基于PLC的数控加工刀具选择监控系统设计Word文件下载.docx
《基于PLC的数控加工刀具选择监控系统设计Word文件下载.docx》由会员分享,可在线阅读,更多相关《基于PLC的数控加工刀具选择监控系统设计Word文件下载.docx(41页珍藏版)》请在冰豆网上搜索。
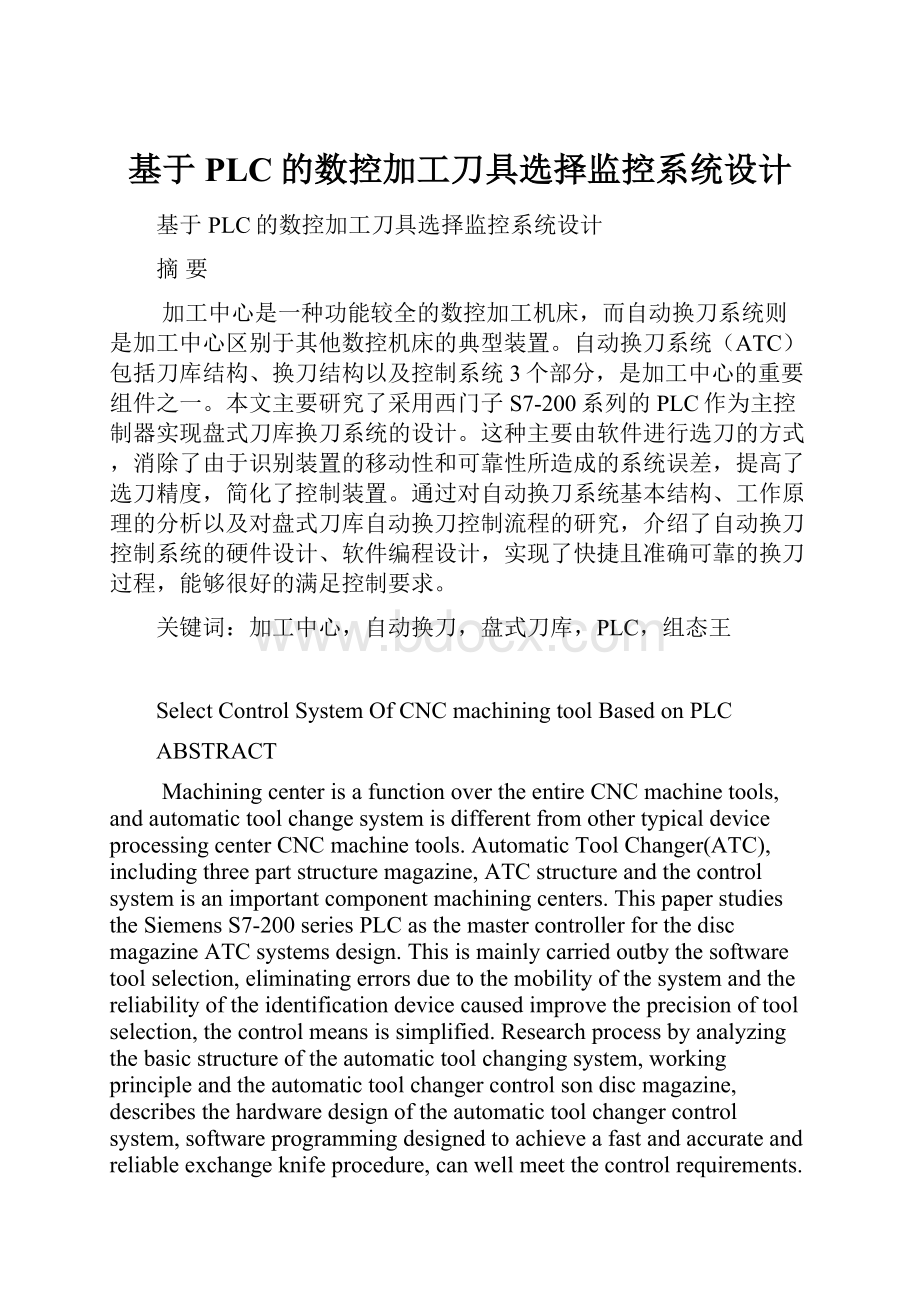
1.1数控加工中心自动换刀系统的背景与意义
1.1.1加工中心的国内外研究动态
工业发达国家对自动换刀系统的研究起始于上世纪50年代。
1956年日本富士通成功研究出数控转塔式冲床,美国MBI公司同期也成功研制了“APT”(刀具程序控制装置),1958年美国K&
T公司首次把铣、钻、镗等多种工序集中于一台数控机床上,通过换刀方式实现连续加工,成功研制了第一台带ATC(自动刀具交换装置)的加工中心。
70年代后,步入机床发展的黄金时代,1983年国际标准化组织制定了数控刀具锥柄的国际标准,自动换刀系统形成了统一的结构模式。
现如今,世界上出现了卧式、立式、落地式、龙门式等各种加工中心,据不完全统计,大约有1000多个品种规格。
目前,德国、日本、奥地利等国家都将自动换刀装置成功应用到高端加工中心上了,采用机械手换刀,刀库布置在主轴周围并可随主轴一起移动,换刀时间仅需0.5s。
相比工业发达国家,我国对加工中心的研究起步较晚,也相对较为落后。
从上世纪80年代起,北京研究所、大连组合机床研究所等先对自动换刀装置开展了研究与开发,其最短换刀时间已达到2s以内。
随着我国工业的快速发展,模具制造业、机械加工业也得到了巨大发展,使得数控机床的使用越来越普遍,而加工中心则是以其高自动化高精度的功能得到了广泛应用。
然而,目前市场上生产和销售的都是以大、中型的数控加工中心为主,小型数控加工中心几乎是空白,而机械加工业、小型模具的制造、工科院校、技工学校等对小型加工中心都存在着大量的需求。
为加速我国加工中心的发展,需进一步加强对加工中心的研究、设计、制造和应用。
1.1.2研究加工中心的目的及意义
加工中心是一种功能较全的数控加工机床,而自动换刀系统则是加工中心区别于其他数控机床的典型装置。
它能够解决工件一次装夹后多工序连续加工中,工序与工序间的刀具自动更换任务,实现了一次装夹完成多种加工,因而可减少工序装夹、测量和调整时间,减少工序周转及搬运存放时间,大大的提高了加工效率,缩短了生产周期,并保证加工精度。
数控加工刀具选择监控系统的研究具有重要的价值:
取代了传统复杂的控制设计,减少了操作者的劳动强度,降低了生产成本;
缩短了加工时间,提高了工作效率;
使得经济效率得以提高,有利于生产管理的现代化。
1.2数控加工中心自动换刀系统的结构类型
1.2.1自动换刀装置的结构特点
加工中心的自动换刀装置(ATC)由刀库和机械手组成,能使加工中心在工件一次装夹中完成多种甚至所有加工工序,它能缩短辅助时间,减少多次安装工件所引起的误差,提高产品的加工精度。
自动换刀装置性能的好坏将影响整个加工中心的好坏,因此自动换刀装置必须满足刀具储存量足够、刀具定位精度高、刀具库占地面积小、换刀时间短以及安全可靠等控制要求。
刀库的类型和容量主要是为了满足数控机床的工艺范围,目前常用的刀库类型如下:
(1)盘式刀库此刀库结构简单,应用较为广泛。
此换刀装置的特点是结构简单,成本较低,换刀安全可靠性较好,不足之处是刀库呈环形排列,空间利用率低,换刀时间长,适用于刀库容量较小的加工中心上采用。
(2)链式刀库此刀库结构精密,刀库容量较大,链环的形状可根据数控机床的布局制成各种形状,也可将换刀位突出以便于换刀,能充分利用数控机床的占地空间,但此类换刀装置通常为轴向取刀,定位精度较低,成本也较高。
(3)格子箱式刀库此刀库结构设计紧凑,刀库空间利用率高。
但换刀时间较长,且布局不灵活,通常刀库安装在工作台上,应用者较少。
当前常用的换刀机械手类型有:
(1)单臂单手式机械手其结构较为简单,各种换刀动作都需要按顺序进行,且不能重合,因此换刀时间也较长。
(2)双手式机械手其结构紧凑,对刀库的还刀动作和取刀动作,均可在主轴正在加工时进行,因此换刀时间较短。
(3)回转式单臂双手机械手此类机械手可以同时抓住和拔、插位于主轴和刀库里的刀具。
与单臂单手式机械手相比,可以缩短换刀时间。
应用最为广泛,形式也较多。
1.2.2自动换刀系统的设计形式
根据自动换刀系统设计的控制要求可知,系统主要研究刀库的选刀、送刀过程即系统软件信号的接收以及步进电机控制刀库的正反转。
关于机械手的控制在此不多做研究。
本设计中刀库只需容纳六把刀具,故刀库类型采用盘式刀库,结构简单易于控制。
软件设计采用西门子S7-200系列为主控制器来实现。
六把道具以此在盘式刀库上环形排列,根据刀库的正反转将要进行交换的刀具以较短路径送至机械手位置,以此完成自动换刀动作。
数控加工中心刀具库选择转盘示意图如图1-1所示。
图1-1数控加工中心刀具库选择转盘示意图
如图1-1所示,数控加工中心刀具库由六把刀具组成,按钮SB1-SB6分别是六种刀具的选择按钮,ST1-ST6为刀具的到位行程开关。
加工中心的工作过程:
在初始状态时,PLC记录当前处于机械手位置的刀具号VW0;
当按下按钮SB1-SB6时中的任意一个时,PLC记录该请求交换刀具号VW10;
根据VW0与VW10的大小比较以及一系列的运算,确定步进电机控制刀盘进行正转或反转以使刀盘能够按照离请求交换刀号最近的方向转动;
当请求刀具到达换到位置时刀盘停止转动,到位指示灯亮,机械手开始换刀,同时换刀指示灯闪烁;
5s之后换刀结束,换到完毕后,PLC再次记录当前刀号,等待下一次换刀请求。
需要注意的是换刀过程中,其他的换刀请求信号均无效。
由加工中心的工作过程可知刀具选择监控系统的大致控制框架,系统控制框图如图1-2所示。
图1-2系统控制框图
1.3PLC的简介
1.3.1PLC的工作原理及特点
可编程逻辑控制器实质上是一种专用于工业控制的计算机,其硬件结构基本上与微型计算机相同,基本结构主要有电源、中央处理单元(CPU)、存储器、输入输出接口电路、编程器、功能模块以及通信模块等部分组成。
可编程逻辑控制器有两种基本工作状态,即运行(RUN)状态和停止(STOP)状态。
也就是说PLC的工作原理是循环扫描的方式。
当PLC工作在停止状态时,其扫描过程包括内部处理和通信处理两个阶段;
当PLC工作在运行状态时,其扫描过程包括输入处理、程序执行和输出处理三个阶段。
PLC具有一下比较鲜明的功能特点:
(1)可靠性高,抗干扰能力强。
(2)编程容易,简单易学。
(3)功能完善,使用方便。
(4)设计、安装、调试工作量小。
(5)体积小,质量轻,能耗低。
1.3.2PLC的型号
PLC的选择主要应从PLC的机型、容量、I/O模块、电源模块、特殊功能模块、通信连网能力等方面加以综合考虑。
PLC机型的选择是在满足功能要求及保证可靠、维护简便的前提下,力争最佳的性能价格。
在此次设计中采用西门子S7-200系列的PLC作为主控制器。
接下来主要是针对S7-200系列的PLC进行简单的介绍。
西门子S7-200PLC在实时模式下具有速度快,具有通讯功能和较高的生产力的特点,在集散自动化系统中充分发挥其强大作用。
使用范围可涵盖从替代传统继电接触器的简单控制到单片机或更复杂的自动化控制。
应用领域极为广泛,覆盖所有与自动检测,自动化控制有关的工业及民用领域,包括各种机床、机械、电力设施、民用设施、环境保护设备等等。
S7-200系列PLC可提供4个不同的基本型号的8种CPU供选择使用。
CPU规格是CPU221、CPU222、CPU224和CPU226,且CPU221~226各有2种类型CPU,具有不同的电源电压和控制电压。
开关量输入和输出点:
CPU221具有6个输入点和4个输出点,CPU222具有8个输入点和6个输出点,CPU224具有14个输入点和10个输出点。
CPU226具有24个输入点和16个输出点。
西门子S7-200系列PLC具有非常出色的特点:
(1)强大的性能,极高的可靠性。
(2)丰富的指令集,且简单易于掌握。
(3)大容量程序和数据存储器。
(4)优秀的实时特性,在任何时候均可对整个过程进行完全控制。
(5)高质量、高效率。
(6)使用STEP7-Micro/WIN工程软件进行调试较为简便。
(7)极其快速和精确的操作顺序和过程控制。
第2章硬件设计
2.1硬件设备的选型
2.1.1按钮开关
按钮开关是一种结构简单、应用广泛的主令电器。
在电器控制线路中用于远距离手动发出控制信号以控制继电器、接触器、电磁启动器等。
本设计选择型号为LA19—11A/D的按钮开关,额定工作电压:
380VAC,额定工作电流:
0.79A,额定发热电流:
5A。
2.1.2行程开关
行程开关也成为位置开关、限位开关,是用于反映机械设备的行程、发布命令以控制其运动方向和行程大小的主令电器。
行程开关主要分为接触式结构和电子非接触式结构两大类。
本设计使用的电子非接触式由霍尔元件构成的行程开关。
其工作原理是利用霍尔元件由于磁性物质的靠近而产生的霍尔效应使开关内部电路状态发生变化,由此识别附近有磁性物体存在,进而控制开关的通或断。
选择型号为LX19K的行程开关,额定工作电压:
5A,动作行程:
1.5~3.5mm。
2.1.3接触器
接触器是用于远距离频繁接通和分断交直流主回路及大容量用电回路的低压控制电器,是电力拖动和自动控制系统中最常用的控制电器之一,主要控制对象是电动机,实现其启停、正反转、制动以及调速等控制功能。
交流接触器利用主触头来开断主电路,用辅助触头来通断控制回路。
主触头一般是敞开触头,而辅助触头常用两对常开触头和常闭触头。
交流接触器的接点,由银钨合金制成,具有良好的导电性和耐高温性。
交流接触器的动力源来自带铁芯线圈通以交流电产生的交变磁场,电磁铁芯由两个「山」字形的硅钢片叠成。
其中一个固定铁芯绕有线圈,额定工作电压根据不同情况可进行多种选择。
由于电磁吸力瞬时值是脉动的,要在铁芯端面安装一个铜制的短路环,避免震动和噪声,以使电磁机构稳定工作。
另一个是活动铁芯,构造和固定铁芯一样,用以带动主触点和辅助触点的通断。
本设计采用型号为西门子3TF47的交流接触器,工作电压:
220V,额定电流:
63A。
3TF系列交流接触器为交流50Hz或60Hz,额定绝缘电压为690-1000V,在AC-3使用类别下额定工作电压为380V时的额定工作电流为9A-400A,主要供远距离接通及分断电路之用,适用于控制交流电动机的起动、停止及反转。
西门子3TF47交流接触器如图2-1所示。
图2-1西门子3TF47交流接触器
2.1.4驱动刀库电机选型
在刀盘旋转过程中,驱动刀库电机需要频繁的启动、制动、正转、反转,经常工作在重点短时状态、电动状态、制动状态下,对电机要求较高。
根据工作性质,应使电动机有以下特点:
能频繁的制动启动而且启动电流较小;
要有发电制动的特性以及较硬的机械特性;
电动机运转较为平稳,工作可靠性高,运行噪声低。
普通交流感应电动机的启动电流以及转矩较大,难以满足要求。
在此,刀库的驱动电机使用交流异步电动机,用行程开关检测,此种驱动方式相较于液压马达驱动运行稳定,定位准确、可靠,换刀速度快。
本设计驱动刀库电机选型为Y7-712-2,额定电压:
220V,额定功率:
0.55KW,额定转速:
2800rpm,效率高,节能效果好,启动转矩大,噪声震动较小。
Y7-712-2型异步电动机如图2-2所示。
图2-2Y7-712-2型异步电动机
电动机主要控制刀盘的正反转,以实现所选刀具能以较短路径输送到机械手换刀位置的功能,驱动刀库电机正反转主电路如图2-3所示。
图2-2驱动电动机主电路
2.1.5熔断器的选择
熔断器选择RT14系列的高分断能力有填料圆柱型熔断体。
产品型号有RT14-20、RT14-32、RT14-63。
RT14系列高分断能力有填料圆柱型熔断器符合GB13539、IEC60269、VDE0636标准。
适用于交流50Hz,额定电压交流380/500V,额定电流至63A的配电线路中,作过载和短路保护。
(变压器保护或电动机保护)
。
由上述对主要元器件的分析以及型号的选择可以列出本设计所用到的主要电气元件,电气元件明细表如表2-1所示。
表2-1电气元件明细表
序号
符号
名称
规格
数量
单位
备注
1
M
电动机
Y2-712-2
台
刀库转台的正反转
2
KM
接触器
3TF47
3
只
控制电机正反转
ST
行程开关
LX19K
6
刀具到位检测
4
SB
按钮开关
LA19-11A/D
刀具选择
5
HL
指示灯
---
到位指示和换刀闪烁
PLC
可编程逻辑控制器
S7-200
CPU226
系统自动控制器,24入/16出,AC220V
7
FU
熔断器
RT14-32
过载和短路保护
2.2加工中心刀具库的I/O资源配置
2.2.1刀具库I/O点分配
通过对数控加工中心刀具选择系统控制要求的分析,可知自动换刀系统的控制流程,由此得出系统的I/O点分配资源。
I/O点分配表如表2-2所示。
表2-2I/O点分配表
输入
输出
元器件名
对应I/O点
刀
具
选
择
按
钮
SB1
I0.0
到位指示灯
HL1
Q0.0
SB2
I0.1
换刀指示灯
HL2
Q0.1
SB3
I0.2
刀库正转
KM1
Q0.2
SB4
I0.3
刀库反转
KM2
Q0.3
SB5
I0.4
换刀
KM3
Q0.4
SB6
I0.5
到
位
行
程
开
关
ST1
I1.0
ST2
I1.1
ST3
I1.2
ST4
I1.3
ST5
I1.4
ST6
I1.5
由上表可知PLC有14个输入点5个输出点,因此选用PLC时可选用西门子S7-200CPU226,输入点24,输出点16,并留有一定的裕量。
2.2.2刀具库I/O外部接线图
由系统的I/O资源分配可以绘出控制系统外部接线图。
系统I/O外部接线图如图2-4所示。
图2-4I/O外部接线图
第3章软件设计
3.1自动换刀控制系统的组成
自动换刀控制系统主要包含选刀系统、送刀系统以及换刀系统。
选刀系统是经过接收外部输入信号,使PLC识别信号并记录所选刀具号,为输送刀具的方向确定做准备。
送刀系统是根据检测位置的刀具号与所要交换刀具号的比较运算确定刀盘的正反转,即输送刀具的方向使其输送路径最短以缩短时间。
换刀系统主要是控制机械手的动作来完成的,机械手在刀库与主轴之间进行取刀、换刀。
在本设计中主要分析选刀系统以及送刀系统,机械手控制部分不多做分析。
3.2自动换刀控制系统的原理分析
3.2.1系统控制要求
加工中心刀库处于初始状态时,使PLC记录当前置于机械手取刀位置的刀具号,当有换刀命令即按下按钮SB1~SB6中的任何一个时,PLC记录请求交换的刀具号,根据两次记录刀具号的比较大小运算,确定刀盘按照请求交换刀具离机械手最近的方向转动即实现最短距离送刀以缩短送刀时间,刀盘的转动由驱动电机的正反转来实现,当所请求交换刀具转到机械手位置时,刀盘停止转动,到位指示灯亮起,机械手开始换刀,同时换刀指示灯闪烁,5s之后,换刀结束。
需要注意的是,在进行换刀过程中,其他换刀请求命令均无效。
一次换刀结束后,记录当前刀具号,等待下一次的换刀请求。
3.2.2控制流程
经过对加工中心工作原理的分析,可知数控加工中心刀具选择监控系统的程序流程图如图3-1所示。
图3-1程序流程图
3.3编程软件STEP7Micro/WIN概述
STEP7Micro/WIN编程软件是西门子公司专为S7-200系列PLC设计开发的编程软件。
进行S7-200PLC编程时,单击编程软件安装图标,进入如图3-3所示的操作界面。
图3-3STEP7Micro/WIN操作界面
STEP7Micro/WIN编程软件由SIMATIC管理器、符号编辑器、通信组态、硬件组态、编程语言、硬件诊断工具等部分组成。
SIMATIC管理器可以浏览SIMATICS7、M7、C7的所有工具软件和数据。
符号编辑器可以管理所有的全局变量,可用来定义符号名称、数据类型以及全局变量的诠释。
编程语言包含功能块图语言(FBD)、梯形图语言(LAD)以及指令表语言(STL)。
功能块图语言(FBD)是基于数字电子电路设计演变的,类似于与门、或门的方框图来表示逻辑运算关系的一种编程语言,其中功能方框图的左侧是操作变量,右侧是操作结果输出,信号也是从左流向右的,方框图内的符号表达了该框内的运算功能。
梯形图语言(LAD)是使用最多的PLC图形编程语言,沿用了传统电器控制系统控制图中继电器的触点、线圈、串并联等术语和图形符号,并在此基础上增添了继电接触器控制系统中没有的指令符号,不仅实现了逻辑运算,还具备了算术运算、数据处理以及联网通信等功能。
梯形图的特点主要有以下几点:
(1)梯形图自上而下按行绘制,最左边竖线为母线,从左至右依次连接触点,最后以继电器线圈输出结束,且继电器线圈只能并联不能串联。
(2)梯形图中编程元件所使用的内部继电器以及定时/计数器等都是由软件实现的。
(3)其优点是形象直观,编程容易,简单易学,后期修改也较为简便。
与传统继电接触控制系统的控制原理有一定的对应性,这比较有益于电气技术设计者的掌握学习。
指令表语言(STL)是一种符号编程,用来表示PLC各种功能的缩写符号和相应的器件编号组成的程序表达方式。
但指令表符号也会由于生产厂家的不同而有所不同。
在如图3-3所示的STEP7Micro/WIN编程软件的操作界面单击File--New即可在新建的命令窗口写入编程语言,在STEP7Micro/WIN的三个编辑器即FBD、LAD、STL中的任何一个进行编程都可以在其它两个编辑器中进行浏览和编译,编程语言可相互转换。
本设计中采用梯形图语言进行编程,并转化成指令表语言表示。
3.4自动换刀系统的PLC程序设计
3.4.1程序梯形图
根据控制要求,设计出的数控加工中心刀