精脱硫系统催化剂及转化催化剂的升温与还原复件.docx
《精脱硫系统催化剂及转化催化剂的升温与还原复件.docx》由会员分享,可在线阅读,更多相关《精脱硫系统催化剂及转化催化剂的升温与还原复件.docx(67页珍藏版)》请在冰豆网上搜索。
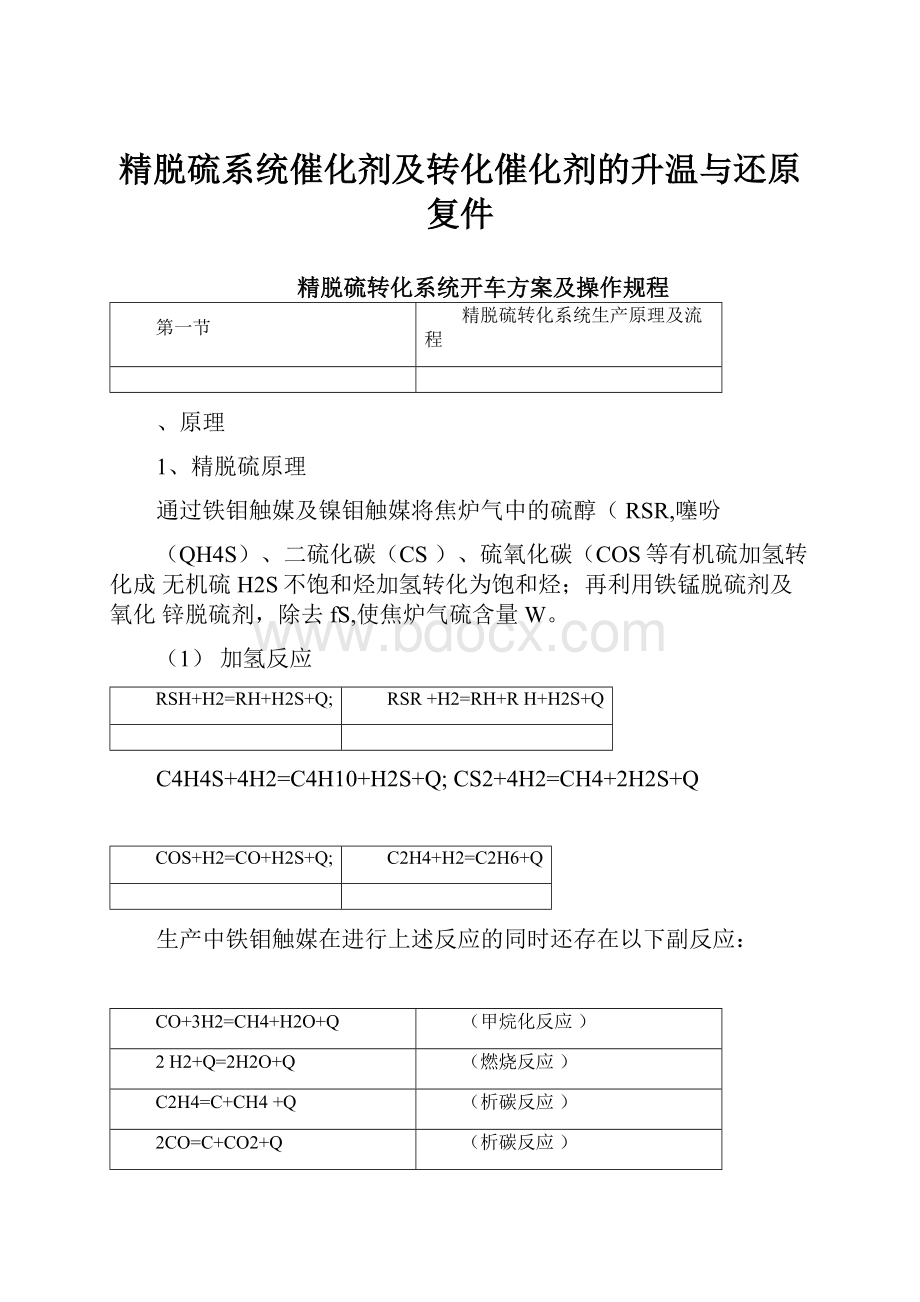
精脱硫系统催化剂及转化催化剂的升温与还原复件
精脱硫转化系统开车方案及操作规程
第一节
精脱硫转化系统生产原理及流程
、原理
1、精脱硫原理
通过铁钼触媒及镍钼触媒将焦炉气中的硫醇(RSR,噻吩
(QH4S)、二硫化碳(CS)、硫氧化碳(COS等有机硫加氢转化成无机硫H2S不饱和烃加氢转化为饱和烃;再利用铁锰脱硫剂及氧化锌脱硫剂,除去fS,使焦炉气硫含量W。
(1)加氢反应
RSH+H2=RH+H2S+Q;
RSR+H2=RH+RH+H2S+Q
C4H4S+4H2=C4H10+H2S+Q;CS2+4H2=CH4+2H2S+Q
COS+H2=CO+H2S+Q;
C2H4+H2=C2H6+Q
生产中铁钼触媒在进行上述反应的同时还存在以下副反应:
CO+3H2=CH4+H2O+Q
(甲烷化反应)
2H2+Q=2H2O+Q
(燃烧反应)
C2H4=C+CH4+Q
(析碳反应)
2CO=C+CO2+Q
(析碳反应)
生产中加氢反应及副反应均为放热反应,在操作中应控制好触媒层温度。
铁钼触媒主要的副反应是甲烷化反应,因此操作中要注意原料气中CO含量的变化。
(2)脱硫反应
①铁锰脱硫剂对H2S的吸收反应:
FeS+H2S=FeS2+H2
MnO+H2S=MnS+H2O
MnS+HkS=MnS2+H2
②氧化锌脱硫剂对硫的吸收反应:
ZnO+H2S=ZnS+H2O
2、转化原理
在焦炉气中加入水蒸汽,在一定压力及温度下,通过催化剂作用,生成合成甲醇有用的H2、CO及CC2。
转化反应:
Cf+H2O=CO+3H—Q
CO+HO=CQ+H2+Q
CH4=C+2H—Q
二、流程
1、精脱硫转化系统流程叙述
来自焦炉气压缩机(C201)的焦炉气含H2S<20mg/Nm3,有机硫250mg/Nm3,其压力为,温度100〜110C。
焦炉气通过两台并联的脱油剂槽(D106a、b)脱除掉焦炉气中的油水之后进入冷热交换器(E104),被来自铁锰脱硫槽D103aD103b的一级脱硫气第一次加热;然后进入原料气第一预热器(E101)被来自转化气废热锅炉(E105)的转化气第二次加热;再经原料气第二预热器(E102)被来自气气换热器(E103)的转化气第三次加热;最后进入加热炉B101被第四次
加热。
四次加热后焦炉气温度升至320C,进入两台并联的铁钼预加
氢槽(D101a、D101b)再进入一台铁钼加氢槽(D102)。
在铁钼触媒的作用下,焦炉气中绝大部分有机硫加氢转化成无机硫H2S,不饱和
烃加氢转化为饱和烃。
由铁钼加氢槽出来的焦炉气进入两台可并可串的铁锰脱硫槽(D103a、D103b),焦炉气中的大部分无机硫H2S被脱除(此焦炉气称为一级脱硫气)。
一级脱硫气经冷热交换器(E104)与原料气换热,温度降至360C之后进入镍钼加氢槽(D104),在镍钼催化剂的作用下,焦炉气中剩余的少量有机硫进一步加氢转化成无机硫,之后进入两台可串可并的氧化锌脱硫槽(D105),最终将焦炉气中的总硫脱除至小于(此焦炉气称为二级脱硫气,或净化气)。
净化气送往转化工序。
来自脱硫系统装置的净化气,总SW,配入中压蒸汽混合后进入气-气换热器E103被转化气加热后,进入开工加热炉B101b升温,温度至到500C,进入换热式转化炉H101管程在催化剂作用下CHI经过初步转化,混合气进入二段转化炉B102内,与从开工加热炉B101b来的热氧气混合燃烧,为二段炉催化剂内转化反应提供热量,二段炉出口转化气CH4<%,温度900C,进入H101壳程放热,为H101管程内初步转化反应提供热量,从H101壳程出来的气体,温度为600-700C,依次进入多个换热器、预热原料气、精馏液及副产中压蒸汽回收转化气热量,进换热器的次序为:
气-气换热器E103原料气第二预热器E102、转化废锅E105原料气第一预热器E101、第一锅炉给水预热器E106第一分离器F102及精馏主塔再沸器E405预塔再沸器E404脱盐水预热器E107及转化气水冷器E108,再进入第
四分离器F105,分离冷凝液后,转化气去循环压缩机供合成甲醇用
2、精脱硫转化方块流程
D106a——
焦炉气来自压缩
E104壳程E101壳程
D106b
D103a
D105b
E104管程
At
D104
At
■
•
■
D103b
D105b
V
E103壳程
B101b中间
H101管程
■
B102
■
H101
煤气盘管
壳程
第二节精脱硫系统催化剂的硫化与还原方案
一、原理及目的
1加氢催化剂的硫化原理及目的
加氢催化剂是指铁钼加氢催化剂与镍钼加氢催化剂。
加氢催化剂在使用前必须对其进行硫化,也即使其在较高温度下与H2S反应,催化剂则由氧化态变为硫化态,获得较高的活性。
硫化剂为H2S。
H2S来源于CS+H2的反应或者高硫焦炉煤气。
FeO+HS=FeS+HO+Q
MOO2+2H2S=MoS2+2H2O+Q
FezO3+2H2S+H=2FeS+3HO+Q
NiO+HtS^NiS+HO+Q
转化为FeS、M0S2的硫化态催化剂对有机硫加氢具有催化作用。
2、脱硫剂升温还原的原理及目的
脱硫剂是指铁锰脱硫催化剂与氧化锌脱硫催化剂。
脱硫剂的升温还原指的是铁锰脱硫剂的升温还原,即将氧化态的
铁锰与H2、CO反应,成为还原态的铁锰。
还原态的铁锰催化剂具有吸附H2S活性。
还原剂为焦炉气中的H2、CQ
铁锰催化剂还原反应:
MnO2+H2=MnO+H2O+Q
MnO2+CO=MnO+CQ+Q
3FQO3+H2*2Fe3O4+H2O+Q
氧化锌脱硫剂本身具有吸附H2S的活性,只需要升温,不需要进行还原操作。
3、转化催化剂升温还原的原理及目的转化催化剂的主要成分为镍。
厂家提供的催化剂为氧化态形式,使用前必须使其与巴、CO反应,将其还原成具有活性的还原态形式,同时脱除催化剂中少量的毒物(硫化物)。
还原剂为SW的合格焦炉气(H2、CO)。
还原反应如下:
NiO+H2=Ni+H2O-QNiO+CO=Ni+CO2+Q
3NiO+CH4=3Ni+CO+2H2O-Q
转化催化剂还原需在650C以上进行。
还原压力为~,空速40~60h-1,还原时间达规定温度后不小于8h。
还原初期要求水碳比5〜7,随还原过程的进行和结束水碳比逐渐调至正常。
二、脱硫转化系统升温
(一)升温
1、升温流程
脱硫转化系统升温用N2作为载体。
脱硫装置与转化系统串联进行升温。
流程如下:
空分来的低压N2经焦炉气压缩机C201压缩后,通过正路也即煤气管线依次进入油过滤器D106ab冷热交换器E104壳程、原料气第一预热器E101壳程、第二预热器E102壳程及开工加热炉B101a盘管进行加热
B101a出来后的热N2,沿N2升温线进入并联的单槽铁钼预加氢
槽,然后依次串联进入铁钼加氢槽D102、并联的铁锰脱硫槽D103ab、
镍钼加氢槽D104及并联的氧化锌脱硫槽D105ab。
从D105ab出来的N2沿主流程管线进入转化系统。
N2首先进入E103壳程,再进入开工加热炉B101b中间盘管进行再加热,再加热N2沿主流程依次进入一段转化炉H101管程、二段转化炉B102、一段转化炉H101壳程、气气换热器E103管程、原料气第二预热器E102管程、废热锅炉E105管程、原料气第一预热器E101管程、第一锅炉给水预热器E106管程、第一分离器F102、脱盐水换热器E107管程、转化气水冷器E108管程、第四分离器F105,最后进入新鲜气入口缓冲罐F203。
将F203来的N2与空分来的中压N2引入联合压缩机C202,启动C202,将压缩后的N2一部分与C201出口N2混合补充进入D106ab,—部分沿02管线直接进入B101b上层、与下层盘管加热后进入B102,与主流程N2混合,进入下一轮升温循环。
升温方块流程图:
放空放空放空
2.升温
开工加热炉点火开车依开车方案进行(见开工加热炉B101ab操作规程)。
(1)B101a升温速率控制
从C201来的N2温度约90〜100C,在B101a内被加热升温,升温速率控制在20〜50C/h。
通过B101a第一组盘管后温度计TI-126及第二组盘管后温度计TI-166观察温度;用HIC102a调节进B101a的燃料气量来控制升温速率。
N2流量依空分送来的气量,通过精脱硫煤气调节阀FRCA102控
制稳定。
(2)B102升温速率控制
经过加热升温脱硫催化剂后,温度降低的N2进入B101b中间盘
管继续加热,同时联压机C202送出的N2沿02管线进入B101b上层盘管与下层盘管加热,观察进入B102前后温度TI-116、TI-117及TI-112、TI-115,通过HIC102b调节进B101b燃料气量,控制其升温速率为20〜50C/h。
(3)压力控制
升温阶段系统压力可控制在〜。
3、升温、恒温阶段,脱除催化剂的吸附水
(1)空分N2量约2500〜3000Nm3/h,通过煤气流量调节阀FRCA102控制稳定其流量;通过HIC101b调节燃气量,控制B101a盘管出口气温度TI-166(TI-176)〉首先加热催化剂床层温度50C,调节床层升温
速率为20〜50C/h,通过升温管线对串联的脱硫转化系统进行升温
(2)当首先加热的D101ab床层温度升到120C时,打开D102升温线阀门,同时关小D101ab升温线阀,关闭D101ab出口阀,用其放空阀控制压力为〜,120C恒温2〜3小时。
D102催化剂则成为首先加热对象。
(3)当D102床层温度达120C时,打开并联的D103ab升温线阀,同时关小D102升温线阀,关闭D102出口阀,用其放空阀控制压力为〜,120C恒温2〜3小时。
并联的D103ab催化剂则成为首先加热对象。
(4)当D103ab温度达120C时,打开D104升温线阀,同时关小并联的D103ab升温线阀。
关闭D103ab出口阀,用其放空阀控制压力为〜,120C恒温2〜3小时。
D104催化剂则成为首先加热对象。
(5)当D104床层温度达120C时,打开关联的D105ab升温线阀,同时关小D104升温线阀,并关闭D104出口阀,用其放空阀控制压力为〜,120C恒温2〜3小时。
并联的D105ab成为首先加热对象。
(6)当D105ab床层温度达120C时,关小D105ab升温线阀,关闭D105ab出口阀,用其放空阀控制压力为〜,120C恒温2〜3小时。
同时,打开B101a后煤气正路阀,加热N2沿主流程CG-0112线进到D101ab前,通过大旁路CG-0136隔离脱硫装置后,进入E103壳程,对转化系统继续进行升温。
(7)当D105ab恒温2〜3小时后,(D105前面的催化剂120C恒温均已大于2〜3小时),再将D101ab到D105ab及转化系统串联,继续以30〜50C/h速率升温。
脱硫装置大旁路阀可用于调节转化系统温度。
(8)当D105ab升温到220C时,按
(2)〜(7)方式操作,220C各槽依次切除恒温4〜5小时。
转化系统则继续升温。
(9)转化系统温度达220〜250C时,恒温4〜5小时。
4、220C恒温4〜5h后,精脱硫装置各槽及转化系统运行状态。
(1)加氢催化剂
将铁钼预加氢槽D101ab铁钼加氢槽D102及镍钼加氢槽D104用N2保温保压,准备配含硫焦炉气进行升温硫化。
(2)铁锰脱硫剂
将铁锰脱硫槽D103abN2保温保压,准备配用过热蒸汽直接进入
D103ab继续升温,同时准备配入适量焦炉气作氢源进行铁锰催化剂
的还原。
(亦可待加氢催化剂硫化结束后再升温还原)
(3)氧化锌脱硫槽D105ab切除,用N2保温保压。
(4)转化催化剂
转化系统准备配入蒸汽升温。
即切除N2将中压蒸汽通过FFRCA102调节气量,通过E103旁路管线CG-0133^CG-0134,进入B101b中间盘管内加热,用于转化催化剂的升温。
三、加氢催化剂的硫化
(一)硫化条件及合格标准
1、系统N2置换合格
2、硫化剂为高硫焦炉气或焦炉气+CS。
本工艺采用焦炉气+CS。
气体中含S量:
〜%(vol),O2W%(vol%)
3、空速为200〜500h-1(空速:
气体标准m3气/m3催化剂•h)。
4、压力:
控制系统压力w
5、硫化合格标准:
加氢槽进出口气体中硫含量相等时,则加氢催化剂硫化结束。
(二)硫化
加氢催化剂硫化时,特别是采用CS,反应剧烈,要一槽一槽地进行。
1、铁钼预加氢、铁钼加氢及铁钼加氢催化剂串联硫化。
(1)将C201加压后的N2流程改走N2管道,即加压后的N2直接进入B101a盘管内加热后,沿升温线并联进入脱S各槽保温保压。
注:
铁钼预加氢槽D101只硫化一槽,另一槽隔离,待开车过程中加入少许含硫煤气逐渐硫化。
(2)启动备用煤气压缩机C201加压含硫焦炉气。
焦炉气沿主流程
与N2混合进入B101a盘管内加热,加热温度未达220C前煤气在
B101a后放空。
煤气温度达220C后沿主煤气流程线CG-0112进入D101a或b、D102,从D102出来的N2+煤气沿旁路进入D104对三个槽的加氢催化剂串联硫化,同时关闭D102、D104并联的N2阀。
硫化初始,控制焦炉气+N2中H2S较低含量,随着硫化反应的进行,逐渐减小N2量,加大焦炉气量,控制混合气量》3000Nm3/h。
因焦炉煤气含硫高,所以不可以进入D103ab与D105aboD103ab
用过热蒸汽继续升温,D105ab则切除用N2保温保压。
(3)向串联的铁钼预加氢槽D101a或b、铁钼加氢槽D102及镍钼加氢槽D104内导入含硫焦炉气,通过D104后的放空阀放空,在低压下进行硫化反应,压力控制在MPa。
(4)导入焦炉气后,调节B101a燃气量控制铁钼预加氢槽D101a或b床层温度为200〜220C,恒温1h以上,待催化剂床层温度均匀后,用N2将CS加压通过硫化线加入D101a或b。
控制升温速率30〜50C/h,升温到250C,恒温12〜24h或更长时间进行等温硫化。
硫化初期,配入CS后,分析入口气中H2S<10g/Nm3,即用未经湿法脱硫的焦炉气。
硫化主期,需逐步增加CS2量,分析入口气H2S<10〜20mg/Nm3。
注:
CS加入量通过流量计及分析数据控制初始加入量30L/h,缓慢增加。
(5)250C恒温12〜24h后,逐步关放空阀,将压力以〜h的速率提高到〜,继续硫化。
压力达到需求后,稳定1小时,以20°C/h升温速率,控制催化剂床层温度V350〜380C,恒温恒压12〜24h。
注意:
升压时不允许同时升温;同样,升温时不允许同时升压。
(6)B101a出口焦炉气温度根据催化剂床层温度调节。
使用CS硫
化时反应剧烈,放热量大,要控制D101a或b进口焦炉气温度为280〜300C(如果使用高硫焦炉煤气硫化,则控制D101a或b进口焦炉气温度为300〜320C)。
严格控制床层热点温度V450C,若有超温趋势,立即降低入口气温度,必要时打开冷激线CG-0200进D101ab的阀门
冷激降温(D106ab出口煤气-各加氢槽),均设有冷激线。
(7)当D101ab进出口硫含量基本相等时,则铁钼预加氢催化剂硫化基本结束。
然后通过调节B101a出口焦炉气温度逐渐提高床层温度至380〜400C,但最高不得超过450C,恒温2h。
分析D101ab进出口气体硫含量不变停止加入CS2,则铁钼预加氢催化剂硫化结束。
(8)铁钼预加氢催化剂硫化时,串联的铁钼加氢及镍钼加氢催化剂同时在硫化。
D101a或b硫化结束,切除D101a或b保温保压,按照同样的程序对铁钼及镍钼加氢催化剂D102、D104进行串联硫化。
D102、D104串联硫化时,将焦炉气温度及床层温度降到250C,加热焦炉气沿升温线进入D102内,再开始向D102内配入CS,以防温升太快。
2、放硫
放硫即将硫化过程中吸附在催化剂床层中的硫充分释放出来。
D104硫化结束后,将D101a或b、D102、D104串联起来,控制床层温度为380C左右,将系统压力逐渐降至〜,将焦炉气切换为湿法脱硫后的合格低硫(S<20mg/m3)焦炉气吹扫硫化后的催化剂。
吹扫催化剂要有足够时间释放床层中的fS,分析进出口H2S含量不变,则放硫结束。
放硫结束后,将系统压力逐步提高到MPa,关闭进出口阀及放空阀,保温保压。
注:
四个加氢槽的催化剂串联硫化时,硫化过程是按前后顺序一槽一槽地进行。
硫化反应首先在第一槽进行,当第一槽中催化剂吸附硫较多时,开始有H2S穿透,第二槽催化剂开始有较强的硫化反应。
串联硫化的温度最高点在首先硫化的第一槽即铁钼预加氢槽,控制好
其床层温度非常重要。
串联硫化时,热量及焦炉气利用充分。
第二槽开始硫化时,要先配入含S浓度较低的焦炉气,将入口气温度控制在250〜280C左右才可进行。
四、加氢催化剂硫化曲线及分析项目
1、加氢催化剂升温硫化及放硫曲线
温度范围
升温升压速率
时间
(h)
介质
流量
压力MPa
说明
常温-120C
20C/h
5-6
N2
3000-4000
驱赶水
120C
恒温
2-3
N2
恒温
1
未脱硫焦炉气
小气量
开始硫化
250C
30C/h
12-24h
未脱硫焦炉气
等温硫化
250C
h
焦炉气
+CS
硫化初期
250C
恒温恒压
1
焦炉气
+CS
硫化主期
350-380C
20C/h
12-24h
焦炉气
+CS
硫化主期
380-400C
20C/h
2
硫化末期
380-400C
h
放硫
380-400C
充分硫化
合格的湿法脱硫气
放硫
380-400C
h
合格的湿法脱硫气
保温保压
注:
1、升温还原曲线按厂家提供的方案执行
2、D101ab铁钼预加氢催化剂硫化时间约为70〜80小时。
3、精脱硫系统加氢催化剂全部硫化结束约130〜150小时
2、加氢催化剂硫化过程分析一览表
加氢催化剂硫化结束后,铁锰脱硫剂开始进行升温还原。
升温可以用N2作介质,也可以用过热蒸汽作介质。
本装置用N2作升温介质。
(一)升温还原过程控制
1.升温流程(以N2作为升温介质)
N2TC201—N2路线TB101a盘管内升温—升温管线进入
D103ab^放空
2.配焦炉气还原铁锰脱硫催化剂
1)还原流程
焦炉气TC201T焦炉气主线TCG-0107TCG-0108(B101a旁路,
即焦炉气不经加热)—D101ab前tCG-0140管线(还原线路)并联进
入D103abT放空
2)还原过程控制
(1)D103ab催化剂床层温度用N2维持220C,D103ab出口放空,控制系统尽可能低压力,一般控制为〜。
(2)系统配H2。
通过FRCA102阀调节焦炉气量,打开还原线路DN25旁路阀,控制焦炉气量FI-104,焦炉气与N2混合并联进入D103ab,严格控制起始浓度CO+Hw%。
即N2量控制3000Nm3/h,焦炉气量FI-104为30Nm3/h。
配氢时,控制焦炉气压力大于N2压力。
(3)配H2后每小时分析一次进出口COH2浓度,以观察还原进行程度。
控制床层温升10C/h,床层温度控制在250〜350C,若还原激烈,温升过快,可通过MS-0109管线阀门加入过热蒸汽调节降温或者调节B101a出口N2温度,以控制温升。
(4)根据床层温度及进出口H2浓度变化情况,逐步提高H2浓度,通过提H2浓度,控制床层温度》350C,但最高不超过400C。
注:
提高氢量时不允许同时提高温度,提高温度时不允许同时提高氢量。
(5)当床层热点下移,温度在350C,H2浓度在20%左右,进出口H2浓度消耗无明显变化时,恒温10〜16h,然后逐渐减小蒸汽量至全停蒸汽,同时减小N2量控制混合气量中H2浓度为20%,提高H2浓度1h后无明显温升,无反应水析出,无H2耗,则还原结束。
注:
铁锰催化剂升温还原,也可全部采用过热蒸汽作载体配焦炉气进行。
过热蒸汽温度TI-1302控制在300〜340C为宜(此温度由电厂来的蒸汽决定)。
不允许带水,升温速率控制为20〜30C/h。
(二)升温还原安全注意事项
1升温速率严格按供货商提供的升温速率控制,一般控制为20〜40C/h。
2、当床层温度达250〜350C时,要密切注意,有可能出现温度飞升现象,此时要立即减少配氢量,放慢升温速率,同时加大蒸汽量,增大放空量,及时移走反应热。
3、严格要求焦炉气中02W%,否则催化剂床层会出现超温而损坏。
(三)铁锰催化剂还原曲线及分析项目
1、升温速度控制表(升温曲线,以热点为准)
温度C
速率C/h
时间
压力
介质
说明
常-120
20
5
N2
出水、升温
120
恒
8
N2
出水、升温
120-270
10
8
蒸气
升温
270
恒
10
蒸气+焦炉气
开始还原
270-400
15
13
蒸气+焦炉气
还原
400
恒
15
焦炉气
彻底还原
累计
60
注:
升温还原曲线以厂家提供的方案为准。
2、铁锰还原过程分析项目
序号
位号
取样地点
分析项目
分析频次
CO
CO
2
H2
CH
4
02
N2
S
1
S-101
D106ab前
每半小时分析一次CO
2
S-105
D103a后
02、H2,其余依要求分析。
3
S-106
D103b后
六、氧化锌脱硫剂
氧化锌脱硫剂不需要还原操作。
在加氢催化剂硫化及铁锰脱硫剂还原期间,将其切除用N2保温保压。
待加氢催化剂硫化及铁锰脱硫剂还原结束后,氧化锌槽串入升温流程,用N2升温,以50C/h速率
升温,温度升到320〜350C,恒温4小时。
七、精脱硫全流程
1、氧化锌320〜350C恒温四小时,至此,精脱硫催化剂的升温