PCB各制程不良分析手册.docx
《PCB各制程不良分析手册.docx》由会员分享,可在线阅读,更多相关《PCB各制程不良分析手册.docx(35页珍藏版)》请在冰豆网上搜索。
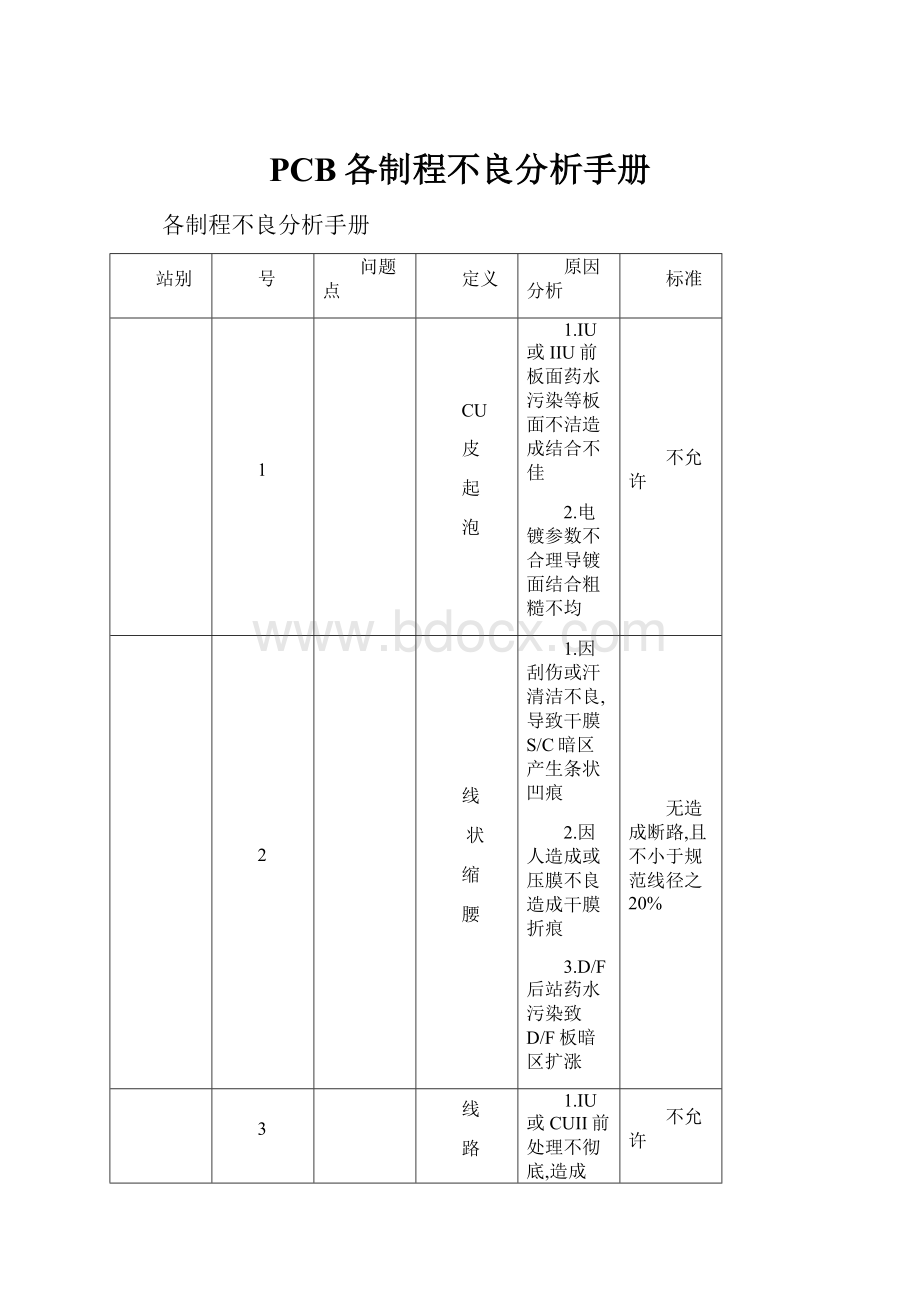
PCB各制程不良分析手册
各制程不良分析手册
站别
号
问题点
定义
原因分析
标准
1
CU
皮
起
泡
1.IU或IIU前板面药水污染等板面不洁造成结合不佳
2.电镀参数不合理导镀面结合粗糙不均
不允许
2
线
状
缩
腰
1.因刮伤或汗清洁不良,导致干膜S/C暗区产生条状凹痕
2.因人造成或压膜不良造成干膜折痕
3.D/F后站药水污染致D/F板暗区扩涨
无造成断路,且不小于规范线径之20%
3
线
路
分
层
1.IU或CUII前处理不彻底,造成CU层之间结合不牢
2.槽液温度过低等参数不当致CU层沉积粗糙,与前者之CU不能很好结合
3.D/F湿影不彻底,导致铜层结合不好
不允许
4
蚀
刻
不
尽
1.蚀刻参数未管控好
2.流锡或剥膜不尽
3.IU或IIU前干膜掉落(刮落或与板面结合不牢)
4.干膜前板面沾胶
线路间不超过规范线径之20%,且未造成短路
电
镀
5
线
路
分
层
1.IU或CUII前处理不彻底,造成CU面结合不牢
2.槽液温度过低等参数不当致CU层沉积粗糙,与前者之CU不能很好结合
3.D/F湿影不彻底,导致铜层结合不好
不允许
6
脏
点
短
路
1.干膜底片未清洁净,导致其明区沾污部分未被曝光固化,即此线距部分会被镀上CU及sn/pb而造成短路
不允许
7
CU
面
凹
陷
1.基材本身有针点凹陷不良(检查基板表面)
2.压合时CU皮表面沾尘或PP质量不良造成压合后此瑕玼
3.电镀铜时因槽液特别是光泽剂不正常导致CU积不良。
(2.3.可通过做切片观查,以作为参考)
A手指不允许,板面每点不大于20mil,不超过板厚的1/5
8
CU
面
残
缺
1.D/F沾膜,撕膜不净,导致蚀刻时被蚀掉
2.板面沾胶或沾药水导致CU面无锡层保护层
3.电镀部分喷嘴坏损造成局部过蚀
4.板面镀锡层被刮伤
大铜面每点不大于20mil,每面只允许1点,其它地方不允许
电
镀
9
短
路
1.干膜S/C未清洁净,致其明区沾污部分未被曝光固化,即此线距部分会被镀上CU及sn/pb而造成短路
2.外层干膜刮伤,导致镀上锡层而造成短路
不允许
加
工
10
孔
内
塞
SN
1.喷锡时风刀塞SN,浸锡时间不够等参作业参数不合理
2.孔内有毛刺其它杂物造成孔塞
3.L/Q塞墨孔内积墨或塞墨不良
喷锡板导通孔塞锡不高出板面可允收;零件孔塞锡不允收;A手指附近15mm内导通孔塞锡不允收
11
孔
边
锡
高
1.喷锡前孔边CU面不洁,造成CU/SN结合力小于SN/PB内聚力
2.前后风刀间距过大,,造成一面之锡被回吹
3.风刀距轨道间距过大,风量扫锡整平力不够
4.浸锡时间不足等参数不良
锡厚40U″-1000U″,且锡面上无毛尖状颗粒状突起
加
工
12
锡
面
凹
坑
1.喷锡前CU不洁或CU面不平整
2.锡铅不纯或空气内含有杂物
3.风刀不良
1.不影响焊锡性
和锡厚(40U″-1000U″)
13
板
面
树
脂
1.L/Q显影时绿油未彻底去除干净,致化A时药液沉积不上
不允许
14
A
面
花
斑
1.化A前CU面不洁
2.NI槽NI含量不足等参数不合理;NI槽污染
3.摇摆动作不到位
不允许
15
架
锡
桥
1.喷锡前板面有不洁
2.锡铅内或空气中含有杂质
3.风刀不良
不允许
16
板
面
沾
锡
1.喷锡前因防焊漏印或CU面防焊被刮掉,致露出CU面,在此HAL时露CU部分被喷上锡
线路上不允并列存在;大铜面每面不超过3个点,每点不大于10mil
加
工
17
A
手
指
针
孔
1.前站CU面有凹坑
2.镀A时电流密度过大,致NI/A沉积时粗糙不平整
3.镀A地槽液含量不当或受污染
每点不超过10mil,每排不超过3个点,
18
A
面
手
印
1.化A前CU面不洁
2.NI槽NI含量不足等参数不合理;NI槽污染
3.摇摆动作不到位
(此现象一般为手印所致)
不允许
19
锡
面
锡
高
1.喷锡前板面有不洁
2.锡铅内或空气中含有杂质
3.风刀不良(此板有造成锡面粗糙)
锡厚40U″-1000U″,锡面不允许有颗粒状或毛尖
20
锡
高
不
良
1.喷锡前板面有不洁
2.锡铅内或空气中含有杂质
3.风刀不良
锡厚40U″-1000U″,锡面不允许有颗粒状或毛尖
加
工
21
PAD锡
高
1.喷锡前板面有不洁
2.喷锡时风压小/风刀间距不对等制作参数不佳
锡厚40U″-1000U″,锡面不允许有颗粒状或毛尖
湿
膜
2
防
焊
露
CU
1.棕片不良
2.挡点偏移或过大
3.印刷后碰及板面未干之油墨
4.网版不洁致漏墨不良
每点≤10mil,每面不超过3点
23
防
焊
异
物
1.印刷前板面有脏物
2.板面沾干油墨
每点≤10mil,每面不超过3点,且无明显色差
24
刮
伤
露
铜
1.印刷防焊后因人为操作不当造成板面之防焊被刮掉而露
CU
每点≤10mil,每面不超过3点
湿
膜
25
织
纹
显
露
1.L/Q退洗时间长
2.基板质量问题
3.压合不良
基材上无明显白点白斑,经热冲击试验不会造成分层起泡
26
板
面
积
墨
1.该处电镀镀铜较厚,致印刷时下墨不良
2.刮刀不平整
3.网版高度等参数不合理
4.网版漏墨不均
不会造成色为准
27
防
焊
侧
蚀
1.油墨质量不行
2.显影槽液对CU漆界面处之油墨攻击过度
3.防焊重工次数过多
1.线路上不允许
2.PAD边缘不超过10mil
湿
膜
28
防
焊
侧
蚀
1.油墨质量不行
2.显影槽液对CU漆界面处之油墨攻击过度
3.防焊重工次数过多
1.线路上不允许
2.PAD边缘不超过10mil
29
孔
边
起
泡
1.有污染或前处理刷磨时水气未烤干
2.孔边积墨致油墨较厚,致不能均一固化
3.L/Q烘烤条件不当,热固化不均
每点不超过3点,每点不超过10mil,3M撕胶防焊不脱落
30
板
面
漏
印
1.印刷时因网版未清洁尽或网版脏点或干油墨致印一下
2.刮刀不平整
3.电镀镀铜不均
4.设PIN不平致不能规范作业
每点不超过3点,每点不超过10mil
31
板
面
脏
污
1.印防焊后因人为操作不当使防焊表面沾上油脂或其它物质
不破坏防焊且不影响客户防焊颜色之要求
湿
膜
32
对
偏
阴
影
1.因棕片对偏致使沾在CU面上之防焊被曝光而不能被显影掉(PAD阴影)
2.因印刷后静置时间过长或烘烤时间过长或烤箱未保养好造成(主要为孔边阴影)
PAD阴影部分不超过本身宽度1/8,SMT允许1mil,光学点允许2mil
33
孔
边
露
CU
1.网版挡点偏移或过大或作业过程中有变形不良
≤2mil
34
防
焊
阴
影
1.因棕片对偏致使沾在CU面上之防焊被曝光而不能被显影掉(PAD阴影)
2.因印刷后静置时间过长或烘烤时间过长或烤箱未保养好造成(主要为孔边阴影)
PAD阴影部分不超过本身宽度1/8,SMT允许1mil,光学点允许2mil
35
孔
边
起
泡
1.有污染或前处理刷磨时水气未烤干
2.孔边积墨致油墨较厚,致不能均一固化
3.L/Q烘烤条件不当,热固化不均
每点不超过3点,每点不超过10mil,3M撕胶防焊不脱落
湿
膜
36
孔
边
起
泡
1.一般为印板过程中有滴到防白水等外物造成防焊色差
每点不超过3点,每点不超过10mil,3M撕胶防焊不脱落
37
防
焊
起
泡
1.有污染或前处理刷磨时水气未烤干
2.孔边积墨致油墨较厚,致不能均一固化
3.L/Q烘烤条件不当,热固化不均
每点不超过3点,每点不超过10mil,3M撕胶防焊不脱落
38
板
面
脏
污
1.一般为印板过程中有滴到防白水等外物造成防焊色差
不允收
39
孔
内
积
墨
1.印刷时刮刀压力过大,致下墨过大,挤入孔内
2.如孔过小在作业中也易产生此不良
3.以上为空网印刷时产生
零件孔不允收;导通孔每面不超过3个孔;卡板A手指15mm内不允许;其它无明确定义
文
字
40
沾
文
字
漆
1.网版未调正导致印偏沾漆
2.A/W文字划线条太靠近CUPAD
3.网片破损
不允许
41
文
字
印
偏
1.网版未调正
2.PIN针套错或没套好
3.定位PIN孔钻偏
PAD部分不超过本身宽度1/8,SMT允许1mil
42
文
字
漏
印
1.制作中覆墨不良
2.刮刀未研磨好不锋利
3.印刷时用力不够
不允许
43
文
字
印
反
印刷时人为误操作导致套PIN套反
不允许
文
字
44
文
字
印
反
印刷时人为误操作导致套PIN套反
不允许
45
文
字
漏
印
1.制作中覆墨不良
2.刮刀未研磨好不锋利
3.印刷时用力不
不允许
46
沾
文
字
漆
1.机台上有油墨沾在板面
2.印刷手手上沾有油墨并反沾于板面
3.网版有破洞造成感光膜脱落
不允许
47
文
字
积
墨
1.油墨粘度过小,下墨不均
2.覆墨时间太长
3.印刷架网高度过低
以清晰可认为准
文
字
48
文
字
沾
漆
1.网版未调正导致印偏沾漆
2.A/W文字划线条太靠近CUPAD
3.网片破损
不允许
49
文
字
漏
印
1.网版显影不尽或油墨太干致下墨不良
2.覆墨不良或印板时用力不均
3.刮刀不锋利
不允许
50
文
字
阴
影
1.多次印刷或吸纸不当
2.网版未抬起覆墨或网版反面有残墨
3.板弯板翘
PAD部分不超过本身宽度1/8,SMT允许1mil
51
文
字
印
倒
1.套PIN套错误
不允许
52
53
文
字
52
文
字
脱
落
1.油墨质量差,结合力不强
2.烘烤时间或温度不当,致文字固化不够
3.板面油烟等不洁物造成文字与板面结合力不强
不允许
53
文
字
重
影
1.印刷时有多次重印
2.网版未调正或上PIN不牢
3.重印时上PIN偏移未与网版对正
不允许
54
文
字
印
偏
1.网版未调正
2.PIN未套正
3.PIN孔偏移
PAD部分不超过本身宽度1/8,SMT允许1mil
55
沾
文
字
漆
1.机台上沾有油漆或手上沾漆
2.脏点沾漆或刮伤沾漆
3.网板破损
不允许
干
膜
56
条
状
短
路
1.棕片上沾有条状杂物或贴膜前板面沾条状油污
(此现象多为底片保护膜破损)
2.贴膜或曝光后因人为操作不当将铜面干膜刮
不允许
57
干
膜
脱
落
1.贴膜前板面沾油污/沾胶或其它杂物
2.贴膜时压力/温度过小等不当致干膜与铜面结合不牢
3.贴膜或曝光后因人为操作不当将铜面干膜刮
4.干膜自身附着力不好
不允许
58
条
状
短
路
1.棕片上沾有条状杂物或贴膜前板面沾条状油污
2.贴膜或曝光后因人为操作不当将铜面干膜刮伤
不允许
59
点
状
短
路
1.棕片上沾有点状杂物或贴膜前板面沾点状油污
2.贴膜或曝光后因人为操作不当将铜面干膜刮伤
不允许
干
膜
站
60
干
膜
膜
破
1.干膜韧性不足,较脆
2.CU板板面杂物或巴厘过高
3.贴膜后静置时间过长,曝光能量太低
4.显影、水洗喷压过大或显影速度过慢
不允许
61
板
面
沾
污
1.板面沾胶/沾油垢等不良物
不允许
62
干
膜
脱
落
1.干膜挈性不足,较脆
2.CU板板面杂物或巴厘过高
3.贴膜后静置时间过长或显影速度过慢
不允许
63
干
膜
沾
膜
1.棕片之暗区被刮伤
2.显影不尽或显影时残膜反沾
大铜每面不超过2个点,每点小于10mil,其它部位不允收
干
膜
站
64
线
路
突
出
1.贴膜后沾有脏点或底片上沾有脏点
2.操作刮伤干膜
不超过原稿线径的20%
65
干
膜
断
路
1.底片之暗区被刮伤
2.显影不尽或显影时残膜反沾
不允许
66
干
膜
短
路
1.棕片上沾有点状杂物或贴膜前板面沾点状油污
2.贴膜或曝光后因人为操作不当将铜面干膜刮伤
不允许
67
干
膜
对
偏
1.干膜站对底片时未保证孔环之ring各方向宽度相等(前提为孔正),
2.板子或底片有涨缩
零件孔余环≥2mil,导通孔孔偏不超过孔环的1/4,且与线路相连处不小于2mil
干
膜
站
68
撕
膜
不
尽
1.割膜不良致撕膜时未能整块撕起
2.撕膜时起膜位置不对
成型线以内不允许
69
NPTH孔
膜
破
1.钻孔后巴厘处理不彻底,即巴厘高
2.干膜封孔能力不够
3.跨孔过大
4.干膜静置时间过长或显影时冲压过大
不允收
70
干
膜
脱
落
1.贴膜前板面沾油污/沾胶或其它杂物
2.贴膜时压力/温度过小等不当致干膜与铜面结合不牢
3.贴膜或曝光后因人为操作不当将铜面干膜刮
4.干膜附着力不好
不允许
71
板
面
油
污
1.贴膜以前,因设备漏油或人为操作不当,致使油污直接或间接沾污板面
不允许
成
型
站
72
模
具
冲
偏
1.板弯板曲或吹气过大或人为操作不当致板子未套好PIN孔时模冲造成
不允许
73
槽
孔
捞
偏
1.定位PIN栽斜
2.程式有错误
超客户公差不允许
74
模
冲
伤
孔
1.套PIN套偏
2.模具弹力胶不平衡
3.板材涨缩或PIN针偏大
不允许
75
斜
边
金
丝
1.铣刀不利或下刀点过于靠刀边
2.因设备或人为调试不当致铣刀抖动较大
3.斜板行进时用力不平衡
不允许
成
型
站
76
V-CUT过
穿
1.调刀过深或铣刀不水平
2.过板时叠板所致
3.板弯板曲或V-CUT刀具运转不稳
不允许
77
V-CUT
过
反
1.未按进料方向放板过V-CUT
2.程式错误
不允许
78
V-CUT
伤
铜
1.V-CUT两边挡板不平行
2.板子外型有偏差
3.V-CUT间距过小
4.V-CUT刀角度偏大或刀片磨损过重
不允收
79
V-CUT
过
穿
1.调刀过深或铣刀不水平
2.过板时叠板所致
3.板弯板曲或V-CUT刀具运转不稳
不允许
成
型
站
80
V-CUT
冲
反
1.未按磨具进料方向入板
2.S/C面设计相似,识别有误
3.模具未设防呆PIN
不允收
81
V-CUT
毛
屑
1.V-CUT在要求范围内调试
2.客户外形公差小,且槽口偏小
3.刀片角度过大或刀口不锋利
按客户要求有不同
82
V-CUT
伤铜
1.V-CUT两边挡板不平行
2.板子外型有偏差
3.V-CUT间距过小
4.V-CUT刀角度偏大或刀片磨损过重
不允收
83
模
具
冲
偏
1.板弯板曲或吹气过大或人为操作不当致板子未套好PIN孔时模冲造成
不允许
成
型
站
84
斜
边
不
齐
1.板弯板曲/斜边台面不平
2.斜边行进时用力平均
3.斜边不锋利/铣刀运转时稳定性不佳
不允收
85
断
导
线
1.铣刀不锋利或下刀点太靠刀边
不允收
86
织
纹
显
露
1.PP之玻璃布间距过大/TG点不稳定等PP品质不良
2.压合时参数不当致流胶过大
3.L/Q重工时退洗时间过长,导致药水对树脂攻击严重,显露出玻织布
基材上无明显白点白斑,经热冲击试验不会造成分层起泡
87
靶
孔
偏
1.D/F对S/C时对偏
2.钻靶时钻偏
无线路土3mil,有线路土2.5mil
钻
孔
站
88
钻
孔
孔
偏
1.钻孔资料有误
2.钻机精度不够(超出土3mil)或机台有故障
3.叠板数超规范或钻头质太差
土3mil
89
多
钻
孔
1.程式有误
不允收
90
孔
烧
焦
1.钻孔速度过快
2.钻头排屑不良或钻针设定过深
3.断半针作业或spindle掉刀
不允许
91
光
学
点
残
1.干膜沾膜
2.电镀过蚀
3.人为刮伤
不允收
品
检
站
91
A手
指
氧
化
1.镀A时A槽药水浓度不当或有槽液污染,或水洗不尽
2.转运和生产作业时手接触污染
3.
不以收
92
锡
面
凹
坑
1.喷锡前CU不洁或CU面不平整
2.锡铅不纯或空气内含有杂物
3.风刀不良
1.不影响焊性及锡厚为为准
93
线
路
断
路
1.D/F棕片刮伤,即暗区部分线路被固化,蚀刻时被蚀掉
2.操作中锡铅被刮全伤,CU线路无保护层
3.镀锡铅前CU线路处有油污或沾胶
不允许
94
线
路
断
路
1.D/F棕片刮伤,即暗区部分线路被固化,蚀刻时被蚀掉
2.操作中锡铅被刮全伤,CU线路无保护层
3.镀锡铅前CU线路处有油污或沾胶
不允许
品
检
站
95
A面
发
白
1.化A前处理微蚀过度
2.因化NI后水洗不洁或A槽槽液非正常导致A厚不足
无明色差且A厚在管控范围
96
A手
指
刮
伤
1.因人为操作不当造成镀A前或镀A后A手指上之刮痕
不造成露NI,不超过3根,无明显刮痕
97
刮
伤
露
铜
1.防焊印刷后,人为操作不当将板面之防焊刮掉
每点不超过3点,每点不超过10mil
98
条
状
针
点
1.此为较有规律的直条状,应与机器设备之规律性运转有关
2.D/F磨刷时板面被沾有油脂或点状胶类物
3.D/F显影影时有去膜不尽或有不浴物附于板面
每PCS不超过3点,每点不超过10mil,厚度不超过1/5板厚
品
检
站
99
CU
面
凹
陷
1.基材本身有针点凹陷不良(检查基板表面)
2.压合时CU皮表面沾尘或PP质量不良造成压合后此瑕玼
3.电镀铜时因槽液特别是光泽剂不正常导致CU积不良
(2.3.可通过做切片观查,以作为参考)
A手指不允许,每面少于3点,每点不大于20mil,不超过板厚的1/5
100
板
面
沾
锡
1.喷锡前因防焊漏印或CU面防焊被刮掉,致露出CU面,在HAL时露CU部分被喷上锡
线路上不允并列存在;大铜面每面不超过3个点,每点不大于10mil
101
CU
面
花
班
1.此为防焊之后之花班
2.防焊之前CU有沾胶或油脂等物污染
3.因防焊本身品质不良造成显影溶解时局部不尽
4.因退洗不尽重工或显影时未冲洗净致有药水水痕
不允许
102
SN手指
刮
伤
1.此锡手指刮伤处有喷上锡,另此为明显人为造成
2.为喷锡前因人为操作不当导致锡手指被刮掉部分
不允收
品
检
站
103
电
镀
针
点
1.此仅指电镀本站造成之此不良
2.镀铜时槽液有机污染或金属污染致CU2+沉积不均
3.光泽剂中之carrier不足或过量
4.电镀前处理CU面未处理净
A手指不允许;大铜面每面少于3点,每点不大于20mil,不超过板厚的1/5
104
线
细
1.干膜曝光时赶气不到位或吸真空不足或曝光能量不足不均导致S/C线复制线在干膜板时比原稿小且小于标准
2.显影过度或走蚀刻时因速度过慢或槽液管控不当导蚀刻出之线路小于原稿之20%
不于原稿之20%
105
板
面
沾
锡
1.喷锡前因防焊漏印或CU面防焊被刮掉,致露出CU面,在HAL时露CU部分被喷上锡
线路上不允并列存在;大铜面每面不超过3个点,每点不大于10mil
106
板
损
1.在生产过程中或板料转运中因人员操作不当导致板子有碰到机器或地面,造成板子局部破损
不允收
品
检
站
107
板
面
CU
瘤
1.D/P活化/去脂平整或微蚀槽液受有机或金属污染
2.电镀铜槽添加剂不当或阳极有破损导致金属污染
不允收
108
电
镀
铜
残
1.因撕膜不尽或板面油脂/沾胶等造成D/F后该处未镀上CU与锡铅保护层,蚀刻时被蚀掉
2.镀锡铅后因锡铅氧化或锡铅刮伤致蚀刻时被掉
大铜面每点不大于20mil,每面只允许1点,其它地方不允许
109
线
路
断
路
1.D/F棕片刮伤,即暗区部分线路被固化,蚀刻时被蚀掉
2.操作中锡铅被刮全伤,CU线路无保护层
3.镀锡铅前CU线路处有油污或沾胶时每刻
不允许
110
防
焊
刮
伤
1.印刷防焊后因人为操作不当造成板面之防焊被刮伤
不允收
品
检
站
111
A手
指
刮
伤
1.因人为操作不当造成镀A前或镀A后A手指上之刮痕
不造成露NI,不超过3根,无明显刮痕
112
A
面
花
斑
1.化A前CU面不洁
2.NI槽NI含量不足等参数不合理;NI槽污染
3.摇摆动作不到位
不允收
113
板
面
上
金
1.因前站防焊脱落,导致后续走化A时化上A/NI
2.走A线前处理磨刷过重致防焊有被刷掉
不允收
114
A
氧
化
1.化A时A槽药水浓度不当或有槽液污染,或水洗不尽
2.转运和生产作业时手接触污染
不允收