纵向伺服进给系统的设计.docx
《纵向伺服进给系统的设计.docx》由会员分享,可在线阅读,更多相关《纵向伺服进给系统的设计.docx(19页珍藏版)》请在冰豆网上搜索。
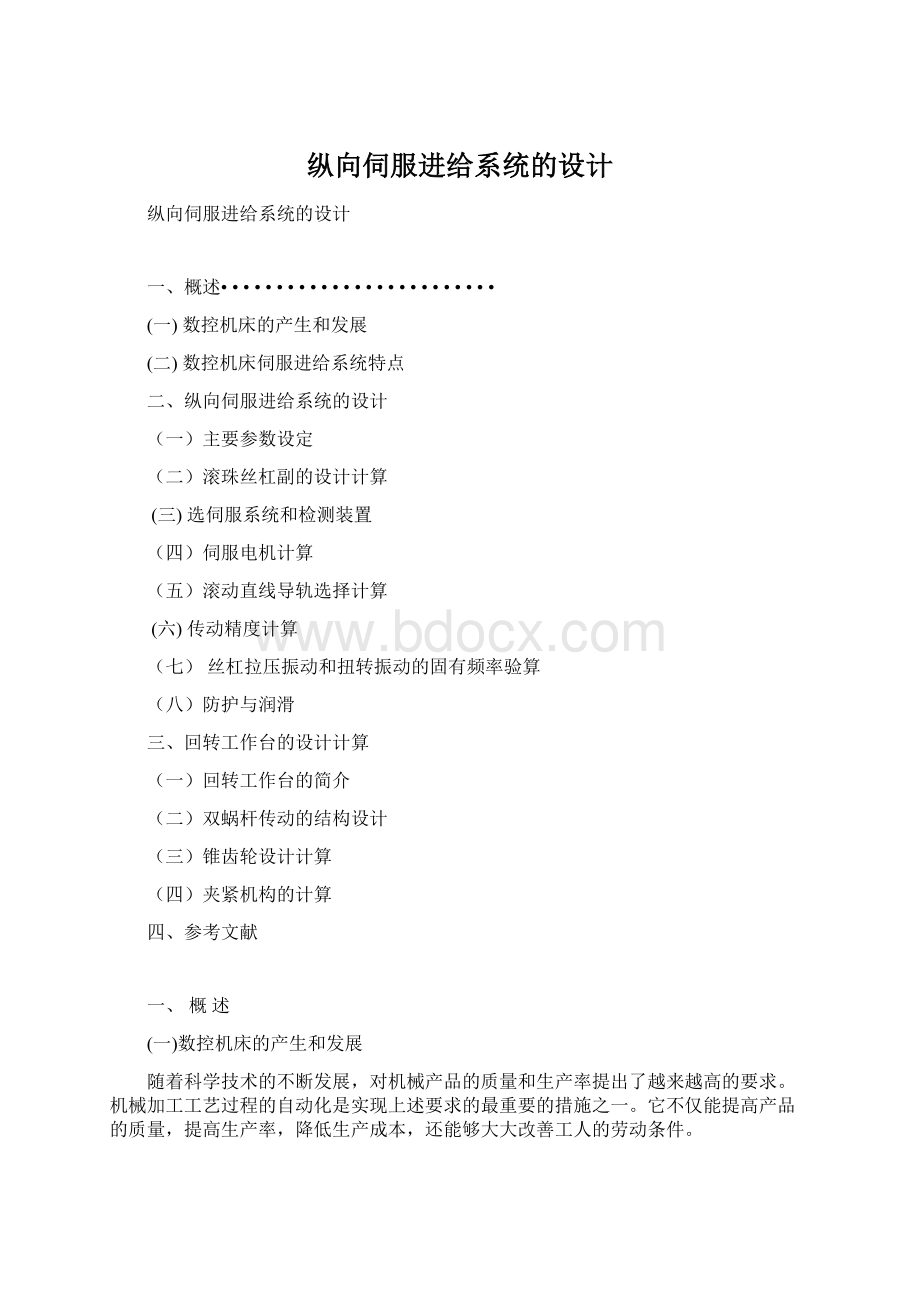
纵向伺服进给系统的设计
纵向伺服进给系统的设计
一、概述•••••••••••••••••••••••••
(一)数控机床的产生和发展
(二)数控机床伺服进给系统特点
二、纵向伺服进给系统的设计
(一)主要参数设定
(二)滚珠丝杠副的设计计算
(三)选伺服系统和检测装置
(四)伺服电机计算
(五)滚动直线导轨选择计算
(六)传动精度计算
(七)丝杠拉压振动和扭转振动的固有频率验算
(八)防护与润滑
三、回转工作台的设计计算
(一)回转工作台的简介
(二)双蜗杆传动的结构设计
(三)锥齿轮设计计算
(四)夹紧机构的计算
四、参考文献
一、概述
(一)数控机床的产生和发展
随着科学技术的不断发展,对机械产品的质量和生产率提出了越来越高的要求。
机械加工工艺过程的自动化是实现上述要求的最重要的措施之一。
它不仅能提高产品的质量,提高生产率,降低生产成本,还能够大大改善工人的劳动条件。
在机械制造业中,尤其是在宇航、造船、以及国防工业中,单件小批量生产的零件灼占机械加工总产量的80%以上,其特点是:
加工批量小、改型频繁、零件精密度高而且形状复杂。
采用专用机床和生产线来加工这类零件就显得不合理,因此,制造业产生了对于通用、高精度、具有“柔性”的自动化机床的迫切需求,要求机床设备不仅要精度高而且要生产率高、自动化程度高、工人操作简单、劳动强度低。
在此背景下,于1952年在美国诞生了世界上第一台数控机床样机,用于直升飞机叶片加工。
其控制器全部采用电子管。
它的诞生标志着世界制造业进入数控时代。
从此,数控机床的发展引起世界范围的重视,并极大地促讲了制造业的发展。
在近十年中,特别是随着计算机技术的飞速发展,数控技术的发展也日新月异。
数控技术是综合应用了电于计算机、自动控制、伺服驱动和精密测量等多学科的技术成果的一门综合性技术,因此它的发达程度在某种程度上体现了一个国家的综合工业实力。
1958年我国开始研制数控机床。
近年来,由于引进了国外的数控系统与伺服系统的制造技术,使我国数控机床在品种、数量和质量方面得到了迅速发展。
虽然我国与先进的工业国家之间还存在着较大差距,但这种差距正随着工厂、企业技术改造的深入开展不断缩小,发展数控机床的生产已成为目前机床行业的目标。
数控机床必将成为我国机械工业生产中的主要设备,为我国的四个现代化做出巨大的贡献。
(二)数控机床进给伺服系统特点
从第一台数控机床产生到现在的40年间,数控技术发展非常迅速,并在机械行业中得到曰益广泛的应用,它具有以下特点:
(1)能适应不同零件的加工;
(2)生产效率和加工精度高,加工盾量稳定;
(3)能完成复杂型面的加工;
(4)工序集中,一机多用,有着良好的经济效益;
(5)减轻了操作者的疲劳强度,有利于生产管理的现代化。
数控机床的进给伺服系统由伺服电路、伺服驱动装置、机械传动机构及执行部件组成,它的作用是:
接受数控系统发出的迸给速度和位移指令信号,由伺服电路做一定的转换和放大后,经伺服驱动装置(直流/交流伺服电机、电液脉冲马达、功率步进电机、电液伺服阀.液压马达等)和机械传动机构,驱动机床的工作台、主轴等执行部件实现工作进给和快速运动。
数控机床的进给伺服系统与一般机床的控制系统有本质的区别,它能根据指令信号精确地控制执行部件的运动速度与位置,以及几个执行部件按一定的规律运动所合成的运动轨迹。
发展高性能的数控进给伺服系统,在很大程度上可以决定机床的加工精度、表面质量和生产效率。
数控进给伺服系统的性能取决于伺服驱动系统与机械传动结构中各环节的特性,也取决于系统中各环节参数的合理分配。
以伺服驱动装置和控制调节器为中心的伺服驱动系统已有较成熟的理论分析、实验研究和设计方法。
机械传动结构以及整个进给系统的研究,近几年也逐渐受到重视,并做了不少工作。
数控进给伺服系统是一个位置控制系统,按其控制方式,可分为开环、闭环和半闭环三类。
开环较,但如果负荷突然加大,或者脉冲频率变化较大,则执行机构的运动可能发生误差,这就是常说的“失步”现象。
在数控机床发展的初期(50年代至80年代),开环曾被广泛应用,后因“失步”现象未能解决而逐步让位于闭环和半闭环,近年来步进电机技术有了很大的发展,今后开环系统仍有可能占有一席之地。
闭环系统有反馈,可检查执行的情况,所以精度很高。
半闭环系统的反馈信号来源于伺服电机轴和滚动丝杠,不能纠正丝杠的导程误差和丝杠轴承的轴向跳动以及受力丝杠轴承的变形,因而精度比闭环要低一些但是半闭环系统的执行机构和机械传动机构构成一个振荡环节,一般不易引起振荡。
因此,设计闭环系统和半闭环系统的出发点不同,设计半闭环系统主要考虑保证系统的定位精度,而设计闭环系统一般应以计算稳定性为主,在保证有足够稳定性的条件下决定系统的参数。
为确保数控机床进给系统的传动进度和工作平稳性,对设计机械传动装置提出如下要求:
1)高传动精度和定位精度;2)宽的进给调速范围;3)响应速度要快;4)无间隙传动;5)稳定性好、寿命长;6)校正维护方便。
二、 纵向伺服进给系统的设计
(一)主要参数设定
纵向工作台面尺寸(长×宽×高):
900×500×50
回转工作台面尺寸(直径×高)ф320×220
则得:
工作内台重量:
G1=ρ·V·g=7.85×103×900×500×50×9.81×10-9=1733N
回转工作台重量:
G2=ρ·V·g=7.85×103×π×1602×220×9.81×10-9=1363N
工作台承重初估为:
G3=2500N
根据以上估算得总的重量为:
G=G1+G2+G3=1733+1363+2500=5600N
设定工作进给速度为1-1500mm/min,快速进给速度15m/min,工作台综向工作行程为750mm,横向工作行程为500mm,铣削最大直径为ф100mm。
根据最大切削条件为:
端铣刀直径为100mm,Z=10齿,S齿=0.13毫米/齿,B=80mm,t=3.5mm,
加工σb=80公斤/毫米的高碳钢。
查《铣工工艺学》中级本P18表1—1得:
p=4230牛/毫米2。
则得F切==4230=4900N
查《铣工工艺学》中级本P19表1-2得:
纵向切削力FX=F纵=0.35F切 =0.35×4900=1715N
横向切削力 FY=F横=0.9F切=0.9×4900=4410N
垂直切削力 FZ=F垂=0.5F切=0.525×4900=2573N
选择宽调速直流电机驱动,半闭环控制。
根据《机床设计手册》选用FANUC-BESK宽调速直流电机驱动,型号为FB-15,它属于永磁型多极电机,其特点是:
定子磁极是高性能铁氧体,能承受高的峰值电流,加速性能好;转子惯量大,热容量大,过载能力强;低速高转矩,可与进给机构直接相联接;调速范围可达1~10000,在0.1r/min低速下仍能平滑运转;电刷换向性能好,可靠性高;绝缘性好(185℃),寿命长;可配装各种反馈元件。
(二)滚珠丝杠副的设计计算
(1)滚珠丝杠的导程的确定
在本设计中,电机和丝杠直接相连,传动比i=1,选择电机FB-15的最高工作转速nm=1500r/min,则丝杠的导程
Ph=Vmax/nm=15000/1500=10mm
导轨采用滚动直线导轨。
(2)确定丝杠的工作负载
工作负载是指机床工作时,实际作用在滚珠丝杠上的轴向压力,它的数值可用进给牵引力的试验公式计算。
选定导轨为滚动导轨,而一般情况下,滚动导轨的摩擦系数为0.0025--0.005,取摩擦系数f为0.005,则丝杠所受的最大牵引力:
Fmax=KFX+f(FY+FZ+G)
其中K为颠覆力矩影响系数,K一般取为1.1--1.15,现取K为1.12。
则得最大工作负载:
Fmax=1.12×1715+0.005(4410+2573+5600)=1984N
而丝杠的最小工作负载荷为摩擦力:
Fmin=fG=0.005×5600=28N
故其平均负载可按下式计算:
Fm=(2Fmax+Fmin)/3=(2×1984+28)/3=1332N
(3)确定丝杠的平均转速
最大进给时,丝杠的转速为:
nmax=Vmax/Ph=15000/10=1500r/min
最慢进给时,丝杠的转速为:
nmin=Vmin/Ph=1/10=0.1r/min
则得到丝杠的平均转速为:
nm=(2nmax+nmin)/3=(2×1500+0.1)=1000r/min
(4)确定丝杠所受的最大动载荷
查数控机床P121表6-13,取丝杠的工作寿命为15000h同时取精度系数fa=1,负荷性质系数Fw=1.5,,温度系数ft=0.95,硬度系数fh=1,可靠性系数fk=0.53
(可靠性为96%)。
而丝杠的旋转圈数L=60nmh=60×1000×15000=900(106r)
从而算得最大的动载荷Cm为:
CM=
查《数控机床》表6-14选用插管埋入式双螺母垫片预紧滚珠丝杠副,型号为CMD5010-3,丝杠公称直径为φ50mm,基本导程Ph=10mm,其额定动载荷Ca=38547N(Ca>Cm),额定静载荷COA=112798N,圈数×列数=1.5×2,丝杠螺母副的接触刚度Kc为1692N/um,螺旋升角λ=3o38",丝杠底径43.5mm,螺母长度为170mm,取丝杠的精度为1级。
(5)滚珠丝杠副轴向间隙的调整和施加预紧力的方法
采用双螺母预紧的方法,可把弹性变形量控制在最小限度内,双螺母经加预紧力调整后基本上能消除轴向间隙。
常用的双螺母消除轴向间隙的结构型式有三种:
垫片式预紧、螺纹式预紧和齿差式预紧。
考虑到双螺母垫片式结构简单,可靠性好,刚度高、装卸方便,故在本设计中采用双螺母垫片式预紧,预加载荷为Ca/4=38.5/4=9.63KN,而最大载荷的1/3为1984/3=661N,可见预加载荷远大于最大载荷的1/3,故满足要求。
(6)丝杠的长度
确定丝杠螺纹部分的长度LU,LU等于工作台的最大行程(750mm)加上螺母长度(170mm)加两端余程(40mm)。
LU=750+170+80=1000mm
确定丝杠的支承跨距,支承跨距应略大于LU取为:
L1=12OOmm
丝杠全长:
L=1300mm
(7)临界压缩负荷
临界压缩负荷:
Fcr=≥Fmax
其中E为材料的弹性模量E=2.1×1011N/m2
I为丝杠最小截面惯性矩I=
L0为最大受压长度,按照结构设计取L0=1140mm.
K1为安全系数,一般取K1=1/3
Fmax一为最大轴向工作载荷Fmax=1984N
f1为丝杠支承方式系数,查《数控机床》P119表6-12得f1=4,则:
Fcr=N>Fmax=1984N
可见Fcr远大于Fmax,满足要求。
(8)临界转速验算
长丝杠在高速下工作时,为防止弯曲共振,应验算其临界转速
ncr=
其中A为丝杠最小横截面
A=
LC为临界转速计算长度:
LC=+750+40+
K2为安全系数,一般取0.8
ρ为材料的密度,ρ=7.85×103Kg/m3
f2为丝杠支承方式系数,查《数控机床》表6-12得f2=3.927,
则:
ncr=>nmax=1500r/min
可见ncr远大于nmax,满足要求。
(9)确定滚珠丝杠的支承结构形式及支承轴承
滚珠丝杠的支承方式有以下几种:
A)单支承方式:
这种安装方式只适用于短丝杠,它的承载能力小,轴向刚度低。
一般用于数控机床的调节环节或升降台式数控铣床