工艺管理规程.docx
《工艺管理规程.docx》由会员分享,可在线阅读,更多相关《工艺管理规程.docx(20页珍藏版)》请在冰豆网上搜索。
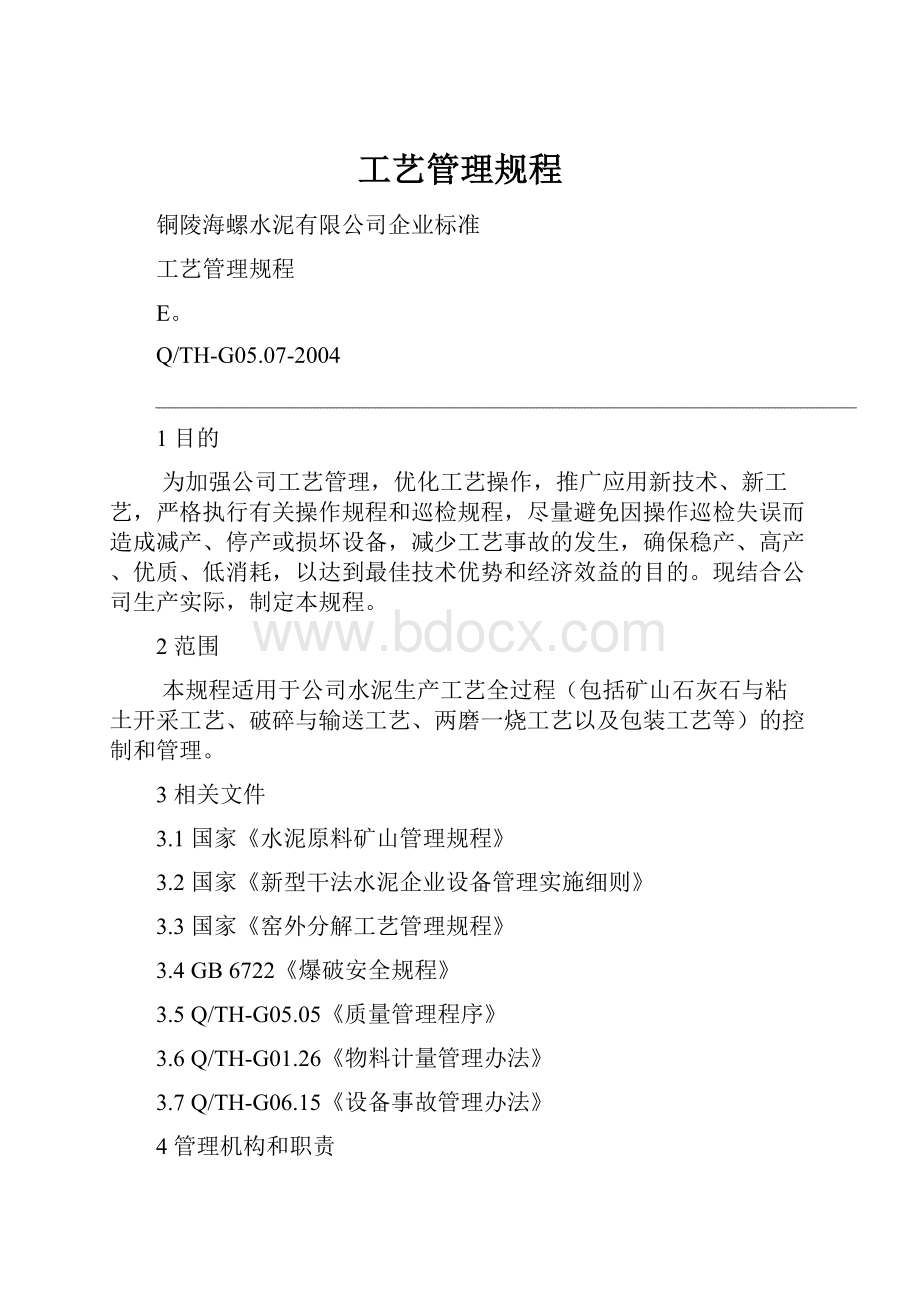
工艺管理规程
铜陵海螺水泥有限公司企业标准
工艺管理规程
E。
Q/TH-G05.07-2004
1目的
为加强公司工艺管理,优化工艺操作,推广应用新技术、新工艺,严格执行有关操作规程和巡检规程,尽量避免因操作巡检失误而造成减产、停产或损坏设备,减少工艺事故的发生,确保稳产、高产、优质、低消耗,以达到最佳技术优势和经济效益的目的。
现结合公司生产实际,制定本规程。
2范围
本规程适用于公司水泥生产工艺全过程(包括矿山石灰石与粘土开采工艺、破碎与输送工艺、两磨一烧工艺以及包装工艺等)的控制和管理。
3相关文件
3.1国家《水泥原料矿山管理规程》
3.2国家《新型干法水泥企业设备管理实施细则》
3.3国家《窑外分解工艺管理规程》
3.4GB6722《爆破安全规程》
3.5Q/TH-G05.05《质量管理程序》
3.6Q/TH-G01.26《物料计量管理办法》
3.7Q/TH-G06.15《设备事故管理办法》
4管理机构和职责
4.1公司成立工艺质量管理委员会,下设采矿、粉磨、窑、包装、耐火材料五个工艺管理专业小组。
4.2生产安全处负责工艺管理委员会的日常工作,主要内容有:
4.2.1组织工艺系统全面技术标定,审订工艺技术参数、主机台时产量及消耗定额等。
4.2.2指导生产单位的工艺技术,解决生产工艺及质量管理中出现的主要技术问题。
4.2.3组织审查工艺技术革新和合理化建议;积极推广新技术、试制新产品、改进新工艺,努力提
共13页第1页
标准化委员会2004-01-10批准2004-01-15实施
Q/TH-G05.07-2004
高产量和产品质量。
4.2.4组织调查、分析、处理工艺事故。
4方针和原则
5.1工艺管理的方针:
以质量为中心,以节能增产为重点,提高矿山开采技术和管理水平,加强工艺系统主机设备的科学管理,改善粉磨工艺和烧成工艺,提高设备运转率,积极推广新技术、新工艺,保证安全、高效生产,创造最佳经济效益。
5.2工艺管理原则
根据公司生产工艺特点,制定矿床开采、穿孔爆破、原料破碎、粉磨、烧成、包装等主机的管理制度及操作方法,确定合理的经济技术指标和技术参数,充分运用计量监测仪表、计算机等先进技术手段,加强过程控制,确定合理的安全运转周期,实现优质、稳产、高效、低耗、安全和文明生产。
6矿山工艺管理
6.1矿山管理总则
6.1.1严格遵守“采剥并举、剥离先行”的采矿工作原则,在安全、经济的前提下重点抓好计划开采、穿爆工作和设备管理工作,经常保持合理的“三量”(开拓矿量、准备矿量、可采矿量)关系,以保证窑磨对石灰石、粘土质量与数量的要求。
6.1.2认真贯彻执行《中华人民共和国矿产资源法》、《全民所有制矿山企业采矿登记管理暂行办法》和《矿产资源监督管理暂行办法》,提高矿产资源综合利用水平。
6.1.3严格执行国务院颁发的《矿山安全法》,建立健全安全生产体系,矿山第一责任人全面负责安全工作,班组设兼职安全员,分厂设专职安全员,爆破安全纳入专业技术管理,确保安全生产。
6.1.4矿山做好长、中、短期开采计划,每周召开分厂生产调度会,对前一周的工作进行总结评价,并部署下周工作;每月底召开分厂工艺质量分析会,总结分析当月生产、质量指标完成情况,同时提出下月生产质量作业计划。
6.2定义
6.2.1开拓矿量:
指开拓工程已经完成,出矿和废石的运输系统已经形成,具备了进行采准工作的条件。
6.2.2准备矿量:
是开拓矿量的一部分,指已完成剥离工程和开段沟的各水平上所有的台阶的矿量。
6.2.3可采矿量:
是准备矿量的一部分,指生产中能连续采出的矿量。
6.2.4剥离量:
指为了采掘有用矿石所进行的废石、覆盖土、裂隙充填物的剥离,并已运至指定堆放地点的数量。
共13页第2页
Q/TH-G05.07-2004
6.2.5爆落量:
指爆落下来的有用矿石(包括采准工程中的有用矿石)。
6.2.6挖掘机效率:
指电铲(油铲)装车的效率,其计算公式为:
挖掘机装车采掘总量(吨)
挖掘机效率=
(吨/米3.班)各台挖掘机斗容量×实际工作台班之和
6.2.7钻机效率:
指钻机每一台班钻孔深度。
钻孔总深度(米)
钻孔效率=
(米/台班)钻机实际工作台班数
6.2.8设备完好:
指设备处于完好的技术状态。
第一、设备性能良好,机械设备能稳定的满足生产工艺要求,动力设备的功能达到原设计或规定标准,运转无超温超压等现象。
第二、设备运转正常,零部件齐全,安全防护装置良好,磨损、腐蚀程度不超过规定的标准,控制系统、计量仪器、仪表和润滑系统工作正常。
6.3加强矿石的损失管理,尽量搞好边坡矿体的回采工作,提高回收率
6.4开展必要的取样和地质编录、地质测量工作,摸准矿石品位的变化规律,建立三维坐标网和采掘终了平面图。
6.5质量控制
6.5.1石灰石矿每次爆破前,质量控制处应对炮孔样取样分析,指导下料。
6.5.2石灰石下料口要严格执行下料配比要求,做好优劣搭配工作。
6.5.3质量控制处按有关要求对石灰石生产样进行取样分析,如遇到不合格数据,应及时通知矿山分厂生产调度调整。
6.5.4各质量控制指标见公司《年度生产经营综合计划》。
6.6采矿准备
6.6.1有计划地进行采矿准备工作,保持一定的“三量关系”,按《规程》要求各级矿量至少保持下列数值:
开拓矿量:
24个月矿产量
准备矿量:
12个月矿产量
可采矿量:
6个月矿产量
6.6.2公司下达年度生产计划的同时下达采矿、采准和剥离任务并列为考核矿山三项指标。
6.6.3矿山根据剥离、采准的工作量配备固定设备和人员的专业队伍,合理安排剥采比,尽量减少排废,对排出的废料一次性运到开采境界外。
共13页第3页
Q/TH-G05.07-2004
6.6.4石灰石矿山采掘面的工作参数应符合以下要求:
6.6.4.1台阶高度:
正常段高为15米,台段坡面角为75°-90°。
6.6.4.2工作平台宽度:
平台初始宽度不小于30米,正常生产时为45-50米。
6.6.4.3工作线长度:
每台4.6立方米电铲的最小工作线定为120米-150米。
6.6.5粘土矿采掘面的工作参数应符合以下要求:
6.6.5.1台段高度2-5米,台段坡面度75°-90°。
6.6.5.2采场面坡度0.5-5%。
6.6.5.3工作线长度20米。
6.6.6在上下两台段同时开采时,运输车辆外缘至穿孔设备内缘应保持5米以上的距离,穿孔设备外缘至平台边缘,应保持2.5-3米。
6.6.7根据地质地形条件采用一定的技术措施减少三角矿的遗留,其三角矿的高度不得超过台阶高度。
6.7矿床开采
6.7.1矿山按设计院编制的总体设计方案,认真编写年度采掘计划(进度计划表,开采计划平面图等),报公司审批,严禁乱采乱挖。
6.7.2按计划处理边坡残留的矿块,在采掘终了境界时需特殊的爆破方法(光面或预裂法)保护边坡,开采属边坡危险地带需设安全平台或清扫平台,保证正常均衡生产。
6.7.3采用自上而下水平分层开采法。
上下台段同时生产时,上一台段保持50米的超前关系,保证铲装安全与穿孔作业。
6.7.4每一台段有个合乎技术要求的固定出入沟,采矿场地保持一定的规则形状与尺寸。
沿采掘线方向保持平整,平整程度为±50厘米/100米,在工作平台横断面方向从上台段坡底线至该工作平台边缘(坡顶线)应形成微坡,高差小于0.3-0.5米。
6.7.5保持采场的整体推进,铲装不得留堆(当采场面过小时造成的散堆要及时处理),散落地面的矿石要及时清理。
6.7.6测量人员每季度应对整个矿山的开采进行实测,并绘制相应的平面图用于指导生产。
台段间要有符合技术标准的联络道。
6.8穿孔爆破
6.8.1爆破工作严格遵守GB6722-86《爆破安全规程》,采矿技术人员根据本矿岩石力学特性,结合开采爆破方法,制定穿爆参数;从事爆破工作及有关爆破器材管理的人员要经过培训持证上岗。
6.8.2爆破工作要有严格的审批制度,10吨以下炸药量的中深孔常规爆破由矿山分厂内部审批,10吨以上炸药量的中深孔常规爆破或特殊性质爆破上报公司审批。
6.8.3每批布孔由技术人员现场实测,炮孔深度由操作人员测量,特殊地形条件下要有设计施工图一式两份,一份分厂归档备查,一份自用。
穿孔施工的孔位误差为±0.3米。
6.8.4矿山中深孔爆破,主要采用ROC860HC钻机和DM45钻机穿孔,中深孔爆破和特殊性质爆破,
共13页第4页
Q/TH-G05.07-2004
每次必须编写爆破设计说明书,其内容包括:
炮孔平面布置图、施工说明、安全防范措施等。
特殊情况下还必须有爆破网络平面图、装药结构图等内容。
6.8.5矿山爆破规模,必须根据公司年生产计划按季、月安排。
为保证穿爆工作的正常进行,不得
低于30天左右的爆落矿量。
6.8.6爆破时,飞散物对人员的安全距离:
裸露药包爆破法:
400米;
浅眼爆破法:
300米;
中深孔爆破的安全距离按设计要求,但不得小于300米。
沿下边方向的飞石安全距离应增大50%。
6.8.7特殊情况下的爆破,矿山应根据需要及时进行必要的测量,并组织有关人员研究爆破效果,总结和积累爆破经验。
6.8.8矿山钻机各班效率应达到以下指标:
钻机类型f系数班效率
手风钻机6-10≥35米/台班
ROC860HC钻机8-10≥90米/台班
DM45钻机8-10≥110米/台班
6.8.9中深孔爆破应满足以下基本要求:
6.8.9.1大块率在1%以下,矿石粒度有利于铲装和破碎作业。
6.8.9.2爆堆高度、形状有利于高效挖掘和安全作业。
6.8.10遇有下列情况之一者,禁止爆破:
6.8.10.1爆破参数或施工质量不符合设计要求。
6.8.10.2危及设备或建筑物安全,没有防护措施。
6.8.10.3危险区边界未设立警戒。
6.8.10.4大雾或雷雨。
6.8.10.5现场光线不足。
6.8.11在地质条件较差难以成孔时应采取糊孔的方法,遇溶洞裂隙时要减慢穿孔速度,多疏通孔内石碴并注意钻机仪表盘相关数据,避免出现卡钻现象。
6.8.12加强成孔控制,爆破前应对孔进行实测,不合格孔进行疏通或重补,要在成孔的合格率大于95%时方可爆破。
6.8.13装药时若孔内有水,禁止用粉状炸药直接装药,要用密度大于1.0的乳化炸药(散装)。
若孔内有溶洞时采取用整卷炸药吊药卷且上面用粉状炸药,以确保有效爆破。
6.8.14装药时应避免药卷直接冲击,在任何情况下绝对禁止整卷药直接冲击炮头。
为保证炮孔的充填效果,技术人员要经实测方可充填。
若装药量过多,则应采取水冲或掏药法以保证适度充填,但整个过程要避免铁器与炸药直接接触。
6.8.15在边坡地带应适当增加穿孔密度,使炸药单耗增加10-20%,在特殊情况下应有技术人员指
共13页第5页
Q/TH-G05.07-2004
导施工,要通过改变装药结构或充填方式达到降低大块的效果,保持每孔上下面积和均衡性及同批爆破孔向的一致性。
6.8.16出现爆破质量事故时,应由矿山分厂领导召集有相关技术人员参加的分析会,查明原因,
拿出书面处理方案和整改意见。
6.9铲装运输
6.9.1严禁挖掘机挖掘未松动的矿岩和底根,超过1000毫米石灰石大块严禁装车。
严格按比例装厚、薄岩灰层。
6.9.2多台设备同一工作面作业时,相邻两机之间距离大于两作业半径之和。
电铲作业时,15米内不许有人或非指定设备。
6.9.3当爆破和作业面出现伞岩、偏滑等危及安全时,应停止作业,转移到安全的区域作业。
挖掘机操作人员应每班巡视架头大块情况,避免设备被砸。
6.9.4加强道路的维护,保持良好的路况,降低矿车轮胎的消耗和油耗。
6.9.5挖掘机生产效率达到如下指标:
挖掘斗容(立方米)1.64.66.17.0
台班效率(吨)500130029003900
台年效率(万吨)2565145195
6.9.6矿车出勤率应达到65%以上。
铲装作业选定相对的工作位置,保持合理的铲车比,并做好质量控制记录。
6.9.7进行必要的剥离和排废时,要在开采境界外设立排废场,对排废的物料一次性运到排废场,排废场要有推土机,排废的物料要按推土工艺排废,排废时要保证安排专门人员。
6.9.8电铲在各采场的推进速度应由月生产作业计划统一安排,作业计划必须结合地质勘探和生产勘探,矿山采矿工段管理人员应对采掘进度负责。
6.10以上内容对石灰石矿有效,除爆破工程和工作面参数外,对粘土矿也同样有效。
7原燃材料破碎及输送工艺管理
7.1科学管理好破碎机及其输送系统,合理控制出料粒度,确保各类原料(石灰石、粘土、砂岩、煤、石膏等)供应,满足上下道工序间的物流需要。
局控操作人员要及时根据破碎机、板喂机电流及台时产量等信息合理调整喂料量,优化操作方式,使各项指标最优。
7.2根据产品粒度及破碎机的生产能力及时更换锤头(板)或调整出料篦条,确保出料粒度合格。
7.3喂入破碎机石灰石要严格控制含土量、含水量,并在工艺线设立除铁器和金属探测报警系统,以预防铁件进入破碎机和下道工序。
7.4为控制好石灰石质量,质控处应每一小时取料检验一次,检测结果有异常情况,应及时通知矿山分厂,以便调整搭配.
共13页第6页
Q/TH-G05.07-2004
7.5破碎后的物料由皮带输送机输送至堆料机堆到堆场或进入水泥磨磨头仓。
运输过程中,工艺线巡检人员应加强巡检,发现问题及时处理,确保物料运输顺畅。
停机前应卸空皮带上物料,尽量避免设备带负荷起动。
加强各下料溜子的监控,预防堵料。
严禁定点堆料,确保均化效果。
7.6喂入破碎机的石料粒度严禁大于1000×1000×1000mm,料量输入均匀,防止堵料;石灰石出
料粒度≤75mm。
7.7其它原燃材料(粘土、煤、石膏、混合材等)粒度控制指标按如下要求执行:
7.7.1粘土/砂岩破碎机进料粒度≤400mm,出料粒度≤80mm,并防止金属件进入堆场。
7.7.2砂岩出料粒度≤30mm(占85%以上)。
7.7.3原煤出料粒度≤25mm(占85%以上)。
7.7.4石膏出料粒度≤30mm。
7.7.5混合材粒度≤30mm。
7.8以上各原燃材料的各质量控制指标按《公司年度生产经营综合计划》执行。
8原料磨系统工艺管理
8.1科学管理磨机,合理调整立磨喂料量、研磨压力、差压等关系,稳定料床,减少振动。
8.2在保证产品质量的前提下,努力提高磨机产量。
保持料、风、选粉机效能的相互适应,以提高粉磨效率,降低电力消耗。
各种入磨物料量和比率由计算机自动控制,必要时也可手动设定。
8.3立磨烘干热源由预热器废气提供,进磨风温250℃左右,出磨风温<95℃。
加强磨机密闭堵漏,系统漏风量不超过总风量8%。
8.4加强对增湿塔管理,定期检查修理喷水系统。
停磨时,入电收尘气体温度控制在160℃以下,要求出增湿塔物料不结块。
8.5加强磨机系统收尘设备(电收尘、袋收尘等)管理,提高收尘效率。
粉尘排放浓度要达到设计要求。
坚持定期维护保养,及时检修,注意保温和密闭堵漏,防止漏风。
8.6根据需要在磨机作业时定期测定物料相对易磨系数、筛余曲线,以检查粉磨效果。
9窑系统工艺管理
9.1回转窑系统工艺管理
9.1.1窑外分解工艺管理的原则是:
根据入窑生料经过预热分解的特点,合理的确定回转窑系统风、煤、料、窑速和各种温度压力等参数,调整好窑与分解炉、预热器、冷却机的相互关系,稳定系统的热工制度,保护好窑皮,延长运转周期,实现优质、稳产、低耗和安全文明生产。
9.1.2全系统设备和自动化仪表,PLC要满足生产工艺要求,一次风、入分解炉三次风、窑尾排风、窑速、喂料、喂煤等设备的阀门、计量仪崐表指示准确,系统密封装置完好。
共13页第7页
Q/TH-G05.07-2004
9.1.3稳定喂料量、喂煤量的目标值和窑速,如有异常情况,相关单位、和班组人员应及时排除,保障目标值的准确性。
9.1.4窑内燃料要完全燃烧,电收尘器入口一氧化碳含量在0.2%以下,烧成带筒体表面温度控制
在330℃以下,最高不超400℃。
9.1.5加强日常的生产操作管理,使回转窑工况处于受控之下运转、崐延长耐火砖使用寿命,降低砖耗。
窑皮不好应及时补挂,严格执行掉砖崐红窑必停制度。
9.1.6加强系统设备的管理工作,做好计划检修和日常维护,建立健全设备巡回检查制度,确保回转窑年运转率达到90%以上。
9.1.7因故停窑或计划检修时,制造一分厂或制造二分厂应安排专人对窑、冷却机、预热器和分解炉等设备内部进行全面检查,清理系统的积灰和结皮,对系统耐火材料要仔细检查其厚度、剥落等情况并认真记录,如有蚀薄、松动、脱落等要修补或更换,确保下一个周期安全运转。
9.1.8严格控制原燃料中的有害成份含量,入窑生料一般控制在:
R2O〈1.0%。
(烧制特种水泥熟料时另行规定)有害成份超标时,制造一分厂、制造二分厂和质控处应采取有效措施加以解决。
9.1.9检修后预热器人孔门密封前,制造一分厂、制造二分厂应组织机械、工艺技术人员对冷却机、回转窑、预热器进行最后检查验收,确认无问题后,进行单机试车,确保下一个周期长期安全运转。
9.1.10根据生产需要及时对回转窑进行单项测定,必要时进行全面热工平衡计算。
9.2预分解系统工艺管理
9.2.1预分解系统管理原则是:
稳定控制入窑生料分解率,各级旋风筒内撒料均匀,通风畅通,稳定系统热工制度。
9.2.2定期检查清理各预热器锥部、窑尾斜坡、缩口等处的结皮和积料。
9.2.3认真搞好熟料冷却机进料端、窑头、窑尾、三次风管系统及各级预热器、连接风管的捅灰孔、人孔门等处的密闭堵漏工作,努力提高二次风温、三次风温。
9.2.4及时调节分解炉喂煤量和三次风量,分解炉出口温度控制在850至890℃,一级筒出口温度控制在330℃以下,不得高于350℃,高温风机进口气体温度应小于350℃,入窑物料分解率控制在90-95%。
9.2.5合理调节三次风量,稳定系统各处压力,三次风管进分解炉负压控制在400pa左右,一级筒出口负压控制在:
4600至5200pa,高温风机进口负压控制在5200至5700pa。
9.2.6定期检查分解炉内燃烧情况及各预热器翻板阀动作情况,保持各级下料翻板阀灵活动作,防止因翻板阀动作不灵造成积料堵塞。
9.3窑尾收尘系统工艺管理
9.3.1适时检查增湿塔喷头雾化情况并及时清洗喷头,增湿塔出口温度控制在160±10℃,电收尘器进口温度控制在150±10℃,电收尘器运转率要达到主机运转率的95%以上,废气中的粉尘排放浓度达到国家标准。
9.3.2增湿塔供水系统要灵活可调,增湿塔出口气体温度和水量投入实现自控,以满足工艺要求。
共13页第8页
Q/TH-G05.07-2004
卸料装置避免漏风。
9.3.3电收尘的防爆和报警装置要保持完好,进电收尘器CO含量严格控制在0.8%以下。
9.3.4及时清理电收尘的阴极丝、阳极板和石英套管、积灰斗上的积灰,调整好极丝极板间距,维
护好振打及电控装置并防止气流短路。
9.3.5增湿塔、电收尘的回灰要采用优先入均化库,其次考虑入预热器的方式。
9.4熟料冷却及破碎系统
9.4.1篦冷机的管理原则:
合理设定各风室风量和风压,加速熟料冷却,努力提高二次风和三次风温度,减少热损失,提高冷却效率。
9.4.2合理控制篦床下各风室压力,减少各风室漏风,篦床下压力和篦速要实现自控,以保证料层厚度稳定在600mm左右;根据熟料出口温度相应调节各风室的风量,保证出冷却机熟料温度小于环境温度+65℃。
9.4.3篦冷机电收尘的排风量要根据窑尾排风相应调节,保持窑头罩负压稳定在30至50pa,同时二线还要满足地坑各扬尘点的收尘要求,保证崐地坑收尘点负压。
9.4.4要经常检查篦床和篦板的运行情况,出破碎机的熟料粒度要小于25mm。
9.4.5停窑时,篦冷机二、三段篦床的熟料要卸空,但一段篦床可保持一定厚度的料层,应注意停窑时间较长时要开冷却机,防止压住篦床。
9.4.6每次停窑检修,要同时检查冷却机的耐火材料,磨损严重的地方要进行更换。
10煤粉制备系统工艺管理
10.1为保证煤磨安全运转,选用最佳的操作参数,做到风、煤、温度、研磨体相互适应,提高粉磨产量和质量。
10.2煤磨入口气体温度控制在250℃以下,出口气体温度要保证煤粉水份合格,一般控制在65℃至80℃,不得超过80℃,入磨原煤粒度在25mm以下,原煤水分小于8%。
10.3系统设备必须完好。
密闭安全可靠,防止结露;防爆及惰性气设施和检测装置要灵敏。
煤磨电收尘出口O2含量<11%,CO<0.2%。
袋收尘器入口温度65-75℃。
10.4计划检修时要放空煤粉仓;紧急停窑时,关注煤粉仓温度变化,必要时要加生料粉,并加强巡检,一旦出现煤粉仓温度上升,应及时组织处理,确保安全。
10.5风扫球磨应制定合理配球方案,定期清仓补球,改变配球方案要将前、后台时产量、细度、水分、原煤性能、研磨体配比、消耗量、电耗等记录在技术台帐上,用数理统计的方法分析,不断提高技术管理水平。
煤立磨要定期检查磨盘磨辊衬板磨损情况,磨损严重的要及时更换。
10.6所配的仪表,特别是报警仪表,必须在完好状态下工作,若有损坏,必须及时修复或补齐。
10.7根据生产需要,对风扫球磨及时进行风量、温度、回粉细度、风压等单项技术测定。
对煤立
共13页第9页
Q/TH-G05.07-2004
磨进行风量、温度、风压、选粉机转速、叶片开度等进行测定、检查和调整。
10.8对煤磨电收尘、袋收尘系统要作好密闭堵漏工作。
防爆阀应灵活好用,灰斗定期
清理,不准积灰,保证电收尘及袋收尘正常运行。
11水泥磨系统工艺管理
11.1缩小入磨粒度,保证磨内通风良好,确定合理的研磨体级配和最佳装载量,改进磨内结构形式和能量传递方式,经常保持各仓能力的平衡和料、风、选粉效率的相互适应,以提高粉磨效率,降低能耗。
11.2根据入磨物料,循环负荷和产品质量情况及时调整喂料和选粉设备,努力做到均匀喂料,防止发生饱磨、空砸现象。
11.3各种入磨物料严格按质控处规定均匀搭配,努力防止、减少喂料秤断料现象的发生。
11.4严格控制入磨物料的粒度、水份和温度。
入磨物料粒度≤25mm。
入磨物料温度≤100℃。
加强磨内通风,提高粉磨效率,出磨水泥温度控制在130℃以下。
11.5水泥磨要定期清仓补球。
清仓时研磨体要分规格挑选过磅,按配球方案规定的数量装入磨内,若改变研磨体级配和装载量,应报请公司分管领导批准。
11.6根据需要,在磨机作业期间,定期测定物料相对易磨系数、选粉效率、循环负荷率,以检查粉磨效果。
11.7凡配球方案、选粉设备和磨内结构改进时,装运分厂工艺技术主管人员应将前后的筛余曲线、台时产量、质量、原材料性能、研磨体级配和电耗等按时记录在技术台帐上,做出技术分析并报公司分管领导。
11.8每次检修,装运分厂要详细检查研磨体、隔仓板、衬板、选粉机、细粉分离器及袋收尘各处连接风管、密封装置和工艺阀门,发现异常及崐时处理。
磨机在运行中发现衬板或螺栓松动、脱落,必须停磨处理。
11.9补加研磨体数量应结合以下三方面考虑:
11.9.1以实际球耗计算补球量:
补