航空先进制造技术Word文档格式.docx
《航空先进制造技术Word文档格式.docx》由会员分享,可在线阅读,更多相关《航空先进制造技术Word文档格式.docx(10页珍藏版)》请在冰豆网上搜索。
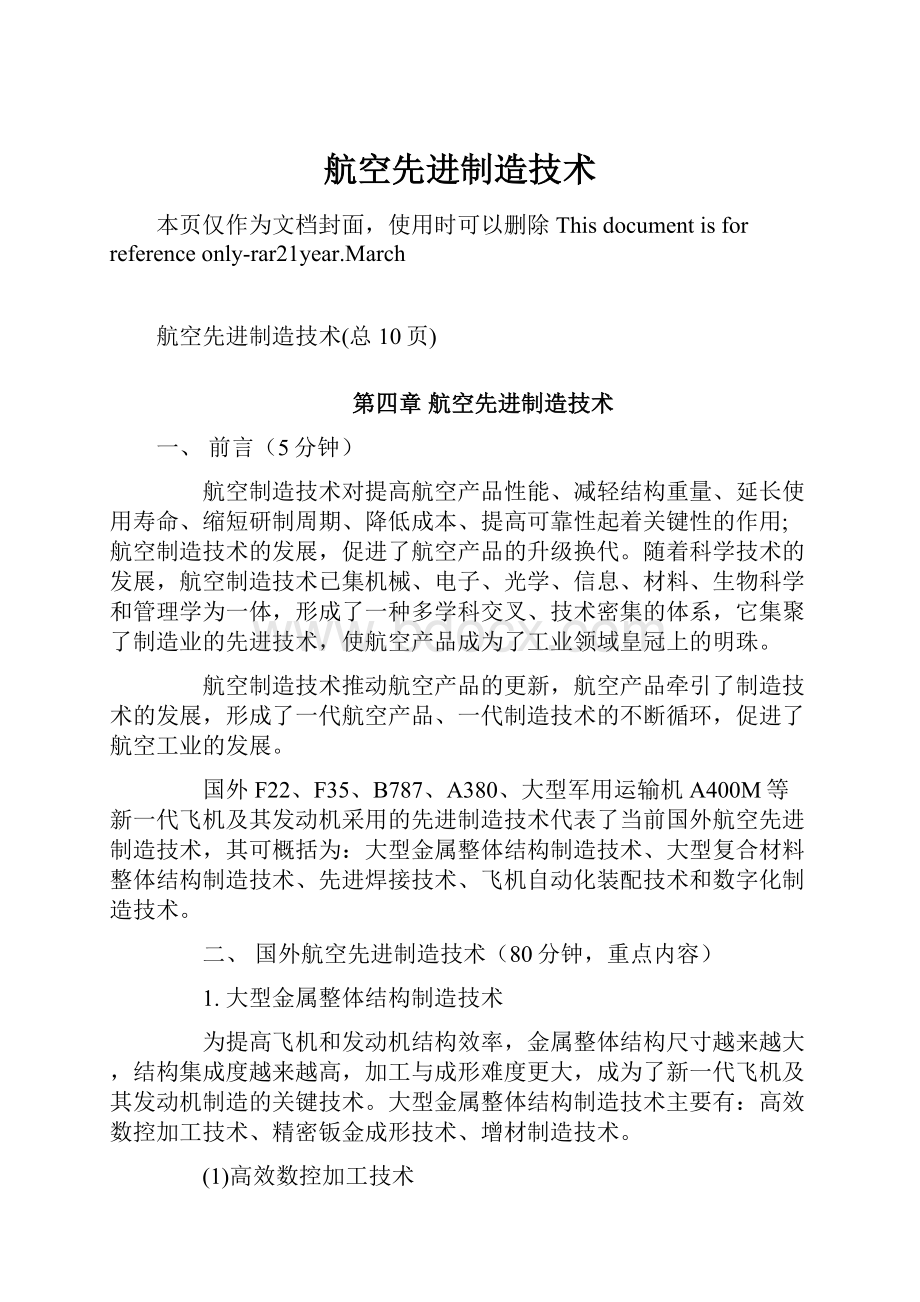
1.大型金属整体结构制造技术
为提高飞机和发动机结构效率,金属整体结构尺寸越来越大,结构集成度越来越高,加工与成形难度更大,成为了新一代飞机及其发动机制造的关键技术。
大型金属整体结构制造技术主要有:
高效数控加工技术、精密钣金成形技术、增材制造技术。
(1)高效数控加工技术
数控加工技术在飞机和发动机金属零件加工中得到广泛应用,由于零件采用难加工材料和结构的大型化整体化,配置先进的数控加工技术和设备十分必要。
国外软件先进、配置完善,形成了以CATIA、UG(NX)、Pro/E等为典型代表的三维CAD/CAM软件环境,开发了以VeriCut为代表的数控加工仿真工具、ICAM为代表的后置处理软件,形成了从三维设计模型到数控程序生成的全三维数据的数字化处理环境和商品化工具。
数控加工技术趋于成熟,设备研制生产能力强,并形成系列化产品。
高速铣削新技术的研究近十年来发展迅速,当前日本Kitamura研制的SPARKCUT600加工中心主轴转速达到150000rpm,代表了高速铣削设备的最先进水平。
数控加工技术发展迅速,在美国JSF项目、欧洲空客A380项目和英国RollRoyce公司发动机项目上得到了广泛应用;
在高速铣削工艺方面的典型应用有:
Remele公司采用转速40000r/min的高速切削设备对壁厚0.76mm的直升机薄壁结构件进行了精确加工。
普惠公司钛合金叶片采用主轴转速为20,000rpm的高速机床加工,生产效率提高15%~20%。
(2)精密钣金成形技术
精密钣金成形技术广泛用于飞机和发动机金属零件制造,它与计算机技术、现代测控技术相结合,构成了金属塑性先进成形技术。
国外金属成型领域广泛采用数字化制造技术。
在工艺仿真研究方面:
根据美国科学研究院的测算,采用工艺仿真能缩短产品研发周期30%~60%,材料利用率提高25%,成本降低5%~20%。
在产品制造中:
实现了工艺过程数字化控制和检测,大幅提高了产品制造精度和生产效率。
数字化应用的典型实例有,柔性多点模具蒙皮拉形工艺,采用了几何信息数字传递方式,作为生成模具型面、拉形过程控制、检测蒙皮外形和蒙皮切边的依据,通过数字化工装,数字化检测和切边工具,实现全过程数字化制造。
精密钣金成形技术在飞机和发动机结构制造中应用的典型技术:
蠕变时效成形技术应用于空客A380飞机机翼上壁板制造,喷丸成形技术应用于空客A380飞机机翼下壁板制造;
超塑成形/扩散连接技术(SPF/DB)应用于美国F-22飞机后机身高强钛合金隔热板、B-2飞机大型钛合金零件和英国RollRoyce发动机大型钛合金宽弦空心风扇叶片等零件制造。
(3)增材制造技术
增材制造技术是一种基于“离散-堆积”成形的先进制造技术,从零件的3D模型出发,通过分层切片及路径规划,离散成加工路径,以激光或电子束等为热源,逐层熔化粉末或丝材,直接制造出任意复杂形状的零件。
增材制造技术是制造技术的最新发展方向。
根据金属增材制造技术用途主要分两类:
第一类是基于电子束、激光束堆焊技术的增材制造技术(快速成形技术),是将快速原型和同步送粉或丝材多层熔覆技术相结合的新技术。
适用于近净成形制造或熔覆修复,对零件还需少量加工;
激光熔覆技术及设备已商业化,典型设备供应商有德国Trumpf和美国POM公司、Huffman公司、Optomec公司等,飞机厂商采用上述几家公司已商业化的技术与设备,生产的产品有金属基叠层复合材料零件、叶片、壁板、梁等构件,但更多用于零件修复。
研究成果已在武装直升机、AIM导弹、波音7X7客机、F/A-18E/F、F22战机等方面得到应用;
美国霍尼韦尔公司采用该项技术修理了上百万件的发动机高压涡轮、中压涡轮和低压涡轮叶片。
在电子束熔丝沉积成形技术方面,美国波音公司、洛克希德•马丁(LockheedMartin)公司与美国航空宇航局Langley研究中心及西雅基(SciakyInc.)公司联合,先后开展了相关技术研究和设备研制,能制造出形状比较复杂的零件,最大沉积速率超3500cm3/h,性能达到锻件水平,譬如F-22飞机钛合金AMAD支座、F-35飞机襟翼梁等,并形成了相关材料及工艺标准。
第二类是基于铺粉的选区熔化精密增材制造技术,适用于零件的净成形制造,无需对零件加工。
该项技术已用于航空产品金属零件制造。
R-R、GE、P&
W、MTU、Boeing、EADS、Airbus等公司应用激光/电子束选区熔化增材成形技术已生产出GH4169、AlSi10Mg、CoCr、TC4等航空金属零部件,如发动机燃烧室、叶片、叶轮、飞机舱门支架、进气罩、B777座舱灯框等。
2.大型复合材料整体结构制造技术
复合材料质量轻、模量高、强度高、可设计性强、工艺性好,更容易制造大型整体结构,倍受飞机和发动机设计师的青睐,得到了广泛应用。
F22、F35、A400M、A380、A350、B787等新型军民用飞机树脂基复合材料用量得到了大幅度提升,B787、A350达到50%以上。
广泛采用的先进制造技术有复合材料自动化制造技术(自动铺带、丝束铺放等)和低成本制造技术(液体成形、拉挤成形以及快速成形技术等),自动铺带技术广泛应用于机翼、翼梁的复合材料结构制造;
丝束自动铺放技术主要应用于机身、机头、翼梁及进气道制造;
液体成形技术用于飞机复合材料后压力框、发动机叶片、机匣等复杂结构件制造;
拉挤成形技术应用于复合材料地板横梁及筋条制造。
碳碳复合材料广泛应用于飞机刹车装置,主要采用化学气相渗透及浸渍/炭化工艺制造。
陶瓷基复合材料已用于X37、X43等高速飞行器的头锥、翼面等承力、隔热及烧蚀结构;
在发动机上广泛应用于F414、M88-II等喷口调节片/密封片等构件,在涡轮叶片、燃烧室隔热屏等构件上的应用处于装机试验阶段。
陶瓷基复合材料主要采用化学气相渗透及先驱体转化工艺制造。
3.先进焊接技术
焊接技术是飞机和发动机结构广泛采用的连接技术。
近年来在飞机和发动机主承力结构上的应用得到了迅速的发展。
先进焊接技术主要有:
电子束焊接、激光焊接、线性摩擦焊和搅拌摩擦焊。
(1)电子束焊接
电子束焊接是在真空环境下采用电子束流对金属结构进行焊接的一种方法,具有焊缝深宽比大的特点,更适用于大厚度结构件的焊接,已广泛应用于飞机、发动机主承力结构的焊接。
利用电子束可达性好的特点,还适用于复杂外形蒙皮及壁板类结构的焊接。
国外著名的研究机构有德国PTR精密技术有限公司、PRO-BEAM公司、英国剑桥真空工程有限公司、TWI焊接研究所、法国的TECHMETA公司和乌克兰的巴顿研究所。
国外在电子束焊接新型材料的焊接冶金特性,气孔、裂纹等缺陷产生的机理和焊接质量控制技术,电子束束流品质的改善和对材料作用机理的基础理论研究,焊接过程温度场、应力场及裂纹生成扩展行为进行了数值仿真模拟等深入研究。
另一方面注重电子束焊接成果在飞机、发动机重要零部件上的应用研究,西方第三、四代战斗机的主承力框、梁结构上广泛采用了电子束焊接技术。
如:
美国F-22飞机钛合金前梁、后机身钛合金梁均采用了电子束焊接技术,其中后机身钛合金梁电子束焊缝长度达87.6m,厚度在6.4~25mm之间,在发动机结构上,A340、A500、A600、A380等大型客机的发动机吊架、Trent700发动机的转子、阿波罗飞船门的框架构件等结构上均采用了电子束焊接技术。
(2)激光焊接
目前,激光焊接采用的光源主要是CO2激光和YAG固体激光。
进入21世纪,以盘式(DISK)激光和光纤激光为代表的高亮度大功率激光技术问世,尤其是光纤激光,其功率已超过了50kW,且束流品质高,能使材料瞬间熔化、气化并形成深穿透匙孔,可实现薄板高效焊接(速度达20m/min)以及20mm以上厚板的高质量焊接,设备体积小可实现大型结构现场移动焊接,当前光纤激光焊接应用研究已成为国际上的热点。
国外在新型高强合金的焊接性、焊接过程质量、应力与变形技术研究,焊接自动化和智能化技术研究,机器人柔性激光焊接技术研究,先进的激光薄壁焊接技术和光纤激光中厚板焊接技术等研究均取得了突破性进展。
英国焊接研究所采用光纤激光填丝和激光电弧复合焊接技术完成了20mm以上厚度的高强钢管道和舰船结构的焊接,英国曼切斯特大学采用长焦距光纤激光焊接和窄间隙光纤激光焊接技术完成了核反应装备上200mm厚板结构的焊接。
2006年美国、加拿大、德国等政府公布科技发展计划中均将激光焊接技术列为航空工业尖端发展技术之一,促进了激光焊接在航空产品上广泛的应用,A380飞机机身铝合金焊接下壁板是激光焊接在航空结构应用上的典型代表。
(3)线性摩擦焊
线性摩擦焊是一项固相连接技术,焊缝能达到锻造组织的状态;
可实现同种或异种材料的连接;
已用于叶片与叶盘的焊接及修复。
国外在完成了深入的基础理论和应用技术研究后,MTU公司与罗罗公司合作,把线性摩擦焊用于欧洲战斗机Typhoon的发动机3级低压压气机整体叶盘的制造,目前已经提供了100多个线性摩擦焊接的整体叶盘。
F119发动机的风扇和压气机1~2级均采用了线性摩擦焊整体叶盘结构。
其中风扇是采用宽弦空心叶片结构。
F135发动机的升力风扇以及一、二级风扇(为空心叶片)也是采用了线性摩擦焊整体叶盘。
F136发动机3级整体叶盘全部采用罗罗公司生产的线性摩擦焊接,并开展了采用线性摩擦焊技术维修与更换整体叶盘零件的探索研究。
此外,日本开展的一项小型民机飞机发动机的研究计划中,其高压压气机整体叶盘采用了线性摩擦焊制造。
美国波音787客机的发动机叶盘也采用了线性摩擦焊整体叶盘结构。
(4)搅拌摩擦焊
搅拌摩擦焊1991年由英国焊接研究所发明,其原理是通过搅拌头与被焊金属材料的摩擦搅拌产生热能,使金属塑化并形成固相连接,适用于铝合金、镁合金、钛合金等轻质合金和钢材的
焊接,在航空工业主要应用于飞机机体结构制造。
以空客、波音、洛克希德•马丁等公司为代表的研究机构,多年来持续开展飞机结构搅拌摩擦焊基础理论、工程技术和综合验证研究,并应用于飞机生产。
具有代表性的研究工作有:
空客公司针对A340-600型大型民用客机翼肋及A350机身纵缝焊接,开展了搅拌摩擦焊试验验证研究,巴西Embracer公司针对Legacy-450及Legacy-500中型客机机身壁板,开展了搅拌摩擦焊工艺及结构强度性能研究。
具有代表性的应用结构有:
美国大型军用运输机C-17的舱内地板和斜台地板;
C-130J压力舱壁板、地板及隔板;
Eclipse-500型商务飞机蒙皮、翼肋、弦状支撑和舱内地板。
5.飞机自动化装配技术
飞机自动化装配是指从组合件、盒段件及部件对合装配机械连接工艺采用自动化、数字化技术,实现飞机装配全过程的自动化;
柔性装配是自动化装配发展的一个新方向。
自动化装配技术中的柔性装配技术得到了迅速的发展,Gemcor、Brotje、EI、Mtorres、ATI、SERRA、DULL、BC、柯马等公司研制出各类工装单元、加工单元、检测单元及集成系统,实现了模块化、通用化,降低了制造成本,缩短了生产准备周期;
集成的柔性装配生产线有:
壁板、翼梁等组合件装配线;
机身舱段、翼盒等盒段大部件装配线;
机翼对接、机身舱段对接、翼身对接等大部件对接装配线;
部件总装、全机移动总装生产线。
实现了从组合件级、盒段级、大部件对接、部件总装至全机移动生产线全线贯通的高度柔性化和自动化装配,广泛地应用于F-22、F-35、B787、A380、A400M、A350等新一代飞机装配。
大幅提升了产品的装配精度、实现了低应力装配。
波音、空客、洛克希德•
马丁等飞机制造公司在波音系列民机、F-35及A380等飞机的总装生产线中,为了满足飞机的快速生产需求,降低装配成本,吸取了汽车行业流水生产线的理念,变革传统的批量装配生产方式变为单件流拉动式生产方式,在总装中采用了移动生产线,大大缩短了飞机总装时间,降低了飞机的成本,提高了装配质量。
在飞机装配过程中,移动生产线技术是当前应用的新技术,采用移动生产线技术能提高生产效率,节省车间空间,在F-35飞机研制中,洛克希德•马丁公司将首次采用连续移动装配线。
波音、空客等公司,还大量采用了气垫运输和自动运输小车(AGV)技术,与先进的测量与定位技术(iGPS)、数控技术结合,实现飞机制造过程中运输和装配自动化,大大提高了飞机制造与装配的技术水平、工作效率和装配质量。
6.数字化制造技术
数字化制造是一种全新的制造技术体系,在数字化制造过程中,从产品设计到最终产品,数字化的信息贯穿始终。
在优化的数字化工艺导引、快捷的数字化执行系统驱动以及高性能数字化装备支持下,生产系统灵活、准确、高效率地运转,并以最佳的质量和最短的周期提供最终产品。
在航空企业应用数字化制造技术将大幅提升产品制造。
波音、空客公司在新机研制中采用信息化和数字化平台,将B787、A380、F35等机型的研制从设计到生产过程实现市场化、全球化。
实现产品全寿命周期管理(PLM技术):
产品的开发管理实现所有产品/项目/技术状态的数据进行集中、统一、分类和可视化管理;
产品的数据管理扩展至维护和维修阶段,实现全寿命周期管理。
实现全球性协同:
打通壁垒,实现数据积累、共享和管理产品信息传输渠道,从企业内部的交互式工作方式过渡到全球协同。
实现产品开发仿真:
建立了较完善的从设计、测试、制造到虚拟企业的产品开发虚拟环境,B787采用这项技术实现了无物理样机的目标;
发展以计算流体力学CFD、计算结构力学CSD为核心的数值仿真软件,提高发动机的设计预测能力。
数字化技术在发动机应用:
罗罗等发动机公司发展了集测量、控制、处理、管理为一体的试验信息系统,增强了发动机试验验证能力。
三、结束语(5分钟)
21世纪航空产品更新换代速度加快以及人类对绿色制造技术提出了新的需求,全球航空制造技术进入了高速发展时期。
近年来我国对航空产品的需求急剧增长,促进了航空制造业快速发展,大幅提升了航空先进制造技术水平,我国将迅速进入航空制造强国行列,参与全球航空产品市场竞争。