机械制造工艺学实验指导书Word文件下载.docx
《机械制造工艺学实验指导书Word文件下载.docx》由会员分享,可在线阅读,更多相关《机械制造工艺学实验指导书Word文件下载.docx(25页珍藏版)》请在冰豆网上搜索。
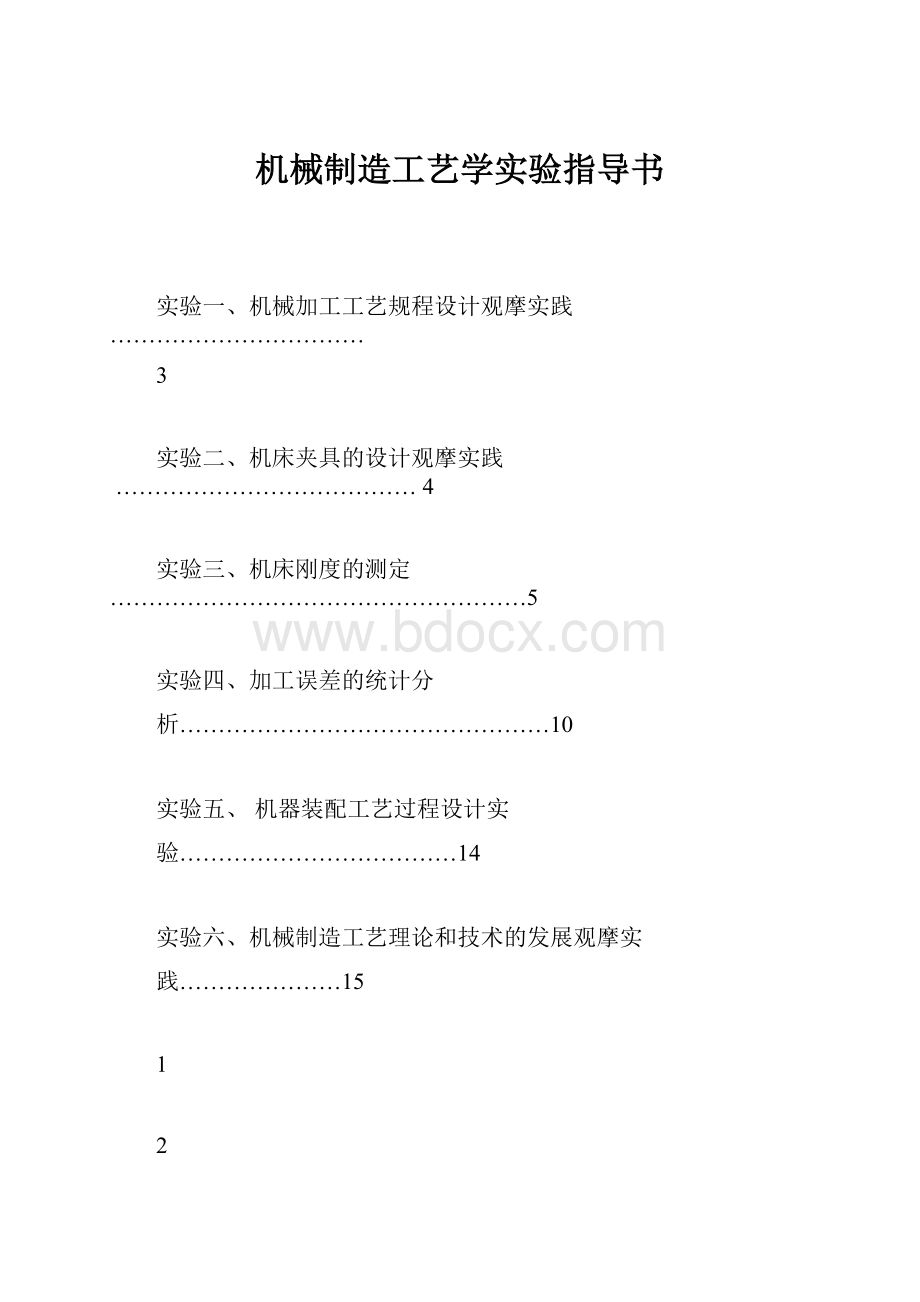
(4)通过实物观摩,分析车床夹具结构主要由哪几部分组成?
(5)实物观摩中见到的哪些夹具设有对刀装置,以结构示意图的形式表示对
刀装置结构特点,指出对刀工作面,如何减少对刀过程中对刀块工作面的磨损?
由实验指导教师给出学生实验成绩(优、良、中、及、差),其中差为不及
格。
实验报告占70%,实验过程占30%。
5
6
实验三、机床刚度测定
1、机床静刚度测定实验(2
一、实验目的:
通过实验,使学生进一步了解由机床(包括夹具)一工件一刀具所组成的
工艺系统是一弹性系统,在此系统中因切削力、零件自重及惯性力等的作用,
工艺系统各组成环节会产生弹性变形及系统中各元件之间若有接触间隙,在外
力的作用下会产生位移,并且熟悉机床静刚度的测量方法和计算方法,从而更
深的理解机械制造工艺中的工艺设备及其对零
件加工质量的影响,提高学生分析和处理问题
的能力。
二、实验设备与仪器
1、普通卧式车床机床一台
。
2、单向静刚度测定装置一套。
三、
实验原理
机床静刚度测定实验是在机床不工作状态
下,模拟切削时的受力情况,对机床施加静载荷,然后测出机床各部件在不同
静载荷下的变形,就可作出各部件的刚度特性曲线并计算出其刚度。
图
1
机床静刚度测定装置图
四、
实验步骤
如图
所是:
在
C616
车床的顶尖间装上一根刚度很大的光轴Ⅰ,其受力
后变形可忽略不计,螺旋加力器
5
固定在刀架上,在加力器
6
与光轴间装一
测力环
7
,在该环之内孔中固定安装一千分表
3
,当对如图所安装的测力环
加力时,千分表
的指针就会转动,其转动量与外载荷的对应关系可在材料实
验机上预先测出。
本实验中测力环的变形与外载荷(
0
-
1500N
时)的对应关
系见表
实验时,将测力环抵在刚性轴的中点处,在刚性轴靠近主轴端装有
千分表
,在刚性轴靠近尾架端装有千分表
2
,在刀架处装有千分表
4
,用
扳手转动带有方头的加力螺杆
施一外载荷(
Fy
),加载大小由千分表
的指针转动量所指示,千分表
的指针转动量与加载关系如表
所示,每次
加载和卸载时,分别记录下千分表
1,2,4
的读数。
为了说明机床的静刚度与尾
7
尾座套筒伸出
5mm
105mm
测力环
受载荷
(N)
千分表读数(μm)
N
千分表读数(μm
车头
刀架
尾座
加
载
减
100
200
300
400
500
600
700
800
900
1000
测力环所受载
荷(kg)
10
20
30
40
50
60
70
80
90
千分表指示数
(μm)
座套筒的伸出长度有关,实验时,可将套筒分别伸出
5mm
和
10mm
后各进行
一次实验,可对实验结果进行比较。
具体步骤:
1、.按图
把单向静刚度仪装在车床上,同时装好千分表。
2.、把测力环抵在刚性轴的中点处,使千分表
的指针指零,转动加力螺
杆
预加载荷
500N后卸载,然后,重新调整千分表
,使其指针指零。
3.、按照表
所给出的测力环所受载荷与千分表指示数之间的对应关系,
测力环每次加载
100N,顺次加至
1000N,把每次加载后千分表
的位移
数值记录到表
2中。
4.加载至
1000N时,这时进行卸载,每次卸载
100N,直至载荷为零,切
把每次卸载后千分表
的位移数值记录到表
5.加载、卸载、记录要有专人负责,要严肃、认真。
表1
表2
外载荷与千分表读数记录
五、
单向静刚度的计算
8
机床的静刚度是由机床各个部件刚的刚度决定的。
实验时把测力环抵在刚性轴的中点
处,则机床的静刚度与床头、尾座、刀架它们之间的刚度关系可以用下式表示:
k
机
=
+
(
机
尾
)
式中
k
头
F头
y头
刀
F刀
y刀
F尾
y尾
式中
y头
、
y刀
y尾
为在其所受不同载荷的情况下,床头、尾座、刀架的对应
位移值,该值可由千分表
中读出,
即千分表3对应数值,
F
头
F
,则
刀
等于加载数值。
六
六、实验结果与分析
1.当测力环承受载荷800N时,分别计算尾座套筒伸出长度5mm和
105mm机床静刚度的具体数值。
2.画出尾座套筒分别伸出5mm和105mm时尾座的刚度曲线图,其中横坐标
为刀架水平位移量(μm),纵坐标为
y
值。
3、根据实验数据及所作刚度曲线对实验结果进行分析
(1)尾座套筒伸出
105mm
时所做刚度曲线倾斜度不同说明什么问
题?
(2)为何加载曲线与卸载曲线不重合?
(3)刚度曲线上的残留变形由何而来?
(4)根据实验结果,讨论提高工艺系统刚度的措施
七、考核方式与评分办法
9
2、用“生产法”测定车床刚度实验(2
1、深入理解机床刚度、工艺系统刚度、毛坯误差复映系数三个基本概念,并掌握它们
的计算方法。
2、掌握“生产法”测定机床刚度的原理和方法。
3、分析机床刚度,毛坯误差对加工精度的影响规律,并绘制表示所产生的形状误差。
二、实验原理
本实验主要运用复映规律及工艺系统刚度与各组成环节刚度的关系,计算
机床各部件的刚度。
根据:
⊿g/⊿m=λCFyf0.75/kxt=ε(复映系数)
K
XT
=λCFyf0.75
ε
在车床顶尖装夹一根刚度极大的心轴。
心轴在靠近前顶尖、后顶尖及中间
三处各预先车出一台阶,尺寸分别为
DⅠ1
、DⅠ2
、D21、D22
、D31
D32
给定一个已知的毛坯误差⊿m,一次走刀后,尺寸分别为
dⅠ1、、、dⅠ2、d21、、d22、d31、、d32,实测出⊿g,算出误差复映系数
ε1、ε2、ε3.并根据
给定的工件材料,切削条件,由“切削原理”查得
CFy、λ,故可用上式计算出
各个位置的系统刚度,即
kxtⅠ、kxtⅡ、kxtⅢ。
由于心轴刚度极大,其变形可忽略
不计,车刀的变形也可忽略,故上面三处的系统刚度就是三处的机床刚度。
因
此可用以下三元一次方程,求解机床三个部件的刚度。
既
ktj(头架刚度)、
kwz(尾座刚度)、kdj(刀架刚度)。
1/kxtⅠ=(1/ktj)+(1/kdj)
1/kxtⅡ=(1/kdj)+0.25[(1/ktj)+(1/kwz)]
1/kxtⅢ=(1/kwz)+(1/kdj)
三、实验设备及试件
1、设备:
带尾座的车床
2、量具:
外径千分尺
3、试件:
预车如图所示三个台阶来形成三个⊿m。
DⅠ1DⅠ2D21D22D31D32
毛坯误差
⊿mⅠ=
⊿mⅡ=
⊿mⅢ=
零件误差
⊿gⅠ=
⊿gⅡ=
⊿gⅢ=
复映系数
εⅠ=⊿gⅠ/⊿mⅠ=
εⅡ=⊿gⅡ/⊿mⅡ=
εⅢ=⊿gⅢ/⊿mⅢ=
试件图
四、实验步骤
1、熟悉机床操作,将试件安装在两顶尖间,松紧适度。
2、选择切削参数,可参考以下范围:
f=0.1~0.4mm/r,ap=0.5~1mm,v
根据
所选择刀具材料确定,不宜过高或过低。
3、测定试件毛坯误差⊿m(三处)并记录。
4、按所选择参数调整机床,一次走刀车削三个台阶。
5、加工完毕,测量工件有关尺寸,列表记录△m、△g
的值,填入表
一中。
表一
误差记录及复映系数计算表
1、计算出三处的复映系数
ε
并填入表一。
2、按公式
K
XT
=λCFyf0.75ε
计算出三处系统刚度,并按相应公式算出
机床三部件的刚度
Kct、Kwz、Kdj。
3、分析
1)三处的
Kj
值是否相同?
为什么?
2)分析本车床刚度情况,并估计它对工件形状误差的影响。
3)若要提高本机床的刚度,可采取哪些措施?
七、注意事项
1.安装心轴前,松开屋座架,移动屋座架使两顶尖之间的距离略大于夹具
11
心轴的距离,然后紧固尾座,应注意尽量缩短尾座套筒的悬伸长度。
2.转动尾座手轮,使心轴在两顶尖之间松紧程度适宜,既不允许整个装置
有轴向或径向移动,又不能顶得太紧烧坏顶尖孔,然后锁紧尾顶尖。
3.
由于心轴较重.装拆时须注意安全。
4.开动车床时,注意安全操作,以免意外事故。
八、考核方式与评分办法
由实验指导教师给出学生实验成绩(优、良、中、及、差),其中差为不及格。
实验报
告占
12
实验四、
加工误差的统计分析(2
一、实验的任务、性质和目的
1、任务:
在调整好的万能外圆磨床上连续加工一批同样尺寸的试件(实验
前已加工好,并编号序号),测量其加工尺寸,对测得的数据进行不同的处理,
以巩固机制工艺学课程中所学到的有关加工误差统计分析方法的基本理论知识,
并用来分析此工序的加工精度。
2、性质:
综合性实验。
3、目的:
(1)掌握加工误差统计分析方法的基本原理和应用。
(2)掌握样本数据的采集与处理方法,要求:
能正确地采集样本数据,并能
通过对样本数据的处理,正确绘制出加工误差的实验分布曲线和图。
(3)能对实验分布曲线和图进行正确地分析,对加工误差的性质、工序
能力及工艺稳定性做出准确的鉴别。
(4)培养对加工误差进行综合分析的能力。
二、实验设备、仪器及试件
设备:
万能外圆磨床;
测量仪器:
千分尺一把
;
01
试件:
已加工好的
φ50
++0.06
mm
的
45
钢(淬火)100
件
三、实验原理
在实际生产中,为保证加工精度,常常通过对生产现场中实际加工出的一
批工件进行检测,运用数理统计的方法加以处理和分析,从中寻找误差产生的
规律,找出提高加工精度的途径。
这就是加工误差统计分析方法。
加工误差分
析的方法有两种形式,一种为分布图分析法,另一种为点图分析法。
1.分布图分析法
分布图分析法是通过测量一批加工零件的尺寸,把所测到的尺寸范围分为
若干个段。
画出该批零件加工尺寸(或误差)的实验分布图。
其折线图就接近
于理论分布曲线。
在没有明显变值系统误差的情况下,即工件的误差是由很多
相互独立的微小的随机误差综合作用的结果,则工件尺寸分布符合正态分布。
利用分布曲线图可以比较方便地判断加工误差性质,确定工序能力,并估算合
格品率,但利用分布图分析法控制加工精度,必须待一批工件全部加工完毕,
测量了样本零件的尺寸后,才能绘制分布图,因此不能在加工过程中及时提供
控制精度的信息,这在生产上将是很不方便的。
2.点图法
13
每组件数
n
A2
D1
D2
0.73
2.28
0.58
2.11
在生产中常用的另一种误差分析方法是点图法或图法。
点图法是以顺
序加工的零件序号为横坐标,零件的加工尺寸为纵坐标,把按加工顺序定期测
量的工件尺寸画在点图上。
点图可以反映加工尺寸和时间的关系,可以看出尺
寸变化的趋势,找出产生误差的原因。
图称为平均尺寸——极差质量控制图。
一般是在生产过程开始前,先
加工一批试件(本实验中即用本批加工的零件作为试件),根据加工所得的尺寸,
求出平均值
x
和极差
R
而绘制成的。
点图:
中线
i=1
上控制线
下控制线
xs
=
+
A2
R
xx
∑
Ri
上控制线Rs
D1
下控制线Rx
D2
xi
是将一批工件依照加工顺序按
n
个分为一组第
i
组的平均值,共分成
组;
Ri
是第
组的极差;
A2、D1、D2
的数值根据数理统计原理而定出(见表
1)。
表
将生产中定期抽样的尺寸结果,点在图上,从点子在图中的位置便可
看出
的波动,它反映了工件平均值的变化趋势和随机误差的分散程度。
图上的控制界限线,就是用来判断工艺是否稳定的界限。
因此图是
用来判断工艺过程的稳定性的。
1.
按万能外圆磨床操作方法,加工一批零件(本实验为
100
件)。
加工完的零件,
擦洗干净,按加工顺序放置好。
2.
按加工顺序测量工件的加工尺寸,记录测量结果。
绘制直方图和分布曲线
14
1)找出这批工件加工尺寸数据的最大值
xmax
和最小值
xmin,按下式计算出极差
R。
R=xmax
一
xmin
2)确定分组数
K(K
一般根据样本容量来选择,建议可选在
8~11
之间)。
3)按下式计算组距
d。
4)确定组界(测量单位:
微米)。
5)做频数分布表。
6)计算
和σ
7)画直方图
以样本数据值为横坐标,标出各组组界;
以各组频率密度为纵坐标,画出直方图。
8)画分布曲线
若工艺过程稳定,则误差分布曲线接近正态分布曲线;
若工艺过程不稳定,则应
根据实际情况确定其分布曲线。
画出分布曲线,注意使分布曲线与直方图协调一致。
9)画公差带
在横轴下方画出公差带,以便与分布曲线相比较。
4.
绘制图
1)确定样组容量,对样本进行分组
样组容量
m
通常取
或
件。
按样组容量和加工时间顺序,将样本划分成若干
个样组。
2)计算各样组的平均值和极差
对于第
个样组,其平均值和极差计算公式为:
m
j=1
式中——第
个样组的平均值;
——第
个样组的标准差;
——第
个样组第
j
个零件的测量值;
个样组数据的最大值;
个样组数据的最小值
3)计算图控制限(计算公式见实验原理)
4)绘制图
以样组序号为横坐标,分别以各样组的平均值和极差
为纵坐标,画出
15
图,并在图上标出中心线和上、下控制限。
5.
按下式计算工序能力系数
Cp
6.
判别工艺过程稳定性
可按下表所列标准进行判别。
注意,同时满足表中左列
个条件,工艺过程稳定;
表
中右列条件之一不满足,即表示工艺过程不稳定。
7.
加工误差综合分析
通过对分布图和图的分析,可以初步判断误差的性质。
进而结合具体加工条件,
分析影响加工误差的的各种因素,必要时,可对工艺系统的误差环节进行测量和实验。
五、实验基本要求
明确实验目的、内容、条件及实验步骤,记录好实验原始数据。
绘制直方图和分布曲线;
绘制图。
计算工序能力系数
Cp。
根据实验结果分析并讨论:
1)本工序的实验分布曲线图是否接近正态分布曲线?
并估算合格品率或者不合
格品率。
若有不合格品,判断为可修复还是不可修复。
2)根据工序能力系数
Cp,本工序属哪一级?
如果出现了废品,试分析产生废品的原因。
3)从图看,本工序的工艺过程稳定吗?
如果不稳定,试分析其原因。
4)分析判别加工误差的性质,分析影响加工误差的主要因素,并对加工方案提出改进
措施。
实验
报告占
16
实验五、
机器装配工艺过程设计实验(2
通过实验掌握机器装配的基本方法和绘制装配系统图的方法。
二、实验环境和设备
1、机械装配车间。
2、装配工具一套。
3、机床减速箱或车床主轴箱或溜板箱或进给箱等部件一套。
三、实验内容
按要求进行机器或部件(减速箱、车床主轴箱、溜板箱)拆装,掌握机器
装配的基本方法并绘制装配系统图。
1、选择拆装对象;
2、进行拆装过程;
3、绘制装配系统图。
五、实验要求
1、掌握机器装配的基本方法并绘制装配系统图。
2、回答以下问题:
(1)何谓零件、套件、组件和部件?
何谓机器的总装?
(2)常用的装配方法有哪些,分别应用于什么场合?
(3)对实验有何建议?
六、考核方式与评分办法
17
实验六
、机械制造工艺理论和技术的发展
观摩实践(2
了解机械制造工艺理论和技术的发展的方向,了解现代制造工艺的常用的
方法。
二.实践环境
1、先进制造车间。
2、线切割机床、快速成形机床等。
(1)
通过观摩,分析电火花加工的基本原理和加工特点。
通过观摩,分析快速成形制造方法的特点及其应用场合。
(3)通过观摩,结合理论教学,总结你所知道的现代制造工艺方法有哪些?
先进制造模式有哪些?
(4)总结实验的心得体会。
18