孔55米捣固焦炉烘炉方案54页word.docx
《孔55米捣固焦炉烘炉方案54页word.docx》由会员分享,可在线阅读,更多相关《孔55米捣固焦炉烘炉方案54页word.docx(54页珍藏版)》请在冰豆网上搜索。
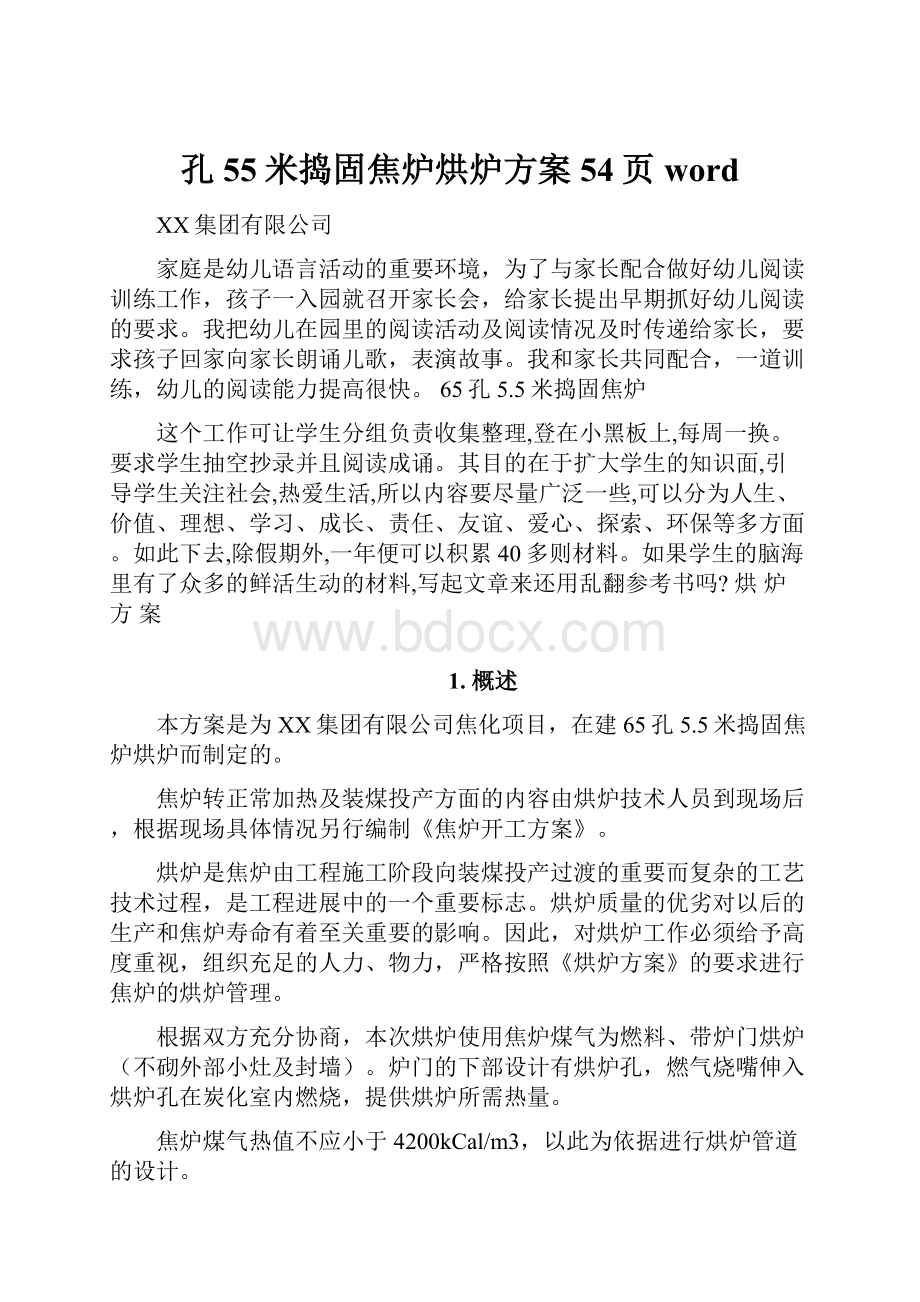
孔55米捣固焦炉烘炉方案54页word
XX集团有限公司
家庭是幼儿语言活动的重要环境,为了与家长配合做好幼儿阅读训练工作,孩子一入园就召开家长会,给家长提出早期抓好幼儿阅读的要求。
我把幼儿在园里的阅读活动及阅读情况及时传递给家长,要求孩子回家向家长朗诵儿歌,表演故事。
我和家长共同配合,一道训练,幼儿的阅读能力提高很快。
65孔5.5米捣固焦炉
这个工作可让学生分组负责收集整理,登在小黑板上,每周一换。
要求学生抽空抄录并且阅读成诵。
其目的在于扩大学生的知识面,引导学生关注社会,热爱生活,所以内容要尽量广泛一些,可以分为人生、价值、理想、学习、成长、责任、友谊、爱心、探索、环保等多方面。
如此下去,除假期外,一年便可以积累40多则材料。
如果学生的脑海里有了众多的鲜活生动的材料,写起文章来还用乱翻参考书吗?
烘炉方案
1.概述
本方案是为XX集团有限公司焦化项目,在建65孔5.5米捣固焦炉烘炉而制定的。
焦炉转正常加热及装煤投产方面的内容由烘炉技术人员到现场后,根据现场具体情况另行编制《焦炉开工方案》。
烘炉是焦炉由工程施工阶段向装煤投产过渡的重要而复杂的工艺技术过程,是工程进展中的一个重要标志。
烘炉质量的优劣对以后的生产和焦炉寿命有着至关重要的影响。
因此,对烘炉工作必须给予高度重视,组织充足的人力、物力,严格按照《烘炉方案》的要求进行焦炉的烘炉管理。
根据双方充分协商,本次烘炉使用焦炉煤气为燃料、带炉门烘炉(不砌外部小灶及封墙)。
炉门的下部设计有烘炉孔,燃气烧嘴伸入烘炉孔在炭化室内燃烧,提供烘炉所需热量。
焦炉煤气热值不应小于4200kCal/m3,以此为依据进行烘炉管道的设计。
烘炉煤气送至烘炉管道预留接点处(焦炉间台或短台),接点处的压力应达到5000Pa左右,压力稳定。
当炉温达到或接近800℃时转为地下室正常加热,为装煤投产做好准备。
烘炉过程中,在750℃前使用自动测温装置对温度进行监测:
由电子模块采集焦炉各测点热电偶的温度信号,再传输到计算机,在控制室的计算机上由烘炉软件显示测温结果及升温曲线。
烘炉自动测温软件工作时,每隔5分钟将全炉所有测点的温度自动测量一次,在计算机上显示管理火道、直行、蓄顶、篦子砖等处的温度,并显示管理火道的升温曲线。
操作人员可以根据升温曲线的变化的趋势,及时控制小灶燃烧情况,避免炉温偏高或偏低现象的发生,保证升温严格按计划进行。
炉温超过750℃后为便于热态工程施工和开工准备工作的顺利进行,拆除自动测温设备,改为用红外高温计人工测量直行温度。
在烘炉过程中,各项施工仍在进行中。
现场人员多、情况复杂,为避免发生安全事故,所有烘炉人员要事先进行安全教育及岗位培训,配备必要的安全防护用品。
2.焦炉烘炉升温计划制定
焦炉炉体主要是用硅砖砌筑的,在局部区域还采用粘土砖、断热砖、红砖、缸砖及其它耐火材料。
由于硅砖在炉体砖型中占绝大多数,而且烘炉期间硅砖的膨胀量比其它耐火材料大,所以,炉体在烘炉升温时膨胀特性主要由硅砖膨胀特性决定。
升温曲线的制定依据所用硅砖的热膨胀性质,对其它材料仅应注意升温时与硅砖砌体的膨胀差。
2.1.硅砖的线膨胀率数据的采集要求
烘炉升温曲线的计算和制定是以业主方提供的硅砖代表砖样的热膨胀数据为依据(列于附录表中)。
代表砖样应选自焦炉砌筑现场,从燃烧室、斜道和蓄热室三个区段的砖号中选取砖样。
选取时,选择对焦炉横向膨胀和高向膨胀影响较大(通常是用量最多)的砖号。
每个区段内选3~4个砖号,每个砖号选2块砖,组成两套砖样,一套砖样用于测定热膨胀曲线,另一套在现场保留备查。
为保证选择的砖样能正确反映焦炉的膨胀特性,所选砖号一定与烘炉测温段相一致:
例如燃烧室部位要取炭化室墙面砖中用量多的砖号;斜道部位不同层的重复砖号较少,要从每层用量较多的砖号中选取,最少取4个砖号,分布在不同层数;蓄热室区域重复砖号多,取主墙、单墙代表砖号即可,应取篦子砖之上的砖层;有的情况下尚须以小烟道区域为下部主控测温区,例如分格蓄热室焦炉,此时应选取小烟道区域的砖样。
测定热膨胀数据时,常温至300℃区间每25℃测定一个数据,300℃至500℃区间每50℃测定一个数据,500℃至1000℃区间每100℃测定一个数据。
在焦炉硅砖砖号到齐后就应取砖样进行测定热膨胀曲线。
2.2.焦炉烘炉的主要工艺过程及升温计划制定原则
在整个烘炉过程主要包含有干燥期、升温期、热态工程、转地下室正常加热等几个主要阶段,每个阶段制定升温计划时都有不同的工艺考虑。
2.2.1.干燥期
新建的焦炉含有数百吨的水分,这些水分主要在烘炉干燥期内排出,因此要保证足够的干燥时间。
干燥阶段是指烘炉点火开始至砌体水分完全排出的一段时间,砌体干燥阶段结束时温度约130℃。
但在制定烘炉方案时为了方便也把温度达100℃前称为干燥期。
超过100℃后,仍有部分内在水分残留在砌体中,随着温度的升高逐步排出。
由于100℃后进入晶形转换期,每日升温幅度较小,有充足时间可以保证所有水分的安全排出。
管理火道温度达到130℃,并不意味整座焦炉的水分都完全排出,而是焦炉主体部分(炭化室、燃烧室、斜道)砌体中的水分完全排出。
在蓄热室、篦子砖、小烟道砌体中的水分仍未完全排出,该部分砌体的干燥是在焦炉升温的同时进行的。
干燥期阶段应尽量减少烘炉气流阻力,增加烟囱吸力,产生大的风量。
同时,应注意监测气体流动末端(小烟道等处)的温度,保证前段后段合理的温度比例关系,使末端在露点以上,以保证炉体水分的正常排出。
实践证明,这种砌体干燥工艺方法可以有效安全地排出水分,能够满足烘炉的工艺需要。
2.2.2.升温期
升温期主要是指干燥期结束后到热态工程开始前的这段区间。
在升温期,硅砖晶型开始产生变化,焦炉大部分膨胀都集中在这个区间。
升温期每日温度升高幅度较小,温度控制严格要求按计划进行。
在升温期,硅砖本身及各砌体间由于晶型转化产生较大膨胀,在炉体上产生热应力。
如果控制不当,热应力就会破坏砌体,引起炉体变形及裂缝。
根据国内外大量的烘炉经验,最大日膨胀率控制0.035%是安全的,升温曲线也按此计算制定。
2.2.3.热态工程
管理火道温度达到600℃后,炉体主要部位的硅砖晶型转化已全部结束,炉体状态基本趋于稳定,开始进入热态工程施工阶段。
热态工程施工质量的好坏对焦炉投产后能否正常生产有极大的影响,而热态工程时间紧、施工环境艰苦、项目众多而繁杂、施工量大,一定要引起充分重视。
在升温计划的制定中要保证足够的热态工程施工时间,升温速度不宜过快。
2.2.4.拆除烘炉测温用临时仪表设备
炉温升至约750℃时,管理火道温度已渐趋烘炉测温热电偶量程的最大极限,自动测温临时仪表设备故障率提高,误差加大。
同时为了给热态工程及开工前试车让出场地,以及配合随后进行的转入地下室正常加热时看火的要求,需要及时拆除烘炉测温用临时仪表设备。
通常在转正常加热前两天拆除热电偶。
2.2.5.转地下室正常加热及装煤
炉温接近或达到800℃时即可转入地下室进行正常加热。
转正常加热后需要控制炉温,根据总体工程进展及焦炉机械调试情况确定装煤出焦时间,并以此来制定合理的加热制度。
详细情况另参见《焦炉开工方案》。
2.3.烘炉升温曲线的计算和确定
各区域硅砖砖样的热膨胀曲线、烘炉天数计算书、确定的升温计划及升温曲线见后面附录。
3.烘炉前必须完成的工作项目
焦炉的烘炉只能在焦炉工程施工进展到满足一定的条件时才能开展,并且与后续未完工程密切配合。
烘炉开始后,工程施工进度安排应与焦炉升温协调,力求同时达到具备装煤投产的要求。
对于烘炉开始时未能按要求完成的项目,必须逐项列出,并定出完成时间。
3.1.机、焦侧操作平台
机、焦侧操作平台施工完毕。
为保证烘炉人员安全,机焦侧操作台在烘炉过程中必须增加安全设施。
安全设施安装位置及形式根据现场具体情况定,在确保烘炉操作人员安全基础上,兼顾烘炉操作及工程施工作业,并由相关安全部门检查通过。
临时增加的安全设施在投产前酌情拆除。
3.2.护炉设备
3.2.1.保护板、炉柱
(1)保护板主体安装、调整完毕,记录检查结果。
(2)炉柱安装、调整完毕,对原始曲度以及安装位置尺寸要做出详细记录。
(3)保护板与炉体间(肩部)缝隙按要求勾缝。
(4)炉柱编号牌就位(或临时用油漆书写清晰)。
(5)保护板与炉柱相对位置调节到满足工艺要求。
(6)检查蓄热室小保护板与钢柱是否有点焊处,有则断开(小弹簧加压前)。
(7)炉柱下端滑动处清理干净,做好标记。
地脚螺栓松调至用手拧紧的状态。
3.2.2.纵、横拉条
(1)纵、横拉条已经安装完毕并检查合格。
(2)横拉条弹簧调节到烘炉前吨位,横拉条用木块(或木楔)垫平,全段处于水平状态。
(3)纵拉条调整器安装完毕,调整到规定高度,不能压到最边部的横拉条。
**纵拉条弹簧在抵抗墙冷态尺寸测量结束前先不要加压。
3.2.3.炉门框、炉门
(1)炉门框主体就位调整完毕。
(2)对磨板安装情况作检查,测量记录磨板顶面与炭化室底面距离。
(3)炭化室内火床砌筑完成并通过验收后安装炉门。
(4)安装炉门时严防碰倒炭化室内火床。
(5)炉门安装好后按图纸要求调节横铁弹簧压紧炉门,保证烘炉期间严密。
3.3.焦炉炉体砌筑收尾
(1)清理工程施工垃圾,对炉体进行清扫并同过检查。
(2)调节砖按要求安放完毕,并做好记录。
(3)炉体斜道区正面膨胀缝临时用硅酸铝纤维绳填塞严密。
(4)炉端墙30mm膨胀缝清扫完毕,正面临时用硅酸铝纤维绳密封。
(5)干燥孔检查并清扫完毕。
(6)抵抗墙内通风道清理完毕。
3.4.炉顶部位工作项目
(1)炉顶表面清理干净(最晚应在烘炉前5天,以便于安装烘炉测温设备)。
(2)所有炉顶导烟孔大盖均用废火泥密封。
(3)看火孔盖涂抹黄干油。
(4)烘炉自动测温系统辅助物品(电偶座、铺线用槽钢等)准备齐全(最晚应在烘炉前7天完毕)。
(5)烘炉自动测温设备安装调试完毕(炭化室点火前一天)。
(6)上升管安装就位并固定好,上升管根部按设计要求用隔热板密封。
(7)如果集气管主体部分已经安装就位,应逐个检查集气管滑动座滑动情况。
检查有无点焊,松开固定螺栓,确保滑动良好。
(8)如果桥管、水封阀部位已安装完毕,则应逐个检查连接部位,不能影响到炉体的膨胀,并酌情做好滑动标记。
(9)抵抗墙顶中心卡钉埋设完成二次浇注,并在中心点处作刻印标记。
3.5.烟囱及总、分烟道、废气开闭器
(1)总、分烟道土建部分完工,通过验收。
烟道内的膨胀缝、沉降缝清理干净,并按要求做好密封。
(2)总烟道、分烟道翻板安装就位(烟道翻板安装前应进行预组装)。
转动轴承注满黄油,翻板动作灵活,开关核对刻印。
(3)机、焦侧分烟道翻板上部土建处理,检查后交安装。
(4)烟道内所有测温、测压点预埋管件埋设就位,出口处做临时密封。
(5)交换开闭器及其附件,按设计安装就位,检查合格。
(6)小烟道承插部位按设计要求用硅酸铝纤维绳密封。
(7)交换开闭器与烟道弯管间按设计要求置入硅酸铝纤维绳。
(8)交换开闭器上小翻板核对开关位置,检查运转顺畅情况,做好开关标记。
(9)箅子砖正面测温孔放置塞子砖临时密封。
3.6.烘炉设备、设施
(1)烘炉炭化室内部火床砌筑验收完毕。
(2)炉顶烘端墙小烟囱、烘端墙外部小灶可拖后几天砌,具体位置应按照现场烘炉技术人员的要求定。
(3)焦炉测线、调弹簧用临时走台、梯子安装完毕。
(4)测线架安装完毕,具体位置应与烘炉技术人员现场确定。
(5)烘炉专用温度计、热电偶、测压U型表斜形表等专用工具备齐。
(6)烘炉用记录帐、表及其工、器具准备齐全。
(7)烘炉人员劳动防护用品准备齐全。
3.7.烘炉点火前应完成的测量和调节工作
(1)炉长、炉高、大弹簧等作测点标记。
(2)所有大、小弹簧负荷按照烘炉方案要求吨位调节好。
(3)测线架挂线完成,挂线后应至少初测一次以检查挂线的准确性。
(4)炉长、炉高、炉柱曲度及其它所有冷态测量完成。
(5)纵拉条、上下横拉条及炉柱各线小弹簧试压表和安装记录帐纸与施工单位做好交接工作,核对清楚完整无误。
(6)压保护板顶丝与保护板顶面距离调至全炉一致,即距保护板顶面间隙调整为50mm。
(7)炉端墙30mm膨胀缝作测点标记。
(8)抵抗墙作测量垂直度标记;抵抗墙顶部作出外移测量标记。
在纵拉条弹簧加压前测量好冷态值,确认后保留记录。
(9)炉柱和保护板间隙测点标记等。
(10)作好各种滑动标记:
操作台四角、操作台与支柱、炉柱底、单叉处等。
(11)废气砣杆提起高度为200mm(支撑用角钢或木块30×30,L=200mm)。
(12)交换开闭器进风口铁板已安装完毕,并盖上隔热板密封。
(13)交换开闭器废气筒小翻板按烘炉技术人员的要求调好开度,必要时用铁丝固定好。
(14)燃烧室、炭化室、蓄热室按烘炉编号要求进行编号,用油漆写好。
3.8.烘炉用其它准备工作
(1)焦炉用消防设施齐备,有醒目的安全标志。
(2)各岗位的烘炉操作人员培训完毕全部到岗。
要求安全教育合格,熟悉烘炉工艺过程,对工具及仪表使用方法掌握熟练。
(3)烘炉用自动测温仪表值班室准备好,工作电源稳定并符合要求:
~220V,50Hz。
值班室内桌、椅、文件柜、工具柜等准备齐全,联络电话安装完毕并交付使用。
(4)烘炉用仪表、设备工器具仓库准备好,安全可靠。
(5)焦炉用水、电具备外部供应条件,烘炉区域照明符合要求。
(6)烘炉人员休息室、卫生间等的设施施工完毕可以使用。
4.烘炉操作管理
4.1.烘炉升温管理总则
管理火道温度的控制应按照升温计划的要求,按照烘炉现场技术人员的指导进行管理。
干燥期阶段在保证燃气火焰不熄灭的前提下,尽量减少烘炉气流阻力,适当增加吸力,产生大的风量,以保证炉体水分的正常排出,避免小烟道出水。
升温期应力求炉体温度升温均匀稳定,避免炉温出现大的波动。
总、分烟道吸力控制在规定值,不允许随意变化,或用吸力调温度。
在整个烘炉过程中,应控制一个合理的高向温度比例。
4.2.炭化室点火操作
4.2.1.点火操作前准备工作
点火前,烘炉燃气管道安装就位,按照通用标准打压实验合格。
准备好引火物,并预先实验点火效果。
点火前一天,将废气盘的进风口用隔热板盖严,废气筒小翻板开度按要求调整完毕,废气砣支起。
点火烘炉前一小时将总烟道翻板四周添塞物清理干净,总烟道、分烟道翻板关闭,点火开始后逐步打开。
4.2.2.点火操作步骤
(1)按照单双数,机、焦侧各点一半,逆向进行点火。
(2)点火时要先送入火源,然后点火。
点燃后,在保证不灭火的情况下,关小烧嘴阀门,防止旺烧。
(3)在点火过程中,如果发现火焰旺烧难以控制,火床倒塌等情况,应关闭阀门处理后再点火
(4)点火过程中要安排专门人员控制煤气管道压力,当煤气总管压力低于2000Pa时,要暂停点火,查找原因。
(5)点火完成后,当班升温班长应及时调节分烟道吸力,控制机焦侧烘炉支管压力。
同时组织升温人员加强巡视,防止灭火。
(6)升温工根据电脑屏幕炉温变化情况及时调节煤气支管压力,稳定曲线。
(7)剩余一半小灶点燃的时间,由烘炉技术负责人根据烘炉升温情况确定。
(8)抵抗墙在炉温升至70℃时点火,初期控制抵抗墙温度不低于管理火道温度30℃,后期控制抵抗墙温度不低于管理火道50℃,600℃以后可以停止烘抵抗墙。
4.3.炉温管理
4.3.1.烘炉温度的监测
烘炉中以管理火道温度作为烘炉升温计划控制温度。
采用计算机自动测温系统自动检测焦炉达到的温度,同时可监测直行温度、横墙温度、抵抗墙、蓄顶、篦子砖、分烟道等处温度作为参考温度。
温度的采集、显示为每5分钟一次。
值班人员应根据显示出的温度变化情况及时调节小灶内燃烧,使升温符合预定的曲线。
每班的温度应按计划均匀升温,每天的计划温度是指白班应达到的温度。
每班的计划温度是指每班下班前1小时应达到的温度。
每天的班报所采用的监测温度为每4小时一次。
4.3.2.高向升温比例的控制
烘炉时控制焦炉上下的温度比例具有非常重要的意义:
(1)保证上下温度按一定的规律性过渡到接近生产时的上下比例,防止焦炉砌体在烘炉过程中产生裂缝。
(2)防止在干燥期焦炉下部产生冷凝水。
因此,在整个烘炉期间要严格控制炉体高向升温比例。
在烘炉的初期蓄热室温度要力争达到燃烧室温度的90%以上,在末期达到燃烧室温度的80~85%。
烘炉末期小烟道温度不得高于450℃,以避免在焦炉转入正常加热后在小烟道区域产生过多的裂缝以及造成混凝土基础高温。
4.3.3.燃烧状态控制
烘炉操作人员应加强对燃烧状态的巡视,半小时巡视一遍。
每次对煤气压力做较大调整后,都应该全面检查各烧嘴的燃烧情况。
发现灭火时不能马上点火,防止发生回火爆炸。
应先关闭阀门,等待两分钟后再点火。
4.3.4.烘炉升温控制
各温度阶段管理火道实际温度与计划温度允许偏差波动范围见下表:
温度范围(℃)
允许波动范围(℃)
备注
常温~300
±1
合格率达85%为合格;大于95%为优秀。
300~500
±2
500~800
±3
对直行火道的管理应力求做到温度均匀,偏差应在±10℃以内。
超过此温度,自动测温的烘炉管理软件会有提示。
各升温班对高低温号必须认真查找原因,及时处理并做好记录。
不允许用调节烟道吸力的方法控制炉体温度。
要注意刮风、下雨等天气因素对升温造成的影响,及时采取必要措施。
遇到刮风天气影响机焦侧温度分布,需要根据情况关闭相应风向侧风门。
遇到大雨天气需要准备防雨设施。
如因工程进展需要保温,应提前做好预案,注意避免硅砖晶型转化温度点。
当升温困难或者烘炉煤气支管压力长时间保持3000Pa以上时更换烘炉用孔板,更换孔板后支管压力不得小于500Pa。
4.3.5.升温偏离计划的处理
由于停煤气等原因造成焦炉温度远低于计划值时,严禁急剧升温追赶计划,应在烘炉技术人员的指导下,及时制定新的升温计划,逐渐地接近原定计划值。
若升温超计划,应马上进行保温,不允许采用降温的手段!
4.3.6.空气系数的监测
空气系数是通过废气采样分析测定的。
采样是用长2.5米左右的不锈钢管由炉顶立火道取得,然后用奥氏分析仪(testo350废弃分析仪)分析成分。
烘炉不同阶段空气系数控制参考范围:
温度区间(℃)
<100℃
100-300℃
300-500℃
500-700℃
700℃以上
空气系数范围
50-25
25-10
10-5
5-3
3-2
4.4.烘炉过程中升温班的监控项目
4.4.1.温度测定的内容、测点、频度
序号
监测项目
工具
监测位置
监测频度
说明
1
管理火道温度
热电偶﹑电脑自动测温
1、2、7、13、19、25、31、37、43、49、55、61、65、66燃烧室1、3、8、14、19、25、30、32火道,距炉顶面2.5m
5分钟一次
用作控制升温管理依据
2
直行温度
热电偶﹑电脑自动测温
所有燃烧室8、25火道,距炉顶面2.5m
5分钟一次
检查全炉温度的均匀性
3
横墙温度
热电偶﹑电脑自动测温
31#燃烧室全部火道
5分钟一次
焦炉横向温度分布情况
4
蓄热室顶部温度
热电偶﹑电脑自动测温
2、7、13、19、25、31、37、43、49、55、61、66#蓄顶测温孔,距封墙表面1.5米
5分钟一次
检查焦炉高向温度分布
5
篦子砖温度
热电偶﹑电脑自动测温
2、7、13、19、25、31、37、43、49、55、61、66#距封墙表面1.5米(篦子砖测温孔)
5分钟一次
检查焦炉高向温度分布
6
小烟道温度
人工测量
小烟道两叉(或单叉)部
根据需要
双金属温度计或500℃温度计
7
分烟道温度
热电偶﹑电脑自动测温
分烟道翻板附近,2.5米深
每5分钟一次
检测烟道温度
8
端墙温度
同上
抵抗墙处,距炉顶面2.5米
每5分钟一次
检查抵抗墙温度
9
大气温度
玻璃温度计,人工测量
室外背光、通风处
每班一次
测量烘炉期间大气温度的变化情况
10
交换开闭器表面温度
手持式红外测温仪
交换开闭器表面规定点
根据需要
4.4.2.压力测定和废气分析的内容、测点、频度
监测项目
所用仪表
监测次数
说明
烘炉煤气总管压力
U型压力计
值班人员随时观察
半小时记录一次
机、焦侧煤气管压力
U型压力计
值班人员随时观察
半小时记录一次
看火孔压力
斜型压力计(或电子微压计)
根据现场烘炉技术负责人的要求
如果用电子微压计测量效果会更好
总烟道吸力
U型压力计
每小时测调一次
并保持规定值
分烟道吸力
U型压力计或电子微压计
每小时测调一次
根据实际情况调节
并保持规定值
废气分析
奥式分析仪(或其它气体成分分析仪)
两天一次,机、焦侧各取四个样
选作项目,如无分析人员可以不作
4.5.烘炉过程中铁件班的各项测量调节工作
4.5.1.点火前的准备
(1)测线架、测线走台应在点火前及早完成。
(2)点火前应将上下各线大小弹簧按要求加压完毕。
并反复调整两次,保证弹簧高度稳定,并为冷态尺寸的测量打好基础。
(3)最晚应在点火前两天开始进行挂线工作(机焦侧各三线),并进行测量,对挂的线进行检查校正,确定冷态尺寸。
(4)膨胀测定各项目的原始标记和尺寸必须在点火前测量完毕。
(5)铁件操作人员全部到岗,熟知现场情况和本人职责。
(6)各种调弹簧用的工器具(包括特殊制作件)及划线工具备齐。
4.5.2.工作内容
(1)弹簧负荷管理
烘炉过程中根据铁件观测的具体情况,可能需要随时对初步确定的弹簧负荷值做出调整。
具体弹簧吨位变化由烘炉技术人员现场确定。
烘炉期间炉柱上大、小弹簧初步负荷值见下表:
度
温
弹
吨
簧
上部大弹簧(10kN)
下部大弹簧(10kN)
小弹簧(包括小炉柱)(10kN)
300℃前
10
10
1~7线为0.65×2
其它各线:
0.5×2,蓄热室单墙三线都为1
300℃~500℃
12.5
11.5
1~7线为0.75×2
500℃后
14.5
12.5
1~7线为1.1×2
纵拉条:
烘炉前6t;150℃时12t;700℃后24~30t;
调节时用炉顶托架提起到规定高度然后加上吨位。
在烘炉过程中,根据抵抗墙垂直度的变化需要对纵拉条的吨位做出适当调整。
应确保抵抗墙顶部的外倾距离小于10mm,内倾距离小于5mm。
**纵拉条拉紧弹簧在加压前,需要测量抵抗墙垂直度及顶部冷态位置。
(2)炉长膨胀测量:
测量位置在保护板上,大概位置是:
一线大致在上横铁处;二线大致在下横铁处;三线大致在箅子砖处。
可以根据事情情况适当调整。
一、二线测量点应选择在大保护板上,冷态时做好标记。
第三线测点在小保护板上,应尽量避免把测量点直接选在砖面上。
(3)炉柱曲度:
测量位置在炉柱上,冷态时要在炉柱上打好测量标记。
采用三线法进行测量。
三线法曲度计算原理见下图。
计算公式如下:
式中,A炉柱曲度,毫米;
a上部钢丝线至炉柱正面的距