新型干法水泥生产工艺葸国隆.docx
《新型干法水泥生产工艺葸国隆.docx》由会员分享,可在线阅读,更多相关《新型干法水泥生产工艺葸国隆.docx(27页珍藏版)》请在冰豆网上搜索。
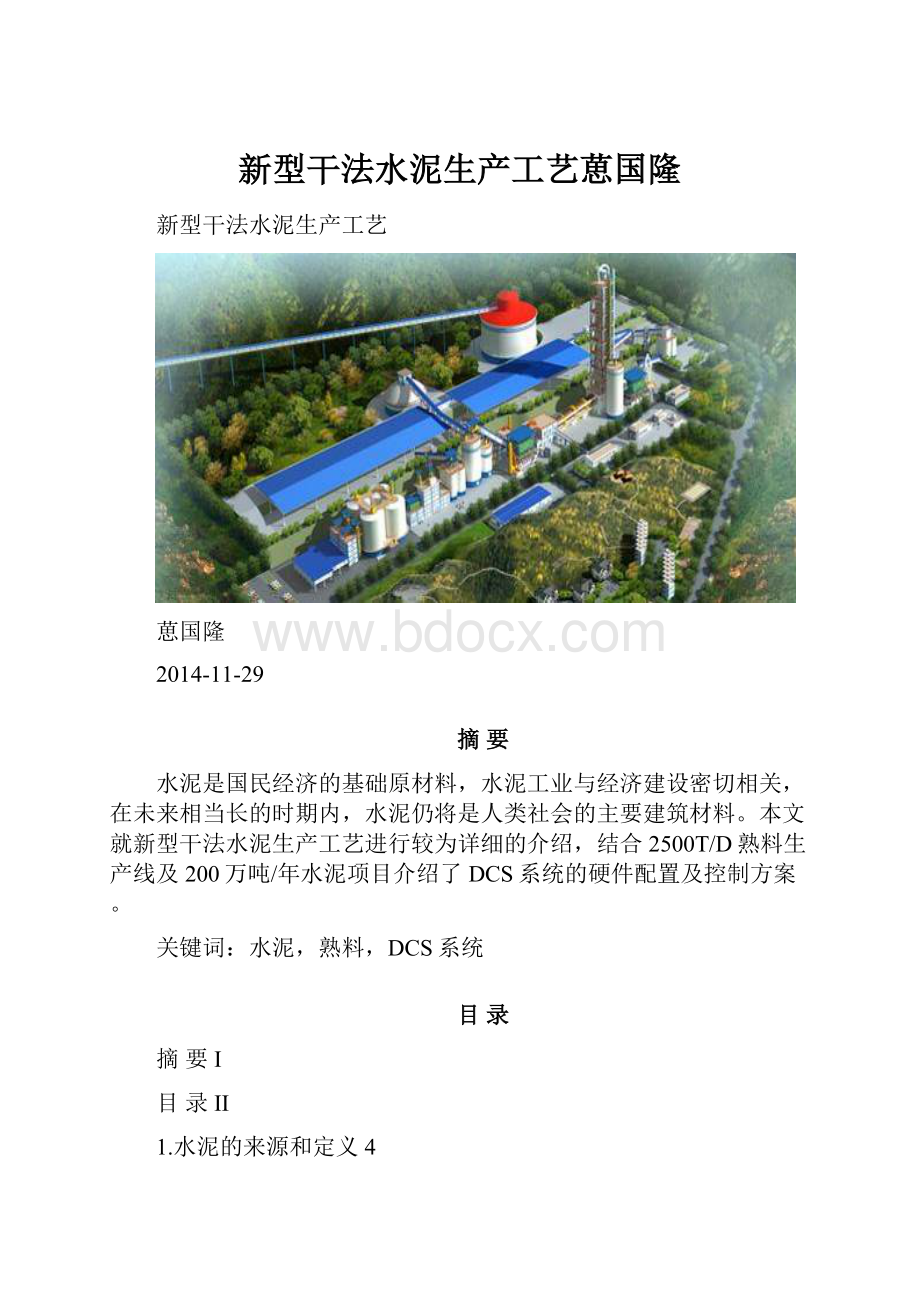
新型干法水泥生产工艺葸国隆
新型干法水泥生产工艺
葸国隆
2014-11-29
摘要
水泥是国民经济的基础原材料,水泥工业与经济建设密切相关,在未来相当长的时期内,水泥仍将是人类社会的主要建筑材料。
本文就新型干法水泥生产工艺进行较为详细的介绍,结合2500T/D熟料生产线及200万吨/年水泥项目介绍了DCS系统的硬件配置及控制方案。
关键词:
水泥,熟料,DCS系统
目录
摘要I
目录II
1.水泥的来源和定义4
1.1水泥的来源4
1.2水泥的定义4
1.3.水泥分类4
2.水泥生产工艺的发展及分类5
2.1水泥生产工艺的发展5
2.2水泥生产工艺的分类5
3.硅酸盐水泥的生产7
3.1硅酸盐水泥生产原料及配料7
3.2硅酸盐水泥熟料的矿物组成7
3.3硅酸盐水泥生产工艺流程8
3.3.1硅酸盐生产工艺流程图8
3.3.2工艺流程10
4.2500T/D熟料生产线及200万吨/年粉磨生产线DCS系统设计14
4.1测点清单及网络结构14
1I/O点表14
2系统结构图14
4.2DCS系统硬件配置15
4.3DCS系统工艺流程图及控制方案18
1工艺流程图总貌18
2原料处理18
3原料粉磨19
4废气处理20
5窑尾窑中20
6烧成窑头21
7煤粉制备22
8水泥粉磨23
9水泥储存23
1.水泥的来源和定义
1.1水泥的来源
cement一词由拉丁文caementum发展而来,是碎石及片石的意思。
水泥的历史可追溯到古罗马人在建筑工程中使用的石灰和火山灰的混合物。
1796年英国人J.帕克用泥灰岩烧制一种棕色水泥,称罗马水泥或天然水泥。
1824年英国人J.阿斯普丁用石灰石和粘土烧制成水泥,硬化后的颜色与英格兰岛上波特兰地方用于建筑的石头相似,被命名为波特兰水泥,并取得了专利权。
20世纪初,随着人民生活水平的提高,对建筑工程的要求日益提高,在不断改进波特兰水泥的同时,研制成功一批适用于特殊建筑工程的水泥,如高铝水泥,特种水泥等,水泥品种已发展到100多种。
1.2水泥的定义
粉状水硬性无机胶凝材料。
加水拌和成塑性浆体后,既能在空气中硬化又能在水中硬化,并能将砂、石等材料牢固地胶结在一起。
1.3.水泥分类
水泥按用途及性能分为:
1.通用水泥:
一般土木建筑工程通常采用的水泥。
通用水泥主要是指:
GB175—1999、GB1344—1999和GB12958—1999规定的六大类水泥,即硅酸盐水泥、普通硅酸盐水泥、矿渣硅酸盐水泥、火山灰质硅酸盐水泥、粉煤灰硅酸盐水泥和复合硅酸盐水泥。
2.专用水泥:
专门用途的水泥。
如:
G级油井水泥,道路硅酸盐水泥。
特性水泥:
某种性能比较突出的水泥。
如:
快硬硅酸盐水泥、低热矿渣硅酸盐水泥、膨胀硫铝酸盐水泥。
2.水泥生产工艺的发展及分类
2.1水泥生产工艺的发展
水泥生产自1824年诞生以来,生产技术历经了多次变革。
从间歇作业的土立窑到1885年出现回转窑;从1930年德国伯力鸠斯的立波尔窑到1950年联邦德国洪堡公司的悬浮预热器窑;1971年日本石川岛公司和秩父水泥公司在悬浮预热技术的基础上研究成功了预分解法,即预分解窑。
新型干法水泥生产技术,是以悬浮预热和预分解技术为核心,利用现代流体力学、燃烧动力学、热工学、粉体工程学等现代科学理论和技术,并采用计算机及其网络化信息技术进行水泥工业生产的综合技术。
新型干法水泥生产技术具有高效、优质、节能、节约资源、环保和可持续发展的特点,充分体现了现代水泥工业生产大型化、自动化的特征。
新型干法水泥生产技术的出现,彻底改变了水泥生产技术的格局和发展进程,它采用现代最新的水泥生产工艺和装备,逐步取代了立窑生产技术、湿法窑生产技术、干法中空窑生产技术以及半干法生产技术,从而把水泥工业生产推向一个新的阶段。
2.2水泥生产工艺的分类
1.水泥生产随生料制备方法不同,可分为干法(包括半干法)与湿法(包括半湿法)两种:
(1)干法生产:
将原料同时烘干并粉磨,或先烘干经粉磨成生料粉后喂入干法窑内煅烧成熟料的方法。
但也有将生料粉加入适量水制成生料球,送入立波尔窑内煅烧成熟料的方法,称之为半干法,仍属干法生产之一种。
(2)湿法生产:
将原料加水粉磨成生料浆后,喂入湿法窑煅烧成熟料的方法。
也有将湿法制备的生料浆脱水后,制成生料块入窑煅烧成熟料的方法,称为半湿法,仍属湿法生产之一种。
干法生产的主要优点是热耗低(如带有预热器的干法窑熟料热耗为3140~3768焦/千克),缺点是生料成分不易均匀,车间扬尘大,电耗较高。
湿法生产具有操作简单,生料成分容易控制,产品质量好,料浆输送方便,车间扬尘少等优点,缺点是热耗高(熟料热耗通常为5234~6490焦/千克)。
2.水泥生产随煅烧熟料的设备结构不同,可分为立窑和回转窑两类。
(1)立窑:
窑筒体立置不转动的称为立窑。
分普通立窑和机械化立窑。
普通立窑是人工加料和人工卸料或机械加料,人工卸料;机械立窑是机械加料和机械卸料。
机械立窑是连续操作的,它的产、质量及劳动生产率都比普通立窑高。
近年来,国外大多数立窑已被回转窑所取代,但在当前中国水泥工业中,立窑仍占有重要地位。
根据建材技术政策要求,小型水泥厂应用机械化立窑,逐步取代普通立窑。
(2)回转窑:
窑筒体卧置(略带斜度,约为3%),并能作回转运动的称为回转窑。
分煅烧生料粉的干法窑和煅烧料浆(含水量通常为35%左右)的湿法窑。
①干法窑:
干法窑又可分为中空式窑、余热锅炉窑、悬浮预热器窑和悬浮分解炉窑。
70年代前后,发展了一种可大幅度提高回转窑产量的煅烧工艺──窑外分解技术。
其特点是采用了预分解窑,它以悬浮预热器窑为基础,在预热器与窑之间增设了分解炉。
在分解炉中加入占总燃料用量50~60%的燃料,使燃料燃烧过程与生料的预热和碳酸盐分解过程,从窑内传热效率较低的地带移到分解炉中进行,生料在悬浮状态或沸腾状态下与热气流进行热交换,从而提高传热效率,使生料在入窑前的碳酸钙分解率达80%以上,达到减轻窑的热负荷,延长窑衬使用寿命和窑的运转周期,在保持窑的发热能力的情况下,大幅度提高产量的目的。
②湿法窑:
用于湿法生产中的水泥窑称湿法窑,湿法生产是将生料制成含水为32%~40%的料浆。
由于制备成具有流动性的泥浆,所以各原料之间混合好,生料成分均匀,使烧成的熟料质量高,这是湿法生产的主要优点。
湿法窑可分为湿法长窑和带料浆蒸发机的湿法短窑,长窑使用广泛,短窑目前已很少采用。
为了降低湿法长窑热耗,窑内装设有各种型式的热交换器,如链条、料浆过滤预热器、金属或陶瓷热交换器。
立窑适用于生产规模较小的工厂,大、中型厂宜采用回转窑。
目前我国单条线产量最大的回转窑生产线为安徽芜湖海螺12000t/d熟料生产线,而单台立窑熟料最大产量为1200t/d。
3.硅酸盐水泥的生产
硅酸盐类水泥的生产工艺在水泥生产中具有代表性,是以石灰石和粘土为主要原料,经破碎、配料、磨细制成生料,然后喂入水泥窑中煅烧成熟料,再将熟料加适量石膏(有时还掺加混合材料或外加剂)磨细而成。
3.1硅酸盐水泥生产原料及配料
生产硅酸盐水泥的主要原料为石灰原料和粘土质原料,有时还要根据燃料品质和水泥品种,掺加校正原料以补充某些成分的不足,还可以利用工业废渣作为水泥的原料或混合材料进行生产。
1.石灰石原料
石灰质原料是指以碳酸钙为主要成分的石灰石、泥灰岩、白垩和贝壳等。
石灰石是水泥生产的主要原料,每生产一吨熟料大约需要1.3吨石灰石,生料中80%以上是石灰石。
2.黏土质原料
黏土质原料主要提供水泥熟料中的
、
、及少量的
。
天然黏土质原料有黄土、黏土、页岩、粉砂岩及河泥等。
其中黄土和黏土用得最多。
此外,还有粉煤灰、煤矸石等工业废渣。
黏土质为细分散的沉积岩,由不同矿物组成,如高岭土、蒙脱石、水云母及其它水化铝硅酸盐。
3.校正原料
当石灰质原料和黏土质原料配合所得生料成分不能满足配料方案要求时(有的
含量不足,有的
和
含量不足)必须根据所缺少的组分,掺加相应的校正原料
(1)硅质校正原料含80%以上
(2)铝质校正原料含30%以上
(3)铁质校正原料含50%以上
3.2硅酸盐水泥熟料的矿物组成
硅酸盐水泥熟料的矿物主要由硅酸三钙(
)、硅酸二钙(
)、铝酸三钙(
)和铁铝酸四钙(
)组成。
详见以下表格:
表格3-1
矿物名称
化学式
简写
范围
(wt,%)
硅酸三钙
37~60%
硅酸二钙
15~37%
铝酸三钙
7~15%
铁铝酸四钙
10~18%
3.3硅酸盐水泥生产工艺流程
3.3.1硅酸盐生产工艺流程图
3.3.2工艺流程
1.破碎及预均化
(1)破碎:
水泥生产过程中,大部分原料要进行破碎,如石灰石、黏土、铁矿石及煤等。
破碎过程要比粉磨过程经济而方便,合理选用破碎设备和和粉磨设备非常重要。
在物料进入粉磨设备之前,尽可能将大块物料破碎至细小、均匀的粒度,以减轻粉磨设备的负荷,提高磨机的产量。
物料破碎后,可减少在运输和贮存过程中不同粒度物料的分离现象,有得于制得成分均匀的生料,提高配料的准确性。
石灰石是生产水泥用量最大的原料,开采后的粒度较大,硬度较高,因此石灰石是生产水泥用量最大的原料,开采后的粒度较大,硬度较高,因此石灰石的破碎在水泥厂的物料破碎中占有比较重要的地位。
图3-1石灰石矿厂图3-2破碎机房图3-3石灰石输送皮带
(2)原料预均化预均化技术就是在原料的存、取过程中,运用科学的堆取料技术,实现原料的初步均化,使原料堆场同时具备贮存与均化的功能。
原料预均化的基本原理就是在物料堆放时,由堆料机把进来的原料连续地按一定的方式堆成尽可能多的相互平行、上下重叠和相同厚度的料层。
取料时,在垂直于料层的方向,尽可能同时切取所有料层,依次切取,直到取完,即“平铺直取”。
图3-4石灰石矩形预均化堆场图3-5石灰石圆形预均化堆场图3-6煤预均化堆场
2.生料制备
水泥生产过程中,每生产1吨硅酸盐水泥至少要粉磨3吨物料(包括各种原料、燃料、熟料、混合料、石膏),据统计,干法水泥生产线粉磨作业需要消耗的动力约占全厂动力的60%以上,其中生料粉磨占30%以上,煤磨占约3%,水泥粉磨约占40%。
原料磨(立式磨)工作原理:
电动机通过减速装置带动磨盘转动,物料通过锁风喂料装置经下料溜子落到磨盘中央,在离心力的作用下被甩向磨盘边缘交受到磨辊的辗压粉磨,粉碎后的物料从磨盘的边缘溢出,被来自喷嘴高速向上的热气流带起烘干,根据气流速度的不同,部分物料被气流带到高效选粉机内,粗粉经分离后返回到磨盘上,重新粉磨;细粉则随气流出磨,在系统收尘装置中收集下来,即为产品。
没有被热气流带起的粗颗粒物料,溢出磨盘后被外循环的斗式提升机喂入选粉机,粗颗粒落回磨盘,再次挤压粉磨。
图3-7立式磨图3-8立式磨原理图
3.生料均化图3-9均化库原理图
新型干法水泥生产过程中,稳定入窖生料成分是稳定熟料烧成热工制度的前提,生料均化系统起着稳定入窖生料成分的最后一道把关作用。
均化原理:
采用空气搅拌,重力作用,产生“漏斗效应”,使生料粉在向下卸落时,尽量切割多层料面,充分混合。
利用不同的流化空气,使库内平行料面发生大小不同的流化膨胀作用,有的区域卸料,有的区域流化,从而使库内料面产生倾斜,进行径向混合均化。
4.预热分解
把生料的预热和部分分解由预热器来完成,代替回转窑部分功能,达到缩短回窑长度,同时使窑内以堆积状态进行气料换热过程,移到预热器内在悬浮状态下进行,使生料能够同窑内排出的炽热气体充分混合,增大了气料接触面积,传热速度快,热交换效率高,达到提高窑系统生产效率、降低熟料烧成热耗的目的。
工作原理:
预热器的主要功能是充分利用回转窑和分解炉排出的废气余热加热生料,使生料预热及部分碳酸盐分解。
为了最大限度提高气固间的换热效率,实现整个煅烧系统的优质、高产、低消耗,必需具备气固分散均匀、换热迅速和高效分离三个功能。
(1)物料分散
换热80%在入口管道内进行的。
喂入预热器管道中的生料,在与高速上升气流的冲击下,物料折转向上随气流运动,同时被分散。
(2)气固分离
当气流携带料粉进入旋风筒后,被迫在旋风筒筒体与内筒(排气管)之间的环状空间内做旋转流动,并且一边旋转一边向下运动,由筒体到锥体,一直可以延伸到锥体的端部,然后转而向上旋转上升,由排气管排出。
(3)预分解
预分解技术的出现是水泥煅烧工艺的一次技术飞跃。
它是在预热器和回转窑之间增设分解炉和利用窑尾上升烟道,设燃料喷入装置,使燃料燃烧的放热过程与生料的碳酸盐分解的吸热过程,在分解炉内以悬浮态或流化态下迅速进行,使入窑生料的分解率提高到90%以上。
将原来在回转窑内进行的碳酸盐分解任务,移到分解炉内进行;燃料大部分从分解炉内加入,少部分由窑头加入,减轻了窑内煅烧带的热负荷,延长了衬料寿命,有利于生产大型化;由于燃料与生料混合均匀,燃料燃烧热及时传递给物料,使燃烧、换热及碳酸盐分解过程得到优化。
因而具有优质、高效、低耗等一系列优良性能及特点。
图3-10悬浮预热分解炉
5.水泥熟料的烧成
生料在旋风预热器中完成预热和预分解后,下一道工序是进入回转窑中进行熟料的烧成。
在回转窑中碳酸盐进一步的迅速分解并发生一系列的固相反应,生成水泥熟料中的
、
、
等矿物。
随着物料温度升高近
时,
、
、
等矿物会变成液相,溶解于液相中的
和
进行反应生成大量
(熟料)。
熟料烧成后,温度开始降低。
最后由水泥熟料冷却机将回转窑卸出的高温熟料冷却到下游输送、贮存库和水泥磨所能承受的温度,同时回收高温熟料的显热,提高系统的热效率和熟料质量。
图3-11水泥磨图3-12回转窑
6.水泥粉磨
水泥粉磨是水泥制造的最后工序,也是耗电最多的工序。
其主要功能在于将水泥熟料(及胶凝剂、性能调节材料等)粉磨至适宜的粒度(以细度、比表面积等表示),形成一定的颗粒级配,增大其水化面积,加速水化速度,满足水泥浆体凝结、硬化要求。
7.水泥包装
水泥出厂有袋装和散装两种发运方式。
图3-13水泥库图3-14散装水泥库图3-15水泥包装车间
4.2500T/D熟料生产线及200万吨/年粉磨生产线DCS系统设计
4.1测点清单及网络结构
1I/O点表
表4-1I/O点表
控制站名称
DI
DO
AI
AO
合计
实际点数
备用点数
实际点数
备用点数
实际点数
备用点数
实际点数
备用点数
实际总点数
备用总点数
石灰石预均化远程站
44
20
16
16
3
5
0
8
63
49
原料调配远程站
58
22
23
9
13
11
6
10
100
52
原料粉磨控制站
207
33
56
24
144
16
18
14
425
87
窑尾控制站
201
39
72
24
76
20
12
12
361
95
窑头控制站
49
31
13
19
81
15
14
10
157
75
煤粉制备控制站
190
50
64
32
79
17
12
12
345
111
水泥粉磨A线
267
37
87
25
143
17
17
7
514
86
水泥粉磨B线
279
25
59
21
139
21
15
9
492
76
包装控制站
265
23
87
25
26
6
9
7
387
61
总计
1560
280
477
195
704
128
103
89
2844
692
2系统结构图
图4-1
系统结构图
4.2DCS系统硬件配置
整个控制系统共分为9个工段,分别是:
石灰石预均化、原料调配、原料粉磨、窑尾、窑头、煤粉制备、水泥粉磨A线、水泥粉磨B线及水泥包装,共配置5台操作员站(其中1台兼工程师站、两台兼服务器)、,14面机柜(其中7面I/O机柜、7面扩展柜),1面电源分配柜,1面网络柜。
注:
水泥现场行业习惯所有DI点查询电源为220VAC,因此所有DI模块底座均配置FM131E并配置SM3611(目前已被SM3615替代)。
1.系统结构图
图4-2系统网络结构图
2.根据I/O清单各个工段模块统计如下表:
控制站名称
DI(每个模块16点)
DO(每个模块16点)
AI(每个模块8点)
AO(每个模块8点)
合计
隔离器
备注
模块数量
模块数量
模块数量
模块数量
模块数量
石灰石破碎远程站
4
2
1
1
8
8
作为原料粉磨控制站的远程站
原料调配远程站
5
2
3
2
12
20
作为原料粉磨控制站的远程站
原料粉磨控制站
15
5
20
4
44
168
窑尾控制站
15
6
12
3
36
88
窑头控制站
5
2
12
3
22
96
煤粉制备控制站
15
6
12
3
36
88
水泥粉磨A线
19
7
20
3
49
152
水泥粉磨B线
19
5
20
3
47
152
包装控制站
18
7
4
2
31
32
总计
115
42
104
24
285
804
3.由于水泥现场设备较为分散,现场所有I/O机柜与中控室采用光纤通讯。
7面I/O柜内均成套2台七点一光光口交换机,中控室内对应安装7对光纤收发器,如下图所示:
4.3DCS系统工艺流程图及控制方案
1工艺流程图总貌
2原料处理
(1)包括石灰石破碎及输送、石灰石预均化、辅助原料破碎及输送等。
(2)工艺子组:
石灰破碎输送组、石灰输送入库组、辅助原料破碎输送组。
(3)板喂机自动调速控制,根据破碎机负荷自动调节板喂机喂料量。
3原料粉磨
(1)包括原料配料、原料磨。
(2)工艺子组:
原料配料输送组、立磨系统组、立磨回料组、生料入库输送组
4废气处理
(1)包括窑尾收尘、增湿塔。
(2)工艺子组:
窑灰输送组、点收尘高压组、增湿塔排灰组。
(3)尾排风机联锁控制,尾排风机与高温风机、循环风机联锁,尾排风机故障停机时要联锁停止高温风机、循环风机。
保证窑头不出现正压,这对窑操安全至关重要。
(4)增湿塔出口温度自动调节。
通过调节喷水量来控制增湿塔出口温度,以增湿降温提高电收尘器的收尘效率,电收尘入口温度一般控制在150℃以下。
(5)电收尘与C1筒出口CO含量的联锁保护。
CO含量大于1.5%时,要停止窑尾收尘高压电场,否则会引起爆炸,是相当危险。
5窑尾窑中
(1)包括烧成窑尾、烧成窑中。
(2)分解炉出口温度自动调节。
(3)窑尾空气炮自动控制,自动定时吹堵、预热器堵料报警及联锁控制。
(4)窑直流传动控制。
(5)窑液压挡轮油站控制。
6烧成窑头
(1)工艺子组:
窑头熟料输送、收尘输灰组、收尘高压组。
(2)弧形阀自动控制,对篦冷机下的细料,通过弧形阀自动循环控制进行卸料,根据工艺要求,可以设定弧形阀工作时间及循环时间。
(3)窑头罩压力与窑头排风机转速(或排风阀开度)的闭环自动控制。
(4)篦冷机一室篦下压力与篦速的闭环自动控制。
7煤粉制备
(1)工艺子组:
原煤输送组、煤磨选粉组、煤磨润滑组。
(2)磨负荷控制。
(3)煤磨出口风温自动调节。
8水泥粉磨
(1)工艺子组:
辊压系统组、磨机润滑组、水泥粉磨组、水泥输送入库组、库底卸料组。
(2)磨负荷自动与产量闭环自动控制。
9水泥储存