表面处理的概念汇总文档格式.docx
《表面处理的概念汇总文档格式.docx》由会员分享,可在线阅读,更多相关《表面处理的概念汇总文档格式.docx(33页珍藏版)》请在冰豆网上搜索。
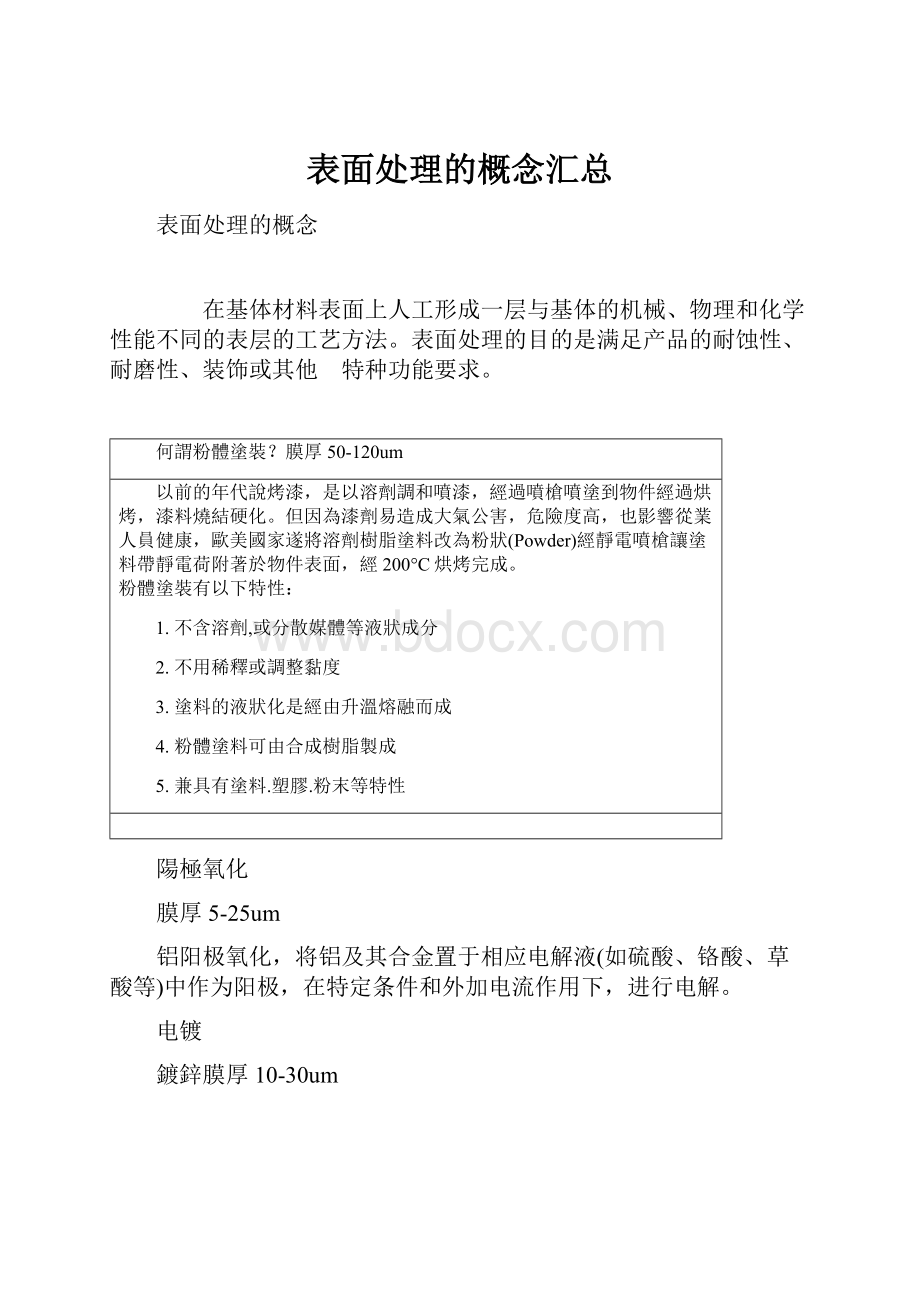
因此,在选择药剂时应考虑环境保护的需要。
所以选择除油剂时要求配制简单,去污能力强,不含常温下难清洗的氢氧化钠,硅酸盐,OP乳化剂等成分,常温下易水洗,不含毒性物质,不产生有害气体,劳动条件好;
选择除锈剂时要求内含促进剂,缓蚀剂和抑制剂,能提高除锈速度,防止工件产生过腐蚀和氢脆,能较好的抑制酸雾。
尤其值得重视的是酸雾抑制,酸洗除锈过程中产生的酸雾,不仅腐蚀设备和厂房,污染环境,而且可引起人们牙齿腐蚀,牙结膜发红,流泪,疼痛,咽喉干燥,咳嗽等症状,所以,有效抑制酸雾,不但是环保的需要,还是本单位自身的需要。
考虑上述要求,经筛选,除油和除锈剂我们采用了,常温下使用,处理时间10-30min,它能提高除锈速度,防止工件产生过腐蚀和氢脆,能较好的抑制酸雾。
2、水洗
除油除锈后的水洗,虽然属于涂装前的辅助工序,但同样需引起足够的重视。
除油除锈后工件表面易附着某些非离子表面活性剂,及CL-等。
这些物质若清洗不彻底,就可能引起磷化膜变薄,产生线状缺陷,甚至磷化不上。
因此,要提高除油除锈后的水洗质量。
须经多次漂洗,采用两道水洗,时间1-2min,并经常更换清水,保证清水PH值在5-7值之间。
3、磷化
所谓磷化,是指把金属工件经过含有磷酸二氢盐的酸性溶液处理,发生化学反应而在其表面生成一层稳定的不溶性磷酸盐膜层的方法,所生成的膜称为磷化膜。
磷化膜的主要目的是增加涂膜附着力,提高涂层耐蚀性。
磷化的方法有多种,按磷化时的温度来分,可分为高温磷化(90-98℃),中温磷化(60-75℃),低温磷化(35-55℃)和常温磷化。
为提供良好的涂装基底,要求磷化膜厚度适宜,结晶致密细小。
中、高温磷化工艺,虽然磷化速度快,磷化膜耐蚀性好,但磷化膜结晶粗大,挂灰重,液面挥发快,槽液不稳定,沉渣多,而低、常温磷化工艺所形成的磷化膜结晶细致,厚度适宜,膜间很少夹杂沉渣物,吸漆量少,涂层光泽度好,可大大改善涂层的附着力、柔韧性、抗冲击性等,更能满足涂层对磷化膜的要求。
值得注意的是,过去一直认为磷化膜厚,涂装后涂层的耐蚀性高,磷化膜本身在整个涂装体系中并不单独承担多大的耐蚀作用,它主要起到使漆膜具有强粘附性,而整个涂层系统的耐蚀力则主要取决于漆膜的耐蚀力以及漆膜与磷化膜的优良配合所形成的强粘附力。
磷化液一般由主盐、促进剂和中和剂所组成。
过去使用的磷化液,大多采用亚硝酸钠(NaNO2)作促进剂,效果十分年、明显,但在NaNO2在磷化液中有很大危害:
一是影响磷化液的稳定性,NaNO2在酸性条件下极不稳定,在极短的时间内就分解了。
因此,不得不经常添加。
NaNO2的这种特性,往往引起磷化液的主盐不稳定,磷化液沉淀较多,磷化膜挂灰严重,槽液控制困难,磷化质量不稳定;
二是NaNO2是世界公认的致癌物质,长期接触危害人体健康,环境污染严重。
解决的方法:
一是减少NaNO2的用量;
二是寻找替代物。
4、钝化
磷化膜的钝化技术,在北美和欧洲国家被广泛应用,采用钝化技术是基于磷化膜自身特点决定的,磷化膜较薄,一般在1-4g/m2,最大不超过10g/m2,其自由孔隙面积大,膜本身的耐蚀力有限。
有的甚至在干燥过程中就迅速生黄锈,磷化后进行一次钝化封闭处理,可以是磷化膜孔隙中暴露的金属进一步氧化,或生成钝化层,对磷化膜可以起到填充、氧化作用,使磷化膜稳定于大气之中。
5、磷化膜的干燥
对磷化膜进行干燥处理,可起到两个方面的作用,一方面是为下道工序涂漆作准备,以除去磷化膜表面的水分,另一方面是进一步提高涂装后膜的耐蚀性。
建立涂装前处理生产线,先要完成工艺设计,然后才能进行非标设备的设计、制造和安装。
因此工艺设计是建立生产线的基础,正确、合理的路线对生产操作及产品质量将会产生良好的影响。
工艺设计的内容主要包括:
处理方法,处理时间,工艺流程等。
1处理方式工件处理方式,是指工件以何种方式与槽液接触达到化学预处理之目的,包括全浸泡式、全喷淋式、喷淋浸泡组合式、刷涂式等。
它主要取决于工件的几何尺寸及形状、场地面积、投资规模、生产量等因素的影响。
例如几何尺寸复杂的工件,不适合于喷淋方式;
油箱、油桶类工件在液体中不易沉入,因而不适合于浸泡方式。
1.1全浸泡方式将工件完全浸泡在槽液中,待处理一段时间后取出,完成除油或除锈磷化等目标的一种常见处理方式,工件的几何形状繁简各异,只要液体能够到达的地方,都能实现处理目标,这是浸泡方式的独特优点,是喷淋、刷涂所不能比拟的。
其不足之处,是没有机械冲刷的辅助使用,因此处理速度相对较慢,处理时间较长,特别是象连续悬挂输送工件时,除工件在槽内运行时间外,还有工件上下坡时间,因而使设备增长,场地面积和投资增大。
仅对磷化而言,目前国外比较趋向于采用全浸泡方式,据称全浸泡磷化易形成含铁量较高的颗粒状结晶磷化膜,与阴极电泳具有好的配套性。
1.2全喷淋方式用泵将液体加压,并以0.1~0.2Mpa的压力使液体形成雾状,喷射在工件上达到处理效果。
由于喷淋时有机械冲刷和液体更新使用,因此处理速度加快、时间缩短。
生产线长度缩短,相应节首了场地、设备、不足之处是,几何形状较复杂的工件,像内腔、拐角处等液体不易到达,处理效果不好,因此只适合于处理几何形状简单的工件。
喷淋方式也不太适合于酸洗除锈,它会带来设备腐蚀、工序间生锈等一系列问题,因此在选择喷淋酸洗时必须十分慎重。
据报道,全喷淋磷化易形成结晶枝状粗大、含铁量较低的磷化膜,国外不提倡作为阴极电泳漆前打底的前处理。
全喷淋方式主要应用于家用电器、零部件类的粉末涂装、静电涂漆、阳极电泳等。
1.3喷淋-浸泡结合式喷淋-浸泡结合式,一般是在某道工序时,工件先是喷淋,然后入槽浸泡,出槽后再喷淋,所有的喷淋、浸泡均是同一槽液。
这种结合方式即保留了喷淋的高效率,提高处理速度,又具有浸泡过程,使工件所有部位均可得到有效处理。
因此喷淋-浸泡结合式前处理即能在较短时间内完成处理工序,设备占用场地也相对较少,同时又可获得满意的处理效果。
目前在国内外,对于前处理要求较高的汽车行业,一般都趋向于采取喷淋-浸泡结合方式。
1.4刷涂方式直接将处理液通过手工刷涂到工件表面,来达到化学处理的目的,这种方式一般不易获得很好的处理效果,在工厂应用较少。
对于某些大型、形状较简单的工件,可以考虑用这种方式。
2处理温度从节省能源、改善劳动环境、降低生产成本、化学反应速度、处理时间和生产速度要求出发,在生产应用中普遍采用的是低温或中温前处理工艺。
工件除有液态油污外,还有少量固态油脂,在低温下,固态油脂很难去除,因此脱脂温度不管是浸泡还是喷淋均应选择中温范围。
如果只有液态油脂,选用低温脱脂完全可以达到要求。
对一般锈蚀及氧化皮工件,应选择中温酸洗,方可保证在10min内彻底除掉锈蚀物及氧化皮。
除非有足够的理由,一般不选择低温或不加温酸洗除锈,低温酸洗仅限于如:
工件锈蚀很少、无氧化皮;
除锈时间不受限制;
允许采用盐酸酸洗等情况。
表面调整工序,通常不需加温,一般就是常温处理。
低温或中温磷化,磷化速度都没有明显的差别,都可在较短的时间内快速形成磷化膜。
磷化后的工件,如果要求有较长的工序间存放时间,变应该选择中温磷化,才会有较好的防锈效果。
整个前处理过程,都可采用常温不加温洗方式,如果最后一道水洗是热水烫干,其水温应在80℃以上。
3处理时间处理方式、处理温度一旦选定,处理时间应根据工件的油污、锈蚀程度来定。
一般可参考前处理药剂使用说明书的处理时间要求。
4工艺流程根据工件油污、锈蚀程度以及底漆要求,分为不同的工艺流程。
4.1完全无锈工件预脱脂--脱脂--水清洗--表调--磷化--水清洗--烘干(电泳底漆时可不干燥,直接进入电泳槽)。
这是标准的四工位流程,应用面广,适合于各类冷轧板及机加工的无锈工件前处理,还可将表调剂加到脱脂槽内,减少一道表调工序。
4.2一般油污、锈蚀、氧化皮混合工件脱脂除锈“二合一”--水清洗--中和--表调--磷化--水清洗--烘干(或直接电泳)。
这套工艺是国内应用最为广泛的流程,适合各类工件(重油污除外)的前处理;
如果采用中温磷化,还可省掉表调工序,简单的板型工件,也可省掉中和工序,成为标准带锈件的四工位工艺。
4.3重油污、锈蚀、氧化皮类工件预脱脂--水清洗--脱脂除锈“二合一”--水清洗--中和--表调--磷化--水清洗--烘干(或直接进入电泳槽)。
对于重油污的工件,首先应进行预脱脂,除去大部分的油脂,以保证在下一步脱脂除锈“二合一”处理后,得到完全洁净的金属表面。
5几点注意事项在工艺设计中有些小地方应该十分注意,即使有些是与设备设计有关的,如果考虑不周,将会对生产线的运行及工人操作产生很多不利的影响,如工序间隔时间,溢流水洗,磷化除渣,工件的工艺孔,槽体及加热管材料等。
5.1工序间隔时间各个工序间的间隔时间如果太长,会造成工件在运行过程中二次生锈,特别是有酸洗工艺时,酸洗后工件极易在空气中氧化生锈泛绿,最好设有工序间水膜保护,可减少生锈。
生锈泛黄泛绿的工件,严重影响磷化效果,造成工件挂灰、泛黄,不能形成完整的磷化膜,所以应尽量缩短工序间的间隔时间。
工序间的间隔时间若太短,工件存水处的水,不能完全有效的沥干,产生串槽现象,特别在喷淋方式时,会产生相互喷射飞溅串槽,使槽液成分不易控制,甚至槽液遭到破坏。
因此在考虑工序间隔时,应根据工件几何尺寸、形状选择一个恰当的工序间隔时间。
5.2溢流水清洗提倡溢流水洗,以保证工件充分清洗干净,减少串槽现象。
溢流时应该从底部进水,对角线上部开溢流孔溢流。
5.3工件工艺孔对于某些管形件或易形成死角存水的工件,必须选择适当的位置钻好工艺孔,保证水能在较短的时间内充分流尽。
否则会造成串槽或者要在空中长时间沥干,产生二次生锈,影响磷化效果。
5.4磷化除渣对于任何一种磷化液都会或多或少产生沉渣(轻铁系彩色磷化沉渣很少),应在工艺予设计时注明设有磷化除渣装置,特别是喷淋磷化时,除渣装置必不可少,典型的除渣装置有:
斜板沉淀器、高位沉淀塔、离心除渣器、纸布袋滤渣等都可供选择。
5.5槽体及加热管材料虽然对于槽体加热管材料的选择不是工艺设计的内容,如果在工艺设计时不予提醒,可能会造成设备设计人员的疏忽,而影响整个生产线的运行。
对于硫酸、盐酸酸洗时,其槽体材料只能选用玻璃钢、花岗岩、塑料,加热管只能选用铅锑合金管、陶瓷管,而不能选用不锈钢材料。
如果是采用磷酸酸洗,其槽体及加热管材料均可选用不锈钢材料,当然玻璃钢、塑料、花岗岩均可。
勤动手,多思考,勤分析,多动脑,勤记录,多比较
前处理工艺容易存在的问题及解决办法
工艺环节
问题
原因
解决方法
除油部分
除油不干净
1、除油液浓度低
2、除油时间短
3、除油温度低
4、局部油脂太厚
5、除油槽表面的油脂浮层厚
6、喷淋处理中喷嘴堵塞
7、工件处理量大,无及时补加
1、增加浓度
2、延长时间
3、温度升高
4、增加预处理(手工)
5、将油层撇出
6、加强清洗喷嘴
7、及时添加药剂
除锈部分
除锈不彻底
1、除锈液浓度低
2、除锈时间短
3、高温形成的氧化皮太厚,太致厚
4、除锈液中铁离子含量过高,防锈液失效
3、增加机械辅助除锈
4、更换新槽液
除锈液酸太大或工件除锈后有氢脆或过腐蚀
1、浓度太高
2、添加剂不足
3、时间过长
1、加入水稀释
2、加入添加剂
3、时间减少
磷化部分
磷化膜结晶粗糙
1、游离酸度高
2、有残酸
3、工件表面过腐蚀
1、用中和剂降低游离酸度
2、加强中和水洗
3、控制浓度、时间
磷化膜过薄,无明显结晶
1、游离酸度低
2、总酸度高
3、工件表面有硬化层
4、温度过低
5、亚铁离子含量过低
1、加磷化液后再加中和剂调整
2、用水稀释
3、加强酸洗
4、提高温度
5、增加亚铁离子
磷化膜耐蚀性差,在干燥过程中出现返锈现象
1、磷化膜粗
2、总酸度低
3、工件表面有残液
4、磷化温度低
5、磷化时间短
6、工件在干燥过程中有重叠现象
7、工件局部有积水现象
1、降低游离酸度
2、增加磷化液
3、加强中和水洗
5、增加时间
6、分开单体摆放
7、改变工件放置角度
磷化后工件有挂灰现象
1、游离酸度过低
2、水洗不干净
1、增加游离酸度
2、加强水洗
磷化膜不均匀
1、除油不净
2、工件表面有硬化层
3、热处理后材质不均匀
1、加强除油
2、加强酸洗
3、加强酸洗
粉末喷枪操作、保养
1、安全规则:
为确保安全和有效地使用本设备,必须遵守以下原则。
1.1
带有心脏起搏器的人在任何情况下都不要接近喷枪喷嘴和待喷涂工件的区域!
1.2
只能在装配有工业通风设施的粉末喷房或者粉末喷房工作台内使用本喷枪
1.3
用户必须确保粉末、空气浓度的平均值不超过低爆水平(LEL)的50%(粉末在空气中的最大浓度)假如LEL未知用户应假设其为20G/M3。
1.4
维修工作只能由受过专业培训的人员实施。
1.5
工作区域所有的人员必须穿静电导电鞋。
如果使用手套,必须由防静电材料制
成的手套或者手掌区域剪有开口的手套。
1.6
穿好合适的工作服,使用呼吸用具
2、危险及防范措施
危险
防范措施
静电弧光可能引起爆炸或火灾。
粉末、空气混和物可能爆炸或燃烧,引起财产损失和人员伤亡
A、操作者必须接地。
当穿橡胶鞋底时必须使用接地条
B、操作者必须接触喷枪把手,使用掌心部分开有缺口的工作手套
C、操作者应去除周围一切未接地的金属物体。
D、被喷涂工件必须接地。
E、喷涂区域所有金属必须接地(包括喷房、工件吊具、灭火装置等)
F、喷涂区域内使用导电地板
G、清理喷枪时必须切断电源
爆炸或者火灾。
粉末空气混和物可能爆炸或燃烧引起财产损失或人员伤亡。
A、喷涂区域内注意排气和输入新鲜空气。
防止空气可燃气体的聚集。
B、喷涂区域内严禁吸烟。
C、喷涂区域内需配备灭火设备。
D、避免电晕弧光产生。
E、避免各种火种的发生,如静电火花、烟头、电器开关产生的火花。
有害物质:
部分材料有害身体不得下咽
A、遵守生产商提供的材料安全数具表的各项要求。
B、喷涂区域内注意排气及输入新鲜空气、避免粉末高度沉积
C、须带口罩,确保能有效地防止吸入粉末。
无害放电
A、高压打开时电极针尖处会产生电辉和电晕放电。
当电极接近工件时可以观察到这种物理现象。
这种电辉放电电力不会产生任何点火能力,也不会对设备处理产生任何影响。
B、如果手指碰到喷枪的塑料部件,会发生无害得放电(所谓的环形放电)塑料部件的电荷是由喷枪的高静电场引起的。
这内放电不会造成任何点火能力
粉末静电喷涂作业的常见问题及解决方法:
现象
分析
对策
涂层杂质
喷粉室或烘干炉内环境颗粒
粉末添加剂或挤压产生的杂质
提高粉末质量,改善储运条件
前处理工艺中的杂质
涂层缩孔
工件表面有油污
彻底清理室体内壁和设备,注意开口部的封堵
压缩空气中含水过量
采用无油干燥压缩空气
输送系统的油滴
做好输送系统润滑油的防滴落措施
不同种类的粉末混在一起
换粉时要清理彻底
涂层色差
烘干温度和时间不同
控制输送速度及烘炉温度
粉末颜料分布不均
改善粉末质量
涂层厚度不均匀
调整喷粉设备的参数
涂层附着力差
前处理后水洗不彻底
调整系统参数,改善水洗效果
局部磷化膜质量差
调整磷化液浓度和温度
工件表面水分去除不干净
提高水分烘干效果
固化温度低
重新调整烘干炉供风温度
粉末静电喷涂技术的典型工艺流程
粉末静电喷涂技术的典型工艺流程为:
工件前处理→喷粉→固化→检查→成品
1.1前处理
工件经过前处理除掉冷轧钢板表面的油污和灰尘后才能喷涂粉末,同时在工件表面形成一层锌系磷化膜以增强喷粉后的附着力。
前处理后的工件必须完全烘干水分并且充分冷却到35℃以下才能保证喷粉后工件的理化性能和外观质量。
1.2喷粉
1.2.1粉末静电喷涂的基本原理
工件通过输送链进入喷粉房的喷枪位置准备喷涂作业。
静电发生器通过喷枪枪口的电极针向工件方向的空间释放高压静电(负极),该高压静电使从.喷枪口喷出的粉末和压缩空气的混合物以及电极周围空气电离(带负电荷)。
工件经过挂具通过输送链接地(接地极),这样就在喷枪和工件之间形成一个电场占粉末在电场力和压缩空气压力的双重推动下到达工件表面,依靠静电吸引在工件表面形成一层均匀的涂层。
1.2.2粉末静电喷涂的基本原料
用室内型环氧聚酯粉末涂料。
它的主要成分是环氧树脂、聚酯树脂、固化剂、颜料、填料、各种助剂(例如流平剂、防潮剂、边角改性剂等).粉末加热固化后在工件表面形成所需涂层。
辅助材料是压缩空气,要求清洁干燥、无油无水[含水量小于1.3g/m3、含油量小于1.0×
10-5%(质量分数)]
1.2.3粉末静电喷涂的施工工艺
●静电高压60-90kV。
电压过高容易造成粉末反弹和边缘麻点;
电压过低上粉率低。
●静电电流10~20μA。
电流过高容易产生放电击穿粉末涂层;
电流过低上粉率低
●流速压力0.30-0.55MPa.流速压力越.高则粉末的沉积速度越快,有利于快速获得预定厚度的涂层,但过高就会增加粉末用量和喷枪的磨损速度。
●雾化压力0.30~0.45MPa。
适当增大雾化压力能够保持粉末涂层的厚度均匀,但过高会使送粉部件快速磨损。
适当降低雾化压力能够提高粉末的覆盖能力,但过低容易使送粉部件堵塞。
●清枪压力0.5MPa。
清枪压力过高会加速枪头磨损,过低容易造成枪头堵塞。
●供粉桶流化压力0.04~0.10MPa。
供粉桶流化压力过高会降低粉末密度使生产效率下降,过低容易出现供粉不足或者粉末结团。
●喷枪口至工件的距离150~300mm。
喷枪口至工件的距离过近容易产生放电击穿粉末涂层,过远会增加粉末用量和降低生产效率。
●输送链速度4.5~5.5m/min。
输送链速度过快会引起粉末涂层厚度不够,过慢则降低生产效率。
6.不含溶劑,或分散媒體等液狀成分
7.不用稀釋或調整黏度
8.塗料的液狀化是經由升溫熔融而成
9.粉體塗料可由合成樹脂製成
10.兼具有塗料.塑膠.粉末等特性
為何要用粉體塗裝?
粉體塗裝之於液體烤漆,明顯有下面幾種好處:
1.沒有溶劑揮發的針孔
2.噴塗膜厚度較厚,覆蓋力一定較好
3.烘烤溫度較高,樹脂硬化較硬,較耐磨耗,邊角不易擦傷
4.原廠電腦配製色粉,不易色差,不像液體三原色,烤漆廠可隨意調色造成困擾
基於對地球環境的愛護,並減低不良塗裝所造成的二次公害(如腐蝕,醜陋外觀…等),請選擇無溶劑施工方式的粉體塗裝。
粉體塗裝的作業流程為何?
作業作業流程主要包含了前處理藥液技術和粉體塗料技術,將前處理藥液技術和粉體塗料技術,徹底的結合與切實執行,即是優良粉體塗裝的完整流程。
阳极氧化
金属或合金的电化学氧化。
将金属或合金的制件作为阳极,采用电解的方法使其表面形成氧化物薄膜。
金属氧化物薄膜改变了表面状态和性能,如表面着色,提高耐腐蚀性、增强耐磨性及硬度,保护金属表面等。
例如铝阳极氧化,将铝及其合金置于相应电解液(如硫酸、铬酸、草酸等)中作为阳极,在特定条件和外加电流作用下,进行电解。
阳极的铝或其合金氧化,表面上形成氧化铝薄层,其厚度为5~25微米,硬质阳极氧化膜可达60~200微米。
阳极氧化后的铝或其合金,提高了其硬度和耐磨性,可达250~500千克/平方毫米,良好的耐热性,硬质阳极氧化膜熔点高达2320K,优良的绝缘性,耐击穿电压高达2000V,增强了抗腐蚀性能,在ω=0.03NaCl盐雾中经几千小时不腐蚀。
氧化膜薄层中具有大量的微孔,可吸附各种润滑剂,适合制造发动机气缸或其他耐磨零件;
膜微孔吸附能力强可着色成各种美观艳丽的色彩。
有色金属或其合金(如铝、镁及其合金等)都可进行阳极氧化处理,这种方法广泛用于机械零件,飞机汽车部件,精密仪器及无线电器材,日用品和建筑装饰等方面。
补充:
除金属外,其他物质在阳极所引起的氧化作用,也称为“阳极氧化”
阳极处理,阳极氧化用电解方式给(金属面)镀上一层保护性或装饰性的氧化物
化学抛光化学抛光是靠化学试剂对产品表面凹凸不平区域的选择性溶解作用消除磨痕、浸蚀整平的一种方法。
化学抛光的优点化学抛光设备简单,可以处理形状比较复杂的零件
化学抛光的缺点
1、化学抛光的质量不如电解抛光。
2、化学抛光所用溶液的调整和再生比较困难,在应用上受到限制。
3、化学抛光操作过程中