X数控铣床进给传动系统设计方案.docx
《X数控铣床进给传动系统设计方案.docx》由会员分享,可在线阅读,更多相关《X数控铣床进给传动系统设计方案.docx(41页珍藏版)》请在冰豆网上搜索。
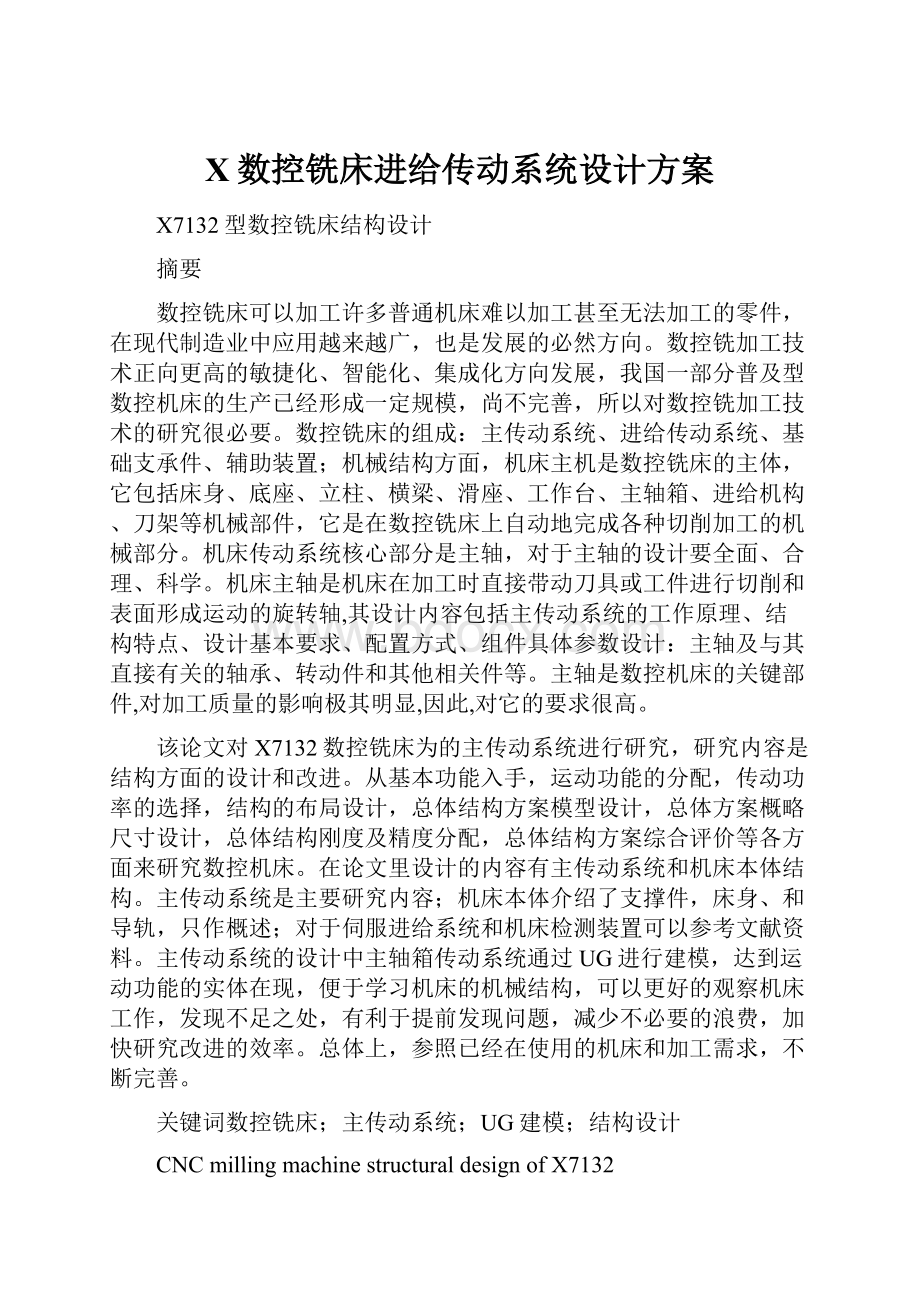
X数控铣床进给传动系统设计方案
X7132型数控铣床结构设计
摘要
数控铣床可以加工许多普通机床难以加工甚至无法加工的零件,在现代制造业中应用越来越广,也是发展的必然方向。
数控铣加工技术正向更高的敏捷化、智能化、集成化方向发展,我国一部分普及型数控机床的生产已经形成一定规模,尚不完善,所以对数控铣加工技术的研究很必要。
数控铣床的组成:
主传动系统、进给传动系统、基础支承件、辅助装置;机械结构方面,机床主机是数控铣床的主体,它包括床身、底座、立柱、横梁、滑座、工作台、主轴箱、进给机构、刀架等机械部件,它是在数控铣床上自动地完成各种切削加工的机械部分。
机床传动系统核心部分是主轴,对于主轴的设计要全面、合理、科学。
机床主轴是机床在加工时直接带动刀具或工件进行切削和表面形成运动的旋转轴,其设计内容包括主传动系统的工作原理、结构特点、设计基本要求、配置方式、组件具体参数设计:
主轴及与其直接有关的轴承、转动件和其他相关件等。
主轴是数控机床的关键部件,对加工质量的影响极其明显,因此,对它的要求很高。
该论文对X7132数控铣床为的主传动系统进行研究,研究内容是结构方面的设计和改进。
从基本功能入手,运动功能的分配,传动功率的选择,结构的布局设计,总体结构方案模型设计,总体方案概略尺寸设计,总体结构刚度及精度分配,总体结构方案综合评价等各方面来研究数控机床。
在论文里设计的内容有主传动系统和机床本体结构。
主传动系统是主要研究内容;机床本体介绍了支撑件,床身、和导轨,只作概述;对于伺服进给系统和机床检测装置可以参考文献资料。
主传动系统的设计中主轴箱传动系统通过UG进行建模,达到运动功能的实体在现,便于学习机床的机械结构,可以更好的观察机床工作,发现不足之处,有利于提前发现问题,减少不必要的浪费,加快研究改进的效率。
总体上,参照已经在使用的机床和加工需求,不断完善。
关键词数控铣床;主传动系统;UG建模;结构设计
CNCmillingmachinestructuraldesignofX7132
Abstract
CNCmillingmachinecanbedifficulttoprocessmanyordinaryprocessingcannotevensparepartsprocessing,theapplicationofmodernmanufacturingintheincreasinglywide,istheinevitabledevelopmentdirection.CNCmillingprocessingtechnologybeingmoreagile,intelligentandintegratedway,partofouruniversalCNCmachinetoolproductionhasformedacertainscale,isnotyetperfect,sotheCNCmillingtechnologyresearchisnecessary.CNCmillingmachine:
themaindrivesystem,intothetransmissionsystem,basedonsupportingpieces,assistivedevices。
mechanicalstructure,thehostmachineisthemainCNCmillingmachine,whichincludesbed,thebase,column,beam,WaterlooBlock,workingplatforms,spindlebox,feed,Turret,andothermechanicalcomponents,itisinCNCmillingmachineautomaticallyonthecompletionofvariouscuttingthemechanicalparts.Machinedrivesystemisthecoreofthespindle,thespindletothedesignofacomprehensive,rational,scientific.Machinespindleisintheprocessingmachinetoolordirectlyledtotheworkpieceandthecuttingmovementformedonthesurfaceoftherotationaxis,themaindrivesystemdesignincludingtheprincipleofstructuralfeatures,basicrequirementsforthedesign,configuration,thedesignparametersofspecificcomponents:
SpindleAnddirectlyrelatedtothebearing,rotatingpiecesandotherrelateditems,suchas.SpindleCNCmachinetoolsarethekeycomponents,theimpactonprocessingqualityisextremelyclear,soit'sverydemanding.
ThepaperontheX7132CNCmillingmachineforthemaindrivesystemtostudy,researchisthestructureofthedesignandimprovement.Startfromthebasicfunction,thefunctionofthedistribution,transmissionpowerofchoice,thelayoutofthestructure,theoverallstructureoftheprogrammemodeldesign,theapproximatesizeoftheoverallplandesign,structuralrigidityandprecisionoftheoveralldistribution,theoverallstructureofcomprehensiveevaluation,andotherareastostudyafewControlledMachineTools.Inthepaper,thedesignofthecontentsofthemaindrivesystemandmachinebodystructure.Maindrivesystemisthemaincontentofmachinebodyonthesupportpieces,bedandtherails,justoutlined,theservofeedsystemandmachinedetectiondevicescanmakereferencetoliterature.MaindrivesysteminthedesignoftransmissionthroughtheUGspindleboxmodel,totheentitiesinthemotorfunctionistofacilitatethemechanicalstructureofmachinelearning,canbetterobservethemachine,founddeficiencies,toidentifyproblemsinadvance,Reduceunnecessarywasteandspeedingupresearchtoimproveefficiency.Overall,thedesignhasmoreinreferencetotheuseofthemachinetoolsandprocessingneeds,andconstantlyimprove.
KeywordsCNCmillingmachine;UGModeling;Maindrivesystem;StructuralDesign
不要删除行尾的分节符,此行不会被打印
摘要
Abstract
千万不要删除行尾的分节符,此行不会被打印。
在目录上点右键“更新域”,然后“更新整个目录”。
打印前,不要忘记把上面“Abstract”这一行后加一空行
第1章绪论
1.1课题背景
随着计算机技术的高速发展,传统的制造业开始了根本性变革,各工业发达国家投入具资,对现代制造技术进行研究开发,提出了全新制造模式。
在现代制造系统中,数控技术是关键技术,它集微电子、计算机、信息处理、自动检测、自动控制等高新技术于遗一体。
数控铣加工是数控加工技术最为重要的应用之一。
近年来我国企业的数控机床占有率逐年上升,在大中企业已有较多使用,在中小企业甚至个体企业也普遍开始使用。
目前数控铣床主要用于加工精度高、品种多、批量小,形状复杂零件,而且数控铣床可以加工许多普通机床难以加工甚至无法加工的零件,主要用于铣削以下四类零件:
平面类零件、空间曲面类零件、变斜角类零件、进行孔加工和攻螺纹等。
工件上的曲线轮廓内、外型,特别是由数学表达式给出的非圆曲线与列表曲线等轮廓;形状复杂,尺寸繁多,划线与检测困难的部位;用通用机床加工时难以观察,测量和控制进给的内、外凹槽;以尺寸协调的高精度控与面;能在一次安装中一起铣削出来的简单表面或形状,常采用铣削加工。
1.2数控铣床的组成和特点
机床主机是数控铣床的主体,它包括床身、底座、立柱、横梁、滑座、工作台、主轴箱、进给机构、刀架等机械部件。
它是在数控铣床上自动地完成各种切削加工的机械部分。
数控铣床中的机床本体,在开始阶段使用通用机床,只是在自动变速、刀架或工作台自动转位和手柄等方面作些改变。
实践证明,数控铣床除了由于切削用量大、连续加工发热多等影响工件精度外,还由于是自动控制,在加工中不能像在通用机床上那样可以随时由人工进行干预。
所以其设计要求比通用机床更严格,制造要求更精密。
因而在后来的数控铣床设计时,采用了许多新的加强刚性、减小热变形、提高精度等方面的措施,使得数控铣床的外部造型、整体布局、传动系统及刀具系统等方面都发生了很大的变化。
机床示意图见图1-1。
数控铣床主体的主要结构特点如下:
1.采用具有高刚度、高抗振性及较小热变形的机床新结构。
通常用提高结构系统的静刚度、增加阻尼、调整结构件质量和固有频率等方法来提高机床主体的刚度和抗振性,使机床主体能适应数控铣床连续自动地进行切削加工的需要。
采取改善机床结构布局、减少发热、控制温升及采用热位移补偿等措施,可减少热变形对机床主体的影响。
2.现代数控铣床广泛采用高性能的主轴伺服驱动和进给伺服驱动装置,使数控铣床的传动链缩短,可简化机床机械传动系统的结构。
3.采用高传动效率、高精度、无间隙的传动装置和传动元件,如滚珠丝杠螺母副、塑料滑动导轨、直线滚动导轨、静压导轨等传动元件。
另外,数控铣床还应包括辅助装置。
辅助装置作为数控铣床的配套部件,挥数控铣床功能所必需的。
常用的辅助装置包括气动、液压装置,排屑装置,置,回转工作台和数控分度头,防护、照明等各种辅助装置。
气动和液压装置是应用气动、液压系统,使机床完成自动换刀所需的动作,实现运动部件的制动和滑移齿轮变速移动,完成工作台的自动夹紧、松开,工件、刀具定位表面的自动吹屑等辅助功能。
排屑装置的作用是将切屑从加工区域排出。
迅速有效地排除切屑可以保证数控铣床高效率运行。
1.3数控加工的特点
1.加工精度高。
数控机床是精密机械和自动化技术的综合产品,所以机床的传动系统与机床的结构设计都考虑到很高的刚度和热稳定性。
在设计传动机构时采取了减少误差的措施,并由数控装置进行补偿,所以数控机床有较高的加工精度。
由于加工过程自动化,加工精度不受人的操作技能、情绪和疲劳的影响。
计算机还可以自动进行刀具寿命管理,不会因刀具磨损而影响工件精度和一致性。
另外,数控系统中增加了机床误差、加工误差修正补偿的功能,使加工精度得到进一步提高。
2.可以加工出具有复杂的曲线、曲面的零件。
由于计算机有高速的运算能力,可以瞬时准确地计算出每个坐标轴瞬时的运动量,因此可以方便地复合成复杂的曲线或曲面。
3.加工效率高,可实现自动化生产。
由于计算机有记忆和存储能力,可以将输人的程序记住和存储下来,然后按程序的顺序自动去执行,从而实现自动化。
对夹具要求低,只需通用夹具,又可免去划线等工作还可以实现自动换刀,利用交换工作台可进行自动换位加工,加工准备时间大大缩短。
4.可实现多工序的集中,减少零件在机床间的频繁搬运。
如加工中心,在工件装夹好后,可实现钻、铣、镬、攻丝、扩孔等多种工序的加工。
这些多种工序是在同一基面、同一次装夹下实现的,从而提高了加工精度,现已出现其他工序集中的机床,如车削中心、车铣中心、磨削中心等。
5.拥有自动报带、自动监控、自动补偿等多种自律功能这是在配备多种传感器条件下,计算机威力的体现,可以实现白班有人看管和作好充分准备工作,使得二班、三班在无人条件下进行自动加工(国外称为“熄灯生产”)。
工人只工作8小时,而机床可工作24小时。
这样,机床利用率大幅度提高。
一台机床在不增加占地面积的条件下,等价于2-3台机床。
国外有少数工厂不仅实现了夜间无人,周六和周日两天也可实现无人加工。
因此带来的劳动生产率的提高和生产周期的缩短等效率是非常明显的。
6.有利于生产管理。
数控机床是由数字信息的标准代码输人,有利于计算机通信,构成由计算机来控制的批量生产系统,使之在技术上和管理上共同达到自动化,这就是柔性制造系统(FMS)。
主轴座
图1-1机床示意图
十字工作台
1.4国内外数控铣的加工现状
国外近年来发展迅速,主轴转速可达4000r/min~10000r/min,快速进给可达30m/min~40m/min,加速度可达1G,换刀时间提高到1s~2s。
大幅度提高了加工效率,并可获得Ra≤1µm的粗糙度。
另外,还可以加工硬度达60HRC的模块,形成对电火花加工的挑战。
高速切削加工与传统切削加工相比具有温度低(加工工件只升高3℃)、热变形小等优点。
目前它已经向更高的敏捷化、智能化、集成化方向发展。
高速铣削必须与相应的软件、加工工艺、刀具及夹紧头相配合。
高速铣削加工的发展促进了模具加工技术的发展,特别是对汽车、家电行业中大型型腔模具制造注入了新活力。
近年来,我国的数控铣加工技术发展迅速,数控产品的技术水平和质量在不断提高。
目前我国一部分普及型数控机床的生产已经形成一定规模,产品技术性能指标较为成熟,价格合理,在国际市场上有一定的竞争力。
但是我国数控加工技术的发展还存在着以下不足:
1.信息化技术基础薄弱,对国外技术依存度高。
我国数控机床行业总体的技术开发能力和技术基础薄弱,信息化技术应用程度不高。
行业现有的信息化技术来源主要依靠引进外国技术,对国外技术依存度教高,对引进技术的消化吸收停留在掌握已有技术和提高国产效率上,没有上升到形成产品自主开发能力和技术创新的高度。
具有高精度、高速、高效、复合功能、多轴联动等特点的高性能数控机床基本上还的依赖进口。
2.产品成熟度低,可靠性不高。
国外数控系统平均无故障时间在10000H以上,国内自主开发的数控系统仅3000H-5000H;整机平均无故障工作时间国外达800H以上,国内最好只有300小时。
3.创新能力低,市场竞争力不强。
我国生产数控机床的企业虽达百余家,但大多数位能形成规模生产,信息化技术利用不足,制造成本高,产品市场竞争力不强。
1.5数控铣加工的发展趋势
目前,世界先进制造技术不断兴起,超高速切削、超精密加工技术的应用,柔性制造系统的迅速发展和计算机集成系统的不断成熟,对数控加工技术提出了更高要求。
当今数控加工技术正朝以下几个发面发展:
1.高速度、高精度是数控机床的两个重要指标,它直接关系到加工效率和产品质量。
目前,数控系统采用位数、频率更高的处理器,以提高系统的处理速度。
同时采用大规模的集成电路和多微处理器,以提高系统的数据处理能力,即提高插补运算的速度。
并采用直线电动机直接驱动机床工作台的直线进给伺服进给方式,其高速度和动态响应特性相当优越。
采用前馈控制技术,使追踪滞后误差大大减小,从而改善拐角切削的加工精度。
为适应超高速加工的要求,数控机床采用主轴电动机与机床主轴和二为一的结构形式,实现了变频电动机与机床主轴一体化,主轴电动机的轴承采用磁浮轴承、液体动静压轴承或陶瓷滚动轴承等形式。
2.多功能化配有自动换刀机构各类加工中心,能在同一台机床上同时实现铣削、镗削、钻削、车削、饺孔、扩孔、攻螺纹等多种工序加工。
3.智能化现代数控机床将引进自适应控制技术。
4.数控编程自动化随着计算机应用技术的发展,UG、CAD/CAM/CAPP集成应用于数控编程。
5.可靠性最大化,数控机床的可靠性一直是用户最关心的指标。
6.控制系统小型化数控系统小型化便于将机、电装置结合为一体。
第2章主传动系统设计
2.1数控铣床的结构设计
数控铣床是机械和电子技术相结合的产物,它的机械结构随着电子控制技术在铣床上的普及应用,以及对铣床性能提出的技术要求,而逐步发展变化。
从数控铣床发展史看,早期的数控铣床是对普通铣床的进给系统进行革新、改造,而后逐步发展成一种全新的加工设备。
1952年,美国研制的世界上第一台三坐标数控铣床,其特点是用三个数控伺服系统替代了传统的机械进给系统。
早期的数控铣床同普通铣床相比,除进给系统是数控伺服系统外,外形和结构基本相同。
国内现生产的经济型数控铣床,就属于这种类型,因为这些产品是在普通铣床的总体结构基础上经局部改进而发展起来的。
2.1.1数控铣床的结构组成
1.主传动系统。
它包括动力源、传动件及主运动执行件(主轴)等,其功用是将驱动装置的运动及动力传给执行件,以实现主切削运动。
2.进给传动系统。
它包括动力源、传动件及进给运动执行件(工作台、刀架)等,其功用是将伺服驱动装置的运动与动力传给执行件,以实现进给切削运动。
3.基础支承件。
它是指床身、立柱、导轨、滑座、工作台等,它支承机床的各主要部件,并使它们在静止或运动中保持相对正确的位置。
4.辅助装置。
辅助装置视数控机床的不同而异,如自动换刀系统、液压气动系统、润滑冷却装置等。
2.1.2数控铣床机械结构的主要特点
1.高刚度和高抗振性。
铣床刚度是铣床的技术性能之一,它反映了铣床结构抵抗变形的能力。
根据铣床所受载荷性质的不同,铣床在静态力作用下所表现的刚度称为铣床的静刚度;铣床在动态力作用下所表现的刚度称为铣床的动刚度。
在铣床性能测试中常用铣床柔度来说明铣床的该项性能,柔度是刚度的倒数。
为满足数控铣床高速度、高精度、高生产率、高可靠性和高自动化的要求,与普通铣床比较,数控铣床应有更高的静、动刚度,更好的抗振性。
2.减少铣床热变形的影响。
铣床的热变形是影响铣床加工精度的重要因素之一。
由于数控铣床主轴转速、进给速度远高于普通铣床,而大切削量产生的炽热切屑对工件和铣床部件的热传导影响远比普通铣床严重。
而热变形对加工精度的影响,操作者往往难以修正。
因此,应特别重视减少数控铣床热变形的影响。
‘
3.传动系统机械结构简化。
数控铣床的主轴驱动系统和进给驱动系统,分别采用交流、直流主轴电动机和伺服电动机驱动,这两类电动机调速范围大,并可无级调速。
因此主铀箱、进给变速箱及传动系统大为简化,箱体结构简单,,齿轮、轴承和轴类零件数量大为减少,甚至不用齿轮,由电动机直接带动主轴或进结滚珠丝杠。
4.高传动效率和无间隙传动装置。
数控铣床在高进给速度下,要求工作乎稳,具有高的定位精度。
因此,对进给系统中的机械传动装置和元件要求具有高寿命、高刚度、无间隙、高灵敏度和低摩擦阻力的特点。
目前,数控铣床进给驱动系统中常用的机械装置主要有三种,即滚珠丝杠副、静压蜗杆—蜗轮机构和预加载荷的双齿轮—齿条机构。
5.低摩擦因数的导轨。
铣床导轨是铣床的基本结构之一,铣床加工精度和使用寿命在很大程度上决定于铣床导轨的质量,数控铣床的导轨则有更高的要求。
如在高速进给时不振动。
低速进给时不爬行,具有很高的灵敏度,能在重载下长期连续工作,耐磨性要高,精度保持性要好等。
2.1.3数控铣床的布局形式
立式数控铣床是数控铣床中数量最多的一种,应用范围也最为广泛。
小型数控铣床一般都采用工作台移动、升降及主轴转动方式,与普通立式升降台铣床结构相似;中型立式数控铣床一般采用纵向和横向工作台移动方式,且主轴沿垂直溜板上下运动;大型立式数控铣床,因要考虑到扩大行程、缩小占地面积及刚性等技术问题,往往来用龙门架移动式,其主轴可以在龙门架的横向与垂直溜板上运动,而龙门架则沿床身作纵向运动。
2.2数控铣床的工作原理和主传动系统的特点
2.2.1数控铣床的工作原理
数控铣床工作前,要预先根据被加工零件的要求,确定零件加工工艺过程、工艺参数,并按一定的规则形成数控系统能理解的数控加工程序。
即将被加工零件的几何信息和工艺信息数字化,按规定的代码和格式编制成数控加工程序。
然后用适当的方式将此加工程序输入到数控铣床的数控装置中。
此时,即可启动机床运行数控加工程序。
在运行数控加工程序的过程中,数控装置会根据数控加工程序的内容,发出各种控制命令,如启动主轴电机、打开冷却液,并进行刀具轨迹计算,同时向特殊的执行单元发出数字位移脉冲并进行进给速度控制,正常情况下可直到程序运行结束,零件加工完毕为止。
具体而言,数控铣床的工作过程,即加工零件的过程。
其主要步骤如下:
1.根据被加工零件图中所规定的零件形状、尺寸、材料及技术要求等,制定工件加工的工艺过程,刀具相对工件的运动轨迹、切削参数及辅助动作顺序等,进行军件加工的程序设计。
2.用规定的代码和程序格式编写零件加工程序单。
3.按照程序单上的代码制作控制介质。
4.通过输入装置把力D工程序输入给数控装置。
5.启动机床后,数控装置根据输入的信息进行一系列的运算和控制处理,将结果以脉冲形式送往机床的伺服系统(如步进电机、直流伺服电机、电液脉冲马达等)。
6.伺服系统驱动机床的运动部件,使机床按程序预定的轨迹运动,从而加工出合格的零件。
2.2.2主传动系统的特点
1.加工精度高。
控机床是精密机械和自动化技术的综合产品,所有的传动系统与机床的结构设计都考虑到很高的刚度和稳定性。
在设计传动机构时采取了减少误差的措施,并由数控装置进行补偿,所以数控机床有较高的加工精度。
由于加工过程自动化,加工精度不受人的操作过程、情绪和疲劳的影响,计算机还可以自动进行刀具补偿,不会因刀具磨损而影响工件精度和一致性。
数控系统中增加了机床误差、加工误差修正补偿,使加工精度得到进一步提高。
2.可以加工出具有复杂的曲线、曲面的零件。
由于计算机有高速的运算能力,可以瞬时准确地计算多个坐标轴瞬时的运动量,因此可以方便地复合成曲线或曲面。
3.主轴变速迅速可靠。
数控铣床的变速是按控制指令执行的,因此变速