生产车间内IE现场管理方法应用的观察与思考.docx
《生产车间内IE现场管理方法应用的观察与思考.docx》由会员分享,可在线阅读,更多相关《生产车间内IE现场管理方法应用的观察与思考.docx(10页珍藏版)》请在冰豆网上搜索。
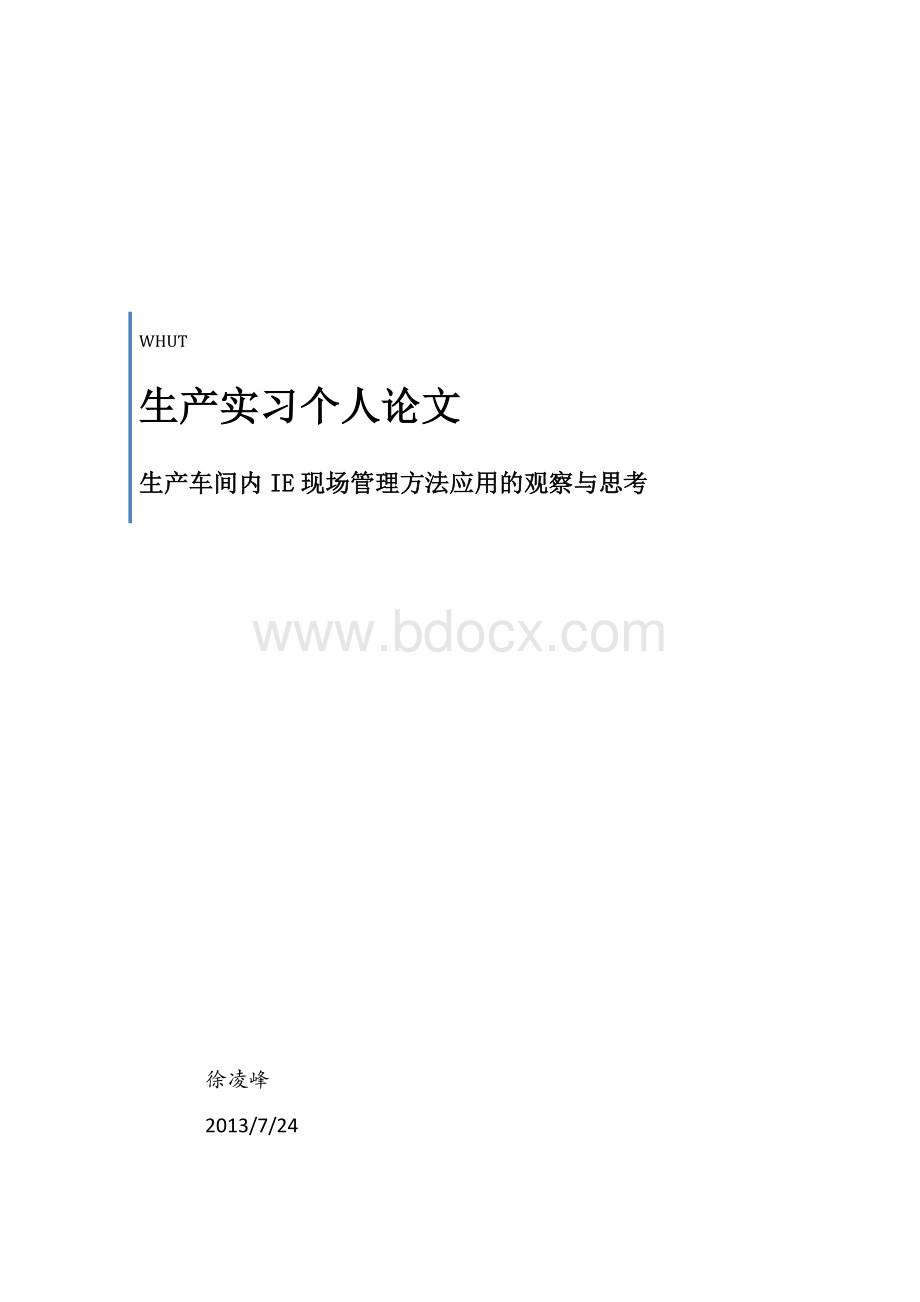
徐凌峰
2013/7/24
WHUT
生产实习个人论文
生产车间内IE现场管理方法应用的观察与思考
目录
1现场管理概述 2
2现场管理的内容与方法 3
2.1现场管理的内容 3
2.2现场管理的方法 3
3洛阳各企业生产车间现场管理方法的应用 5
3.1现场管理概况 5
3.2现场管理方法的应用 6
4结语 8
5致谢 8
参考文献 9
生产车间内IE现场管理方法应用的
观察与思考
按照美国工业工程师学会(AIIE)的定义,工业工程(IndustrialEngineering)是指对有关人员、物资、设备、能源和信息等组成的整体系统进行设计、改进和实施的学科。
它应用数学、物理和社会科学的专门知识与技能,并且使用工程分析的原理和方法,对上述系统可能取得的成果予以阐述、预测和评价。
虽然不同的组织对工业工程的定义和表述有一些差别,但是内容基本相同。
在工业工程的研究和应用中,包括了许多技术,比如:
工作设计(工作研究+人机工程),设施规划与物流系统设计,工程经济分析,生产计划与控制,质量管理与质量保证,成本控制,现场管理方法等。
现场管理方法基本上是使用最普遍的技术之一。
1现场管理概述
“现场”是为顾客制造产品或提供服务的地方,是整个制造业的中心,是可以不断改善的园地。
[1]现场是一个动态系统,它包括人、机、物、环境、信息、资金、能源等各个生产要素和Q(Quality)、C(Cost)、D(Delivery)、P(Production)、S(Safety)、M(Morale)即质量、成本、交货期、效率、安全、士气六个重要的管理目标要素。
现场管理是指运用科学的管理手段,对现场中的生产要素和管理目标要素进行设计和综合治理,达到全方位的配置优化,创造一个整洁有序、环境优美的场所,使现场中最具活力的人心情舒畅,操作得心应手,达到提高生产效率,提高产品质量,降低成本,增加经济效益的目的。
[1]
通过实习期间对一些企业的生产车间的观察,可以看出国内的制造业企业的现场管理水平和素养参差不齐,整体水平都不是很高。
这也是国内大多数企业在管理工作中存在的严重误区,即重市场,轻现场。
企业管理者要规避这个误区,首先需要改变的就是对现场的认识,市场与现场在企业运营中的关系是相互关联、相互制约并且密不可分的,企业的客户在选择合作前需要到企业的现场了解现场条件和管理水平是否能够保证其所要求达到的产品服务质量,是否具备足够的合作履约能力,因此,现场对于企业销售来讲,绝不是“远水解不了近渴”,提升企业的核心竞争力,既要抓市场,也要抓现场。
2现场管理的内容与方法
2.1现场管理的内容
现场管理的内容就是通过运用有效资源,使用各种方法和工具,实现Q、C、D、P、S、M六大管理目标。
这就需要不断改善、改进现场中存在的问题,消除一切不利因素,消除各种浪费,使整个现场处于“受控”状态。
传统的现场管理内容主要是消除浪费、落实现场管理职责、领导效应、治理现场等。
而信息作为一种特殊生要素,随着制造业高度信息化的发展,现场的信息管理的重要程度也不言而喻。
具体来讲,对于制造业,现场管理的任务包括:
消除生产现场的各种浪费现象;加强定员定额管理、降低物料和能源消耗、减少生产储备和资金占用;科学地组织生产,采用新工艺、新技术,开展技术革新活动,不断的完善各项专业管理保证体系;落实现场管理职责,严格按标准组织现场生产,严格按工艺规范进行生产,组织均衡生产;治理现场,改变生产现场“脏、乱、差”的状况。
2.2现场管理的方法
现场管理有九个基本方法,包括:
1、三直三现法。
即“马上现场、马上现品、马上现象”。
目的是帮助生产现场的管理者,端正正确的管理作风,准确把握问题、查明真相,实施最有效的对策,到现场解决实际问题。
2、5W2H法。
是一种综合分析的方法,适用于解决问题。
什么事情(What)?
什么地方(Where)?
什么时间(What)?
什么人(Who)?
什么原因(Why)?
怎样做(How)?
成本和代价是什么(HowMuch)?
3、PDCA法。
由美国戴明博士提出的,也称戴明模式,即策划(Plan)-实施(Do)-检查(Check)-改进(Action)。
闭环管理,环环相扣,持续改进。
4、目视管理。
即通过视觉导致人的意识变化的一种管理方法。
目视三要素:
无论是谁都能判明是好是坏(异常),能迅速判断,精度高,判断结果不会因人而异。
5、看板管理。
是管理可视化的一种表现形式,即对数据、情报等状况一目了然地表现,主要是对管理项目、特别是情报进行的透明化管理活动,是发现问题、解决问题的非常有效且直观的手段。
6、定置管理。
即为确定物品等的位置并进行分类标识,易于找寻。
有物必有区,有区必分类,分类必挂牌。
人和物有三种结合状态。
A状态:
即人和物处于紧密结合状态,人需要的物随手可以拿到,物和人结合非常紧密。
B状态:
人和物处于寻找状态,这时物不能随手拿到,需要到处寻找,要浪费一些时间才能找到。
C状态:
即对人不起作用的物,或者就现场不需要的物。
定置管理的目的就是取缔C状态,不断改善B状态,使其达到A状态,尽量保持A状态。
7、5S管理。
5S是整理(SEIRI)、整顿(SEITON)、清扫(SEISO)、清洁(SEIKETSU)、素养(SITSUKE)的简称。
5S活动是一项基本活动,是现场一切活动的基础。
整理。
将工作场所任何东西区分为有必要的与不必要的,把必要的东西与不必要的东西明确地、严格地区分开来,不必要的东西要尽快处理掉。
整顿。
对整理之后留在现场的必要的物品分门别类放置,排列整齐。
明确数量,有效标识。
清扫。
将工作场所清扫干净,保持工作场所干净、亮丽。
清洁。
将上面的3S实施的做法制度化、规范化。
素养。
通过晨会等手段,提高员工文明礼貌水准,增强团队意识,养成按规定行事的良好工作习惯。
6S,增加安全(SAFETY)。
7S,增加节约(SAVING)。
8S,增加服务(SEVICE)。
8、TPM管理。
工厂全面改善。
为了解决设备运行过程中的诸多问题,美国把维护设备的经验进行了总结,将装备出现故障以后采取应急措施的事后处置方法称为“事后保全(BM)”,将装备在出现故障以前就采取对策的事先处置方法称为“预防保全(PM)”,将为延长装备寿命的改善活动称为“改良保全(CM)”,把为了制造不出故障不出不良的装备的活动叫做“保全预防(MP)”,最后将以上BM、PM、CM、MP四种活动结合起来称之为“生产保全(PM)”,这就是TPM的雏形。
二战后,日本在向美国学习的过程中,将美国的PM生产保全活动引进日本,成功地创立了日本式PM,即“全员生产保全(TPM)”。
因有80~90%的员工都参与了此项活动,于是在PM前加了“T”(Total),正式将该公司的PM活动命名为TPM。
9、JIT管理。
JIT管理(JustInTime),又称即时管理,零库存管理。
日本丰田公司首创。
其核心思想是“在需要的时间,使用需要的资源,生产需要的产品”。
生产原料及产品实现零库存。
3洛阳各企业生产车间现场管理方法的应用
3.1现场管理概况
虽然国内制造企业,尤其是改革开放以来不断改革的这些老国企一直强调工业工程应用,尤其是生产管理,目的是希望企业有干净整洁、有序高效的生产环境,学习的榜样是多年来一直坚持5S管理的日本企业,用5S、6S甚至发展出7S与8S来规范现场、现物。
然而几十年下来,国内很多企业,尤其是洛阳一拖部分分厂这些老国企,脏乱现象随处可见,有规定而不按照规定内容执行,物料随意堆放,设备维护随心所欲等等现象司空见惯。
相比之下,日本企业,不论办公楼还是工厂车间,真正做到干净整洁,有序高效,甚至可以说是“窗明几净”。
与国内的现场管理,有着天壤之别。
对于这些企业与国外在现场管理水平上差距巨大的原因,根据在实习参观期间的观察与总结,我认为有以下几点:
1、实施方法差异
国内企业现场管理的实施上,大多热衷口号而流于表面,如我们在洛阳建筑机械厂、洛阳轴承厂所看到的那样,似乎在厂区、车间黑板上铺天盖地宣传“xx守则”、“文明生产xxx”诸如此类的标语就能改变一名员工的工作素质,这种方法的效果,很显然,几乎为零。
因为在一个脏乱环境中工作、工作细节毫无约束的员工,是不会具有认真对待每一个工作细节和管理规范的素质的。
现场管理不结合日常工作和生产规范,取而代之的是空洞的口号、标语,这对提升员工素质和现场管理水平毫无裨益。
相反,世界的优秀企业,都把5S等标准规范看作现场管理的基础技术,结合实际工作环境,生产流程,明确每一项管理内容的具体做法,什么物品放在何处,如何放置,数量几何,如何清晰标识等等,简单有效。
2、管理定位差异
国内许多企业管理者将整洁干净、有序高效的现场管理仅仅认为是一个卫生上问题,而不是一个生产上的问题。
既然不是生产上的问题,自然在日常生产的过程中,现场管理问题就被放在一边,不引起重视。
或者当有上级领导来检查工作时临时做一次全面的整理、清洁工作,检查结束之后,又将问题置于不顾。
而日本企业管理者认为5S是现场管理之基石,5S做不好的企业不可能成为优秀的企业,因此将坚持5S管理作为重要的经营原则。
3、生产文化差异
日本制造的精细品质在世界享有盛名的原因,是因为日本文化的“匠人精神”,所谓匠人,即是能够亲手操作干好一件活的工人。
中国原先对匠人是非常崇敬的,都尊称为师傅,颂之为能工巧匠。
对工艺刻苦钻研,为之付出全部心血的精神,可谓匠人精神。
一个日本人,让他每天擦六遍桌子,他一定会这样做;而一个中国人开始会擦六遍,慢慢觉得五遍、四遍也可以,最后索性不擦了,中国人做事的最大毛病是不认真,做事不到位,每天工作欠缺一点,天长日久就成为落后的顽症。
——这正是现今低水平车间现场管理原因的真实写照。
现场管理实际上应该是一种生产文化,作为员工每天都在一个对生产中各个过程的“正确”与“错误”都了然于胸的环境中工作,严格要求每个员工必须约束自己的行为,久而久之就能实实在在地提升员工的素质[2],现场管理水平自然而然也就提高了。
3.2现场管理方法的应用
对于现场管理的评价是指对现场人员管理、现场定制管理、现场作业管理、现场物流管理、现场质量控制、现场安全控制、现场设备管理和经营效果评价等现场管理的综合评价。
鉴于实习条件所限,通过参观与问询,目前洛阳一拖、中信重工等企业生产车间使用最多的现场管理方法有5S管理、目视管理、看板管理、定置管理。
下面从5S管理的角度来分析企业车间的现场管理状况。
实习参观过程中,不难发现,在所参观的洛阳企业中,宣传和使用的最广泛的现场管理方法就是5S管理。
从现场参观的角度,最能体现一个车间的生产管理水平的也就是5S管理的效果,因为5S管理是一种管理理念和制度,通过规范现场、现物,营造一目了然的工作环境,培养员工良好的工作习惯,保证优质、低耗、高效生产,进而实现企业经营目标。
现场管理做的不好的企业也体现在5S管理上,譬如洛阳一拖建筑机械厂,在整理(SEIRI)方面,厂房内大量的废弃材料、边角料,以及暂时或无法使用的吊运设备、剪床等机加工设备占据了很大的空间,甚至于影响了物料的物流路径以及人员的通行。
在整顿(SEITON)上,工人在生产过程中存在量具、工具等随处摆放的行为且较为严重,半成品或暂存成品的堆放区域不固定,这样既增加无效劳动,又浪费了物品的取放时间。
再者,清扫(SEISO)和清洁(SEIKETSU)也是国内很多企业尤其是重工业企业的最大诟病,在建筑机械厂的生产现场,油污遍地、灰尘堆积、生产垃圾随意堆放,一眼可见现场管理水平的低下。
“污秽的机器智能生产出污秽的产品”,现场的油垢、废物可能降低生产效率,使生产的产品不合格,甚至引发意外事故。
[1]
相较之下,中信重工的总厂及发电设备公司的5S管理水平则相当优秀,车间整洁明亮