塑料套注塑成型工艺与模具设计解析Word下载.docx
《塑料套注塑成型工艺与模具设计解析Word下载.docx》由会员分享,可在线阅读,更多相关《塑料套注塑成型工艺与模具设计解析Word下载.docx(43页珍藏版)》请在冰豆网上搜索。
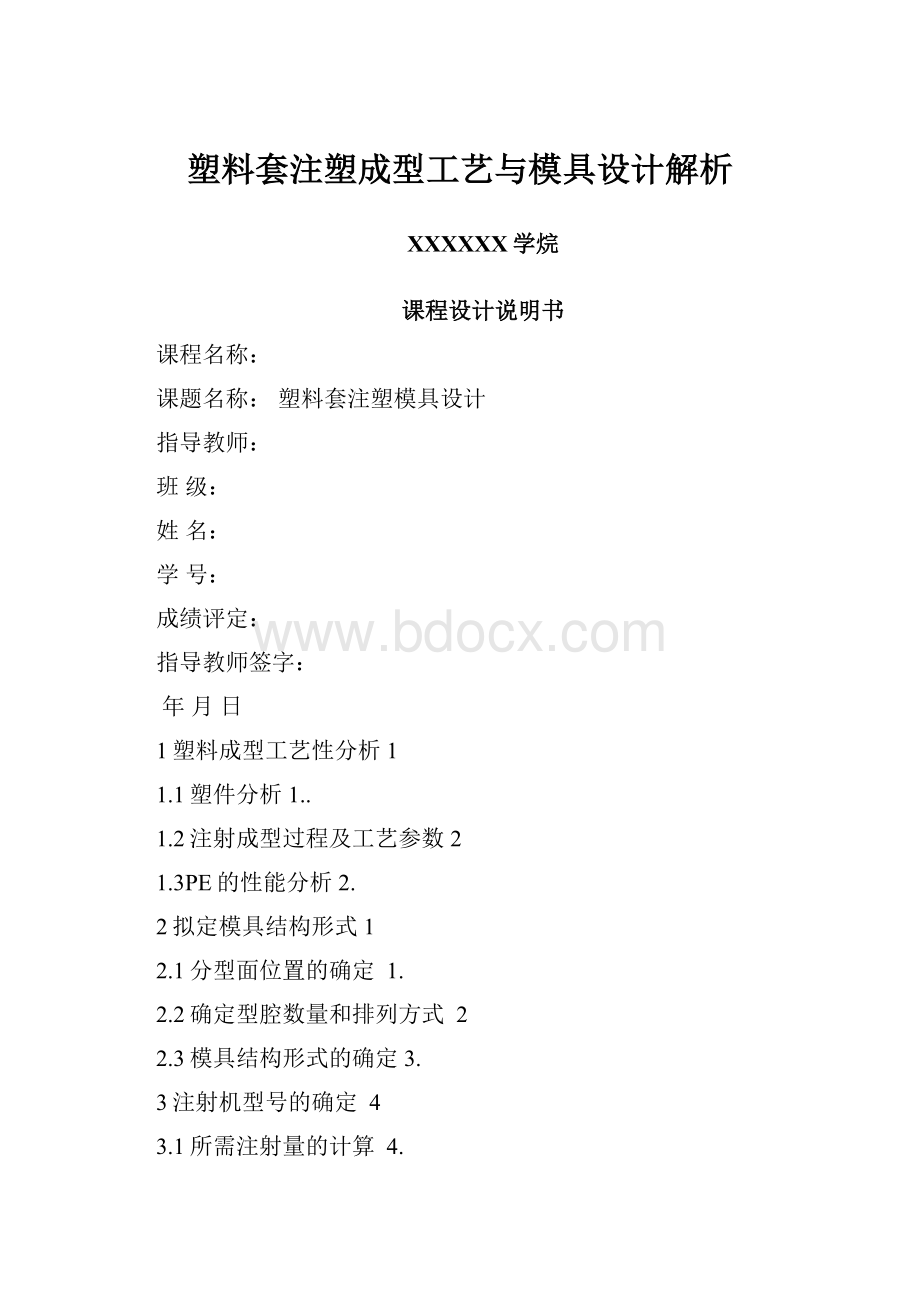
分析该塑料可知,本塑料套为阶级圆筒直壁塑件,中间为一台阶,而且有一个31的圆环,周边是四个加强筋。
该塑件为塑料套,所用材料为PE,无颜色要求,生产批量为中批量。
由塑件图分析可知,精度未注,采用一般经济级精度6级。
所用塑料为聚丙烯,该塑料流动性好,注射充型流动平稳,塑件外设置有脱模斜度,脱模斜度为30'
-1°
1.2注射成型过程及工艺参数
聚乙烯为典型的热塑性塑料,是无臭、无味、无毒的可燃性白色粉末。
成型加工的PE树脂均是经挤出造粒的蜡状颗粒料,外观呈乳白色。
其分子量在1万一loa万
范围内。
分子量超过10万的则为超高分子量聚乙烯fUHMWPE3o分子量越高,其物理力学性能越好,越接近工程材料的要求水平。
但分子量越高,其加工的难度也随之增大。
聚乙烯熔点为10---130C其耐低温性能优良。
在一60C下仍可保持良好的力学性能,但使用温度在80~110C。
聚乙烯化学稳定性较好,室温下可耐稀硝酸、稀硫酸和任何浓度的盐酸、氢氟酸、磷酸、甲酸、醋酸、氨水、胺类、过氧化氢、氢氧化钠、氢氧化钾等溶液。
但不耐强氧化的腐蚀,如发烟硫酸浓硝酸、铬酸与硫酸的混合液。
在室温下上述溶剂会对聚乙烯产生缓慢的侵蚀作用,而在90---100C下,浓硫酸和浓硝酸会快速地侵蚀聚乙烯,使其破坏或分解。
聚乙烯在大气、阳光和氧的作用下,会发生老化,变色、龟裂、变脆或粉化,丧失其力学性能。
在成型加工温度下,也会因氧化作用,使其熔体戮度下降,发生变色、出现条纹,故而在成型加工和使用过程或选材时应予以注意。
正因为聚乙烯拥有如上特质,容易加工成型,因此聚乙烯的再生回收具有非常深远的价值。
[2]注射工艺参
数
表1-1PE注射工艺参数
注射成型机类型
螺杆式
转速
(30~60)r/min
料筒温度
后段160~170C
中段200~220
前段180~200
喷嘴温度
250~260C
模具温度
40~80C
喷嘴形式
直通式
注射压力
70~120Mpa
保压力
50~60MPa
注射时间
0~5s
成型周期
40~120s
保压时间
20~60s
冷却时间
15~50s
注:
源自参考文献[1]中的表4-18
1.3PE的性能分析
使用性能
聚乙烯为白色蜡状半透明材料,柔而韧,比水轻,无毒,具有优越的介电性能。
易燃烧且离火后继续燃烧。
透水率低,对有机蒸汽透过率则较大。
聚乙烯的透明度随结晶度增加而下降在一定结晶度下,透明度随分子量增大而提高。
高密度聚乙烯熔点范围为132-135C,低密度聚乙烯熔点较低(112C)且范围宽。
常温下不溶于任何已知溶剂中,70C以上可少量溶解于甲苯、乙酸戊酯、三氯乙烯等溶剂中。
2拟定模具结构形式
2.1分型面位置的确定
在塑件设计阶段,就应该考虑成型时分型面的形状数量,否则就无法用模具成型。
在模具设计阶段,应首先确定分型面的位置,然后才选择模具的结构。
分型面选择是否合理,对塑件质量工艺,操作难易程度和模具设计制造有很大影响。
因此分型面的选择是注射模设计中的一个关键因素。
1)分型面的选择原则⑴:
(1)分型面的选择应便于塑件脱模和简化模具结构,选择分型面应尽量使塑件开
模时留在动模;
(2)分型面应尽可能选择在不影响外观的部位,并使其产生的溢料边易于消除和
修整;
(3)分型面的选择应保证塑件尺寸精度;
(4)分型面选择应有利于排气;
(5)分型面选择应便于模具零件的加工;
(6)分型面选择应考虑注射机的规格
2)分型面的选择方案
(1)分型面选择方案I。
分型面与开模方向垂直,位置选在直径为33的端面如
图2-1所示,动模上的型芯凸出,开模后,塑件包紧型芯,留于动模,然后采用脱模板将塑件推出,整个塑件成型精度较高,模具也比较简单。
1
图2-1分型面形式与位置
1—动模部分2一分型面
3疋模部分
(2)分型面选择方案U。
分型面与开模方向垂直,位置选在直径为33与25
的相交处如图2-2所示,33和.25分别在动模和定模内成型,这将由于合模误差不
利于保证其同轴度要求。
采用圆筒形推杆将塑件推出,整个塑件成型精度较方案I低,模具也较方案I复杂。
图2-2分型面形式与位置
1—定模部分2—分型面
3一动模部分
综上所述,分型面选择方案I,模具结构相对简单,塑件成型精度可靠,因此采用方案I。
2.2确定型腔数量和排列方式
该塑件为小型塑件,精度要求不高,又是中等批量生产,可以采用一模多腔的形式。
考虑到模具制造费用、设备运转费用低一些,初定为一模四腔的模具形式。
如图2-3所示。
图2-3型腔的排列
2.3模具结构形式的确定
从上面分析中可知,本模具拟采用一模四腔,推件板推出,流道采用平衡式,浇口采用侧浇口,定模不需要设置分型面,动模部分需要一块型芯固定板和支撑板,因此基本上确定模具结构形式为A4型带推件板的单分型面注射模。
3注射机型号的确定
3.1所需注射量的计算
1)塑件质量、体积计算
对于该设计,提供了塑件图样,据此建立塑件模型并对此模型用建模分析得:
塑件体积V8.64cm3
塑件质量m,=讦=0.918.64:
7.902g
2)浇注系统凝料体积的初步估算
可按塑件体积的0.6倍估算,由于该模具采用一模四腔,所以浇注系统凝料体积为
V2=4乂0.6=48.640.620.736cm3
3)该模具一次注射所需塑料PE
体积V。
=4V,V2=48.6420.736二55.296cm3
质量m0=20=0.9155.296=50.32g
3.2注射机型号的选定
根据以上的计算初步选定型号为XS-ZY-125,型卧式注射机,查表⑵其主要技术
参数见表3-1o
表3-1XS-ZY-125型注射机主要技术参数
额定注射量
3
125cm
锁模力
900KN
螺杆直径
42mm
拉杆内间距
260x360mm
额定注射压力
150MPa
最大开模仃程
300mm
1.8s
最大模具厚度
塑化能力
50kg/h
最小模具厚度
200mm
螺杆转速
10〜140r/min
定位孔直径
©
100mm
喷嘴球半径
SR12mm
喷嘴孔直径
4mm
合模方式
液压-机械
该注射机由上海塑料机械厂生产
3.3型腔数量及注射机有关工艺参数校核
1)型腔数量的校核
(1)按注射机的最大注射量校核型腔数量
KVg-Vj
n—
Vn
式中K——注射机最大注射量的利用系数,结晶型塑料一般取0.8;
Vg——注射机允许的最大注射量,Vg=125cm3;
Vj——浇注系统所需要的塑件体积,Vj=20.736cm3;
Vn单个塑件的质量或体积,Vn=8.64g;
0.8125-20736
(2)由注射机料筒塑化速率校核型腔数量
KMt-m2
m-i
M——注射机的额定塑化量,该注射机为50kg/h=13.89g/s;
t——成型周期,因塑件小,壁厚不大,取50s;
mi单个塑件的质量和体积,取m18.64g;
m浇注系统所需塑件质量和体积,取0.64m-。
上式中左边=4;
右边=0.813・8950一°
.648.6仁6.19
8.64
满足要求
2)注射机工艺参数的校核
(1)注射量的校核
注射量以容积表示,最大注射容积为
Vma^aV=0.75125二93.75cm
式中VmaX模具型腔和流道的最大容积;
V-指定型号与规格的注射机注射量容积,该注射机为125cm3;
a——注射系数,取0.75~0.85,无定型塑料取0.85,结晶型塑料取0.75,该处取0.75。
倘若实际注射量过小,注射机的塑化能力得不到发挥,塑件在料筒中停留的时间就会过长。
所以最小注射容积Vmin=0.257=0.25125=31.25cm3。
故每次注射的实际注射容积V•应满足Vmin;
:
:
Vg:
Vmax,而乂55.296cm‘,符合要求。
(2)锁模力的校核
当高压的塑料熔体充满型腔时,会产生一个沿注射机轴向的很大推力T推,其大
小等于制件浇注系统在分型面上的垂直投影面积之和乘以型腔内塑料熔体的平均压力。
该推力应小于注射机额定的锁模力T合,否则在注射成型时会因锁模不紧而发生
溢边跑料现象。
型腔内塑料熔体的推力T推:
丁推=A卩平均一A=Akpo
式中T推型腔内塑料熔体沿注射机轴向的推力;
A——塑料与浇注系统在分型面上积投影面积;
P平均——型腔内塑料熔体的平均压力,一般是注射压力的30%~50%,PE流动性好,所薄壁容器类,取型腔平均压力为50Mpa;
P型腔内塑料熔体的压力;
Po注射压力;
K——压力损失系数,可在0.2~0.4的范围内选取,此处选0.4。
上式左边=50A乞60A=右边,符合要求。
(3)最大注射压力校核注射机的额定注射压力即为该机器的最高压力Pmax=150MPa(见表3-1),应该
大于注射成型是所需调用的注射压力P0,即
Pmax-kR式中「——安全系数,常取k'
1.25〜1.4。
R——注射成型是所需调用的注射压力
实际生产中,该塑件成型时所需注射压力P。
为70~120Mpa由于选用的是螺杆式
注射机,其注射压力的传递比柱塞式要好,同时PE流动性好,因此注射压力P。
选用90Mpa。
代值计算:
左边=150MPa右边=1.2590~1.490=112.5〜140MPa
符合要求。
3)安装尺寸校核
(1)喷嘴尺寸
1主流道的小端直径D大于注射机喷嘴d,通常为
D=d(0.5〜1)mm
对于该模具d=4mm,取D=5mm,符合要求。
2主流道入口的凹球面半径SF0应大于注射机注射机喷嘴球半径SR,通常为
SR二SR(1~2)mm
对于该模具SR=12mm,取SF0=13mm,符合要求。
(2)最大与最小模具厚度
模具厚度H应满足Hmin:
H:
Hmax
式中Hmin=200mm,Hmax=300mm
而该套模具厚度H-25502532406325=260mm,符合要求。
4)开模行程和推出机构的校核
(1)开模行程的校核
H_出H2(5~10)mm
式中H——注射机动模板的开模行程,取300mm,见表3-1;
出——塑件推出行程,取22.5mm;
H2——包括流道凝料在内的塑件高度为80mm
其值为H_8022.5(5~10^107.5mm~112.5mm,符合要求
(2)推出机构的校核
该塑件的推出行程为22.5mm小于注射的机推出行程,符合要求。
5)模架尺寸与注射机拉杆内间距校核
该套模具模架的外形尺寸为250mm250mm,而注射机拉杆内间距为
260mm360mm,因360mm>
250mm,符合要求。
对上面2、3、4、5的校核内容是与后面的模具结构设计交叉进行的。
4浇注系统的形式和浇口的设计
浇注系统是引导塑料熔体从注射机喷嘴到模具型腔的进料通道,具有传质、传压和传热的功能,对塑料质量影响很大。
它分为普通流道浇注系统和热流道浇注系统。
该模具采用普通流道浇注系统,包括主流道、分流道、冷料穴和浇口。
4.1主流道的设计
主流道置于模具中心塑料熔体的入口处,它将注射机喷嘴射出的熔体导入分流道
或型腔中。
主流道的形状为圆锥形,以便于熔体的流动和开模时主流道凝料的顺利拔出。
1)主流道尺寸
(1)主流道小端直径
d=注射机喷嘴直径(0.5~1二4(0.5~1)
取D=5mm。
(2)主流道球面半径
S&
二注射机喷嘴球头半径(1~2)12■(1~2)
取SR)=13mm。
(3)球面配合高度
h=3mm~5mm。
取h=3mm
(4)主流道长度
由标准模架结合该塑料制件的结构决定
取L=80mm
(5)主流道大端直径
D=d+2LtaZ拓5+2江80"
a2s=8.4mm(半锥角。
为1,~2,取=2:
)
取D=8.5mm。
(6)浇口套总长
L0=2550h2=80mm。
2)主流道衬套的形式
主流道小端入口处与注射机反复接触,属易损件,对材料要求较严。
因而模具主流道部分常设计成可拆卸更换的主流道衬套形式即浇口套,以便有效的选用优质的钢
材单独进行加工和热处理,采用碳素工具钢T10A热处理硬度为50HRC~55HRC,如
图4-1所示。
图4-1主流道衬套
由于该模具主流道较长,定位圈和衬套设计成分体式较宜,其定位圈结构尺寸如图4-2所示。
图4-2定位圈
3)主流道衬套的固定主流道衬套的固定形式如图4-3所示。
4-3主流道衬套的固定形式
4.2冷料穴的设计
冷料穴的作用是贮存两次注射间隔而产生的冷料及熔体流动前锋冷料,以防止熔
体冷料进入型腔。
冷料穴一般设置在主流道的末端,当分流道较长时,在分流道的末端有时也设冷料穴。
同时冷料穴兼有分模时将主流道凝料从主流道衬套中拉出并滞留在动模一侧。
本设计采用推板脱模机构,由于PE的弹性很强,故采用沟形头冷料穴,结构如图4-4所示。
图4-4冷料穴图
4.3分流道的设计
1)分流道的布置形式
在分型面上与前面所述型腔排列密切相关,有多种不同的形式,但应遵循两个方面的原则:
一是排列紧凑,缩小模板尺寸,二是流程尽量短,锁模力均匀。
该流道布置采用平衡式
2)分流道的长度
长度应尽可能短,结合模具尺寸结构,取分流道长度L=30mm
3)分流道形状及尺寸
圆形分流道截面积虽然效率高,但其是以分型面为界分成两半进行加工才利于凝
料脱出,因而其加工工艺性不佳,不予采用。
许多模具设计采用梯形截面,加工工艺
性好,且塑料熔体的热量散失,流动阻力均不大,一般采用如下公式(参考文献⑻公
式5-5,5-6)可确定截面尺寸,即
B=0.2654m4L
H:
2/3B
式中B梯形大底面的宽度(mm)
m塑件质量(g)
L——分流道的长度(mm)
H——梯形高度
上述公式的适用范围,塑件厚度在3mm以下,质量小于200g,且B的计算结果在3.2-9.5mm才合理。
由于B=0.2654.m4L二0.26457.902470:
2.15mm,不在适用范围,需自
行设计。
分流道设计为梯形,由参考文献⑵中图9.2-12(分流道直径尺寸曲线一)和参考文献⑻中(常用分流道形状及尺寸)取得分流道直径D'
4.1mm,考虑到分流道长度
系数fL=1.1,所以修正后分流道直径为D二fLD=4.51mm,圆整为4.5mm。
梯形斜角通常取5~10,此处取6;
底部圆角R=1mm~3mm,取R=1mm。
其截面形状及尺寸如图4-6所示。
宀
一皿
L
■
图4-6分流道截面形状及尺寸
4)分流道表面粗糙度
分流道表面不要求太光洁,表面粗糙度常取Ra=1.25-25^,这可增加对外层塑料熔体流动阻力,使外层塑料冷却塑料皮层固定形成绝热层,有利于保温。
此处取
Ra二1.5丄m。
5)分流道与浇口连接形式
分流道与浇口采用斜向与圆弧连接,这样有利于塑料的流动与填充,防止塑料流动产生反压力,消耗动能。
4.4浇口的设计
浇口是连接流道与型腔之间的一段细短通道,是浇注系统的关键部分,起着调节控制料流速度,补料时间及防止倒流等作用。
浇口的形状、尺寸、位置对塑件的质量产生很大的影响。
1)类型及位置的确定
该模具是中小型塑件的多型腔模具,同时从所提供塑件图样中可看出,在底部?
36的圆周上设置浇口比较合适。
类型选用常用的侧浇口,这类浇口加工容易,修整方便,并且可以根据塑件的形状特征灵活选择进料位置。
2)浇口结构尺寸的经验计算
矩形侧浇口的大小由其厚度,宽度和长度决定(参考文献⑴式6-5,6-6)
h=ntb=止
30
式中h——侧浇口厚度(mm)
b——侧浇口宽度(mm)
t塑件壁厚(mm)
n与塑料品种有关的系数,查文献⑴表6-4得n=0.7
A塑件外表面积(mm)
代入数据得h=0.7X2.5=1.75mm。
浇口长度取L=1.0mm
4.5浇注系统的平衡
对于该模具,从主流道到各个型腔和分流道的长度相等,形状及截面尺寸相同,各个浇口也相同,浇注系统显然是平衡的。
4.6浇注系统凝料体积的计算
1)主流道与主流道冷料井凝料体积
兀了5+10孑”兀21433
7主=V推"
^冷=ih+"
12汇4.5—汇兀汇5=2631mm3
4i2丿423
该值远小于前面对浇注系统凝料体积的估算,所以前面有关浇注系统的各项计算与校核符合要求,不需要重新设计计算。
4.7浇注系统各截面流过熔体的体积计算
1)流过浇口的体积
Vg=V塑=8.64cm
2)流过分流道的体积
VR=V塑■7橈二4.31■8.64=12.95cm
3)流过主流道的体积
Vs=4VrV主=54.43cm
4.8普通浇注系统截面尺寸的计算与校核
1)确定适当的剪切速率
根据经验浇注系统各段的•取以下值,所成型塑件质量较好
(1)
主浇道
s=5102s°
~5103s"
⑵
分浇道
r=5102s」
⑶
浇口
gMs」
⑷
其他浇口
—5103s'
~5104sJ
2)
确疋体积流量
1)
主浇道体积流量qs
主流道体积体积流率并不大,取;
=2103s,
.3•…333
qs
亍s蔦0・2521。
a.33cm/s
2)浇口体积流量qG
侧浇口用适当的剪切速率G=1104s4代入得
2
=8.44cm/s
3)注射时间的计算
(1)模具充模时间
ts
Vs
牛2.08s
24.33
(2)单个型腔充模时间
tG
Vg
qG
d"
14s
(3)注射时间
根据经验公式求得注射时间
t=ts/32tG/3=1.45s
校核各处剪切速率
浇口剪切速率
根据文献[3]中表3.3-5可知t_注射机最短注射时间,所选时间合理。
4)
叫6V3
G乙h2
610.712=1.24104s」,基本合理。
0.160.18
分流道剪切速率
"
鲁=疇=6.13102gJ,合理。
式中
qR
Vr
t
12件8.06心,Rg2A
X兀L
1.55
0.24
(3)主流道剪切速率
33=2.57103sJ,基本合理。
-0.243
式中Rs二Rn=0.24,qs
=Vs=32.56cm3/s。
t
5成型零件的结构设计和计算
5.1定模部分的型芯与型腔
由于该塑件圆筒内的中间有一凸台,故需要在动,定模部分同时设置型芯。
取凸
台向小内径的一面为动,定模两型芯的接触表面。
该模具的型腔开设在定模上。
成型零部件工作尺寸计算有平均值法和公差带法两种。
本设计为便于计算采用平均值法。
塑件尺寸按经济级6级计算。
(公式参考文献⑴7-7,7-9,7-11,7-13,7-14)
1)型腔尺寸的计算(见图5-1)
(1)采用整体式型腔
(2)尺寸的计算。
其中塑件尺寸按入体原则查文献⑴表3-2(SJ1372-1987公差数值表)
式中Sep——塑件的平均收缩率,PE为2.0%;
塑件的尺寸公差,见上塑件尺寸公差值;
、•——模具成型零件制造误差,该塑件为小型塑件,取=-■:
。
x——修正系数,对于中、小塑件,二八/3,:
c八/6,则得:
型腔径向尺寸:
Lm=[(1Scp)Ls^-.-j0Z
4
同理,型腔高度尺寸:
Hm二[(1Scp)Hs1Jo'
.52/3
=38.4100.173
_.-0.44/3
②Hm2二[(1Sep)Hs2-;
:
]o'
Z=10.0219-20.44=19.O900.147
定模上型芯I尺寸的计算(见图5-2)
(1)采用台肩固定的形式,上底面用定模座板压紧。
其中塑件尺寸按入体原则查文献⑴表3-2(SJ1372-1987公差数
值表)
塑件尺寸dsi二2。
°
.44,hsi=25.5o0.40,*=3。
024,Q二就44,
标注制造公差后得文献[1]公式7-8,7-12:
Im=[(1Sep)IsX:
][z
厶——塑件的尺寸公差,见上塑件尺寸公差值;
、•——模具成型零件制造误差,该塑件为小型塑件,取亠
x——修正系数,对于中、小塑件,「八13,、:
c-1/6,则得:
型芯径向尺寸: