精品难加工材料的切削技术及其新发展.docx
《精品难加工材料的切削技术及其新发展.docx》由会员分享,可在线阅读,更多相关《精品难加工材料的切削技术及其新发展.docx(8页珍藏版)》请在冰豆网上搜索。
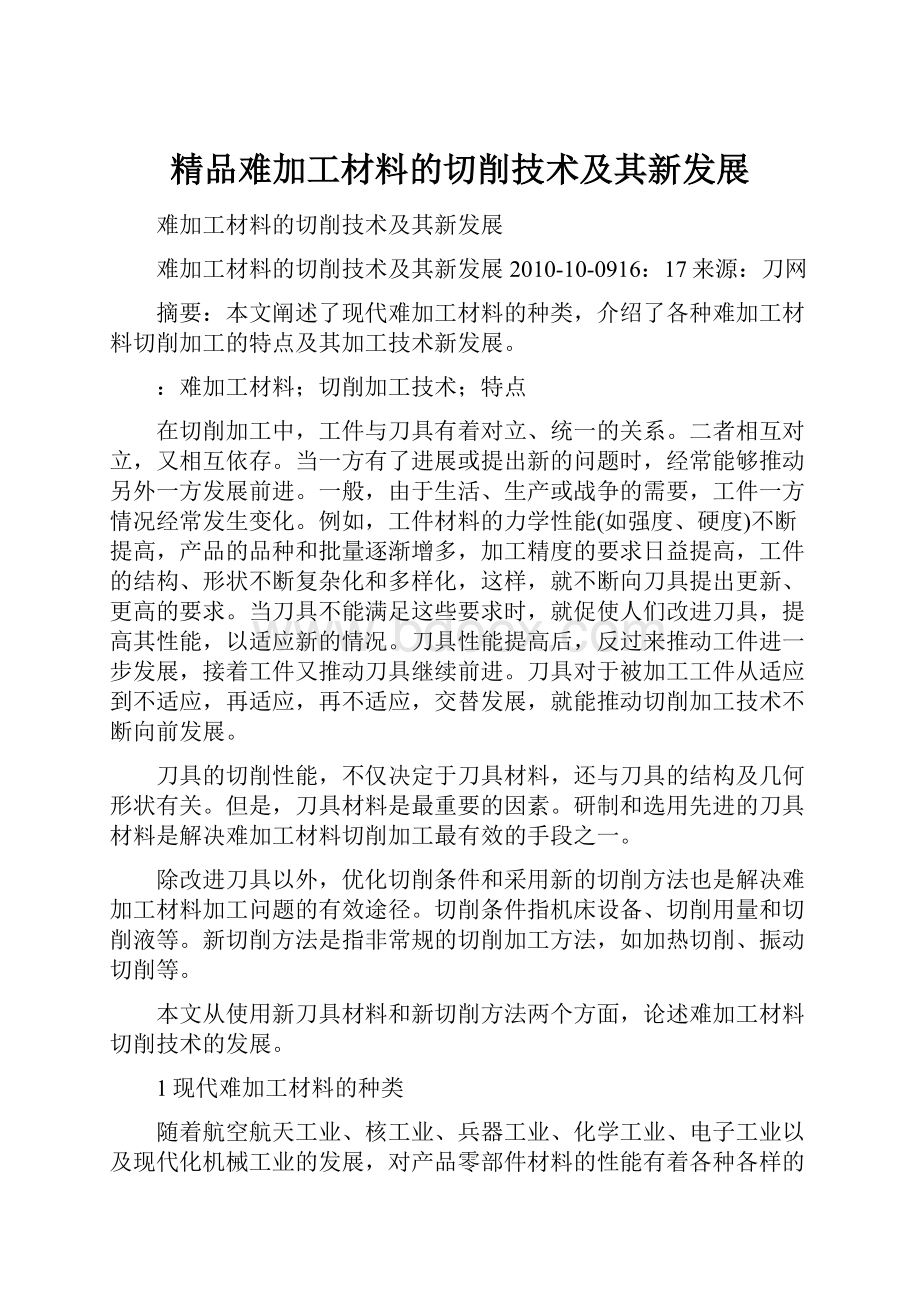
精品难加工材料的切削技术及其新发展
难加工材料的切削技术及其新发展
难加工材料的切削技术及其新发展2010-10-0916:
17来源:
刀网
摘要:
本文阐述了现代难加工材料的种类,介绍了各种难加工材料切削加工的特点及其加工技术新发展。
:
难加工材料;切削加工技术;特点
在切削加工中,工件与刀具有着对立、统一的关系。
二者相互对立,又相互依存。
当一方有了进展或提出新的问题时,经常能够推动另外一方发展前进。
一般,由于生活、生产或战争的需要,工件一方情况经常发生变化。
例如,工件材料的力学性能(如强度、硬度)不断提高,产品的品种和批量逐渐增多,加工精度的要求日益提高,工件的结构、形状不断复杂化和多样化,这样,就不断向刀具提出更新、更高的要求。
当刀具不能满足这些要求时,就促使人们改进刀具,提高其性能,以适应新的情况。
刀具性能提高后,反过来推动工件进一步发展,接着工件又推动刀具继续前进。
刀具对于被加工工件从适应到不适应,再适应,再不适应,交替发展,就能推动切削加工技术不断向前发展。
刀具的切削性能,不仅决定于刀具材料,还与刀具的结构及几何形状有关。
但是,刀具材料是最重要的因素。
研制和选用先进的刀具材料是解决难加工材料切削加工最有效的手段之一。
除改进刀具以外,优化切削条件和采用新的切削方法也是解决难加工材料加工问题的有效途径。
切削条件指机床设备、切削用量和切削液等。
新切削方法是指非常规的切削加工方法,如加热切削、振动切削等。
本文从使用新刀具材料和新切削方法两个方面,论述难加工材料切削技术的发展。
1现代难加工材料的种类
随着航空航天工业、核工业、兵器工业、化学工业、电子工业以及现代化机械工业的发展,对产品零部件材料的性能有着各种各样的高水平要求。
有的在高温、高应力状态下工作,有的要耐腐蚀、耐磨损,有的要能绝缘,有的则需有高导电率。
故现代新的工程材料形形色色,多种多样,不断涌现,犹如雨后春笋。
不仅使用一般的碳素结构钢,而且使用了高强度钢、超高强度合金结构钢、高猛钢和不锈钢;不仅使用一般的灰铸铁、球墨铸铁和可锻铸铁,而且使用了合金耐磨铸铁和冷硬铸铁;不仅使用黑色金属,而且使用了钛合金、铜合金、铝合金及其它有色金属;不仅使用一般的铁碳合金,而且使用了多元合金如高温合金等;不仅使用以珠光体、铁素体为主的普通钢材,而且使用了以索氏体、托氏体为主的中硬钢和马氏体淬硬钢;不仅使用冶炼方法制成的金属材料,而且使用了粉末冶金和热喷涂等方法制成的金属零件;不仅大量使用金属材料,而且大量使用了各种非金属材料,如石材、陶瓷、工程塑料、纤维和颗粒增强的复合材料等。
在上述各种新工程材料中,有不少是属于难切削的,即所谓"难加工材料"。
难加工的原因一般是以下几个方面:
①高硬度,②高强度,③高塑性和高韧性,④低塑性和高脆性,⑤低导热性,⑥有微观的硬质点或硬夹杂物,⑦化学性质活泼。
新工程材料的这些特性一般都能使切削过程中的切削力加大,切削温度升高,刀具耐用度下降;有时还将使已加工表面质量恶化,切屑难以控制;最终则使加工效率和加工质量降低
机械加工工作者的任务是针对难加工材料的特点,对症下药,提出措施,采用新的加工技术,保证所需的加工效率和加工质量。
2各种难加工材料的切削加工特点
1)高强度和超高强度钢调质(淬火,中温回火)后σs1000MPa或σb1100MPa的结构钢,称为高强度钢。
调质后σs1200MPa或σb1500MPa的结构钢,称为超高强度钢。
在这类钢材中,凡含碳量在0.30%~0.50%之间,合金元素总量不超过6%的,为低合金高强度、超高强度钢,在生产中用得最多。
还有合金元素含量较多的中合金、高合金高强度与超高强度钢,它们的加工难度更大。
高强度、超高强度钢的金相组织一般为索氏体和托氏体。
与普通碳素结构钢相比,它们的硬度、强度较高(约比45钢高出1倍或1倍以上),冲击值较大,导热系数偏低,故切削力较大,切削温度较高。
加工高强度、超高强度钢时,可选用与加工普通碳素钢相同的刀具材料。
根据粗加工、半精加工、精加工的要求,分别采用不同牌号的YT类硬质合金,最好是添加钽铌的牌号。
高速精加工时,应采用高TiC含量的YT类合金,也可采用YN类合金(金属陶瓷)、涂层合金与Al2O3陶瓷。
在工艺系统钢性允许的情况下,前角和主偏角应较小,刀尖圆弧半径应较大。
必须采用低于加工中碳正火钢的切削用量,尤其是切削速度。
2)高猛钢高猛钢的典型牌号有Mn13,40Mn18Cr3,50Mn18Cr4等。
经过水韧处理,金相组织为均匀的奥氏体。
它的原始硬度虽不甚高,但其塑性和韧性特别高,加工硬化特别严重。
硬化后可达HBW500。
它的导热系数很小,只为45钢的1/4。
切削力比加工中碳钢时增大60%,切削温度很高。
应选用硬度高、有一定韧性、导热系数较大、高温性能好的刀具材料。
一般,粗加工时应选用YG类和YW类硬质合金;精加工时可用YW或YT14合金,用Al2O3陶瓷刀具进行高速精加工效果很好。
宜采用较小的前角和主偏角,较大的后角,切削速度应较低,进给量应较大。
3)淬硬钢和冷硬铸铁淬硬钢的组织为回火马氏体,硬度可达HRC60以上。
塑性和导热系数均极低。
冷硬铸铁的特点是铸铁表面经激冷而发生"白口"(组织为渗碳体加珠光体),硬度亦达HRC52~HRC60,其它性能与淬硬钢相近。
宜采用YG类合金(YG类的弹性模量大于YT类合金)。
用Al2O3或Si3N4基陶瓷刀具对淬硬钢和冷硬铸铁进行精加工、半精加工,效果比硬质合金好。
刀具前角和主偏角应小,切削速度应低。
半精加工和精加工时可用CBN刀具。
4)不锈钢和高温合金铁素体、马氏体不锈钢的切削加工并不太难。
奥氏体不锈钢(如1Cr18Ni9Ti)加工难度较大,它的原始硬度、强度都不太高,但塑性、韧性很高,加工硬化严重,且有一定数量的硬质夹杂物,导热系数很小(为45钢的1/3),切削力较大,切削温度较高。
高温合金的加工难度更大,其原始硬度、强度偏高,导热系数很小(为45钢的1/3~1/4),硬夹杂物多,加工硬化严重,切削力大,切削温度高。
高温合金中含有许多高熔点合金元素,如Fe,Ti,Cr,Co,Ni,V,Mo,W等,它们与非金属元素N、C、B等结合成比重小、熔点高的高硬度化合物,还能形成有一定硬度和韧性的金属间化合物,这些都能加剧刀具的磨损。
加工不锈钢和高温合金都应采用YG类和YW类硬质合金,而不能用含Ti的YT类合金。
采用适当的刀具前角,切削速度应较低,进给量应较大。
必要时也可采用高速钢刀具。
5)热喷涂材料利用不同热源,将合金粉末(Ni基、Fe基、Co基等)或陶瓷等材料加热至溶化状态,并在较大压力和喷射速度下喷涂到工件表面上,从而形成一层牢固的、耐高温、耐磨损的保护层。
热喷涂材料的成分、性能及加工性都与高温合金相似,硬度尤高,刀具材料及切削用量的选用原则亦与高温合金相近。
株洲厂的YC09硬质合金加工热喷涂材料很有效。
6)钛合金钛合金的导热系数极小(只为45钢的1/6),化学性质活泼,易与大气中氧、氮等化合而形成硬脆物质,刀屑接触界面短,切削温度高,弹性模量小。
只能采用YG类硬质合金。
刀具前角应小,切削速度应低,进给量应较大。
必要时也可采用高速钢刀具。
7)石材石材不仅是建筑材料,而且越来越多地用作机械工程材料。
石材都较硬,例如辉绿岩为HS80,大理石为HS50,花岗岩达HS100以上。
它们都是抗压强度高,抗弯强度低,材质不如金属材料均匀。
出粉状或粒状碎屑。
一般用YG类硬质合金加工,切割时常用金刚石镶齿锯片。
8)工程塑料工程塑料的品种非常多,按其性质的不同可分为热塑性塑料和热固性塑料两大类。
前者有聚氯乙烯、聚丙烯、有机玻璃等,后者有胶木、玻璃钢等。
塑料的比重小,比强度高,耐磨损,抗腐蚀,不导电,具有良好的使用性能。
它们的硬度、强度虽然不高,但导热系数极小,只为碳钢的1/175~1/450,加工时容易引起烧伤和热变形。
弹性模量小,不易保证加工尺寸。
刀具材料一般选用YG类硬质合金或高速钢。
9)复合材料和纤维增强材料复合材料可以由金属、高聚物和陶瓷三者中任意两个人工合成。
复合材料包括纤维增强材料和颗粒增强材料。
纤维增强的有碳纤维(CFRP)、玻璃纤维(GFRP)和Kevlar纤维(KFRP)等。
纤维增强材料的弹性模量和导热系数都很小,已加工表面易发生回弹、撕裂,产生毛刺;纤维对刀具切削力有一定擦伤作用。
故表面质量不易保证,刀具耐用度亦受影响。
切削力和表面粗糙度常因切削方向不同而变化。
刀具材料宜选用YG类硬质合金或高速钢。
颗粒增强复合材料的基体(如铝合金)虽较软,但颗粒(如SiC)很硬,对刀具切削力有冲击和刮伤,故刀具受损伤很大。
一般,高速钢、硬质合金和陶瓷刀具切削颗粒增强复合材料均不能胜任;建议用CBN或金刚石刀具,但应采取增强刀具切削力的措施。
新的难加工工程材料不仅是以上所提到的,还有其它的类型,如纯金属(纯铁、纯铜、纯镍)、高比重合金以及陶瓷等等,它们的加工性也各有特色,此处不一一介绍。
3难加工材料切削技术的新发展
3.1采用高性能的新刀具材料
在难加工材料的切削加工中,刀具材料是最活跃的因素。
新刀具材料的出现和应用有力地推动了难加工材料切削加工效率的提高。
当前,新型高速钢有各种超硬高速钢、粉末高速钢和涂层高速钢,切削性能比普通高速钢大为提高。
新型硬质合金有各种添加钽、铌等元素的WC基合金、细晶粒和超细晶粒的WC基合金、TiC基和Ti(C,N)基合金、涂层和稀土硬质合金,还有热压复合陶瓷和超硬刀具材料CBN、金刚石等。
可以分别用于切削各种难加工材料。
应注意工件、刀具材料的合理匹配。
3.2采用非常规的新切削方法
上述各种新型刀具材料仍是在常规的切削状态下工作的。
但有时刀具材料的性能尚不敷需要。
例如,对于某些高硬度材料的加工,新型硬质合金的硬度和耐磨性还嫌不足,因此不得不降低切削速度,加工效率不够高。
CBN和金刚石刀具硬度虽高,但强度不足,且金刚石不能加工黑色金属,故只能在一定的切削条件下用于难加工材料的加工,并可取得效益。
1)加热切削法一种是导电加热切削,即在工件和刀具的回路中(工件必须是导电体)施加低电压(约5V)、大电流(约500
A),利用刀具、工件间及剪切面处的电阻,使切削区产生热量,从而使局部工件材料的力学性能、接触和摩擦条件都发生变化。
另一种是等离子体加热切削,即用等离子弧对靠近刀尖将要被切除的工件材料进行加热,使其硬度、强度降低,从而改善了切削条件。
两种方法的效果相近。
可较大幅度地降低切削力,可以消除积屑瘤等现象,从而降低了表面粗糙度。
在中束定切削刀具耐用度有明显提高。
因此用这样的方法进行大切深、大进给加工硬材料是有效的。
沈阳工业大学和北京理工大学曾用等离子体加热切削法加工高锰钢和高强度钢,华南理工大学和安徽工学院曾用电热切削加工高强度钢及其它材料,取得了系统的试验数据,并部分在生产中应用。
还有激光辅助切削法是另一种加热切削。
近年,国内发明了"电熔爆"切削法。
带电的刀盘与被加工表面产生剧烈放电,将被加工表层快速熔化、爆离,从而切掉余量,但工件内部材料不受热的影响。
此方法效率高,对硬、软、粘料均适用,既可用于粗加工,又可用于精加工。
2)低温切削法用液氮(-180℃)或液体CO2(-76℃)为切削液,降低切削区温度。
据试验,主切削力可降低20%,切削温度可降低300℃以上,同时积屑瘤消失,提高了已加工表面质量,刀具耐用度可提高2~3倍。
在加工高强度钢、耐磨铸铁、不锈钢、钛合金时均有效果。
3)振动切削用不同形式的振动发生器,使刀具发生强迫振动。
f10kHz者为高频,f200Hz者为低频。
振动方向有V方向、f方向等。
V方向振动较常用。
振动切削可使刀屑间摩擦系数和切削力大幅度降低,变形系数及切削温度亦下降,积屑瘤消失,加工硬化降低,故能提高已加工表面质量。
但对刀具耐用度有些不利,必须采用韧性强的刀具材料(如高速钢、超细硬质合金等)。
国内有十余所高等院校及研究所对振动切削进行过研究,被加工材料涉及钛合金、淬硬钢、不锈钢、热喷涂层、紫钢、陶瓷及GFRP等,工种有车削、攻丝、钻孔、铰孔等,都取得了好的效果。
如同时使用切削液,效果尤佳。
4)真空中切削在真空中切削出现了一些不同于在空气中切削的现象。
日本东洋大学对真空中切削进行了研究。
加工铜、铝时,真空度对变形系数、切削力及已加工表面粗糙度无影响。
但加工中碳钢和钛合金时,真空度越大,其变形系数、切削力及粗糙均加大,这是因为在真空中刀屑界面不能产生有利于减小摩擦的氧化物。
如此看来,在真空中切钢并不一定肯定是有益的。
5)有惰性气体保护下切削这也是针对切削钛合金这类材料所采取的一种措施。
南京航空学院曾在钛合金的切削区喷射氩气,使切削区材料与空气隔离,因而被加工材料不与空气中元素化合而成不利于加工的化合物,从而改善了钛合金的加工性。
这种方法对化学性质活泼金属的加工有一定效果。
以此类推,如果采用某些特殊成分的切削液,也会有效果。
6)绝缘切削在切削过程中,如将工件、刀具连成回路,则可看出有热电势,回路中有热电流刀具磨损加剧。
如将工件、刀具与机床绝缘,切断电流,则刀具耐用度有所提高。
西北工业大学用这种方法钻削高温合金K14,西安黄河机械厂切削1Cr13、2Cr13钢,均有不同程度的效果。
这种方法的机理虽未查明,但简单易行,有使用价值。
7)超高速切削在常规切削下,切削速度提高将使刀具耐用度降低。
然而,有人提出,当切削速度提高到一个临界值,切削温度就达到最高值,然后温度将随着速度继续提高而降低,切削力也下降,零件表面质量好。
这就是超高速切削的理论基础。
美国、德国、日本的学校和工厂在这方面有很多实践,用硬质合金、陶瓷刀具切削钢、铸铁、钛、铝合金等材料,切削速度达500~800m/min甚至3000~8000m/min,刀具耐用度尚能保持在正常水平。
这种切削方法常受到设备条件限制而不能推广。
还有人用更高的切速(例如达到枪弹的速度)进行试验。
超高速切削能否在难加工材料切削中发挥作用,尚有待探讨。
新的切削方法不断出现,为难加工材料加工增添了新的途径。
3.3采用特种加工方法
以上切削方法都离不开刀具,即用高硬度材料作为刀具切除较软材料的余量。
本世纪初以来,人们相继研究出一些与上述切削加工原理完全不同的加工方法,如电火花加工、电解加工、超声加工、激光加工、电子束加工、离子束加工等称为特种加工方法。
在特种加工中,工具与工件基本上不接触,加工时无明显的机械作用力,可加工脆性材料、精密细微零件、薄壁和弱刚性零件等;不是用机械能,而是用电能、化学能、声能、热能去除被加工材料,瞬时能量密度很高,可加工任何高硬度材料,而工具的硬度却不很高。
目前,电火花加工多用于加工模具和异形孔等;电解加工多用于加工特形表面和异形孔,但可获得更高的表面质量;超声加工可加工许多非金属硬脆材料,尤其是加工异孔、切削等;激光加工主要表面质量;超声加工可加工许多非金属硬脆材料,尤其是加工异孔、切割等;激光加工主要用于各种金属、非金属材料的打孔与切割;电子束加工主要用于打微孔和切缝;离子束加工可对零件表面进行超精密、超微量加工。
这些特种加工方法都需要特殊的专用设备,有的很昂贵,消耗能量很大。
因此使用范围受到很大的限制。
然而它们已在难加工材料的加工中起了很大的作用,而且有着广阔的发展前景。
4结语
在切削加工中,刀具与工件双方有着相互对立又相互推动的作用。
自20世纪以来,工件材料特别是难加工材料的品种和性能有了很大的发展,刀具材料也随之出现了惊人的发展。
提高刀具材料的性能是解决难加工材料加工的最有效的手段。
刀具材料与工件材料有着匹配的关系,他们之间要在机械(力学)、物理、化学性能方面有着良好的匹配。
许多非常规切削加工方法和特种加工方法的出现为难加工材料的加工增添了新的途径。
特别声明:
1:
资料来源于互联网,版权归属原作者
2:
资料内容属于网络意见,与本账号立场无关
3:
如有侵权,请告知,立即删除。