陶瓷烧结概述.docx
《陶瓷烧结概述.docx》由会员分享,可在线阅读,更多相关《陶瓷烧结概述.docx(6页珍藏版)》请在冰豆网上搜索。
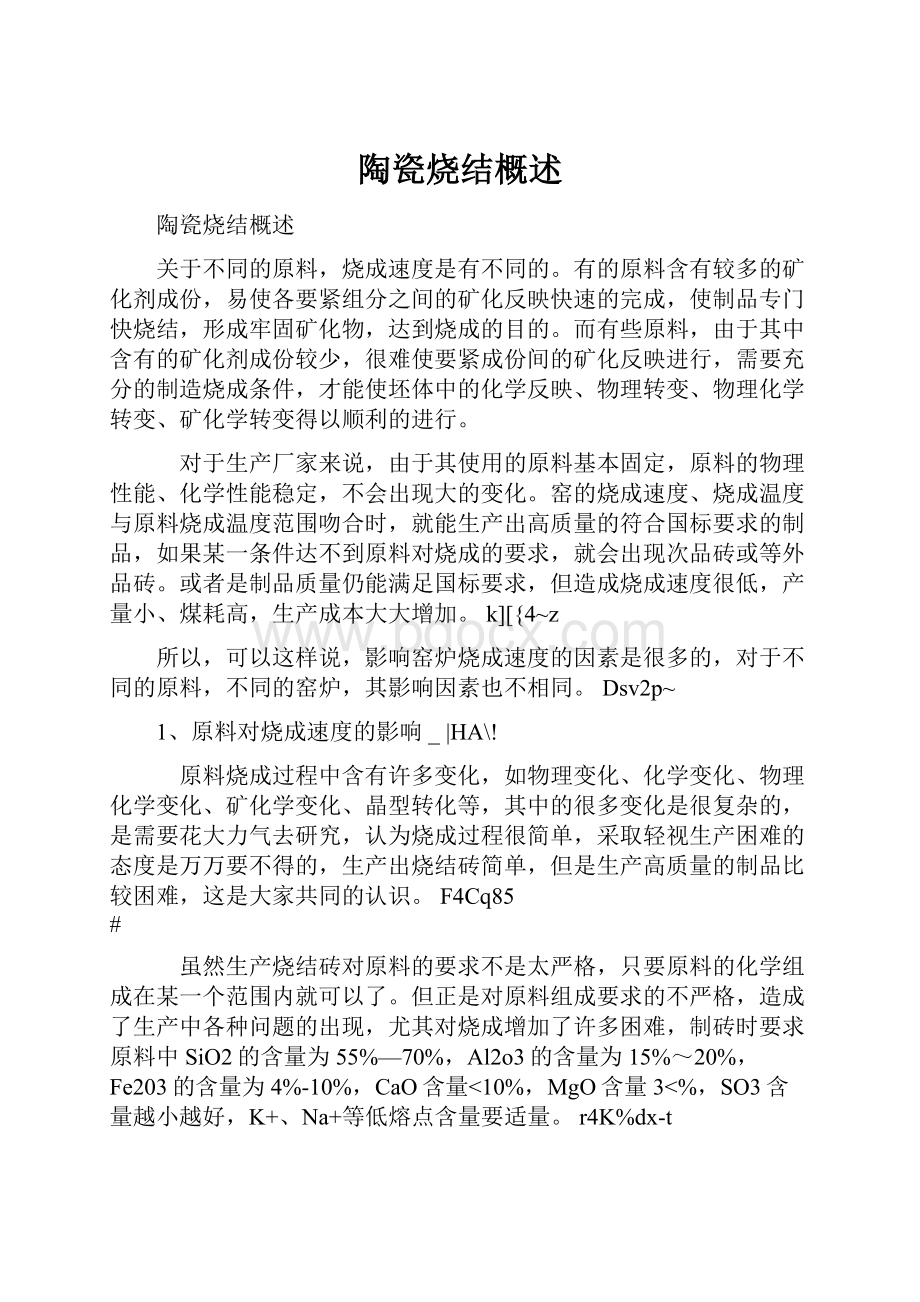
陶瓷烧结概述
陶瓷烧结概述
关于不同的原料,烧成速度是有不同的。
有的原料含有较多的矿化剂成份,易使各要紧组分之间的矿化反映快速的完成,使制品专门快烧结,形成牢固矿化物,达到烧成的目的。
而有些原料,由于其中含有的矿化剂成份较少,很难使要紧成份间的矿化反映进行,需要充分的制造烧成条件,才能使坯体中的化学反映、物理转变、物理化学转变、矿化学转变得以顺利的进行。
对于生产厂家来说,由于其使用的原料基本固定,原料的物理性能、化学性能稳定,不会出现大的变化。
窑的烧成速度、烧成温度与原料烧成温度范围吻合时,就能生产出高质量的符合国标要求的制品,如果某一条件达不到原料对烧成的要求,就会出现次品砖或等外品砖。
或者是制品质量仍能满足国标要求,但造成烧成速度很低,产量小、煤耗高,生产成本大大增加。
k][{4~z
所以,可以这样说,影响窑炉烧成速度的因素是很多的,对于不同的原料,不同的窑炉,其影响因素也不相同。
Dsv2p~
1、原料对烧成速度的影响_|HA\!
原料烧成过程中含有许多变化,如物理变化、化学变化、物理化学变化、矿化学变化、晶型转化等,其中的很多变化是很复杂的,是需要花大力气去研究,认为烧成过程很简单,采取轻视生产困难的态度是万万要不得的,生产出烧结砖简单,但是生产高质量的制品比较困难,这是大家共同的认识。
F4Cq85
#
虽然生产烧结砖对原料的要求不是太严格,只要原料的化学组成在某一个范围内就可以了。
但正是对原料组成要求的不严格,造成了生产中各种问题的出现,尤其对烧成增加了许多困难,制砖时要求原料中SiO2的含量为55%—70%,Al2o3的含量为15%~20%,Fe203的含量为4%-10%,CaO含量<10%,MgO含量3<%,SO3含量越小越好,K+、Na+等低熔点含量要适量。
r4K%dx-t
对于生产厂家的原料来说,如果主要成分在制砖要求含量的范围以内,则会使生产较顺利地进行,如果某种成分超出了原料的要求范围,就要对烧成过程进行相应的调整。
如原料中大颗粒SiO2含量多时,一方面将增加制品的耐火度,提高制品的烧成温度,干燥收缩小、干燥敏感性低起到瘠化剂的作用。
另一方面,由于SiO2在烧成过程中要进行晶型转换,使其体积发生变化,如果控制不好,会造成制品缺陷,降低制品的力学强度,特别是抗折强度。
可是小颗粒的SiO2:
易于熔融,使制品结构均匀、密实,当原料中SiO2含量大于75%时,对制品的烧成过程是不利的。
如果含量超过80%,烧成后制品的体积不但不收缩,反而发生膨胀,使抗折强度大大降低。
与此相反,当原料中SiO2含量小于50%时,则制品抗冻性能很差。
同时,SiO2含量高低,也是影响窑炉烧成速度的主要因素。
AAB_Ytf
虽然Al2O3是耐火度很高的氧化物,它是砖瓦产品中必不可少的组分,它赋予制品一定的力学强度。
当原料中Al2O3,,的含量小于10%时,烧成制品的力学强度较低,提高原料中Al2O3的含量,可使制品的力学强度增加,但烧成温度也将随之升高,燃料消耗量增大,也会影响到窑炉的烧成速度。
HoWK#Nz\
原料中的Fe203,在烧成过程中起到几方面的作用:
①它是一种着色剂,能使制品颜色发生转变,当窑内为氧化气氛时,铁是以高价形式存在,制品呈红色,当窑内为还原性气氛时,铁是以低价形式存在的,制品呈黑色或青蓝色;②大颗粒的铁氧化物在制品烧成中会显现褐色或黑色斑点。
Fe203在烧成进程这几方面的作用,说明Fe203对制品在窑炉中的烧成速度具有必然的阻碍。
G#uB%:
)&0u
原料中的CaO虽然是一种助熔剂,但它不利于制品烧成,表现在:
①含量太高时会缩小原料的烧成温度范围,给烧成带来困难;②会与含铁的矿物化合,使制品的红色取得漂白,而变成黄色或浅黄色;③大颗粒的CaO存在于烧成后的制品中,会产生石灰“爆裂”,阻碍制品强度,乃至使制品失去利用功能。
因此,原料中CaO含量越低越好,若是含量高,那么应将其破碎551mm以下。
烧成时,应适当提高烧成温度,让CaO与其他组分充分结合,达到“死”烧的目的。
这也充分说明了其对窑炉烧成速度的阻碍。
G[OJ 原料中的Sio2颗料较大、含量较高时,应适当提高烧成温度,当原料中SiO2颗粒较小、含量较低时,可适当降低烧成温度。
根据原料中Al2o3与其他组分的结合,提供必要的充分的烧成条件,当原料中Al2O3含量较高时,采用较高的烧成温度,当Al2O3含量较低时,采用适宜的烧成温度,按照CaO含量的多少,制定制品的烧成温度范围。
当CaO含量高时,烧成温度范围要小一些,应注意烧成温度的被动范围不要太大,否则会出现欠火砖或者过火砖。
&/otoAr(
所以,只有当对生产所用的原料有了全面、准确的认识后,就可根据各组分含量的多少,对窑炉烧成速度才有准确的认识。
可根据SiO2晶型转化、发生体积膨胀的规律,控制窑炉烧成的升温速度和冷却的降温速度。
+9<:
z\B|
2、烧成过程的变化对烧成速度的温度j[t2Bp
干坯人窑水分的高低,也是影响烧成速度的重要环节,坯体中的水分在烧成过程中是要被排出窑外的,坯体中含水率的变化会影响窑内预热速度的变化,当坯体中含水率高时,预热就必须在一定的速度下进行,不能太快,太快就会导致坯体开裂。
同时,坯体中残余含水率高时,也会增加预热热耗,提高了窑烧成的能耗。
所以,为了提高窑炉的烧成产量,在干坯进窑时,要准确掌握坯体的含水率,以便于控制预热速度,进窑坯体的残余含水率不应超过6%,而且含水率越低越好。
6bf!
v
坯体在烧成时,依次经过预热、烧成、冷却这三个阶段,烧成速度的快慢是受这三个阶段‘陕慢的影响。
x&EMg!
①在预热时期,坯体先要吸收大量的热量,用于排出其中的干燥残余含水量,坯体吸收热量越多,排出的水量越大,排水速度越快。
在这一时期,由于坯体的干燥收缩已经停止,排水再快,也可不能使坯体产生开裂。
因此,能够加速排水速度,采纳较快的升温速度。
第二,坯体吸收的热量用于本身的加热,使自身的温度慢慢升高,慢慢地接近烧成温度。
在这一升温进程中,由于有SiO2的晶型转化,必需给原料中SiO2组分晶型转化必然的时刻,故在180℃~270℃、573℃、870℃、1000℃时,应严格操纵升温速度,使晶型转化在意隐的进程中进行,专门是在180~170℃、870℃、1000℃时,晶型转化的体积膨胀率别离为2.8%、16%、15%,操纵不行时,很容易使坯体产生开裂。
在其他温度区间,能够快速升温,而可不能阻碍制品质量。
因此,只要注意操纵几个温度点的升温速度,而加速其余温度段的升温速度。
X>]这是影响坯体在窑炉中烧成速度的第一个因素。
{
!
.w}
②烧成时期是坯体中各化学组分在高温下进行猛烈的化学反映、矿化学反映、物理化学反映的进程,从600℃开始、各矿物成份间的反映就比较猛烈地进行了。
在600℃,MgO+Fe203=MgFe204。
生成镁铁矿;在700℃反映,Fe2o3+Sio2→FeO·Si03生成铁橄榄石;在740℃反映,Na2O+Al2o3+Sio2→Na2o·Al2o3·Sio2生成共熔化合物;在800℃反映,Al2o3+Fe2o3→Fe2o3·Al2o3发生反映生成混晶;在900℃下,K20+Fe20+Sio2→K20·Fe2o3io2反映生成共熔化合物。
各类反映在进行中需要大量的能量,因此,必需有充分的热能作保证。
这时窑炉烧成速度的操纵以保证各类化学反映完全进行,生成牢固的共熔物作为操纵速度快慢的依据。
若是窑炉烧成速度太快,其中的转变没有完全进行,那么坯体强度就会较低,质量不符合国家标准要求。
若是窑炉烧成速度太慢,尽管烧成的制品强度高、质优,但产量太低,能耗高,企业没有效益,也就达不到烧成的目的。
只有尽可能的为各组分及时地提供反映所需的条件,达到快速、完全的反映,这是阻碍坯体在窑炉中烧成速度的第二个因素。
I:
MrX
③冷却时期是烧成进程的最后一个时期,它的速度操纵的成功与否,不但关系到窑炉烧成速度的快慢,也关系到产品的质量。
通太高温烧成的坯体,里面有许多高温共熔物,在冷却时期的慢慢冷卸进程中,熔融物从头结晶变成坚硬如石的新物质。
由于砖体中含有未参与反映的游离的SiO2,故在制品冷却进程中,SiO2的品型转化带来的体积转变仍然是操纵窑炉烧成速度必需考虑的问题。
在晶型转化的温度区间和温度点,应严格操纵降温速度,以排除晶型转化产生体积转变对制品的阻碍,其他温度区间实行快速冷却的方式,加速制品的冷却速度,为快速烧成打下坚实的基础,这确实是阻碍坯全在窑炉中烧成速度的第三个因索。
x{rjngp2
通过以上分析,可以肯定地说,只要抓住了窑炉烧成过程中预热、烧成、冷却这三阶段烧成速度的问题,就能很好地实现窑炉烧成速度的控制。
3、隧道窑烧成速度的控制tWTC'Gx-J
在隧道窑的操作中,主要控制的就是三个方面的工作:
一是控制窑内的通风量,包括冷却带的冷却风量,烧成带的通风量,预热带的通风量及排烟量。
二是控制好窑内温度,包括烧成带的最高温度,预热带、冷却带各点的温度。
三是控制好进车速度。
[~n|ROo
控制了窑内的通风量大小,就是控制了预热带的升温速度、冷却带的降温速度)$*B
及维持了烧成带的温度。
制品的烧成过程实际上一个坯体与气体之间的热交换过程,在预热带,热气体将热量传递给坯体,自身温度下降,而坯体被加热,温度升高,窑内通风量越大,流速越高,综合换热系数越大,单位时间换热量越多,坯体升温越快,反之,则坯体升温速度变慢。
在冷却带高温制品与进入窑内的冷空气相遇,制品将热量传递给气体,制品被冷却,而冷空气吸收制品传递的热量后,自身被加热,温度不断上升,窑内通风量越大,制品传递给空气的热量越多,制品被冷却的速度越快。
在烧成带,燃料与空气中的氧结合后,发生氧化反应,并放出大量的热量。
供氧量愈充足,燃料燃烧愈快,但燃料燃烧放出的热量要维持烧成带的高温,仍然需要控制通过烧成带的风量,如果风量太大,就会将热量全部或大部分带往预热带,而对稳定烧成带温度没有意义。
如果风量太小,则燃料燃烧不完全,热量不够,而使温度达不到烧成温度或者是烧成带热量过剩,不能及时排走,而导致烧成带温度急剧上升。
所以。
控制烧成带的通风量时,要注意热量平衡,让燃料燃烧存余在烧成带的热量与维护烧成温度所需的热量相等,这时的通风量,就是窑炉内烧成带所需要达到的风量。
rQTG-&,
控制窑内温度就是要控制各温度控制点的温度及各温度控制区间的温度,让预热带的坯体在加热过程中不至于由于Sio2的晶型转化而产生升温裂纹。
冷却带的制品不会因为冷却速度太快,降温过急而引起SiO2体积发生较大变化,产生冷却裂纹。
烧成带温度控制的要点,就是要保持烧成带的温度始终处于原料烧成温度范围内,使制品中的化学反应一直具有强劲的反应动力。
窑内温度与通风量是有密切关系的,通过调整通风量,可以控制窑内温度,通过窑内温度的高低,可以反应通风量是否适合。
4>Nig.#
控制进车速度是稳定隧道窑各带位置的重要手段,通过进车速度快慢的调节,可以使三带始终处于均衡平衡的应用状态。
如果烧成带后移,那么可以通过减慢进车速度的方法,使烧成带向前移,如果烧成带前移,则应加‘陕进车速度,使烧成带向后移动,回到它应该处于的位置。
在用进车速度控制烧成速度的过程中,应根据窑内温度,配以适当的风量调节手段,这样就能达到控制窑炉烧成速度的目的。
8'v:
26
4、轮窑烧成速度的控制"#U-*Z7
轮窑烧成速度的控制,在原理上与隧道窑一点差别都没有,不同的是两种烧成设备的形式相差较大,一种是被烧物体不动,烧成曲线在随时移动、而另一种则是被烧物体在移动,而烧成曲线始终处于同一位置不发生移动。
表现在控制方面的就是要采取不同的操作手段。
在轮窑的烧成速度控制中,就是要控制好提闸进度、提闸高度和数量、纸挡处理的速度和方式,冷却带打门的速度和方式。
h]VC 控制提闸进度就能控制烧成曲线向前移动的进度,当提闸进度快时,预热带向前移动快,带动烧成带和冷却带电快速地向前移动。
当提闸进度慢时,预热带向前移动缓慢,致使烧成带和冷却带向前移动的速度也缓慢,从而影响烧成曲线向前移动。
)}i2x:
\|_
控制提闸高度和数量,就是控制窑内通风量划、,当提闸高度高、提闸数量多时,窑内通风量就大。
当提闸高度低,提闸数量少时,窑内通风量就小。
提闸高度和数量多少,要根据原料烧成性能确定。
Q}g"pl
纸挡处理的速度要与提闸相配合才能达到处理的目的,只提闸不处理纸挡,等于没有提闸,没有明确的控制目的。
纸挡处理宜采用提纸挡的处理方法。
如果采用燃纸挡或自然纸挡的方法,同样达不到处理纸挡的目的。
冷却带打窑门速度的快慢也决定了窑烧成速度的快慢,以及烧成曲线向前移动的快慢。
窑门多打或大开度增大时,窑冷却带进风量也增大,冷却速度快,反之,则冷却速度慢,烧成速度也慢。
:
e}j$vF
总之,原料的各种性能、正确的控制方法,是影响窑炉烧成速度的主要因素,只要熟悉掌握了原料的各种性能,采用正确的控制方法,就能顺利地进行窑炉烧成速度的控制。