压圈冲压模具设计.docx
《压圈冲压模具设计.docx》由会员分享,可在线阅读,更多相关《压圈冲压模具设计.docx(14页珍藏版)》请在冰豆网上搜索。
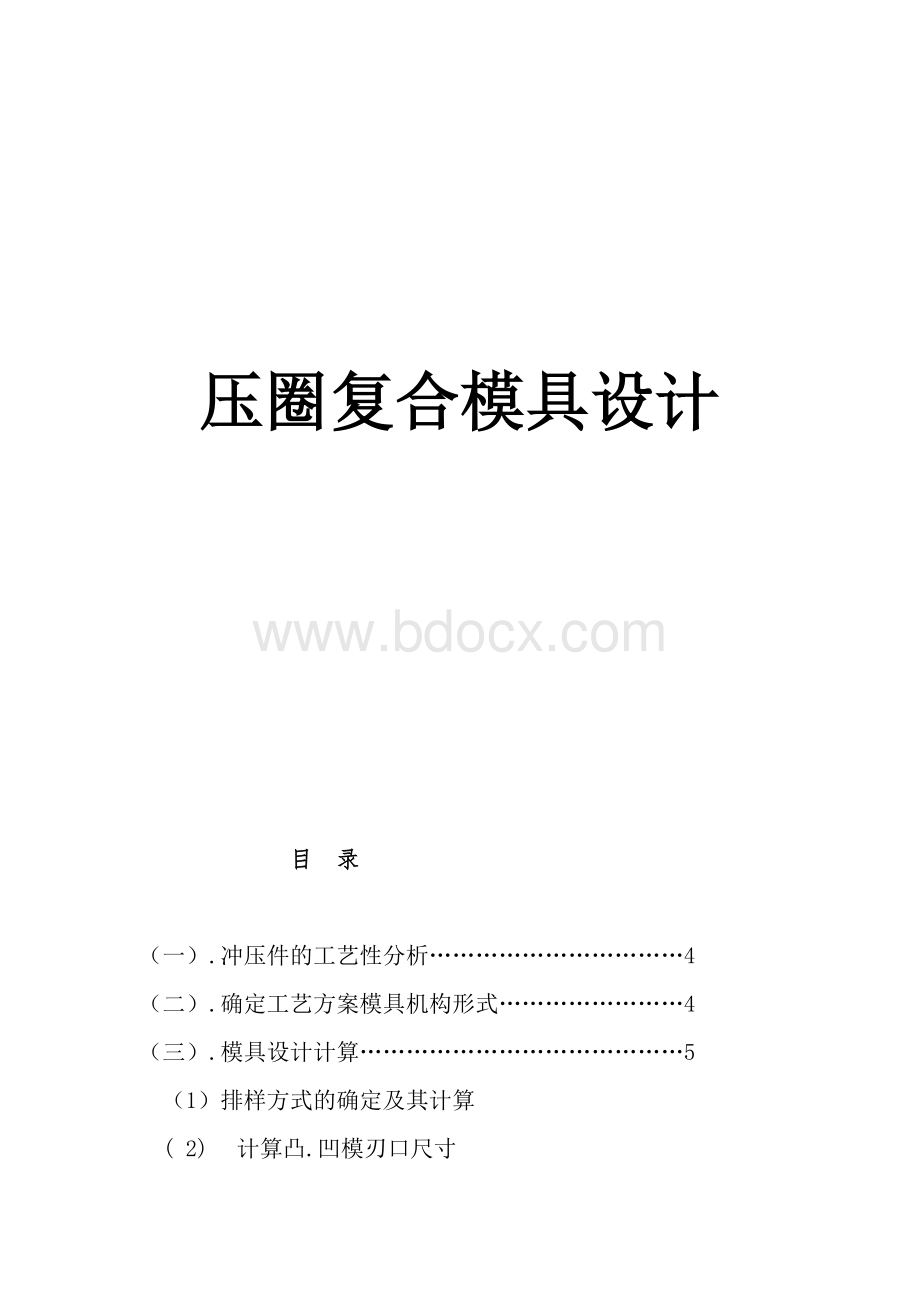
压圈复合模具设计
目录
(一).冲压件的工艺性分析……………………………4
(二).确定工艺方案模具机构形式……………………4
(三).模具设计计算……………………………………5
(1)排样方式的确定及其计算
(2) 计算凸.凹模刃口尺寸
(3)外形落料凸、凹模刃口尺寸的计算
(4)冲压力的计算
(5)压力中心的计算
(四).模具总体设计……………………………………8
(五).模具主要零部件的结构设计……………………9
(1)落料凸、凹模的结构设计
(2)弹性元件的设计计算
(3)模架的设计
(六).冲压设备的选择…………………………………12
(七).绘制模具总装图…………………………………13
(八).拆画零件图………………………………………13
(九).参考文献…………………………………………14
序言
加入WTO后,我国经济将从真正意义上溶入全球经济一体化,中国的市场将不再只属于中国企业。
产品,不仅仅是性能与价格的较量,从外观、实用性到环保,哪一点输给别人那只能堆放在仓库或贱卖,不会创造效益的企业只好关门。
手抄书式的靠机床和操作工来实现工程师设计产品化的老机械制造已成为历史,现代制造业驾驭着微电子和新材料,敲击着键盘,在加工中心与模具组成的流水线上精密的复制着工程师在计算机辅助下设计的从市场捕捉来的最新产品。
进入21世纪,先进制造技术将全面担负起快速、精确的生产更多门类的产品,以保障和提高人类现代化生活的质量。
模具已不仅仅是人类用来浇铸钱币和内燃机壳的砂箱。
今天,它凝聚了各类高技术,能快速精密的直接把材料成型、焊接、装配成零部件、组件或产品,其效率、精度、流线、超微型化、节能、环保,以及产品的性能、外观等,都是传统工艺所无与伦比的。
展望21世纪,无论电子、生物、材料、汽车、家电等哪个行业,不装备由计算机、模具和加工中心砌成的生产线,都不可能在制造业中担纲支柱产业。
模具是现代制造技术的重要装备,其水平标志着一个国家或企业的制造水平和生产能力。
今后一段时期内,我国五大支柱产业的产品质量、批量化成本和包括产业更新在内的技术进步的关键是模具。
现在全球模具总产值早已超过传统机械工业机床与工具类产值的总和。
该零件在汽车,机械,家电,飞机,火车等方面都有广泛的应用。
该零件在生活中到处都可以看到,它具有使两个零件连在一起从而减少之间的磨损。
到处都可以买到,价格便宜,制造简单,方便等。
金属压圈复合模具设计
【摘要】:
本设计进行了落料、冲孔连续模的设计。
文中简要概述了冲压模具目前的发展状况和趋势。
对产品进行了详细工艺分析和工艺方案的确定。
按照冲压模具设计的一般步骤,计算并设计了本套模具上的主要零部件,如:
凸模、凹模、凸模固定板、垫板、凹模固定板、卸料板、导尺、挡料销、导正销等。
模架采用标准模架,选用了合适的冲压设备。
设计中对工作零件和压力机规格均进行了必要的校核计算。
冲孔凹模和落料凹模则采用整体固定板固定。
落料凸模内装有导正销,保证了工件上孔和外形的相对位置准确,提高了加工精度。
如此设计出的结构可确保模具工作运行可靠和冲压产品大批量生产的要求。
关键词:
冲压成型
落料
冲孔
一.冲裁件工艺分析
1、材料:
Q235是普通的碳素钢。
2、工件结构形状:
该零件形状简单、对称,是由圆弧和直线组成的。
3、尺寸精度:
零件图上所有尺寸均未标注公差,属自由尺寸,可按IT14级确定工件尺寸的公差,经查公差表,各尺寸公差为:
φ42-00.62mmφ20+00.52mm22+00.52mm4+00.3mm
结论:
将以上精度与零件的精度要求相比较,该零件的精度要求能够在冲裁加工中得到保证,其他尺寸标注、生产批量等情况,也均符合冲裁的工艺要求,故决定采用冲压方式进行加工。
二.确定工艺方案及模具的结构形状
该工件包括落料、冲孔两个基本工序,可有以下三种工艺方案。
方案一:
先落料,后冲孔。
采用单工序模生产。
方案二:
落料—冲孔复合冲压。
采用复合模生产。
方案三:
冲孔—落料级进冲压。
采用级进模生产。
方案一模具结构简单,但需要两道工序两副模具,成本高而生产效率低,难以满足大批量生产要求。
方案二只需一副模具,工件的精度及生产效率都较高,在模具同一位置时可完成数道分离工序的模具,成本低、操作方便、工件精度也能满足要求。
方案三也只需一道模具,生产效率高,但不在同一个位置就可以完成,操作不方便,精度要求不能满足,成本高。
因此从零件加工精度和经济性角度综合考虑,选则方案二是较为合适的,即选择复合模作为本设计的模具方案。
三.模具设计计算
(1)排样方式的确定及其计算
设计复合模时,首先要设计条料的排样图,因该零件外形为圆形,可采用有废料排样的直排比较合适,确定其排样方式为直排画出排样图。
最小工艺搭边值a=1.5,a1=1.2,分别取a=2,a1=2
条料宽度:
B=(D+2a)-△
B=(42+2*2)-0
B=46mm
步距:
S=42+2=44mm
材料利用率的计算:
计算冲压件毛坯的面积:
A=π×R2=π×212=1384.74mm2
一个步距的材料利用率:
η==1384.74/46×44=68.4﹪
(2)计算总冲压力
F落=Ltτb=(2πR×2×450)N=118.692KN
F冲=Ltτb=(336.9×10π/180+4+2×2.2)×2×450=60.453KN
F推=nK推F孔
查表,得h=6mm则n=h/t=6mm/2=3
K推=0.05
所以,有F推=nK推F孔=3×0.05×60.453=9.068KN
又F卸=K卸F落
查表,得K卸=0.04
所以,有F卸=K卸F落=0.04×118.692=4.748KN
总冲压力为:
F总=F落+F孔+F推+F卸=(118.692+60.453+9.068+4.748)KN=192.961KN
为了保证冲压力足够,一般冲裁时压力机吨位应比计算的冲
F总′=1.3×F总=1.3×192.961=250.8KN
(3)压力中心的计算
由图可知工件上下对称,将工件冲裁周边分成L1、L2、L3、L4、L5基本线段,求出各段长度的重心位置:
因工件相对x轴对称,所以Yc=0,只需计算XC.
L1=2πr=131.88㎜X1=0
L2=58.77mmX2=-0.68
L3=L5=2.2mmX3=X5=10.9㎜
L4=4mmX4=12㎜
将以上数据代入压力中心坐标公式
X=(L1X1+L2X2+…+L5X5)/L1+L2+…+L5
X=[131.88×0+58.77×(-0.68)+2.2×10.9+4×12+2.2×10.9]/(131.88+58.77+2.2+4+22.2)
=0.28mm
(4)凹凸模刃口尺寸的计算
1)冲孔凹凸模刃口尺寸的计算
查表,得间隙值Zmin=0.246mm,Zmax=0.360mm。
由于制件结构简单,精度要求不高,所以采用凹模和凸模分开加工方法制作凸、凹模。
其凸、凹模刃口尺寸计算如下:
查表,得φ20mm凸、凹模制造公差:
δ凸=0.020mmδ凹=0.025mm
校核:
Zmax-Zmin=(0.360-0.246)㎜=0.114mm
而δ凸+δ凹=(0.020+0.025)㎜=0.045mm
满足Zmax-Zmin≥δ凸+δ凹的条件
查表,得:
IT14级时标准公差△=0.52㎜,
因为0.52>0.20,所以磨损系数X=0.5。
按式(2.5)d凸==(20+0.5×0.52)-00.020=mm
D凹===mm
查表,得2.2mm×4mm的矩形凸、凹模制造公差:
δ凸=0.020mmδ凹=0.020mm
δ凸+δ凹=0.020+0.020=0.040mm
满足Zmax-Zmin≥δ凸+δ凹的条件
2)外形落料凸、凹模刃口尺寸的计算
由于外形形状简单,精度要求不高,所以采用凸模和凹模分开加工的方法制作凸、凹模。
查表,得凸、凹模制作公差
δ凸=0.020mmδ凹=0.030mm
校核:
Zmax-Zmin=0.360-0.246=0.114mm
而δT+δA=0.050mm
满足Zmax-Zmin≥δ凸+δ凹的条件
查表,得:
IT14级时磨损系数X=0.5,
d凸==42.26-00.020mm
d凹==42.506+00.030mm
四.模具的总体设计
根据上述分析,本零件的冲压包括冲压和落料两个工序,且孔边距较大,可采用倒装复合模,可直接利用压力机的打杆装置进行推件,卸料可靠,便于操作。
工件留在落料凹模空洞中,应在凹模孔设置推件块,卡于凸凹模上的废料可由卸料板推出;而冲孔废料则可以在下模座中开设通槽,使废料从空洞中落下。
由于在该模具中压料是由落料凸模与卸料板一起配合工作来实现的,所以卸料板还应有压料的作用,应选用弹性卸料板卸下条料。
因是大批量生产,采用手动送料方式,从前往后送料。
因该零件采用的是倒装复合模,所以直接用挡料销和导料销即可。
为确保零件的质量及稳定性,选用导柱、导套导向。
由于该零件导向尺寸较小,且精度要求不是太高,所以宜采用后侧导柱模架。
五.模具主要零部件的结构设计
(1)凸模、凹模、凸凹模的结构设计,包括一下几个方面:
①落料凸、凹模的结构设计
在落料凹模内部,由于要放置推件块,所以凹模刃口应采用直筒形刃口,并查《冲压工艺与模具设计》书中表2.21,取得刃口高度h=6mm,该凹模的结构简单,宜采用整体式。
查《冲压工艺与模具设计》书中表2.22,得k=0.40
即凹模高度H=ks=0.40×42mm=16.8mm
凹模壁厚C=1.5H=1.5×16.8mm=25.2mm
凹模外形尺寸的确定:
凹模外形长度:
L=(42+25.2×2)㎜=92.4㎜
凹模外形宽度:
B=(42+25.2×2)㎜=92.4㎜
凹模整体尺寸标准化,取为100mm×100mm×16mm
凹模的工艺路线
工序号
工序名称
工序内容
1
下料
将毛坯锻成平行六面体。
尺寸为:
155mm×155mm×35mm
2
热处理
退火
3
铣平面
铣各平面,厚度留磨削余量0.8mm,侧面留磨削余量0.5mm
4
磨平面
磨上下平面,留磨削余量0.3~0.4mm磨相邻两侧面,保证垂直
5
钳工划线
划出对称中心线,固定孔及销孔线
6
型空粗加工
在仿铣床上加工型孔,留单边加工余量0.15mm
7
加工余孔
加工固定孔及小孔
8
热处理
淬火回火,保证58~62HRC
9
磨平面
磨上下面及基准面达要求
10
型孔精加工
在坐标磨床上磨型孔,留研磨余量0.01mm
11
研磨型孔
钳工研磨型孔达规定技术要求
②冲孔凸模的设计
为了增加凸模的强度与刚度,凸模固定板厚度取24mm,因凸模比较长,所以选用带肩的台阶式凸模,凸模长度根据结构上需要来确定。
L=h凸模固定板+h落料凹模=(24+16.8)mm=40.8mm(取40mm)
③凸凹模的结构设计
本