我国弹药装药装配技术现状及发展对策.docx
《我国弹药装药装配技术现状及发展对策.docx》由会员分享,可在线阅读,更多相关《我国弹药装药装配技术现状及发展对策.docx(5页珍藏版)》请在冰豆网上搜索。
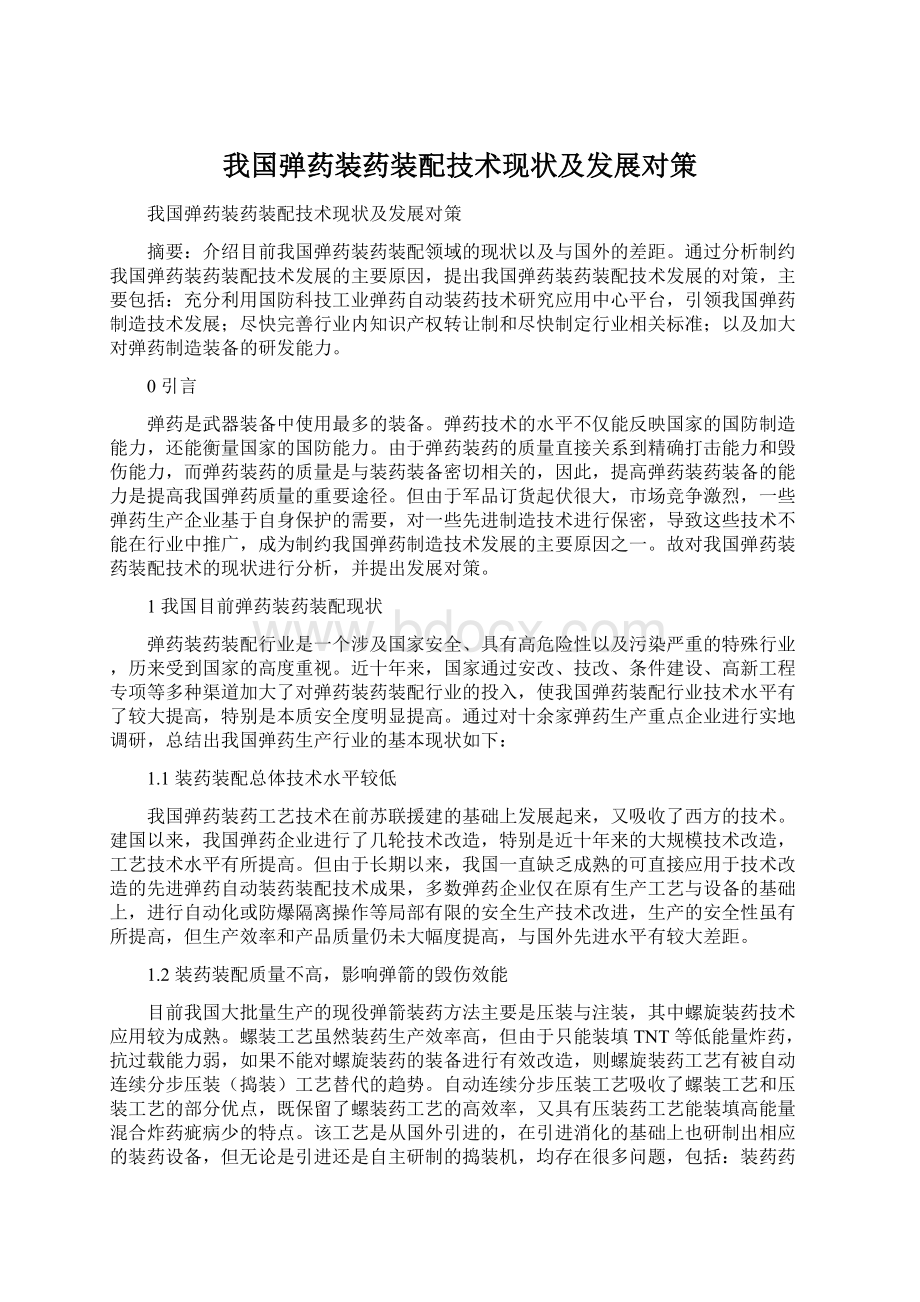
我国弹药装药装配技术现状及发展对策
我国弹药装药装配技术现状及发展对策
摘要:
介绍目前我国弹药装药装配领域的现状以及与国外的差距。
通过分析制约我国弹药装药装配技术发展的主要原因,提出我国弹药装药装配技术发展的对策,主要包括:
充分利用国防科技工业弹药自动装药技术研究应用中心平台,引领我国弹药制造技术发展;尽快完善行业内知识产权转让制和尽快制定行业相关标准;以及加大对弹药制造装备的研发能力。
0引言
弹药是武器装备中使用最多的装备。
弹药技术的水平不仅能反映国家的国防制造能力,还能衡量国家的国防能力。
由于弹药装药的质量直接关系到精确打击能力和毁伤能力,而弹药装药的质量是与装药装备密切相关的,因此,提高弹药装药装备的能力是提高我国弹药质量的重要途径。
但由于军品订货起伏很大,市场竞争激烈,一些弹药生产企业基于自身保护的需要,对一些先进制造技术进行保密,导致这些技术不能在行业中推广,成为制约我国弹药制造技术发展的主要原因之一。
故对我国弹药装药装配技术的现状进行分析,并提出发展对策。
1我国目前弹药装药装配现状
弹药装药装配行业是一个涉及国家安全、具有高危险性以及污染严重的特殊行业,历来受到国家的高度重视。
近十年来,国家通过安改、技改、条件建设、高新工程专项等多种渠道加大了对弹药装药装配行业的投入,使我国弹药装配行业技术水平有了较大提高,特别是本质安全度明显提高。
通过对十余家弹药生产重点企业进行实地调研,总结出我国弹药生产行业的基本现状如下:
1.1装药装配总体技术水平较低
我国弹药装药工艺技术在前苏联援建的基础上发展起来,又吸收了西方的技术。
建国以来,我国弹药企业进行了几轮技术改造,特别是近十年来的大规模技术改造,工艺技术水平有所提高。
但由于长期以来,我国一直缺乏成熟的可直接应用于技术改造的先进弹药自动装药装配技术成果,多数弹药企业仅在原有生产工艺与设备的基础上,进行自动化或防爆隔离操作等局部有限的安全生产技术改进,生产的安全性虽有所提高,但生产效率和产品质量仍未大幅度提高,与国外先进水平有较大差距。
1.2装药装配质量不高,影响弹箭的毁伤效能
目前我国大批量生产的现役弹箭装药方法主要是压装与注装,其中螺旋装药技术应用较为成熟。
螺装工艺虽然装药生产效率高,但由于只能装填TNT等低能量炸药,抗过载能力弱,如果不能对螺旋装药的装备进行有效改造,则螺旋装药工艺有被自动连续分步压装(捣装)工艺替代的趋势。
自动连续分步压装工艺吸收了螺装工艺和压装工艺的部分优点,既保留了螺装药工艺的高效率,又具有压装药工艺能装填高能量混合炸药疵病少的特点。
该工艺是从国外引进的,在引进消化的基础上也研制出相应的装药设备,但无论是引进还是自主研制的捣装机,均存在很多问题,包括:
装药药面高度不能精确控制;补药与上下弹人工操作,粉尘污染较重;气动逻辑控制系统不可靠;可压药剂品种与弹种还需扩展等,离大范围推广使用还有一定的差距。
由于我国自制的压药设备是民用普通压机加防爆改装而成的,与国外先进的专用精密数控压装药设备相比,还存在许多问题,包括:
不能精密双向自动压药;在压制成型过程中,药柱的温度、比压、保压时间、药柱高度不能精确控制;推拉模、称装药、模具转换、模具清擦等辅助工序均为手工作业等。
注装药技术基本上是通过引进发展起来的,但对引进技术尚未完成消化吸收,近十年,国内自行改建和新建十余条注装生产线,在安全、环保、劳动条件自动化程度和装药质量方面均有较大提高,但在混药均匀性和装药疵病方面仍存在问题。
北京理工大学的低比压顺序凝固技术是一种注装药中冷却的新工艺,具有药柱疵病少、药柱密度较均匀等优点,尽管已在个别企业应用,但其冷却工艺较复杂,产品质量一致性等有待提高。
在热塑装药工艺方面,我国从上世纪60年代中期开始自主开发,70年代初定型推广应用,并不断改进提高。
由于采用了真空熔混、真空振动浇注、加压凝固养护和程序控制冷却等新技术,有效降低了装药疵病,提高了装药密度,使塑装药工艺可广泛应用于大口径、大当量的海空各类导弹、航弹及水中兵器等新型弹药。
但由于TNT凝固收缩补充有限,故时有超标疵病产生,塑化设备和装药工艺有待进一步提高。
1.3弹药装配效率低,不能满足突发性弹药消耗量大的需求
目前,我国枪弹和中小口径炮弹的弹药装配技术水平仍与国外有一定差距。
我国枪弹装药装配生产仍然沿用从原苏联引进的技术,采用各工位自动专机技术的成批生产方式。
而美国则采用多头快速转子技术的连续生产方式,其枪弹生产效率和发射药装药质量高得多(美国为1200发/min,而我国仅为100发/min)。
我国小口径炮弹装药装配生产大多采用手动或半自动专机由人工参与完成,生产效率低、生产线上待制品与人员多而混杂、安全隐患严重。
全自动装药装配技术尚未完全突破,生产节拍现只能达到每分不超过10发。
与美国G&W公司设计的20、25、30、35mm弹药装药装配转子自动线每分生产600发的先进水平相比,相差很远。
1.4弹药生产线在线无损检测技术不能满足快速生产要求
大、中口径弹药的检测重点是药柱密度与装药疵病,目前国内大多采用批抽样离线切割检测的方法。
抽样合格,一批就合格,否则一批都报废。
虽然引进了工业CT等无损检测设备,但由于检测精度受弹体壁厚差影响大,检测速度慢,仍需离线抽样检测。
小口径弹弹药的检测重点是弹药装配质量,如弹药产品的同轴度、底火的装入深度、弹头与弹壳间的结合度等。
目前,国内只有少数生产线采用在线光电无损自动检测,但检测效率较低,成为提高生产节拍的主要障碍。
枪弹生产的高速在线无损检测技术的研究刚刚起步,离工程化应用还有距离。
1.5药重与弹重自动计量技术自动化水平低
弹箭的药剂重与弹重、火工品的药剂重主要靠人工用天平来称量,称量效率低,无法保证称量精度与安全。
枪弹发射药采用计量板定容法自动计量,而枪弹弹头和全弹重采用机械旋转天平进行自动称量分类。
计量、分类精度低,稳定性差,效率较低。
1.6弹药自动包装技术落后
无论是炮弹还是枪弹与火工品的弹药成品,均采用人工方式进行包装。
包装是弹药生产线中人员最多最密集、弹药制品存量最大的危险点。
另外,我国弹药包装未形成完善的标准体系,导致各弹药厂的包装方式、结构、尺寸、装弹数量、重量不统一,包装标志混乱,通用化程度低。
2制约我国弹药制造技术发展原因分析
通过长期不断的技术攻关,我国弹药制造技术取得了显著的成绩,特别是近十年来,在上级有关部门的大力支持下,一些先进的制造技术得到应用,正在逐步缩小与国外发达国家的差距。
但由于别人也在进步,缩小与国外发达国家差距的进程比较缓慢,其原因主要包括:
2.1缺乏总体发展目标,技术推进缓慢
据了解,我国近十年来,均没有制定弹药制造技术的发展总体目标,每当制定五年计划时,基本上都是企业根据自身产品的需求提出项目,仅靠企业自身的技术力量或寻找一家合作伙伴进行实施,难以聚集整个行业专家的力量,不仅项目推进缓慢,而且实施效果也很难达到预期目标,更谈不上具有带动整个行业的作用。
2.2企业间相互封锁意识严重,制约行业技术发展
弹药装药装配技术大同小异,在一些关键环节得到突破,就可以使技术大进一步。
企业出于自身的利益,不可能公开这些关键技术。
因此,对某种产品,企业之间采用的技术并不相同,有的已经是比较先进的技术,但有的还是比较原始的制造模式。
目前,如何转让这些技术还缺乏行之有效的办法,这种封锁意识制约了整个行业的技术进步。
2.3相关标准不适应技术发展,制约先进技术发展
近年来,在上级部门的支持下,不少企业通过技改或安改,在装药装配技术方面取得了进步,特别是在枪弹和中小口径炮弹的装配方面取得了历史性的突破,使长期依靠手工或部分专机的装配方式转变为自动装配方式。
不仅使弹药的质量得到了提高,而且完全实现了人机隔离,提高了生产的安全性。
尽管这些技术已在企业得到应用,但要在整个行业进行推广还有一些难度,主要问题是成本高,而产生成本高的主要原因是目前我国没有这种自动装配线的相关安全标准,在安全评估时,都是参照原手工装配的相关标准。
在生产线中,有的元件本身既不会产生静电也不会引起爆炸,但就是要求采用防爆产品,使部分元件价格增加几倍甚至十几倍,从而造成整体成本的增加,直接影响到推广应用。
2.4难以更改定型工艺,制约先进技术的应用
目前,我国弹药装药装配工艺已经定型多年,凡是定型工艺均不能随意更改。
由于这些工艺绝大多数都是针对原手工生产方式而制定的,随着技术的发展以及将手工装配方式改为自动方式,往往需要对原有工艺进行变更,而这种工艺变更手续非常复杂。
再加上工艺变更后生产的产品必须经过多种试验,需要一定的经费支持。
因此,不少企业在现有手段能满足需求的情况下,不愿意采用新的技术,也制约了弹药行业的技术进步。
3我国弹药制造技术发展思路探讨
为尽快提升我国弹药制造水平,在分析制约我国弹药制造技术发展原因的基础上,对弹药制造技术的发展提出以下建议:
3.1充分利用工程中心平台,引领我国弹药制造技术发展
2008年,原国防科工委正式挂牌成立的“国防科技工业弹药自动装药技术研究应用中心”(简称“工程中心”)标志着弹药技术的发展已引起国家的高度重视。
该工程中心成立后,立即组织了对重点弹药企业的调研,通过分析目前我国弹药制造企业的现状以及与国外发达国家的差距,根据国家对弹药的需求,编制出了近十年来我国第一个关于弹药行业的发展规划。
该规划得到了有关部门的认同和高度评价。
但这仅仅是迈出了第1步,下面的工作还任重道远。
如何通过工程中心来引领我国弹药制造技术的进步,这不仅是对工程中心的考验,也需要决策部门在管理上进行创新。
1)以“十二五”规划为发展目标
由于工程中心“十二五”规划站在整个行业角度提出,故上级部门在项目安排上应考虑符合发展规划中所涉及的研究内容,在弹药行业技改或安改等方面的安排上也应尽可能将是否符合发展规划作为条件之一,这样,才能确保该发展规划的实施。
2)充分发挥行业专家的作用
工程中心成立了由行业专家组成的中心专家委员会,他们对行业的现状以及急待解决的问题了如指掌。
故上级在安排弹药制造方面的项目时,应尽可能由工程中心专家委员会评审决定,以免造成以前“广撒网”的方式:
只解决相对容易的技术,而制约我国弹药制造技术发展的关键技术却长期得不到解决。
同时,对项目实施中出现的问题,由工程中心召开专家委员会专门攻关,对项目进度实行监控。
3.2尽快完善行业内知识产权转让制
目前,通过上级单位的支持,有不少企业在弹药制造技术方面取得了成绩,许多技术都可在行业中推广。
但由于市场企业间的竞争关系,企业不愿公开其技术(某些国防基础科研项目所取得知识产权并非企业独有),更不用说技术转让。
其根本原因是没有在行业内部制定如何保护知识产权的相关制度,通过技术转让,使企业不仅能保住自己的饭碗,还能产生良好的经济效益。
因此,尽快制定这方面的制度也是推动行业技术进步的一个重要的手段。
3.3尽快制定行业相关标准
目前,很多弹药制造方面的标准都不能适应当前技术的发展。
在没有对应标准的情况下,就只能套用相关标准,因此,2个差异较大的生产方式可能会套用同一个标准。
如前所述,弹药自动装配生产线的安全标准就套用原手工装配的相关标准,为了满足相关标准的要求,不得不耗费不必要的人力和财力。
因此,为了适应高新技术在弹药制造技术领域的应用,制定相关标准已经迫在眉睫。
4加大对弹药制造装备的研发能力
弹药装药所采用的工艺基本类似,但某些产品,我国的毁伤威力就是比国外的低,其主要原因是我国的装药装备与国外差别较大,典型的例子就是螺旋装药这种使用较普遍的装药工艺,国外对螺装机进行改造,使改造后的螺装机能装高能炸药,弹药的毁伤威力立即提高30%以上。
由此可见装药装备的重要性。
另一方面,弹药制造装备的水平如何,也直接关系到弹药制造自动化的实现。
4.1加大对称装药装备的研发能力
在手工装配中,采用天平人工称重的称装药方式,而在自动装配中,自动