精编数控高速滚齿机总体布局及尾座部件设计.docx
《精编数控高速滚齿机总体布局及尾座部件设计.docx》由会员分享,可在线阅读,更多相关《精编数控高速滚齿机总体布局及尾座部件设计.docx(45页珍藏版)》请在冰豆网上搜索。
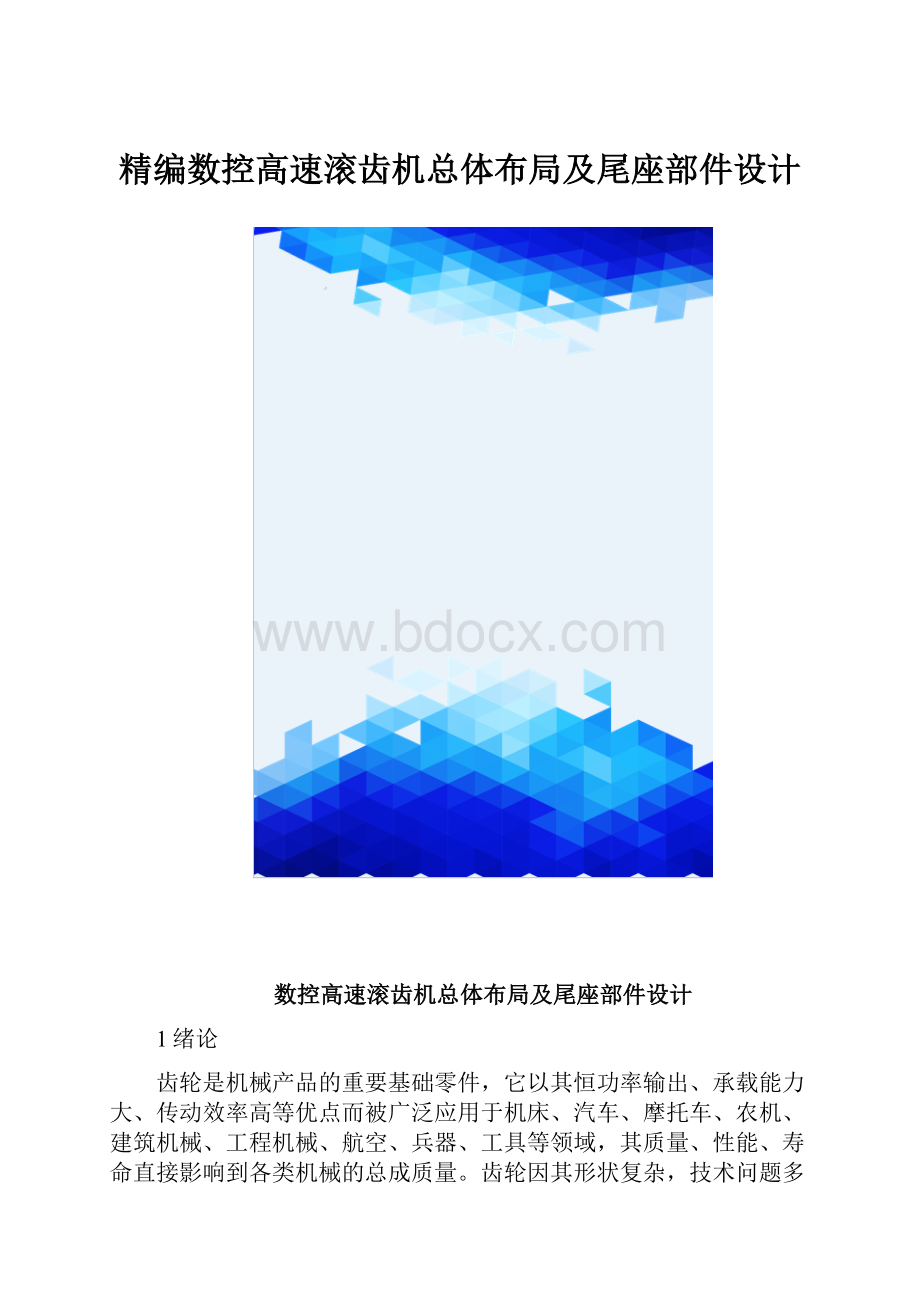
精编数控高速滚齿机总体布局及尾座部件设计
数控高速滚齿机总体布局及尾座部件设计
1绪论
齿轮是机械产品的重要基础零件,它以其恒功率输出、承载能力大、传动效率高等优点而被广泛应用于机床、汽车、摩托车、农机、建筑机械、工程机械、航空、兵器、工具等领域,其质量、性能、寿命直接影响到各类机械的总成质量。
齿轮因其形状复杂,技术问题多,制造难度较大,也造成齿轮加工机床的高度复杂性,所以齿轮制造水平在较大程度上反映了一个国家机械工业的水平。
近年来,随着汽车、机械、航天等工业领域的不断发展,对齿轮提出了更高的要求:
传动速度大、承载能力强、使用寿命长、运行噪音小、制造成本低,相应地对齿轮的设计、加工、检测等方面也提高了要求。
在这种背景下,现代设计方法、先进制造技术、计算机技术及相关技术的交叉融合,使齿轮相关技术的研究进入了一个崭新的阶段。
1.1齿轮加工技术
圆柱齿轮的加工方法很多,按齿廓形成原理,可以分为成形法和展成法两大类。
成形法是用刃部形状与被切齿轮槽形状相同的成形刀具来加工齿轮的,属于成形法的齿轮加工方法有铣齿、拉齿、冲齿、成形磨齿、压铸等。
展成法又称滚切法,是加工时切削刀具与工件作相对展成运动,刀具和工件的瞬心线相互作纯滚动,两者之间保持确定的速比关系,所获得加工表面就是刀刃在这种运动中的包络面。
现代齿轮生产中,主要是展成法。
属于展成法的齿轮加工方法有滚齿、插齿、剃齿、珩齿、展成法磨齿、车齿等。
①滚齿加工
滚齿是一种高效的、应用最广泛的一种齿廓加工方法,是依照交错轴斜齿轮啮合原理进行加工的。
滚齿精度一般可达7~8级,当采用高精度滚刀和高精度滚齿机时,可滚切5级精度的齿轮。
目前滚齿加工的先进技术有:
1)多头滚刀滚齿,可以大幅度提高生产效率,滚刀头数最多可达7头,但各头之间的偏差影响齿轮的齿向精度。
2)硬齿面滚齿技术,国外硬齿面滚齿精度达DIN6级,加工费用仅为磨齿的1/3,效率较普通的磨齿高1~5倍,且无磨削烧伤或裂纹。
3)滚齿机数控化,大幅度提高了机床的加工精度及工艺能力指数,增加了机床的可靠性并且扩大了机床的加工范围。
4)干切工艺。
德国Liebherr公司的LC80系列滚齿机,美国Gleason一Pfauter公司的GP130系列滚齿机,日本三菱重工公司的GN10系列滚齿机等均可以采用高速干式切削加工。
国内齿轮机床制造厂家在齿轮加工干切技术方面,目前正处于研究的初级阶段。
在CIMT2005机床展上,日本三菱公司展出的GE15A滚齿机上,采用了表面涂有超级干切涂层的MACH7高速钢滚刀,线速度达250m/min;重庆机床厂展出的YKS3112滚齿机上,采用了表面涂有DUAL涂层的硬质合金滚刀,线速度达181m/min。
干式滚削具有高的生产率、高精度和高的工件质量,无切削液,工件不受油液污染,符合环保要求,属于无污染的绿色加工工艺。
②插齿加工
插齿也是广为采用的切齿方法,它是用形状为齿轮或齿条的插齿刀具,与被加工齿轮按一定的速度作相啮合运动的同时,刀具沿齿长方向作往复运动形成切削加工,特别适合于加工内齿轮和多联齿轮。
采用特殊刀具和附件后,还可加工棘轮、内外花键、扇形齿轮、齿条、端面齿轮等。
插削速度最高可达1000~2500次/min冲程数,加工精度达5~6级。
插齿技术的研究重点有:
1)插齿机的数控化,以便加工椭圆齿轮、非圆齿轮和特殊形状的齿轮。
2)提高插齿机的冲程次数,从而提高插齿效率。
3)硬齿面齿轮的插削工艺的研究。
4)数控插螺旋齿,以提高螺旋齿轮的加工精度。
③剃齿加工
剃齿方法除了人们所熟知的平行轴剃齿、对角剃齿外,径向剃齿的发展近年来格外引人注目。
径向剃齿由于只作径向进给运动而省掉了轴向或对角进给,因而效率大大提高。
径向剃齿时,齿轮的齿形和齿向修形均靠剃齿刀修形完成。
剃齿刀齿面轮廓形状和精度要求高,齿形要求中凹,齿向要反鼓,同时对剃齿刀刃口槽形位置、形状(如刃口错位排列)、矩形槽都有很高要求,因此剃齿刀设计和制造上都有相当的难度。
近年来由于径向剃齿刀的研制成功,使径向剃齿这一高效方法在越来越多的齿轮加工中得到应用。
国内一些工具厂近年来成功地研制出径向剃齿刀,同时不少齿轮制造厂引进了相应的剃齿刀修磨机床,因而径向剃齿工艺在我国也得到了越来越广泛的应用。
由与径向剃齿比平行剃齿或对角剃齿产生更大的径向挤压力,因此要求机床具有更高的刚性。
重庆机床厂近年开发的YA4232A剃齿机和YAT4232径向剃齿机均具有很高的刚性,适合于汽车、摩托车和机床齿轮的剃齿加工。
④珩齿加工
珩齿技术的发展经历了从自由珩到强迫珩,从最初的齿轮式外啮合珩到蜗杆珩再到现在的内啮合珩等阶段。
最初的齿轮式外珩齿技术,采用的是自由珩技术,靠珩轮轮齿对工件齿轮表面进行光整加工,可有效地改善齿面质量。
80年代,卡谱(Kapp)公司推出的VAC65型珩齿机,采用了称为Coronieren的硬齿面精加工方法。
其珩磨轮是一个有高精度内齿轮的钢环,内齿轮齿面上电镀单层CBN磨料。
工具齿轮与工件齿轮间采用电子同步系统相联系,运转中通过进给使工件齿轮的各项误差逐渐得到修正,从而达到十分稳定的精度。
目前晰齿都用于中、小模数的齿轮。
我国大连理工大学研究了可控电解珩磨工艺,解决大模数齿轮的珩齿,其特点是不受齿轮模数、齿数、尺寸及结构形式限制,可在滚齿的基础上,将齿形精度提高1~2级,表面粗糙度降低到Ra0.5m以下。
⑤磨齿加工
磨齿是获得高精度齿轮最有效和可靠的方法。
由于现在多用硬齿面的齿轮,磨齿成为高精度齿轮的主要加工方法。
目前碟形砂轮和大平面砂轮磨齿精度可达DIN2级,蜗杆砂轮磨齿精度达DIN3~4级,锥形砂轮磨齿精度达DIN4~5级。
磨齿的主要问题是效率低、成本高,所以提高磨齿效率,降低费用成为当前主要研究方向。
近年来出现的新技术有:
1)改进磨削方法,Maag公司提出了“K"磨削法和Niles公司提出了“双面磨削法”,提高了磨齿效率。
2)应用立方氮化硼砂轮高效磨齿,比用单晶刚玉砂轮磨削效率提高5-10倍,被磨削表面不易发生烧伤和裂纹,疲劳强度高。
3)采用数控技术,提高了效率和自动化程度,获得了稳定和可靠的精度。
4)开拓新的磨削原理和磨齿工艺,瑞士赖斯豪尔公司新开发的RZP200型磨齿机采用了环面蜗杆砂轮磨削的连续成形磨齿工艺,其效率是普通磨齿法的5倍。
以上几种圆柱齿轮工艺方法与加工精度的比较见表1.1
表1.1圆柱齿轮工艺加工方法和加工精度比较
工艺方法
工艺方法简图
加工精度
加工特点
滚齿
5~9
生产率高,通用性大,连续分度滚齿,运动误差易保证
插齿
5~8
适用于中小模数齿轮加工,通用性好,广泛用于内齿轮、双联及多联齿轮加工
剃齿
5~7
主要用于齿轮的滚、插预加工后的精加工,和磨齿相比,具有效率高,成本低,齿面无烧伤和裂纹等优点
珩齿
6~8
效率高,成本低,表面质量好,齿面无烧伤,尤其适用于作硬齿面滚、插后改善表面粗糙度的后续工序
磨齿
成型砂轮磨齿
7~8
生产率很高,砂轮是专用的,适用于较大批量生产齿轮
蝶形砂轮磨齿
4~7
采用碟形砂轮的棱边磨削不加冷却液,生产率较低
蜗杆砂轮磨齿
5~7
生产率很高,特别适用于成批生产和大量生产
1.2传统滚齿机分析
传统滚齿机典型机型Y3150E,传动系统图如图1.1所示。
传统的滚齿机传动采用单电机驱动,用分流传动方式驱动多个执行机构,内联传动链严格的速度同步与行程同步关系是靠具有准确传动比的传动元件(齿轮、蜗轮、蜗杆等)实现的,调整环节采用挂轮以保证足够精度的传动比与调整范围。
传动系统有五条传动链:
主运动传动链、展成运动传动链、轴向进给传动链、附加运动传动链、快速空行程传动链。
这些传动使滚齿机只具有滚切圆柱齿轮、蜗轮的加工能力,其工作范围不仅较窄,而且机械结构复杂,且传动链上的工作元件多。
例如展成运动链和附加运动链除了要必须经过合成运动机构外,从首端件到末端件还各自需要经过9对齿轮、蜗杆蜗轮、以及10根左右轴的顺序传递;轴向进给传动链则需要经过8对齿轮、蜗杆蜗轮、丝杠螺母、7根轴的顺序传递。
这些传动链不仅传动元件多,积累误差大,而且误差还交替传递,尤其是展成运动链和附加运动链有一部分重复使用,这样就易形成误差的交替传递,从而将附加运动的传动误差,传入到要求分度运动准确性很高的展成运动上。
传统机械滚齿机的滚刀主轴转速最高为500rpm,工作台转速最高为32rpm。
传统机械传动链滚齿机已经不适合新型机床对传动精度与传动速度的要求。
由于各传动元件的制造和安装误差,使得内联传动链首端件和末端件不能按理想的传动关系运动,存在传动误差。
滚齿机传动链精度是指按规定的工件齿数调整后,工件主轴相对于滚刀主轴回转运动的转角误差。
传动链中的传动环节与传动元件越多,传动误差的来源越多,传动误差也越大,传动链的传动误差是影响齿轮加工精度的主要因素。
提高内联传动链的传动精度一直是此类机床的研究重点。
图1.1Y3150E滚齿机传动系统图
1.3数控滚齿机分析
二十世纪80年代以来,数控滚齿机进入了实用阶段。
随着计算机技术、电子技术和自动控制技术的发展,国外滚齿机产品中,数控滚齿机已占主导作用,我国研制的数控滚齿机始于二十世纪80年代中期。
数控滚齿机的机械结构,在很多方面继承了传统机械滚齿机的特点,但由于应用了数控技术所以在结构上作了相应的改进,以充分发挥机电一体化的优势。
现代数控滚齿机,各个运动都由单独的伺服电机驱动,交流主轴电机直接安装在刀架上,经过几对高精度圆柱斜齿轮传至滚刀主轴,区别于传统滚齿机设计中主轴运动由普通或变频电机通过较长传动链传至主轴,而此设计大大降低了传动误差,提高了传动精度,并增强了相关的传动特性和传动刚性,转速可达1500rpm。
工作台采用大直径高精度圆柱斜齿轮传动,改变了传统的工作台由蜗轮、蜗杆传动的形式,提高了加工效率,采用高精度、高刚性滚动轴承支承,最高转速可达150rpm,显著提高了机床的加工精度。
数控滚齿机采用全数字控制,并带有EGB(ElectronicGearBox)电子齿轮箱,由它代替了传统机械滚齿机各种交换齿轮的功能,所以机床各项运动精度高,调整方便。
机床的柔性好,切削循环可设置一次、二次方框循环,L循环等多种切削循环方式,除可加工圆柱直齿轮、斜齿轮、短花键轴、链轮、蜗轮等外,还可加工多种锥齿轮、鼓形齿等特殊齿形的齿轮。
图1.2数控滚齿机传动系统图
数控滚齿机由于传动链大大缩短,减少了轴、轴承和齿轮等元件的制造误差、间隙和装配误差的影响;另一方面由于刚度的提高和热变形的减少保持了精度的稳定性;第二是可以方便地对机械误差进行补偿。
所以相对传统机械滚齿机来说,机械误差对加工精度的影响能得到有效的控制。
图1.2是国内目前最先进的数控滚齿机传动系统图。
1.4滚齿加工技术的发展趋势
滚齿是国内外应用最广的切齿方法,一些国家滚齿机的拥有量约占所有齿轮机床总量的45~50%。
为适应齿轮加工行业对制造精度、生产效率、提高质量及清洁生产的要求,滚齿机及滚齿加工技术出现了以下几个发展趋势:
①全数控化
所谓的全数控化,指不仅齿轮加工机床的各轴进给运动是数控的,而且机床的展成运动和差动运动也是数控的,即机床的各运动轴进行CNC控制及轴间实现联动。
齿轮加工机床全数控化后具有如下特点:
1)机床结构发生革命性的变化
齿轮加工机床全数控化使得机床传动链大大缩短,并且各轴间没有机械传动的联系,与传统机床相比机床的结构大大简化,增强了机床的刚性。
机床结构的简化,更有利于实现结构的模块化。
2)提高齿轮的加工精度
机械传动链缩短或完全被取代,刀具磨损的自动补偿,计算机技术的快速发展,新的智能控制算法的应用,伺服系统的脉冲当量的进一步减小,从而提高了机床的加工精度及工艺能力指数。
3)提高齿轮加工的效率
完全排除了交换齿轮和行程挡块的调整,缩短调整时间,而且可在一次安装下不经过任何调整就可加工多联齿轮。
工件程序可以储存供再次加工时调用,调整时间显著缩短,一般调整时间仅是非数控系统的10%~30%。
4)高精度快速地加工非圆齿轮、修形齿轮
由于数控技术的采用,可以方便调整、控制各轴间的运动关系,从而加工出
椭圆齿轮等各种非圆齿轮和各种修形齿轮,且加工精度远高于传统的机械靠模加工方法。
5)高度自动化和柔性化
可实现任意工作循环,缩短调整时间,便于实现小批量多品种加工。
同时机床本身柔性大为增加,易于实现机床重组,易于组成柔性齿轮制造系统,实现齿轮制造的柔性自动化过程。
②零传动技术的应用
“零传动”即直接驱动,由电机直接驱动刀具、回转工作台的回转及直线进给系统,完全取消所有机械传动环节,实现动力源对机床工作部件的直接传动传动链的长度为“零”。
一般数控滚齿机的滚刀主轴由变频交流主电机通过一到两对斜齿轮驱动,直接驱动工件主轴的分度副,一般采用高精度蜗轮副或特殊齿形的多头双蜗轮副以及大尺寸齿轮副,各进给轴通过滚珠丝杠副实现旋转运动向直线运动的转换。
近几年国外的各齿轮制造厂家在小直径(<200mm)、小模数(m<3mm)齿轮加工方面已推出滚刀轴和工件轴直接驱动的机型。
如Gleason—Pfauter公司制造的P60、P100、P210、GP130,Liebherr公司制造的LC80、LC120、LC150、LC180,Koepfer公司制造的Koepfer160,Hurth公司制造的5160等。
直接驱动的实现是使用电主轴直接驱动滚刀主轴,用同步力矩伺服电机直接驱动工作台。
由于直接传动,去掉了高精密齿轮等关键零件,这样就消除了由于传动装置而产生的误差,如反向间隙、啮合误差等。
而各进给轴仍通过滚珠丝杠副实现旋转运动向直线运动的转换,如果各进给轴采用直线电机直接驱动,将完全实现零传动。
零传动齿轮加工机床不仅可以大幅度提高机床的加工精度和加工速度,也可以完全解决机械传动链中存在的磨损问题,可以长期保持机床的精度。
此外,零传动方案还可极大地简化机床的机械结构,提高机床的动静刚度,也有利于实现可重构机床的设计和制造。
③高速、高精度
滚齿机的高速化,主要是指机床拥有高的刀具主轴转速和高的工作台转速。
它们是影响切削效率的主要指标。
传统机械滚齿机的滚刀主轴转速最高为500rpm,工作台转速最高为32rpm。
电主轴和大扭矩同步力矩伺服电动机的应用使刀具主轴和工作台转速得到提高。
Gleason—Pfauter公司制造的P60卧式滚齿——磨齿复合机床,刀具主轴转速达12000rpm,工作台转速达3000rpm。
德国Liebherr公司制造的LC80干式切削滚齿机,滚刀主轴转速为9000rpm,工作台转速为800rpm。
国外厂家在小直径小模数方面均有刀具主轴转速达3000rpm,工作台转速达1000rpm的机型。
在CIMT2005机床展上,日本三菱公司展出的GE15A滚齿机上,采用了表面涂有超级干切涂层的MACH7高速钢滚刀,线速度达250m/min,滚切模数1.4mm,齿数34,螺旋角22.5的齿轮,切削时间为lOs,加上上下料等辅助时间,加工一个齿轮总循环时间仅为14.3s。
提高加工精度的途径可分为两大类,一是提高机床本身的精度,二是通过误差补偿来减少加工误差。
由于采用了高精度、具有预加负荷的高刚性直线导轨、滚珠丝杠、滚动轴承、电主轴、大扭矩同步力矩伺服电动机,使齿轮加工机床在高速加工的条件下精度得到保证并有所提高。
电主轴精度一般为径向振摆0.002mm,轴向跳动0.001mm;大扭矩同步力矩伺服电动机定位精度达0.5",重复定位精度达0.01"。
直线运动轴的定位精度小于0.008mm,重复定位精度小于O.OO5mm。
影响齿轮加工精度的因素很多,除了电气方面的以外,还有如机床结构特性与热特性、刀具磨损、机床主轴运动误差、各种静态载荷,以及工件装火和机床振动等因素。
所有这些因素都可以通过建模(如神经网络建模)来加以补偿。
由于计算机技术的迅速发展和插补算法的不断改进,数控系统的数据处理和曲线拟合精度可以达到很高。
采用多种智能控制方式,可以改善伺服系统的跟踪响应特性,也可以提高加工精度。
滚齿尽管一般用于粗加工,但在高速切削的条件下仍能达到DIN6~7级精度,为其后的精加工工序获得高精度提供了保证。
④环保化
众所周知,金属切削中的切削液具有冷却、润滑和排屑等作用,可获得良好的加工质量,并提高刀具耐用度和生产率。
但随着近年来切削速度和切削功率的急剧提高,单位时间内金属切除量大量增加,切削液的用量也越来越大,并且在高速切削过程中,切削液产生飞溅、形成油雾,不仅提高了企业生产成本,还污染了生态环境,并损害了工人的身体健康。
为此,通常将加工区用保护罩封闭起来,安装上油雾分离器,使排出的只是不含油的雾,而切削油则重新流回机床内循环利用。
但这并不能从根本上解决环保问题,因为变质切削液的更换排放会严重污染环境。
因此,不使用切削液的干切削就成为改善生态环境,降低生产成本的有效措施,也是实现清洁化生产的一条重要途径。
国内外著名的齿轮加工机床制造商及齿轮刀具制造商,均把研制满足环保要求的干式切削机床和刀具作为产品开发的一项首要的任务来抓。
有的机床甚至不采用液压油及循环润滑油,实现绿色制造及清洁加工。
干式切削要解决的问题是刀具寿命问题、刀具价格问题和切屑的安全迅速地排走问题。
采用硬质合金涂层刀具进行干切削,尽管第一次购刀价格比湿式刀具价格高,但因切削效率高且刀具寿命长,还节省了切削液及喷淋过滤装置的费用,从而单件齿轮的加工成本反而有所降低,同时又符合环保无污染的要求。
据日本三菱重工资料报道,采用高速干式切削刀具的使用寿命是湿式切削的3倍,刀具费用降低47%,加工效率提高2倍,单件齿轮加工成本(刀具费、设备费、切削油费、人员费)降低40%。
因此,干式切削降低了单件齿轮的加工成本。
目前,国外主要的齿轮加工机床厂家都在大力开发数控高速干切滚齿机。
例如:
德国Liebherr公司的LC80系列滚齿机,美国Gleason—Pfauter公司的GP130系列滚齿机,日本三菱重工公司的GN10系列滚齿机等均可以采用高速干式切削加工。
国内齿轮机床制造厂家在齿轮加工干切技术方面,目前正处于研究的初级阶段。
在CIMT2005机床展上,日本三菱公司展出的GE15A滚齿机上,采用了表面涂有超级干切涂层的MACH7高速钢滚刀,线速度达250m/min;重庆机床厂展出的YKS3112滚齿机上,采用了表面涂有DUAL涂层的硬质合金滚刀,线速度达181m/min。
⑤复合化
齿轮机床(特别是大型齿轮机床)有集多种工艺于一体的趋势。
如Hurth公司的WF3500滚齿机,将插齿、滚齿(包括滚内齿轮)、磨齿和齿轮检测集于一体,工件一次装夹只需更换切削头,就可实现相应的齿轮加工功能,同时还可以对加工过程中的齿轮进行检测,以决定加工用量。
Gleason公司的P60滚齿—磨齿复合机床,能完成先用铣刀加工双头蜗杆,再用CBN磨轮磨该蜗杆,并具有去除蜗杆端面毛刺的功能。
同时该机床还配有自动对齿机构和工件自动上下料机械手及料仓。
Liebherr公司的LC80型滚齿机,机床采用模块化设计,只要更换切削头,就可组合成滚齿、单分度铣齿或插齿。
重庆机床厂的YKS3120系列六轴数控高速滚齿机,能在一次安装中加工不同模数、不同齿数、不同螺旋角及不同螺旋方向的双联齿轮及单分度铣槽,并可配备自动对齿机构、去除齿轮端面毛刺及工件自动上下料装置,在该系列机床上还可进行硬齿面滚齿。
⑥网络化
数控系统的通讯联网功能不断加强。
开放式的CNC系统已成为数控行业不可抵挡的趋势,开放性的CNC系统可以方便地进入各级通用网络,从而可以柔性地实现DNC、FMS、CIMS和FA(自动化工厂)。
NC技术使FMS和CIMS成为可能;FMS和CIMS的发展反过来要求CNC系统应具有通讯和联网功能,以便实现CIM环境中的信息集成和系统管理。
现代CNC系统一般都具有用于通讯的串行口和DNC接口,高档数控系统充分利用Internet/Intranet的功能,使网络化生产、远程调试、远程诊断等功能得以实现。
⑦智能化
由于计算机技术及数控技术的发展智能技术也逐渐用于高性能数控齿轮机床中,具体表现在:
1)完成加工质量与加工过程智能控制。
根据对工件在线检测的结果和实时采集的机床状态,预测工件的加工质量,并及时调整加工过程的工艺参数,以保证机床的加工精度。
2)智能诊断。
故障诊断的智能化表现在两方面:
一方面是机床会对曾经产生的故障作记录,当下次碰到该故障时,它会首先提示可能的原因;另一方面,现场信息经过压缩,存贮在机床的“黑匣子”中,一旦机床发生的故障超出其自身的诊断能力,就可以通过Internet从网上专家系统获得支持,进行交互式的远程协同诊断。
1.5零传动滚齿机及其关键技术的研究进展
1.5.1零传动滚齿机国内外研究进展
目前为止,国际上著名的齿轮加工机床生产厂家:
美国Gleason—Pfauter、德国Liebherr、日本的三菱重工等企业都投入大量的人力、物力和财力研究零传动技术在齿轮加工机床中的应用,这些厂家在小直径(<200mm)、小模数(m<3mm)齿轮加工方面推出的最新产品都部分应用了零传动技术及其它相关新技术,使得齿轮加工机床的性能达到了一个新的高度。
如:
Gleason—Pfauter公司研制的P60、P100、P210、GP130滚齿机;Liebherr公司制造的LC80、LC120、LC150、LC180滚齿机;Koepfer公司制造的Koepfer160滚齿机,Hurth公司制造的S160滚齿机等。
LC80干式切削滚齿机,滚刀主轴最高转速为9000rpm,工作台转速为800rpm;P60卧式滚齿——磨齿复合机床,刀具主轴转速达12000rpm,工作台转速达3000rpm。
在回转运动方面取消机械传动副,不仅大幅度提高了机床的加工精度和加工速度,也可以完全解决机械传动链中存在的磨损问题,可以长期保持机床的精度,此外,还极大地简化了机床的机械结构。
但是,这些厂家提供的机床价格却非常昂贵,高达400万元人民币/台。
图1.3为Liebherr公司生产的LC80直接驱动滚齿机。
图1.3LiebherrLC80直接驱动滚齿机
目前国内齿轮加工机床的最高水平如下:
在工作台直线移动方面,采用数控驱动系统代替普通滚齿机的各种交换挂轮,采用交流伺服电机通过多对降速齿轮副和一对滚珠丝杠副来驱动机床的运动部件;在滚刀回转运动方面,采用交流伺服电机通过2~3对降速齿轮副来实现;在工作台回转运动方面,绝大多数齿轮加工机床仍然需要采用多对高精度齿轮副和一对高精度蜗轮蜗杆副实现。
由于存在着大量的机械传动元件,对机床的加工精度产生极大的影响,也使得机械结构变得更为复杂,调整维修也极不方便。
例如,我国最大的齿轮加工机床生产厂——重庆机床厂于2000年通过鉴定的YKS3120六轴四联动数控高速滚齿机曾被列入“国家重大技术装备创新项目”,被称为是国产高档数控滚齿机的里程碑,但该机床仍然采用了滚珠丝杠副和齿轮传动链。
因此目前为止国内在零传动齿轮机床方面还是一个空白。
二十世纪八十年代末,日本人TakashiEmura,ZhaoweiZhong等人就进行了直接驱动滚齿机的研究,他们利用伺服电机直接驱动滚刀和工件,其他运动仍采用齿轮、丝杠等减速机构。
所研究的原型机床可以加工模数1.5mm、直径57mm,JIS2级精度(相当于GB/T6级)的齿轮。
经检索,有关零传动滚齿机研究的文献仅此而已。
2005年日本三菱重工MichiakiHashitani等进行了直接驱动磨齿机的研究,如图1.4所示,用同步内置电机分别驱动刀具轴和工件轴,刀具轴和工件轴速度分别可达4500rpm和1500rpm。
为了减小负载周期波动的影响,运用前馈系统可以减小15%的周期误差,极大地提高了机床的加工精度。
图1.4ZE15A直接驱动磨齿机主轴和工作台轴结构图
1.5.2电主轴
在高速运转条件下,传统的齿轮变速系统已不能适应要求,代之以宽调速交流变频