化工工艺设计Word文档下载推荐.docx
《化工工艺设计Word文档下载推荐.docx》由会员分享,可在线阅读,更多相关《化工工艺设计Word文档下载推荐.docx(63页珍藏版)》请在冰豆网上搜索。
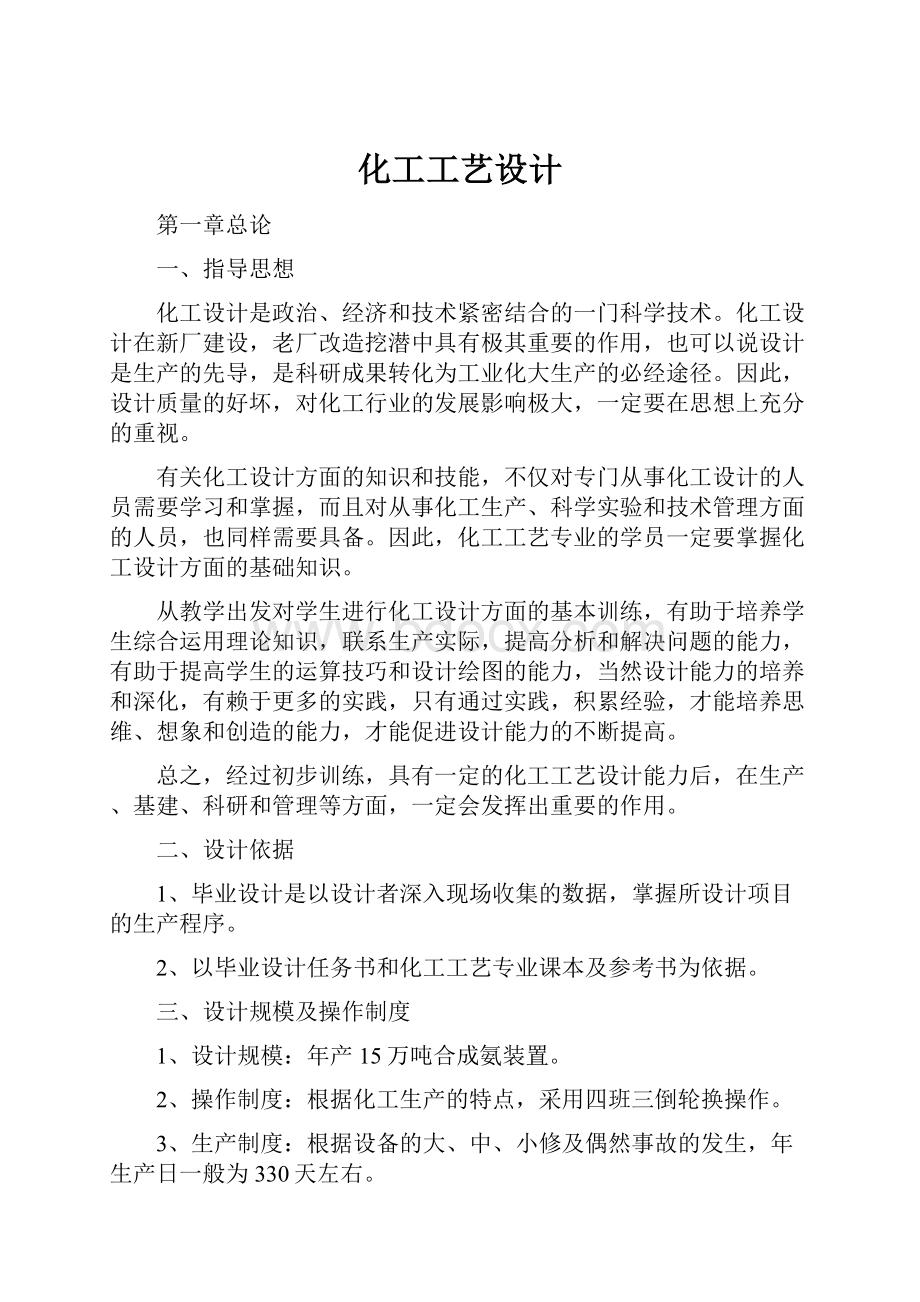
H2=74.63%N2=24.87%(CH4+Ar)=0.5%
2、消耗定额
氢氮混合气:
2800m3∕吨氨
河水:
62吨∕吨氨
锅炉用化学净水:
7.5吨∕吨氨
电:
130千瓦∕小时吨氨
五、辅助原料来源、组成及数量
来源:
来自水、气及其它副产品。
合成氨触媒:
在300大气压、温度475~510℃下合成氨则用氧化
铝与氧化钾为促进剂的融铁触煤。
河水:
供合成系统的水冷却气作用。
水温24℃(夏季)所含之悬浮物,不超过50毫克∕升,在洪水期水中悬浮物达100毫克∕升。
供锅炉房用的化学净水:
于合成系统水冷却器上部的列管中,作冷却气体用。
氨气:
用耐15气压的钢瓶充装,使用时减压力5个气压,供系统置换水冷却器的吹出和局部灭火用,氮气中的氧含量不得超过2%。
润滑油:
供循环压缩机机械部位及气缸部位润滑用的。
机械油:
牌号“”,闪点110℃,粘度50℃时,5.5—6.5恩氏度。
汽缸油:
牌号“T”的汽缸油闪点为240℃,粘度在100℃时2—2.5恩氏度,也可用“C”牌的航空油。
六、产品规格:
氨包括气氨产品占总产量的75%荷叶按产品占总产量的20%,以及将气缸气和吹出气送至硫铵车间所回收的氨产品占总产量的5%。
液氨的品种分两种:
第一类:
水分含量不超过0.2%。
第二类:
水分含量不超过1%,并含有微量的油份。
七、装置组成
1、合成塔
作用:
在高温、高压和催化剂存在的条件下由氢氮气合成氨。
组成:
外筒是一个多层焊接的高压容器,筒体内径为300㎜,高为13600㎜,筒体的两端焊有两个法兰,上部有一密闭式顶盖,下面是一高压盖子,盖子与法兰有螺栓连接,在上法兰之侧有一气体入口,下盖有一气体出口及冷气入口。
在上盖设有安装电炉用的小盖及两个温度计插入管的孔,该筒体最高操作温度为300℃,最高操作压力320个大气压,安装前经过400大气压的压力水压强试验。
触媒筒的内径为690㎜,由钢板焊接而成。
上有触煤筒盖,下有多孔板,在多孔板上放有铁丝网,触煤筒内装油28根双层管,其外管直径为44×
2.5毫升,内管直径为29×
2.5㎜,为造成触煤层上部的绝热层,约在触煤层上部1000㎜处,设有双层管进行冷却,在双层管下端有一分气盒,管内还装有两根温度计套管,在触煤筒多孔板之上,填充的触煤体积约2.1m3,触煤筒中有一中心管,管内装有电热器。
热交换器与触媒筒下部相连,其筒体直径约为680㎜,筒体内装有约900多根直径为14×
2㎜,长约3700㎜的管子,在管间装有隔板,隔板为圆环式,共计27块,整个热交换器面积约为130㎡。
2、冷凝塔:
该塔上部是冷却循环压缩机出来的气体,下部是进行
二次氨的分离,以降低合成塔入口的氨含量。
冷凝塔的外筒是多层焊接的高压容器,在塔底的循环气入口上焊有一个中心管,在塔内上部焊有一个套筒,套筒与高压筒体的间隙用作液面计导压之用,并且套筒还兼作冷交换器的外壳,在塔内的上部装有列管式冷交换器,它有下面一截外壳,上面有一圈法兰线,与高压筒体内的套筒紧密接触,起密封作用。
在下部有分气套筒,由四层圆筒组成,焊接在一块圆板之下,圆板再用螺栓固定在冷交换器之下。
3、快速水冷却器:
该设备是用来冷却从合成塔出来的反应后的高
温气体120—180℃,经冷却后能使气体中氨冷凝为液氨,另外,加热锅炉房用的化学净水,回收一部分热量。
4、氨蒸发器:
该设备的作用是借助于液氨蒸发为氨,将蛇管中的
循环气进一步冷却,使气体中残留的氨冷凝下来,然后到冷凝塔中进行分离。
该设备的外筒是一直径约为2100㎜,高约为3900㎜的直立式焊接而成的圆筒,该设备上有泡沫分离器。
5、滤油器:
该设备用除去循环气和新鲜气中的油份、碳酸铵及其他杂质,以免带入合成塔,使触煤中毒。
该设备的外筒是多层焊接的高压容器,其内径为700㎜,高约
1014㎜,筒体上部的侧面设有一高压盖子,盖子与筒体是用螺栓连
接的以铝垫密封。
该器装有一内筒,内筒的外形尺寸约580×
3900㎜,
内装25×
25×
0.8㎜的铜环0.85m3,在内筒的外面饶有∮25×
2㎜
的钢管呈螺旋形。
在内筒下有几个气体的入口圆洞,内筒在操作过程
中,承受的最高压力差必须小于3.0气压。
6、氨分离器:
该设备外筒是一内径600㎜、高4500㎜的立式多
层的焊接筒体,上有一高压盖子,与筒体用螺栓连接,以铝垫进行密
封。
内筒由四层圆筒组成,圆筒上开有长方形的孔,但各层孔的位置
相错,使气体流动时改变方向,圆筒固定在上面的圆板上,圆板安装
在高压筒体上,圆板的中心有一气体出口。
7、氨水回收器:
该设备用于贮存自氨蒸发器排出来的累积氨水,
和触媒还原时放出的氨水,并在氨水回收器内蒸发出来,送往气氨主
管,把这部分氨回收。
氨水回收器为立式焊接圆筒,它的直径约为1200㎜,高约3500
㎜,容许的最高操作压力为16气压,内设有蒸汽蛇管器的侧面有一
玻璃管液面计。
8、填函气油膨胀器:
该设备用以回收循环压缩机的填函漏处的
气体中所带的油份,气体自器的侧面进,体积突然膨胀,因而流速大
大降低,大部分油份因含有水分及溶解的气体,从油中蒸出,油份则
从器的底部排出。
该设备是立式焊接设备,直径约为1200㎜,高约
为2200㎜,器内填充有钢环,下面有一底座支架。
9、放空槽:
该设备为卧式圆筒,用钢板焊接而成,其直径约为
500㎜,长约1827㎜。
从冷凝塔、氨分离器、油过滤器出口排出来
的气体,都经过放空槽集中后,排入大气。
10、循环气压缩机:
用来把未反应的氢氮混合气自285大气压压
缩到320大气压,重新返回合成塔,使气体循环使用。
该设备是双动
单级的,是由同轴同步电动机带动的,主轴考曲柄的一端支承在机座
的主轴承上,主轴是由碳素钢锻造加工而成。
该设备的润滑分两个系
统,一个是机械油循环润滑泵系统,另一个是汽缸油加压润滑系统。
循环压缩机技术特性如下:
生产能力:
270米3/小时
转速:
125转/分钟
同步电动机容量:
450千瓦
八、生产技术依据,生产步骤及生产方法的选择
1、生产技术依据
《合成氨器、氨的合成》;
《无机化工工艺学》;
《化工工艺设计
概论》;
无机化工专业业设计任务书。
2、生产步骤:
工业上采用的氨合成工艺流程虽然很多,而且流程中设备结构
操作条件也各有差别,但是实现氨合成过程的基本步骤是相同的。
(1)气体的压缩:
为使气体达到氨合成所要求的压力,须将经过精细净化除去所有
有害成分的氢氮混合气经压缩机进行压缩。
当使用往复式压缩机时,部分润滑油在气缸内的高温条件下产生气化,并被气体带出。
因此,在往复式压缩机眉端出口都设有水冷却器和油分离器将气体中的油份除净十分重要,这不仅因为油冷凝后会附着在热交换器壁上,降低传热效率,更重要的是当油随气体带入合成塔,会使催化剂中毒,当油进入合成塔电加热器内时,会使其绝缘不良而引起短路,为避免气体带油,目前已推广往复式压缩机无油润滑,并取得较好效果,使用离心式压缩机从根本上解决了气体带油问题,使生产流程得以简化。
(2)气体的预热和合成:
如前所述,氨合成铁催化剂有一定的活性温度,氢氮混合气体需加热到催化剂的起始温度,才能进行氨合成反应,正常操作的情况下,是反应前的氢氮混合气被反应后的高温气体预热到反应温度后进入催化机床层。
这种换热过程有一部分在催化剂床层中层过换热装置进行。
合成过程中的反应热有很大回收价值,可以直接通过废热锅炉副产品蒸汽,也可加热高压锅炉给水。
因此,在新的氨合成流程中,都没有反应热回收装置。
(3)氨的分离:
进入氨合成塔催化剂床的氢氮混合气,只有一小部分反应生成氨,大部分未反应的氢和氮,同氮混合在一起,流出催化剂床层,混合气体中氨需经过分离才能得到,方法有两种。
a、水吸收法:
用水吸收混合气体中的氨时,由于高压下氨在水中溶解度较大,因而氨的分离比较完全,但分离氨后氢氮混合气体中含有少量水蒸气,在再次利用这部分气体进行合成时,需将水分除去,否则将影响催化剂的活性,用水吸收氨后的产品为浓氨水,如得到液氨产品,需将浓氨水蒸馏。
b、冷凝法:
首先需将出合成塔的高温混合气体冷却、降温,在经气—液分离设备冷凝后获得的液氨即可从氢氮混合气中分离出来。
(4)未反应氢氮气的处理:
为了回收这部份氢氮,工业上有两种处理方法:
a、串联法:
将几个氨合成和氨分离串联起来,出第一合成塔的气体经氨分离后进入第二合成塔,再分离。
b、循环法:
为反应的氢氮混合气,经分离氨后用循环压缩机补足压力,与新鲜的原料气混合,重新进入合成塔进行反应,目前,绝大数的氨合成工艺流程都采用循环法。
(5)惰性气体的排放
如前所述,因制取合成氨原料气所用的原料和净化方法的不同,在新鲜原料气中通常含有一定数量的甲烷和氩,氩气来自空气,新鲜气中氩气与氮气的比例大体和空气中相同,即新鲜气中氩的含量通常在0.3%左右。
采用循环法时,新鲜原料气中的氢和氮会连续不断地合成氨,而惰性气体除一部分溶解于液氨中被带出外,大部分在循环气中积累下来,在工业生产上,为了保持循环气体中惰性气含量不致过高,常采取将一部分含惰性气体较高的循环气体连续获间断地排除氨合成系统的方法。
(即放空的方法)
在氨合成循环系统中,流程中各部位的惰性气体含量是不同的,惰性气体排除的位置应该选择在惰性气体含量最小的地方。
因为这时放空的损失最小,显然,放空的位置应该在氨已大部分分离掉以后,而又在新鲜气加入之前。
放空气中的氨可用吸收法或冷凝法加以回收,其余的气体一般可用作燃料。
分离放空气可采用冷凝、冷却和减压、膨胀降温等方法。
利用深度冷冻过程可以分别得到氢、氮、氩、甲烷,也可以将放空气中甲烷用冷凝方法得到氢氮气,然后将甲烷转化成氢,这样气体回收就比较完全,新鲜气的消耗可大大降低。
3、生产方法
(1)高压法压力700~1000气压温度550~650℃
(2)中压法压力300气压温度500~550℃
(3)抵押法压力70~150气压温度400~450℃
高压法工艺优缺点:
此法是采用较高的操作压力和温度,合成率
比较高,其优点为:
a、与同样产量的中、低压法比较,所用的高压设备的体积小,用料少,节省工厂用地面积。
b、在高压下合成率高,在高压和较高浓度下,容易在混合气体分离,用水冷却后液氨便可以分离出来。
c、电的定额消耗较低,显然因提高压力消耗的电能提高,但氨的合成率增大的更快,所以单位产品的消耗定额降低了。
d、由于合成率高,因此每立方米触媒的生产力也相应增大。
缺点:
a、由于氨的合成率高,所生成的反应热多,可使触媒温度上升到1000℃,在这样的温度下,触媒因过热而损坏,因此触媒的寿命很短,约使用600小时就须换一次。
b、由于采用高压和高温,合成塔及附属设备需要特殊的合金钢制造,不易制作,因此价格很贵,而且检修次数多。
使用日期短,操作管理也比较困难。
低压法工艺的优缺点:
a、所需压力温度低,亚铁氰化钾触媒的活性较大。
b、由于压力低,设备物质要求不高,并且易于制造。
c、触媒对毒害物的灵敏性很大,易受伤害,而且操作中温度不易控制,所以触媒的使用寿命短。
d、再生产过程中,经常有触媒分解物产生,很容易堵塞管道和设备,影响生产正常进行。
e、精制触媒反应热量不能自行维持,反应前必须加热,其热源由合成塔出口高温气体和精致塔出口高温气体供给。
因此,设备与管线的材质要求很高,由于高温高压下氨气对钢材有脱碳作用,因此采用的高温管线易爆炸。
f、由于操作压力低,氨的生成率少,气氨不易液化,需要附设比较庞大的冷冻设备。
中压法工艺的优缺点:
a、所用合成氨触媒对触媒的毒害物灵敏性小,如果在混合气中触媒的毒害物质含量不高,可采用非产品精致塔进行气体精制,进行双循环生产,如果混合气中毒害物含量很少,则可不采用精致塔。
b、混合气不直接进入合成塔,而先与循环气在冷却系统前汇合,经冷却后,油及水分随分离下来的液氨一同排出氨分离器,使油及水份的分离更为彻底,可防止水及油份对触媒的毒害作用。
c、合成系统的热交换器全部放在合成塔内,可以减少脱碳作用而引起的设备及管线的爆炸。
d、中压法所用操作压力较低压法高,因此,循环气中的氨容易分离,所用的冷凝设备也比较小,可不专门设置氨的冷冻系统,即使设置冷冻系统,其冷冻系统的生产能力也可以较低压法小,因此耗电量也随之降低。
e、合成塔的操作温度较高压法低,触媒的灵敏性小,反应时又无触媒分解物生成。
因此触媒的使用寿命长,停车修理的间歇时间长,总产量高。
f、如果精制系统只用作消除杂质和触媒的毒害物,则触媒温度低(350~400℃),氢氮合成为氨的量极少,因此放出的热量甚微,难以经特精致反应所需的温度,必须动用电热器,这样,除了要消耗电能外,有时还因输电系统与线路发生故障,而影响生产。
g、采用双循环时,必须装设喷射器,如果操作不当,也会影响操作的正常进行。
九、对所选择方法的工艺原理、反应机理和催化剂的评述
1、产品的性质、用途
(1)物理性质
①一般物理性质(在温度0℃及压力760毫米汞银柱时):
气体比重0.57%(空气为1)液体比重0.618(水为1)
沸点-33.4℃熔点-77.3℃
临界压力112.3气压临界温度132.5℃
密度0.77溶解度1300升氨/升水,0℃约50%的溶液
②有特殊刺激性臭味的无色气体,对人的粘膜,特别是眼睛刺激更厉害,人只能在含0.03%氨的空气中停留1小时左右。
③加压时易被液化为物色液体,(不纯时为淡黄色或淡蓝色)。
④氨液体呈中性,是碘、磷、硫及其它许多有机、无机化合物的良好溶剂。
⑤溶于水时,放出热量、水溶液成为氨水,其浓度随比重的增大而降低。
⑥蒸汽压力与蒸发潜热。
(2)化学性质
①氨在空气中不能燃烧,在氧气中燃烧,它与氧化合,并有黄绿色火焰,主要反应为:
4NH3+3O2→2N2+6H2O有触媒存在时,氧化过程按下面反应式进行:
4NH3+5O2→4NO+6H2O
②在高温下气态氨分解成氢和氮
2NH3→3H2+N2
③和各种酸化和成盐:
与硝酸作用NH3+HNO3=NH4NO3
与硫酸作用2NH3+H2SO4=(NH4)2SO4
与盐酸作用NH3+HCL=NH4CL
与碳酸作用2NH3+CO2+H2O=2NH4HCO3
(NH4)2CO3+CO2+H2O=2NH4HCO3
④有水存在时氨对铜和铜的化合物有侵蚀性。
⑤在空气中含有13~27%氨时,即产生爆炸。
⑥检定方法:
a、氨气与氯化氢气体时生成白烟。
b、水溶液呈碱性反应。
c、燃烧硫磺时遇氨气生成白烟。
d、微量的氨或其化合物,用纳氏试药可生成褐色沉淀,加量多则色深,加量少则色浅。
(3)产品用途:
氨的用途很广,它是工业上的重要原料,可继续处理变成其它产品。
①液氨本身既是良好的肥料,氨与硫酸、硝酸、盐酸作用生成硫酸铵、硝酸铵、氯化铵,与二氧化碳作用生成碳酸氢铵,在一定温度、压力下生成尿素。
它们都是良好的肥料。
硝酸铵有强烈的爆炸性,可用作矿山爆炸药或用于国防工业。
②用氧化法合成的浓硝酸可用于各种有机化学工业、国防。
③有的用于有机合成,以制造各种氨基化合物,是为各种近代医药及燃料等中间体。
④用于制冷工业,为良好的冷媒质。
⑤用于其它方面。
2、反应原理
反应原理从热力学和动力学两方面考虑。
(1)氨合成的热力学基础
氨合成反应可以用下式表示:
1/2N2+3/2H2=NH3+Q
氨合成反应是一个可逆的放热反应,反应热的数值随反应的温
度、压力而改变,在不同的压力、温度下的反应热可用下式计算:
常压时:
△HR=-9500-4.96T-5.75×
10-4T2+1.7×
10-6T3
△HR=-〔0.54562+846.609/T+459.734×
106〕P-5.34685-0.2525×
10-3+1.69167×
10-6T3-9157.09
上式中的△HR系指纯氢弹混合气完全转化为氨时的热效应,工业生产中合成氨的氢氮原料气中含有甲烷、氩等气体。
同时,合成反应不能进行到底,反应后的气体中含氨一般在20%一下,其余为反应的氢、氮气和不能参加反应的惰性气体,这些气体混合在一起是需要吸收热量,所以表现出来的反应热要比按上式算出的数值小,真正的反应热与混合热之合称为表现反应热,即△HT=△HR+△HM,混合热的数值显然与反应后气体中的氨含量有关,气体中的氨含量越高,混合热越大。
(2)氨合成反应动力学:
氨合成反应和其它可逆放热反应一样,温度对化学平衡与反应速
度有不同影响,即降低温度有利于提高平衡氨浓度,从而提高平衡氨浓度与气相中即时浓度的差值,使合成反应推动力增加,但反应速度常熟降低,提高温度时的情况则正好相反。
为了加速反应而又不过分提高温度,就必须使用催化剂,常用铁催化剂,其中加有其它催化剂:
如三氧化二铝、氧化钾等,催化剂的化学和物理性质对氨合成过程有重大影响。
氨合成过程由下列步骤组成:
a、反应气体混合物中的氢和氮从气相主流扩散到铁催化剂的外表面。
b、氢和氮的绝大部分,自外表面向催化剂的毛细孔内部扩散,进入内表面。
c、氢和氮(分别或同时)被催化剂表面(内表面)活性吸附。
d、吸附状态的气体在催化剂表面上起化学反应,生成一系列中间化合物,最后形成在催化剂表面吸附状态的氨。
e、氨从催化剂表面上吸解。
f、解析后氨从催化剂毛细孔组织内部向外表面扩散。
g、氨由催化剂外表面扩散至气相主流。
以上七个步骤,a、g为外扩散至气相主流,d、f为内扩散过程,c、d、e三步骤总称化学动力学过程。
下面分别进行讨论:
1氨合成的化学动力学机理
当氨合成时的气流速度相当大,催化剂颗粒足够小时,外部和内
部扩的影响都不显著。
这时可以认为氨合成过程处于化学动力学控制区,目前一般认为在铁催化剂表面上氨合成反应机理可能如下:
②、氨合成的动力学方程
根据氮在铁催化剂表面上的活性吸附是氨合成过程的控制步骤,
由捷姆金和佩热夫导出的微分动力学方程如下:
W=
dNNH3/ds=KiPN2(P3H2/P2NH3)2-K2(P2NH3/P3H2)β
此式使用时有一定范围,如当混合气体中的氨的分压为0,或极
小时,就不能运用,因在极限时反应速度将为无限大。
实际上,在远离平衡时,出于氨浓度极低,氮的活性吸附速度比
起吸附以后的氮转变为氨的反应速度来说,已经不是唯一的速度控制步骤,而变为化学吸附和加氢反应两步联合控制。
3、催化剂
触媒就是采用一种能加快反应速度而本身又不起化学变化的物
质,对于氨的合成来说,可以做触媒的物质很多,如铁、铂、锰等,工业上采用的触媒必须能满足活性高,不易中毒,价钱低,易创造的特点,还需耐热性能好,使用寿命长,机械强度大的特点。
因此,国内外目前都采用铁触媒加入各种促进剂的铁催化剂,即:
AL2O3、K2O、CaO、MgO促进剂。
本工段所采用的触媒:
A110—2,A109型铁触媒。
A:
促进剂的作用:
K2O是电子型促进剂,它可以提高催化剂的固有活性,由于它的强碱性,使表面逸出功降低,有利于氮的活性吸附,可提高催化剂活性,氧化铝也属电子型促进剂。
同时CaO能降低固溶体的熔点和粘度,有利于氧化铝和四氧化三铁固溶体的形成,还可以提高催化剂的热稳定性和抗毒害能力。
CaO是成矿剂,即触媒制造过程中,熔融态的铁氧化物粘度较大,加入CaO后可生成CaFeO2,降低熔融物的熔点和粘度,有利于K2O、Al2O3在氧化铁中均匀分布,增加热稳定性。
B、触媒的性能:
氨合成的触媒是一种黑色有金属光泽,带磁性,外观不规则和圆柱形的固体颗粒,氨触媒在合成塔内用氢氮混合气还原,成为活性很高的铁触媒,这对氢氮混合气合成为氨的反应起催化作用,还原过的氨触媒如若暴露在空气中则迅速燃烧失去活性。
C、触媒的选择:
①触媒层的阻力,应在允许阻力降的范围。
②触媒层上部气体质量不好时,易中毒。
2生产后期热点下降。
3触媒层的温度分布,应符合触媒最佳的活性温度范围。
4大颗粒触媒存在内扩散的影响,其活性较小颗粒触媒差。
5触媒颗粒大小的选择,应依据情况而定,一般在阻力降低的
允许范围内尽可能采用较小颗粒的触媒为主。
D、触媒的还原
(1)铁触媒还原反应原理
主要反应:
3FeO3+H2=2Fe3O4+H2O+Q
4Fe3O4+4H2=3Fe+4H2O-Q
触媒还原必须使触媒具有高活性,使全部触媒得到还原切还原彻
底,尽可能缩短还原时间。
(2)还原操作程序
a、升温阶段:
触媒在达到还原温度以前的纯升过程一般为350
℃以下。
b、还原初期:
触媒开始还原反应出水以后,经过摸索,使之进
入正常的大量还原反应出水阶段,一般为350~480℃。
C、还原主期:
长时期大量还原出水阶段,一般为480~515℃。
d、还原末期:
提升触媒底部温度使还原彻底,一般控制热点≤525℃。
e、加负荷阶段,还原已基本结束,缓慢使触媒转入正常生产。
(3)、触媒还原工艺条件
高空速、高氢最后高温,低水汽浓度。
(3)触媒的快速还原
a、以水汽浓度作为主要控制指标(﹤191Nm3)。
b、控制低的同平面温差或同圆柱面温差。
C、还原初期实现四低四高。
d、力争缩短还原主期时间。
e、还原后期力争近似地实现等温还原。
f、采用二次副线。
4、工艺条件选择:
氨合成的工艺条件一般包括压力、温度、空速和合成塔进口气体成份等。
(1)压力
在氨合成过程中,合成压力是决定其它工艺条件的前提,是决定生产强度和技术指标的主要因素。
提高操作压力有利于提高平衡氨含量和氨合成速度,增加装置的生产能力,有利于简化氨分离流程。
但是,压力高时对设备材质及加工制造的技术要求均高,同时,高压下反应温度一般较高,催化剂使用寿命缩短。
总之,可认为30MPa左