区(大包钢液浇入中间包的区域)和浇注区(中间包钢液流出中间包区域)。
采取该方法解决了液面波动而引发的夹杂、引流砂、钢渣等进入浇注区,影响铸坯质量的问题。
新型导管将冲击区和浇注区连通的理论基础与作用:
新型导管利用虹吸现象,钢液由冲击区吸入到浇注区,由此可大幅度降低连浇换罐时由于液面波动造成的夹杂物大量进入浇注区现象。
以100吨钢包为例,每次开浇有15公斤左右引流沙,其主要成分Cr2O3和SiO2等,每个中间包连浇十包钢液,相当于向钢液中加150公斤的Cr2O3和SiO2夹杂。
在中间包包底安装“新型导管”,根据数值模拟计算和水模模拟得到的中间包内钢液流动的情况,确定新型导管安装位置,方向,使温度场、流场合理,钢液沿渣和钢的界面流动,易使夹杂去除。
在冲击区内,钢液浇注到中间包在这里充分混合,钢液成分温度都比较均匀,因注流冲击形成的钢液湍动也比较激烈(湍流碰撞增加)。
在冲击区相对平缓位置作为新型导管入口。
布朗碰撞速度梯度碰撞增加,为使夹杂有利上浮,我们将入口高于中间包底50-70毫米。
在浇注区内,由于导管的导引钢液流动不是直接流向水口,而是在浇注区内作倾向上的旋转运动,这样可以把钢液的夹杂物带向中间包熔池的表面去除。
从整体上来看,改进后的新型中间包有五大优点:
一是可消除中间包内的钢液的短路流动。
中间包内死区较少,充分利用了中间包的空间,钢液在中间包的停留时间比较充足,营造了一个夹杂物上浮排除的环境,强化了中间包的冶金功能,提高进入结晶器的钢液纯净度,改善铸坯质量。
二是可降低中间包水口长度,减少结流现象。
形成新型导管连接相对独立的冲击区和浇注区后,冲击区与浇注区落差增大,钢液在冲击区通过新型导管进入浇注区时流股向上,浇注安全得以保证,浇注区永久层的厚度降低。
三是可减少中间包剩余钢液。
浇注区的液面高度决定汇流旋涡现象的产生,由于冲击区与浇注区的落差,可使冲击区钢液面降低,钢液收得率提高,每个中间包钢液减少30-60%。
四是具有过滤功能,可减少结流,纯净钢液。
在新型导管上采取在导管内复合一层CaO,复合的钙与Al2O3反应生成低熔点12CaO·7Al2O3(1400℃),解决铝镇静钢易絮水口结流的问题。
根据钢种要求,在新型导管内壁可采用相应的复合材料或采用蜂窝、狭缝式导管,以提高过滤效果。
与现有中间包钢液流动方式的对比:
现有中间包钢液流动方式:
流—液-液射流区—驻点流动—汇流旋涡—水口出流注入流
新型中间包钢液流动方式:
流—液-液射流区—驻占流动—汇流旋涡—出口出流—液-液射流区—驻点流动—汇流旋流—出口出流
结论:
这种新型结构的中间包可以使连铸操作简便,提高连铸生产效率,增加钢液收得率,大幅度减少夹杂物。
该项目获得国家技术。
专利号:
200320105201.5