汽车车身设计现状及发展.docx
《汽车车身设计现状及发展.docx》由会员分享,可在线阅读,更多相关《汽车车身设计现状及发展.docx(78页珍藏版)》请在冰豆网上搜索。
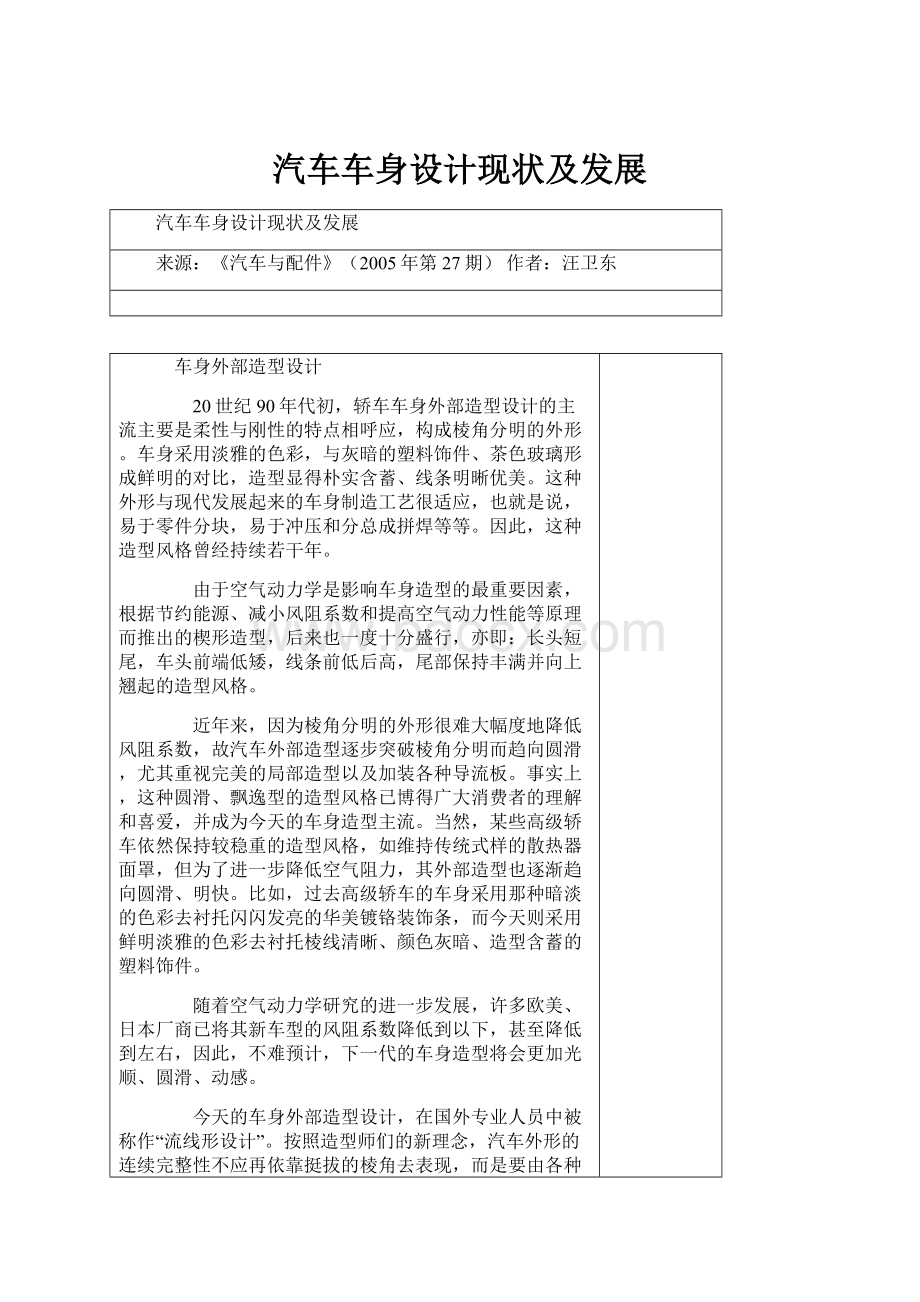
汽车车身设计现状及发展
汽车车身设计现状及发展
来源:
《汽车与配件》(2005年第27期)作者:
汪卫东
车身外部造型设计
20世纪90年代初,轿车车身外部造型设计的主流主要是柔性与刚性的特点相呼应,构成棱角分明的外形。
车身采用淡雅的色彩,与灰暗的塑料饰件、茶色玻璃形成鲜明的对比,造型显得朴实含蓄、线条明晰优美。
这种外形与现代发展起来的车身制造工艺很适应,也就是说,易于零件分块,易于冲压和分总成拼焊等等。
因此,这种造型风格曾经持续若干年。
由于空气动力学是影响车身造型的最重要因素,根据节约能源、减小风阻系数和提高空气动力性能等原理而推出的楔形造型,后来也一度十分盛行,亦即:
长头短尾,车头前端低矮,线条前低后高,尾部保持丰满并向上翘起的造型风格。
近年来,因为棱角分明的外形很难大幅度地降低风阻系数,故汽车外部造型逐步突破棱角分明而趋向圆滑,尤其重视完美的局部造型以及加装各种导流板。
事实上,这种圆滑、飘逸型的造型风格已博得广大消费者的理解和喜爱,并成为今天的车身造型主流。
当然,某些高级轿车依然保持较稳重的造型风格,如维持传统式样的散热器面罩,但为了进一步降低空气阻力,其外部造型也逐渐趋向圆滑、明快。
比如,过去高级轿车的车身采用那种暗淡的色彩去衬托闪闪发亮的华美镀铬装饰条,而今天则采用鲜明淡雅的色彩去衬托棱线清晰、颜色灰暗、造型含蓄的塑料饰件。
随着空气动力学研究的进一步发展,许多欧美、日本厂商已将其新车型的风阻系数降低到以下,甚至降低到左右,因此,不难预计,下一代的车身造型将会更加光顺、圆滑、动感。
今天的车身外部造型设计,在国外专业人员中被称作“流线形设计”。
按照造型师们的新理念,汽车外形的连续完整性不应再依靠挺拔的棱角去表现,而是要由各种曲面光滑的连接以及微妙的光学效果与视觉效果显示出来。
根据这种理念设计出来的车型,其显著的优点就是可获得甚至更低的风阻系数。
众所周知:
普通汽车在换档行驶时,发动机的功率和燃料大部分都消耗在克服空气阻力上(约占汽车总阻力65%),而具有”连续流动”曲面光滑的外部造型的轿车就可采用功率较小的发动机而达到较高的行驶速度,从而节约燃油消耗。
这种车身造型设计的最大特点就是弯曲的大弧面,其模型制作要用玻璃纤维或碳纤维。
车身内部设计
从“舒适”到“愉快”
力求精致、考究、装备齐全,内饰设计从强调“舒适”到重视驾乘的“愉快”、“享受”是近年来车身内部设计的特点。
大量采用柔性的内饰设计。
内饰装备和覆盖物的造型都比较圆滑,恰好与外形发展的趋势相呼应。
面料和座椅软垫一体化成型的座椅,整体模塑成型的仪表板和复合材料饰板给人以精致、明快的感觉,而内饰面料触感柔软则给人以和谐、舒坦的视觉效果。
总之,软化的内饰不仅是舒适的需要,而且也是安全的需要。
座椅可说是保证乘员舒适性的最重要的装备。
座椅的设计和布置首先要保证乘客的坐姿符合人体工程学。
然而,一个座椅要满足各种体形的人,就得能够对座椅从各个方位进行调节。
愈是讲究的座椅,调节机构就愈复杂。
现代汽车座椅的调节方式有10种之多,例如,座垫的升降调节、靠背角度与腰部支撑的调节、头枕的角度与高度的调节、座椅左右侧支撑与靠背左右侧支撑的调节、整个座椅的前后移动与回转的调节等等。
为了使座椅适合各种身材的人,就要按照人体工程学和数理统计原理对座椅的调节方式和调节范围进行精确的计算并设计,同时保证车身内部空间的尺寸尽可能紧凑。
按照现代车身内部设计的趋势,讲求“愉快感”比“舒适感”更为强烈。
因为在车身内部所采用的音响设备、电视、无线电话以及小型冰箱等设备其实与乘客舒适性的几项常规评价指标毫不相干。
随着旅游的兴旺发达,“娱乐型”汽车的概念应运而生。
显然,消费者已不只满足于“舒适”地坐在汽车内,他们希望所购的汽车不但能容纳长度较大的滑雪板,而且还可作为“移动的野营帐篷”等等。
消费者的意愿给车身设计师们提供了一个广阔的设计想象,如日本新一代本田“市民”厢式车就是一个较成功的例子,其总长只有4106mm,但其车厢内部空间却比较大,该车的座椅经过精心设计,在后排座椅折叠的情况下,足以容纳各种旅行用具及物品,此外座椅还可移动和摊平,拼成卧铺。
这款汽车不但性能优良,而且既实用又经济,加上价格较低,已成为日本新生代喜爱的畅销车。
良好的安全性
近年来,车身碰撞安全性显得愈来愈重要。
这是因为,目前世界上每年不少人在汽车碰撞事故中丧生,而且这个数字在逐年增加。
因此,无论是设计师或是消费者都把安全性作为衡量汽车优劣的重要依据。
白车身的主要防护原则是周边柔软而客舱刚硬,即白车身的刚性由周边至乘员舱逐渐增大。
这样在车碰撞时,车身的周边产生一定的损坏和变形以便吸收碰撞能量,但尽量使乘员舱不变形和完好无损。
依据这个刚度分配原则,近年来,国外厂商对白车身的结构进行了大力研发。
例如:
日本的日产和丰田公司采用了局部加强的方法,对前风窗支柱、侧围上边粱、后门后支柱等拐角部位均增添了加强板,以确保在车身轻量化的前提下使白车身刚度分配更趋合理。
又例如,德国梅塞德斯一奔驰的各种轿车采用了双重翻边的支柱,保证了车门在汽车碰撞后不会被“卡”住,车身呈腰鼓形的造型可使汽车在侧翻时顺利地翻滚从而逐渐消耗动能和缓和冲击,以避免汽车在翻车时会被突然“卡”住而使车身砸扁。
车身内部的防护原则是力求避免在汽车碰撞时乘员与车身内部刚硬的零件相撞击。
安全带是保护乘员最有效的装备。
梅赛德斯一奔驰公司在各种轿车的转向盘中都装备了发全气囊,在前、后排各个座椅上都配备了三点式安全带。
安全气囊和安全带均由同一套电子装置控制。
在汽车发生碰撞时,安全气囊充气,安全带自动张紧以起到应有的保护作用。
为了使乘客在座椅各种不同的调节位置都能正确地佩带安全带,该公司把安全带插扣设计在座椅上。
此外,依据车身内部安全防护原则,在车身内部尽可能安装柔软的内饰而取消带有棱角的造型,如采用耐冲击而富弹性的夹层玻璃等等。
座椅头枕是避免乘客颈椎受伤的重要防护装备,近年来的设计主要集中在使头枕具有足够的高度以及正确的角度和形状。
此外带有孔油的头枕可改善后部的视野,预计这种形式的头枕将逐渐增多。
新材料与新技术带来传统车身造型设计与制造工艺的挑战
现行钢制车身制造工艺的核心部分是冲压工艺和焊接工艺。
用各种冲压设备组成的车身部件生产线具有效率高和精度易保证等显著优点。
焊接生产线的构成有多点焊机为主的车身分总成装配线和以计算机操纵的机器人焊机为骨干的车身总装配线。
这种焊接机器人在整个车身厂所使用的机器人中占50%以上。
这样的车身总装配线“柔性”化很强,只须修改计算机的运行程序就可以改变机械手的点焊操作程序,也就是说,可在同一条车身焊接装配线上生产不同车型的车身。
毫无疑问,这种完善且有效的生产方式将会延续很长时间。
不过,从最新发展趋势来看。
新材料与新技术的应用,正在挑战以上传统车身造型设计与制造工艺。
新材料和新技术的出现,促使车身设计师们在突破传统的车身结构和生产方式方面进行了更多的探索和尝试。
如英国利兰TX-450型载重车,其车身造型独特,采用计算机全面控制焊装设备,驾驶室采用碳纤维材料制成,其车厢底板、底板横梁和车架纵梁全部由复合铝型材制成并相互连接成刚性的半承载系统。
小密度材料和新颖结构的使用使车身质量大幅度变轻,而采用较小的轮胎则降低了汽车的重心和车厢的装载高度。
如德国尼奥普兰设计的新型大客车,其车身取消了金属骨架,整个车身由碳纤维材料分成左右两半模压制成:
后围没有了后窗玻璃以便提高车身的刚度。
这样的车身有两个显著优点:
质量大幅度减轻和耐蚀性强。
由于车身很轻,不但可以采用尺寸较小的悬架和轮胎,而且还可以采用较小的发动机、传动系和其它底盘总成。
虽然该车的总长度是,但比同等尺寸的普通大客车轻三分之一;该车地板离地高度仅320mm,整车高度大幅降低,只有2560mm;其动力性和燃料经济性都比普通大客车好得多。
由于耐腐蚀性强,预计车身的使用寿命可达20年。
虽然使用碳纤维材料使车身的造价升高,但汽车的营运费用却显著降低,因此其经济效益仍十分可观。
上述两种车型的车身在一定程度上代表了车身设计发展的某种趋势。
由于车身材料及其结构的革新,加上底盘和整车布置的改进,使得汽车的性能大幅度提高。
不过,革新后的车身结构难以用现行的车身制造工艺制造,故仍有人怀疑其市场前景。
汽车车身新材料的应用及发展趋势
newmaker
现代汽车车身除满足强度和使用寿命的要求外,还应满足性能、外观、安全、价格、环保、节能等方面的需要。
在上世纪八十年代,轿车的整车质量中,钢铁占80%,铝占3%,树脂为4%。
自1978年世界爆发石油危机以来,作为轻量化材料的高强度钢板、表面处理钢板逐年上升,有色金属材料总体有所增加,其中,铝的增加明显;非金属材料也逐步增长,近年来开发的高性能工程塑料、复合材料,不仅替代了普通塑料,而且品种繁多,在汽车上的应用范围广泛。
本文着重介绍国内外在新型材料应用方面的情况及发展趋势。
车身新材料的种类
高强度钢板
从前的高强度钢板,拉延强度虽高于低碳钢板,但延伸率只有后者的50%,故只适用于形状简单、延伸深度不大的零件。
现在的高强度钢板是在低碳钢内加入适当的微量元素,经各种处理轧制而成,其抗拉强度高达420N/mm2,是普通低碳钢板的2~3倍,深拉延性能极好,可轧制成很薄的钢板,是车身轻量化的重要材料。
到2000年,其用量已上升到50%左右。
中国奇瑞汽车公司与宝钢合作,2001年在试制样车上使用的高强度钢用量为262kg,占车身钢板用量的46%,对减重和改进车身性能起到了良好的作用。
低合金高强度钢板的品种主要有含磷冷轧钢板、烘烤硬化冷轧钢板、冷轧双相钢板和高强度1F冷轧钢板等,车身设计师可根据板制零件受力情况和形状复杂程度来选择钢板品种。
含磷高强度冷轧钢板:
含磷高强度冷轧钢板主要用于轿车外板、车门、顶盖和行李箱盖升板,也可用于载货汽车驾驶室的冲压件。
主要特点为:
具有较高强度,比普通冷轧钢板高15%~25%;良好的强度和塑性平衡,即随着强度的增加,伸长率和应变硬化指数下降甚微;具有良好的耐腐蚀性,比普通冷轧钢板提高20%;具有良好的点焊性能;
烘烤硬化冷轧钢板:
经过冲压、拉延变形及烤漆高温时效处理,屈服强度得以提高。
这种简称为BH钢板的烘烤硬化钢板既薄又有足够的强度,是车身外板轻量化设计首选材料之一;
冷轧双向钢板:
具有连续屈服、屈强比低和加工硬化高、兼备高强度及高塑性的特点,如经烤漆后其强度可进一步提高。
适用于形状复杂且要求强度高的车身零件。
主要用于要求拉伸性能好的承力零部件,如车门加强板、保险杠等;
超低碳高强度冷轧钢板:
在超低碳钢(C≤%)中加入适量的钛或铌,以保证钢板的深冲性能,再添加适量的磷以提高钢板的强度。
实现了深冲性与高强度的结合,特别适用于一些形状复杂而强度要求高的冲压零件。
轻量化迭层钢板
迭层钢板是在两层超薄钢板之间压入塑料的复合材料,表层钢板厚度为~,塑料层的厚度占总厚度的25%~65%。
与具有同样刚度的单层钢板相比,质量只有57%。
隔热防振性能良好,主要用于发动机罩、行李箱盖、车身底板等部件。
铝合金
与汽车钢板相比,铝合金具有密度小(cm3)、比强度高、耐锈蚀、热稳定性好、易成形、可回收再生等优点,技术成熟。
德国大众公司的新型奥迪A2型轿车,由于采用了全铝车身骨架和外板结构,使其总质量减少了135kg,比传统钢材料车身减轻了43%,使平均油耗降至每百公里3升的水平。
全新奥迪A8通过使用性能更好的大型铝铸件和液压成型部件,车身零件数量从50个减至29个,车身框架完全闭合。
这种结构不仅使车身的扭转刚度提高了60%,还比同类车型的钢制车身车重减少50%。
由于所有的铝合金都可以回收再生利用,深受环保人士的欢迎。
根据车身结构设计的需要,采用激光束压合成型工艺,将不同厚度的铝板或者用铝板与钢板复合成型,再在表面涂覆防腐蚀材料使其结构轻量化且具有良好的耐腐蚀性。
镁合金
镁的密度为cm3,仅为钢材密度的35%,铝材密度的66%。
此外它的比强度、比刚度高,阻尼性、导热性好,电磁屏蔽能力强,尺寸稳定性好,因此在航空工业和汽车工业中得到了广泛的应用。
镁的储藏量十分丰富,镁可从石棉、白云石、滑石中提取,特别是海水的盐分中含%的镁。
近年来镁合金在世界范围内的增长率高达20%。
铸造镁合金的车门由成型铝材制成的门框和耐碰撞的镁合金骨架、内板组成。
另一种镁合金制成的车门,它由内外车门板和中间蜂窝状加强筋构成,每扇门的净质量比传统的钢制车门轻10kg,且刚度极高。
随着压铸技术的进步,已可以制造出形状复杂的薄壁镁合金车身零件,如前、后挡板、仪表盘、方向盘等。
泡沫合金板
泡沫合金板由粉末合金制成,其特点是密度小,仅为~/cm3,弹性好,当受力压缩变形后,可凭自身的弹性恢复原料形状。
泡沫合金板种类繁多,除了泡沫铝合金板外,还有泡沫锌合金、泡沫锡合金、泡沫钢等,可根据不同的需要进行选择。
由于泡沫合金板的特殊性能,特别是出众的低密度、良好的隔热吸振性能,深受汽车制造商的青睐。
目前,用泡沫铝合金制成的零部件有发动机罩、行李箱盖等。
蜂窝夹芯复合板
蜂窝夹芯复合板是两层薄面板中间夹一层厚而极轻的蜂窝组成。
根据夹芯材料的不同,可分为纸蜂窝、玻璃布蜂窝、玻璃纤维增强树脂蜂窝、铝蜂窝等;面板可以采用玻璃钢、塑料、铝板和钢板等材料。
由于蜂窝夹芯复合板具有轻质、比强度和比刚度高、抗振、隔热、隔音和阻燃等特点,故在汽车车身上获得较多应用,如车身外板、车门、车架、保险杠、座椅框架等。
英国发明了一种以聚丙烯作芯,钢板为面板的薄夹层板用以替代钢制车身外板,使零件质量减轻了50%~60%,且易于冲压成型。
工程塑料
与通用塑料相比,工程塑料具有优良的机械性能、电性能、耐化学性、耐热性、耐磨性、尺寸稳定性等特点,且比要取代的金属材料轻、成型时能耗少。
二十世纪七十年代起,以软质聚氯乙烯、聚氨酯为主的泡沫类、衬垫类、缓冲材料等塑料在汽车工业中被广泛采用。
福特公司开发的LTD试验车,塑料化后的车身取得了轻量化方面的明显成果(见表2)。
中国工程塑料工业普遍存在工艺落后、设备陈旧、规模小、品种少、质量不稳定的状况,而且价格高,缺乏市场竞争力。
工程塑料在汽车上的应用仅相当于国外上世纪八十年代的水平。
如上海桑塔纳轿车塑料用量仅为辆,红旗CA7228型轿车为辆,而日本轿车平均为14kg/辆,宝马则更高,为辆。
但这种局面将很快被打破,由上海普利特复合材料有限公司投资新建、国内最大的汽车用高性能ABS工程塑料生产基地日前在上海建成投产。
此项目引进了世界先进的工程塑料生成线和试验检测仪器等设备,形成了年产15,000吨高性能ABS工程塑料的能力。
高强度纤维复合材料
高强度纤维复合材料,特别是碳纤维复合材料(CFRP),因其质量小,而且具有高强度、高刚性,有良好的耐蠕变与耐腐蚀性,因而是很有前途的汽车用轻量化材料。
碳纤维复合材料在汽车上的应用,美国开展的最好。
二十世纪八十年代后期,复合材料车身外覆件得到大量的应用和推广,如发动机罩、翼子板、车门、车顶板、导流罩、车厢后挡板等,甚至出现了全复合材料的卡车驾驶室和轿车车身。
据统计,在欧美等国汽车复合材料的用量约占本国复合材料总产量的33%左右,并继续呈增长态势,复合材料作为汽车车身的外覆件来说,无论从设计还是生产制造、应用都已成熟,并已从车身外覆件的使用向汽车的内饰件和结构件方向发展。
图2为法国SORA公司为雷诺汽车公司开发的全复合材料轿车车身和重型卡车驾驶室。
上海通用柳州汽车公司和东风公司计划推出全复合材料车身的家庭用小轿车。
车身新材料应用的现状
目前,国内外车身轻量化的研究方向是开发具有较高强度的轻质高性能新材料及设计新的轻量化结构。
通过多年的探索,已取得了新的进展。
德国大众九十年代末开发的路波TDI车型就是采用新设计、新材料、新工艺的综合成果。
TDI所有车身部件都是轻质金属制成的,包括前挡泥板、车门、发动机罩和尾门,其中尾门的金属外层是铝质,内板是镁制成的。
汽车的内部设备许多也是轻质金属制成的,如,座椅的框架由铝制成,方向盘的内骨架是镁制成。
乘客舱和发动机室之间组合隔板是铝质的。
支撑结构通常也是由高强度的薄板金属制成的。
为解决新材料的防腐蚀保护和连接,大众采用创新的冲孔铆接法、迭边压接、激光钎焊等技术。
路波TDI的自重为830kg,包括417kg(%)的钢、136kg轻质金属(%,包括的镁)、116kg塑料(%)。
在保证车身抗扭刚度、使用寿命和安全性的前提下,车身的重量减轻了50kg,汽车的总重减轻了154kg。
由于汽车自重大幅度减轻,使得百公里油耗降至升,总能量消耗只是传统汽车的一半。
这意味着二氧化碳的排放量也将减少一半,碳氢化合物的排放量降到四分之一,是典型的环保型轿车,也是世界上批量生产的最经济轿车之一。
新材料应用的发展趋势
新材料回收再用性的研究
研究汽车新材料的最终处置问题至关重要,从某种程度上讲,关系到它的生存与发展。
目前,汽车上约占自重25%的材料无法回收再用,其中三分之一为各种塑料,三分之一为橡胶,还有三分之一为玻璃、纤维。
鉴于这种情况,世界各国都花费大量的人力、物力进行材料的回收再生问题的研究。
现在可以通过三种途径进行回收:
颗粒回收,重新碾磨;化学回收,高温分解;能源回收,将废弃物作为燃料。
德国在回收塑料等材料的法规是世界上最为完善的,其管理方式非常明确,即首先是避免产生,然后才是“循环使用”和“最终处理”。
1991年规定回收塑料中的60%必须是机械性回收,另有40%可以机械回收,也可以采用填埋或能量回收的方式。
通过十年的努力,现在的回收率已高达87%。
日本是循环经济立法最全面的国家,其目的是建立一个资源“循环型社会”。
为此,日本对废旧塑料的回收利用一直保持积极态度。
此外,日本还大力支持以废塑料为主的工业垃圾发电事业。
计划到2010年在全国建立150个废塑料发电设备。
减少材料的品种
未来汽车在工程塑料类型的选择上将会发生巨大的变化。
目前汽车使用的塑料由几十种高分子材料组成,当前世界各大汽车公司致力于减少车用塑料的种类,并尽量使其通用化。
这将有利于材料的回收再生和生态环境的保护。
降低成本
制约汽车车身新材料应用的重要因素是价格。
作为主要新材料的高强度钢、玻璃纤维增强材料、铝和石墨增强,其成本分别为普通碳钢的倍、3倍、4倍和20倍。
所以只有大幅度降低这些新材料的制造成本,才可能使诸多新材料进入批量生产。
如玻璃纤维增强材料将在成本上成为钢材的有力竞争者,虽然它的重量减轻有限,但价格却能为用户接受。
石墨合成材料尽管性能良好,但因其成本居高不下,目前它在汽车工业上很难有所作为。
先进的制造工艺的研发
采用新材料与先进的制造工艺是相辅相成的,汽车工业正在努力开发新的制造方法,对传统的工艺进行更新。
例如:
适用于轻量化设计的连接工艺今年来有所发展,如德国某汽车公司在大批生产的轿车上采用CO2激光束焊接,与传统的焊接工艺相比,焊接成的高强度钢板车身的强度提高了50%。
又如,一些复合材料的SMC壳体的材料较厚,大约为~3mm,限制了轻量化的幅度。
法国雷诺公司采用新的A级表面精度的SMC模压技术和低密度填料,减薄了零件厚度,使轿车壳体重量比普通SMC工艺下降了30%。
车身设计方法的革命
据欧洲汽车界人士预测,在今后十年中,轿车自身质量还将减轻20%,除了大量采用复合材料和轻质合金外,车身设计方法也将发生重大变化。
由于大量采用新型材料,传统的车身结构及其设计方法可能不再适用,取而代之的是一种基于生物学增长规律的形状优化设计法,这种设计方法即能减少零件质量,又延长了零件的使用寿命。
此外,采用新的设计方法还能使车身零件数大幅度减少。
如某车型的零件数已由400个减少到75个,质量减轻30%。
美国克莱斯勒汽车公司尚未投放市场的概念车由于采用了创新的优化设计法,使整车自重降至544kg。
这说明轻量化设计具有极大的潜力。
实施我国汽车铸造检测技术现代化的设想
一汽铸造公司何明必
摘要:
根据对现代铸件质量评定的具体要求,首次提出现代化铸造检测与控制技术的详细项目并归纳分类,同时提出近期我国汽车铸造检测技术现代化的具体实施设想。
关键词:
汽车铸件;检测与控制技术;现代化
1.二十一世纪初对我国汽车铸造检测技术的挑战
从20世纪末的现代铸造观点来看,铸件质量的评定已经赋予了全新的概念。
评定铸件质量要从产品质量、工艺过程质量和铸件设计质量三个方面去考虑,其主要内容如下。
(1)产品质量
铸造产品质量包括表面质量、内在质量以及使用质量。
而表面质量主要有:
尺寸精度、形位公差、表面粗糙度、表层硬度、重量公差、内腔清洁度及表面铸造缺陷程度等。
内在质量主要有:
化学成分、金相组织、冶金缺陷、物理力学性能、铸件内部的可靠程度(用无损探伤查),近年来还有晶粒度(共晶团数)、共晶饱和度、致密度、纯度、连续度等。
使用质量主要有:
切削性能、焊接性能、运转性能、耐磨性能、耐蚀性能、耐温性能、工作寿命及其它工作条件要求等,而且其指标也在不断提高。
(2)工艺过程质量
它是保证铸件产品质量的基础,包括从原材料、生产过程到半成品(如铁液、型砂)直到成品的铸造过程质量。
(3)铸件设计质量
近年来对铸件设计质量越来越重视,这是因为许多铸造缺陷孕育在设计过程中,即不良的铸件设计会降低生产过程质量与产品质量。
回顾建国以来的汽车铸造业同全国的铸造企业一样,与国外铸造的先进水平来比较.我国当前铸造行业最大的问题就是产品质量低、经济效益差、材料消耗高、环境公害大。
为了把产品质量和经济效益搞上去,今后我国铸造行业除了急需要提高企业管理水平、深入贯彻IS09000族标准管理、扩展与完善铸造标准、解决原材料质量差及不断提高工艺与设备水平以外,还必须不断补充、完善与提高铸造过程的质量检测与质量控制手段。
因为铸造的材质、工艺与设备水平和质量管理水平的提高在很大程度上依赖于铸造全过程的检测与控制手段能否配套、能否跟上,就是说,一切要用数据说话,一切要用计量管理,一切要上质量与成本控制才行。
然而,回顾建国以来汽车铸造厂的检测与控制技术发展,也同全国铸造企业一样,与国外现代铸造相比,如果说我们的铸造工艺、设备与管理水平仍然比较落后的话,那么铸造工厂的质量检测和质量控制技术就显得更加落后。
造成这种状况的原因虽然有相当的客观因素,但主要还是不少企业对于铸造质量检测与控制的关键作用、巨大威力和经济效益缺乏足够的认识。
特别需要指出的是,近年来微电子技术特别是计算机自动控制技术的迅速发展给多因素、多变量的复杂铸造检测与控制难题的解决带来了空前的机遇和广阔的前景。
铸造工艺过程的检测与控制设备仪器采用微电子技术已是近年来铸造设备与仪器发展的重要动向之一。
从最能代表世界铸造先进水平的最近几届铸造博览会可见,将最新的铸造工艺、设备仪器与最新的微电子、计算机自动检测与控制技术相结合表现得最为突出。
国外现代铸造的实践已经表明,这种先进的检测与控制技术如能尽快地、有效地应用到铸造生产中不但能明显地提高与稳定铸件的质量,而且能有效地提高劳动生产率,改善劳动条件,减少能耗、物耗,降低铸件的功能重量、功能成本及最终成本(包括节省加工费用等),从而给铸造企业带来巨大的经济效益。
在以上技术方面,我国国内虽然已经开始开展这方面的工作,并已取得了一些初步的成效,但仍处在起步、低水平的缓慢发展阶段,与国外先进水平相比,更是差距很大。
综上所述,20世纪末现代铸造的发展已经对我们提出了更高的要求,如果我们汽车铸造企业再不重视并大力补充与发展铸造质量检测、控制与计量技术手段的话,不但无法适应现代铸件质量评定的标准和现代汽车铸件日益发展的需求,而且必将使我们汽车铸造的材质、工艺、设备和管理水平与