内齿轮铣齿机的铣削动力头设计.docx
《内齿轮铣齿机的铣削动力头设计.docx》由会员分享,可在线阅读,更多相关《内齿轮铣齿机的铣削动力头设计.docx(52页珍藏版)》请在冰豆网上搜索。
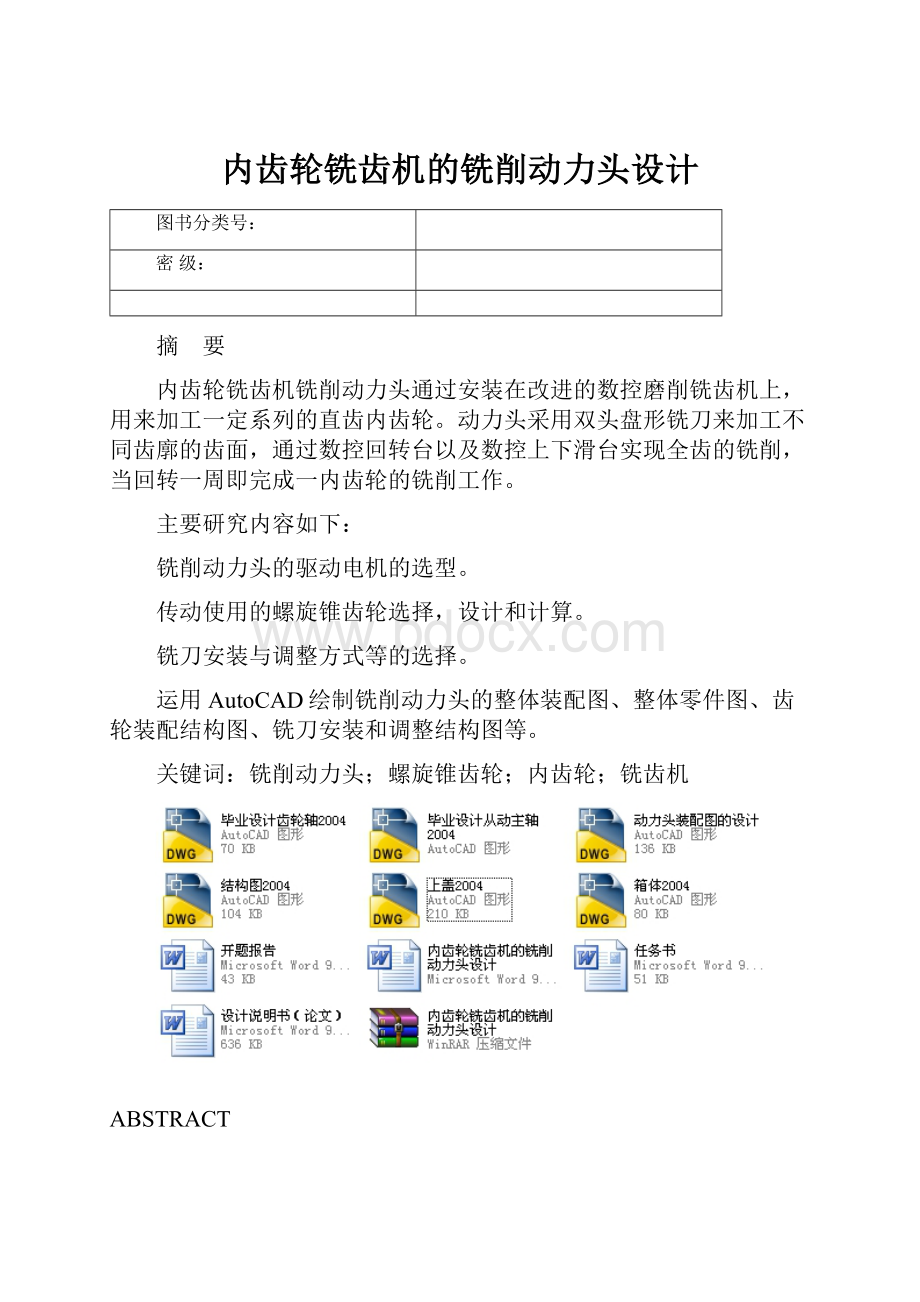
内齿轮铣齿机的铣削动力头设计
图书分类号:
密级:
摘 要
内齿轮铣齿机铣削动力头通过安装在改进的数控磨削铣齿机上,用来加工一定系列的直齿内齿轮。
动力头采用双头盘形铣刀来加工不同齿廓的齿面,通过数控回转台以及数控上下滑台实现全齿的铣削,当回转一周即完成一内齿轮的铣削工作。
主要研究内容如下:
铣削动力头的驱动电机的选型。
传动使用的螺旋锥齿轮选择,设计和计算。
铣刀安装与调整方式等的选择。
运用AutoCAD绘制铣削动力头的整体装配图、整体零件图、齿轮装配结构图、铣刀安装和调整结构图等。
关键词:
铣削动力头;螺旋锥齿轮;内齿轮;铣齿机
ABSTRACT
Innergearcuttermillingpowerheadthroughinstallsontheimprovementnumericalcontrolmillingmachinebed,usingforcertainseriesthestraighttoothannulargear.Thepowerheadusesthedoubleheadeddisccuttertoprocessthedifferenttoothprofilethetoothface,theslidingtablerealizestheentiretoothmillingthroughaboutthenumericalcontrolrotaryabutmentaswellasthenumericalcontrol,whenrotatesaweeknamelytocompleteanmillingannulargear.
Mainresearchcontentasfollows:
ChoosingforMillingpowerheadactuationelectricalmachinery
Thetransmissionusespiralbevelgearchooses,designandcomputation.
Themillingcutterinstallsthewayandsoonthechoice.
UsingAutoCADplanmillingpowerheadoverallassemblydrawing,overalldetaildrawing,gearassemblystructuredrawing,millingcutterinstallmentandadjustmentstructuredrawingandsoon
Thistopicdevelopmentinnergearcuttermillingpowerheadthroughinstallsontheimprovementnumericalcontrolmillingmachinebed,usesforcertainseriesthestraighttoothannulargear.Thepowerheadusesthedoubleheadeddisccuttertoprocessthedifferenttoothprofilethetoothface,theslidingtablerealizestheentiretoothmillingthroughaboutthenumericalcontrolrotaryabutmentaswellasthenumericalcontrol,whenrotatesaweeknamelytocompleteanmillingannulargear.
KEYWORDS:
Millingpowerheadspiralbevelgearannulargearnumericalcontrolmillingmachinebed
1绪论
1.1计算机辅助设计概述
计算机辅助设计(computeraideddesign,CAD)是一种用计算机硬、软件系统辅助人们对产品或工程进行设计的方法与技术,包括设计,绘图、工程分析与文档制作等设计活动,它是一种新的设计方法,也是一门多学科综合应用的新技术。
从技术角度看,CAD技术把产品的物理模型转化为存储在计算机中的数字化模型,从而为后续的工艺,制造,管理等环节提供了共享的信息源。
现在CAD技术已不仅仅用于自动绘图或三维建模,而已成为一种广义的、综合性的关于设计的新技术,它涉及以下基础技术∶
(1)图形处理技术。
如二维交互图形技术、三维几何造型技术及其他图形输入输出技术
(2)工程分析技术。
如有有限元分析、优化设计方法、物理特性计算(如面积、体积、惯性矩等计算)、模拟仿真以各行各业中的工程分析等。
(3)数据管理与数据交换技术。
如产品数据管理(PDM)、数据库、异构系统间的数据交换和接口等。
(4)文档处理技术。
如文档制作、编辑及文字处理等。
(5)界面开发技术。
如图形用户界面、网络用户界面、多通道多媒体智能用户界面等。
(6)基于Web的网络应用和开发技术。
任何设计都表现为一种过程,每个过程都由一系列设计活动组成。
活动间既有串行的设计活动,也有并行的设计活动,目前设计中的大多数活动都可以用CAD技术来实现,但也有一些活动目前尚很难用CAD技术来实现,如设计的需求分析、设计的可行性研究等。
将设计的过程中能用CAD技术实现的活动集合在一起就构成了CAD过程,图
(1)说明了设计过程与CAD过程的关系。
随着CAD技术的发展,设计过程中越来越多的活动都能用CAD工具加以实现,因此,CAD技术的覆盖面将越来越宽,以至整个设计过程就是CAD过程。
图1设计过程与CAD过程的关系
在过去50多年中,CAD技术经历了五个主要发展时期∶
(1)世纪50年代。
美国麻省理工学院(MIT)于1950年在它研制的名为“旋风”的计算机上采用了阴极射线管(CRT)做成的图形终端,并能被动地显示图形。
(2)20世纪60年代。
这是交互式计算机图形学发展的最重要时期。
1962年美国学者IvanSutherland研究出了名为Sketchpad的系统,这是一个交互式图形系统,能在屏幕上进行图形设计与修改,开始出现CAD术语。
(3)20世纪70年代。
计算机交互图形技术和三维几何造型技术(线框、曲面和实体模型)为CAD技术的发展奠定了基础。
总的说,70年代是CAD单元技术的发展和应用阶段,个功能模块渐趋完善,但数据结构尚不统一,应用主要集中在计算机绘图和有限元分析方面,集成性差。
(4)20世纪80年代。
随着超级微型机和32位字长的工程工作站迅速占领市场,各CAD厂商将原来在大型机和小型机上的CAD/CAM系统纷纷向新的硬件平台移植或重新开发。
这一阶段的应用特点是∶从二维绘图发展为三维建模,实现了CAD/CAE/CAM的集成,应用取得了显著效益
(5)20世纪90年代。
随着世界市场的多变与激烈竞争,随着各种先进设计理论和先进制造模式的发展,随着高档微机、操作系统和编程软件的发展,随着因特网的迅速发展,CAD技术正在经历着前所未有的发展机遇与挑战,正向集成化、网络化、智能化和标准化方向发展。
1.2计算机辅助设计的现状及发展趋势
CAD技术推动了几乎一切领域的设计革命,对加速工程建设和缩短产品开发周期、提高产品质量、降低成本、增强企业的市场竞争能力与创新能力发挥着重要作用。
CAD技术已成为衡量国家科技与工业现代化的重要标志之一,成为企业信息化的重要技术基础。
分析CAD技术的发展趋势,主要表现在四个方面∶
1.集成化
在一个由多种软件组成的复杂系统中,例如计算机集成制造(CIMS)、并行工程(CE)等,集成的含义有多种,一般有功能集成、信息集成过程集成及动态联盟中企业的集成此处所说的集成是指信息集成。
由于设计是产品开发的首要环节,因此,CAD信息处于产品生命周期中信息链的源头。
为了提高系统的集成水平,CAD技术必须在以下几个方面提高水平∶
(1)数字化产品建模。
必须提供针对产品全生命周期的统一的产品模型,该模型应该符合某种标准或者规范,其内容应该包括产品结构形状、设计过程以及设计所用的知识;在建模技术上,应该能提供性能优良的特征建模、参数化设计、变量化设计等方法。
(2)产品数据交换。
除了提供按目前已有的交换规范或者标准所开发中性交换文件及其接口(如DXF,IGES,STEP文件)外,还需要发展新的交换思想和规范(如VRML,XML文件等)。
(3)产品数据管理。
应继续改进与提高PDM软件性能,有效管理与产品相关的所有数据以及与产品相关的所有过程。
(4)继续改进与开发各种CAx(CAD,CAE,CAPP…)以及DFx(DFA,DFM,DFT…)并使它们有机地集成起来。
2.网络化
因特网及Web技术的发展,迅速将设计工作推向网络协同的模式,因此,CAD技术必须在以下几个方面提高水平∶
能够提供基于因特网的完善的协同设计环境。
提供网上多种CAD应用服务,例如设计任务规划,设计冲突检测与消
解、网上虚拟装配等工具。
3.智能化
现有的CAD技术在机械设计中只能处理数值型的工作,包括计算,分析与绘图。
然而在设计活动中存在另一类符号推理型工作,包括方案构思与拟定、最佳方案选择、结构设计、评价、决策以及参数选择等。
这些工作赖于一定的知识模型,采用符号推理方法才能获得圆满解决。
因此将人工智能技术,特别是专家系统技术,与传统CAD技术结合起来,形成智能化CAD系统是机械CAD发展的必然趋势。
以下几个问题应该给予更多的注意∶
(1)发展新的设计理论与方法。
例如并行设计的理论,概念设计的理论,创新设计的理论等。
(2)继续深入研究机械设计型专家系统的一些基本理论与技术问题。
例如设计知识模型的表示与建模、知识获取、工具系统的技术等。
4.标准化
随着CAD技术的发展,工业标准化问题越来越显出它的重要性。
迄今已制定了不少标准,随着技术进步,新标准还会出现,基于这些标准推出的有关软件是一批宝贵的资源,用户的应用开发常常离不开它。
1.3铣齿机简介
铣齿机可使用于重型机器制造、造船、矿业、石油和冶金工业中,用来少量或成批加工大模数的螺旋锥齿轮。
其主要参数如下:
加工锥齿轮最大直径<1600mm
加工锥齿轮的平均法向模数8~22
加工锥齿轮最大外齿高(大端)60mm
加工锥齿轮最大齿面宽250mm
加工锥齿轮的齿数范围10~50
加工锥齿轮的节锥角5~80°
切齿最大传动比10∶1
最大双曲线位移±260mm
1.3.1 转盘螺旋锥齿轮切削方法
转盘螺旋锥齿轮切削方法的选择取决于齿型参数、生产特点、对接触区的质量要求等因素。
a) 粗切 通过三面或双面刀盘在一个切削行程内完成,采用双面刀盘同时切出大小齿槽的两侧齿面。
b) 精切 按照精切大小齿轮同时加工的数目和铣齿机重新调整的次数分为普通双面法、旋转单面法、普通单面法、双重双面法。
综合各种具体因素,选择普通双面法进行加工。
所谓普通双面法就是在加工大齿轮时一次调整同时加工齿的凸面和凹面,而加工小齿轮时对齿的凸面和凹面采用不同的调整状态单独完成切削过程。
由于切削大齿轮同时加工齿的凹凸面,显著提高了劳动效率,适用于批量生产,但所用刀盘刀具错刀量必须保证获得应有齿厚。
1.3.2 转盘螺旋锥齿轮加工用刀盘
a) 粗切刀盘 用于粗切的刀盘通常有双面刀盘和三面刀盘。
双面刀盘具有外刀和内刀。
三面刀盘有外刀、内刀和中刀。
双面刀盘主要用于滚切法粗切节锥角50°以内的齿轮;三面刀盘则是用切入法粗切节锥角大于50°的齿轮。
采用切入法粗切大齿轮,应该使用3面刀盘,带外、中、内3种刀具,由于不具备条件,只好改为双面刀盘,其结果可导致生产效率下降。
b) 精切刀盘 精切刀盘通常有双面和单面刀盘。
前者具有外刀、内刀2种刀具型式,可同时加工齿的凹、凸面,用于切制大轮。
单面精切刀盘用于精切小轮,它只有内刀或外刀,用于切齿的凸面或凹面。
1.3.3 调整计算
a) 计算过程建立在厂家提供的公式之上并根据计算原理对其进行了校核。
b) 了解计算过程、方法,对调整数据进行手算。
c) 准确编制5A284苏联铣齿机调整计算程序。
d) 利用计算程序,对示范齿轮进行计算,结果完全符合资料所给出的结果(包括中间、最后结果)。
计算程序编制准确。
e) 计算时需确认系数Fe和Fh。
Fe为接触区长度系数,Fh为接触区高度系数,选取如表1。
鉴于Fe,Fh的选取对计算结果影响较大,程序对Fe,Fh每隔0.01取值,同时监测几个主要的数据,如假想冠轮齿数,径向调整数值,刀具形成直径,工作台横向移动,准双曲线移动。
通过计算发现在Fe=0.58,Fh=0.87时,最为符合要求。
表1 Fe和Fh的选取
加工精度等级齿长系数Fe齿高系数Fh
4~50.65~0.800.75~0.90
6~70.60~0.750.75~0.90
7~90.50~0.700.70~0.85
10~120.45~0.650.60~0.80
1.3.4 试制
a) 进刀 先将根锥角加到尺寸,安装距留余量,粗切后逐渐将安装距加到尺寸。
b) 刀高 考虑铣齿机结构的特殊性,兼顾刀具的重磨,从刀尖到铣齿机刀具心轴的距离h发生变化。
理论上要求h=0,但采用测高量具测量h=19mm,对相关数据进行了调整,保证根锥角及安装距离增加到尺寸后所切齿深准确。
c) 铣齿机前后 铣齿机排削出口处规定在铣齿机后面,其对面为铣齿机前面。
在工作物架底板装有调整铣齿机是工作物架横向移动的机构。
移向摇台前,工件与刀盘间距缩小,所切齿深增大,相反则减少。
d) 垂直轮位 粗切时垂直轮位应处于零位,否则所切齿形有误。
1.3.5 转盘锥齿轮副接触区的修正
锥齿轮副接触区的大小、形状、位置对转盘的平稳转动、使用寿命和噪声有直接影响。
齿面接触区是衡量转盘锥齿轮质量的重要标志之一。
采用以大轮为基准,小轮精铣各面后分别在锥齿轮检查机上检查齿面接触区,然后,再上铣齿机根据实际情况修正小轮。
1.3.6 刀具的刃磨
刀具有2种刃磨方式,湿磨时,将苏制磨齿胎具稍加改进后使之可在M7130型平面磨床上使用,所磨刀具锋利,耐用。
一次装夹可磨6把刀具,效率高。
干磨时,可重新设计干磨胎具,一次可磨1把,效率低,但符合已有工艺习惯,所磨刀具质量较好,可满足生产需要。
1.3.7检验标准
齿轮加工铣齿机主要采用国家标准、行业标准,个别产品尚有企业标准。
国家标准均等效目前国际标准或工业先进国家标准,此外尚有50多个相关标准。
所有产品均有质量分等标准,出口产品不得低于一等品。
主机的专业标准有:
GB4686-84《插齿机精度》,JB/T3193-92《插齿机技术条件》,JB/T54458-94《插齿机产品质量分等》,GB9059-88《精密插齿机精度》,ZBnJ56006-88《精密插齿机制造与验收技术条件》,JB5571-91《齿条插齿机精度》,JB/T6343-92《齿条插齿机技术条件》,JB/T6606-93《高速插齿机技术条件》,JB/T6342-92《数控插齿机技术条件》,GB8064-98《滚齿机精度》,JB/T6344-92《滚齿机技术条件》,JB/T54468-94《滚齿机产品分等规定》,JB5569-91《精密滚齿机精度》,JB/T54505-94《精密滚齿机质量分等规定》,JB/T6345-92《重型滚齿机技术条件》,JB/T5570-91《卧式滚齿机精度》,JB/T6346-92《卧式滚齿机技术条件》,ZBJ56005.2-88、JB/T6597-93《小模数齿轮滚齿机精度》,ZBJ56005.3-88《小模数齿轮滚齿机制造验收技术要求》,JB/T4177-93《直齿锥齿轮刨齿机技术条件》,JB4176-86《直齿锥齿轮刨齿机精度》,JB/T54457-94《直齿锥齿轮刨齿机产品质量分等》,JB6095-92《直齿拉齿机精度》,JB/T54011-93《直齿锥齿轮拉齿机技术条件》,JB2267-86《弧齿锥齿轮铣齿机精度》,JB/T3192-93《弧齿锥齿轮铣齿机技术条件》,JB/T54450-94《弧齿锥齿轮铣齿机质量分等》,JB/T3732-94《剃齿机精度》,JB/T3865-92《剃齿机技术条件》,JB/T5451-94《剃齿机质量分等》,JB3953-85《弧齿锥齿轮磨齿机精度》,JB/T3954-96《弧齿锥齿轮磨齿机技术条件》,JB3988-85《蝶形砂轮磨齿机精度》,JB3991-85《锥形砂轮磨齿机精度》,JB3993-85《蜗杆砂轮磨齿机精度》,JB3990-85《成形砂轮磨齿机精度》,JB3992-85《大平面砂轮磨齿机精度》,JBn3989-85《渐开线圆柱齿轮磨齿机制造验收技术要求》,ZBJ56007-88《齿轮导角机精度》,JB/T6347-92《齿轮导角机技术条件》等。
1.3.8检验项目
检验时除按相关标准和产品技术条件要求检查外,主要进行精度和性能检验,各类齿轮加工铣齿机的精度,检验项目均在10项以上。
几何精度:
包括安装加工件的主轴(心轴)及工作台等项的有关精度,安装刀具的主轴(心轴)及刀架等项的有关精度,以及两者间的相关和相互位置精度。
传动精度:
包括长周期误差和短周期误差。
工作精度:
是指对加工件进行测量的检验项目,包括周节偏差、周节累积误差、齿向误差和齿面粗糙度等。
精度检验时还须参照JB2670-82《金属切削铣齿机精度检验通则》进行。
1.3.9主要生产厂及输往国家和地区
目前生产出口齿轮加工铣齿机的主要厂家有:
天津第一铣齿机总厂、重庆铣齿机厂、秦川铣齿机厂、南京铣齿机厂、南京第二铣齿机厂、上海第一铣齿机厂等,其产品主要销往美国、香港、东南亚、巴基斯坦、孟加拉、中东及欧洲等30余个国家和地区。
1.3.10包装及储运
齿轮加工铣齿机多采用木箱包装,各木箱生产厂家在制造木箱时,依据GB7284-98《框架木箱》,GB/T13384-92《机电产品包装通用技术条件》及相关标准。
上述标准对包装箱的材质、结构、含水率等项目做了具体规定。
包装箱检验抽样判定时还须参照SN/T0275-93《出口商品运输包装木箱检验规程》。
箱内铣齿机应进行有效的固定和衬垫,其电器及加工未涂漆表面应做防锈防潮处理,其防锈有效期为两年。
在存放及滞港期间铣齿机类产品应库内保管,暂时露天存放时应垫高并加苫盖防止雨淋、水浸。
箱面重心、防雨、勿倒置、轻放等标识应齐全,以保证运输时产品完好、安全运抵目的地。
1.3.11齿轮加工数控系统体系结构
传统齿轮加工铣齿机的运动关系复杂,以滚齿机(或蜗杆砂轮磨齿机)为例,在齿轮铣齿机中存在着展成分度链、差动链、进给传动链等。
调整既复杂又费时。
快速趋近、工进、快退的位置和距离都需要精心调试或试切才能完成,且需要的辅件多。
为了提高齿轮加工精度和加工效率,到了20世纪80年代以后,国内外开始对齿轮加工铣齿机进行数控化改造和生产数控齿轮加工铣齿机。
特别是近年来,由于微电子技术的迅速发展和以现代控制理论为基础的高精度、高速响应交流伺服系统的出现,为齿轮加工数控系统的发展提供了良好的条件和机遇。
我们将齿轮加工系统分为全功能和非全功能两大类。
1)非全功能齿轮加工数控系统的结构
配这类数控系统的铣齿机进给轴为数控轴,多采用伺服系统。
由于80年代齿轮加工数控化刚开始起步,当时数控技术无法满足齿轮加铣齿机展成分度链的高同步性的要求,因此展成分度链和差动链仍为传统的机械传动。
这种数控加工方式,调整比机械式齿轮加工铣齿机要方便的多。
它们可以通过几个坐标轴的联动来实现齿向修形齿轮的加工,省去了传统加工修形齿轮所需要的靠模等装置,提高了生产率和加工精度。
但是这类齿轮加工数控系统属经济型数控系统,由于其展成分度链和差动链仍为传统的机械式,齿轮加工精度取决于机械传动链的精度。
目前这种齿轮加工数控系统多用于对现有机械式齿轮加工铣齿机的数控改造。
2)全功能齿轮加工数控系统的结构
近年来,由于计算机技术的迅猛发展和高精度、高速响应的伺服系统的出现,全功能数控齿轮加工铣齿机已成为国际市场上的主流产品。
全功能数控指不仅齿轮铣齿机的各轴进给运动是数控的,而且铣齿机的展成运动和差动运动也是数控的。
目前展成分度链和差动链的数控处理方法不尽相同,有基于软件插补以及基于硬件控制的两种类型。
3)基于软件差补的齿轮加工数控系统
这类数控系统的刀具主轴一般采用变频装置控制,工件主轴通过数控指令经伺服电动机直接驱动。
目前国产数控齿轮加工铣齿机所配置的数控系统大多为国外知名品牌的通用数控系统,因而都是采用这种基于软件插补的数控加工方式。
基于软件插补方法的优点是工件主轴的转速完全由数控系统的软件控制,因此,可以通过编制适当的软件,用通用的刀具来高精度快速地加工非圆齿轮、修形齿轮,且加工精度远远高于传统的机械靠模加工方法。
目前,由于控制精度、动态响应等方面的原因,基于软件插补的齿轮加工数控系统还不能胜任高速高精度磨齿机的要求。
随着计算机速度的不断提高、新控制方法的出现和控制精度的提高,这种方法的应用面越来越广。
基于硬件控制的齿轮加工数控系统在传统齿轮铣齿机的展成分度链中,刀具和工件是由同一个电动机来拖动的,传动链很长,并常需要采用精度不易提高的传动元件(如锥齿轮、万向联轴节等),所以提高铣齿机精度受到限制制。
目前多采用光电盘脉冲分频分度传动链。
砂轮主轴以固定转速旋转,并带动发信元件(如光电盘),光电盘信号经数字分频后,控制工件轴伺服电机以一定的转速旋转以实现精确分度传动关系。
同时把铣齿机的差动链也纳入控制系统。
基于硬件控制的齿轮加工数控系统的优点:
采用硬件控制,特别是采用高同步精度的锁相伺服控制时,精度高,响应速度快。
缺点:
机构上比较复杂,比软件插补的方式多一个硬件控制电路部分。
硬件控制的电子齿轮比(差动系数、主传动比),目前还不能做到实时修改,即不能实时改变工件主轴的转速,因而不能用于加工非圆齿轮等。
非全功能数控系统由于加工精度取决于机械传动链,仍存在交换挂轮,操作较繁,已较少使用。
目前多用于现有机械式齿轮加工铣齿机的数控化改造;基于软件插补的齿轮加工数控系统具有柔性大的优点,可以很方便地通过程序控制,能加工非圆齿轮和各种修形齿轮,因而在加工精度不高的滚齿机和插齿机中有广泛的应用;基于硬件控制的齿轮加工数控系统,由于展成运动是直接采用硬件控制,特别是采用跟踪精度极高的锁相伺服技术时,能很好地保证齿轮铣齿机差动和展成运动精度,响应速度快,但柔性差,适于加工精度要求高的磨齿机。
全功能的齿轮加工数控系统在国际上已是主流产品,也必将在国内成为主流产品
1.4本课题完成的主要工作
本课题运用CAD技术对内齿轮铣齿机动力铣削头进行设计能够缩短产品设计周期、减轻设计人员的工作强度、降低设计成本、增强企业的市场竞争能力。
(1)广泛查阅资料,了解国内外CAD技术的发展现状;深入分析研究铣齿机的结构。
(2)对内齿轮铣齿机铣削头