完整版冲压毕业论文设计.docx
《完整版冲压毕业论文设计.docx》由会员分享,可在线阅读,更多相关《完整版冲压毕业论文设计.docx(29页珍藏版)》请在冰豆网上搜索。
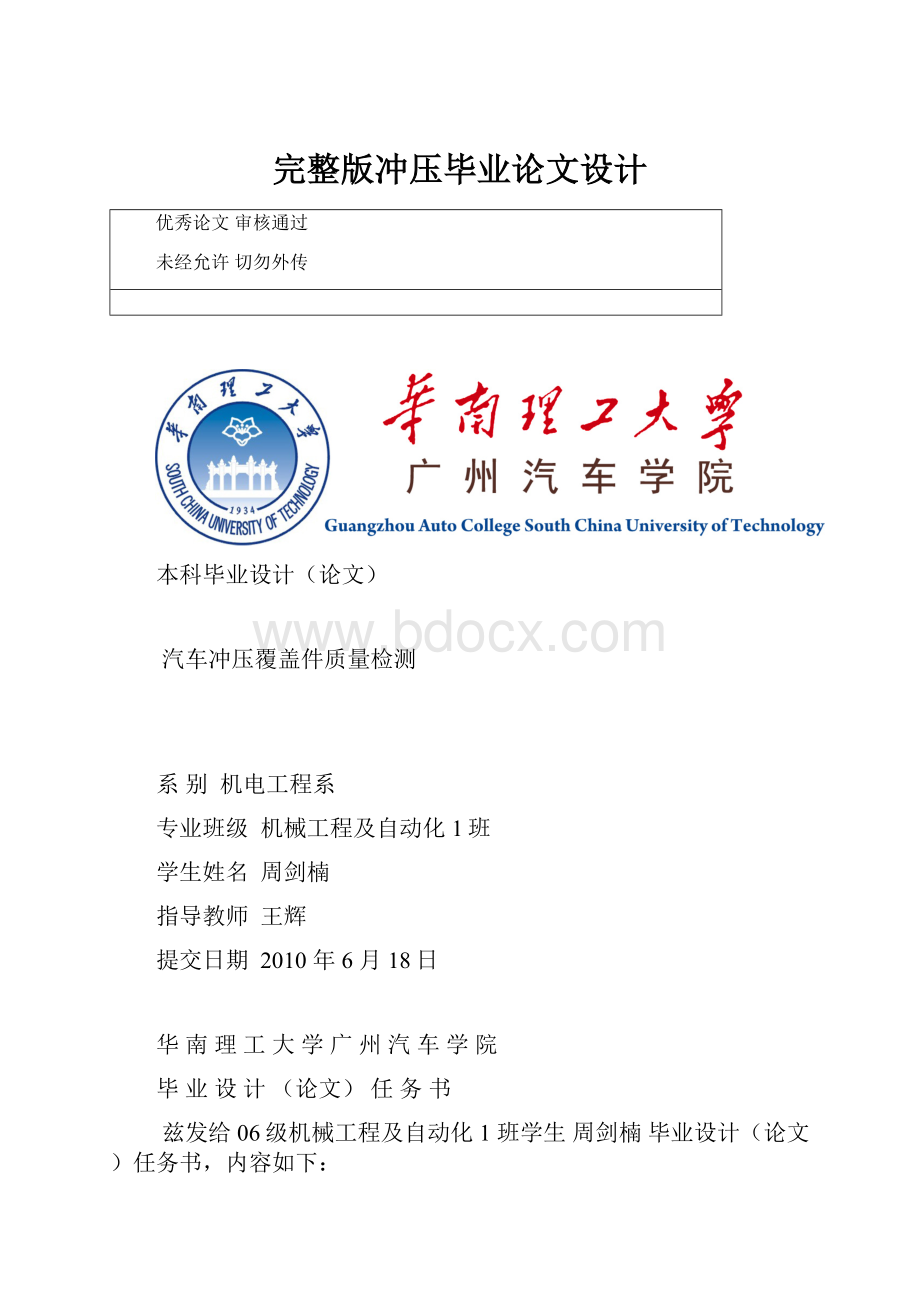
完整版冲压毕业论文设计
优秀论文审核通过
未经允许切勿外传
本科毕业设计(论文)
汽车冲压覆盖件质量检测
系别机电工程系
专业班级机械工程及自动化1班
学生姓名周剑楠
指导教师王辉
提交日期2010年6月18日
华南理工大学广州汽车学院
毕业设计(论文)任务书
兹发给06级机械工程及自动化1班学生周剑楠毕业设计(论文)任务书,内容如下:
1.毕业设计(论文)题目:
汽车冲压覆盖件质量检测
2.应完成的项目:
(1)了解汽车冲压覆盖件工艺过程和工艺过程的质量要求
(2)对常用质量检测技术进行分析,选取合理的检测技术
(3)完成某覆盖件的检测设计,确定质量检测方案
(4)检测设计中,选定质量检测设备
3.参考资料以及说明:
(1)姚贵升,景立媛.汽车用钢应用技术[M].北京:
机械工业出版社,2007
(2)刘贵民,无损检测技术[M].国防工业出版社,2006
(3)吴平川,等.钢板表面缺陷的无损检测技术与应用[J].无损检测2000,22(7)
(4)李申.超声兰姆液探伤研究与应用[J].机械设计与制造,2001,(6)
(5)鲍文华.汽车外覆盖件钢板表面缺陷及改进[J].轻型汽车技术,2004(8)
(6)刘镇清.无损检测中的超声兰姆波[J].无损检测,1999,21(9)
4.本毕业设计(论文)任务书于2010年1月25日发出,应于2010年5月30日前完成,然后提交毕业考试委员会进行答辩。
专业教研组(系)负责人审核年月日
指导教师(导师组)签发年月日
毕业设计(论文)评语:
课题结合自身实际的工作情况,开展了汽车的覆盖件在冲压工艺过程的质量检测方案设计工作。
论文分析了目前开展的人工质量检测的技术能力、不足等,并在此提出上,提出了结合人工检测和仪器表面检测、仪器内部检测为一体的零件冲压工艺过程质量检测的方案。
实现了多层次质量检测,能在较高程度上发现汽车覆盖件坯板和冲压成品的各类质量问题。
论文研究内容具体,结构合理,分析设计较严密。
课题研究工作与实际工作结合的较为密切,能够对实际工作有较好的参考价值。
论文已达到本科毕业论文水平。
毕业设计(论文)总评成绩:
毕业设计(论文)答辩小组负责人签字:
年月日
摘要
汽车覆盖件是质量要求最严格的汽车冲压件,鉴于此其质量检测应得到人们高度重视。
但纵观现代汽车业的发展状况,因汽车覆盖件质量问题而产生的经济损失较为严重。
本文意在通过对汽车覆盖件的加工工艺及质量要求的分析研究,及对汽车覆盖件工艺过程的常用质量检测技术的比较,并结合个人的社会实践经验,从而得出发动机盖工艺过程的质量检测方案。
该方案包括人工表面检测,表面无损探伤和内部无损探伤。
关键词:
冲压,覆盖件,质量检测方案
Abstract
ThecoverpartofAutomobileisoneoftheautomotivestampingparts,andthequalityrequirementofwhichisverystrick.So,weshouldpaytoitsqualityinspection.Butthroughoutthedevelopmentofthemodernautomobileindustry,seriouseconomiclossesarearisingbecauseofthequalityproblemsofthecoverpartofautomotive.Thisarticleisintendedtoanalyzetheprocessingtechnologyandqualityrequirementsofthecoverpartofautomobile,compairsthecommonqualitytestingtechnologyoftheautomobilecoverpart’scraftprocessing,andcombinesthesocialexperienceofindividuals,arrivesatthequalitytestingprogramofenginecovercraftprocessing.Theprogramcontainsthefalsesurfacetesting,thesurfacenon-destructivetestingandtheinsidenon-destructivetesting.
KeyWords:
stamping,Automobilecover,qualitytestingprogram
摘要Ⅰ
AbstractⅡ
第一章绪论1
1.1课题研究背景1
1.2国内外发展现象1
1.3课题研究目标和课题意义2
第二章汽车覆盖件的加工工艺及质量要求4
2.1汽车覆盖件的工艺过程概述4
2.2汽车覆盖件工艺过程的质量要求4
2.2.1表面质量要求4
2.2.2内部质量要求6
2.3本章小结7
第三章汽车覆盖件工艺过程的常用质量检测技术8
3.1人工检测8
3.2常用的无损探伤技术9
3.2.1线阵CCD扫描检测技术9
3.2.2超声兰姆波检测11
3.2.3超声纵波喷水检测技术13
3.2.4漏磁检测技术14
3.3工业常用检测技术的对比分析与总结15
3.4本章小结16
第四章汽车发动机盖的工艺过程及质量检测17
4.1工艺过程的概述17
4.2工艺过程的质量要求17
4.2.1落料线上的表面质量要求17
4.2.2冲压线上的内部和表面质量要求17
4.3工艺过程检测要求18
4.3.1落料线的表面检测要求18
4.3.2冲压线的内部检测要求和表面检测要求18
4.4工艺过程质量检测的方案设计18
4.4.1落料线的检测方案18
4.4.2冲压线的检测方案20
4.5本章小结22
结束语23
参考文献24
致谢25
第一章绪论
1.1课题研究的背景
汽车的覆盖件都是质量要求最严格的汽车冲压件,这类零件不允许冲压后进行较大的修整,而且在表面喷涂后不能出现任何缺陷和不足。
实际生产中,每年都有大量不良冲压覆盖件流到后工序,导致机械产品总体质量水平下降和严重的经济损失。
覆盖件坯板常常由于卷材在吊运、海运、陆运时的碰撞、摩擦和淋雨,仓储时受潮,落料时灰尘污染,落料线清洗机清洗油不纯等原因,导致坯板表面出现了夹杂、麻点、锈斑、压痕、压印等缺陷,这些缺陷影响了坯板外观和成形性能,更重要的是降低了抗腐蚀性、抗磨性、疲劳极限等使用性能;而由于不能及时发现坯板存在的缺陷,造成冲压产品的报废,浪费材料增加了成本且生产效率也受到较大影响。
因此,对冲压件坯板在落料线上检测己就变得至关重要了。
在实际生产过程中,对于坯板表面的检测,本人所在单位落料线采用目视观察和油石打磨。
实践证明,由于检测精度和检测速度等方面的限制,目前这些检测方法很难胜任冲压件坯板的在线检测。
众所周知,金属薄板的生产工艺决定了其内部最易存在的缺陷类型为平行于材料表面的分层性缺陷。
由于分层严重影响板材的强度,冲压成品焊接时若板材受到垂直于表面的拉应力,分层会在焊接过程中被撕裂。
目前,本人所在单位冲压线的检测方法也是目视检测和油石打磨,粗糙的检测带来的结果是在实际生产中常常出现因分层而报废的现象,所以必须在冲压线上对冲压前的坯板进行内部探伤。
随着无损探伤技术的深入发展,超声兰姆波检测、超声喷水检测、线阵CCD扫描检测、漏磁检测、涡流检测等技术变得越来越成熟。
本文旨在通过开展对落料线上坯板质量检测和冲压线上冲压件质量检测的研究,作出合理的检测方案,实现对汽车冲压覆盖件质量管理,提高冲压覆盖件的质量和生产效率。
1.2国内外发展现状
无损探伤技术在汽车用薄板上的应用是近十年国内外工业界的一个热点,其发展也是日新月异。
在日本,超声探伤装置已广泛使用(表1.1)。
1999年,日本NKK首次将“Delta—Eye”系统引入到福山厂2号连续热浸镀锌生产线上,用于改善汽车外板用镀锌板的质量。
2002年,日本NKK公司成功采用带钢表面裂纹自动检测装置。
检测装置采用了一种两极分化光源和三个摄像仪,可识别钢带表面的反射光,记录图像数据,进而识别这种反射光。
该装置可100%地检测出钢带表面的细小裂纹,并自动标记。
2000年,CEA(法国原子能委员会)在国际无损探伤技术交流活动中,展示了新开发的“SPARTACUS”系统,其主要特征是通过工作台利用超声波的收集扫描分析资料,可连续350Kos的高速大规模处理数据,而且排除了汽车用薄板材料微粒发出的噪声,大大提高了信号与噪声的比例,能进行各种深度下的无损探伤。
在国内工业界,无损探伤技术在薄板上的应用也逐渐受到人们的重视。
1999年宝钢成立了表面检测项目组,先后开发出了带钢表面质量在线检测系统、高速带钢多功能检测系统和针孔检测系统。
宝钢带钢表面质量在线检测系统对高速运行的带钢实施非接触实时在线表面缺陷检测并进行智能分类,是国内第一套自主研发并投入生产使用的冷轧带钢表面检测系统。
宝钢高速带钢多功能在线检测系统是宝钢自主开发的适用于轧机出口高温、高湿、污染、震动等恶劣生产环境的视觉检测系统。
该系统在速度高达1800mmin的生产线上,对直径大于1mm的孔洞,开口深度大于2mm的边裂的检测精度达到100%,同时对带钢表面常见缺陷在线检出率达到99%,缺陷分类准确率达到80%以上。
宝钢针孔检测系统主要用于检测冷轧薄板表面的微小缺陷,系统对直径大于等于15μm的针孔的检出率达到99%以上,边缘盲区小于等于1mm。
序号
厂名
型式
探速
·min
处理能力
块·
投产时间年
制造厂
处理钢板尺寸mm
1
名古屋
脉冲反射
60
25000
2001
三菱电机
0.6~6×550~2500×c
2
福山
脉冲反射
60
20000
2001
帝国通信
0.6~6×550~2000×c
3
加古川
脉冲反射
50
12000
2002
东京计器
0.6~6×550~2200×c
4
君津
脉冲反射
55~60
30300
2005
三菱电机
0.6~6×480~2500×c
5
鹿岛
脉冲反射
60
34000
2006
三菱电机
0.5~6×500~2500×c
无损探伤技术在汽车用薄板上的应用越来越广泛,但还有许多汽车制造企业还没有利用这一先进的技术。
本人所在单位里,汽车冲压覆盖件的质量检测技术不够完善,因此来探索和研究本课题。
1.3课题研究目标和课题意义
近两年单位分别出现了汽车覆盖件落料线不良2.01%和2.10%、冲压线3.04%和
2.96%、装配线3.20%和3.16%,从以上不良数据可以看出,不良率到下一工序有增加的现象。
对覆盖件钢板的常见缺陷作出分析,发现检测技术的不完善是造成不良率上升现象的原因。
本文对人工检测的检测范围作详细分析,并对常用工业无损检测技术的原理、发展、特点、应用范围等进行对比分析,找出最合理最能满足质量要求的检测技术,实现多层次质量检测的方法,能够在较高程度上发现汽车覆盖件坯板和冲压成品的各类质量问题。
同时,设计出发动机盖工艺过程的质量检测方案,提高发动机盖检测的准确性和全面性。
第二章汽车覆盖件的加工工艺及质量要求
2.1汽车覆盖件的工艺过程概述
汽车覆盖件的加工过程大致如下:
卷材——落料——堆垛——运输——(冲压线)仓储——清洗——冲压成型。
在落料过程中,由起重机将卷料放上卷料备料台,然后装载到上料小车上,上料小车运行到开卷机,上料小车回位后,完成卷料与整线的对中,穿带结束后,料带经过四辊式送料机组进行料头剪切,进入清洗机进行料带的清洗;经过清洗后的料带进入校平机组;被校平后的板料进入地坑,形成一个缓冲带(补偿环),以补偿卷材在开卷校平部分连续运行和进入落料切断冲模时的间歇动作的速度差。
在地坑的一侧,装有光电反射器,当卷材下落到地坑时,反射器给出信号使驱动开卷装置的电机停止工作,卷材进给中断;经过几次落料切断后,地坑中的卷材逐步上升到一定程度,光电反射器发出信号,使驱动开卷装置的电动机起动,恢复卷材进给,开卷校平;从地坑上来的板料进入落料压力机进给的装置;落料压机落料及堆垛。
在冲压成形过程中,钢板的成型都是借助模具对薄板施加外力所引起的结果。
一定力的作用方式和大小,都对应着一定的变形。
不论采用什么样的成形方式,冲压成形件所要求的几何形状,都是通过钢板在冲压成形过程中的塑性变形来完成的。
根据冲压成形过程中钢板变形区的应力、应变的不同,可将零件变形划分为拉伸、压缩、弯曲、扭转等多种成形方式。
2.2汽车覆盖件工艺过程的质量要求
由于不能及时发现坯板表面存在的缺陷,造成冲压产品的报废,浪费材料增加了成本且生产效率也受到较大影响,所以落料线上的质量检测是最重要的,必须对坯板进行表面检测。
分层缺陷是薄板最危险的缺陷,生产现场必须对坯板进行内部探伤。
经过检测合格的坯板进行冲压成型,因表面缺陷引起不良而报废时有发生。
因此,对冲压成品的检测我们也需要进行表面的探伤。
2.2.1表面质量要求
覆盖件坯板的表面质量要求与冲压成品表面要求相似,坯板需要无划伤、无麻点、无压印、无压痕、无锈斑、无夹杂等;冲压成品需要无划伤、表面光洁、无压痕、无夹杂、无锈斑、无麻点等。
(1)划伤
划伤是最常见的表面缺陷(图2.1)。
划痕起着缺口的作用,变形时引起应力集中,因而导致零件冲压开裂,划痕越深,缺口作用越明显;划痕越长,缺口作用的区域就越大,即使是微细的划痕,也可能成为零件冲压开裂并迅速向金属内部渗透裂纹的起始点,同时又有可能成为零件疲劳断裂的潜伏
因素。
实践证明,零件冲压成形时,如果钢板表面存在着划痕,并处于零件变形部位,包括拉延和弯曲变形的部位时,势必沿着划痕开裂。
划痕有多长,零件就有多长,甚至沿着划痕处向表面无划痕处扩展。
划痕越深,零件的裂口就越大,实为零件冲压开裂的一个原因。
(2)表面脏污
覆盖件冲压成品表面的光洁度是指覆盖件冲压成品表面受污染的程度(图2.2),表面的残留物会降低外耐腐蚀性同时会给表面磷化带来影响,进而影响车身漆膜的附着力。
(3)麻点图2.3麻点缺陷的表面OM低倍形貌
“麻点”(图2.3)的产生是由于钢和
杂质的塑性不同,在冲压或通过夹送辊时杂质被轧入钢板表面的细小颗粒,结果钢板表面呈现满布的“麻点”。
“麻点”以独特的形状并具有促使污垢聚集的作用,使钢板表面质量恶化,对于要求具有良好表面质量的汽车覆盖件是很不利的。
图2.4压痕
(4)压痕
覆盖件表面压痕(图2.4)是运输时碰撞造成的缺陷,压痕的出现大大影响了覆盖件的外观,对于外观要求严格的覆盖件,这是不允许的。
(5)压印
由于辊面受损或有异物黏结导致在钢板上周期性地出现压印(图2.5),其形状,大小基本相同。
其周期(L)与辊子直径(D)的关系为:
L=μπD(μ为延伸系数)。
压印也是严重影响覆盖件外观的因素之一,必须杜绝其出现。
(6)锈斑
仓储时湿度大、卷材包装损坏、长期在库等都是钢板生锈的原因。
锈斑(图2.6)会降低覆盖件表面喷涂时油漆的附着力或者磷化处理的质量。
同时,钢板表面的锈斑增大了焊接时的电阻,容易引起焊点烧穿或焊接不牢,直接影响焊接质量。
2.2.2内部质量要求
金属薄板的内部缺陷主要是分层(图2.7),薄板中的分层由于板材中的缩孔残余、开口气泡和夹杂物等在轧制过程中被轧扁而形成。
当薄板受到垂直于表面的拉应力时,分层会严重影响薄板的强度,如图2.8所示。
若焊接坡口处有分层存在,它会促使焊缝产生缺陷。
如果焊接应力与分层的平面垂直,即使分层并不在坡口处开口,也会在焊接过程中被撕裂。
因此,覆盖件坯板要求无分层缺陷。
图2.7分层图2.8金属薄板中分层缺陷
2.3本章小结
本章介绍了覆盖件加工过程,大致如下:
卷材——落料——堆垛——运输——(冲压线)仓储——清洗——冲压成型。
并对覆盖件的质量要求作出分析,确定了最终的质量要求。
第三章汽车覆盖件工艺过程的常用质量检测技术
3.1人工检测
人工检测,即利用肉眼观察,油石打磨观察。
这种人工检测方法的检测范围如表3.1所示。
检测对象
检测范围
不良缺陷图片
卷材
撞伤、锈斑
图3.1、图3.2
落料线上的坯板
划伤、麻点、压印、压痕、锈斑等
图2.12.32.42.52.6
冲压线上的坯板
外周撞伤、锈斑
图3.3、图3.4
冲压成品
划伤、麻点、压印、压痕、锈斑、表面脏污
图2.1~图2.6
图3.3坯板撞伤图3.4坯板锈斑
表3.1中,对落料线上坯板的检测虽能检测出常见表面缺陷,但人工检测具有以下突出的弊端,即抽检率低,不能100%反映坯板表面质量;实时性差,远不能满足在线高速的生产节奏。
此外,人工检测不能发现坯板的分层缺陷。
这样,我们必须想出更好的方法去完善质量管理工作。
3.2常用的无损探伤技术
从检测技术的观点看,无损探伤有如下一些特点:
(1)检测对象形式多样,从连铸板坯到各种型号的冷、热轧带钢和各种机械零
件,因此检测机理具有多样性。
(2)表面缺陷的种类随着加工工序的延仲呈现逐渐增加的趋势,而且不同缺陷
类别之间的光学、几何和电磁等特性参数各异,增加了检测的难度。
(3)针对大量微细的缺陷,要求检测系统的分辨力和灵敏度高,高速的生产节
奏决定了检测系统的高实时性的特点。
因此,对检测坯板的表面缺陷和内部缺陷的无损检测技术提出了很高的要求。
下面介绍几种常用的无损探伤技术:
它们能进行坯板表面和内部的在线检测,与人工检测相比有了较大的提高。
3.2.1线阵CCD扫描检测技术
(1)线阵CCD扫描检测原理
固体摄像器件CCD检测原理(如图3.5)是用特殊光源以一定方向照射到钢板表面上,CCD摄像机在带钢上扫描成像,扫描所得的图像信号经过图像采集卡输入计算机,通过图像预处理、二值化、确定检测区域等处理方法后得到钢板表面缺陷的二值图像,提取二值图像中的几何特征参数,然后再进行图像识别,判断出是否存在缺陷。
图3.5线阵CCD扫描检测系统原理图
(2)视觉检测技术的发展
随着本世纪60年代激光技术、CCD技术的相继问世和计算机技术的飞速发展,机器视觉技术应运而生,并迅速在工业无损检测领域推广普及,有效拓展了无损检测技术的应用范围。
机器视觉技术应用于钢板表面缺陷在线检测的机理是绝大多数表面缺陷的光学特性之间存在着明显差异。
70年代中期日本川崎公司开始研制镀锡板在线检测装置,先后采用了斜交激光扫描系统和平行激光扫描系统进行钢板表面缺陷检测,并针对特定缺陷(如周期性缺陷)的信号处理问题采用了自相关技术和Fractal分析方法。
1988年美国Sick光电了公司研制成功平行激光扫描检测装置,检测原理如图3.6所示,低功率He-Ne激光器发出的激光经过反射镜投射到一个高精度的多面体棱镜表面,通过多面体棱镜的旋转运动产生垂直于带钢运动方向的横向扫描。
光线经多面体棱镜反射后通过远心光路系统投射到带钢表面,带钢表面反射和散射的光线被光接收装置接收并由光电倍增器完成光电转换后,传输至后级计算机系统,完成图象信号处理和缺陷识别任务。
Sick系统可检出40多种表面缺陷。
图3.6Sick激光扫描检测原理
1.激光或白色光源2.旋转棱镜3.抛物面镜4.扫描光线出射窗
5.带钢6.光接收棒7.光电倍增管
在美国能源部的资助下,Honeywell公司于1983年开发出采用线阵CCD器件的连铸板坯表面在线检测装置。
通过增加CCD芯片的有效象元数和提高其帧转移速率,并采用先进的数字图象处理部件,该装置能可靠地检出针孔等微细的表面缺陷。
1986年,Westinghouse公司和EastmanKodak公司在美国钢铁陇会(AISI)的资助下,分别研制出各自的带钢表面缺陷在线检测系统,其中Westinghouse系统在最高带速和最大带宽下可提供0.7mm×2.3mm的纵、横向缺陷分辨力。
此外,为满足轧制带钢表面在线检测中高速数据处理的需求,意大利和美国的多家公司都相继研制出专用的计算机处理系统。
90年代以来,进一步完善和提高机器视觉检测系统的自动化功能(缺陷自动分类等)及实用化水平己成为研究热点,其中前者的应用研究最多。
视觉检测技术经过几十年的发展,技术正逐步成熟,功能不断完善。
(3)线阵CCD扫描检测的特点及检测范围
线阵CCD扫描检测系统通常由LED光源,明暗域结合成像光学系统、高速高分辨率线阵CCD器件、FPGA嵌入式处理系统和缺陷自动分类子系统等组成。
系统能对钢板表面的麻点、夹杂、压印、划伤和压痕等常见缺陷进行无损检测,并基于Bayes决策理论,实现缺陷的自动分类功能。
这类系统在实验室检测指标一般为:
宽度最大为1800mm,运行速度不大于1.5ms,振动幅度小于1mm,横纵向检测分辨率为0.8mm×0.8mm,尺寸检测误差不大于1mm。
(4)线阵CCD扫描检测技术总结
线阵CCD扫描检测是一项世界先进的表面检测无损检测技术,经过几十年的发展,技术成熟。
能检测出麻点、夹杂、压印、压痕和划伤等常见表面缺陷,横纵向检测分辨率达到0.8mm×0.8mm,尺寸检测误差不大于1mm。
可以说,线阵CCD扫描检测是一种全面、准确、高效的表面检测技术。
3.2.2超声兰姆波检测
(1)超声兰姆波检测原理
兰姆波又称板波,是超声纵波倾斜入射到薄板中引起共振而形成的波。
如图3.7所示,可推导出
(1)
式中α——透声材料中纵波的入射角图3.7兰姆波波型的产生与换能器入射角度关系
——透声材料中纵波的波速
——薄板中兰姆波的相速度
兰姆波分为对称型(S型)和非对称型(A型)两种(图3.8)。
其产生和传播的速度是与检测对象的介质性质、波的频率f及薄板的厚度d的乘积f·d相关的。
其相关的波动方程如下
S模态
(2)
A模态(3)
(
式中为薄板中横波的波速。
从公式
(1)~(3)可以看出,在入射角不变或f·d不变的情况下,其适用的范围和产生的兰姆波的模式是不同的,其相速度与f·d以及入射角度与f·d的关系如图3.9和3.10所示,因此需要通过试
验来选取最佳的检测模式。
薄板的检测主要采用脉冲反射法,使用一
个探头兼作发射和接收探头。
换能器(探头)发出的超声波在板中激发的板波在传播过程中遇到缺陷或端面而产生反射波,被传感器接收后在示波屏上显示出缺陷波和底波的位置和幅度。
(2)超声兰姆波探伤发展概况
兰姆波的发现是在1917年,英国力学家H·Lamb按平板自由