应用IE对企业进行咨询.doc
《应用IE对企业进行咨询.doc》由会员分享,可在线阅读,更多相关《应用IE对企业进行咨询.doc(5页珍藏版)》请在冰豆网上搜索。
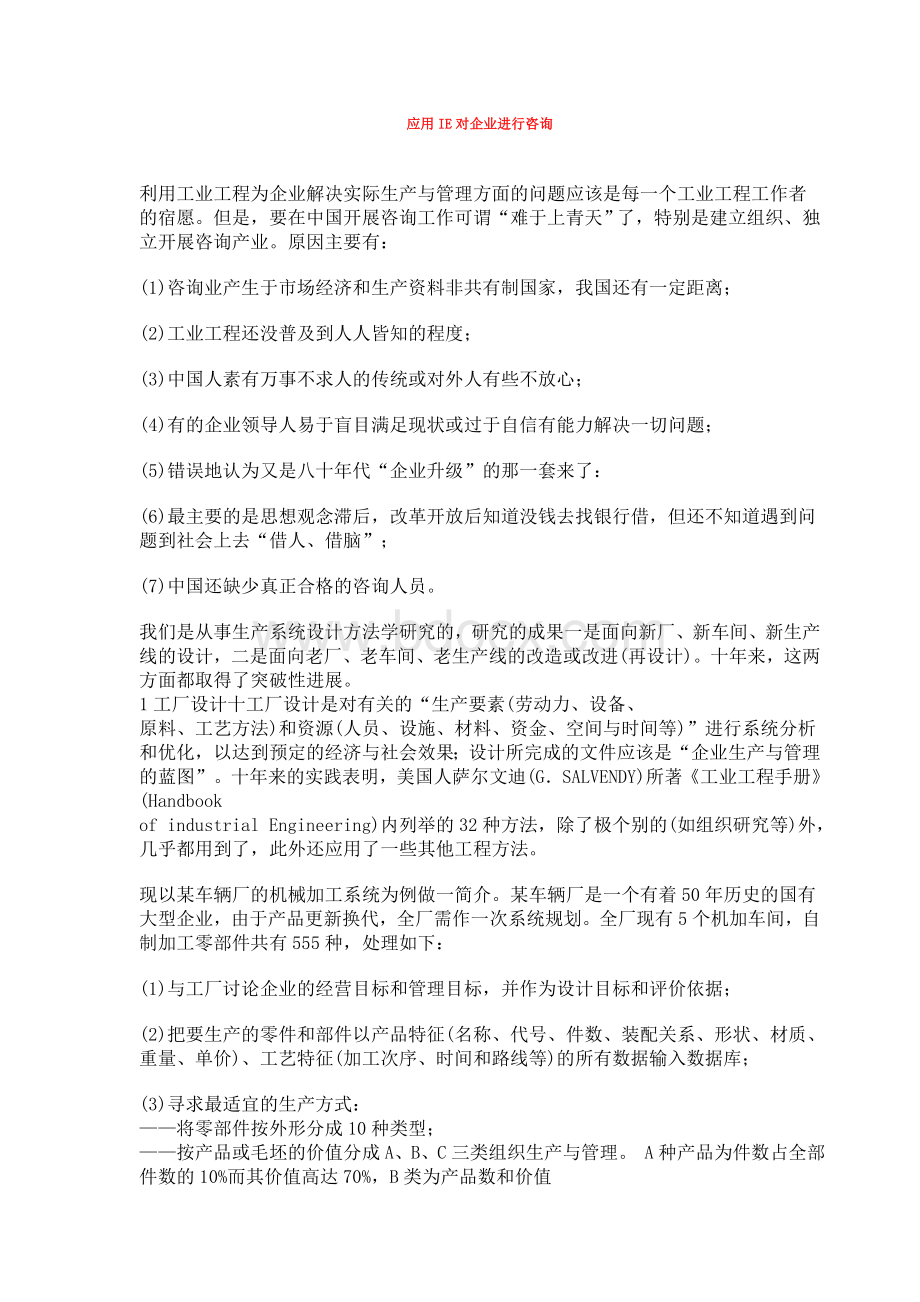
应用IE对企业进行咨询
利用工业工程为企业解决实际生产与管理方面的问题应该是每一个工业工程工作者的宿愿。
但是,要在中国开展咨询工作可谓“难于上青天”了,特别是建立组织、独立开展咨询产业。
原因主要有:
(1)咨询业产生于市场经济和生产资料非共有制国家,我国还有一定距离;
(2)工业工程还没普及到人人皆知的程度;
(3)中国人素有万事不求人的传统或对外人有些不放心;
(4)有的企业领导人易于盲目满足现状或过于自信有能力解决一切问题;
(5)错误地认为又是八十年代“企业升级”的那一套来了:
(6)最主要的是思想观念滞后,改革开放后知道没钱去找银行借,但还不知道遇到问题到社会上去“借人、借脑”;
(7)中国还缺少真正合格的咨询人员。
我们是从事生产系统设计方法学研究的,研究的成果一是面向新厂、新车间、新生产线的设计,二是面向老厂、老车间、老生产线的改造或改进(再设计)。
十年来,这两方面都取得了突破性进展。
1工厂设计十工厂设计是对有关的“生产要素(劳动力、设备、
原料、工艺方法)和资源(人员、设施、材料、资金、空间与时间等)”进行系统分析和优化,以达到预定的经济与社会效果;设计所完成的文件应该是“企业生产与管理的蓝图”。
十年来的实践表明,美国人萨尔文迪(G.SALVENDY)所著《工业工程手册》(Handbook
ofindustrialEngineering)内列举的32种方法,除了极个别的(如组织研究等)外,几乎都用到了,此外还应用了一些其他工程方法。
现以某车辆厂的机械加工系统为例做一简介。
某车辆厂是一个有着50年历史的国有大型企业,由于产品更新换代,全厂需作一次系统规划。
全厂现有5个机加车间,自制加工零部件共有555种,处理如下:
(1)与工厂讨论企业的经营目标和管理目标,并作为设计目标和评价依据;
(2)把要生产的零件和部件以产品特征(名称、代号、件数、装配关系、形状、材质、重量、单价)、工艺特征(加工次序、时间和路线等)的所有数据输入数据库;
(3)寻求最适宜的生产方式:
——将零部件按外形分成10种类型;
——按产品或毛坯的价值分成A、B、C三类组织生产与管理。
A种产品为件数占全部件数的10%而其价值高达70%,B类为产品数和价值
均占20%,余者为C类;
——推广GT(成组技术)与JIT(准时制)生产,将价值高的组织为大件、四轮、平衡肘、扭力轴四个专用生产线,中小件按加工工艺和形状的相似性组成为轴杆、盘套、叉头、座架等6个成组生产单元:
——将现行的成批轮换生产改进为按产品线生产或成组单元生产。
(4)均衡生产与控制库存;
(5)应用计算机优化流程和设施布置:
(6)应用计算机对多机床、多工序的加工进行优化排序,并用CAD与LISP给出生产作业计划;
(7)推广计算机生产信息管理系统,开发出计算机生产管理系统以代替沿用几十年的“调度指挥”生产,取消每天的调度会:
(8)向用户推荐多个设计方案以供选择。
以上设计取得了如下成果:
——在工厂的现有场地和环境限制下,生产流程长度减少了70%—94%;
——生产流程的回流或倒流总长度减少了70—97%;
——劳动生产率提高约30%:
——年节省生产资金1240万元(1990年价)/年;
——合计潜在经济效益189万元/年(未包括提高生产率的)。
2管理咨询
这几年完成的主要项目有重庆西南车辆厂、中国嘉陵工业(集团)有限公司、长安集团、北京轻型汽车有限公司(全公司所有生产部门)等。
咨询目的这些企业都是国有大型企业,技术和管理有相当的基础,自己的产品也有很强的竞争力。
通过改进现有的生产系统,充分利用现有资源(劳动力、设备、厂房、原料、资金等),增加产量,改善管理,进一步增强竞争力和提高经济效益。
一般程序应该指出的是,目前国内的多数出版物所介绍的咨询程序多为日本的,并被广泛用于企业升级;而西方国家则比较灵活,根据雇主的要求约定内容和程序。
实际的咨询,不同的雇主有不同的目的与要求,咨询程序也就不能雷同。
根据实践,我们归纳如下程序(详见附表)供参考。
限于咨询的职业道德,恕不能详细介绍,现以三个实例做简要说明。
例一,某车辆厂的变速箱分厂生产从德国引进的ZF型变速箱,原分厂由某设计院采用传统的设计方法设计,实际生产中总觉得有点什么问题,就请我们给咨询一下。
我们经一个多月的现场考察和研究,提出了84条改进建议,涉及如下方面:
(1)迅速树立优秀企业的意识和素质;
(2)制定变速箱分厂的发展规划;
(3)加强基础工作,完善产品与工艺数据;
(4)集中力量,早日取得ZF认证;
(5)抓好现场管理;
(6)加强物资管理;
(7)按实际物耗计算成本;
(8)推广计算机技术;
(9)调整设备布局;
(10)加强职工培训,严格上岗制度;
(11)按5S搞好环境与安全,吸引工人参与决策,激发劳动者热情;
(12)保护好产品;
(13)强化质量意识;
(14)精化毛坯,提高材料利用率;
(15)在全体人员中普及工业工程知识。
以上改进建议的潜在经济效益如下:
(1)精化毛坯,提高材料利用率和减少加工费,每年约为114-137万元;
(2)用计算机安排生产计划,可节省工时以多创产值151万元/年;
(3)改进布局,缩短加工流程和减少物料搬运费用29.2万元/年;
(4)缩短生产周期,减少在制品及库存,节省利息150万元/年。
例二,某摩托车厂的发动机生产,要求在“现有工艺、设备、人员的基础上,提高劳动生产率10%以上,减少在制品30%—50%,缩短加工路线10%以上,减少生产面积15%以上,扩大生产能力15%。
30%”方面提出建议。
该摩托厂是国内著名厂家之一,发动机车间生产气缸头、左/右箱体、左/右曲柄、连杆、变速鼓、凸轮轴7种零件,各自组成一条专用生产线。
根据合同要求,我们重点考察生产现场,跟班现场观察、记录、测定工人的操作、机器的运行、现场的布置(设备、坯料、零件、工具、检具等的布置)。
提出的主要工作和建议有:
(1)“用MODAPTS”(模特时间预定系统)给出了所有岗位手动操作时间,结合工厂给定的机器时间(我们做过测定校核)一起作为加工循环时间,经技术处理后成为标准时间:
(2)分析了机器的装/卸和运行过程,并绘制成工作过程图;
(3)分析了加工流程,对生产设备的布局进行了大的调整,将现有的直列式或并列式布局改进为U形,这样将大大缩短加工流程和作业者的行走距离;
(4)过量库存,是企业生产的万恶之源;在制品过量,是现场生产的万恶之源。
所有零件的生产工序间都有将近一个班产量的在制品,不仅占用大量的资金、地方,而且掩盖了生产过程的一切问题(如
出现加工次品、机器故障、工人溜号或缺勤等),还消耗大量原材料、动力、劳动力。
该发动机车间就有过堆积成千上万个不合格待处理的箱体;
(5)作业者操作不合理造成的浪费,例如毛坯、在制品、零件的摆放位置、方式、数量,都要影响到作业者的动作及时间;
(6)零件传送方式不当。
原车间内加工的零件是由可装载200件的专用小车运送,装、摆、运都要耗费时间,积累起来就不是一个小数值。
例如气缸头的生产,平均每道工序耗费5.2秒,占生产循环的
20-30%;
(7)将现在的间断生产改进为连续生产,缩短生产流程和生产周期。
以右曲柄加工为例,改进后减少搬运次数94.1%,缩短等待加工时间97.7%。
缩短流程53.3%。
例三,某轻型汽车公司涂装生产线漆生产能力的查定。
该涂装线是某专业设计院设计的,原设计能力单班为年产l万台。
由于市场看好,开三班也仅能生产2万多台,工厂希望能进一步扩大产量又不花许多钱,因而求教于咨询。
我们通过了解情况、熟悉产品和工艺、现场观察、跟班测量与写实,收集到大量有关设备、操作、定额和流程的第一手数据,通过系统分析,从生产工人的工作绩效评定、设备的利用率和运行参数的关系,找到了提高生产率和增加产量的途径。
由附图可以看到,各工序的作业时间极不平衡。
为此重新设计操作岗位,适当合并岗位,兼顾多种操作。
咨询效果汇总如下:
(1)原生产线共有操作人员36人,改进后为24—28人,提高劳动生产率约50%;
(2)三班生产能力为4.47万辆,较原来近翻了一翻;
(3)潜在经济效益近1000万元/年;
(4)咨询建议成为公司下达1994年生产计划的依据。