塑料模具课程设计1.docx
《塑料模具课程设计1.docx》由会员分享,可在线阅读,更多相关《塑料模具课程设计1.docx(25页珍藏版)》请在冰豆网上搜索。
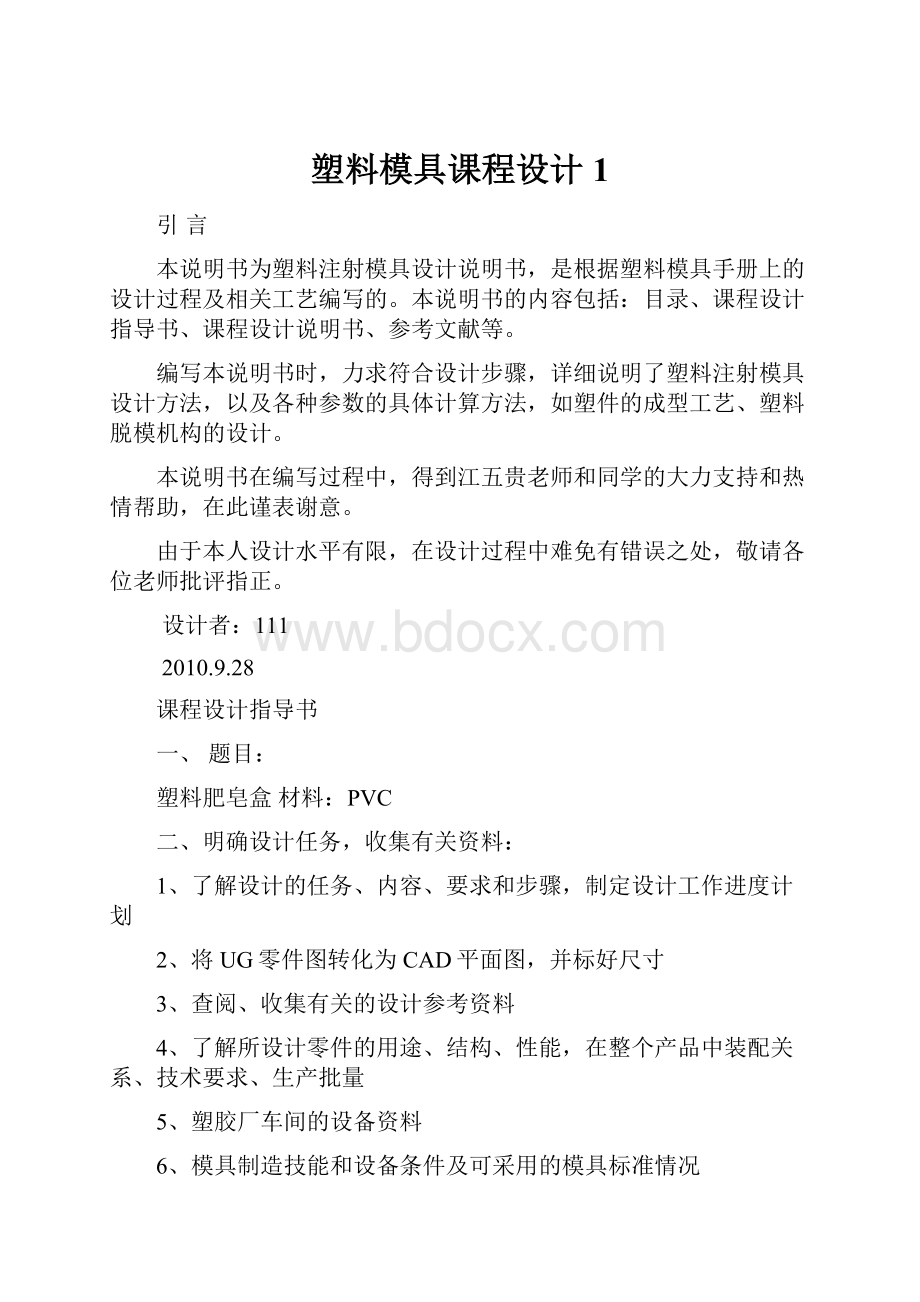
塑料模具课程设计1
引言
本说明书为塑料注射模具设计说明书,是根据塑料模具手册上的设计过程及相关工艺编写的。
本说明书的内容包括:
目录、课程设计指导书、课程设计说明书、参考文献等。
编写本说明书时,力求符合设计步骤,详细说明了塑料注射模具设计方法,以及各种参数的具体计算方法,如塑件的成型工艺、塑料脱模机构的设计。
本说明书在编写过程中,得到江五贵老师和同学的大力支持和热情帮助,在此谨表谢意。
由于本人设计水平有限,在设计过程中难免有错误之处,敬请各位老师批评指正。
设计者:
111
2010.9.28
课程设计指导书
一、题目:
塑料肥皂盒材料:
PVC
二、明确设计任务,收集有关资料:
1、了解设计的任务、内容、要求和步骤,制定设计工作进度计划
2、将UG零件图转化为CAD平面图,并标好尺寸
3、查阅、收集有关的设计参考资料
4、了解所设计零件的用途、结构、性能,在整个产品中装配关系、技术要求、生产批量
5、塑胶厂车间的设备资料
6、模具制造技能和设备条件及可采用的模具标准情况
三、工艺性分析
分析塑胶件的工艺性包括技术和经济两方面,在技术方面,根据产品图纸,只要分析塑胶件的形状特点、尺寸大小、尺寸标注方法、精度要求、表面质量和材料性能等因素,是否符合模塑工艺要求;在经济方面,主要根据塑胶件的生产批量分析产品成本,阐明采用注射生产可取得的经济效益。
1、塑胶件的形状和尺寸:
塑胶件的形状和尺寸不同,对模塑工艺要求也不同。
2、塑胶件的尺寸精度和外观要求:
塑胶件的尺寸精度和外观要求和模塑工艺方法、模具结构型式及制造精度等有关。
3、生产批量
生产批量的大小,直接影响模具的结构型式,一般大批量生产时,可选用一模多腔来提高生产率;小批量生产时,可采用单型腔模具等进行生产来降低模具的制造费用。
4、其它方面
在对塑胶件进行工艺分析时,除了考虑上诉因素外,还应分析塑胶件的厚度、塑料成型性能及模塑生产常见的制品缺陷问题对模塑工艺的影响。
四、确定成型方案及模具型式:
根据对塑胶零件的形状、尺寸、精度及表面质量要求的分析结果,确定所需的,模塑成型方案,制品的后加工、分型面的选择、型腔的数目和排列、成型零件的结构、浇注系统等。
五、工艺计算和设计
1、注射量计算:
涉及到选择注射机的规格型号,一般应先进行计算。
对于形状复杂不规则的制品,可以利用UG的“分析/质量属性”来计算质量。
或者采用估算估计塑料的用量,及保证足够的塑料用量为原则。
2、浇注系统设计计算:
这是设计注射模的第一步,只有完成注系统的设计后才能估算型腔压力、注射时间、校核锁模力,从而进一步校核所选择的注射机是否符合要求。
浇注系统设计计算包括浇道布置、主流道和分流道断面尺寸计算、浇注系统压力降计算和型腔压力校核。
3、成型零件工作尺寸计算:
主要有凹模和型芯径向尺寸高度尺寸,其最大值直接关系到模具尺寸大小,而工作尺寸的精度则直接影响到制品精度。
为计算方便,凡孔类尺寸均及其最小尺寸作为公称尺寸,凡轴类尺寸均及最大尺寸作为公称尺寸;进行工作尺寸计算时应考虑塑料的收缩率和模具寿命等因素。
4、模具冷却和加热系统计算:
冷却系统计算包括冷却时间和冷却参数计算。
冷却参数包括冷却面积、冷却水空长度和孔数的计算及冷却水流动状态的校核和冷却水入口和出口处温差的校核。
模具加热工艺计算主要是加热功率计算。
5、注射压力、锁模力和安装尺寸校核:
模具初步设计完成后,还需校核所选择的注射机注射压力和锁模力能否满足塑料成型要求,校核模具外形尺寸可否方便安装,行程是否满足模塑成型及取件要求。
六、进行模具结构设计:
1、确定凹模尺寸:
先计算凹模厚度,再根据厚度确定凹模周界尺寸,在确定凹模周界尺寸时要注意:
第一,浇注系统的布置,特别是对于一模多腔的塑料模应仔细考虑模腔位置和浇道布置;第二,要考虑凹模上螺孔的布置位置;第三,主流道中心和模板的几何中心应重合;第四,凹模外形尺寸尽量按国家标准选取。
2、选择模架并确定其他模具零件的主要参数;在确定模架结构形式和定模、动模板的尺寸后,可根据定模、动模板的尺寸,从《塑料模国家标准》GB/T12555-1990和GB/T12556-1990中确定模架规格。
待模架规格确定后即可确定主要塑模零件的规格参数。
再查阅有关零件图表,就可以画装配图了。
七、画装配图
一般先画上主视图,再画侧视图和其他视图。
由于注射机大多为卧式的,故注射模也常按安装位置画成卧式,画主视图最好从分型面开始向左右两个方向画比较方便。
1、主视图:
绘制模具工作位置的剖面图
2、侧视图:
一般情况下绘制定模部分视图
3、俯视图、局部剖视图等
4、列出零件明细表,注明材质和数量,凡标准件须注明规格
5、技术要求及说明,包括所选注射机设备型号,所选用的标准模架型号,模具闭合高度,模具间隙及其它要求。
八、绘制各非标准零件图
零件图上应注明全部尺寸、公差和配合、行位公差、表面粗糙度、所用材料、热处理方法及其它要求
九、编写技术文件
1、编写注射成型工艺卡片:
根据塑料的成型特点,查阅有关资料,确定合理的注射成型工艺参数,并作成工艺卡片。
2、编写加工工艺过程卡片:
选取两个重要模具成型零件,确定加工工艺路线,并作成加工工艺过程卡片
3、编写设计说明书
第一部分产品的说明
第二部分塑件分析
第三部分注射机的型号和规格选择及校核
第四部分型腔的数目决定及排布
第五部分分型面的选择
第六部分浇注系统的设计
第七部分成型零件的工作尺寸计算及结构形式
第八部分导柱导向机构的设置
第九部分推出机构的设计
第十部分温度调节系统的设置
第十一部分模具的动作过程
第十二部分设计小结
第十三部分参考资料
第一部分产品的说明
肥皂盒是日常用品,几乎家家户户都有,商店里出售的肥皂盒也是各式各样,丰富多彩,有很特别的设计以赢得消费者的喜爱。
此次设计的是肥皂盒底座,结构比较简单,但考虑的是其实用性。
为了防止香皂遇水软化,将底座设计成了中间凸起的曲面,并在底座水平放置面处开了漏水孔。
为了防止使用香皂后手滑,特别将肥皂盒侧面设计成了内凹的曲面。
此次产品是在UG6.0的辅助下完成的。
产品图如下:
图一零件实体图
第二部分塑件的分析
PVC塑料
化学名称:
聚氯乙烯
比重:
1.38克/立方厘米成型收缩率:
0.6-1.5%
产品需要预热到70~90度,预热时间为4~6小时
成型温度:
230~330℃成型时间为40~130秒
成型特性:
1.无定形料,吸湿性小,但为了提高流动性,防止发生气泡则宜先干燥。
2、流动性差,极易分解,特别在高温下和钢、铜金属接触更易分解,分解温度为200°C.分解时有腐蚀及刺激性气体
3、成型温度范围小,必须严格控制料温
4、用螺杆式注射机及直通喷嘴,孔径易大,以防死角滞料,滞料必须及时处理清除
5、模具浇注系统应粗短,浇口截面宜大,不得有死角滞料,模具应冷却,其表面应镀铬
第三部分注射机的型号和规格选择及校核
注射模是安装在注射机上的,因此在设计注射模具时应该对注射机有关技术规范进行必要的了解,以便设计出符合要求的模具,同时选定合适的注射机型号。
从模具设计角度考虑,需要了解注射机的主要技术规范。
在设计模具时,最好查阅注射机生产厂家提供的有关“注射机使用说明书”上标明的技术规范,。
因为即使同一规格的注射机,生产厂家不同,其技术规格也略有差异。
1、注射机的选用
选用注射机时,通常是以某塑件(或模具)实际需要的注射量初选某一公称注射量的注射机型号,然后依次对该机型的公称注射压力、公称锁模力、模板行程以及模具安装部分的尺寸一一进行校核。
以实际注射量初选某一公称注射量的注射机型号;为了保证正常的注射成型,模具每次需要的实际注射量应该小于某注射机的公称注射量,即:
式子中,
—实际塑件(包括浇注系统凝料)的总体积(
)。
由UG分析/体测量,可得塑料盒的体积为19.60cm3,考虑到设计为2腔,加上浇注系统的冷凝料,查阅塑料模设计手册的国产注射机技术规范及特性,可以选择XS—ZY—60.其最大理论注射容量为60cm3,注射压力为122MPa,锁模力为500KN,最大注射面积为130cm2.模具高度在200~300mm,最大开模行程180mm。
喷嘴圆弧半径为12mm,喷嘴孔直径为4mm。
2、注射压力的校核
该项工作是校核所选注射机的公称压力P能否满足塑件所成型时需要的注射压力P0,其值一般为70~150MPa,通常要求P>P0。
我们这里选70MPa。
3、锁模力的校核
锁模力是指注射机的锁模机构对模具所施加的最大夹紧力,当高压的塑料熔体充填模腔时,会沿锁模方向产生一个很大的胀型力。
为此,注射机的额定锁模力必须大于该胀型力,即:
F锁
F胀=A分×P型
F锁—注射机的额定锁模力(N);
P分—模具型腔内塑料熔体平均压力(MPa);一般为注射压力的0.3~0.65倍,通常取20~40MPa。
我们这里选P型=30MPa。
A分—塑料和浇注系统在分型面上的投影面积之和(mm2)
由UG分析/面测量,可得投影面积为70cm2,浇注系统的投影面积不超过10cm2
∴F锁
F胀=A分×P型
=80×200×30=4.8×105(N)
而锁模力为500KN,大于480KN,符合要求。
4、开模行程和推出机构的校核
开模行程是指从模具中取出塑料所需要的最小开合距离,用H表示,它必须小于注射机移动模板的最大行程S。
由于注射机的锁模机构不同,开模行程可按以下两种情况进行校核:
一种是开模行程和模具厚度无关;二种是开模行程和模具厚度有关。
我们这里选用的是开模行程和模具厚度无关,且是单分型面注射模具。
1、当开模行程和模具厚度无关时
这种情况主要是指锁模机构为液压-机械联合作用的注射机,其模板行程是由连杆机构的做大冲程决定的,而和模厚度是无关的。
此情况又两种类型:
⑴对单分型面注射模,所需开模行程H为:
S
H=H1+H2+(5~10)mm
式中,H1—塑件推出距离(也可以作为凸模高度)(mm);
H2—包括浇注系统在内的塑高度(mm);
S—注射机移动板最大行程(mm);
H—所需要开模行程(mm)。
而我们这里通过资料可得出(结构见图六):
H=15+95+8=118(mm)。
⑵对双分型面注射模,所需开模行程为:
S机
H=H1+H2+a+(5~10)mm
式中,a—中间板和定模的分开距离(mm)。
2、推出机构的校核
各种型号注射机的推出装置和最大推出距离各不同,设计模具时,推出机构应和注射机相适应,具体可查资料。
第四部分 分型面的选择
分型面是指分开模具取出塑件和浇注系统凝料的可分离的接触表面。
一副模具根据需要可能有一个或两个以上的分型面,分型面可以是垂直于合模方向,也可以和合模方向平行或倾斜,我们在这里选用和合模方向倾斜。
1、分型面的形式:
分型面的形式和塑件几何形状、脱模方法、模具类型及排气条件、浇口形式等有关,我们常见的形式有如下五种:
水平分型面、垂直分型面、斜分型面、阶梯分型面、曲线分型面。
2、分型面的选择原则:
a)、便于塑件脱模:
Ⅰ、在开模时尽量使塑件留在动模内
Ⅱ、应有利于侧面分型和抽芯
Ⅲ、应合理安排塑件在型腔中的方位;
b)、考虑和保证塑件的外观不遭损坏
c)、尽力保证塑件尺寸的精度要求(如同心度等)
d)、有利于排气
e)、尽量使模具加工方便
3、我们这里选择曲线分型面
图二分型面
第五部分型腔数目的决定及排布
1、型腔数目的确定:
为了使模具和注射机的生产能力的匹配,提高生产效率和经济性,并保证塑件体精度,模具设计时应确定型腔数目,常用的方法有四种:
a)、根据经济性能确定型腔数目;b)、根据注射机的额定锁模力确定型腔数目;c)、根据注射机的最大注射量确定型腔数目;d)、根据制品精度确定型腔数目。
我们这里选用a),其计算过程如下:
我们设型腔数目为n,制品总件数为N,每一个型腔所需的模具费用为C1,和型腔无关的模具费用为C0,每小时注射制品成型的加工费用为y(元/h),成型周期为t(min),则:
模具费用为
(元),
注塑成型费用为
(元),
总成型加工费用为
,即
为使总的成型加工费用最少,即令
=0,则有:
所以n=
。
对于高精度制品,由于型腔模具难以使各型腔的成型条件均匀,故通常推荐型腔数目不超过4个,塑料件的精度为6级左右,以及模具制造成本、制造难度和生产效率的综合考虑,型腔数目初定为2腔,排布形式为矩形的平衡布局(详细的布局参见零件布局图)。
图三型腔布局图
第六部分浇注系统的设计
1、浇注系统的组成
图四浇注系统的组成
所谓注射模的浇注系统是指从主流道的始端到型腔之间的熔体流动通道。
其作用是使塑件熔体平稳而有序地充填到型腔中,以获得组织致密、外形轮廓清晰的塑件。
因此,浇注系统十分重要。
而浇注系统一般可分为普通浇注系统和无流道浇注系统两类。
我们在这里选用普通浇注系统,它一般是由主流道、分流道、浇口和冷料穴四部分组成,如图四所示:
2、浇注系统各部件设计
A、主流道设计:
主流道是连接注射机喷嘴和分流道的一段通道,通常和注射机喷嘴在同一轴线上,断面为圆形,带有一定的锥度,其主要设计点为:
⑴主流道圆锥角α=2o~6o,对流动性差的塑件可取3o~6o,内壁粗糙度为Ra0.63μm。
⑵主流道大端呈圆角,半径r=1~3mm,以减小料流转向过渡时的阻力。
⑶在模具结构允许的情况下,主流道应尽可能短,一般小于60mm,过长则会影响熔体的顺利充型。
⑷对小型模具可将主流道衬套和定位圈设计成整体式。
但在大多数情况下是将主流道衬套和定位圈设计成两个零件,然后配合固定在模板上。
主流道衬套和定模座板采用H7/m6过渡配合,和定位圈的配合采用
间隙配合。
⑸主流道衬套一般选用T8、T10制造,热处理强度为52~56HRC。
B、冷料穴的设计
冷料穴一般位于主流道对面的动模板上。
其作用就是存放料流前峰的“冷料”,防止“冷料”进入型腔而形成接缝;此外,在开模时又能将主流道凝料从定模板中拉出。
冷料穴的尺寸宜稍大于主流道大端的直径,长度约为主流道大端直径。
冷料穴的形式有三种:
一种是和推杆匹配的冷料穴;二种是和拉料杆匹配的冷料穴;三种是无拉料杆的冷料穴。
我们这里选用和推出杆匹配的倒锥形冷料穴,其结构如图五:
图五冷料穴
1—定位圈2—冷料穴
3—推杆4—动模板
C、分流道的设计
分流道就是主流道和浇口之间的通道,一般开设在分型面上,起分流和转向的作用。
多型腔模具必定设计分流道,单型腔大型腔塑件在使用多个点浇口时也要设置分流道。
①分流道的截面形状:
通常分流道的断面形状有圆形、矩形、梯形、U形和六角形等。
为了减少流道内的压力损失和传热损失,提高效率,我们这里就选用圆形分流道,如图六。
因为圆形截面
分流道的效率是分流道中效率最高的,固选它。
②分流道的尺寸:
因为各种塑料的流动性有差异,图六圆形流道
所以可以根据塑料的品种来粗略地估计分流道的直径,常用塑料的分流道直径推荐值如下表一。
但对于壁厚小于3mm,质量在200g以下的塑料,可用此经验公式确定其流道直径:
式中,m—流经分流道的塑料量(g);L—分流道长度(mm);D—分流道直径(mm)。
对于黏度较大的塑料,可按上式算得的D值再乘以1.2~1.25的系数。
我们这里取m=60*1.05=63g,L=50mm。
固分流道尺寸为1.2D,即D`=1.2D=1.2×0.265×√63×
=8(mm)。
所以S=Л×8*8/22×1.22=72.4(mm2)
③分流道的布置:
分流道的布置取决于型腔的布局,两者相互影响。
分流道的布置形式分平衡式和非平衡式两类,这里我们选用的是平衡式的布置方法。
④分流道和浇口的连接:
分流道和浇口的连接处应加工成斜面,并用圆弧过渡,有利于塑料熔体的流动及充填。
D、浇口的设计:
浇口是连接分流道和型腔之间的一段细短通道,它是浇注系统的关键部分。
浇口的形状、位置和尺寸对塑件的质量影响很大。
浇口的理想尺寸很难用理论公式计算,通常根
据经验确定,取其下限,然后在试模过程中逐步加以修正。
一般浇口的截面积为分流道截面积的3%~9%,截面形状常为矩形或圆形,浇口长度为0.5~2mm,表面粗糙度Ra不低于0.4μm。
浇口的结构形式很多,按照浇口的形状可以分为点浇口、扇形浇口、盘形浇口、环形浇口、及薄片式浇口。
而我们这里选用的是点浇口。
简图如图七
图七点浇口
浇口的截面一般只取分流道截面积的3%~9%,浇口的长度约为0.5mm~2mm,现在可算出我们需要的浇口面积S=5%×s=3.9
。
浇口位置的选择直接影响到制品的质量问题,所以我们在开设浇口时应注意以下几点:
①浇口应开在能使型腔各个角落同时充满的位置。
②浇口应设在制品壁厚较厚的部位,以利于补缩。
③浇口的位置选择应有利于型腔中气体的排除。
④浇口的位置应选择在能避免制品产生熔合纹的部位。
⑤对于带细长型芯的模具,宜采用中心顶部进料方式,以避免型芯受冲击变形。
⑥浇口应设在不影响制品外观的部位。
⑦不要在制品承受弯曲载荷或冲击的部位设置浇口。
第七部分成型零件的工作尺寸计算
一、凹模的结构形式:
凹模又称阴模,它是成型塑件外轮廓的零件。
根据需要有以下几种结构形式:
整体式凹模、组合式凹模、拼块组合式凹模,我们的产品属于小型制件,从各方面分析我们
可选用组合式凹模——整体嵌入式凹模。
整体嵌入式凹模:
于小件一模多腔式模具,一般是将每个型腔单独加工后压入定模中。
这种结构的凹模形状、尺寸一致性好,更换方便。
凹模的外形通常是用带台阶的圆柱形,由台阶定位,以
过渡配合嵌入定模板,然后用定模板座板将其固定。
其结构如图六所示:
二、凸模的结构设计
1、凸模的结构形式:
凸模(即型芯)是成型塑件内表面的成型零件,通常可非为整体式和组合式两种类型。
我们根据凹模的结构形式选择组合式凸模——整体装配式凸模,它是将凸模单独加工后和动模板进行装配而成,如下图所示:
图八型芯图
2、凹模的形状
图九型腔图
三、成型零件的工作尺寸计算
现设制品的名义尺寸LS是最大尺寸,其公差按规定为负值“-Δ”;凹模的名义尺寸LM是最小尺寸,其公差按规定为正值“+δZ”现由公式可得:
式中,“Δ”前的系数(此处为0.5)可随制品的精度和尺寸变化,一般在0.5~0.75之间,ABS的收缩率S为0.005.制品偏差大则取小值,偏差小则取大值。
Δ值由塑料模设计手册《公差数值表》可查基本尺寸为120mm时,其Δ值为0.68,基本尺寸为70mm时,其Δ值为0.52,基本尺寸为15mm时Δ为0.24.(这里塑料件的精度取5级)
固可由以上公式算出其尺寸:
A、型腔尺寸计算:
=[120(1+0.005)-0.5*0.68]+0.2*0.68=120.26+0.14(mm)
=[70(1+0.005)-0.5*0.52]+0.2*0.52=70.14+0.10mm
=[15(1+0.005)-0.5*0.24]+0.2*0.24
=15.0+0.04(mm)
B、型芯尺寸的计算
设塑件内型腔尺寸为ls,公差为正值“+Δ”,制造公差为负值“-δZ”,经过和上面凹模径向尺寸相似推理,可得:
由于我们塑料件的厚度为2mm。
因此相应的尺寸上减去4mm或者2mm。
Δ值的取值分别为。
基本尺寸为116mm的为0.68,66mm的为0.52,13mm的为0.24.
=[116(1+0.005)+0.5*0.68]-0.2*0.68
=116.92-0.14mm
=[66(1+0.005)+0.5*0.52]-0.2*0.52
=66.6-0.10mm
=[13(1+0.005)+0.5*0.24]-0.2*0.24
=13.185-0.04mm
C、型腔壁厚和底板厚度计算
在注射成型过程中,型腔主要承受塑料熔体的压力,因此模具型腔应该具有足够的强度和刚度。
如果型腔壁厚和底板的厚度不够,当型腔中产生的内应力超过型腔材料本身的许用应力时,型腔将导致塑性变形,甚至开裂。
和此同时,若刚度不足将导致过大的弹性变形,从而产生型腔向外膨胀或溢料间隙。
因此,有必要对型腔进行强度和刚度的计算,尤其是对大型塑件。
但我们这里的塑件较小,故不需要对型腔壁厚和底板厚度进行计算,大致得体即可。
第八部分导柱导向机构的设计
为了保证注射模准确合模和开模,在注射模中必须设置导向机构。
导向机构的作用是导向、定位以及承受一定的侧向压力。
导向机构的形式主要有导柱导向和锥面定位两种,我们这里选取导柱导向机构,其结构如图十:
我们在设计此机构的同时还应注意以下几点:
⑴、导柱应合理地均布在模具分型面的四周,导柱中心至模具外缘应有足够的距离,以保证模具的强度。
⑵、导柱的长度应比型芯(凸模)端面的高度高出6~8mm(图十),以免型图十导向机构
芯进入凹模时和凹模相碰而损坏。
⑶、导柱和导套应有足够的耐磨度和强度。
⑷、为了使导柱能顺利地进入导套、导柱端部应做成锥形或半球形,导套的前端也应该倒角。
⑸、导柱的设置应根据需要而决定装配方式。
⑹、一般导柱滑动部分的配合形式按H8/f8,导柱和导套固定部分配合按H7/k6,导套外径的配合按H7/k6。
⑺、一般应在动模座板和推板之间设置导柱和导套,以保证推出机构的正常运动。
⑻、导柱的直径应根据模具大小而决定,可
参考准模架数据选取。
第九部分脱模机构的设计
1、何为脱模机构
在注射成型的每一循环中,都必须使塑件从模具型腔中或型芯上脱出,模具中这种出塑件的机构称为脱模机构。
2、脱模机构的分类及选用
脱模机构的分类分多,我们采用的是混合分类中的一种:
推杆一次脱模机构,因为此机构是最简单、最为常用的一种,具有制造简单、更换方便、推出效果好等优点,在生产实践中比较实用和直观。
所谓一次脱模就是指在脱模过程中,推杆就需要一次动作,就能完成塑件脱模的机构。
它通常包括推杆脱模机构、推管脱模机构、脱模板脱模机构、推块脱模机构、多元联合脱模机构和气动脱模机构等。
3、脱模机构的设计原则
设计脱模机构时,应遵循以下原则:
(1)结构可靠:
机械的运动准确、可靠、灵活,并有足够的刚度和强度。
(2)保证塑件不变形、不损坏。
(3)保证塑件外观良好。
(4)尽量使塑件留在动模一边,以便借助于开模力驱动脱模装置,完成脱模动作。
4、推杆的结构形式及形状
因制品的几何形状及型腔结构等的不同,所用推杆的截面形状也不尽相同,常用推杆的截面形状为圆形。
推杆又可分为普通推杆和成型推杆两种,我们这里选用普通推杆。
其结构形式见图十一。
5、推杆的固定方式(图十二)
图十一推杆图十二推杆固定
第十部分温度调节系统的设计
1、冷却系统设计
塑料在成型过程中,模具温度会直接影响到塑料的充模、定型、成型周期和塑件质量。
所以,我们在模具上需要设置温度调节系统以到达理想的温度要求。
一般注射模内的塑料熔体温度为200℃左右,而塑件从模具型腔中取出时其温度在60℃以下。
所以热塑性塑料在注射成型后,必须对模具进行有效的冷却,以便使塑件可靠冷却定型并迅速脱模,提高塑件定型质量和生产效率。
对于熔