钢件表面发蓝发黑处理.docx
《钢件表面发蓝发黑处理.docx》由会员分享,可在线阅读,更多相关《钢件表面发蓝发黑处理.docx(8页珍藏版)》请在冰豆网上搜索。
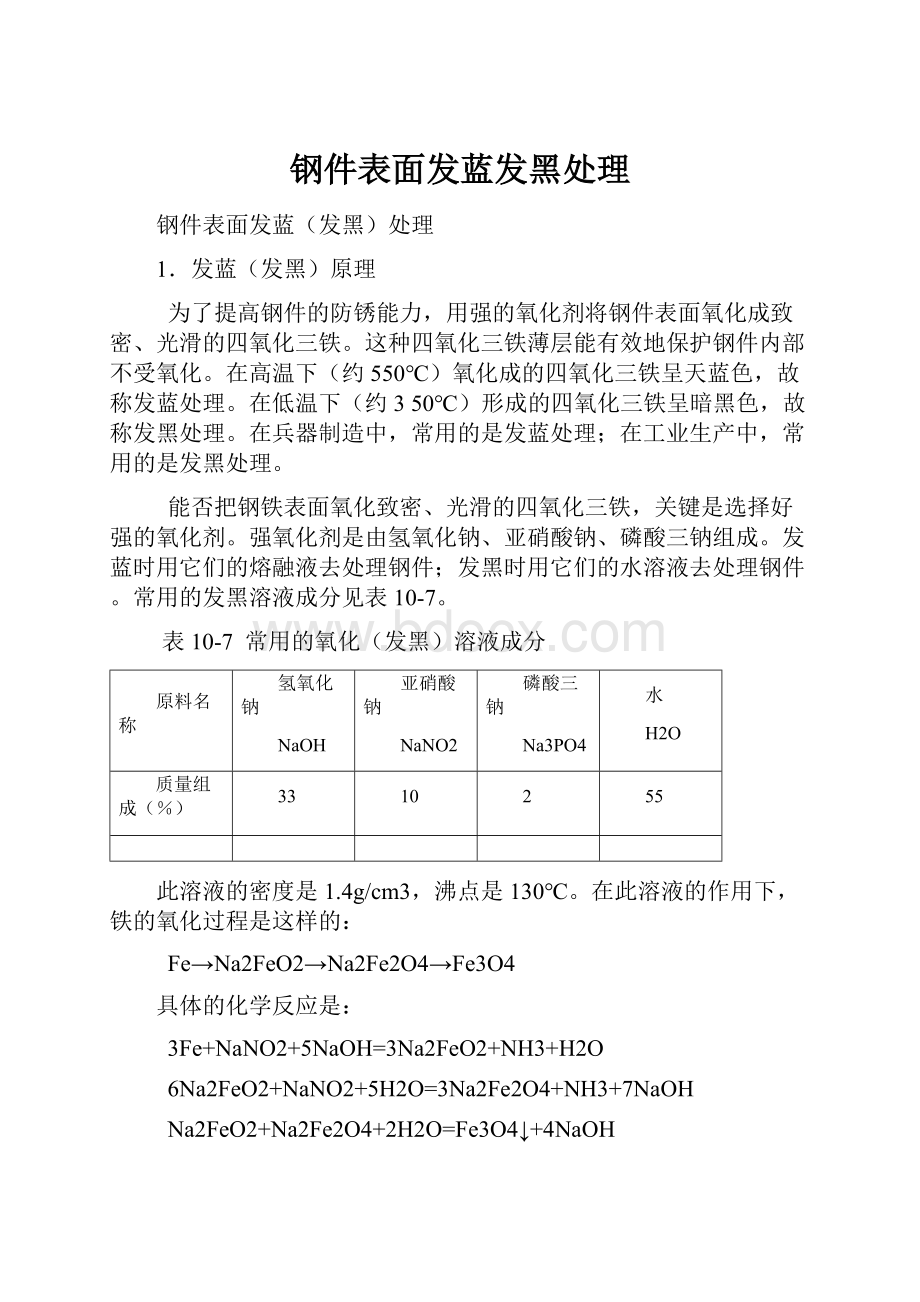
钢件表面发蓝发黑处理
钢件表面发蓝(发黑)处理
1.发蓝(发黑)原理
为了提高钢件的防锈能力,用强的氧化剂将钢件表面氧化成致密、光滑的四氧化三铁。
这种四氧化三铁薄层能有效地保护钢件内部不受氧化。
在高温下(约550℃)氧化成的四氧化三铁呈天蓝色,故称发蓝处理。
在低温下(约350℃)形成的四氧化三铁呈暗黑色,故称发黑处理。
在兵器制造中,常用的是发蓝处理;在工业生产中,常用的是发黑处理。
能否把钢铁表面氧化致密、光滑的四氧化三铁,关键是选择好强的氧化剂。
强氧化剂是由氢氧化钠、亚硝酸钠、磷酸三钠组成。
发蓝时用它们的熔融液去处理钢件;发黑时用它们的水溶液去处理钢件。
常用的发黑溶液成分见表10-7。
表10-7常用的氧化(发黑)溶液成分
原料名称
氢氧化钠
NaOH
亚硝酸钠
NaNO2
磷酸三钠
Na3PO4
水
H2O
质量组成(%)
33
10
2
55
此溶液的密度是1.4g/cm3,沸点是130℃。
在此溶液的作用下,铁的氧化过程是这样的:
Fe→Na2FeO2→Na2Fe2O4→Fe3O4
具体的化学反应是:
3Fe+NaNO2+5NaOH=3Na2FeO2+NH3+H2O
6Na2FeO2+NaNO2+5H2O=3Na2Fe2O4+NH3+7NaOH
Na2FeO2+Na2Fe2O4+2H2O=Fe3O4↓+4NaOH
生产实践经验证明,要获得光亮、致密的四氧化三铁膜层,氧化溶液中亚硝酸钠与氢氧化钠的比例,要保持在1:
3~3.5之间。
2.发蓝(发黑)操作
发蓝(发黑)的操作流程:
工件装夹→去油→清洗→酸洗→清洗→氧化→清洗→皂化→热水煮洗→检查。
(1)工件装夹要根据工件的形状、大小,设计专门的夹具或吊具。
目的是使工件之间留有足够的间隙,工件间不能相互接触,要使每个工件都能完全浸入氧化液中被氧化。
(2)去油目的是除去工件表面的油污。
经过机加工后(发蓝、发黑是最后一道工序),工件表面难免不留下油污,用防锈油作工序间防锈的更是这样。
任何油污,都会严重影响四氧化三铁的生成,所以必须在发蓝、发黑之前除去。
常用的除油溶液配方,见表10-8。
表10-8常用的除油溶液配方
原料名称
碳酸钠
Na2CO3
氢氧化钠
NaOH
磷酸三钠
Na3PO4
水玻璃
Na3SiO3
水
H2O
质量组成(%)
7
3
3
2
85
将除油溶液加热至80~90℃,然后将工件浸入,浸入时间为30min左右,若油污较多,还得延长除油时间,以除油彻底为准。
(3)酸洗酸洗的目的是除去工件表面的锈迹。
因为锈迹、锈斑会阻碍生成致密的四氧化三铁层。
即使工件无锈迹,也应进行酸洗,因为它使油污进一步去除干净,而且酸洗会提高工件表面分子的活化能,有利于下一工序的氧化,能生成较厚的四氧化三铁层。
酸洗溶液一般是10~15%浓度的硫酸溶液,温度是70~80℃,将工件浸入硫酸溶液中,浸入时间为30min左右,锈蚀较轻的钢件可浸20min,锈蚀严重者,则需要浸40min以上。
(4)氧化氧化是发蓝、发黑的主要工序。
四氧化三铁膜层是否致密、是否光滑、是否有足够的厚度,取决于氧化阶段。
发蓝的工艺温度是550℃。
发黑的工艺温度是130~145℃。
浸入时间是50~80min。
含碳量高的高碳钢,氧化速度较快,浸入时间可短些。
含碳量低的低碳钢,氧化速度慢,浸入时间需要长些。
合金钢特别是高合金钢,工件表面有一定的残余奥氏体,对碱溶液有较强的抗抵作用,不易生成Fe3O4,因而浸入时间需更长一些。
表10-9列出了有关钢种氧化(发黑)时溶液的温度及浸入时间。
表10-9不同钢件氧化温度与时间
钢种
入槽温度(℃)
出槽温度(℃)
处理时间(min)
高碳钢
120~125
125~130
40
低、中碳钢
125~130
130~135
50
铬硅钢
125~130
130~140
60
高合金钢
130~135
135~145
70
高速钢
135~140
140~150
80
槽液的正常颜色是白色。
如果槽液呈红色或棕色,表示亚硝钠浓度过大,应及时调整槽液的成分。
如果溶液呈绿色,则表示铁离子浓度过大,应及时更新溶液。
(5)皂化所谓皂化,是用肥皂水溶液在一定温度下浸泡工件。
目的是形成一层硬脂酸铁薄膜,以提高工件的抗腐蚀能力。
常用的皂化液浓度是30~50g(肥皂)/L。
把皂化液加热至80~100℃,将氧化后的工件放入皂化液浸泡10min左右。
(6)检查
氧化完毕后,要对工件进行检查,看Fe3O4膜层是否合格。
检查的方法是:
任意抽取三件工件,置于浓度为2%的硫酸铜溶液中浸泡20s,不退黑色者为合格。
三件工件中有一件以上不合格,则整槽工件视为不合格,需再氧化一次,以加深四氧化三铁的厚度。
3.可能出现的缺陷及解决措施
钢件发黑工艺,在操作过程中,可能会出现如下一些缺陷。
(1)氧化膜疏松氧化膜应很致密,与基本结合很牢固。
如果生成的氧化膜疏松,容易擦掉,这是不正常的现象。
出现这种情况,主要是由于新配制的氧化溶液缺少铁离子引起的。
解决办法,是加入一些旧的氧化溶液,或者加入一些干净的钢屑,煮沸30min,以增加氧化溶液的铁离子浓度,这现象就会消除。
(2)工件表面呈红褐色锈斑氧化膜应呈深黑色,光亮且平滑。
如果工件表面出现红褐色斑点或连成一片,这主要是由于氧化溶液中氢氧化钠过浓、生成氧化铁过多所致。
解决办法是调整溶液成分,补充加入一些亚硝酸钠和水,以降低NaOH浓度。
(3)工件表面呈淡灰色工件表面失去乌黑光泽,呈淡灰色,这是由于氧化溶液中氢氧化钠浓度过低引起的。
解决办法,补充加入适量的氢氢化钠。
(4)不生成氧化膜经处理40~50min后,工件表面仍不上色(生成氧化膜),这主要是由于溶液温度过低,亚硝酸钠浓度不足引起的。
解决办法是提高溶液温度,适当增加亚硝酸钠量。
(5)氧化膜表面发花工件在黑色基体上出现零星的白点,有时白点还较密集,这种现象工人称之为“发花”。
发花原因主要是氧化时间不够引起的。
解决办法,是延长氧化时间(即浸泡时间),还可以补充加入少量氢氧化钠。
(6)工件表面呈绿色如果工件表面的氧化膜不是乌黑色,而是绿色,这是工件过氧化的结果,是由于氧化溶液温度过高、亚硝酸钠浓度过高引起的。
解决办法是加入适量冷水(注意:
加水时必须穿戴好老保护具,缓缓加入,以免槽液飞溅,造成灼伤事故)和加入少量氢氧化钠,以降低溶液温度及亚硝酸钠的浓度。
4.氧化溶液成分的测定
从以上氧化膜缺陷分析中可知,当氧化溶液成分出现波动时,就会造成氧化膜的缺陷,至使发黑操作失败。
氧化溶液成分,主要指氢氧化钠浓度和亚硝酸钠浓度。
在发黑过程中,水分不断被蒸发,亚硝酸钠和氢氧化钠又非等比消耗,所以,此消彼长,浓度变化是必然的。
操作时间越长,变化就越大。
为了不使氧化溶液的成分出现大的波动,应该每隔2~3h,就取样测定它们的浓度,以便及时计算并补充添加有关原料。
下面介绍氢氧化钠、亚硝酸钠浓度的测定方法。
(1)氢氧化钠浓度的测定吸取氧化溶液10ml,置于量瓶中,加蒸馏水至500ml,摇匀,这便是稀释液。
吸取稀释液5ml置于锥瓶中,加蒸馏水100ml,加酚酞1~2滴,溶液变为红色。
用0.1N的盐酸标准溶液进行滴定,滴至红色消失,记下盐酸消耗量V1(ml)。
再加甲基橙2滴,溶液变为黄色。
继续用0.1N的盐酸进行滴定,滴至黄色转变为红色为止,记下盐酸的消耗量V2(ml)。
按下式计算氢氧化钠的浓度(g/l):
或按下式计算氢氧化钠的百分浓度:
(%)
(2)亚硝酸钠浓度的测定吸取氧化溶液10ml,置于量瓶中,加蒸馏水至500ml刻度处,摇匀,这便是稀释的氧化溶液。
吸取0.1N的标准高锰酸钾溶液10ml,置于锥形瓶中,加蒸馏水100ml,硫酸10ml,加热至50℃左右。
这时溶液呈红色。
用稀释的氧化溶液进行滴定,至红色消失为止,记下稀释氧化溶液的消耗量V(ml)。
按下式计算亚硝酸钠的浓度(g/l):
(g/l)
或按下式计算亚硝酸钠的百分浓度:
(%)
式中V—滴定时用去的稀释氧化液的ml数;14—10ml氧化溶液的质量。
5.除油溶液成分的测定
除油与氧化有着密切关系,除油不彻底,很难获得高质量的四氧化三铁层膜。
所以,除油溶液也要经常测定其成分,以便及时补充天加有关原料,以保证除油效果。
(1)氢氧化钠的测定吸取除油溶液5ml置于锥形瓶中,加蒸馏水100ml,摇均匀。
加酚酞指示剂2~3滴,用0.1N的盐酸标准溶液进行滴定,滴至红色消失为终点,记录盐酸消耗量V1(ml)。
在此溶液中加入甲基橙指示剂2滴,溶液变为黄色。
用0.1N盐酸标准溶液进行滴定,至黄色变为粉红色为终点,记录盐酸消耗量V2(ml)(不包括V1量)。
在两次滴定后,将溶液煮沸5~10min,待冷到常温后,加酚酞指示剂2~3滴,用0.1N氢氧化钠标准溶液进行滴定,滴至玫瑰红色为终点,记录氢氧化钠消耗量V3(ml)。
按下式计算氢氧化钠的浓度(g/l):
(g/l)
或按下式计算氢氧化钠的百分浓度:
(%)
式中V1—第一次滴定时用去的盐酸ml数;
V2—第二次滴定时用去的盐酸ml数;
NA—滴定用盐酸的标准当量浓度,在这里是0.1;
0.040—是NaOH分子里与1000的比值(40÷1000=0.040);
5—吸取的除油液ml数;
1000——1L的ml数;
1100——1L除油溶液的质量。
(2)碳酸钠的测定按下式计算碳酸钠的浓度(g/l):
(g/l):
或按下式计算碳酸钠的浓度:
(%)
式中
V2—第二次滴定时用去的盐酸ml数;
NA—滴定用盐酸的标准当量浓度,在这里是0.1;
V3——第三次滴定用的氢氧化钠的ml数;
Nb——滴定用的氢氧化钠的标准当量浓度,这里是0.1;
0.106—是碳酸钠分子量与1000的比值(106/1000=0.106)。
(3)磷酸三钠的测定
按下式计算磷酸三钠的浓度(g/l):
(g/l)
或按下式计算磷酸三钠的百分浓度:
(%)
式中0.380—是磷酸三钠及十二个结晶水的分子量与1000的比值(380/1000=0.380)。
(4)水玻璃(硅酸钠)的测定吸取除油溶液20ml置于烧怀中,加1%浓度的盐酸20ml,摇匀后,加热蒸发至干,待冷却后,再加1%浓度的盐酸10ml,加蒸馏水100ml,加热使盐类溶解,用滤纸过滤,并用1%盐酸洗涤烧怀和沉淀物7~8次,将沉淀和滤纸移于已知重量的瓷坩锅中,在950~1000℃的高温电阻电炉中灼烧10~20min,出炉后置于干燥器中冷却,然后称量,获得沉淀物的质量(g)。
按下式计算水玻璃的浓度(g/l):
(g/l)
或按下式计算水玻璃的百分浓度:
(%)
式中:
G—灼烧后沉淀物的质量(g)
V—吸收的除油溶液ml数;
2.03—Na2SiO2的分子量与SiO2分子量的比值;
1000—1L的ml数;
1100—1L的除油溶液的质量。