数控机床的结构特点.docx
《数控机床的结构特点.docx》由会员分享,可在线阅读,更多相关《数控机床的结构特点.docx(20页珍藏版)》请在冰豆网上搜索。
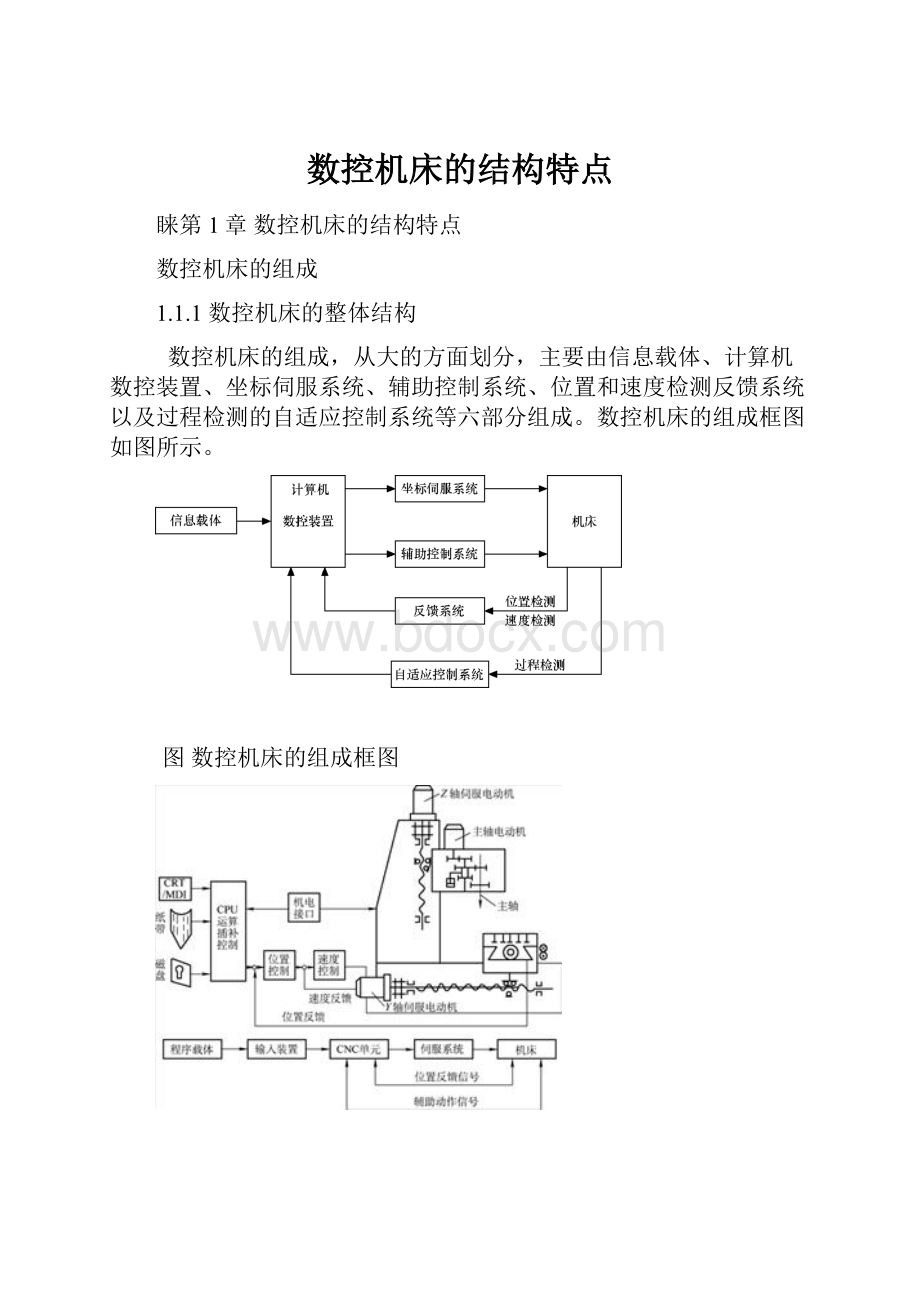
数控机床的结构特点
睐第1章数控机床的结构特点
数控机床的组成
1.1.1数控机床的整体结构
数控机床的组成,从大的方面划分,主要由信息载体、计算机数控装置、坐标伺服系统、辅助控制系统、位置和速度检测反馈系统以及过程检测的自适应控制系统等六部分组成。
数控机床的组成框图如图所示。
图数控机床的组成框图
图1-5 数控机床的组成及框图
1.信息载体
它是把加工零件通过建立数学模型及数学处理后,按规范编制成工艺流程,形成程序文件,然后通过计算机存储到软盘或磁盘上,再将软盘或磁盘的程序输送到数控系统中。
或者通过键盘将加工程序输送到数控系统中,也可通过DNC接口用通用计算机直接将加工程序输送到数控系统中。
这些软盘、磁盘、键盘或通用计算机就是信息载体。
我们把可用不同形式将零件的加工程序记录在上面,并可传输给数控装置的这种载体称为信息载体,也可称为控制介质。
在早期的数控机床上,常用纸带、穿孔卡片、磁带等作为信息载体。
2.计算机数控装置
加工程序由输入装置传送到数控系统中后,经过中央处理单元、运算器、存储器、控制器等,又通过数控系统软件、机床参数等的支持,再经过输出装置,分配到坐标伺服系统和辅助控制系统中去。
同时又将坐标伺服系统中的位置检测信号、速度检测信号和自适应控制的温度、转矩、振动、摩擦、切削力及液压、气压、中心润滑等系统的压力多因素变化过程检测的反馈信息,经与给定值和最佳参数反复比较、处理后,再输出给坐标伺服系统和辅助控制系统。
这里的输入/输出装置、中央处理单元(CPU)、运算器、存储器和控制器等组成的装置称为计算机数控装置。
3.坐标伺服系统
由伺服控制电路、功率放大器、交流伺服电机或线性电机、位置和速度检测装置等组成,将数控装置发出的脉冲信号转换成机床的各坐标运动,这种系统称为坐标伺服系统。
坐标伺服系统中的位置检测装置和速度检测装置,对坐标运行的直线位置、角向位置的准确性和直线运行速度、角向回转速度进行检测、修正。
其中包括主轴转换成伺服坐标的角向位置检测和回转运行的速度检测。
坐标伺服系统中的坐标运行位置精度和运行速度将直接影响数控机床的加工精度和生产效率。
4.辅助控制装置
辅助控制装置的作用,就是通过接收数控装置发出的辅助控制指令,经输入/输出接口电路转换成强电(动力能源)信号,用来控制机床主轴的启动、停止,主轴的无级调速,机械手、刀库、换刀的动作,刀塔的动作,尾座的动作,工作台的交换、定位、夹紧,冷却液装置的动作,排屑器的动作,液压装置的动作,气压装置的动作及中心润滑装置的动作等。
辅助控制装置用辅助指令来控制数控机床各开关量,能使机床在运行过程中形成一套完整或较完整的逻辑工作状态。
数控机床由数控装置、伺服驱动装置、检测反馈装置、和机床本体四大部分组成。
1.1.2计算机数控系统(简称CNC)的组成
计算机数控系统(CNC)主要由微型计算机、外围设备和机床控制装置三大部分组成。
1.微型计算机
微型计算机是CNC系统的核心,是CNC的主体设备,是软件得以施展、完成各项控制功能的硬件保证。
它主要由微处理器(CPU)、存储器和接口电路组成。
图CNC系统的组成框图
CPU由运算器和控制器组成,任务完成对数控系统的运算和管理。
存储器用于存储系统软件和加工程序,在EPROM中存放系统程序,在RAM中存放零件加工程序。
输入/输出(I/O)接口电路完成CPU与机床和外围设备的联系。
2.外围设备
外围设备(简称外设)由操作面板、键盘、显示器、磁盘驱动器、可编程控制器(PLC机)以及外部存储器等组成。
这些外围设备通过I/O接口与计算机相连,形成了计算机与外围设备的双向通信,同时在计算机的统一指挥下对机床各部分进行控制。
操作面板分两大部分,一部分用来安装操作计算机及数控装置的各按键、按钮开关和标准计算机键盘、固定鼠标。
另一部分用来安装操纵机床的各种控制开关、按键、手摇脉冲发生器、机床工作状态指示器、各种信号灯。
键盘输入各种操作指令,工件的加工程序用手动方式(MDI)直接输入到数控系统中存储起来,还可控制数控机床操作。
显示器用来显示CNC系统的相关信息。
软盘驱动器将软盘上存储的加工工件程序通过软盘驱动器输入到数控系统的存储器中存储起来。
可编程控制器对数控机床的顺序动作进行逻辑控制,并分为内置和外置两种。
3.机床控制装置
CNC系统是通过对伺服系统的机构进行控制,来实现对各线性坐标和旋转坐标的直线位置、角向位置的坐标运动速度控制的。
为了提高这些线性坐标和旋转坐标的位置精度和运行速度的准确性,常常采用半闭环和闭环伺服检测系统来检测机床坐标运行的实际位置,用测速电机来检测伺服电机的速度,以提高控制精度。
因此,在机床坐标位置和速度控制中要具有位置反馈和速度反馈系统。
机床逻辑状态检测输入接口电路,用于输入机床上安装的与自适应控制相关的传感元器件和液压、气压、检测元件的输出信号。
机床逻辑状态控制输出接口电路,用于控制机床的各开关量,包括各辅助装置的开关量。
位置控制一般是指控制机床的位移轴的移动位置,比如CNC发出指令,控制轴通过伺服电机,传动装置等移动到指定位置,通过位置检测装置(编码器或者光栅)反馈回CNC,是否准确到达,同时进行位置的补正。
就是CNC通过指令让它能控制移动的东西移动到了它要求的地方,同时检查实际到了没有。
1.1.3主机的组成
主机即数控机床的机床部分。
当主轴驱动系统和坐标伺服系统接收到计算机系统发出的动作信号以后,开始驱动机床的主轴、工作台和刀具去定位或按程序中所指定的轨迹进行动作,并配以必要的机械、液压、气压、冷却液、中心润滑等动作,按照要求的形状和尺寸去完成零件的切削加工。
图数控机床主机的组成框图
1.主传动系统
数控机床的主传动方式有以下三种。
①在大、中型数控机床上常采用变速齿轮的传动方式,这样可以加大主轴的输出扭矩,以满足主轴低速旋转时对大输出扭矩特性的要求。
②在小型数控机床和部分数控机床上采用同步齿形带作为主传动,用这种传动方式可以减少主传动的振动和噪声。
但是,它的输出扭矩要比齿轮传动时的输出扭矩小得多。
③这些年来,在许多数控机床上开始大量使用电主轴,即数控机床的主轴直接与交流调速电机的转子刚性连接,使主轴与电机成为一个整体。
这样大大简化了主轴箱体与主轴结构,有效地提高了主轴部件的刚度。
1.带有变速齿轮的主传动
这是大、种型数控机床采用较多的一种方式。
通过少数几对齿轮减速,扩大了输出扭矩,以满足主轴对输出扭矩特性的要求。
一部分小型数控机床业采用此种传动方式,以获得强力切屑时所需要的扭矩。
滑移齿轮的移位大都采用液压拨叉或直接由液压油缸带动齿轮实现。
2.通过皮带传动的主传动
这主要应用在小型数控机床上,可以避免齿轮传动是引起的振动与噪声。
但它只能使用与要求的扭矩特性的主轴。
3.由调速电机直接驱动的主传动
这种主传动方式大大简化了主轴箱体与主轴的结构,有效地提高了主轴部件的刚度。
但主轴输出扭矩小,电机发热对主轴的精度影响较大。
2.坐标进给系统
数控机床闭环控制的进给系统,通常由位置比较放大单元、驱动单元、机械传动装置及位置检测元件(目前大多采用光栅尺)等几部分组成。
图所示为数控机床闭环控制进给系统的组成框图。
图数控机床闭环控制进给系统的组成框图
1.开环进给伺服系统中没有测量装置。
数控装置根据程序所要求的进给速度,方向和位移量输出一定频率和数量的进给指令脉冲,经驱动电路放大后,每一个进给指令脉冲驱动功率步进电机旋转一个步距角。
经减速齿轮、丝杆螺母付转化成工作台的当量直线位移。
如果工作台的实际位移增多或减少数控装置将不予理会,不会补发指令脉冲加以补偿。
2.闭环进给伺服系统,数控装置将位移指令与位置检测装置(如光栅尺、直线感应同步器等)测得的实际位置反馈信号,随时进行比较。
根据其差值与指令进给位移的要求,按照一定的规律转换后,随时对驱动电机的转速进行校正。
使得工作台的实际位移量与指令位移量相一致。
3.半闭环控系统机床,将位置检测装置安装在驱动电机的端部或是丝杆的端部,虽然没有直接测量出工作台的实际位移,但通过间接测量高精度丝杆的角速度,或驱动电机的角速度从而得到工作台的实际位置。
最后对工作台的实际位移量进行补偿。
3.工作台
工作台可以是固定在某一个加工区间的位置上,也可以是在这个加工区间的位置上作回转运动,还可以作为一台数控机床的附件,安装在固定工作台上,在有些加工中心上,工作台可以进行交换,可以是两个工作台进行交换,也可以是多个工作台进行交换,如此成为柔性(适应新产品变化的能力)制造单元的一个组成部分。
4.换刀装置和刀塔
(1)换刀装置
换刀装置由机械手、刀库、主轴定向机构和主轴拉刀机构组成。
在有些加工中心的换刀装置上只有刀库和主轴换刀机构,省去了机械手。
机械手作为刀库与主轴之间取刀、放刀的装置,起着传递作用。
在没有机械手的加工中心上,是由刀库和主轴的相互配合完成换刀动作的。
刀库的形式一般有鼓轮式(或称斗笠式)、链式和箱体式等几种,也是目前加工中心上常用的几种形式。
机械手在刀库上准确选刀,往往采取刀具编号方式、刀座编号方式和计算机记忆方式。
1.换刀过程
(1)装刀:
刀具装入刀库
任选刀座装刀方式。
刀具安置在任意的刀座内,需将该刀具所在刀座号记下来。
固定刀座装刀方式。
刀具安置在设定的刀座内。
(2)选刀
从刀库中选出指定刀具的操作。
1)顺序选刀:
选刀方式要求按工艺过程的顺序(即刀具使用顺序)将刀具安置在刀座中,使用时按刀具的安置顺序逐一取用,用后放回原刀座中。
2)随意选刀:
①刀具编码方式采用刀套的锥柄和锥柄的尾部编码两种方式
②刀座编码选刀:
对刀库各刀座编码,把与刀座编码对应的刀具一一放入指定的刀座中,编程时用地址T指出刀具所在刀座编码。
③计算机记忆选刀
刀具号和存刀位置或刀座号对应地记忆在计算机的存储器或可编程控制器的存储器内,刀具存放地址改变,计算机记忆也随之改变。
在刀库装有位置检测装置,刀具可以任意取出,任意送回。
(3)换刀
1)主轴上的刀具和刀库中的待换刀具都是任选刀座。
刀库→选刀→到换刀位→机械手取出刀具→装入主轴,同时将主轴取下的刀具装入待换刀具的刀座。
2)主轴上的刀具放在固定的刀座中,待换刀具是任选刀座或固定刀座。
选刀过程同上,换刀时从主轴取下刀具送回刀库时,刀库应事先转动到接收主轴刀具的位置。
3)主轴上的刀具是任选刀座,待换刀具是固定刀座。
选刀同上,从主轴取下的刀具送到最近的一个空刀位。
8421的编码方式4个位置分别代表数字8、4、2、1见下表
(2)刀塔
刀塔(又称刀架)是数控车床或车削中心上的重要部件,是在车削过程中,为满足车削工艺的需要进行自动换刀的装置。
在车削中心的刀塔上还可安装若干个动力装置,以便在车削的同时,又可完成铣削和钻削工序。
常用的刀塔可分为六工位、八工位、十二工位等形式。
刀塔上的动力刀具是由交流伺服电机进行驱动的。
它通过同步齿形皮带、传动轴、齿轮、离合器等将动力传递到动力刀夹,再通过刀夹内部的齿轮传动,刀具可旋转,实现动力刀具的主动切削。
5.液压系统
数控机床的液压系统,常用来控制主轴的拉刀机构、主轴箱或工作台的平衡装置、主轴的立、卧转换装置,对具有齿轮调速装置的主传动机构进行速度变挡。
液压系统还对工作台的夹紧、工作台的交换、机械手的动作、刀库的动作、机械定向机构等进行控制。
在数控车床上,三爪卡盘的夹紧与放松、高压夹紧(加工普通零件采用较大夹紧力)与低压夹紧(加工薄壁零件采用较小夹紧力)之间的转换;回转刀盘的松开与夹紧、刀盘的转位选刀;尾架套筒的伸缩等辅助加工动作,均是机床自动完成的,无需操作者参与。
一些数控机床主运动传动系统带有齿轮变速机构,其滑移齿轮的移位大都采用液压拨叉或直接由液压缸带动滑移齿轮变换啮合位置,实现主轴自动变速。
在加工中心的刀具自动交换装置中,盘式刀库刀盘的抬起→转位选刀→定位;链式刀库的移动;主轴夹紧与松开刀具、机械手的抓刀与插刀、机械手转位等换刀动作,都是按顺序自动完成的。
图液压系统控制框图
6.气动系统
数控机床的气动系统常用来控制机械手的动作、刀库的动作、交换工作台的动作;对有些数控车床来说,还完成主轴卡盘的夹紧、尾顶尖的动作;在有些数控坐标磨床上,气动系统还控制砂轮的高速运转,因为砂轮的高速运转是由气动轴承完成的。
气动系统还对主轴锥孔进行吹气清洁,对各坐标的光栅尺进行吹气清洁。
气动系统也用于润滑系统中的喷雾润滑、冷却液系统的高压冷却等。
加工中心气动系统的设计与加工中心的类型、结构、要求完成的功能等有关。
结合气压传动的特点,一般在要求力或力矩不太大的情况下采用气压传动。
图气动系统控制框图
7.润滑系统
润滑系统分中心润滑系统和齿轮箱润滑两部分。
中心润滑系统是由计算机通过辅助控制装置进行控制的,主要对主轴轴承、各坐标轴承、导轨、滚珠丝杠螺母副、机械手、刀库以及所有滑动、滚动面等部位润滑。
图中心润滑系统润滑部位框图
8.冷却液系统
冷却液系统是由计算机通过辅助控制装置进行控制的,主要是在切削时对刀具和工件进行冷却。
同时,冷却液还可由高压系统经过主轴中心,再经刀柄的中心、刀具的中心对深孔加工进行有效的冷却。
这种冷却方式往往用于加工中心、数控钻床的钻削加工。
冷却液系统的工作部位框图如图所示。
图冷却液系统的工作部位框图
在一些大中型的数控机床上,冷却液还作为清洁装置对工件、工作台、坐标轴、防护罩及工作室内表面进行冲洗清洁。
这样也可以有效地将切削热量由冷却液及时带走,减少机床和工件的热变形。
在有些数控机床上还利用冷却液经过滤后对主轴进行内冷,这种情况大多用在电主轴上。
9.制冷系统
制冷系统是由计算机通过辅助控制装置进行控制的,主要用于对液压系统的液压油进行冷却,或者对用于主轴的冷却液进行冷却。
制冷系统的工作部位框图如图所示。
在有些数控机床上,将被冷却过的液压油、冷却液或水通过电器柜,用风扇将冷气吹进电器柜内,达到使电器柜内的控制单元或模块、电源等散发热量的目的。
这些数控机床的电器柜、液压油或冷却液都是用压缩机进行制冷的。
图制冷系统的工作部位框图
10.自动排屑装置
自动排屑装置(又称排屑器)也是由计算机通过辅助控制装置进行控制的,主要用来排出机床在加工过程中的切屑。
排屑分为自动定时排屑和手动不定时排屑两种方式。
所谓定时自动排屑,即在加工过程中事先设定将排屑指令编入到程序中,使其定时排屑。
所谓手动不定时排屑,即在加工过程中不定时地由操作人员根据排屑情况进行手工操作(MDI方式下)计时排屑。
排屑器有链式、板式、螺旋式等几种结构形式。
数控机床的结构及特点
1.2.1加工中心的结构和特点
加工中心即多工序加工机床,它可通过一次装夹,按工步要求一次完成铣削、钻削、镗孔、铰孔、攻丝和轮廓等工序的加工。
现以比较典型的宁江机床厂生产的THM(精密)6350卧式可交换工作台加工中心为例,分析其结构和特点。
1.性能
THM6350卧式加工中心的主体结构如图所示。
该机床为双工位四轴三联动或四轴四联动卧式可交换工作台加工中心。
刀库容量为32把或60把ISO40型刀具。
机电一体化布局,全封闭罩壳结构,采用直线滚动导轨,运动平稳、灵活、刚性好、承载能力强、使用寿命长。
线性坐标的定位精度可达0.008mm,重复定位精度可达0.004mm。
回转坐标的连续分度定位精度可达10角秒(角度单位,1度=60′=3600″角秒),重复定位精度可达角秒。
主轴采用高精度轴承,并设有主轴锥孔清洁吹气装置。
机械手为凸轮式单臂双爪随机交换方式,可满足15kg以下刀具的交换,换刀时间为。
选用FANUC0M控制系统(日本法兰克)或FAGOR8055M控制系统(西班牙法格),具有X、Y、Z、B四个坐标轴。
坐标采用交流伺服电机和光栅尺闭环监测系统;主轴驱动采用交流驱动或电主轴交流驱动;具有工件检测功能和刀具检测功能,可对工件位置尺寸和工具的磨损或破损情况进行检测,实现刀具的寿命管理;机床操作面板按人机工程要求设计;控制系统配有RS232通信接口,可实现DNC(群控)连网功能。
机床配有双工位或六工位可自动交换工作台,工件装卸方便、操作简单、节约工件和工装装夹时间,进一步提高了生产效率。
2.结构特点
THM6350加工中心的主机主要由机床床体、可交换工作台、机械手换刀系统、刀库、主轴拉刀机构、排屑器、液压系统、气动系统、冷却液系统和中心润滑系统等组成。
CNC系统主要由微型计算机、坐标伺服系统、主轴驱动系统、辅助控制装置、I/O接口电路等组成。
图THM6350加工中心外形
机床的传动系统如图所示。
传动系统主要分为坐标轴的伺服进给驱动系统和回转坐标轴的分度系统。
另外,还有双工位工作台的交换系统、刀库分度系统和机械手传动系统。
(1)主轴系统的结构特点
如图所示,主传动系统是由交流主轴驱动电机通过一对圆弧齿轮13、15与圆弧同步齿形带14直接驱动主轴旋转。
主轴的定向是由交流主轴电机所带编码器来实现的。
主轴转速可在80~8000r/min范围内进行无级调速。
主轴箱安装在双立柱的框架之间,由直线滚动导轨、滚珠丝杠副实现主轴箱(y坐标)的上下运动。
y轴的伺服电机带有失电制动器,作为断点刹车用,以免主轴箱下滑。
主轴交流调速电机和主轴的拉刀机构安装在主轴箱后部。
主轴箱采用平衡油缸和蓄能器等组成的液压平衡装置来完成主轴箱上下运行时的平衡,以提高y坐标轴的运动精度,同时要减轻y轴交流伺服电机的负载。
主轴组件(如图所示)由主轴2、主轴前支承轴承组4、主轴后支承轴承组22、主轴卸荷装置24、主轴拉刀装置23和主轴支承套7等零部件组成。
主轴的拉刀机构由蝶形弹簧29组成,通过拉杆32、拉杆前端的钢球拉爪6将刀柄拉钉5夹紧在主轴锥孔内,夹紧力约6000~6400N,拉刀夹紧力的大小是由主轴后端螺母16调节的。
主轴松刀是由装在主轴组后端的液压油缸19向前推动主轴拉
杆实现刀具的松开。
主轴拉杆松刀顶出的位置是通过液压油缸的外螺纹调节,并由锁紧螺母21锁紧,主轴刀具的夹紧、松开位置是由两个无触点开关发讯的。
主轴锥孔的清洁是由气动系统通过气管23从主轴拉杆中心孔吹入主轴锥孔的。
主轴刀具冷却是由冷却系统通过主轴支承套上的四路冷却孔9送入主轴前端的冷却喷嘴3对刀具进行冷却的。
(2)直线坐标的结构特点
如图所示,x、y、z三个直线坐标的运行分别由三个交流坐标伺服电机通过弹性联轴器12、17和2分别与滚珠丝杠副4、10和16连接,来驱动这三个直线坐标的位移。
这三个坐标全部采用闭环检测伺服系统。
x、y、z坐标轴的传动结构如图所示。
三个直线坐标轴均采用交流伺服电机通过弹性联轴节3,对滚珠丝杠9进行直接驱动,这种结构传动简单、可靠,传动效率高。
三个坐标轴的滚珠丝杠均采用两端固定,并进行丝杠预拉伸的结构。
轴承值为60°角接触,重预加负荷的成组轴承。
螺母4用于压紧左边支承轴承组,螺母15用于对丝杠进行预拉伸,并通过螺母10将右边支承轴承组固定。
(3)回转坐标B轴的结构特点
如图所示,回转坐标B轴为周围连续分度系统,此时b坐标的运行是由交流伺服电机通过一对圆弧齿轮23、25与圆弧同步齿形带24再与联轴器26相连,然后又与蜗杆、蜗轮27相连,实现旋转工作台b轴的连续分度。
如图所示,回转连续分度工作台安装在B坐标轴的大轴承1上,b轴轴承安装在右滑台上,其回转工作台的精度主要取决于B轴轴系的精度,工作台的分度定位精度和重复定位精度由安装在B轴轴系下的圆光栅尺来检测。
回转分度工作台周围有四个浮动式液压夹紧油缸2,用于B轴分度后的夹紧,以承受工作台的切削扭矩负荷。
(4)双工位工作台托板交换装置的结构特点
双工位工作台的托板交换传动系统如图所示,它是由托板交换装置中的升降油缸同时将双工位工作台的托板抬起,使两托板与锥形定位销6脱开,再由托板交换装置中的回转油缸将两托板交换装置回转180°,使两托板交换,最后托板交换装置中的升降油缸落下到位,实现了工作台两托板的自动交换。
双工位托板交换装置提供了一个手动装卸工位,如图所示。
托板交换后,一个托板放置在回转工作台上,并在加工区进行加工;另一个托板放置在手动装卸工位上,用于工件的装卸。
装卸工位是一个可回转360°的托架,以便工件的装卸。
在装卸工件和调整工件的同时,机床可加工另一个工件,这样既可以进一步提高机床的效率,又可以方便、安全地进行工件或夹具的装卸工作。
(5)自动换刀系统的结构特点
①刀库
②机械手
T1T2
两位五通:
换向、两种回油方式。
1.2.2数控车床的结构及特点
下面以卧式数控车床为例(以下简称数控车床),分析其结构和特点。
1.性能
数控车床具有x坐标和z坐标二联动功能,并配备有多工位的转塔刀架,实现加工过程的自动换刀。
导轨有滑动导轨和滚动导轨两种形式,再配备上滚珠丝杠副可提高机床坐标轴的位置精度,从而提高零件的加工精度。
主轴卡盘可实现加工零件的自动装夹,并可根据需要调整夹紧力。
尾座的运动分两种方式:
一种为人工调整其与主轴或被加工零件的距离;另一种是用手动操作或编程的方法移动尾座到所需要的距离。
尾顶尖伸出的距离可由在MDI方式下操作脚踏开关来控制。
目前,数控车床的CNC系统大都选用FANUCOTD(日本法兰克)系列、SIMENS810TD(德国西门子)系列、SINUMERIK840DT(德国西门子)系列和FAGOR8025T(西班牙法格)系列等。
坐标采用交流伺服电机和光栅尺闭环检测系统,或编码器半闭环检测系统。
主轴驱动采用交流驱动或电主轴交流驱动。
机床操作面板达到人机工程的要求。
控制系统配有RS232通信接口,可实现DNC连网功能。
2.结构特点
数控车床主要由机床床体、主轴装置、刀塔、尾座、x和z坐标传动装置、排屑器以及液压系统、气动系统、冷却液系统和中心润滑系统等组成。
CNC系统主要由微型计算机、坐标伺服系统、主轴驱动系统、辅助控制装置及I/O接口电路等组成。
典型的数控车床的传动系统如图所示。
传动系统主要分主传动系统和坐标传动系统两部分。
数控车床大都采用45°和30°两种斜床身,以便达到足够的刚性和热稳定性。
45度斜床身这种结构的机床,起码有二个优点:
1:
加工精度高。
数控机床的拖板传动丝杆都是高精度的滚珠丝杆,丝杆与螺母之间的传动间隙很小,但也不是说没有间隙,而只要有间隙,当丝杆向着一个方向运动后再反向传动时,难免会产生反向间隙,有反向间隙就会影响加工精度,而这种45度床身的机床由于有重力的作用,重力直接作用于丝杆的轴向,传动时的反向间隙几乎为零。
如果你还不明白,你可以找一个普通螺母与螺丝,竖直向上,拧动螺丝,再反向退回,就会明白螺母始终往一边压着丝杆,所以就不会有反向间隙,假如让螺母与螺丝平放,就不会有这种效果了。
2:
机床刚性好,切削时不易引起振动。
因为这种机床的刀具是在工件的斜上方切削,切削力与主轴工件产生的重力相一致,所以主轴运转相对平稳,不易引起切削振动,而普通数控车床在切削时,刀具与工件产生的切削力是向上的,与主轴工件产生的重力不一致,所以就容易引起振动。
3:
铁屑由于重力的关系不易产生緾绕刀具,利于排屑。
3.液压系统的原理特点
图所示为某进口数控车床主轴卡盘夹紧、放松的液压原理图。
主轴卡盘夹紧、放松液压油路由一个三位四通电磁换向阀1来控制油缸6,以达到主轴卡盘的夹紧和放松。
当液压油通过可调节5~40bar(巴1MPa=10bar巴)压力的减压阀2和压力表3后,经过三位四通电磁换向阀(左边吸合工作),液压油进入卡盘夹紧、放松油缸的右腔,推动活塞向左