自动生产线转为机械手液压系统设计Word下载.docx
《自动生产线转为机械手液压系统设计Word下载.docx》由会员分享,可在线阅读,更多相关《自动生产线转为机械手液压系统设计Word下载.docx(13页珍藏版)》请在冰豆网上搜索。
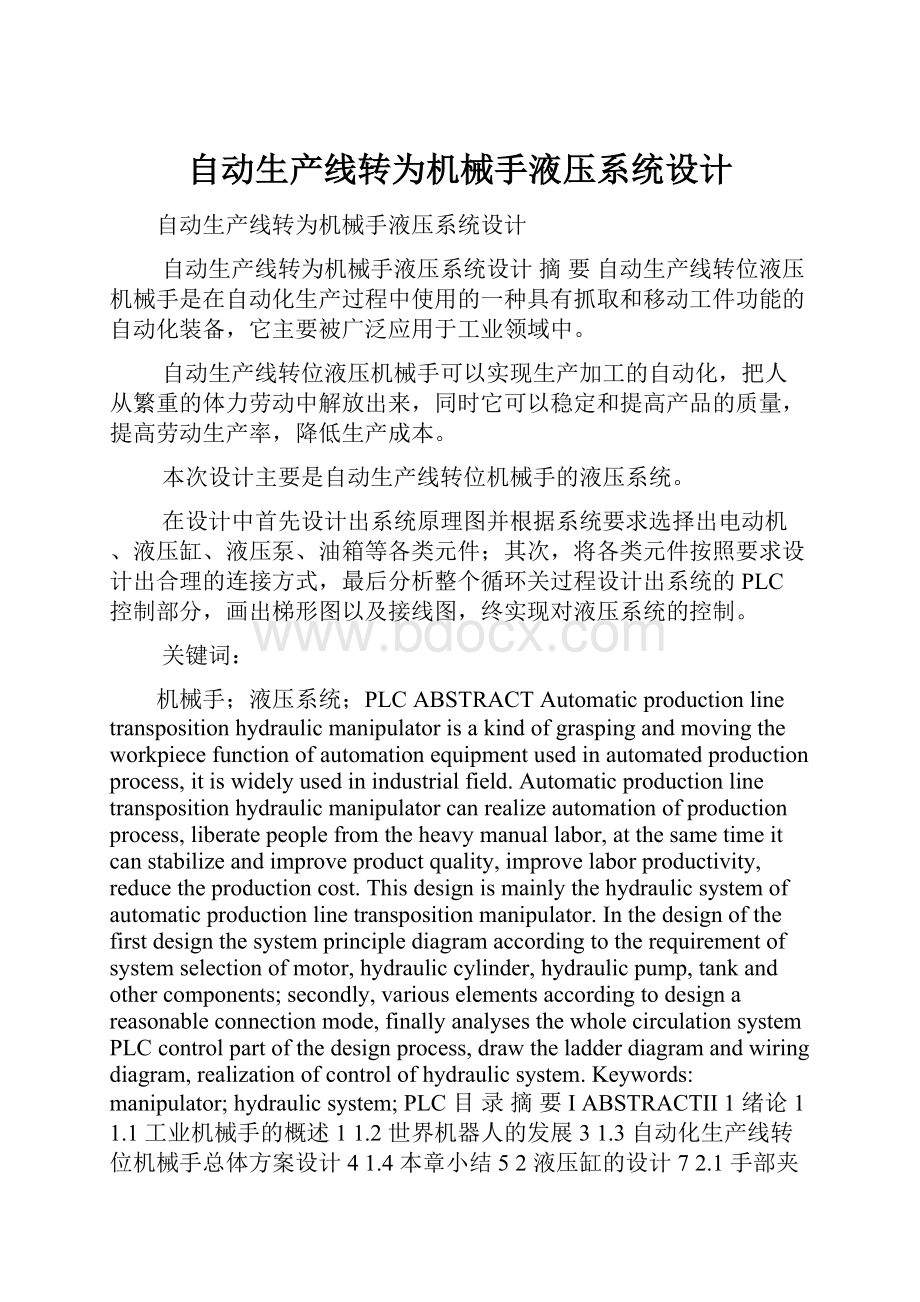
不少球坐标式通用机械手就是在这个基础上发展起来的。
同年该公司和普鲁曼公司合并成立万能自动公司(Unimaton),专门生产工业机械手。
1962年美国机械铸造公司也试验成功一种叫Versatran机械手,原意是灵活搬运。
该机械手的中央立柱可以回转,臂可以回转、升降、伸缩、采用液压驱动,控制系统也是示教再现型。
虽然这两种机械手出现在六十年代初,但都是国外工业机械手发展的基础。
1978年美国Unimate公司和斯坦福大学、麻省理工学院联合研制一种Unimate-Vic-arm型工业机械手,装有小型电子计算机进行控制,用于装配作业,定位误差可小于±
1毫米。
美国还十分注意提高机械手的可靠性,改进结构,降低成本。
如Unimate公司建立了8年机械手试验台,进行各种性能的试验。
准备把故障前平均时间(注:
故障前平均时间是指一台设备可靠性的一种量度。
它给出在第一次故障前的平均运行时间),由400小时提高到1500小时,精度可提高到±
0.1毫米。
德国机器制造业是从1970年开始应用机械手,主要用于起重运输、焊接和设备的上下料等作业。
德国KnKa公司还生产一种点焊机械手,采用。
瑞典安莎公司采用机械手清理铸铝齿轮箱毛刺等。
日本是工业机械手发展最快、应用最多的国家。
自1969年从美国引进二种典型机械手后,大力研究机械手的研究。
据报道,1979年从事机械手的研究工作的大专院校、研究单位多达50多个。
1976年个大学和国家研究部门用在机械手的研究费用42%。
1979年日本机械手的产值达443亿日元,产量为14535台。
其中固定程序和可变程序约占一半,达222亿日元,是1978年的二倍。
具有记忆功能的机械手产值约为67亿日元,比1978年增长50%。
智能机械手约为17亿日元,为1978年的6倍。
截止1979年,机械手累计产量达56900台。
在数量上已占世界首位,约占70%,并以每年50%~60%的速度增长。
使用机械手最多的是汽车工业,其次是电机、电器。
预计到1990年将有55万机器人在工作。
第二代机械手正在加紧研制。
它设有微型电子计算机控制系统,具有视觉、触觉能力,甚至听、想的能力。
研究安装各种传感器,把感觉到的信息反馈,使机械手具有感觉机能。
目前国外已经出现了触觉和视觉机械手。
第三代机械手(机械人)则能独立地完成工作过程中的任务。
它与电子计算机和电视设备保持联系。
并逐步发展成为柔性制造系统FMS(FlexibleManufacturingsystem)和柔性制造单元(FlexibleManufacturingCell)中重要一环机械手是模仿人的手部动作,按给定程序、轨迹和要求实现自动抓取、搬运和操作的自动装置。
它特别是在高温、高压、多粉尘、易燃、易爆、放射性等恶劣环境中,以及笨重、单调、频繁的操作中能代替人作业,因此获得日益广泛的应用。
机械手一般由执行机构、驱动系统、控制系统及检测装置三大部分组成,智能机械手还具有感觉系统和智能系统。
驱动系统多数采用电液(气)机联合传动。
机械手在工业生产中应用极为广泛,这主要是因为它具有下列优点:
模仿人的手部动作,按给定程序、轨迹和要求实现自动抓取、搬运和操作的自动装置。
1.2世界机器人的发展
(1)工业机器人性能不断提高(高速度、高精度、高可靠性、便于操作和维修),而单机价格不断下降,平均单机价格从91年的10.3万美元降至97年的6.5万美元。
(2)机械结构向模块化、可重构化发展。
例如关节模块中的伺服电机、减速机、检测系统三位一体化:
由关节模块、连杆模块用重组方式构造机器人整机;
国外已有模块化装配机器人产品问市。
(3)工业机器人控制系统向基于PC机的开放型控制器方向发展,便于标准化、网络化;
器件集成度提高,控制柜日见小巧,且采用模块化结构:
大大提高了系统的可靠性、易操作性和可维修性。
(4)机器人中的传感器作用日益重要,除采用传统的位置、速度、加速度等传感器外,装配、焊接机器人还应用了视觉、力觉等传感器,而遥控机器人则采用视觉、声觉、力觉、触觉等多传感器的融合技术来进行环境建模及决策控制多传感器融合配置技术在产品化系统中已有成熟应用。
(5)虚拟现实技术在机器人中的作用已从仿真、预演发展到用于过程控制如使遥控机器人操作者产生置身于远端作业环境中的感觉来操纵机器人。
(6)当代遥控机器人系统的发展特点不是追求全自治系统,而是致力于操作者与机器人的人机交互控制,即遥控加局部自主系统构成完整的监控遥控操作系统,使智能机器人走出实验室进入实用化阶段。
美国发射到火星上的“索杰纳”机器人就是这种系统成功应用的最著名实例。
(7)机器人化机械开始兴起。
从94年美国开发出“虚拟轴机床”以来,这种新型装置已成为国际研究的热点之一,纷纷探索开拓其实际应用的领域。
我国的工业机器人从80年代“七五”科技攻关开始起步,在国家的支持下,通过“七五”、“八五”科技攻关,目前己基本掌握了机器人操作机的设计制造技术、控制系统硬件和软件设计技术、运动学和轨迹规划技术,生产了部分机器人关键元器件,开发出喷漆、弧焊、点焊、装配、搬运等机器人;
其中有130多台套喷漆机器人在二十余家企业的近30条自动喷漆生产线(站)上获得规模应用,弧焊机器人己应用在汽车制造厂的焊装线上。
但总的来看,我国的工业机器人技术及其工程应用的水平和国外比还有一定的距离,如:
可靠性低于国外产品:
机器人应用工程起步较晚,应用领域窄,生产线系统技术与国外比有差距;
在应用规模上,我国己安装的国产工业机器人约200台,约占全球已安装台数的万分之四。
以上原因主要是没有形成机器人产业,当前我国的机器人生产都是应用户的要求,“一客户,一次重新设计”,品种规格多、批量小、零部件通用化程度低、供货周期长、成本也不低,而且质量、可靠性不稳定。
因此迫切需要解决产业化前期的关键技术,对产品进行全面规划,搞好系列化、通用化、模块化设计,积极推进产业化进程.我国的智能机器人和特种机器人在”863”计划的支持下,也取得了不少成果。
其中最为突出的是水下机器人,6000m水下无缆机器人的成果居世界领先水平,还开发出直接遥控机器人、双臂协调控制机器人、爬壁机器人、管道机器人等机种:
在机器人视觉、力觉、触觉、声觉等基础技术的开发应用上开展了不少工作,有了一定的发展基础。
但是在多传感器信息融合控制技术、遥控加局部自主系统遥控机器人、智能装配机器人、机器人化机械等的开发用方面则刚刚起步,与国外先进水平差距较大,需要在原有成绩的基础上,有重点地系统攻关,才能形成系统配套可供实用的技术和产品,以期在“十五”后期立于世界先进行列之中。
1.3自动化生产线转位机械手总体方案设计自动化生产线转位机械手是将待要加工的工件从传送带上夹装到专用机床上,待加工完毕后在夹装回传送带的专用机械手。
机械手总体设计分为夹紧机构、升降机构、回转机构设计和液压站四大部分设计及二个系统:
液压控制系统与PLC控制系统。
机械手在工作过程中需三种运动,其中手指的夹紧和立柱的升降为两种直线运动,而手臂的回转为圆周运动,所以采用圆柱坐标形式。
其特点是,结构简单,手臂运动范围大,有较高的定位准确度。
机械手的动作要求分为7步。
从原位开始—手指夹紧—立柱上升—手臂右回转—立柱下降—手指松开—手臂左回转,依次循环动作。
根据课题设计任务书的要求,确定总体方案:
工件夹紧负载:
30㎏;
夹紧缸行程:
800㎜;
夹紧速度:
Amin。
(2-30)式中qmin—流量阀的最小稳定流量,一般从选定流量阀的产品样本中查得;
Vmin—液压缸的最低速度,由设计要求给定。
A=50.24cm2,Amin=17.5cm2,因为A>
Amin,所以满足速度稳定的要求。
3.液压缸壁厚和外径的计算液压缸的壁厚由液压缸的强度条件来计算。
液压缸的壁厚一般是指缸筒结构中最薄处的厚度。
从材料力学可知,承受内压力的圆筒,其内应力分布规律因壁厚的不同而各异。
一般计算时可分为薄壁圆筒和厚壁圆筒。
液压缸的内径D与其壁厚δ的比值D/δ的圆筒称为薄壁圆筒。
起重运输机械和工程机械的液压缸,一般用无缝钢管材料,大多属于薄壁圆筒结构,其薄壁按薄壁圆筒公式计算(2-31)式中δ——液压缸壁厚(m);
D——液压缸内经(m);
Pp——实验压力,一般取最大工作压力的(1.25~1.5)倍(Mpa);
[σ]—缸筒的材料许用应力。
其值为:
锻钢[σ]=110~120Mpa;
铸钢:
[σ]=100~110Mpa;
无缝钢管:
高强度铸铁:
[σ]=60Mpa;
灰铸铁:
[σ]=25Mpa。
在中低压液压系统中,按上式计算所得液压缸的壁厚往往很小,使缸体的刚度往往很不够,如在切削加工过程中的变形、安装变形等引起液压缸工作过程卡死或者漏油。
因此一般不作计算,按经验选取,必要时按上式进行校核。
对于,应按材料力学中的厚壁圆筒公式进行壁厚的计算。
对脆性及塑性材料(2-32)取δ=10mm。
式中符号意同前。
液压缸壁厚算出后,即可求出缸体的外径D1为:
=120mm式中D1值应按无缝钢管标准,或按有关标准圆整为标准值。
4.液压缸工作行程的确定液压缸工作行程长度,可根据执行机构实际工作的最大行程来确定。
参照《液压系统设计简明手册》表2—6液压缸活塞行程参数系列尺寸选取标准值,现取行程L=330mm。
5.缸盖厚度的确定一般液压缸多为平底缸盖,其有效厚度t按照强度要求可用下面两式进行近似计算。
无孔时t=11.49mm(2-33)取t=13mm。
有孔时(2-34)取t=15mm。
式中t——缸盖有效厚度(m);
D2——缸盖止口内径(m);
d0——缸盖孔的直径(m)。
6.最小导向长度的确定当活塞杆全部外伸时,从活塞支承面中点的距离H称为最小导向长度。
如果导向长度过小,将使液压缸的初始挠度(间隙引起的挠度)增大,影响液压缸的稳定性,因此设计时必须保证有一定的最小导向长度。
对一般液压缸,最小导向长度应该满足以下要求:
(2-35)即=66.5mm式中L——液压缸的最大行程;
D——液压缸的内径。
活塞的宽度B一般取B=(0.6~1.0)D=60mm;
缸盖滑动支承面的长度l1,根据液压缸内径D而定:
当D80mm时,取l1=(0.6~1.0)d;
因为D=100mm>
80mm,所以l1=(0.6~1.0)d=40mm,为保证最小导向长度H,若过分增大l1和B都是不适宜的,必要时可在缸盖和活塞之间增加一隔套K来增加H的值。
隔套的长度C由需要的最小导长度H决定,即C=1/2(l1-B)H=7mm。
(2-36)7.缸体长度的确定液压缸缸体内部长度应等于活塞的行程与活塞的宽度之和。
缸体外形长度还要考虑到两端端盖的厚度。
一般液压缸缸体长度不应大于内径的2~3倍,即不应大于200~300mm。
2.2.2活塞杆稳定性的计算由于本设计为低压系统,活塞杆稳定性须校核。
活塞杆的强度校核如下:
为了确保拉压杆正常安全的工作,必须使杆内的最大工作应力不超过材料的拉伸或压缩许用应力,已知活塞杆的直径d=63mm,受到最大拉压力Nmax=9000N(2-37)对脆性材料而言,(强度极限,其值为530MPa),且n=2.0~3.5,则:
(2-38)所以,即活塞杆的强度足够。
2.2.3缸体与缸盖的连接形式缸体端部与缸盖的连接形式与工作压力、缸体材料以及工作条件有关。
由《液压系统设计简明手册》表2—7选择螺纹连接方式。
螺纹连接的优缺点如下:
优点:
1)外形尺寸小;
2)重量较轻。
缺点:
1)端部结构复杂;
2)装拆时需用装用工具;
3)拧端盖时易损坏密封圈。
其中右端盖与钢体的连接采用螺母连接(GB/T5782-1986M10×
50)。
其中左端盖与钢体的连接考虑到法兰盘的安装,采用螺钉连接(GB/T68-1985M8×
30)。
1.活塞杆与活塞的连接结构活塞杆与活塞的连接方式可以分为整体式和组合式结构,本设计中采用整体式结构,它结构简单,适用于缸径较小的液压缸。
结构形式由附图所示。
2.活塞杆导向部分的结构活塞杆导向部分的结构,包括活塞杆与端盖、导向套的结构,以及密封、防尘和锁紧装置等。
导向套的结构可以做成端盖整体式直接导向,也可做成与端盖分开的导向套结构。
后者导向套磨损后便于更换,所以应用比较方便。
导向套的位置可安装在密封圈内侧,也可以装在外侧。
机床和工程机械中一般采用装在内侧的结构,有利于导向套的润滑;
而油压机常采用装在外侧的结构,在高压下工作时,使密封圈有足够的油压将唇边张开,以提高密封性能。
活塞杆处的密封形式有O形、V形、Y形、Yx形密封圈。
为了清除活塞杆处外露部分沾浮的灰尘,保证油液清洁及减少磨损,在端盖外侧增加防尘圈。
常用的有无骨架防尘圈和形橡胶密封圈,也可用毛毡圈防尘。
此处活塞杆的导向与密封及防尘装置选用的结构形式为端盖直接导向,该种形式有以下几种特点:
⑴端盖与活塞杆直接接触导向,结构简单,但磨损后只能更换整个端盖;
⑵盖与杆的密封常用O型、Y型、Yx型密封圈;
⑶防尘圈用无骨架的防尘圈。
3.活塞及活塞杆处密封圈的选用活塞及活塞杆处的密封圈的选用,应根据密封的部位、适用的压力、温度、运动速度的范围不同而选择不同类型的密封圈。
在设计该密封圈时选用O形圈,其使用参数如下表2-1所示。
类型密封部位截面简图材料压力范围(Mpa)温度范围(℃)速度范围(m/s)摩擦/泄漏用途活塞活塞杆O形圈√√NBR≤6-30~+130≤0.5中/低通用FPM-15~+180表2-1活塞及活塞杆的O形密封圈使用参数注:
NBR—丁腈橡胶,FPM—氟碳橡胶,√—应用部位。
4.液压缸的缓冲装置液压缸带动工作部件运动时,因运动件的重量较大,运动速度较高,则在到达行程终点时,会产生液压冲击,甚至使活塞与缸筒端盖之间产生机械碰撞。
为防止这种现象的发生,在行程末端设置缓冲装置。
经分析选取环状间隙式节流缓冲装置,活塞端部的缓冲柱塞1向端盖3方向运动进入圆柱形油腔2时,将封闭在柱塞与端盖间的油液从环间隙中挤出去。
由于间隙很小,因而起节流缓冲作用。
适用于运动惯性不大,运动速度不高的液压系统。
5.液压缸的排气装置对于运动速度稳定性要求较高的机床液压缸和大型液压缸,则需要设置排气装置,如排气阀等。
排气装置的结构有多种形式。
该设计中选择,排气阀一般安装在液压缸两端的最高处。
双作用液压缸需装设两个排气阀。
当液压缸需要排气时,打开相应的排气阀,空气连同油液经过锥部缝隙和小孔排出缸外,直至连续排油时,就将排气阀关死。
6.液压缸的安装连接结构
(1)液压缸的安装连接结构包括液压缸的安装结构、液压缸进出油口的连接等。
液压缸的安装形式根据安装位置和工作要求不同现选用长螺栓安装。
液压缸进、出油口形式及大小的确定液压缸的进、出油口,可布置在端盖或缸体上。
对于活塞杆的固定的液压缸,进、出油口可设在活塞杆端部。
如果液压缸无专用的排气装置,进、出油口应设在液压缸的最高处,以便空气能首先从液压缸排出。
进、出油口的形式一般选用螺孔和法兰连接。
因为缸体直径为100mm,查《液压系统设计简明手册》表2-14知单杆液压杆油口安装尺寸为M272。
7.液压缸主要零件的材料和技术要求液压缸主要零件如缸体、活塞、活塞杆、缸盖、导向套的材料和技术要求见表2-2所示。
表2-2液压缸主要零件的材料及技术要求零件名称材料主要表面粗糙度技术要求缸体灰铸铁:
HT200液压缸内圆柱表面粗糙度为Ra0.2~0.4μm内径用H8~H9的配合活塞杆45钢杆外圆柱面粗糙度为Ra0.4~0.8μm材料热处理:
调质20~25HRC;
外径d和d2的圆度、圆柱度不大于直径公差之半缸盖配合表面粗糙度为Ra0.8~1.6μm配合表面粗糙度为Ra0.8~1.6μm配合表面的圆度、圆柱度不大于直径公差之半;
对D的同轴度不大于0.03mm导向青铜导向表面粗糙度为导向套的长度取活塞杆直径60%~80%2.3手臂回转液压缸的尺寸设计与校核2.3.1尺寸设计液压缸长度设计为b=120㎜,液压缸内径为D1=210㎜,半径R=105㎜,轴径D2=40㎜,半径R=20㎜,液压缸运行角速度ω=90°
/s,加速度时间为=0.5s,压强P=0.4MPa,则力矩:
M=