冶金行业DCS硬件集成设计规范研究和设计Word格式文档下载.docx
《冶金行业DCS硬件集成设计规范研究和设计Word格式文档下载.docx》由会员分享,可在线阅读,更多相关《冶金行业DCS硬件集成设计规范研究和设计Word格式文档下载.docx(31页珍藏版)》请在冰豆网上搜索。
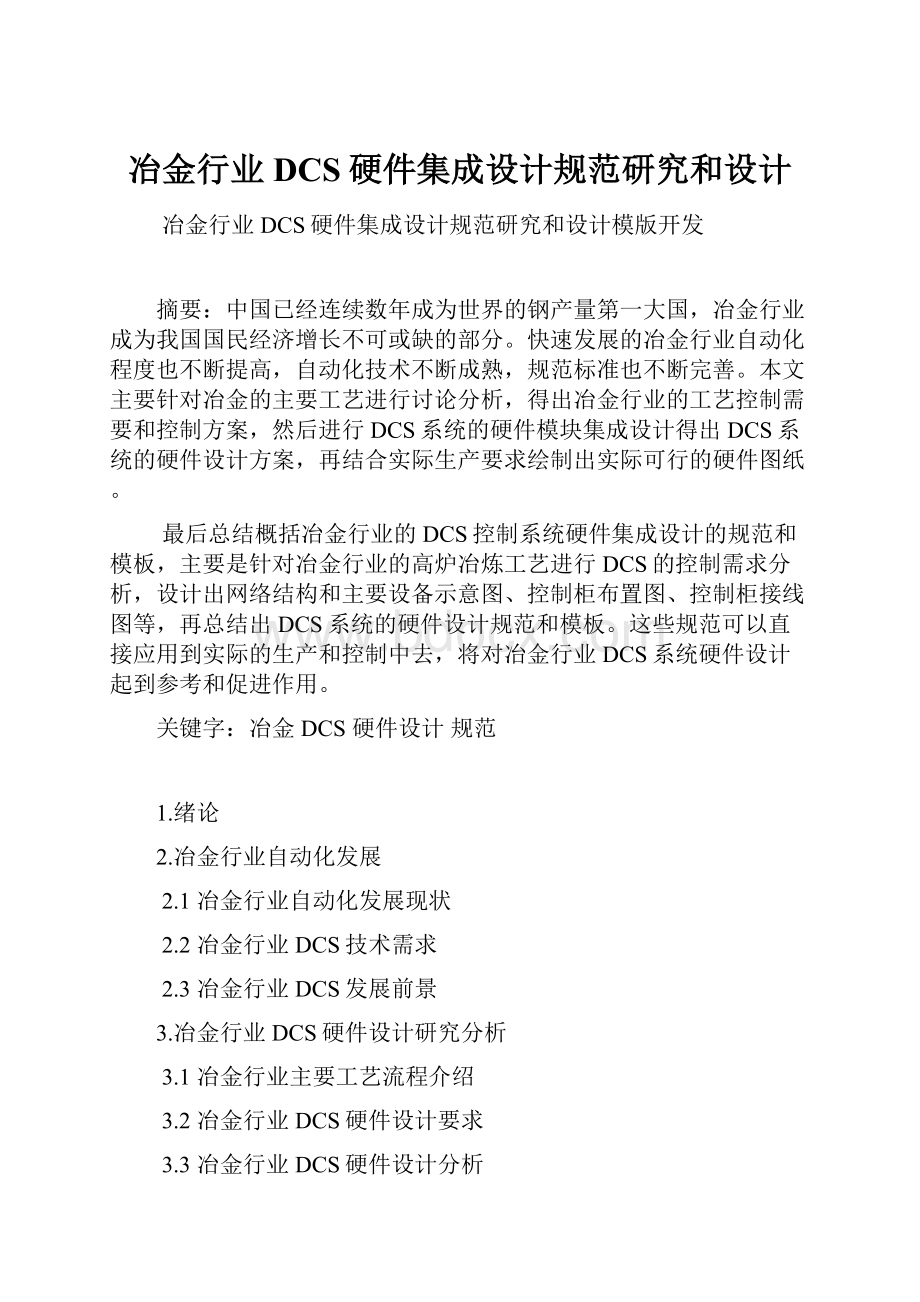
4.1.1机柜设计要求
4.1.2供电电源设计要求
4.1.3机柜布置要求
4.1.4电缆设计要求
4.1.5走线槽设计要求
4.1.6系统标识要求
4.1.7接地设计要求
4.2冶金行业DCS控制柜设计规范
4.2.1网络结构及设备示意图规范
4.2.2DCS控制柜布置图规范
4.2.3DCS控制柜接线图规范
4.3冶金行业DCS硬件设计模板
4.3.1网络结构和机柜设计模板
4.3.2接线柜设计模板
5.结论与展望
1.绪论
现代工业、企业的特点是告诉、连续化、大型化,装置之间、设备之间的联系紧密,特别是为了降低能量小号、提高产品质量和产量,紧靠局部控制的最优化是不够的,迫切需要发展控制理论,大系统理论引入了“分解”和“协调”的设计原理,所谓“分解”就是将一个大系统分解成若干个低级子系统,并解除各系统之间的耦合关系,使它们相互独立,便于使用一般最优控制理论设计局部控制器,使之最优化;
所谓“协调”就是在局部最优的基础上考虑各个子系统之间的耦合关系,设计协调控制器,使整个系统达到最优。
七十年代中期出现的DCS正是4C技术相结合的产物。
它以微型计算机为核心,把数据通信系统、显示操作系统、过程通道和模拟仪表有机地结合妻俩。
运用“分解”和“协调”的设计原理,为综合自动化开辟了广阔的前景。
在冶金生产过程中,过程控制系统完成生产工艺参数的检测、显示、记录、调节、控制、报警等功能,它对生产的产量、质量、安全都起着极其重要的作用。
过程控制系统的特点是对生产过程进行实时控制,控制情况复杂、模拟量参数多且数据变化快,数据处理及贮存量大。
根据过程控制系统的特点及不同的过程实时控制要求,应用不同的工业计算机控制系统才可以既安全可靠又经济高效地完成生产工艺过程控制的任务。
本文主要研究冶金行业的DCS硬件集成设计规范的开发和模板的编写,主要根据冶金行业中高炉冶炼的工艺背景,深入展开分析和讨论,最终得出具有符合实际的DCS硬件集成设计规范和模板。
2.1冶金行业自动化发展现状
冶金生产过程的自动控制包括对采矿、选矿、冶炼、浇铸、轧材等主体生产过程和供水、电、热、氧、气等辅助生产过程的控制。
现代冶金企业采用计算机把生产过程控制和生产管理结合成统一的整体,大大提高了自动化程度。
20世纪50年代在冶金生产过程控制中开始采用顺序控制器和模拟调节器。
60年代英国首先建立全线采用计算机控制的热连轧机。
随着微型计算机的推广,冶金企业已经采用计算机建立完整的计算机控制和管理系统。
在我国冶金自动化及企业信息化系统中,企业资源管理ERP、制造执行系统MES、生产过程控制系统PCS已经建立,并日渐完善和成熟。
目前国内常把冶金自动化系统分为5级,即企业管理级(L4级)、生产控制级(L3级)、过程控制(L2级)、基础自动化级(L1级)、电气和液压传动控制系统(L0级),如图1所示。
纵览冶金企业5级自动化系统,可以看出自动化软件、PLC、DCS、IPC、现场总线、高低压变频、传感器与仪表等动化产品已经应用到冶金生产的多个环节,处处彰显冶金自动化技术应用的价值和发展空间。
实现冶金自动化,可以大大提高劳动生产率和产品质量,减少流动资金的占用,改善劳动条件,获取很高的经济效益。
L0传动级主要完成传动设备本身的控制、I/O控制和管理。
在现代化的控制系统中,变频器、直流调速器、执行机构等传动设备由本体CPU数字装置控制和监视,并与L1级在网进行数据通讯。
L1级基础自动化系统完成冶金轧线、高炉等顺序控制、逻辑控制和设备控制,通常使用PLC、DCS和IPC。
完成炉区、粗轧机、热卷箱、精轧机、液压活套、层流冷却、卷取机、运输机等设备的位置、压力、速度、张力等控制功能。
包括可逆轧制控制、热卷箱控制、飞剪控制、精轧速度控制、液压活套高度及张力控制、液压HAPC控制、精轧液压HAGC控制、终轧温度控制、卷取速度张力控制、液压助卷辊自动踏步控制(AJC)、自动厚度控制(AGC)、自动位置控制(APC)、自动宽度控制(AWC)、板形控制(ASC)、卷取温度控制(CTC)等。
在基础控制方面,以PLC、DCS、IPC为代表的计算机控制取代了常规模拟控制,已在冶金企业全面普及。
L2过程控制级完成过程数据的收集、过程监视、原燃料管理、专家系统数学模型、生产操作指导、数据通讯、历史数据存储和处理、报表打印等功能。
L2过程控制级的核心内容在于各种数学模型,包括:
粗轧模型、精轧模型、板形模型、CTC模型和自学习模型等。
精轧设定模型、卷取温度控制模型、卷取设定模型、板形设定和控制模型、自动宽度控制模型、加热炉自动燃烧控制模型。
一般采用高性能PC服务器担任过程控制计算机,完成模型设定和计算以及自学习功能。
主要功能包括:
板坯初始数据及轧制计划管理、加热炉数据跟踪、轧制节奏计算、设定计算、模拟轧钢和轧辊数据及生产数据管理和历史数据管理,还可以生成班报、日报、工程记录和生产报告(包含质量分类报告)等各种类型的报表。
冶金生产过程自动控制系统如图2所示。
作为企业信息建设的重要组成部分,L3级生产控制级,MES系统包含多种不同的功能。
功能的取舍,取决于特定的工厂环境以及所期望的效益。
冶金企业MES肩负着L2和L4之间的桥梁作用,完成数据交互,进行设备维护管理、生产计划管理功能。
目前从功能上来讲,MES用于信息集成和事务处理的层面多一些,决策支持和动态管理控制作用还没有完全发挥出来。
近年来,冶金企业逐步认识到MES(制造执行系统)的重要性,在综合应用运筹学、专家系统和流程仿真等技术,协调生产线各工序作业,进行全线物流跟踪、质量跟踪控制、成本在线控制、设备预测维护等方面取得了初步成果。
L4级企业管理级,主要用于实现计划管理、质量管理、实绩跟踪、轧辊管理、板方管精整管理、板方管库场管理、发货执行管理、报表及设备状态管理、通讯管理、调度管理等等。
随着企业管理水平的不断提高,“信息化带动工业化”在冶金企业成为共识,企业信息化方兴未艾,受到企业领导高度重视,各企业纷纷开始信息化规划和建设,很多企业已经构造了企业信息网,为企业信息化奠定了良好的基础。
ERP不仅仅涉及MES,甚至和L2级、L1级关系也很大。
水平涉及所有业务流程:
原燃料采购、运输、计量、质检、收货流程,焦化、烧结、炼铁等投料、产出和质检流程,炼钢的投料、产出和质检流程,型棒、线材、中板、卷板等轧钢的投料、产出和质检流程,半成品和产成品的入库、移库、出库、计量、运输等流程;
纵向涉及L0,L1,L2,L3级自动化。
ERP是建立在信息技术基础上,以系统化的管理思想整合企业内部资源,对采购、生产、成本、库存、销售、运输进行计划,从而达到最优及最佳资源组合,为企业提供决策运行手段的管理平台。
2.2冶金行业DCS技术需求
我国已连续9年成为世界钢材产量的第一大国,同时钢材品种、结构调整正在卓有成效地加速进行,冶金自动化也发挥着越来越重要的作用。
回顾我国冶金自动化取得巨大成就的同时,应清楚地看到我们的差距和问题,按照我国走新型工业化道路的要求,结合我国冶金工业发展需求,制订我国冶金自动化技术的战略规划。
冶金自动化技术作为自动化在冶金行业的应用技术,其发展轨迹既遵从自动化学科自身的发展规律,也与钢铁工业的发展,包括工艺路线演化、制造装备的更迭、生产流程和组织方式、企业运营模式的改革和进步等密切关联。
按照目前流行的自动化体系结构,典型的冶金自动化系统按功能层次可分为过程控制系统、生产管理控制系统、企业信息化系统3个层面。
(1)过程控制系统
在基础控制方面,以PLC、DCS、工业控制计算机为代表的计算机控制取代了常规模拟控制,已在冶金企业全面普及。
据最近中国钢铁工业协会的调查结果,按冶金工序划分,计算机控制的采用率分别为高炉100%,转炉95.43%,电炉95.9%,连铸99.42%,轧机99.68%。
近年发展起来的现场总线、工业以太网等技术逐步在冶金自动化系统中应用,分布控制系统结构替代集中控制成为主流。
在控制算法上,回路控制普遍采用PID算法,智能控制、先进控制技术在电炉电极升降控制、连铸结晶器液位控制、加热炉燃烧控制、轧机轧制力控制等方面有了初步应用,取得了一定成果。
在检测方面,与回路控制、安全生产、能源计量等相关的流量、压力、温度、重量等信号的检测仪表的配备比较齐全;
高炉的软熔带形状与位置、高炉炉缸渣铁液位、炼钢过程的熔池钢水含碳量和温度、连续铸钢过程的结晶器钢坯拉漏预报、钢材质量和机械性能预报等软测量技术取得了初步成果。
在电气传动方面,用于节能的交流变频技术普遍采用;
国产大功率交、直流传动装置在轧线上得到成功应用。
在过程建模和优化方面,计算机配置率有较大幅度提高,根据最近中国钢铁工业协会的调查结果,按冶金工序划分,计算机配置率分别为高炉57.54%,转炉56.39%,电炉58.56%,连铸60.08%,轧机74.5%。
但是,应当清醒地看到,过程计算机更多地起到了数据汇总、过程监视和打印综合报表的作用,由于冶金过程的复杂性,数学模型的适应性很差,过程优化方面的功能大打折扣,即使高价从国外引进的过程控制系统充分发挥作用的也不多。
近年来,把工艺知识、数学模型、专家经验和智能技术结合起来,在炼铁、炼钢、连铸、轧钢等典型工位的过程模型和过程优化方面取得了一定的成果,如高炉炼铁过程优化与智能控制系统、有副枪转炉动态数学模型、电炉供电曲线优化、智能钢包精炼炉控制系统、连铸二冷水优化设定、轧机智能过程参数设定等等,但如何保证其长期稳定运行并推广普及还需进一步做工作。
(2)生产管理控制系统
根据最近中国钢铁工业协会的调查结果,按冶金工序划分,生产管理控制系统计算机配置率分别为高炉5.97%,转炉23.03%,电炉26.12%,连铸20.64%,轧机41.68%。
从功能上来讲,信息集成和事务处理的层面多一些,决策支持和动态管理控制作用没有发挥出来。
近年来,冶金企业逐步认识到MES(制造执行系统)的重要性,在综合应用运筹学、专家系统和流程仿真等技术,协调生产线各工序作业,进行全线物流跟踪、质量跟踪控制、成本在线控制、设备预测维护等方面取得了初步成果,但如何真正在冶金企业发挥作用并结合各企业现状进行推广还需做大量细致务实的工作。
(3)企业信息化系统
漆永新在"
解读钢铁企业信息化"
的报告中指出:
“我国钢年产量500万t以上的8家企业100%上了信息化的项目,钢年产量50万t以上的58家企业中有45家上了企业信息化的项目,占77.6%”。
从功能角度讲,企业资源计划(ERP)成为热点,以德国SAP为代表的ERP通用产品和韩国浦项、台湾中钢为代表的定制系统都在冶金企业找到了落脚点。
此外,供应链管理系统(SCM)、客户关系管理(CRM)、企业流程重组(BPR)等概念也被冶金企业所熟悉。
企业信息化工作是企业管理的一场革命,不可能毕其功于一役,需要对其本质意义的深刻理解和方方面面条件的支撑,从观念转变、管理机制变革到信息的上通下达,还有相当长的路要走,才能真正发挥效益,避免掉入信息化投入的“黑洞”。
冶金行业炼铁系统是高炉-转炉流程降低成本和提高环境质量的瓶颈,目前现状和国际炼铁发展目标有相当的差距,要向渣量150~300kg/t、焦比240~300kg/t、喷煤250~300kg/t、风温1250~1300℃、寿命大于20年的21世纪国际先进目标努力。
对自动化技术的需求主要有:
(1)开发更多的专用仪表,特别是直接在线检测质量的仪表,采用数据融合技术;
(2)针对高炉冶炼大滞后系统特点,前馈控制和反馈控制相结合,采用预测控制等先进控制技术;
(3)数学模型、专家系统和可视化技术相结合,保证冶炼过程顺行;
(4)信息技术与系统工程技术相结合,不断优化操作工艺,提高技术性能指标;
(5)应当关注直接还原和熔融还原(HISmelt、Corex、Finex技术)等新一代炼铁生产流程对自动化技术的新需求。
炼钢是钢铁生产的重要工序,对降低生产成本,提高产品质量,扩大产品范围,具有决定性影响:
(1)目前,国内绝大多数钢铁厂(转炉或电炉)均采用人工经验控制炼钢终点,效率低,稳定性差,无法满足洁净钢或高品质钢生产的质量要求,需要完善动态数学模型,并与炉气分析等技术结合,提高炼钢终点的自动控制水平。
(2)炼钢采取了很多综合节能工艺技术,要求针对工艺的变化,建立能量/物料综合优化模型,确定合理化学能输入比例、顶底比例、优化电功率曲线和废钢/铁水比例,以提高冶炼强度,缩短冶炼周期,提高生产效率,达到节能降耗的目的。
(3)铁水预处理和炉外精炼的发展要求建立化学成分、纯净度、钢水温度全线高精度预报模型,并对合金化、造渣、成分调节进行优化控制。
(4)继续优化高效连铸和近终型连铸技术,要求提升电磁连铸自动控制技术;
开发接近凝固温度、高均质、高等轴晶化的优化浇铸技术和铸坯质量保障系统;
同时考虑薄板坯连铸、薄带连铸(Strip-casting)等新工艺的自动化需求。
20世纪轧钢技术取得重大技术进步的主要特征是自动化技术的应用,如计算机自动控制在连轧机上首先应用,使板带材的尺寸精度控制得到了飞跃,AGC的广泛推广应用就是例证,以后的板形自动控制、中厚板的平面形状自动控制、自由规程轧制等,无一不是以计算机为核心的高新技术应用的结果。
今后,轧钢生产工艺流程将更加紧凑,趋于铸轧一体化生产和柔性化生产,对自动化提出新的要求:
(1)要求先进的高精度、多参数在线综合测试技术与高响应速度的控制系统相结合,保证轧钢生产的高精度、高速度以及产品的高质量。
(2)数学模型和人工智能相结合,轧钢工艺控制和管理相结合,实现生产过程的优化和高品质化。
(3)计算力学与数值模拟相结合,由轧制尺寸形状预报和力学模拟转到金属组织性能预报和控制。
(4)扩展控轧控冷技术与"
超级钢"
技术相结合,在自由规程轧制基础上实现真正的柔性化生产,即用同一化学成分的钢坯,在轧机上通过工艺过程参数的控制,生产出不同级别性能的钢材,大大提高轧制效率。
2.3冶金行业DCS发展前景
冶金自动化技术在自动化技术的推动和冶金行业技术需求的拉动的双重机制作用下,必将取得更大进展。
(1)过程控制系统
冶金流程在线连续检测和监控系统。
采用新型传感器技术、光机电一体化技术、软测量技术、数据融合和数据处理技术、冶金环境下可靠性技术,以关键工艺参数闭环控制、物流跟踪、能源平衡控制、环境排放实时控制和产品质量全面过程控制为目标,实现冶金流程在线检测和监控系统,包括铁水、钢水、熔渣成分和温度的检测和预报,钢水纯净度检测和预报,钢坯和钢材的温度、尺寸、组织、缺陷等参数检测和判断,全线废气和烟尘的监测等。
冶金过程关键变量的高性能闭环控制。
基于机理模型、统计分析、预测控制、专家系统、模糊逻辑、神经元网络、支撑矢量机等技术,以过程稳定、提高技术经济指标为目标,在上述关键工艺参数在线连续检测基础上,建立综合模型,采用自适应智能控制机制,实现冶金过程关键变量的高性能闭环控制,包括高炉顺行闭环专家系统、钢水成分和温度闭环控制、铸坯和钢材尺寸及组织性能闭环控制等。
(2)生产管理控制系统
冶金流程的全息集成。
实现铁-钢-轧横向数据集成和相互传递,实现管理-计划-生产-控制纵向信息集成,同时,整合生产实时数据和关系数据库为数据仓库,采用数据挖掘技术,提供生产管理控制的决策支持。
计算机全流程模拟,实现以科学为基础的设计和制造。
采用计算机仿真技术、多媒体技术和计算力学技术,基于各种冶金模型,进行流程离线仿真和在线集成模拟,从而实现生产组织优化、生产流程优化、新生产流程设计和新产品开发。
提升钢铁生产制造智能。
在生产组织管理方面,基于事例推理、专家知识的生产计划与运筹学中网络规则技术,提供快速调整作业计划的手段和能力,以提高生产组织的柔性和敏捷化程度;
根据各工序参数,自动计算各工序的生产顺序计划及各工序的生产时间和等待时间,实现计划的全线跟踪和控制,并能根据现场要求和专家知识,进行灵活的调整;
异常情况下的重组调度技术以及在多种工艺路线情况下,人机协同动态生产调度。
在质量管理方面,基于数据挖掘、统计计算与神经网络分析技术,对产品的质量进行预报、跟踪和分析;
根据生产过程数据和实际数据,判定在生产中发生的品质异常。
在设备管理方面,采用生产设备的故障诊断与预报技术,建立设备故障、寿命预报模型,实现预测维护。
在成本控制方面,采用数据挖掘与预报技术,建立动态成本模型预测生产成本;
利用动态跟踪控制技术,优化原材料的配比、能源介质的供应、产线定修制度、生产的调度管理,动态核算成本,以降低生产成本。
(3)企业信息化系统
企业信息集成到行业信息集成。
信息化的目的之一是实现信息共享,在有效竞争前提下趋利避害,在企业信息系统的编码体系标准化、企业异构数据/信息集成基础上,进一步实现协作制造企业信息集成,全行业信息网络建设及宏观调控信息系统,直至全球行业信息网络建设及宏观调控信息系统。
管控一体化,实现实时性能管理(RealPerformanceManagement)。
协调供产销流程,实现从订货合同到生产计划、制造作业指令、产品入库、出厂发运的信息化。
生产与销售连成一个整体,计划调度和生产控制有机衔接;
质量设计进入制造,质量控制跟踪全程,完善PDCA质量循环体系;
成本管理在线覆盖生产流程,资金控制实时贯穿企业全部业务活动,通过预算、预警、预测等手段,达到控制目的。
知识管理和商业智能。
利用企业信息化积累的海量数据和信息,按照各种不同类型的决策主题分别构造数据仓库,通过在线分析和数据挖掘,实现有关市场、成本、质量等方面数据-信息-知识的递阶演化,并将企业常年管理经验和集体智慧形式化、知识化,为企业持续发展和生产、技术、经营管理各方面创新,奠定坚实的核心知识和规律性的认识基础。
3.1冶金行业主要工艺流程介绍
冶金就是从矿石中提取金属或金属化合物,用各种加工方法将金属制成具有一定性能的金属材料的过程和工艺。
冶金是一门研究如何经济地从矿石或其它原料中提取金属或金属化合物,并用各种加工方法制成具有一定性能的金属材料的科学。
冶金工艺主要分为湿法冶金、火法冶金和电法冶金。
火法冶金是指利用高温从矿石中提取金属或其化合物的方法。
湿法冶金是指利用一些化学溶剂的化学作用,在水溶液或非水溶液中进行包括氧化、还原、中和、水解和络合等反应,对原料、中间产物或二次再生资源中的金属进行提取和分离的冶金过程。
利用电能从矿石或其它原料中提取、回收、精炼金属的冶金过程。
现代钢铁生产流程是将铁矿石在高炉中冶炼成生铁,将铁水注入转炉或电炉冶炼成钢,再将钢水铸成连铸坯或钢锭,经轧制等塑性变形方法加工成各种用途的钢材。
一个钢铁联合企业一般包括原料处理、炼铁、炼钢、轧钢、能源供应、交通运输等生产环节,是一个复杂而庞大的生产体系。
现代炼钢流程图如下图所示。
原料是高炉冶炼的物质基础,精料是高炉操作稳定顺行,获得高产、优质、低耗及长寿的基本保证。
高炉冶炼用的原料主要有铁矿石(天然富矿和人造富矿)、燃料(焦炭与喷吹燃料)、熔剂(石灰石和白云石等)。
冶炼一吨生铁大概需要品位为63%的铁矿石1.60~1.65吨,0.3~0.6吨焦炭,0.2~0.4吨熔剂。
高炉炼铁是以焦炭为能源基础的传统炼铁方法。
它与转炉炼钢相配合,是目前生产钢铁的主要方法。
高炉炼铁的这种主导地位预计在相当长时期之内不会改变。
高炉炼铁的本质是铁的还原过程,即焦炭做燃料和还原剂,在高温下将铁矿石或含铁原料的铁,从氧化物或矿物状态(如Fe2O3、Fe3O4、Fe2SiO4、Fe3O4·
TiO2等)还原为液态生铁。
冶炼过程中,炉料(矿石、熔剂、焦炭)按照确定的比例通过装料设备分批地从炉顶装入炉内。
从下部风口鼓入的高温热风与焦炭发生反应,产生的高温还原性煤气上升,并使炉料加热、还原、熔化、造渣,产生一系列的物理化学变化,最后生成液态渣、铁聚集于炉缸,周期地从高炉排出。
上升过程中,煤气流温度不断降低,成分逐渐变化,最后形成高炉煤气从炉顶排出。
现代钢铁生产流程图如下图所示。
3.2冶金行业DCS硬件设计要求
根据上述的冶金工艺流程可知高炉冶炼钢铁流程一般分为送风系统、渣铁处理系统、喷吹系统、煤气系统、原料系统五部分组成。
(1)送风系统:
风是高炉冶炼过程的物质基础之一,同时又是高炉行程的运动因素。
高炉送风系统是由风机、冷风管道、热风炉、热风管道及相关的各种阀门和烟囱、烟道等所组成。
(2)渣铁处理系统:
渣铁处理系统的任务是将高炉中生成的液态渣铁及时排出炉外。
其主要设备有:
开口机、泥炮、堵渣机、悬臂吊、行车、冲渣系统。
(3)喷吹系统:
高炉喷吹燃料是强化冶炼和降低焦比的有效措施,喷吹的燃料主要有煤粉、重油、天然气等。
高炉冶炼对所喷吹燃料的工艺及设备要求是:
能保证连续、稳定、均匀地喷入炉内;
计量准确、调节灵活;
设备简单、安全可靠。
喷煤工艺由制粉和喷吹两部分组成。
(4)煤气系统:
高炉煤气系统在冶金联合企业中,高炉煤气在燃料平衡中占有重要地位,但高炉煤气含尘量高,必须经除尘处理后才可以使用。
高炉煤气系统的流程是:
炉顶荒煤气→重力除尘器→一级文氏管→二级文氏管(布袋除尘器)→调压阀组→煤气总管。
(5)原料系统:
原料系统是高炉原燃料的供给系统,包括槽上、槽下、上料皮带、炉顶装料设备等组成。
高炉冶炼的示意图如下。
高炉自动化过程主要包含高炉本体控制、上料和炉顶控制、热风炉控制,以及除尘系统控制等。
高炉自动化的目的,主要是保证高炉操作的四个主要问题:
正确配料并以一定的顺序及时装入炉内;
控制炉料均匀下降;
调节炉料分布及保持其与热煤气流的良好接触;
保持高炉整体有合适的热状态。
高炉自动化系统主要包括仪表检测及控制系统、电气控制系统和过程及管理用计算机。
仪表控制系统和电气控制系统通常由DCS或PLC完成。
高炉生产必须要求计算机控制系统能够很好地保证生产过程的连续性和实时监控性,而且要求数据量最多,所有设备的自动化程度要高。
计算机系统要求数据采集周期短,刷新速率快,特别对通讯网络而言,数据传输速率、网络稳定性和正确性尤为重要。
高炉的自动化控制方案,首先应着眼于系统的可靠性、实用性和先进性,