转炉汽包自动化及传动改造技术方案.docx
《转炉汽包自动化及传动改造技术方案.docx》由会员分享,可在线阅读,更多相关《转炉汽包自动化及传动改造技术方案.docx(13页珍藏版)》请在冰豆网上搜索。
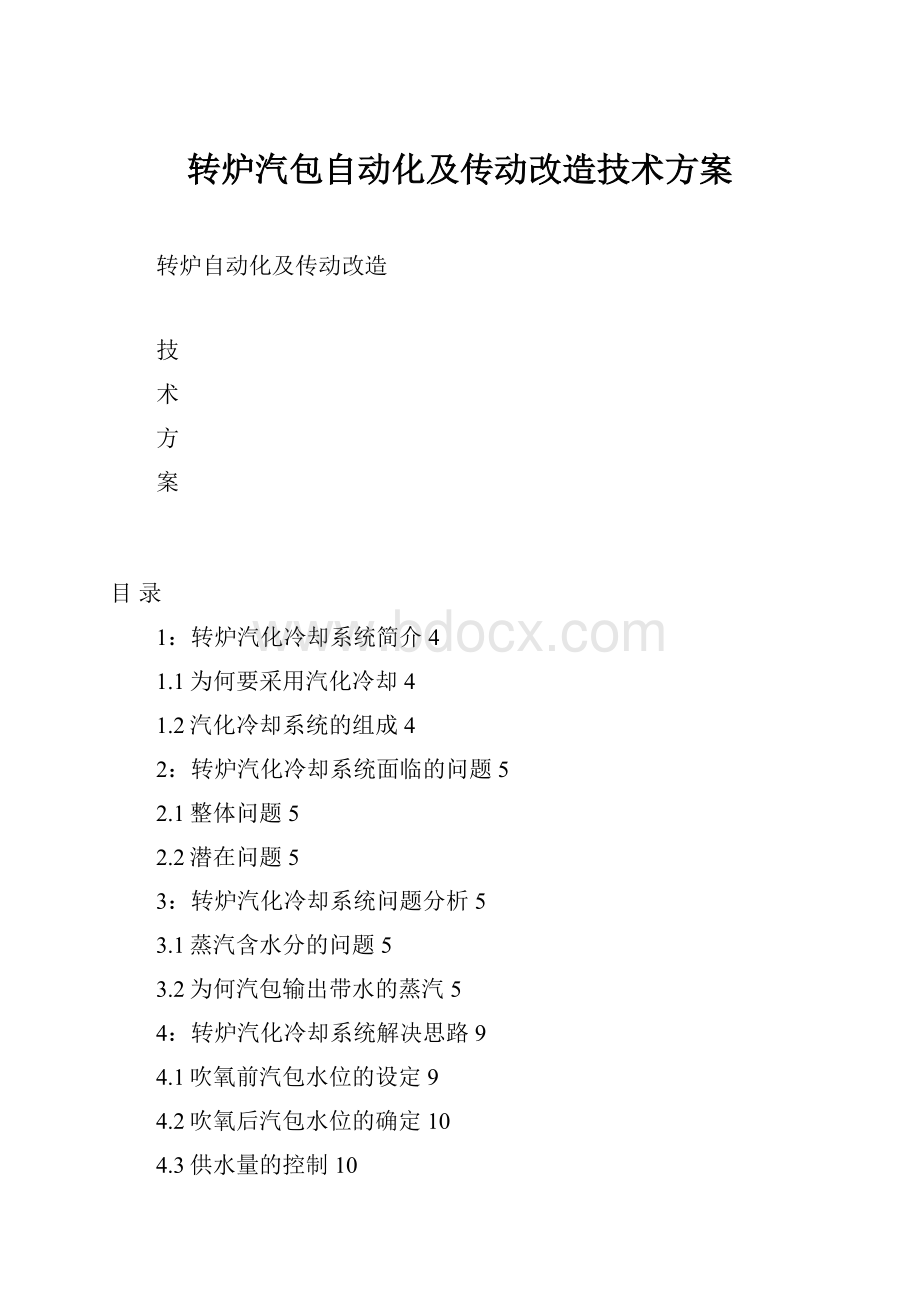
转炉汽包自动化及传动改造技术方案
转炉自动化及传动改造
技
术
方
案
目录
1:
转炉汽化冷却系统简介4
1.1为何要采用汽化冷却4
1.2汽化冷却系统的组成4
2:
转炉汽化冷却系统面临的问题5
2.1整体问题5
2.2潜在问题5
3:
转炉汽化冷却系统问题分析5
3.1蒸汽含水分的问题5
3.2为何汽包输出带水的蒸汽5
4:
转炉汽化冷却系统解决思路9
4.1吹氧前汽包水位的设定9
4.2吹氧后汽包水位的确定10
4.3供水量的控制10
5:
转炉汽化冷却系统的传动11
5.1目前的传动配置11
5.2工频传动的缺点12
5.2针对工频缺点相应的解决方案13
6:
完善转炉汽化冷却系统的基本条件13
6.1检测仪表方面的要求13
6.2执行机构方面的要求14
6.3传动设备方面的要求14
6.4PLC方面的要求14
6.5本体设备方面的要求15
6.6其它方面的要求15
7:
转炉汽化冷却系统的改造预算15
7.1PLC改造工期及费用15
7.2变频柜改造工期及费用15
1:
转炉汽化冷却系统简介
1.1为何要采用汽化冷却
冷却技术是利用水汽化吸热,带走被冷却对象热量的一种冷却方式。
受水汽化条件的限制,在常规条件下汽化冷却只适用于高温冷却对象。
我们知道,对于同一冷却系统,采用液态令缺水温度上升所带走的热量,远远小于液态水汽化所带走的热量。
因此采用汽化冷却,可以大大减少冷却水补充水量。
另外,汽化冷却所产生的蒸汽还可以利用,或者并网发电,可以为企业节省或再生大量能源。
1.2汽化冷却系统的组成
通常情况下,转炉汽化冷却系统包括以下几个部分:
●转炉汽化冷却烟道
●汽包
●蓄热器
●汽水分离器(归电厂)
●冷凝水泵(归电厂)
●除氧器
●给水泵
●汽化冷却传动系统
●汽化冷却PLC及上位系统
2:
某公司转炉汽化冷却系统面临的问题
2.1整体问题
1、在实际的运行过程中,转炉汽化冷却系统向电厂汽轮机供送蒸汽的过程中,屡次出现蒸汽含水量偏高。
2、给水泵在运行的过程中,给水泵电机出现工艺上的频繁启停,造成机械设备的过度损耗和能源的浪费。
2.2潜在问题
1、检测仪表和执行元器件不能精准检测和正确执行。
2、控制程序不完善。
3:
某公司转炉汽化冷却系统问题分析
3.1蒸汽含水分的问题
蒸汽所含的水分,经过我们现场调查与深入分析,可能与以下两个因素有关:
1、蒸汽在输送过程中,由于温度的下降,是过热蒸汽变为饱和蒸汽,继而导致冷凝水的出现。
2、在汽包的蒸汽输出过程中,直接带入了液态水。
从现场的分析来看,第二条是主要原因。
3.2为何汽包输出带水的蒸汽
1、转炉汽化冷却的特点
转炉汽化冷却与其它场合的汽化冷却(如加热炉等)是具有明显的不同。
其中最大的特点就是,它随着在冶炼周期的不同阶段,其吸收热能的幅度有极大的变化。
以一台120T的转炉生产为例,转炉一次的炼钢周期为35分钟左右,吹氧时间段在炼钢周期的中期,用时大约在15分钟左右,在吹氧期间,进入余热锅炉的炉气量可达76000Nm3/h,温度高达1650℃。
从转炉兑铁水开始到吹氧强度达到工作值,炉气量和炉气温度迅速增加。
余热锅炉的热负荷将从极低值升到极高值,热负荷呈陡然上升趋势,锅炉的产气量也迅速增加,瞬时最大产气量可达100t/h。
当转炉停止吹氧后,余热锅炉的热负荷迅速下降至最低,直到下一个吹炼周期开始热负荷再次增加,这个期间大约在20分钟左右。
显然,炼钢工序中受吹氧时间和吹氧强度的变化影响,转炉余热锅炉的热负荷是不稳定的,周期性的。
这使得转炉余热锅炉运行工况是复杂的、多变的,并直接反应在汽包水位的变化上。
2:
冶炼周期内汽包水位的变化情况
转炉吹炼周期内水位变化趋势图
上图是一个典型的转炉余热锅炉汽包水位变化的趋势图(冶炼周期以某炉钢水吹氧至下一炉钢水吹氧)。
我们根据转炉冶炼的工艺特点,结合余热锅炉的运行和汽包水位的变化情况,将冶炼汽包的水位变化分为五个阶段:
1)冶炼前期;
2)吹炼中期补水前;
3)吹炼中期补水后;
4)冶炼结束期;
5)补吹期;
从图中我们可以看到:
1)冶炼前期的水位变化(0-200S)
从第二张图可以看到,吹炼开始前200S,汽包的水位增幅很大,水位增速可达1mm/s,水位增加了210mm左右。
同时,蒸汽流量增幅也很大,可达40t/h。
2)冶炼中期补水前的水位变化(200-300S)
汽包水位在冶炼前达到高水位后,锅炉尚未开始补水前,汽包水位有明显的回落,但回落幅度不大,约为50mm,水位下降速度比前一阶段上升速度要小,约为0.5mm/s,此时蒸汽产量继续上升至大于40t/h。
3)冶炼中期补水后的水位变化(300-850S)
当锅炉开始补水后,补水量约为50t/h,汽包水位回落势头减缓,水位稳定在130mm左右,但在稳定一段时间后(约200S)有逐渐回升现象,此时蒸汽产量稳定于40t/h一段时间后,在后半期有大幅提高,达到50t/h。
4)冶炼后期的水位变化(850-1000S)
当冶炼停止吹氧后,汽包水位下降幅度明显,约为200mm,且下降速度快,约为0.5mm/s。
蒸汽产量也急剧回落,150S内从50t/h下降到15t/h。
5)补吹期的水位变化(1000-1050S)
在补吹期阶段,汽包水位和蒸汽产量均出现急涨急回现象,水位变化率为4mm/s,蒸汽流量变化率4.6t/h/s。
3:
现象分析
毫无疑问,汽包水位的变化显然是由锅炉汽水容积的变化引起的,而锅炉汽水容积的变量因素比较多,但其根源在于转炉炉气热负荷的变化。
当转炉在非吹氧期,余热锅炉的下降管、受热管及上升管中充满了水;当转炉开始吹氧后,受热管中的水开始蒸发,形成汽水混合物,体积急剧膨胀,导致汽包内的水位急剧上升。
吹炼结束,余热锅炉就停止运行,受热管中的水停止蒸发,由吹氧期间的汽水混合物变为水,体积急剧缩小,导致汽包水位急剧下降,形成汽包水位的波动空间。
由此可见,水位波动空间的形成与吹氧紧紧的联系在一起。
由于转炉生产中余热锅炉频繁启动和停炉,使汽包水位频繁上升和下降。
4:
水位升降幅度
水位升降到底有多大?
它与以下因素有关。
1)与转炉的容量有关,转炉容量越大,在吹氧期间产生的炉气量就越大,进入余热锅炉的余热资源量就越大,余热锅炉受热管中产生的蒸汽量就越大,当然体积膨胀量就越大,导致汽包水位上升的幅度就越大。
2)与转炉在吹氧期间的脱碳速度有关。
脱碳速度越高,单位时间内产生的炉气量就越大,单位时间内进入余热锅炉的余热资源就越大,余热锅炉受热管中产生的蒸汽量就越大,体积膨胀就越大,导致汽包水位上升的幅度就越大。
3)与转炉在吹氧期的不同阶段有关。
当转炉开始吹氧时,转炉熔池内铁水的温度相对比较低,因此产生的炉气温度也相对比较低,余热锅炉受热面的热强度也相对比较低,产汽量就比较少,汽包水位上升的幅度就比较小。
当转炉吹炼进入中期,熔池中铁水的温度相对较高,同时,供氧强度增到最大,此时不但炉气温度相对比较高,而且炉气量也达到最大值,当然锅炉的蒸发强度也达到最大值,此时,汽包的水位上升幅度也达到最大值。
当转炉吹炼进入后期,虽然此时熔池温度达到最大值,但是,供氧强度开始下降,炉气量减少,此时,锅炉的蒸发强度也开始降低,汽包水位由最高值开始下降。
4)与转炉煤气是否回收有关。
转炉在吹炼过程中产生的炉气中的CO,在吹炼的前烧期和后烧期内,为了尽可能减少CO对大气的污染,要求在余热锅炉内尽可能将炉气的CO都烧掉,这样,余热锅炉除了吸收炉气的物理热,还要大量吸收CO燃烧的化学热,余热锅炉炉膛内最高理论燃烧温度可以达到2600℃,此时,余热锅炉的蒸发强度达到最大值,也就是汽包水位上升幅度达到最大值。
当转炉吹炼进入回收期,为了提高回收的转炉煤气的质量,希望在余热锅炉内CO的燃烧份额越少越好,因此,炉膛内燃烧温度比最高理论燃烧温度低得多,余热锅炉蒸发量就减少,汽包内的水位上升幅度就比较低。
5)与余热锅炉受热面面积有关。
在同等炉气条件下,锅炉受热面越大,则吸热量就越大,锅炉的蒸发量也就越大,汽包水位上升幅度也越大。
6)与汽包容积有关。
在冶炼条件、锅炉受热面面积相同的条件下,汽包容积越大,水位上升的幅度就越小,汽包容积越小,水位上升幅度就越大。
这是因为在蒸发量相等的条件下,水蒸气体积的膨胀是一定的,容积越大,水蒸气体积的膨胀量占整个汽包体积的比例就越小,因此水位上升的幅度就小,反之越大。
综合上述分析,可以看出,汽包水位的升降,是由多方面因素决定的。
在转炉生产周期的不同不同阶段,出现大的水位波动,也就是人们常说的假水位,这在其它锅炉只有在启停阶段才会出现,平常是不可能出现的,这也就是转炉余热锅炉与其它锅炉的不同之处。
4:
某公司转炉汽化冷却系统解决思路
4.1吹氧前汽包水位的设定
吹氧前汽包内水位的设定非常重要。
如果水位设定过低,当出现突然中止给水时,汽包内的有效水容积很难保证一炉钢顺利炼完,锅炉有烧干锅的危险;如果吹氧前水位设定过高,当吹氧后水位进一步提高,汽包内的汽空间减少,影响汽水分离效果,造成蒸汽带水而恶化蒸汽品质;另外由于汽包在高水位线上运行,给水调节阀门在吹氧后的较长时间内不会开启,造成汽包在吹氧后的较长时间内不能补水,如果给水调节阀门在吹氧即将结束的时候才能开启,就有可能因补水需要较长时间而影响下一炉钢的吹炼,直接影响转炉生产。
再有,吹氧后汽包内的水位过高,就有可能将上升管管口埋入水中,上升管中带来的循环动能使汽包内的水位更加不稳定,增大水位的波动范围,使汽包内的汽空间进一步减小,蒸汽品质进一步恶化,同时有可能使汽包内的一次汽水分离装置受到破坏,一次汽水分离失去作用,蒸汽品质更加恶化。
如果汽包在高水位线上运行时,上述几种不利工况同时出现,除了影响转炉炼钢外,蒸汽带水必然十分严重,影响蒸汽管道的安全运行,在实际生产过程中,很容易发生因转炉余热锅炉蒸汽带水严重造成水击使蒸汽管道破坏的现象。
由此可见,吹氧前汽包水位设定的准确与否,对锅炉的安全运行,蒸汽的品质起着决定性的作用。
吹氧前汽包水位的正确设定是转炉在吹氧期间突然中止锅炉给水的情况下,汽包的有效水容积能保证一炉钢顺利炼完再加适当地裕量,也就是炼一炉钢期间余热锅炉的蒸发量再加适当地裕量即可。
4.2吹氧后汽包水位的确定
吹氧后汽包水位的确定,应该是吹氧开始三分钟后汽包水位的确定。
因为吹氧一开始,余热锅炉受热面中形成汽水混合物需要一定的时间,汽水混合物流到汽包也需要一定的时间。
待吹氧三分钟后汽包的水位已经上升的相对平稳的位置,此时汽包内的水位比吹氧前上升约200-250mm,即汽包中心线上约200mm的位置,以此水位定位吹氧后的汽包水位。
随后蒸汽不断向外排放,水位不断下降,给水调节阀门自动开启,不断向汽包内补水,使汽包内的水位稳定在汽包中心线上约200mm的位置上。
也就是供水量与蒸汽排放量相等。
吹氧结束后水位开始下降,仍然回到吹氧前的水位线上。
保持了供水量与蒸汽排放量的相对平衡,实现了供水量的最佳控制。
使汽包内部有了足够的汽水分离空间,从而保证汽水分离的效果,达到保证蒸汽品质的目的。
4.3供水量的控制
为了实现供水量与蒸汽排放量的相对平衡,控制供水量是十分必要的。
一般情况下,供水量的调节采用三冲量控制,给水流量调节阀的开度自然就会按照蒸汽排放量进行调节。
如果供水量只是按照单冲量控制方式,且只是依据汽包水位进行调节,那么就应该设定最大供水流速,也就是说,最大供水流速的设定实际上已经决定了给水流量调节阀的最大开度。
之所以要设定最大给水流量,就是为了严格保证实现吹氧前后设定的水位。
这是因为最大给水流量不受控制,实际上就是调节阀的最大开度不受控制,当水位一旦低于设定水位时,调节阀就有可能开到最大值,大量的给水涌进汽包,水位就难以控制,一旦水位高于设定水位,就必须采用汽包放水的方式来降低水位,造成给水的浪费;也有可能使汽包内的水位达到报警线,影响锅炉的安全运行,也影响到汽水分离的效果。
同时,如果车间内同时有几台转炉在吹炼而同时需要补水时,就会因调节阀给水流量不受控制,而给水泵能力不足而导致其它转炉得不到补水而危及锅炉的安全运行或转炉的正常冶炼。
最大给水流量的设定,应该按照锅炉的最大蒸发量决定。
严格地说,应该由锅炉的蒸发量、汽包水位、给水量三个因素同时决定,才能严格控制水位和最经济合理的给水流量,因此转炉余热锅炉汽包的给水调节阀应采用三冲量调节方式。
对于单冲量调节阀设定最大给水流量,只是保持蒸发量与给水量基本平衡。
实际上,在转炉的整个吹氧期内,蒸发量的变化是很大的,因此依靠单冲量调节阀来保持蒸发量与给水量的动态平衡是不可能实现的,转炉余热锅炉的给水阀应采用三冲量调节方式。
5:
转炉汽化冷却系统的传动
5.1目前的传动配置
目前采用工频驱动的方式,对3台90KW的进水泵进行驱动。
5.2工频传动的缺点
在汽包进水泵采用工频控制时,会出来一下几方面的问题:
●调节阀的问题
转炉余热锅炉的给水控制主要靠给水调节阀采用二冲量或三冲量调节给水,由于蒸汽流量的不稳定性及汽包水位的波动,造成给水调节阀的频繁动作。
同时,调节阀前后压差变化大,对调节阀的使用寿命造成很大的影响。
●给水泵的起停问题
在转炉炼钢过程中,由于给水的间断性,在冶炼中当给水调节阀处于关闭状态下,给水泵是否要关闭?
如果关闭给水泵,由于每个冶炼周期大约35分钟,那么给水泵每天需要数十次起停,不但对给水泵寿命造成非常大的影响,同时对电网造成一定量的冲击。
如果给水泵不关闭,给水再循环管路就要一直开启,25%~30%的给水流量回流到除氧器,此时,泵在高扬程下最小流量运行,造成给水效率下降及能源的浪费。
●给水压力的问题
通常转炉汽包的工作压力在2.5MPa,给水泵扬程的确定也是以此为基础的。
要求高于汽包压力0.5MPa,并考虑管路阻力损失,一般泵的扬程在330~370米左右。
但在吹炼过程中,汽包的压力是一个不断变化的过程,吹炼开始时,汽包压力约为0.8~1.5MPa,随着吹氧强度的增加,逐步到达工作压力(2.5MPa),维持一段时间随着吹氧的结束,汽包压力很快回落到初始压力。
当调节阀开度减小时,给水调节阀前后压力升高,调节阀前后压差很大,最大超过2MPa,远高于一般设计要求的0.5MPa,不但造成能量的浪费,而且使得水泵的振动和磨损加大,寿命缩短。
5.2针对工频缺点相应的解决方案
我们上面分析了工频供水的一些缺点,这里提出解决方案,就是将变频给水的方式引入炼钢转炉余热锅炉的给水控制中,这是一种非常理想的方法。
水泵运行遵循如下规律:
流量Q与转速N成正比,扬程(压力)H与转速N的平方成正比,轴功率与转速N的三次方成正比,电动机的同步转速N=f*60/p,其中f为供电频率,p为极对数。
由上式可知,改变电机的供电频率即可改变水泵的转速,从而达到改变水泵机组出水流量、扬程与电机输入功率的目的,这就是变频调速供水技术。
水泵采用变频调速后,给水流量的调节就可通过改变转速的方法来实现,此时调节阀开到较大开度,既能方便地调节流量,又可降低能量消耗,使这一问题获得圆满的解决。
同时,调节阀关闭时,给水泵最小流量运行时采用低转速,降低能量消耗的同时,对给水泵也能起到保护作用。
如果采用变频控制,建议变频器采用ABB的ACS800-01的产品,留有适当地裕量,配置3套ACS800-01-0135-3的产品,轻载驱动为110KW。
断路器采用施耐德的250A塑壳断路器。
如果电机距离变频器超过100米,可以加出线电抗器。
三套传动柜之间互为备用(取决于工艺管道的设计)。
6:
完善转炉汽化冷却系统的基本条件
6.1检测仪表方面的要求
●要求汽包液位测量准确,有2个或者两个以上的液位测量点。
●要求汽包压力测量准确。
●要求汽包温度测量准确
●要求出汽流量测量准确。
●要求补水流量测量准确
●要求进水总管压力测量准确
●其它就地显示的仪表(如温度、压力、液位、流量等)显示正确。
6.2执行机构方面的要求
●要求汽包蒸汽出口调节阀运行准确。
●要求补水流量调节阀运行准确。
●要求紧急放散阀运行可靠。
●要求紧急排水阀运行可靠。
●要求机械安全放散阀运行可靠。
6.3传动设备方面的要求
●要求传动柜或变频柜运行准确可靠。
●如果是变频系统,需要变频系统工作正常。
6.4PLC方面的要求
●要求PLC运行准确可靠。
●要求PLC有充裕的I/O点用于功能扩展。
●要求PLC源程序代码开放。
●要求新加I/O点电缆敷设完毕并正确可靠。
●要求有编程平台。
●要求炼钢厂吹氧信号及补吹信号能够到达PLC。
6.5本体设备方面的要求
●要求汽包内汽水分离器工作正常。
6.6其它方面的要求
●要求有最近一个月的各种运行参数的趋势记录。
7:
转炉汽化冷却系统的改造预算
7.1PLC改造工期及费用
PLC改造的费用大约需要20万左右,其主要费用在于过程的调研、方案制作、现场实施以及风险承担。
施工工期大约在一个月左右,其中三分之二时间在于前期的考察调研和方案分析。
7.2变频柜改造工期及费用
变频柜改造的费用大约需要30万左右,其主要费用在于硬件的设计、采购、成套、运输及调试。
施工工期大约在一个月左右。