SMT不良缺陷.docx
《SMT不良缺陷.docx》由会员分享,可在线阅读,更多相关《SMT不良缺陷.docx(60页珍藏版)》请在冰豆网上搜索。
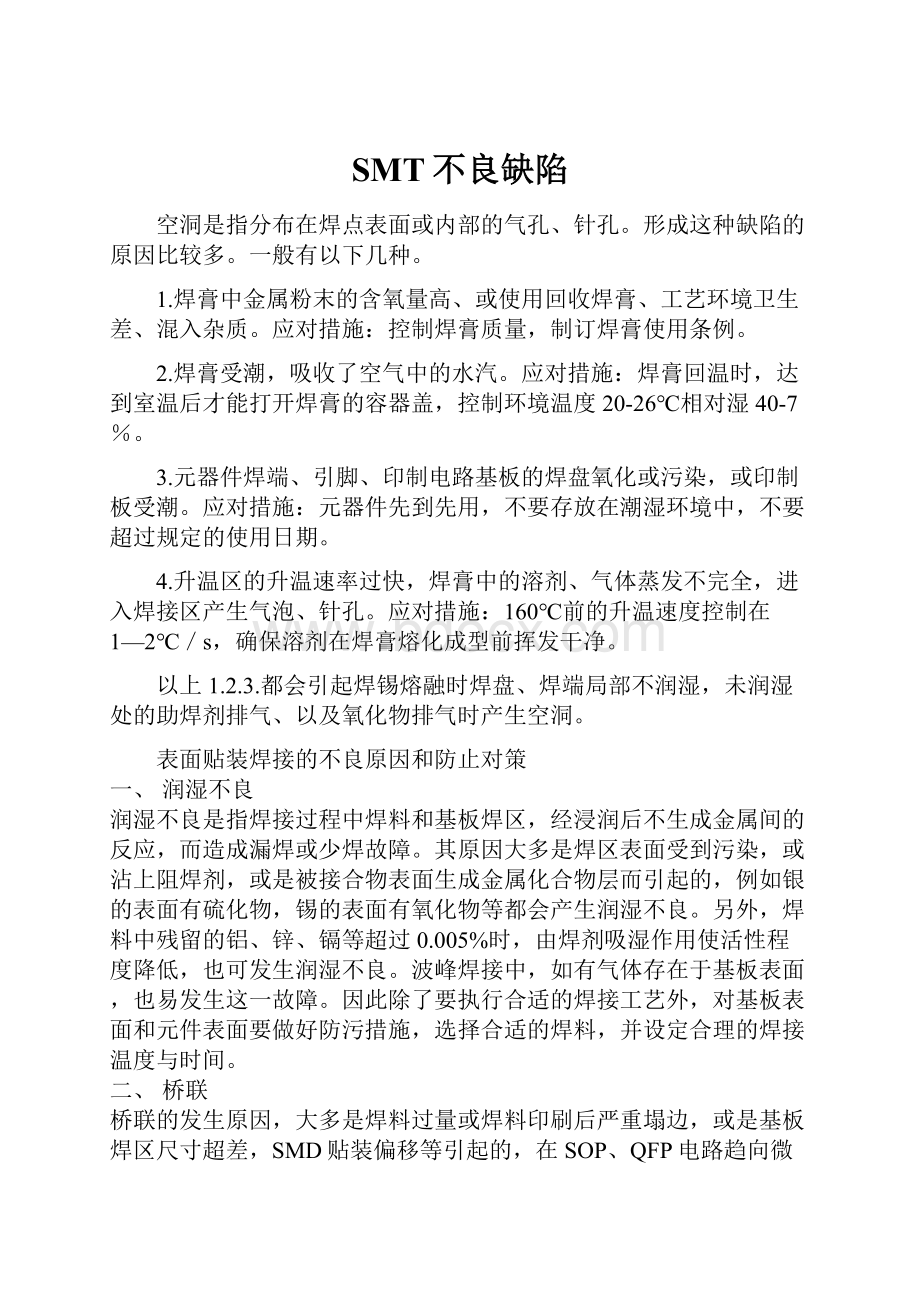
SMT不良缺陷
空洞是指分布在焊点表面或内部的气孔、针孔。
形成这种缺陷的原因比较多。
一般有以下几种。
1.焊膏中金属粉末的含氧量高、或使用回收焊膏、工艺环境卫生差、混入杂质。
应对措施:
控制焊膏质量,制订焊膏使用条例。
2.焊膏受潮,吸收了空气中的水汽。
应对措施:
焊膏回温时,达到室温后才能打开焊膏的容器盖,控制环境温度20-26℃相对湿40-7%。
3.元器件焊端、引脚、印制电路基板的焊盘氧化或污染,或印制板受潮。
应对措施:
元器件先到先用,不要存放在潮湿环境中,不要超过规定的使用日期。
4.升温区的升温速率过快,焊膏中的溶剂、气体蒸发不完全,进入焊接区产生气泡、针孔。
应对措施:
160℃前的升温速度控制在1—2℃/s,确保溶剂在焊膏熔化成型前挥发干净。
以上1.2.3.都会引起焊锡熔融时焊盘、焊端局部不润湿,未润湿处的助焊剂排气、以及氧化物排气时产生空洞。
表面贴装焊接的不良原因和防止对策
一、润湿不良
润湿不良是指焊接过程中焊料和基板焊区,经浸润后不生成金属间的反应,而造成漏焊或少焊故障。
其原因大多是焊区表面受到污染,或沾上阻焊剂,或是被接合物表面生成金属化合物层而引起的,例如银的表面有硫化物,锡的表面有氧化物等都会产生润湿不良。
另外,焊料中残留的铝、锌、镉等超过0.005%时,由焊剂吸湿作用使活性程度降低,也可发生润湿不良。
波峰焊接中,如有气体存在于基板表面,也易发生这一故障。
因此除了要执行合适的焊接工艺外,对基板表面和元件表面要做好防污措施,选择合适的焊料,并设定合理的焊接温度与时间。
二、桥联
桥联的发生原因,大多是焊料过量或焊料印刷后严重塌边,或是基板焊区尺寸超差,SMD贴装偏移等引起的,在SOP、QFP电路趋向微细化阶段,桥联会造成电气短路,影响产品使用。
作为改正措施:
1、要防止焊膏印刷时塌边不良。
2、基板焊区的尺寸设定要符合设计要求。
3、SMD的贴装位置要在规定的范围内。
4、基板布线间隙,阻焊剂的涂敷精度,都必须符合规定要求。
5、制订合适的焊接工艺参数,防止焊机传送带的机械性振动。
三、裂纹
焊接PCB在刚脱离焊区时,由于焊料和被接合件的热膨胀差异,在急冷或急热作用下,因凝固应力或收缩应力的影响,会使SMD基本产生微裂,焊接后的PCB,在冲切、运输过程中,也必须减少对SMD的冲击应力。
弯曲应力。
表面贴装产品在设计时,就应考虑到缩小热膨胀的差距,正确设定加热等条件和冷却条件。
选用延展性良好的焊料。
四、焊料球
焊料球的产生多发生在焊接过程中的加热急速而使焊料飞散所致,另外与焊料的印刷错位,塌边。
污染等也有关系。
防止对策:
1.避免焊接加热中的过急不良,按设定的升温工艺进行焊接。
2.对焊料的印刷塌边,错位等不良品要删除。
3.焊膏的使用要符合要求,无吸湿不良。
4.按照焊接类型实施相应的预热工艺。
五、吊桥(曼哈顿)
吊桥不良是指元器件的一端离开焊区而向上方斜立或直立,产生的原因是加热速度过快,加热方向不均衡,焊膏的选择问题,焊接前的预热,以及焊区尺寸,SMD本身形状,润湿性有关。
防止对策:
1.SMD的保管要符合要求
2.基板焊区长度的尺寸要适当制定。
3.减少焊料熔融时对SMD端部产生的表面张力。
4.焊料的印刷厚度尺寸要设定正确。
5.采取合理的预热方式,实现焊接时的均匀加热。
表面贴片技术指南
第一步为制造着想的产品设计(DFM,DesignforManufacture)
虽然对DFM有各种的定义,但有一个基本点是为大家所认同的,那就是在新产品开发的构思阶段,DFM就必须有具体表现,以求在产品制造的阶段,以最短的周期、最低的成本,达到尽可能高的产量。
第二步工艺流程的控制
随着作为销售市场上具有战略地位的英特网和电子商务的迅猛发展,OEM面临一个日趋激烈的竞争形势,产品开发和到位市场的时机正在戏剧性的缩短,边际利润的压力事实上已有增加。
同时合约加工商(CM)发现客户要求在增加:
生产必须具有资格并持有执照,产品上的电子元件必需有效用和有可追溯性。
这样,文件的存档已成为必不可少的了。
第三步焊接材料
理解锡膏及其如何工作,将对SMT过程的相互作用有更好的了解。
适当的评估技术用来保证与锡膏相联系的生产线的最佳表现。
第四步丝印
在表面贴片装配的回流焊接中,锡膏是元件引脚或端点和电路板上焊盘之间的连接介质。
除了锡膏本身之外,丝印之中有各种因素,包括丝印机,丝印方法和丝印过程的各个参数。
其中丝印过程是重点。
第五步黏合剂/环氧胶及滴胶
必须明确规定黏合剂的稠密度、良好的胶点轮廓、良好的湿态和固化强度、胶点大小。
使用CAD或其它方法来告诉自动设备在什么地方滴胶点。
滴胶设备必需有适当的精度、速度和可重复性,以达到应用成本的平衡。
一些典型的滴胶问题必须在工艺设计时预计到。
第六步贴放元件
今天的表面贴片设备不仅要能够准确贴放各种元件,而且要能够处理日益变小的元件包装。
设备必须保持其机动性,来适应可能变成电子包装主流的新元件。
设备使用者-OEM和CM-正面临激动人心的时刻,成功的关键在于贴片设备供应商满足顾客要求和在最短的时间内提交产品的能力。
第七步焊接
批量回流焊接,过程参数控制,回流温度曲线的效果,氮气保护回流,温度测量和回流温度曲线优化。
第八步清洗
清洗时常被描述成“非增值”过程,但这样现实吗?
或者是太过简化,以致于阻碍了对复杂事物的仔细思考。
没有可靠的产品和最低的成本,一个公司在今天的环球经济中无以生存。
因此制造过程中的每一步都必须经过仔细检查以确保其有助于整个成功。
第九步测试/检查
选择测试和检查的策略是基于板的复杂性,包括许多方面:
表面贴片或通孔插件,单面或双面,元件数量(包括密脚),焊点,电气与外观特性,这里,重点集中在元件与焊点数量。
第十步返工与修理
不把返工看作“必须的不幸”,开明的管理者明白,正确的工具和改进的技术员培训的结合,可使返工成为整个装配工序中一个高效和有经济效益的步骤。
减少溅锡
线性温升曲线,没有保温平台区,对任何焊锡和助焊剂材料都造成一些溅锡
图三、有一个高温保温区的温度曲线,溶剂的消失提高余下的助焊剂粘性,因此减少溅锡
所有温度曲线研究的结果在图四和表六中总结。
光板上测得的飞溅程度,在已贴装元件的生产板上大大减少。
估计表明,光板上少于10-20个飞溅锡球,将在贴装元件板上不产生飞溅。
因此,助焊剂类型D,E和F(表五)都提供了可行的溅锡解决方案。
D型助焊剂载体有其它有点,工艺范围大和可以空气回流。
三种材料的特点都是熔湿速度慢,但溶剂种类不同,这显示所有溶剂都可以有效烘干,熔湿速度才是助焊剂飞溅的关键因素。
每一种材料在内存模块六合一板上的飞溅结果。
Series1:
平坦、滞色的助焊剂小滴数量
Series2:
有形、光泽的助焊剂小滴数量
助焊剂A:
Kester244;B:
92;C:
92J;D:
51SC;E:
73D;F:
75
检查与清洁
如果在清洁的连接器内产生溅锡,那么检查和清洁是对溅锡的昂贵和费时的改正行动。
当然,通过锡膏残留中配方的变化,检查可以通过染色和荧光化学品来简化。
清洁也可以用适当的残留构思来改进。
不幸的是,和预防措施一样,成本和时间使得检查和清洁是人们所不希望的。
结论
锡膏结合正确的温度曲线,可以达到实际消除焊锡和助焊剂的飞溅。
相对易挥发溶剂含量高和熔湿速度慢的锡膏可达到最好的效果。
遮盖连接器手指和检查与清洁可提供临时的解决办法,但没有找到溅锡的根本原因。
溶剂排气模拟
测试描述材料结果
助焊剂载体(无粉末)印于铜箔试样,放于设定为190°C、200°C和220°C的热板上
助焊剂载体B
助焊剂载体D
在试样上没有明显的助焊剂飞溅,第二次结果相似
将锡膏印于铜箔试样,放于设定为190°C、200°C和220°C的热板上回流
锡膏B:
90%金属含量,Sn63/Pb37,-325/+500
锡膏D:
92%金属含量,Sn63/Pb37,-325/+500
两种金属含量都可以看到助焊剂飞溅,金属含量较高的产生飞溅可能较少,但很难说。
第二次结果相似
助焊剂A:
Kester244,助焊剂B:
92,助焊剂C:
92J,助焊剂D:
51SC,助焊剂E:
73D,助焊剂F:
75
表二、从金属焊接中的助焊剂飞溅模拟试验
测试描述材料结果
锡膏(有粉末)印于铜箔试样,放于设定为190°C、200°C和220°C的热板上
锡膏B,90%,Sn63/Pb37,-325/+500
锡膏D,90%,Sn63/Pb37,-325/+500
在所有温度设定上,锡膏B明显比锡膏D湿润较快,结合更积极,结果助焊剂飞溅较多
也看到锡膏D在所有温度上的助焊剂飞溅,但比锡膏程度要小
温度越高,飞溅越厉害
保温区(干燥)模拟--锡膏印于铜箔试样,在设定不同的温度热板上预热不同的时间,保温范围150°C~170°C,时间1~4分钟。
试样然后转到第二块热板上,以220°C回流,并观察助焊剂飞溅。
锡膏B,90%,Sn63/Pb37,-325/+500
在较高温度下保温超过2分钟,减少或消除了助焊剂飞溅
Sn62的锡膏和Sn63的锡膏比较,看是否Sn62较慢的结合速度会减少飞溅
锡膏B:
90%金属含量,Sn63/Pb37,-325/+500
锡膏B:
90%,Sn62/Pb36/Ag2,-325/+500
Sn62和Sn63都观察到助焊剂飞溅,飞溅数量的差别肉眼观察不出,观察到Sn62的结合速度较慢
助焊剂A:
Kester244,助焊剂B:
92,助焊剂C:
92J,助焊剂D:
51SC,助焊剂E:
73D,助焊剂F:
75
可以推断,如果助焊剂沸腾引起飞溅,那么当助焊剂单独加热时应该看到。
可是,由于飞溅是在焊锡结合时观察到的,这里应该可找到其作用原理。
测试说明溶剂排气理论不能解释助焊剂飞溅。
结合理论:
当焊锡熔化和结合时熔化材料的表面张力―一个很大的力量―在被夹住的助焊剂上施加压力,当足够大时,猛烈地排出。
这一理论得到了对BGA装配内焊锡空洞的研究的支持,其中描述了表面张力和助焊剂排气之间的联系(助焊剂排气率模型)。
因此,有力的喷出是助焊剂飞溅最可能的原因。
接下来的实验室助焊剂飞溅模拟说明了结合的影响,甚至当锡膏在回流前已烘干。
尽管如此,完全的烘干大大地减少了飞溅(表三)。
表三、来自金属结合的助焊剂飞溅模拟―烘干研究
温度一分钟二分钟三分钟四分钟150oC
观察到飞溅1-2飞溅无飞溅飞溅160oC1-2飞溅无飞溅飞溅无飞溅
170oC无飞溅无飞溅无飞溅无飞溅用锡膏B90%Sn63/Pb37合金作试验
熔湿速度
因为结合模型看来会成功,所以调查了各种材料的熔湿速度。
熔湿速度受合金类型、温度、助焊剂载体和回流环境的影响。
如图一所说明,温度对熔湿速度有戏剧性的影响,温度越高,速度越快。
图一、一种焊锡配方在不同温度测试的熔湿速度,影响因素包括合金类型、温度、助焊剂载体和回流环境。
李宁成博士在其论文,“通过缺陷机制分析优化回流曲线”中说,惰性气体(氮)也会增加熔湿速度。
SMT专栏作家珍尼.黄博士和其它人的报告说,共晶合金的熔湿速度倾向于比非共晶材料快。
因此,Sn63/Pb37一般比Sn62/Pb36/Ag2熔湿速度更快。
影响熔湿、从而影响结合和潜在飞溅的因素如表四所示。
表四、可能引起溅锡的因素机制对飞溅的影响助焊剂载体活性剂
不同的活性剂在回流时提高不同程度的湿润和结合速度
快速的结合将增加助焊剂被夹住的可能性,将可能增加受夹助焊剂的压力,因此引起助焊剂爆发性的排出。
助焊剂载体溶剂及其含量
溶剂类型和含量将影响预热期间烘干程度
增加溶剂含量将引起受夹住焊剂更激烈的排出
合金类型
合金影响回流期间的湿润和结合速度
快速的结合将增加助焊剂被夹住的可能性,将可能增加受夹助焊剂的压力,因此引起助焊剂爆发性的排出。
回流气氛
惰性(氮)环境增加回流期间的湿润和结合速度
快速的结合将增加助焊剂被夹住的可能性,将可能增加受夹助焊剂的压力,因此引起助焊剂爆发性的排出。
焊锡熔化温度
更高的熔化温度增加回流期间的湿润和结合速度
快速的结合将增加助焊剂被夹住的可能性,将可能增加受夹助焊剂的压力,因此引起助焊剂爆发性的排出。
溅锡的解决方案
预防:
防止溅锡沉积的一个方法就是在金手指上涂敷一层可驳除的阻焊层,在丝印锡膏后涂敷,回流后拿掉。
这个方法还没有印证,可能成本高,因为牵涉手工作业,涂敷板上选择性区域会造成困难,中断生产流水作业。
另外可选择在金手指上贴临时胶带。
这个方法也有同样的缺点。
最小化:
优化助焊剂载体的化学成份,和回流温度曲线,将溅锡减到最低。
为了证明这一点,得到内存模块制造商的支持,通过评估对材料和回流温度曲线优化的影响,来评价表准锡膏系统。
清楚地表明活性剂、溶剂、合金和回流温度曲线对溅锡程度有重要影响。
因此,有信心着手解决问题,这些参数的适当调整可以将溅锡减到最小。
非标准材料,如聚合助焊剂系统由于成本高、货架寿命丝印寿命短、工艺变化范围小、并返工困难,不包括在本研究范围。
但是,聚合助焊剂有希望最终提供一个可能最小化的溅锡解决方案,因为潜在的飞溅材料在温度激化的聚合过程中被包围。
因此,没有液体助焊剂留下来产生飞溅。
测试样板是一块六个小板的内存模块,没有贴装元件。
(已发现元件回减小溅锡的影响,因为元件会阻隔助焊剂从金手指上排出)。
现有生产材料和温度曲线作基本的试验条件(表五)。
生产电路板的飞溅水平大约每100块组合板有一个飞溅锡球。
两个工程师通过20倍的显微镜观察所有的板,以评估溅锡程度。
溅锡的影响
在回流之后,内存模块的连接器“金手指”可能出现溅锡的污染,这意味着产品的品质和可靠性问题和制造流程问题。
溅锡只是表面污染的一种,其它类型包括水渍污染和助焊剂飞溅。
这些影响较小,但由于焊锡飞溅,焊锡已实际上熔湿了“金手指”的表面。
“小爆炸”
溅锡有许多原因,不一定是回流焊接时热的或熔化的焊锡爆发性的排气结果。
例如,通过观察过程,以保证锡膏丝印时的最佳清洁度,溅锡问题可以减少或消除。
任何方法,如果使锡膏粉球可能沉积在金手指上,并在回流过程时仍存在,都可以产生溅锡。
包括:
在丝印期间没有擦拭模板底面(模板脏)
误印后不适当的清洁方法
丝印期间不小心的处理
机板材料和污染物中过多的潮汽
极快的温升斜率(超过每秒4°C)
在后面的原因中,助焊剂的激烈排气可能引起熔化焊接点中的小爆炸,促使焊锡颗粒变成在回流腔内空中乱飞,飞溅在PCB上,污染连接器的“金手指”。
PCB材料内夹住潮气的情况是一样的,和助焊剂排气有相同的效果。
类似地,板表面上的外来污染也引起溅锡。
溅锡的影响
虽然人们对溅锡可能对连接器接口有有害的影响的关注,还没有得到证实,但它仍然是个问题,因为轻微的飞溅“锡块”产生对连接器金手指平面的破坏。
这些锡块是不柔顺的,锡本身比金导电性差,特别是遭受氧化之后。
第一个最容易的消除溅锡的方法是在锡膏的模板丝印过程。
如果这个过程是产生溅锡的原因的话,那么通过良好的设备的管理及保养来得到控制,包括适当的丝印机设定和操作员培训。
如果原因不在这里,那么必须检查其它方面。
水印污染:
其根本原因还未完全理解,虽然可能涉及许多根源。
因为已经显示清洁的、未加工的、无锡膏的和没有加元件的板,在回流后也会产生水印污染,所以其中包括了许多的原因:
PCB制造残留、炉中的凝结物、干助焊剂的飞溅、清洗板的残留和导热金的变色等。
水印污染经常难于发现,但其对连接器接口似乎并无影响。
事实上内存模块的使用者并不关心这类表面污染,常常看作为金的变色。
助焊剂飞溅:
一般理解为,助焊剂水滴在回流炉中变成空中乱飞,分散和附着在整个板上,包括金手指。
有两种理论试图说明助焊剂飞溅:
溶剂排放理论和合并理论(丝印期间的清洁再次认为有影响,但可控制)。
溶剂排放理论:
认为锡膏助焊剂中使用的溶剂必须在回流时蒸发。
如果使用过高温度,溶剂会“闪沸”成气体(类似于在热锅上滴水),把固体带到空中,随机散落到板上,成为助焊剂飞溅。
为了证实或反驳这个理论,使用热板对样板进行导热性试验,并作测试。
使用的温度设定点分别为190°C,200°C和220°C。
膏状的助焊剂(不含焊锡粉末)在任何情况下都不出现飞溅。
可是,锡膏(含有粉末的助焊剂)在焊锡熔化和焊接期间始终都有飞溅。
穿孔回流焊
在传统的电子组装工艺中,对于安装有过孔插装元件(THD)印制板组件的焊接一般采用波峰焊接技术。
但波峰焊接有许多不足之处:
不适合高密度元件焊接;桥接、漏焊较多;需喷涂助焊剂;印制板受到较大热冲击翘曲变形。
因此波峰焊接在许多方面不能适应电子组装技术的发展。
为了适应表面组装技术的发展,解决以上焊接难点的措施是采用穿孔回流焊PIHR(pin—in—hole reflow)。
该技术原理是在印制板完成贴片后,使用一种安装有许多针管的特殊模板,调整模板位置使针管与插装元件的过孔焊盘对齐,然后使用刮刀将模板上的锡膏漏印到焊盘上,然后安装插装元件,最后插装元件与贴片元件一起通过回流焊完成焊接。
穿孔回流焊的优越性在于:
首先是减少了工序,省去了波峰焊这道工序,在费用上自然可节省不少,同时也减少了所需的工作人员,在效率上也得到了提高;其次回流焊相对于波峰焊,产生桥接的可能性要小得多,这样就提高了一次通过率。
穿孔回流焊相对传统工艺在经济性、先进性上都有很大优势。
目前日本SONY公司有在1—2年内以穿孔回流焊全面代替波峰焊的计划,而我国生产调谐器的企业和高技术、高附加值的一些通信产品已率先使用PIHR工艺,预计不远的将来这项新技术将会得到普遍采用。
脉冲加热回流焊接
脉冲加热回流焊接(pulse-heatedreflowsoldering)是一种工艺,将两个预先上好助焊剂的、镀锡的零件加热到足以使焊锡熔化、流动的温度,固化后,在零件与焊锡之间形成一个永久的电气机械连接。
与传统的焊接相反,脉冲加热回流焊接通过对每个连接使用一个热电极加热和冷却来焊接。
在整个加热、回流和冷却周期内要施加压力。
脉冲加热控制将能量传送到安装在回流焊接头上的热电极。
附着在热电极上的热电偶为可重复的、持续的热源控制提供反馈。
焊接头将两个零件直接接触。
以一个精确的压力,头发信号给控制器,开始热电极的加热循环。
热电极将热传导给零件,随后的热传导将零件之间的焊锡熔化。
熔化的区域开始流动,造成两群焊锡的接合。
当控制器终止回流循环,在冷却循环中零件继续保持在一起,因此焊锡重新固化,形成焊点。
一个好焊点应该是焊锡充分地结合两个表面,在两个零件表面发生熔湿(wetting)。
电线元件(FlexComponent)
用于脉冲加热回流焊接工艺的最常见类型的电线是由聚酰亚胺(polyimide)制造的,也叫做“Kapton®”。
两层聚酰亚胺包胶铜迹线(trace)-一般0.5~2盎司(ounce)。
两种最常见的铜导线是轧制韧化(RA,rolledannealed)铜和电解沉淀(ED,electrodeposited)铜;电解沉淀铜最有成本效益,被广泛使用。
铜迹线的厚度范围是0.0007~0.004"(0.02~0.10mm)。
聚酰亚胺的可操作温度范围是130~200°C,可经受高达300°C的短期焊接温度。
热电极的温度总是高于被热电极加热的零件温度。
在热电极与焊点之间、横穿Kapton电线,可能发生50~80°C的温降,决定于厚度。
电线(flex)的厚度范围是0.001~0.0047"(0.0254~0.12mm)。
在脉冲加热回流焊接工艺的柔性电路上使用的三种常见类型的端子设计是:
暴露引线设计(exposedleaddesign)-这种设计将聚酰亚胺材料的两面去掉,留下不绝缘的迹线。
热电极直接接触迹线,将热传导给零件。
如果PCB焊盘与热电极脚印尺寸正确,这种设计将容许一些多余的焊锡在焊盘上,因为焊锡可能流到开放的区域。
在工艺过程中,焊锡也将熔湿迹线顶部。
在处理零件时必须小心,因为迹线容易弯曲或损坏。
单面电线设计(single-sidedflexdesign)-这种设计只从一面去掉聚酰亚胺。
热量从热电极通过固体聚酰亚胺表面传导到底下暴露的迹线。
聚酰亚胺通过绝缘体传导热量到暴露的迹线和PCB焊盘。
在焊接点区域的聚酰亚胺的厚度限制在0.002",使得可以热传导。
如果聚酰亚胺必须加热超过260°C,可能造成表面烧伤和热电极污染。
这个设计不容许过多焊锡在PCB焊盘上,因为存在很少空间来过多流动。
开窗式电线设计(open-windowedflexdesign)-这种设计将焊接区域的两面的聚酰亚胺去掉,但在边缘和迹线尾端都有剩下的聚酰亚胺材料支持。
该设计给予装配一定的强度,并对较生硬的处理有弹性。
因为迹线暴露,对零件的热传导是良好的,有额外的空间给剩余的焊锡流动。
热电极的尺寸是关键的,因为它必须适合窗口,并允许熔化的焊锡流动的空间。
电线与PCB迹线的尺寸(FlexandPCBTraceSizes)
理想地,柔性电路的焊盘应该比PCB上的焊盘在宽度上更窄。
随着焊锡熔化、零件压下,焊锡被挤到旁边。
该设计将允许焊锡在柔性焊盘的另一面流动的空间,将容许PCB上更多的焊锡,避免锡桥问题。
柔性电路上更小的焊盘宽度将帮助两个零件的定位与对中。
对于密间距(finepitch)的应用,PCB迹线的宽度设计成间距的50%。
这种设计减少由于不对准所造成的短路。
通用基板零件设计指南
多数PCB材料诸如FR-2和FR-4对于工艺期间的局部受热是很有弹性的。
象陶瓷基板这样的材料必须以一种更受控的方式来加热,以减少破裂的机会。
两个零件的散热能力太大的差距也可能引起冷却期间的焊接破裂。
沿焊接点长度上的散热差异是最常见的要克服的设计问题。
小的差别影响也小,但沿焊接区域的任何热质量改变都将引起温度和焊接点质量的不一致。
散热、焊盘区域设计问题,解决方案
热可能很容易从焊接区域传导到大的焊盘,如果位置太靠近焊接区域(图一A)。
加大的迹线宽度和电镀的通孔从焊接区域吸走热量(图一B)。
宽度减小的迹线就好象挡热墙,阻止焊盘的任何散热(图一C)。
如果使用小迹线挡热墙,没有散热存在的有效的最小面积是0.08"(0.2mm)(图一D)。
相等尺寸的小迹线作挡热墙用,保证焊接区域相同的加热。
从焊盘引出的迹线应该相同的宽度,尽可能地窄(图二)。
这种设计将起挡热墙的作用,防止焊接期间过多的热量从焊盘区域排走。
对于多层板,将粘结区域下的迹线限制为最小宽度的(信号)迹线,在PCB的焊盘之下均匀地分布。
PCB上任何屏蔽都在焊接区域有同等的影响。
PCB焊盘的焊接要求
焊锡沉积的可重复性对达到良好的过程控制是关键的。
在许多情况中可能要求试验来获得理想的焊锡量。
一个良好的开始点是使用一块0.006"的丝印模板,40%的焊盘覆盖面积。
PCB焊盘上要求的焊锡数量取决于几个因素。
焊盘尺寸与间距决定可施用的焊锡量的最大与最小,使用丝印模板工艺。
模板印刷的焊锡在回流工艺之前应该熔合。
小焊盘与小间距要求较少的焊锡,防止焊点形成锡桥。
电线(flex)的设计也将影响焊锡量。
开窗的电线和暴露的迹线的电线将得到比单面电线稍微较多的焊锡量。
热电极尺寸与对零件的定位
热电极应该按照焊盘和电线的尺寸来确定尺寸,如图三所示。
热电极的长度必须完全覆盖迹线,在每一边超出至少一个焊盘间距。
热电极的宽度应该提供充分的热传导,以达到在最短的时间内完成焊接,因此