毕业论文冲压加工技术毕业论文Word格式文档下载.docx
《毕业论文冲压加工技术毕业论文Word格式文档下载.docx》由会员分享,可在线阅读,更多相关《毕业论文冲压加工技术毕业论文Word格式文档下载.docx(19页珍藏版)》请在冰豆网上搜索。
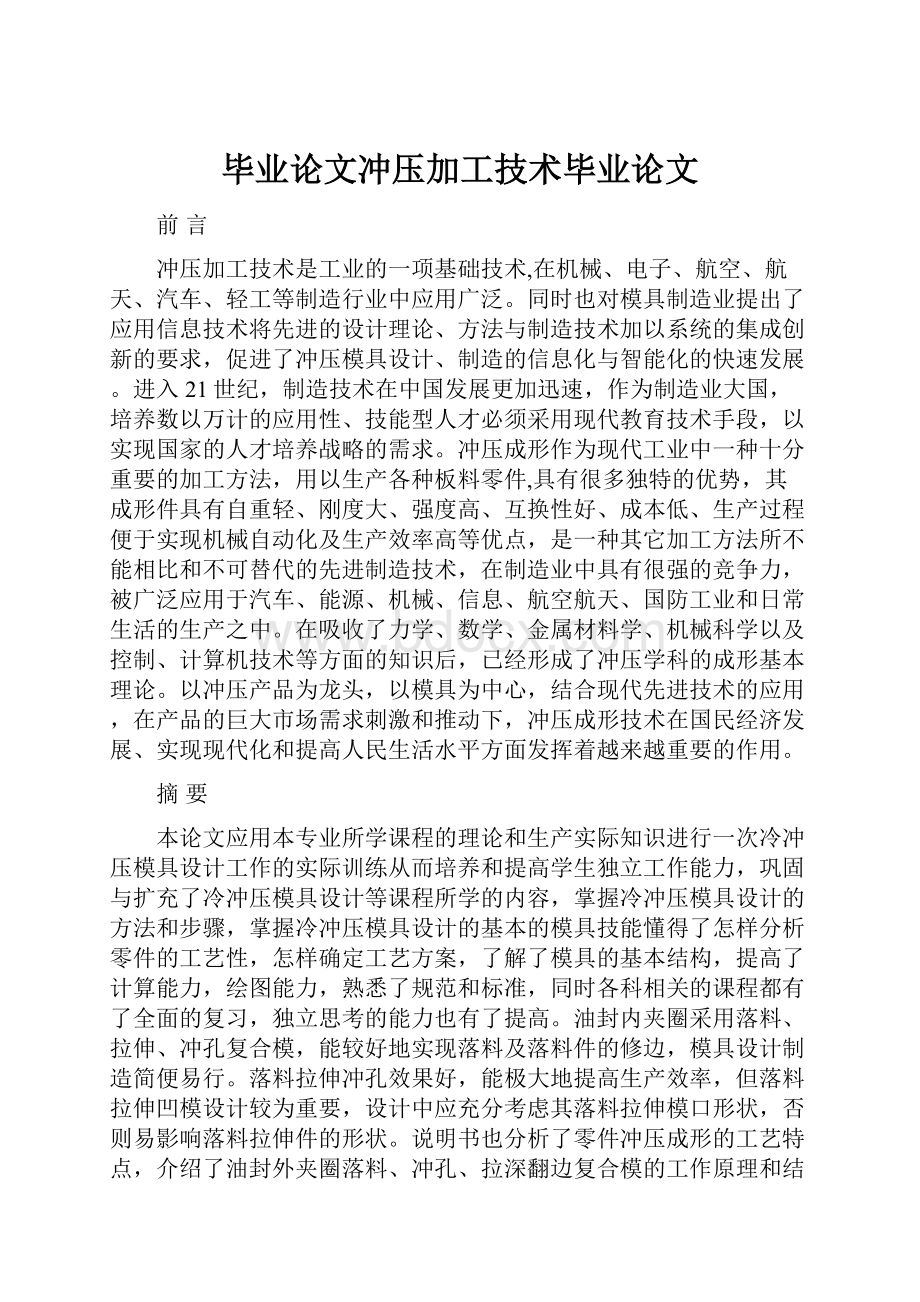
and
introduce
operational
principle
structure
design
compound
moulds
blank-and-cup
piercing
drawing
flanging.
I
designed
a
suit
which
contain
are
reasonable
has
compact
structures
high
reliability
widely
used.
can
complete
flanging
in
position,
so
production
efficiency
economic
benefit
higher
then
old
features.
Determine
type
by
anal
yes
part.
Then
calculate
parts
according
to
normal
way,
such
as:
male
mould,
female
mould
holder.
Keywords:
moulds,blank-and-cup,fallsmaterial,strechmol
punchhole,superposebledie,coldstamping,artographyability
第一章概论
日常生产、生活中所使用到的各种工具和产品,大到机床的底座、机身外壳,小到一个胚头螺丝、纽扣以及各种家用电器的外壳,无不与模具有着密切的关系。
模具的形状决定着这些产品的外形,模具的加工质量与精度也就决定着这些产品的质量。
因为各种产品的材质、外观、规格及用途的不同,模具分为了铸造模、锻造模、压铸模、冲压模等非塑胶模具,以及塑胶模具。
随着科学技术的进步和工业生产的迅速发展,冲压加工技术的应用愈来愈广泛,模具成形已成为当代工业生产的重要手段。
冷冲压:
是在常温下利用冲模在压力机上对材料施加压力,使其产生分离或变形,从而获得一定形状、尺寸和性能的零件的加工方法。
冲压可分为五个基本工序:
冲裁、弯曲、拉深、成形和立体压制。
冲压模具:
在冷冲压加工中,将材料(金属或非金属)加工成零件(或半成品)的一种特殊工艺装备,称为冷冲压模具(俗称冷冲模)。
冲压模按照工序组合分为三类:
单工序模、复合模和级进模。
复合模与单工序模相比减少了冲压工艺,其结构紧凑,面积较小;
冲出的制件精度高,工件表面较平直,特别是孔与制件的外形同步精度容易保证;
适于冲薄料,可充分利用短料和边角余料;
适合大批量生产,生产率高,所以得到广泛应用,但模具结构复杂,制造困难。
冲压模具是冲压生产必不可少的工艺装备,是技术密集型产品。
冲压件的质量、生产效率以及生产成本等,与模具设计和制造有直接关系。
模具设计与制造技术水平的高低,是衡量一个国家产品制造水平高低的重要标志之一,在很大程度上决定着产品的质量、效益和新产品的开发能力。
在现代工业生产中,冲模约占模具工业的50%,,在国民经济各个部门,特别是汽车、航空航天、仪器仪表、机械制造、家用电器、石油化工、轻工日用品等工业部门得到极其广泛的应用。
据统计,利用冲模制造的零件,在飞机、汽车、电机电器、仪器仪表等机电产品中占60%~70%,在电视机、录音机、计算机等电子产品中占80%以上,在自行车、手表、洗衣机、电冰箱、电风扇等轻工产品中占85%以上。
在各种类型的汽车中,平均一个车型需要冲压模具2000套,其中大中型覆盖件模具300套。
我国冲压模具无论在数量上,还是在质量、技术和能力等方面都已有了很大发展,但与国发经济需求和世界先进水平相比,差距仍很大,一些大型、精度、复杂、长寿命的高档模具每年仍大量进口,特别是中高档轿车的覆盖件模具,目前仍主要依靠进口。
一些低档次的简单冲模,已趋供过于求,市场竟争激烈。
据中国模具工业协会发布的统计材料,2004年我国冲压模具总产出约为220亿元,,.
根据我国海关统计资料,,,,市场满足率为82%.在上述供求总体情况中,有几个具体情况必须说明:
一是进口模具大部分是技术含量高的大型精密模具,而出口模具大部分是技术含量较低中的中低档模具,因此技术含量高的中高档模具市场满足率低于冲压模具总体满足率,这些模具的发展已滞后于冲压件生产,而技术含量低的中低档模具市场满足率要高于冲压模具市场总体满足率;
二是由于我国的模具价格要比国际市场低格低许多,具有一定的竟争力,因此其在国际市场前景看好,,%就可说明这一点;
三是近年来港资、台资、外资企业在我国发展迅速,这些企业中大量的自产自用的冲压模具无确切的统计资料,因此未能计入上述数字之中。
我国冲模工业不能满足国内经济需要的原因主要有:
。
,效率低,经济效益也差。
,模具精度不高,制造技术较落后。
,新材料使用量不到10%。
4.力量分散,管理落后。
但改革开放以来,在国家产业政策和与之配套的一系列国家经济政策的支持和引导下,尤其是国民经济的高速发展,大大地提高了模具的商品化程度,推动了模具技术和模具工业的迅速发展,在CAD/CAM/CAE的运用、加工工艺手段、冲压件质量及模具性能方面,均已达到或接近国际水平。
冲压模具水平状况
近年来,我国冲压模具水平已有很大提高。
大型冲压模具已能生产单套重量达50多吨的模具。
为中档轿车配套的覆盖件模具内也能生产了。
精度达到1~2μm,寿命2亿次左右的多工位级进模国内已有多家企业能够生产。
表面粗糙度达到Ra≤,大尺寸(φ≥300mm)精冲模及中厚板精冲模国内也已达到相当高的水平。
⑴模具CAD/CAM技术状况
我国模具CAD/CAM技术的发展已有20多年历史。
由原华中工学院和武汉733厂于1984年共同完成的精神模CAD/CAM系统是我国第一个自行开发的模具CAD/CAM系统。
由华中工学院和北京模具厂等于1986年共同完成的冷冲模CAD/CAM系统是我国自行开发的第一个冲裁模CAD/CAM系统。
上海交通大学开发的冷冲模CAD/CAM系统也于同年完成。
20世纪90年代以来,国内汽车行业的模具设计制造中开始采用CAD/CAM技术。
国家科委863计划将东风汽车公司作为CIMS应用示范工厂,由华中理工大学作为技术依托单位,开发的汽车车身与覆盖模具CAD/CAPP/CAM集成系统于1996年初通过鉴定。
在此期间,一汽和成飞汽车模具中心引进了工作站和CAD/CAM软件系统,并在模具设计制造中实际应用,取得了显著效益。
1997年一汽引进了板料成型过程计算机模拟CAE软件并开始用于生产。
21世纪开始CAD/CAM技术逐渐普及,现在具有一定生产能力的冲压模具企业基本都有了CAD/CAM技术。
其中部分骨干重点企业还具备各CAE能力。
模具CAD/CAM技术能显著缩短模具设计与制造周期,降低生产成本,提高产品质量,已成为人们的共识。
在“八五”、九五“期间,已有一大批模具企业推广普及了计算机绘图技术,数控加工的使用率也越来越高,并陆续引进了相当数量CAD/CAM系统。
如美国EDS的UG,美国ParametricTechnology公司Pro/Engineer,美国CV公司的CADSS,英国DELCAM公司的DOCT5,日本HZS公司的CRADE及space-E,以色列公司的Cimatron还引进了AutoCADCATIA等软件及法国Marta-Daravision公司用于汽车及覆盖件模具的Euclid-IS等专用软件。
国内汽车覆盖件模具生产企业普遍采用了CAD/CAM技术/DL图的设计和模具结构图的设计均已实现二维CAD,多数企业已经向三维过渡,总图生产逐步代替零件图生产。
且模具的参数化设计也开始走向少数模具厂家技术开发的领域。
在冲压成型CAE软件方面,除了引进的软件外,华中科技术大学、吉林大学、湖南大学等都已研发了较高水平的具有自主知识产权的软件,并已在生实践中得到成功应用,产生了良好的效益。
快速原型(RP)传统的快速经济模具相结合,快速制造大型汽车覆盖件模具,解决了原来低熔点合金模具靠样件浇铸模具,模具精度低、制件精度低,样样制作难等问题,实现了以三维CAD模型作为制模依据的快速模具制造,它标志着RPM应用于汽车身大型覆盖件试制模具已取得了成功。
围绕着汽车车身试制、大型覆盖件模具的快速制造,近年来也涌现出一些新的快速成型方法,例如目前已开始在生产中应用的无模多点成型及激光冲击和电磁成型等技术。
它们都表现出了降低成本、提高效率等优点。
⑵模具设计与制造能力状况
在国家产业政策的正确引导下,经过几十年努力,现在我国冲压模具的设计与制造能力已达到较高水平,包括信息工程和虚拟技术等许多现代设计制造技术已在很多模具企业得到应用。
虽然如此,我国的冲压模具设计制造能力与市场需要和国际先进水平相比仍有较大差距。
这一些主要表现在高档轿车和大中型汽车覆盖件模具及高精度冲模方面,无论在设计还是加工工艺和能力方面,都有较大差距。
轿车覆盖件模具,具有设计和制造难度大,质量和精度要求高的特点,可代表覆盖件模具的水平。
虽然在设计制造方法和手段方面基本达到了国际水平,模具结构周期等方面,与国外相比还存在一定的差距。
标志冲模技术先进水平的多工位级进模和多功能模具,是我国重点发展的精密模具品种。
有代表性的是集机电一体化的铁芯精密自动阀片多功能模具,已基本达到国际水平。
但总体上和国外多工位级进模相比,在制造精度、使用寿命、模具结构和功能上,仍存在一定差距。
汽车覆盖件模具制造技术正在不断地提高和完美,高精度、高效益加工设备的使用越来越广泛。
高性能的五轴高速铣床和三轴的高速铣床的应用已越来越多。
NC、DNC技术的应用越来越成熟,可以进行倾角加工超精加工。
这些都提高了模具面加工精度,提高了模具的质量,缩短了模具的制造周期。
模具表面强化技术也得到广泛应用。
工艺成熟、无污染、成本适中的离子渗氮技术越来越被认可,碳化物被覆处理(TD处理)及许多镀(涂)层技术在冲压模具上的应用日益增多。
真空处理技术、实型铸造技术、刃口堆焊技术等日趋成熟。
激光切割和激光焊技术也得到了应用。
根据我国冲模技术的发展现状及存在的问题,今后应朝着如下几个方面发展:
⑴开发、发展精密、复杂、大型、长寿命模具。
⑵加速模具标准化和商品化,以提高模具质量,缩短模具制造周期。
⑶大力开发和推广应用模具CAD/CAM技术,提高模具制造过程的自动化程度。
⑷积极开发模具新品种、新工艺、新技术和新材料。
⑸发展模具加工成套设备,以满足高速发展的模具工业需要。
冲压加工作为一个行业,在国民经济的加工工业中占有重要的地位。
近年来,冲压成型工艺有了很多新的进展,特别是精密冲裁、精密成形、精密剪切、复合材料成形、超塑性成形、软模成形以及电磁成形等新工艺日新月异,冲压件的成形精度日趋精确,生产率有了极大的提高,正把冲压加工提高到高品质、新的发展水平。
由于引入了计算机辅助工程(CAE)冲压成形已从原来对应力应变进行有限元分析而逐步发展到采用计算机进行工艺过程的模拟与分析,以实现冲压过程的优化分析设计。
计算机在模具领域,包括设计、制造、管理等领域发挥着越来越重要的作用。
第二章工件工艺性分析及方案确定
油封内夹圈油封外夹圈
图2-1零件图
工件名称:
油封内外夹圈
生产批量:
大批量
材料:
08钢
料厚:
以上两零件分别为油封内夹圈和油封外夹圈,材料为08钢板,软的碳素钢,强度、硬度低,而韧性和塑性极高,有良好的深冲、拉延、弯曲和镦粗等冷加工性能、焊接性能。
由零件简图2-1可见,该工件的加工涉及到落料、冲孔、翻边或拉深等工序成形。
该零件的外径为Φ92mm和Φ90mm,属于小制件,形状简单且对称,适于冲裁加工。
查《冷冲压工艺手册》得:
孔中心与边缘距离尺寸公差为±
,.
材料08钢,其冲压性能较好,孔与外缘的壁厚较大,复合模中的凸凹模壁厚部分具有足够的强度。
能够进行一般的冲压加工,市场上也容易得到这种材
料,价格适中。
年产量为大批量生产,不允许表面划痕,孔不许有变形,精度要求为IT11,由于零件用于密封,精度要求较高,但零件完全可以用普通的冲压加工方法加工成型。
两零件的直径相同,均为117,而内直径不同,冲压工艺方法有可能不同。
两工件均为轴对称零件,形状简单,都是翻孔件,材料厚度较薄,冲裁性能较好。
⑴翻边工件边缘与平面的圆角半径r=(2~3)t
⑵翻边的高度内夹圈h=≥=,外夹圈h=≥=
⑶翻边的相对厚度d/t>
(~2),所以翻边后有良好的圆筒壁
⑷冲孔毛刺面与翻边方向相反,翻边后工件质量没大影响。
总体看来:
该制件均满足冲裁工艺性和翻边工艺性,适于冲裁加工。
⑴对于内夹圈:
查《冷冲压工艺手册》表2-9,确定凸凹模制造精度为IT11,毛坏翻边的预制孔直径为d=D-2(),由工件可知,D=,H=,t=,查《冲压工艺手册》,选用r=3t=,代以上数据到公式得知d=。
查《冲压工艺手册》,,内夹圈系数k=d/D=79/=>
,尺寸关系满足翻边变形趋向要求,对于内夹圈来说,上述三道工序可行,所以在平板上能一次性翻边成形
⑵对于外夹圈:
查《冷冲压工艺手册》表2-9,确定凸凹模制造精度为IT11,如果按预制孔直接加工,毛坏翻边的预制孔直径为d=D-2(),由工件可知,D=,H=,t=,查《冲压工艺手册》,选用r=3t=,代以上数据到公式得知d=。
查《冲压工艺手册》,,内夹圈系数k=d/D=<
,尺寸关系不满足翻边变形趋向要求,不能一次翻出所需要的高度,所以对于内夹圈来说,上述三道工序不可行。
考虑多采用拉深一道中间工序,再进行翻边。
工艺方案确定
根据工件结构的分析,冲压这两个零件所需的最基本工序为冲孔,落料,拉深,翻边。
按以下表比较单工序模、连续模和复合模,初步确定选复合模。
项目
单工序模
连续模
复合模
工作情况
尺寸精度
精度较高
可达IT13~10级
可达IT9~8级
工件形状
易加工简单件
可加工复杂零件,如宽度极小的异形件、特殊形件
形状与尺寸要受模具结构与强度的限制
孔与外形的位置精度
较高
较差
工件平整性
推板上落料,平整
较差,易弯曲
工件尺寸
一般不受限制
宜较小零件
可加工较大零件
工件料厚
~6mm
~3mm
工艺性能
操作性能
方便
不方便,要手动进行卸料
安全性
比较安全
不太安全
生产率
低,压力机一次行程只能完成一道工序,但在多工位压力机使用多副模具时,生产率高
高,压力机一次行程内可完成多道工序
较高,压力机一次行程内能完成两道以上工序
条料宽度
要求不严格
要求严格
模具制造
结构简单,制造周期短
结构复杂,制造和调整难度大
结构复杂,制造难度大
主要有这几种方案:
⑴采用落料和冲孔的复合,再进行零件的翻孔工艺。
⑵冲孔,落料,翻孔依次按顺序复合加工。
优缺点分析:
按第一方法加工,需要两套模具,工作的累积误差大,操作不方便,但精度相对高,可是成本比较大,而且该零件大批量生产。
第二种方法加工,需要一套模具,但精度稍差,可是能通过改进制造系统和设计方法使精度增大,复合模模具的形位精度和尺寸精度可以保证,且生产率也高。
尽管模具结构比较复杂,但由于零件的几何形状简单对称,模具制造并不困难。
用一套模具降低了成本,缩短了生产周期,提高了生产效率,避免了传统方法生产使用多套模具及送料的麻烦,操作方便而且快捷,冲出制件的质量也较好。
综合考虑,采用三个工艺的复合加工,选用一套复合模具。
⑵对于外夹圈工艺确定为落料,拉深,冲孔,翻边,四个工艺方案的依次顺序只能采用落料,拉深,冲孔,翻边。
工艺方案为:
①采用落料和拉深的复合,再采用冲孔和翻边。
②落料,拉深,冲孔,翻边依次按顺序复合加工。
按第一方法加工,需要两套模具,但精度相对高,可是运行成本比较大。
第二种方法加工,需要一套模具,但精度稍差,可是能通过改进制造系统和设计方法使精度增大,用一套模具降低了成本,缩短了生产周期,同时对于这样的简单零件,完全可以考虑通过复合加工来降低模具套数,从而降低运作成本。
综合考虑,采用四个工艺的复合加工,选用一套复合模具。
正装复合模和倒装复合模的比较见下表
序号
正装
倒装
1
对于薄冲件能达到平整要求
不能达到平整要求
2
操作不方便,不安全,孔的废料由打棒打出
操作方便,能装自动拔料装置,能提高生产效率又能保证安全生产,孔的废料通过凸凹模的孔往下漏掉
3
废料不会在凸凹模孔内积聚,每次由打棒打出,可减少孔内废料的胀力,有利于凸凹模减少最小壁厚
废料在凸凹模孔内积聚,凸凹模要求有较大的壁厚以增加强度
4
装凹模的面积较大,有利于复杂制件拼快结构
如凸凹模较大,可直接将凸凹模固定在底座上省去固定板
正装对于薄冲件能达到平整要求,且废料不会在凸凹模孔内积聚,有利于凸凹模减少最小壁厚。
而倒装不能达到平整要求,而且废料在凸凹模孔内积聚,凸凹模要求有较大的壁厚以增加强度。
从保证冲裁件质量、经济性和安全性前提下,综合考虑采用正装复合模,即模具结构为落料、拉深、冲孔、翻边正装复合模。
第三章排样及计算材料利用率
图3-1零件图
:
该制件是在冲孔后的平板毛坯上翻边成形,在翻边时,同心圆之间的距离变化不显著,预制孔直径可以用弯曲展开的方