燕山石化实习报告讲解.docx
《燕山石化实习报告讲解.docx》由会员分享,可在线阅读,更多相关《燕山石化实习报告讲解.docx(26页珍藏版)》请在冰豆网上搜索。
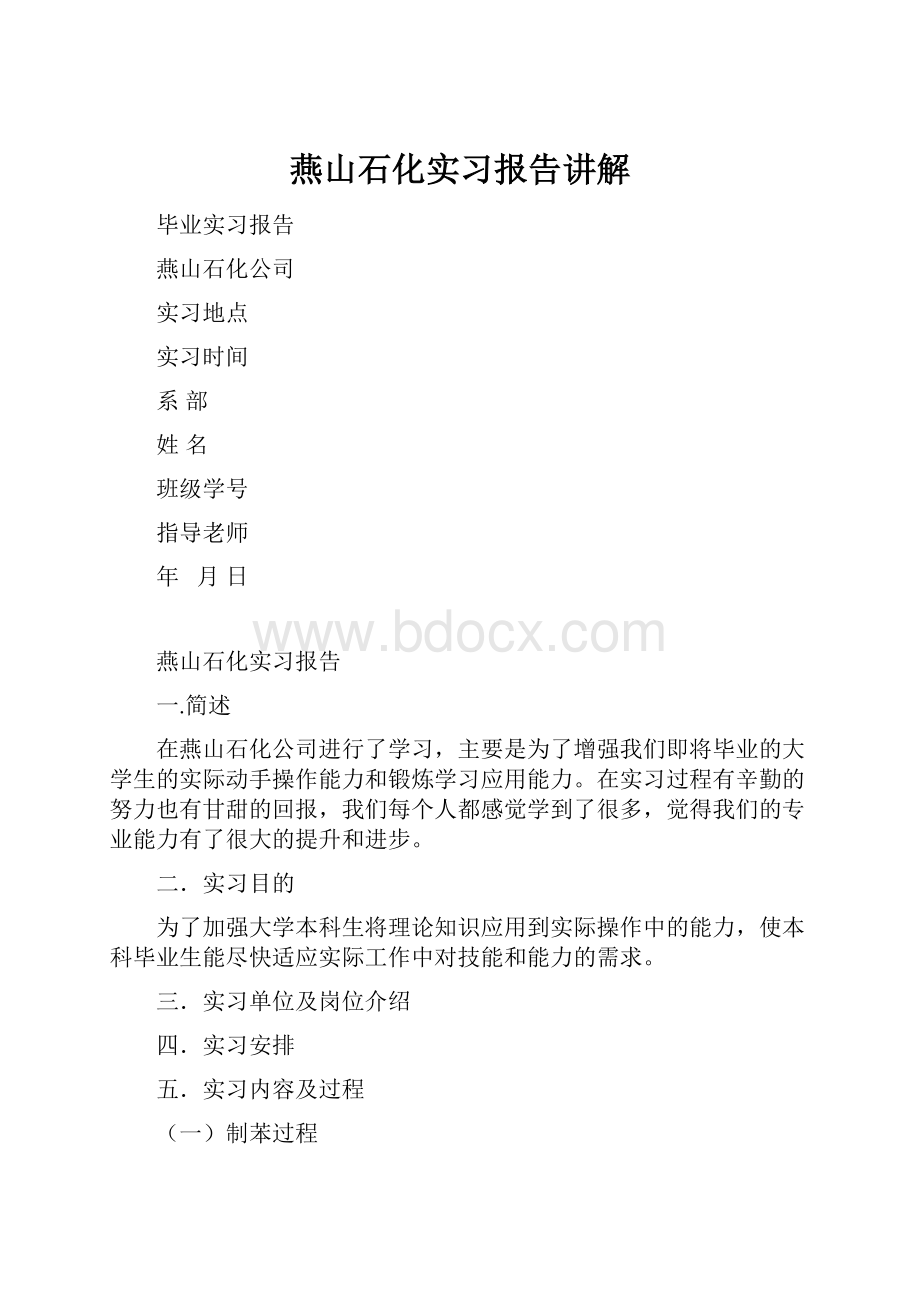
燕山石化实习报告讲解
毕业实习报告
燕山石化公司
实习地点
实习时间
系部
姓名
班级学号
指导老师
年月日
燕山石化实习报告
一.简述
在燕山石化公司进行了学习,主要是为了增强我们即将毕业的大学生的实际动手操作能力和锻炼学习应用能力。
在实习过程有辛勤的努力也有甘甜的回报,我们每个人都感觉学到了很多,觉得我们的专业能力有了很大的提升和进步。
二.实习目的
为了加强大学本科生将理论知识应用到实际操作中的能力,使本科毕业生能尽快适应实际工作中对技能和能力的需求。
三.实习单位及岗位介绍
四.实习安排
五.实习内容及过程
(一)制苯过程
1.治苯装置的主要构成
2.工艺路线
2.1一段加氢反应部分采用Lummus加氢工艺流程,采用低温、低压、高活性的镍系催化剂HTCNi400,不用循环氢而直接使用新鲜氢气。
3.基本原理
3.1脱砷反应原理
本装置采用氧化脱砷技术。
脱砷剂用的是CHP,活性组分是过氧化氢异丙苯,机理是使物料中的砷重质化,反应表示如下:
R1—O—O—R2+ASR
ASRR1+R2—O—ASRR1
的馏程比C9+重,在脱C9+塔底被出去。
3.2加氢反应的影响因素
加氢反应为放热反应。
影响因素:
催化剂的性能、反应温度、反应压力、空速、氢油比、原料油性质等。
(1)反应温度:
在一段反应中采用了高活性催化剂,控制适宜的入口温度50~80℃,二段反应控制入口温度在250~310℃
(2)反应压力:
增加压力对反应有利,特别是增加氢分压,可利于平衡向加氢反应方向进行。
(3)空速:
空速一般用LHSV表述,以表示单位时间单位体积催化剂床层所处理的原料油量来表示。
在加氢反应中,总气体量与原料油的比例称为氢油比。
氢油比大,氢气用量增多,能使反应完全及防止积炭生成。
4.流程概述
4.1脱戊烷塔系统
从裂解装置或油品罐区来的裂解汽油进入本装置后,经进料缓冲罐(D—104)缓冲、沉降脱水,用LICA—101调节裂解汽油进罐的流量,来控制进料缓冲罐(D—104)的液位,用裂解汽油进料泵(P—107)送至脱戊烷塔进料预热器(E—111)。
热物料来自芳烃抽提单元的贫溶剂,将原料裂解汽油预热到泡点温度后,从脱戊烷塔(T—101)的第25块(或29)块塔板进入,由FIRC—103控制进料量为51.87t/h脱戊烷塔塔顶为C5及更轻的烃类,经空冷器(EA-101)冷凝冷却后,凝液至脱戊烷塔回流罐(D-101),经脱戊烷塔回流泵(P-101A/B)送出,一部分用FIRC-106控制作为回流返回塔顶,回流比控制在2.9,一部分作为副产品送经外界外,用LICA-107控制其流量。
随裂解汽油原料一起进入脱戊烷塔的水分,以回流罐(D-101)底部分水包定期排放。
脱戊烷塔回流罐(D-101)的压力通过PV-11A、PV-11B调节补充氮气或放火炬的量来调节。
脱戊烷塔再沸器(E-102A/B)用中压蒸汽加热,通过TIRC-102来调节加热蒸汽的流量,塔釜物料用塔全泵(P-102A/B)抽出后,一部分进入再沸器,强制循环加热,另一部分在LIRC-1110串级控制下进入脱砷反应部分。
4.2脱砷反应部分
罐装的CHP(过氧化氢异丙苯)用气泵送入CHP配料罐(D-105A/B)与加氢后的C7馏分混合,按13wt﹪的浓度配置,配置好的CHP溶液经CHP的进料泵(P-108A/B)加压后,定量打入CHP混合器(M-101),与脱戊烷塔底来的物料混合均匀,一起从底部进入脱砷反应器(R-101),保证足够的停留时间,反应温度为130~150℃。
由于CHP为强氧化剂,因此D-105A/B罐顶有氮封及谁喷淋设施。
4.3预分馏塔系统(T-102)
从R-101来的C6~C9送入预分馏塔(F-102)的中部(第16、20、24块塔板),预分馏塔(F-102)的作用是除掉反应物料中的重质烃(C8、C9),塔顶物料为C6、C7馏分,经预分馏塔冷凝器(E-103)水冷后进入预分馏塔回流罐(D-102),凝液经预分馏塔回流泵(P-103A/B)升压,一部分用FIRC-112控制流量,作为回流返回塔顶,回流比0.7,其余部分在回流罐液位LIRC-113控制下送到C6、C7两段加氢系统,T-102塔为负压操作,用中压蒸汽通过预分馏塔喷射器(J-101A/B)将该塔抽真空,压力通过同PIC-119调节阀调节蒸汽喷射器的旁路流量来控制。
预分馏塔再沸器(E-104A/B)的热量由中压蒸汽提供,灵敏板温度用TIRC-111调节加热蒸汽来控制,塔底C8、C9重组分用预分馏底泵(P-106A/B)送出,一部分进入预分馏塔再沸器(E-104A/B)进行循环,其余部分在FIRC-113的控制下进入C8分馏塔(T-103)继续分离。
4.4C8分离系统(T-103)
来自预分馏塔底C8、C9分在馏分进入C8分离塔(T-103)的中部(第24、28块塔板),塔底得到C9馏分作为副产品,用C9产品输出泵(P-104A/B)再经C9馏分冷却器E-105A冷却后送经界外。
塔底C8馏分经C8分离塔冷凝器(E-108)冷凝,凝液至C8分离塔回流罐(D-107),再经C8馏分(P-112A/B)升压后,一部分用FIRC-134控制流量,作为回流返回塔顶,回流比2.45,其余部分在LICA-147的控制下送到C8一段加氢系统进行C8加氢处理。
F-103塔为负压操作,用中压蒸汽通过C8分离塔喷射器(J-102)将该塔抽真空,压力通过用PIC-152调节阀调节蒸汽喷射器的旁路流量来控制。
C8分离塔再沸器(E-109A/B)的热量由中压蒸汽提供,为了保证换热效果,进入再沸器的物料用塔釜循环泵(P—111A/B)进行强制循环,灵敏板温度用TIRC-144调节加热蒸汽来控制。
3.5阻聚剂注入系统
由于裂解汽油中含有大量的饱和烃,为了防止不饱和烃在高温下聚合,因此设置了阻聚剂注入系统,桶装的阻聚剂用气泵送入阻聚剂罐(D-106)中,用阻聚剂注入泵(P-109A/B/C)分别送到脱戊烷塔的进料线、回流线、塔顶气相采出线、预分馏塔的回流线、塔釜采出线,C8分离塔循环泵(P-111A/B)入口线,C8分离塔釜出泵入口线。
4.6C6、C7馏分一段加氢反应系统
为防止空气进入反应系统,一段进料缓冲罐(D-204)用PIC-210A/B阀控制,使其处于氮封状态,并使一段进料缓冲罐压力保持在0.2MPa。
从预分馏塔来的C6、C7馏分进入分水罐(D-203),分离出水后进入沉降分离罐(D-203),进一步脱除物料中的水分之后,进入一段进料缓冲罐(D-204),用一段(D-204),用一段加氢进料泵(P-201A/B)升压,用FIRC-202控制新鲜进料量,,进入物料混合器(M-201),与反应后的循环物料混合进入一段反应器(R-201)底部,界区来的新鲜氢气(压力为2.8MpaG)也从反应器底部进入,物料与氢气经一段反应器底部的分配器混合通过催化剂底层,进行加氢反应大部分双烯不饱和化合物被加氢,反应的入口温度根据催化剂的活性控制在30~96℃,通过TIRC-230调节通过反应器级间循环换热器(E-201)的物料流量来实现,反应压力为2.6Mpa,由PIRC-205调节氢气进料量来控制。
反应后的气液混合物料经反应器级间闪蒸罐(D-201)进行气液分离,分离的气体先经一段气相出料冷却器(E-202),将温度冷却至40℃,并在二次闪蒸罐(D-205)中将冷凝液分离,富氮气体送往一段循环气压缩机(C-701A/B),分离出的冷凝液在LICAS-208控制下返回到脱戊烷塔(T-101)的进料线。
应严格控制D-205的液位,以防高压气体窜入低压系统。
反应器级间闪蒸罐(D-201)的液体一部分由P-203A/B加压,在FIRC-203控制下,经一段反应器级间循环换热器(E-201)冷却或加热后,进入物料混合器(M-201),作为一段循环反应器内非循环物料,另一部分液体(一段加氢油)用二段反应器进料泵(P-205A/B)升压,用FIRC-205控制流量,送往第二段加氢反应系统。
4.7C6、C7馏分二段加氢反应系统
一段反应器出料经P-205A/B升压后,与二段反应器R-301出料在二段反应器R-301出料换热器E-302内进行换热,用TIC-355控制预热温度,然后送到混合器M-301。
从D-205罐及E-203上部来的氢气用补充氢气压缩机C-701A/B加压后,与循环氢气压缩机C-702A/B/C/D来的循环氢气一起经过第一循环氢预热器E-104、第二循环加氢预热器E-301,经过两次预热后进入气体加热炉F-201加热,其出口温度用TIRCAS-347调节加热炉燃料气的流量来控制,过热后到混合器M-301。
汽化的物料和氢气混合后进入反应器级间加热炉F-301进一步加热到反应器进口温度,其出口温度用FIRCAS-332调节加热炉燃料
气的流量来控制,然后进入二段反应器R-301。
二段反应器入口温度根据催化剂的活性控制在170~290℃,在二段反应器中全部的不饱和烃被完全加氢并脱除硫、氮等杂质。
从二段反应器出来的物料,通过第二段循环氢预热器E-301、二段反应器进出料换热器E-302,稳定塔再沸器E-406、第一循环氢预热器E-404进行换后热后,进入二段出料冷凝器EA-401、二段出料冷凝器ⅡE-402,将温度降至30~50℃后,进入高压闪蒸罐D-401进行气液分离。
闪蒸罐的气体经二段循环气压缩机C-702A/B/D升压后循环使用,二段反应系统的压力通过控制高压闪蒸罐的压力D-401来实现,用PIC-405调节罐顶放燃料气的流量来控制罐的压力,其中PV-0405A控制放燃料气量(或火炬气),PV-405B控制的是送东炼氢气量。
D-401液体在液位调节阀LICA-403的控制下进入低压闪蒸罐D-402再次闪蒸,以除去剩余的轻组分,罐的压力控制在0.8Mpa,用PIC-412调节罐顶放燃料气的流量来控制罐的压力。
从D-402排放的液体在液位调节阀LICA-404的控制下送到稳定塔系统。
苯乙烯装置
5.制苯装置产品去向
制
苯
装
置
自用燃料
C8
抽余油
甲苯
燃料气
C9
C5
化学品事业部间甲酚装置
化学品事业部分酮装置
氮气
裂解汽油
罐
区
6.1预分馏单元主要影响因素及调节方法:
质量问题
问题原因
解决方法
T-101—塔底物料初馏点温度高,C5馏分中苯含量高
(1)塔底温度高
(2)塔压低
(3)回流比低
(1)减少E—102蒸汽量降低塔底温度
(2)减少塔顶放空量,调节塔顶冷却系统负减少E—07冷却水量或关小空气百叶窗
(3)增大回流比
T—101塔底物料初馏点低
(1)塔底温度低
(2)塔压高
(1)增大E—104换热器蒸汽量提高塔底温度
(2)增大回流罐放空量,调节塔顶冷却系统,开打空冷百叶窗,增大E—107冷却水量
加氢进料中砷含量高
(1)脱砷剂注入量少
(2)脱砷剂失效
(1)调节增大脱砷剂注入量
(2)切换脱砷罐或更换脱砷剂
T—102塔塔顶物料终馏点高
(1)T—102塔底温度高
(2)T—102塔压低
(3)回流量小
(1)减少E—104再沸器蒸汽量,降低塔底温度
(2)减少J—101蒸汽喷射泵蒸汽量
(3)增大回流量
T—103塔塔顶物料终馏点高
(1)T—103塔底温度高
(2)T—103塔压低
(3)回流量小
(1)减少E—109再沸器蒸汽量,降低塔底温度
(2)减少J—102蒸汽喷射泵蒸汽量
(3)增大回流量
6.2加氢反应部分及稳定塔系统影响因素及调节方法
一段加氢油双烯、溴价不合格
(1)一段反应器温度低
(2)催化剂使用后期失活
(1)调节TIC—230提高反应器的入口温度
(2)对催化剂进行再生或更换新的催化剂
C8加氢双烯、溴价不合格
(1)C8加氢反应器温度低
(2)催化剂使用后期失活
(1)调节TIC—253提高反应器的入口温度
(2)对催化剂再生或更换新的催化剂
二段加氢油双烯、溴价不合格
(1)二段加氢反应器温度低
(2)催化剂使用后期失活
(1)调整加热炉T—301提高反应器入口温度
(2)对催化剂再生或更换新的催化剂
二段加氢油硫含量不合格
(1)二段反应器温度低
(2)催化剂失活
(3)T—401塔温度低
(1)调节TIC—232提高反应器入口温度
(2)对催化剂进行再生或更换新催化剂
(3)提高T—401塔的温度
稳定塔塔顶放空气体中苯含量高
(1)稳定塔塔顶温度高
(2)稳定塔塔压低
(3)回流比过小
(1)减少E—406再沸器加热量,降低塔釜温度
(2)减少E—411罐放空量提高塔压
(3)增大回流比
6.3抽提系统主要影响因素及调节方法
7.三废处理
进料缓冲罐排气、脱戊烷塔回流罐、大气水封槽排气、蒸汽喷射器凝液罐、高压闪蒸罐排气、低压闪蒸罐排气、稳定塔回流罐排气:
间断排放
加热炉烟气:
连续排放
8.气体主要成分及设备常用类型
(1)
闪蒸气
H2
硫化气
H2S、H2
新鲜氢
H2
C6馏分
甲苯
C7馏分
苯
裂解汽油
C4、C5、C6、C7、C8(其中C6、C7、C8为非芳)、苯、甲苯、C8芳烃、苯乙烯、C9
(2)
【注】:
灵敏板温度控制方法:
调节加热蒸汽量、溶剂量、溶剂进塔温度
(二)石油裂解过程
1.裂解反应原理
1.1裂解原料
裂解原料通常来源于下列装置:
A.天然气加工厂生产的轻烃(乙烯、丙烷、丁烷、天然汽油等)
B.炼油厂生产的油品(炼厂气、石脑油、柴油、重油、油渣等)
拔头油
C.原油
裂
解
装
置
抽余油
芳烃抽提
石脑油
铂重整
常
减
压
装
置
石脑油
常压柴油
原油稳定
轻石脑油
加氢裂化、加氢精制
减压柴油
加氢尾油
焦化加氢汽油
延迟焦化、加氢精制
焦化加氢柴油
渣油
加氢柴油
渣油轻质化
加氢精制
渣油
深
冷
分
离
轻烃
油田
轻烃
天然气
石油
天然气凝析液
乙烯装置裂解原料来源
本装置目前主要的裂解原料为来自炼油厂的重柴油(HOG)、石脑油(NAP)、加氢尾油(HVGO)、LPG(C4/C3),以及装置中乙烯精馏塔釜来的循环乙烷。
P——烷烃(较易裂解生产乙烯、丙烯)
O——烯烃(裂解性能不如相应的烷烃)
N——环烷烃(比烷烃易生成芳烃)
A——芳烃(裂解较难,易生成重质芳烃甚至结焦)
2.裂解工艺流程
H2、CH4
釜
C3以上组分
C3甲基乙炔、丙二烯
顶
丙烷
丙烯
乙烯精馏塔
脱丙烷塔
乙烯99.97﹪
乙烷
塔顶
乙烯精馏塔
37℃
87℃
190℃
97℃
急冷塔
汽油分馏塔
干燥
压缩机
急冷区
裂解炉
脱甲烷塔
11台4台
旧新
脱乙烷塔
C2、C3以上组分切割分离
C4、C5
C4:
橡胶
脱丁烷塔
3.反应原理
C5制苯
1.烷烃的裂解反应
(1)正烷烃:
其裂解反应主要进行的是脱氢反应和断链反应
A、脱氢反应:
是指C—H键断裂反应,产物分子中碳原子数不变
反应通式:
CnH2n+2CnH2n+H2
B、断链反应:
是指碳碳键断裂的反应,产物分子中碳原子数减少
反应通式:
CnH2n+2CmH2m+CkH2k+2,m+k=n
上述两类反应如下规律:
(a)一般认为脱氢反应是可逆反应,断链反应是不可逆反应
(b)断链反应所需要的能量比脱氢反应小,所以断链反应比脱氢反应容易进行,而且随着烷烃分子量的增大,断链反应更占优势,C4以上烷烃裂解时,断链反应占绝大比重。
(c)在分子两端的C—C键断裂反应要优先于在分子中央的C—C键裂解反应,随着分子量的增大,断裂在分子两端的优势弱。
烷烃裂解最有利于生成乙烯和丙烯。
(d)烷烃裂解时,反应速度常数K随裂解温度的升高而增加,在相同裂解温度下,碳原子数较多的正构烷烃,其反应常数也较大,所以裂解较小的烷烃需用较高的裂解温度。
(2)异构烷烃:
各种异构烷烃内结构各异
A、异丁烷:
主要通过断裂反应式脱氢反应获得少一个或同碳原子的烯烃
H2
+
CH4
+
B、新戊烷(2,2—二甲基丙烷):
主要是通过断链反应获得少一个碳原子的烯烃
2.烯烃的裂解反应
(1)断链反应:
较大分子的烯烃可以断链为两个较小分子的烯烃
反应通式:
CnH2n+2CiH2i+CmH2m,m+i=n
由于烯烃分子中有双键存在,因此断链主要发生在双键的C—C键上
如:
2位
1位
(2)脱氢反应:
烯烃进一步脱氢生成二烯烃或炔烃
如:
C4H8C4H6+H2
C2H4C2H2+H2
(3)歧化反应:
两分子的同一烯烃可歧化为两个不同的烃分子
如:
2C3H6C2H4+C4H8
2C3H6C2H6+C4H6
2C3H6C5H8+CH4
2C3H6C6H10+H2
(4)二烯合成反应:
二烯烃与烯烃进行二烯合成环烯烃,进一步脱氢生成芳烃
—2H2
(5)芳构化反应:
六个或更多碳原子的烯烃,可以发生芳构化反应生成芳烃。
—2H2
总之,烯烃的反应特点是即有由大分子烯烃生成乙烯,丙烯的反应,又有乙烯、丙烯进一步消失的反应。
环烷烃裂解由如下规律:
(1)侧链烷基比芳环易裂解,长侧链上离环近的碳键不易断裂,长侧链的断裂反应一般从中部开始,一直进行到侧链为甲基或乙基,然后再进一步裂解,长侧链环烷烃比无侧链环烷烃裂解所得乙烯收率高。
(2)环烷烃脱氢生成芳烃的反应优先于开环生成烯烃的反应。
(3)五碳环的环烷烃比六碳环的环烷烃难于裂解,烷基环戊烷的裂解速度比大体上与比它少三个碳原子的正构烷烃相当,烷基环己烷的裂解速度大体上比它少两个碳原子的正构烷烃相当。
(4)环烷烃比链烃更易于生成焦油,相应更容易产生结焦。
4.芳烃的裂解反应
由于芳环的稳定性,芳烃在裂解过程中不易发生裂开芳环的反应
5.烷基芳烃的断碳反应和脱氢反应
A、芳烃的侧链脱烷基或断键生成烯烃
B、芳烃的侧链脱氢生成烯烃
Ar—芳烃,n=f+m
ArH+CnH2n
Ar—CfH2f+1+CmH2m
Ar—CnH2n+1
Ar—CnH2n+1ArCnH2n-1+H2
(2)环烷基芳烃的反应
A、脱氢和异构脱氢
B、缩合脱氢
(3)芳烃的缩合反应
无烷基和无环烷基的芳烃在反应中,芳环开而是经缩合而成多环芳烃,同时脱出氢,且分子量增大。
总之,芳烃由于其分子结构中芳环的稳定性,在裂解温度下不易发生裂开芳环的反应,而往往把芳环保存下来,主要发生两类反应,一是烷基芳烃的侧链发生断碳反应和脱氢反应,二是烷烃的缩合反应而使产物芳烃分子中的芳环增多,分子量增大,直到生成焦油甚至结焦。
4.关于一次反应和二次反应
一次反应就是指原料烃分子在裂解过程中首先发生的反应。
二次反应就是一次反应的生成继续发生的后继反应。
原料烃分子在裂解过程中生成目的产物乙烯、丙烯的反应称为一次反应。
乙烯、丙烯消失生成分子量较大的液体产物以至结焦生碳的反应称为二次反应。
6.乙二醇工艺生产流程图
▽
吸收水
C2H4
CO2
O2
CO2
△
循环气压缩机(离心式)
甲烷、氮气
乙烯20﹪
氧气7﹪
CO2再生塔(填料塔)
吸收水
环氧乙烷解析塔(板式塔)
环氧乙烷再吸收塔(填料塔)
CO2接触塔
环氧乙烷水洗塔
KHCO3
K2CO3
环氧乙烷反应器
三乙二醇产品
环氧乙烷精馏塔(板式塔)
二乙二醇产品
环氧乙烷产品
乙二酸原料汽提塔(填料塔)
乙二醇产品
二乙、三乙二醇精馏塔
乙二醇精馏塔
粗乙二醇储槽
五效蒸发器
乙二酸水合反应器(管式)
乙二醇脱水塔(板式塔)
乙二醇回收塔(板式塔)
三乙、多乙二醇储槽
入口110℃
出口164℃
1.4MPa
二乙、三乙、多乙二醇储槽
乙二醇工艺生产流程图
7.工艺流程说明
7.1.老区裂解炉系统
本装置老区共十一台裂解炉,其中八台六万吨KTI裂解炉(BA—105~BA—111,BA—115),二十万吨裂解炉(BA—113/114)和一台CBL—Ⅲ型裂解炉(BA—112)。
从界区外来的HGO、石脑油、加氢尾油原料分别储存在进料管FB—103R、FB—150N、FB—151R。
石脑油原料经过泵GA—170AN/BN/CN后,在EA—169N中用急冷水(QW)预热后送至裂解炉,HGO原料经过泵GA—101A/B后,先在EA—119中用急冷水(QW)预热后送至裂解炉,加氢尾油原料经过泵GA—117AN/BN后,先在EA—171N中用急冷水(QW)预热,后在EA—170N中用急冷油(QO)加热后送至裂解炉。
加氢尾油进料中需要注入二甲基二硫(DMDS),而石脑油和HGO中含有足够量的硫,不需要再流硫。
从界区外来的丙烷和LPG原料和界区内的循环丙烷汇合后在丙烷/LPG汽化器(FA—181N)中用急冷水(EA—186N)汽化。
从汽化器出来的丙烷/LPG在EA—187N中急冷水过热,注入DMDS后送至裂解炉。
经在冷箱中汽化和过热的循环乙烷经过EA—121BN过热后送至裂解炉。
经预热后裂解原料进入裂解炉对流段,原料预热段预热后与稀释蒸汽按比例混合后,经裂解炉混合后预热段预热至起始反应温度(即横跨温度),进入裂解炉辐射段进行裂解。
裂解气先进入废热锅炉尽快冷却以防止二次反应炉的发生,并回收裂解气的显热,然后进入急冷器用急冷油进一步冷却后送入汽油分馏塔DA—101。
当裂解炉或废热锅炉结焦到一定程度后(由管壁温度、废热锅炉的出口温度及裂解炉管压力降三个主要因素判断),则应停炉进行清焦。
7.2老区急冷部分
从裂解炉TLE出来的裂解气经急冷油冷却,汇合入两个裂解气总管,进入汽油分馏塔DA—101N的两个进料口,BA—106至BA—111和BA—112出口的裂解气进入一个裂解气总管,BA—114的出口裂解气进入另一个裂解气总管。
裂解气在汽油分馏塔中用循环急冷油进一步冷却,至组分通过塔釜采出作为裂解燃料油产品(PFO)产品,较轻的组分通过侧线采出作为裂解柴油(PGO)产品,裂解汽油和更轻的组分在塔顶以气相采出,急冷油带走的热量经过稀释蒸汽压发生系统,工艺水(DM)汽提塔再沸器、对去工艺水汽提塔及稀释蒸汽发生器的工艺水加热进行回收。
汽油分馏塔用在急冷水塔中冷凝下来的汽油作为回流。
汽油分馏塔的PFO和PGO馏分送至燃料油/柴油汽提塔(DA—102N)的两个独立的部分。
PFO用经过第二段TLE(EA—140N)冷却的乙烷炉出口裂解汽提,PGO用低压蒸汽汽提,中压蒸汽式备用汽提蒸汽。
DA—102N的主要功能是控制循环急冷油的黏度,它液控制PGO的闪点。
PFO和PGO产品分别以DA—102N上下塔塔釜采出,分别经泵在EA—123冷却,然后送出界区。
汽油分馏塔塔顶送出的气相在急冷水塔(DA—103N)中与循环急冷水直接逆流接触,被冷却并部分冷凝。
热的急冷水为工艺提供低能热量,如脱乙烷塔再沸器,石脑油/HGO/HVGO/循环乙烷/循环丙烷的进料预热器。
急冷水用冷凝水进一步冷却。
急冷水塔塔顶气相送至裂解气压缩机(GB—201N),在急冷水塔中冷凝下来的汽油在塔釜沉降槽中与急冷水及工艺水分离,冷凝下来的汽油送至汽油分裂