紧密纺使用关键技术.docx
《紧密纺使用关键技术.docx》由会员分享,可在线阅读,更多相关《紧密纺使用关键技术.docx(14页珍藏版)》请在冰豆网上搜索。
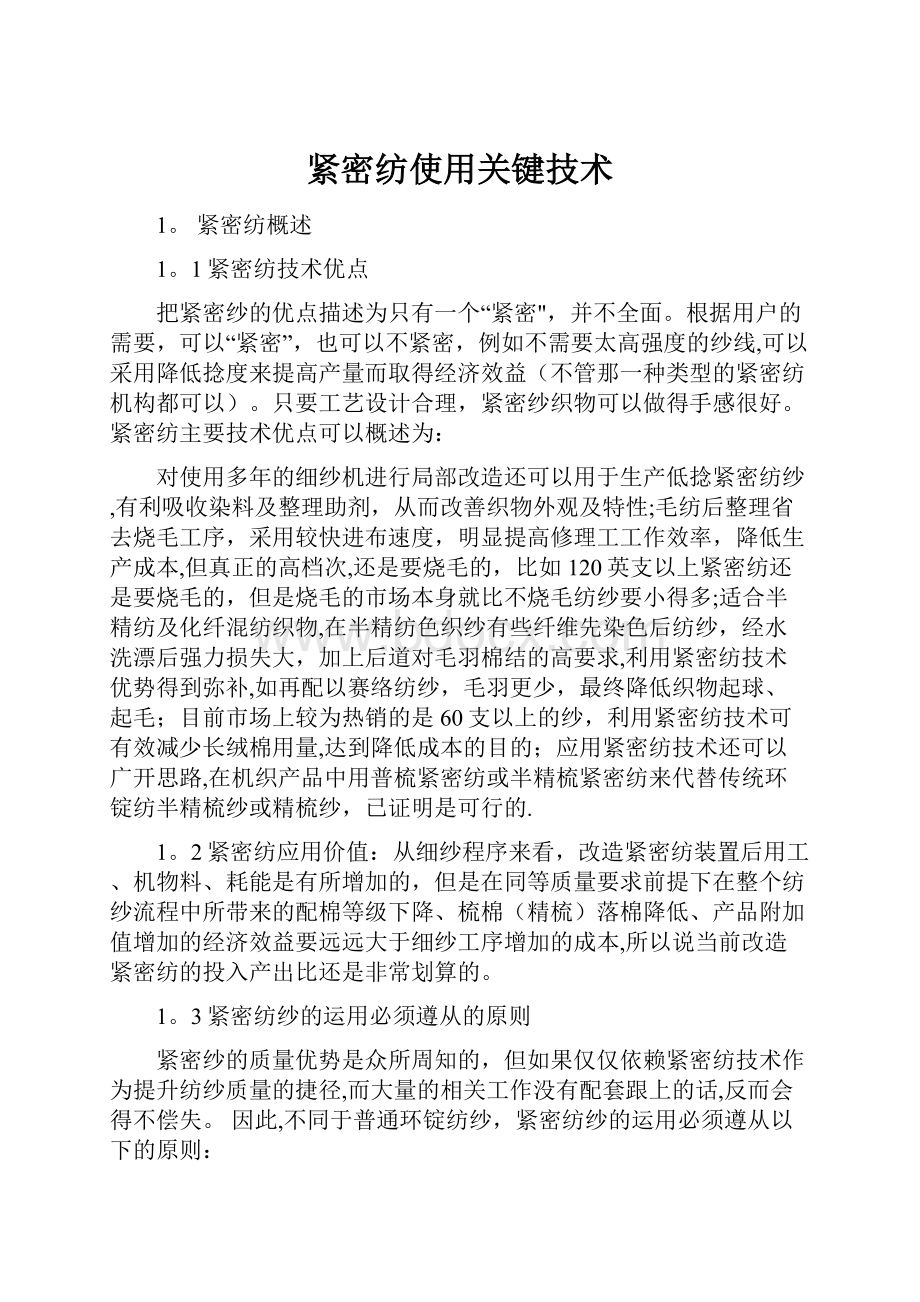
紧密纺使用关键技术
1。
紧密纺概述
1。
1紧密纺技术优点
把紧密纱的优点描述为只有一个“紧密",并不全面。
根据用户的需要,可以“紧密”,也可以不紧密,例如不需要太高强度的纱线,可以采用降低捻度来提高产量而取得经济效益(不管那一种类型的紧密纺机构都可以)。
只要工艺设计合理,紧密纱织物可以做得手感很好。
紧密纺主要技术优点可以概述为:
对使用多年的细纱机进行局部改造还可以用于生产低捻紧密纺纱,有利吸收染料及整理助剂,从而改善织物外观及特性;毛纺后整理省去烧毛工序,采用较快进布速度,明显提高修理工工作效率,降低生产成本,但真正的高档次,还是要烧毛的,比如120英支以上紧密纺还是要烧毛的,但是烧毛的市场本身就比不烧毛纺纱要小得多;适合半精纺及化纤混纺织物,在半精纺色织纱有些纤维先染色后纺纱,经水洗漂后强力损失大,加上后道对毛羽棉结的高要求,利用紧密纺技术优势得到弥补,如再配以赛络纺纱,毛羽更少,最终降低织物起球、起毛;目前市场上较为热销的是60支以上的纱,利用紧密纺技术可有效减少长绒棉用量,达到降低成本的目的;应用紧密纺技术还可以广开思路,在机织产品中用普梳紧密纺或半精梳紧密纺来代替传统环锭纺半精梳纱或精梳纱,已证明是可行的.
1。
2紧密纺应用价值:
从细纱程序来看,改造紧密纺装置后用工、机物料、耗能是有所增加的,但是在同等质量要求前提下在整个纺纱流程中所带来的配棉等级下降、梳棉(精梳)落棉降低、产品附加值增加的经济效益要远远大于细纱工序增加的成本,所以说当前改造紧密纺的投入产出比还是非常划算的。
1。
3紧密纺纱的运用必须遵从的原则
紧密纱的质量优势是众所周知的,但如果仅仅依赖紧密纺技术作为提升纺纱质量的捷径,而大量的相关工作没有配套跟上的话,反而会得不偿失。
因此,不同于普通环锭纺纱,紧密纺纱的运用必须遵从以下的原则:
(1)合理配棉和工艺优化:
一般情况下客户使用紧密纱,因其价格相对较高,均是用在质量要求较高的品种上,所以对纱线的质量要求也更为苛刻。
常规的工艺思路设计难以满足要求,必须进行系统性考虑,从原料、工艺上不断优化,最大限度发挥紧密纺的优势。
(2)更洁净的生产环境:
目前实用的紧密纺基本采用的是气动凝聚方式,虽然紧密纺减少了毛羽和飞花,但是由于负压吸力,使得整个机器成为一个大负压区,它能吸引相邻机器产生的飞花和灰尘.因此,应将紧密纺细纱机安置在单独的房间或空间,并增加清洁频率。
(3)网格圈的清洁:
在一段时间的运转后,网格圈表面会黏附灰尘、短绒、棉蜡和前纺工序中的添加剂如蜜露橙等,从而造成网眼堵塞或网眼各处吸气不匀,导致集聚效果和条干恶化。
因此,必须给网格圈做必要的清洁和周期性的清洗。
(4)钢领、钢丝圈的配置:
由于紧密纺纱的毛羽减少,使得钢领与钢丝圈之间的润滑膜不能快速形成,因此对钢领、钢丝圈的要求较高。
(5)上罗拉皮壳的打磨:
根据主牵伸、纤维材料及纱线支数的不同以及由于紧密纺结构要求粗纱动程较普通环锭纺小等原因,牵伸及引纱胶辊的打磨周期为8~12周,每次打磨皮壳的磨削量大约是单面0。
15mm。
1.4紧密纺好坏的评价标准
标准1成纱的毛羽
有必要把小于2毫米的短毛羽和大于3毫米的长毛羽分开,其中短毛羽对后道工序及最终产品的纺织是最为理想的,而长毛羽则应尽可能去除。
作为进行比较的一种方法,齐格勒(Zweigle)的S3-值已用作今天的标准,此值越小,毛羽越好,纱的强力和伸长率也越好。
标准2纱线的测试值
首先需要确认只有毛羽及与之有关的伸长率及强力主要取决于紧密纱装量,而纱线的其他品质主要受系统设计的影响。
因此对纱的品质测试值进行比较时假设纺纱用的是相同的系统,而且在可进行比较的工作条件下进行。
标准3后序加工的可靠性
关键是要避免纱疵,尤其是在后序加工中或在最终产品中才出现的纱疵,少数的失去控制的纱疵会使最好的纱线质量降低等级。
因此,在实际评价纱疵品值指标时,更为重要的是使离散范围尽可能小以及消除失去控制的纱疵.
标准4购置成本和使用成本
只有当其加工成本不比普通纱线的生产成本高或略高一点,紧密纱才能在大范围内成功推广。
通过在纱线后序加工及其最终产品对可测算的优点加以比较后,投资的偿还期以及其运行成本也必须清清楚楚地回收。
标准5对现有纺纱机的改造及操作灵活性
如果紧密纺系统不仅用于新机而且也可用于已有设备的改造,这对纱厂来说是特殊的优点。
同时,紧密纺系统的可操作性能也是一个非常重要评价因素,如:
对运转操作、设备维护、器材周转等方面的影响。
1。
5紧密纺和环锭纺操作时的几点不同
(1)开车.环纺机台风机启动后就可以开主电机,而紧密纺由于增加了负压系统,由初始值到工艺负压一般需要15-20秒,所以紧密纺机台开车时按下风机启动后需要延15-20秒后启动主电机,否则因为集聚槽负压低会形成一段抱合比较松散的纱段,这种松散段有可能形成断头或者自络切痕,应当予以避免.对此,可采用负压监测的功能并配合机器上增加时间控制,传感器只有在压力到达所设置的压力后给细纱机PLC控制系统一个信号,此时细纱机才可以启动,同时负压室应当在每次落纱时进行清理,保证负压稳定。
(2)清洁。
由于紧密纺增加了网格圈等紧密专件形成负压区,机台清洁的耐久性更差。
清洁维护工作较环锭纺有所增加并且对负压部件的周期性检查也是必须的。
(3)电气。
为了达到负压可调,紧密纺机台一般配备变频器,增加变频器后对电气部分的养护工作要求更高,主要包括变频器内部的周期性清洁和和负载部分的维护与检查.
(4)空调。
紧密纺装置对空调系统的影响主要体现在对车间空气有二次污染并对车间气流走向有一定的影响.对于大风机形式可以把风机气流通过管道外排,而小风机系统形式就没这么幸运了,主要表现在夏季车间温度过高,机台下部气流紊乱使得飞花断头和有害纱疵增加,只有通过加大空调系统的送排风量来改善。
因此,小风机形式对空调系统的影响应该大于大风机形式。
1。
6低负压装置与高负压装置
目前,总风道式结构,经过4次演变,现在各家基本成熟。
短车变截面设计能控制在小于30Pa以内,等截面设计能控制在100Pa以内,长车(1008锭)变截面设计能控制在100Pa以内。
小电机控制的小风机,当堵花时,或清洁不良时,负压会有1000Pa的变化,并且小电机经常坏,这是负压式的第一代;当使用大电机传动多个小风机时,(这是无锡一棉用的)大电机不坏了,但传动小风机的效率差异大了,且传动带在高速下,发热伸长了,传动效率有问题了,因此负压偏差就大了,这是负压式的第二代;第三代是等截面总风道式;第四代是变截面总风道式。
低负压装置的工作原理:
通过气流的横向推力与低负压的吸力的共同作用,使絮条达到一定量的集聚,所以低负压必须大流量,大流量的工作状态好坏,必须通过侧向导流来达到。
低负压装置的特点:
集聚区间宽度大;气流量大;有横向导流装置,由于导流装置的作用,使得絮条只有横向的移动,没有纤维的滚动,同时缺少对絮条顶部的压力。
低负压装置对絮条的紧密作用:
斜槽与直槽作用基本一样;对絮条的密实度有限;对絮条的紧度控制不好.
高负压装置的工作原理:
利用气流的高负压对絮条进行强吸附,在斜槽的作用下产生半自动状滚动,使絮条达到一定量的紧密度与圆整度。
高负压装置的特点:
负压高;流量小;集聚槽窄;无须横向导流装置;须网圈装置向前输送絮条。
高负压装置的作用:
对絮条的作用力强;絮条的密实度随负压的提高而提高;絮条的滚动作用使絮条得到一定圆整度的前提条件;斜槽的斜度必须与负压的作用相匹配;滚动作用的好坏与絮条输送速度有关。
高负压装置对絮条的紧密作用:
斜槽比直槽好;斜槽的方向与纺纱的捻度方向有关;斜槽的宽度与纺纱支数有关;斜槽的宽度与絮条的紧密度有关;负压的作用力与网圈的透气度有关;絮条的密实度与负压的作用力有关,所以随负压的提高能使絮条达到较完美的紧密条件,但能耗也将上升。
1.7紧密纺系统使用过程中应注意的一些问题
(1)所有紧密纺装置的优点都是降低3mm以上的有害毛羽,如果在降低有害毛羽的同时却带来其它常发、偶发性疵点的增加,也是我们不愿看到和不能接受的,所以在使用紧密纺装置降低有害毛羽的同时我们要兼顾其他纱线指标比如:
CV%,CVb%,—50%、50%、140%、200%强力,纱疵等各项质量.
(2)紧密纱由于毛羽少外观整齐光滑在自络捻接时退捻、捻接难度大于环纺纱,紧密纱使用空捻器时退捻及捻接空气压力要稍大于环纺纱,观察捻接质量逐步调整。
现在做紧密纱时也有使用水捻,水捻的一个关键点是捻接时的给水量,给水量小时接头外观和强力甚至不如空捻效果好,给水量大可以优于空捻效果,但增大给水量后由于水雾不能立即蒸发,带来捻腔附近沾花、清洁质量恶化。
总体而言,做紧密纱还是机械搓捻效果好,但是维修成本有点难以接受。
电清及其它方面可以参考环纺纱的设置.
(3)压差问题:
紧密纺技术特点是所纺每根纱都有一个吸风口,吸风口负压一致性和稳定性对凝聚纤维一致性十分关键.早期为保证相距过远造成压差,采取化整为零,采用多单元负压装置来减少压差。
也有通过总风管变截面方式来缩小负压.如按细纱机504锭为例,每侧有252锭,从负压风机吸口至机尾距离十几米,尽管通过工艺设计保证整机负压要求,但从机头至机尾负压差异始终存在,如果使用过程中间数百个风管接头中只要部分出现漏风或异型管凝聚槽及网格圈堵塞等情况,就可能加大锭差。
当然,负压一致性问题技术上通过抽吸嘴直径改变来尽可能趋于一致。
事实上,紧密纺改造最初阶段成纱条干CVb%在同等设备条件下数值比环锭纺波动大,就目前改造的效果看,压差大仍然是一个不容忽视的问题,所以每次平、扫车工作完成后,必须用压力检测表对每一根异型管进行负压值测定。
(4)负压控制:
在紧密纺纱的生产时,不要追求毛羽少之又少,在一定的条件下,多减少一点点毛羽是要付出高额能耗的。
在不影响客户对质量的要求下,应尽量降低消耗,特别是在细支纱生产时。
一般情况下,在做120支纱以上时,负压一般控制在1500Pa左右;做60~80支纱时,负压控制在1700~1800Pa;做40~30支纱时,控制在2000Pa;做21支纱时,控制在2200Pa;做10支纱时,控制在2600Pa。
(5)变频器选择:
如果紧密纺负压风机是采用变频器控制的,则在50hz以下建议你去掉变频器,如果50hz以上建议添加一个压力传感器,把紧密纺负压改为PID衡压控制,既可以很好的控制紧密纺负压,又可以节约能源。
既保证了生产所需又省下了费用.
(6)集聚管选择:
对细支纱采用窄槽集聚管,对粗支纱采用宽槽集聚管,对有横动要求的采用链刀式集聚管,这样能最大限度地节能。
(7)风机选择:
对半紧密纺装置配低速大出口风机;对紧密纺装置配高速小出口风机;对超高压风机配超高速特小出口风机;对特高压风机配多叶轮超高速特小出口风机.
(8)风压控制:
对细支纱可以减小负压,对粗支纱提高负压;对客户要求指标不高的纱,可以减小负压,对客户要求指标特高的纱,可以增加负压;对原料质量差又须达标的纱也可提高负压。
(9)紧密纺装置牵伸区也可以尝试加装压力棒隔距块。
(10)集聚槽倾角:
集聚槽倾角大小对管纱细节、毛羽及断裂强度有明显相关性。
因此在实际生产中应根据纺纱品种及客户要求有选择、兼顾性的优选适宜的集聚槽倾角大小。
(11)细纱工序配置紧密纺装置后在专件、器材允许的情况下可以走高效工艺的路子。
如与环锭纺同样品质的要求时,可适当选用低一等级的配棉,适当降低前纺的落率,降低成本.如果提高紧密纺纱的品质如减少毛羽和棉结,主要还是在梳棉和精梳上下功夫,重点要监控其专件器材的状态和环境,例如管纱测试指标较好,但使用厂家效果不好,主要是梳棉精梳状态不好,对140%以下小棉结没有进行有效梳理和去除.
(12)长车集落改紧密纺方式:
升牵伸系统还是落龙筋相比较而言认为落龙筋比较合理:
升牵伸系统后机台重心较高,运行稳定性差,不利于成纱质量;工作量大,升牵伸系统较落龙筋多约20个工时。
升牵伸系统优点是集落系统不做改动。
如采取落龙筋方式,龙筋按设计尺寸下降后,集落尺寸参数稍作改动即可运行且机台重心低,运行稳定。
2.紧密纺关键器件
2.1钢领与钢丝圈
因为紧密纺纱毛羽少,对钢丝圈的润滑更恶化,磨损更快。
因此,钢领、钢丝圈选型时应从技术方面降低钢丝圈飞行速度、提高钢丝圈运行稳定性来减少钢丝圈磨损,延长钢丝圈使用寿命。
紧密纺钢领、钢丝圈选型时一般原则是:
钢领小直径、宽边型,钢丝圈中高硬度、低弓。
2。
2胶辊
由于紧密纺动程小,胶辊磨砺周期较环纺大幅缩短,一般掌握在50—60天左右。
为避免质量大面积波动,宜把更换时间错开,下机后应使用专用容器摆放整齐,避免长时间挤、压,碰、划.磨砺后不要长时间日光直射,免处理胶辊可以适当过一下紫外线,照射时间灵活掌握.皮圈由于动程小基本上都是采取一次淘汰.三罗拉胶辊组装时应检查传动齿轮状态及润滑情况,保证上机后运行良好.
2。
3摇架
紧密纺通过摇架延伸加压在前胶辊和阻捻胶辊上.如果原有压力不作调整,造成前胶辊实际压力比原来小。
实际生产中如果出现原料及温度湿度波动,或细纱机揩车换新皮辊,可能出现牵伸力增大,使前罗拉处出硬头,造成凝聚纤维区域无法正常向阻捻胶辊处转移,断头增加不可避免。
此外,由于摇架本身力臂延伸前移,使得压力分配不同于环锭纺。
经测定,环锭纺改造机台后,前档实际压力较原来减少约10cN,后档压力约减少30cN。
据了解,紧密纺改造的厂家绝大多数在改造时保留原有摇架,没有考虑改造后对前中后胶辊压力的影响及将会使摇架间差异扩大的问题,因此满足不了紧密纺纱的要求。
为此,有的厂家采取更换摇架圈簧或者增加增压簧片来改善摇架加压。
2.4网格圈
网格圈国产化技术已经比较成熟,材料主要为涤纶和锦纶两种,组织形式主要有平纹和斜纹,斜纹的好于平纹,我们使用的是斜纹的,选择网格圈时主要考虑:
网格圈织造纤维的强力、组织形式、摩擦力、抗电性、透气性及耐磨性,国产网格圈使用周期一般在6—12个月,与纺纱的支数有关。
网格圈能用气清洁的尽量不要水洗.选择目数过低会造成部分纤维的流失,随负压被吸走。
网格圈的清洁直接关系到成纱的毛羽、条干、强力等指标,网格圈的定期清洁保养是非常重要的,网格圈的清洁周期与选用配棉、车间环境、生产品种有直接关系,清洁周期一般以满足成纱指标要求为原则:
一般普梳品种3—5天,精梳品种10—15天。
清洁工具:
压缩空气喷嘴。
网格圈张力架可分为整体式和独立式,作用同样都是为网格圈提供稳定的工作张力.绪森三罗拉紧密纺采用整体式张力杆,清洁时网格圈可以方便的拆下进行集中清洁。
国产四罗拉紧密纺大多采用分体式张力架,网格圈拆装比较麻烦,清洁时可以不拆下网格圈直接用压缩空气吹净.
网格圈规格:
绪森的三罗拉紧密纺114*25mm,国内某四罗拉紧密纺规格是119*10mm.
紧密纺网格圈跑偏现象主要有以下几种原因:
(1)网格圈尺寸不规范,从而造成网格圈两边所受张力不一致,运行中容易一边溜。
(2)前皮辊前冲量不精准,相邻两个罗拉座对皮辊前冲调节位置不一致是网格圈跑偏的一个重要诱因。
(3)弹簧摇架三列胶辊平行度差(即摇架状态),为了片面追求浮游区大小一致而仅仅调节前皮辊的相对位置,从而造成引纱胶辊与网格圈径向不平行而引发网格圈运行状态不良,导致网格圈走偏.
(4)集聚系统安装不良,这种现象一般发生在平、扫车后。
3。
几种常见类型的紧密纺系统
3.1立达卡摩纺
立达卡摩纺优点:
在牵伸上比较完美,前皮辊后移、特种下销张力、弧背型下销、加长上销(上销冲出6mm)、大直径铁芯,使之能满足短纤维与长纤维和混合长度纤维的牵伸要求,同时由于欠伸控制合理,牵伸能力强,又是前区电子牵伸,使之牵伸支数覆盖面大,一般情况下立达卡摩纺的牵伸能覆盖棉型的各种支数,一般讲在10~160S;由于其机构设计特点,卡摩纺可以利用低负压就能产生集聚效果,因此它有可能和“吸棉”共用一个系统,以简化结构,而网圈式紧密纺机构无法用低的负压,必须自成系统;在成纱质量方面要领先其他类型的紧密纺;成纱质量稳定性以及日常的维护、运转成本等方面,都要远好于其他紧密纺系统。
立达的卡摩纺到目前为止,全球安装量已经达到近300万锭,是目前全球主机+紧密纺整机安装量最大的一家。
随着国产化“卡摩纺”价格的平民化,该紧密纺技术将在国内有一个较好的发展前景。
立达卡摩纺缺点:
相比于网格圈式和打孔皮圈式紧密纺,由于采用59MM大直径吸风鼓代替前罗拉,主牵伸区皮圈钳口至前罗拉钳口线之间的距离即浮游区距离增大,不利于对纤维特别是短纤维的控制,使得可纺纤维的最短长度受到限制,主要适纺高支纱;导气辊筒表面的孔隙较大(直径0。
8MM,80孔/cm2),要求加工纤维有一定的刚度,否则在集聚过程中易被吸风从辊筒的孔眼中吸走,所以品种适应性没有格圈式和打孔皮圈式紧密纺广泛;吸风鼓易被纤维、灰尘、棉蜡堵塞且清洁相对较为困难;纺制粗支与特细支时在集聚方面存在不足;价格昂贵,10年来,立达卡摩纺在国内只有约10家纱厂共约30万锭在用,其一直以来全世界最贵紧密纺细纱机,目前仍近2000元/锭的价格使得绝大多数纱厂望而却步,而且立达要求卡摩纺需配套其全流程纺纱设备,从而使得成本进一步增加;不适用于改造,也不能恢复到普通环锭纺状态纺纱;对环境要求较高,不仅要求车间含尘量小,还要求常年温度在28+/-2C,相对湿度38-43%,使用厂家如新疆溢达等大都采用进口瑞士LUWA空调系统。
立达卡摩纺适纺类型:
目前,国内大多数纱厂都用立达卡摩纺纺高支纱,以取得较好的经济效益,而用其纺特低支纱效益不会太好,皮辊等器材消耗太大.
另外,立达的紧密纺能给客户带来以下几个好处:
(1)几乎零额外的紧密纺配件消耗.
(2)几乎没有增加额外的能耗。
(3)紧密纺吸风系统和笛棉吸风系统共用,车间结清.
(4)立达实现了低负压情况下的紧密纺纺纱(负压为网格圈的一半,甚至更低)。
(5)自带的纲领和钢丝圈磨合程序(和布雷克合作)。
(6)电子牵伸的细纱机的品种适应性范围更加广泛。
(7)冷却液冷却系统,电机和空调系统消耗大大的节省。
(8)落纱零卷绕。
(9)全进口的专件配置.
(10)进口的细纱机。
图1RIETERK45卡摩纺
3.2三罗拉式被动传动紧密纺系统
对比四罗拉结构,优点是:
(1)结构简单,安装、使用、维护保养方便,节省保全用工。
(2)对纤维的要求不高,适纺范围广。
(3)对罗拉座的安装间隔精度要求低。
(4)对前罗拉没有特殊要求,改造费用低。
(5)齿轮箱上集聚皮辊与牵伸皮辊的握持距离比四罗拉小,集聚罗拉压力稳定,断头少。
(6)网格圈的传动密封在齿轮箱内,相对四罗拉,对环境(主要指车间飞花,粉尘)要求低,适合老厂改造。
不足:
(1)牵伸与集聚胶辊需要配对磨削,皮辊费用增加。
(2)小风机形式的日常维护太过繁琐,包括风机传动轴的校正、支撑轴承的维护、小龙带的位置调整、风机叶轮的管理、负压吸管的检查和维护等。
3。
3四罗拉式主动传动紧密纺系统
对比三罗拉结构,优点是:
(1)皮辊不需要配对磨削。
(2)集聚区对纤维的实际控制距离加大,更适合纺长度在33-46mm之间的纤维。
不足:
(1)结构复杂,安装、维护困难,相对三罗拉保全用工增加。
(2)要求罗拉座的安装间隔精度高.
(3)老厂改造需更换前罗拉,改造费用增加.
(4)引导罗拉易塞花,敞开式过桥齿轮易磨损,相对三罗拉故障率高。
(5)引导皮辊压力不稳定,断头多。
(6)对车间环境要求高,飞花多会影响开放式齿轮传动的平稳性,所以适纺速度比三罗拉低.
适纺支数:
国产四罗拉紧密纺装置做70支以下纱支比较合适,做细支甚至超细支还是进口设备成纱质量稳定.
国产四罗拉紧密纺装置的常发性故障:
(1)过桥齿轮磨损、龟裂.
(2)负压吸风管内挂花、积花以及负压不匀现象。
(3)改造后机台品种适应性降低,使用高倍牵伸时管纱容易出现8-9cm的周期性不匀,并伴随管纱CVb%增大。
四罗拉紧密纺过桥齿轮使用要点:
(1)目前大多数传动齿轮位于摇架加压中间部位(如1—2工位),此处设计需要再考虑。
在扫车后重新开车前,务必要注意检查粗纱条有无跑偏,如果粗纱进入传动工位,易造成卡齿损坏过桥齿轮。
(2)改造平车要仔细:
要注意罗拉座与罗拉的直角度,罗拉座与罗拉不垂直易造成过桥齿轮非完全啮合,磨损不一致;验车时要检查过桥齿轮轴有无垫纸,因为罗拉座三个齿轮中心为机加工,已考虑啮合中心距,并且安装面与前罗拉中心垂直,在正常的安装情况下,根本无需垫纸。
(3)新改造车验收时,可双手按紧密罗拉两侧轴承部位,若手感发麻震动,则需要检查啮合齿隙是否过紧,在这些锭位,成纱质量也会有影响.
(4)牵伸罗拉与引导罗拉中间的过桥小轮是现在四罗拉紧密纺装置损坏最频繁的机件,有的更换后一个礼拜左右又发生磨损、开裂现象,建议:
牵伸罗拉和引导罗拉能否改为同步带传动,同步带采取粘接形式,日常更换时无需抬下牵伸罗拉且传动平稳。
四罗拉紧密纺装置常见工艺参数设置:
纯粘胶40S,赛络紧密纺粗纱干定量3.18g/10m,捻系数73.5,细纱隔距19*35,后区牵伸倍数1。
14,车头车尾的条干CV锭差相差1。
5个百分点以上,车头较车尾优。
细纱罗拉直径25mm,车头负压在1800左右,车尾负压在2200左右。
四罗拉紧密纺装置机械波问题:
因为四罗拉紧密纺过桥齿轮是开放式的,如果车间环境差、飞花过多过桥齿轮容易塞花.塞花严重的话会影响齿轮及三、四罗拉的传动稳定性,并有可能在管纱条干上形成周期性不匀(机械波),例如如图2所示,机型是FA506改造的国产四罗拉紧密纺,三列罗拉直径25mm,牵伸皮辊29。
7mm,引导皮辊30mm,总牵伸65。
8倍,后区1。
25,直板上销附加压力棒。
图2FA506国产四罗拉紧密纺机械波
由如图2可见:
三列波成倍数关系,像是谐波,最长波等于罗拉直径,先检查一下是否由罗拉引起。
解决机械波,还是排除法比较实用:
(1)三列波成倍数关系,符合谐波的特征,产生在一个部位的可能性大。
(2)三罗拉、皮辊微小的周期性机械振动不至于引起四皮辊的明显压力变化。
3。
4三罗拉式被动传动与四罗拉式主动传动紧密纺系统性能比较分析
3罗拉式紧密纺还会有一定市场,主要原因是4罗拉式在皮辊维护、使用方面比3罗拉式紧密纺具有很多优势,比如3罗拉式牵伸和集聚皮辊不通用且和普通环锭纺皮辊铁芯也不通用,打磨皮辊时需要拆开皮辊盒并同步打磨一对皮辊且要按一定的比例打磨外径保持其传动比不变,而4罗拉式是通过更换带齿前罗拉通过过桥齿轮传动小罗拉在传动紧密纺阻捻皮辊,没有这些繁杂的操作和缺点;还有3罗拉式紧密纺集聚元件由前罗拉—前皮辊-过桥齿轮—阻捻皮辊-网格圈多级摩擦消极传动,集聚元件稳定性易受到摇架加压、前皮辊和集聚皮辊表面状态、网格圈和集聚管、张力架等元件状态的影响,稳定性不如4罗拉式;从皮辊磨砺时的工作量来看三罗拉形式要远远大于四罗拉紧密纺,以一台1008锭长车紧密纺来比较:
三罗拉形式紧密纺在磨砺牵伸、引导胶辊时必须同时拆下,仅504套齿轮盒的拆装、检查1人工作约需多半个工作日,加上磨砺时间、配套组装及齿轮润滑工作所需的时间要大大超过可单独更换和拆卸的四罗拉形式紧密纺。
但是4罗拉式紧密纺系统由于需要更换带齿前罗拉所以需要更高的初期设备投资,且3罗拉式紧密纺吸附毛羽效果更好.
捻度问题:
四罗拉紧密纺有时实测捻度会比设计捻度大,主要原因为:
在做细纱捻度设计时是通过前罗拉和锭子转速的比值来确定捻度大小。
细纱机加装紧密纺装置后增加了集聚网格圈和引纱罗拉和负压组件,四罗拉由于没有集聚牵伸,引纱胶辊、网格圈对引纱罗拉是消极传动,在纺纱过程中网格圈和引纱胶辊对牵伸罗拉会有一定的速度滞后,这种滞后性会造成输出纤维速度会略小于牵伸罗拉的线速度,相当于锭子速度